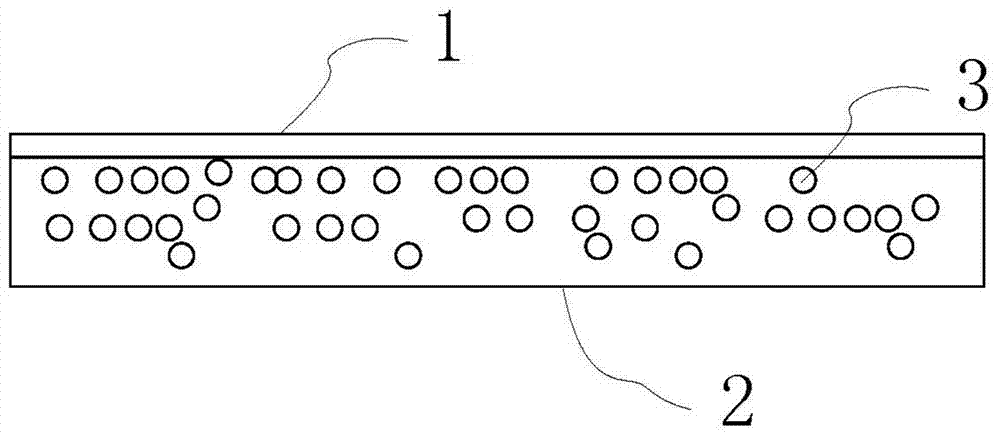
本發(fā)明涉及一種重組竹地板及其制造方法,尤其涉及一種經過油熱浸漬處理的重組竹地板。
背景技術:我國是竹子大國,竹子產量大,且擁有悠久的竹材利用歷史,竹制品豐富。竹材具有韌性好、強度大的優(yōu)點,在市場上被制作成室內地板、戶外地板和家具等的原材料。然而竹材內含有大量的糖分、蛋白質,內含物豐富,因此極易受到竹腐真菌的侵害與腐蝕;木質素、半纖維素和纖維素的存在,使重組竹材料的尺寸穩(wěn)定性差;并且在重組過程中需要大量的使用膠黏劑,因此帶來甲醛釋放量大的問題;上述問題都對重組竹在戶外的應用提出了嚴峻的考驗。為解決上述技術問題,現有技術方案CN201220024883.6中披露了一種表面附有防腐層、防腐層表面一體成型有由溝槽形成立體紋路的一種竹地板結構,該技術方案的防水防腐材料附著力強,無需重復涂刷防水層。但是該技術方案僅從表面解決了竹材霉腐的問題,對竹材(重組竹)內部的霉腐問題無法解決,且該技術方案所解決的技術問題相對單一。在發(fā)明專利CN201110008771.1中披露了一種采用油棕油熱改性木材的方法,利用油棕油對木材進行油浴處理,方法是將加熱到150℃~180℃的油棕油注入木材處理罐中,待木材內部溫度達到150℃時,以30℃/h的速度升溫至200℃~215℃,處理時間為0.5~3h。該技術是針對木材的油浴熱處理技術,改善了木材的吸濕性,同時高溫保護介質由惰性氣體、過熱蒸汽改為油棕油后,處理木材的力學性能損失減少,保護了木材的力學強度。但是該技術需要分階段、緩慢升溫,冷卻時需要在處理罐中冷卻至一定溫度后才能取出,材料在油浴過程中易開裂、變形,處理時間較長,因此生產效率低。同時該技術對于木材改性處理僅停留在熱處理,而竹材的導管結構更為發(fā)達,直接應用在竹材時,處理后的竹材任會與外界水分發(fā)生交換,在使用過程中改變產品的尺寸,影響正常使用。在發(fā)明專利CN201410026572.7中披露了一種防腐重組復合竹材的加工工藝,方法是將竹束在高壓下浸漬納米氧化鋅和竹霉凈的混合水溶液,再通過高溫熱固化處理對重組復合材進行高溫熱處理,達到防霉、改善穩(wěn)定性的效果。該技術浸漬過程需要高壓環(huán)境,再抽真空,浸漬工序復雜,在模具(熱壓機設備)內對復合材進行高溫熱處理,兩道工序間的材料需要重復裝卸,設備、藥劑重復升溫和冷卻,使該工藝技術對設備要求高,熱壓處理效果不均勻,可處理的材料的尺寸(特別是厚度)有一定的局限,生產效率低下,浸漬深度小,熱處理程度淺。
技術實現要素:本發(fā)明的目的之一是提供一種重組竹地板,該地板內外處理均勻一致、力學性能佳、尺寸穩(wěn)定性佳、耐腐防霉性好。本發(fā)明的目的之二是提供一種用于生產上述重組竹地板的生產工藝,該工藝工序簡單、工作效率高、設備投入少、處理效果均勻。本發(fā)明的第一個技術目的是通過以下技術方案得以實現的:一種重組竹地板,由竹絲與膠黏劑壓合組成,所述重組竹地板的導管或其他毛細結構中填充油介質,含油量為2-10%。現有的產品,在經高溫熱處理之后,內部導管或其他毛細結構呈中空或半中空狀態(tài),對產品的力學性能產生極大的損失,影響產品在承重位置的使用;表層的浸漬處理僅針對產品的表面,內部任然存在受到霉腐的風險。本發(fā)明的有益效果是,將油介質填充入產品的導管和其他毛細結構中,起到了加強結構的效果,強化了產品的力學性能,使產品特別適用于戶外環(huán)境的地面鋪裝。作為優(yōu)選,所述油介質在重組竹地板各截面上均勻分布。本發(fā)明中的技術方案中,油介質均勻并充分的填充和替代重組竹導管和其他毛細結構中的物質,使產品的表層與內部防霉腐效果、尺寸穩(wěn)定性、力學性能均勻一致,避免在使用中出現內部霉腐、因表內層穩(wěn)定性不同而產生的變形、以及內部受力破損等的質量問題。作為優(yōu)選,所述重組竹地板含水率為1-5%、防霉防變色性能(霉菌)被害值為0、吸水厚度膨脹率2-10%、吸水寬度膨脹率1-4.5%、水平剪切強度≥12MPa。作為優(yōu)選,所述重組竹地板含水率為1-3%、吸水厚度膨脹率2-4.5%、吸水寬度膨脹率1-3%。產品各項理化性能均優(yōu)于國標的限制要求,產品在使用過程中,不受霉腐、不變形、不開裂、膠層不開膠。作為優(yōu)選,所述重組竹地板的導管或其他毛細結構中填充的油介質為礦物質油、植物油、烷基聯苯型導熱油、烷基聯苯醚型導熱油、聯苯和聯苯醚低熔混合物型導熱油或烷基萘型導熱油的一種或多種。上述油介質熱穩(wěn)定好,僅與竹材發(fā)生物理的浸漬和類似于乙?;幕瘜W反應,在高溫作用下分解少、揮發(fā)物中無毒害物質,生產加工過程安全環(huán)保。作為優(yōu)選,所述重組竹地板的厚度為0-40mm。作為優(yōu)選,所述重組竹地板的厚度為15-24mm。本發(fā)明的技術方案,重組竹地板的厚度范圍大,幾乎可覆蓋各種使用場合對地板厚度的需求。作為優(yōu)選,所述重組竹地板長度方向的兩側具有槽口結構。作為優(yōu)選,它還包括飾面層,所述飾面層有UV紫外光固化油漆層、木蠟油或清漆的一種,涂層厚度為0.05-0.2mm。UV紫外光固化油漆由機器設備自動涂布,固化成膜速度快,漆膜硬度高、耐磨性好、透明度好、質量穩(wěn)定,木蠟油和清漆具有環(huán)保、涂布效果自然的優(yōu)點。本發(fā)明的第二技術目的是通過以下技術方案得以實現的:一種重組竹地板的制備方法,它由以下步驟制得:(1)施膠步驟:將竹絲與熱固型或熱固型改性樹脂膠黏劑混合獲得施膠竹絲;(2)干燥步驟:將所述施膠竹絲干燥至含水率2-30%;(3)冷壓熱固步驟:將所述干燥竹絲冷壓熱固成型;(4)油浸處理步驟:加熱油介質至100-300℃,再將冷壓成型后的型材置入熱油介質中,處理1-10h;(5)自動吸油步驟;(6)企口工序:在重組竹地板長度方向的兩側加工出槽口結構;(7)涂飾工序:在型材表面進行表面涂飾涂料。作為進一步的優(yōu)選,所述施膠步驟,是使用酚醛樹脂、脲醛樹脂或三聚氰胺甲醛樹脂的一種或多種,膠黏劑固含量為30-45%,施膠量為竹絲質量的10-25%;作為進一步的優(yōu)選,所述干燥步驟,是將型材干燥至含水率為2-20%;作為進一步的優(yōu)選,冷壓步驟后還有固化步驟,所述固化步驟是將冷壓步驟中制成的型材送入隧道(連續(xù)熱壓機的組成設備之一)進行熱固化,再將熱固化后的型材從模具中取出,所述固化步驟中的熱固化溫度為120-150℃。在此固化步驟中,膠黏劑還未完全固化,將半固化(即固化不完全)的型材進行油浸步驟后,膠黏劑實現完全固化(即未固化部分發(fā)生固化),提高了膠合性能。作為進一步的優(yōu)選,所述油浸步驟,是將冷壓成型后的型材豎向浸漬,所述豎向浸漬具體是按照使油熱蒸汽方向與冷壓成型后的型材的維管束方向相平行的方式進行浸漬。采用本發(fā)明方法可以避免竹材材料出現炸裂的質量問題,以提高處理過程的安全性和竹材油浸成色的均勻性。本發(fā)明所述維管束是指竹材導管和厚壁纖維。發(fā)明人經過長期研究發(fā)現,竹材油浸處理時的浸漬方向非常重要,不僅影響處理中的安全性,還影響竹材處理的均勻性。如果采用橫向浸漬,油熱蒸汽向上傳輸時,與竹材維管束垂直,油熱蒸汽和竹材維管束中的水汽不容易排出,容易引發(fā)炸裂。作為進一步的優(yōu)選,所述油浸步驟分為以下階段:(1)膠黏劑固化階段;(2)熱處理階段,將竹材含水率降至0-3%;(3)浸漬處理階段,浸漬藥劑為使用的油介質,浸漬深度為10-20mm,所述浸漬深度是指油介質在重組竹型材導管和其他毛細結構中浸漬和滲透的深度,數值表示為厚度方向上自表面至中心的深度;上述三個階段在油浸步驟中一次完成。在本發(fā)明中,重組竹型材初始含水率高,導管和其他毛細管中存在大量水分,經高溫形成水蒸汽,通過重組竹型材兩端排出;同時在高溫環(huán)境下,對重組竹型材進行了高溫熱處理,處理后重組竹型材內部的糖分、蛋白質等營養(yǎng)物質得到了分解。因而,在重組竹型材內部形成外高內低的內部壓力梯度,在壓力梯度驅動下,油介質進入重組竹型材內部,在完成高溫熱處理之后,自動實現常壓高溫浸漬。在高溫狀態(tài)下,隨著易分解的半纖維素的分解,難分解的纖維素所占比例上升,纖維素發(fā)生了類似于乙酰化的反應,形成酯基,酯基具有增容作用,羥基減少和酯基的充脹作用,進一步提高了竹材的防霉、防水性能,使重組竹型材的尺寸穩(wěn)定性提高,后者作用更顯著。高溫熱處理將熱固型數值膠黏劑重新聚合反應,糖、蛋白質等營養(yǎng)物質和水分汽化,提高了重組竹型材的膠合強度、防霉性能、降低了竹材的吸水性;又經浸漬和乙酰化處理鞏固了上述效果,并強化了重組竹型材的力學性能。上述效果均在油浴浸漬處理一個步驟中完成,同一設備、同一處理介質,無需重復裝卸載、無需重復對介質進行升溫和冷卻;整個油浴浸漬處理步驟一次完成升溫,不分階段升溫、保溫,簡化了重組竹材改性的工藝步驟,提高了生產效率,大幅度降低了設備與勞動力投入,降低了生產成本,提高了產品質量。作為進一步的優(yōu)選,所述自動吸油步驟,是將型材從油介質中直接取出,常溫靜置2~10min,使表面附油自動吸入型材導管或其他毛細管結構的步驟。取出的型材內部,未排出的蒸汽和膨脹的空氣冷卻收縮,型材外部壓力大于內部壓力,形成負壓,將型材表面的附油壓入板坯內部,形成自動吸入的效果。通過自動吸油步驟,實現了對型材的包裹,從而達到了減少、甚至消除甲醛釋放的效果,提高了產品的環(huán)保性。所述冷卻步驟是將處理后的竹材堆置于溫度為0-30℃、相對濕度為50-70%的環(huán)境中,自然冷卻。綜上所述,本發(fā)明具有以下有益效果:1、產品性能優(yōu)于現有產品本發(fā)明的技術方案對竹材進行了三種有效的改性處理,改善了型材的防霉性能、尺寸穩(wěn)定性、型材材色,提高了竹材的密度、力學性能和膠層的膠合強度。相較于經過現有技術處理的重組竹型材的密度和力學性能的損失,本技術方案的產品性能優(yōu)良。2、處理效果均勻熱處理的保護介質和導熱為高溫熱油,油是熱的良導體,受熱均勻,因此熱處理效果均勻;處理竹材的初始含水率較高,在熱處理時形成較大的蒸汽壓力,浸漬處理充分,因此油介質填充效果均勻;產品各個方向剖面上密度、力學性能、含油量等物理化學性能均勻一致。3、材色更豐富、自然型材處理后的材色根據油浸處理的溫度和時間的不同而不同,較現有產品僅碳化色和深碳化色,本發(fā)明的技術方案所提供的產品材色更為豐富;熱處理的保護介質和導熱為高溫熱油,相較于真空熱處理和以水蒸氣為保護的熱處理,受熱更均勻,處理后材色具有自然光澤。4、工作效率高不同于傳統(tǒng)的對竹材進行熱處理、或分工序的浸漬和熱處理,本發(fā)明的技術方案,對竹材進行了熱處理、浸漬處理和類似于乙?;幕瘜W反應,且三個處理效果在一個工序中完成,避免了竹材的重復裝、卸載,避免了設備、藥劑的重復升、降溫,因此工作效率高。5、設備投入少、成本低本發(fā)明的技術方案僅涉及冷壓設備和熱浸設備,且油浸處理工藝步驟簡單,對油浸的設備要求不高;生產成本僅為高溫熱油損耗、竹材物料。6、加工過程及產品環(huán)保生產過程中,油循環(huán)利用,除木材自身營養(yǎng)物質、水分、半纖維素降解物質的揮發(fā)外,無任何其他排放;使用的油介質無毒、害,所以生產過程中環(huán)保性能優(yōu),產品的環(huán)保等級優(yōu)。附圖說明圖1是本發(fā)明實施例1地板結構示意圖;圖2是本發(fā)明實施例2、3結構示意圖;圖中,1-飾面層;2-重組竹型材;3-導管與其他毛細結構。具體實施方式以下結合附圖對本發(fā)明作進一步詳細說明。本具體實施例僅僅是對本發(fā)明的解釋,其并不是對本發(fā)明的限制,本領域技術人員在閱讀完本說明書后可以根據需要對本實施例作出沒有創(chuàng)造性貢獻的修改,但只要在本發(fā)明的權利要求范圍內都受到專利法的保護。實施例1:重組竹型材2制備:先將竹絲與熱固性酚醛樹脂膠粘劑以拌膠的方式混合,膠黏劑固含量為30%,施膠量為竹絲質量的10%;再將混合后的竹絲干燥至含水率2-5%,經冷壓熱固后成22mm厚度的型材;在容器內注入植物油,升溫至300℃、保溫;將型材的維管束與油熱蒸汽方向平行,以此形式進行浸漬,并使油液表面浸沒型材,保持1h;取出型材后,靜置10min,表面附油自動吸入型材內部后,將型材置于溫度為30℃、相對濕度70%的環(huán)境中,自然冷卻。得到的重組竹型材2的導管或其他毛細結構3中填充油介質,含油量為5%、含水率為2.6%、防霉防變色性能(霉菌)被害值為0、吸水厚度膨脹率3.5%、吸水寬度膨脹率3.5%、水平剪切強度13.5MPa。通過四面刨在重組竹型材2兩側制作槽口結構,并用涂布機在表面涂布一層厚度為0.1mm的木蠟油,形成飾面層,制成重組竹地板。實施例2:重組竹型材2制備:先將竹絲與熱固性脲醛樹脂膠粘劑以浸膠的方式混合,膠黏劑固含量為45%,施膠量為竹絲質量的25%;再將混合后的竹絲干燥至含水率25-30%,經冷壓熱固后成40mm厚度的型材;在容器內注入植物油,升溫至100℃、保溫;將型材的維管束與油熱蒸汽方向平行,以此形式進行浸漬,并使油液表面浸沒型材,保持10h;取出型材后,靜置2min,表面附油自動吸入型材內部后,將型材置于溫度為30℃、相對濕度50%的環(huán)境中,自然冷卻。得到的重組竹型材2的導管或其他毛細結構3中填充油介質,含油量為6%、含水率為2.1%、防霉防變色性能(霉菌)被害值為0、吸水厚度膨脹率2.8%、吸水寬度膨脹率3.3%、水平剪切強度12.9MPa。通過四面刨在重組竹型材兩側制作槽口結構,制成重組竹地板。實施例3:一種重組竹地板,先將竹絲與熱固性三聚氰胺膠粘劑以浸膠的方式混合,膠黏劑固含量為35%,施膠量為竹絲質量的20%;再將混合后的竹絲干燥至含水率12-17%,經冷壓熱固后成30mm厚度的型材;在容器內注入植物油,升溫至180℃、保溫;將型材的維管束與油熱蒸汽方向平行,以此形式進行浸漬,并使油液表面浸沒型材,保持5h;取出型材后,靜置6min,表面附油自動吸入型材內部后,將型材置于溫度為20℃、相對濕度60%的環(huán)境中,自然冷卻。得到的重組竹地板的導管或其他毛細結構中填充油介質,含油量為5%、含水率為2.3%、防霉防變色性能(霉菌)被害值為0、吸水厚度膨脹率2.7%、吸水寬度膨脹率3.2%、水平剪切強度14MPa。通過四面刨在重組竹型材兩側制作槽口結構,并涂布木蠟油飾面層1,制成重組竹地板。實施例4:一種重組竹地板,先將竹絲與熱固性三聚氰胺膠粘劑以浸膠的方式混合,膠黏劑固含量為32%,施膠量為竹絲質量的20%;再將混合后的竹絲干燥至含水率10-13%,經冷壓固定后成30mm厚度的型材,再將型材送入連續(xù)壓機的隧道中,控制隧道溫度(即熱固化溫度)為130℃;在容器內注入植物油,升溫至180℃、保溫;將型材的維管束與油熱蒸汽方向平行,以此形式進行浸漬,并使油液表面浸沒型材,保持5h;取出型材后,靜置6min,表面附油自動吸入型材內部后,將型材置于溫度為20℃、相對濕度60%的環(huán)境中,自然冷卻。得到的重組竹地板的導管或其他毛細結構中填充油介質,含油量為6%、含水率為2.3%、防霉防變色性能(霉菌)被害值為0、吸水厚度膨脹率2.5%、吸水寬度膨脹率3.1%、水平剪切強度13.6MPa。通過四面刨在重組竹型材兩側制作槽口結構,并涂布木蠟油飾面層。對比實施例1:先將竹絲與熱固性酚醛膠粘劑以浸膠的方式混合,膠黏劑固含量為35%,施膠量為竹絲質量的20%;再將混合后的竹絲干燥至含水率12-17%,經冷壓熱固后成30mm厚度的型材;在容器內注入植物油,升溫至70℃、保溫;將型材的維管束與油熱蒸汽方向平行,以此形式進行浸漬,并使油液表面浸沒型材,保持10h;取出型材后,靜置10min,表面附油沒有自動吸入型材內部,人工擦去表面附油后,將型材置于溫度為20℃、相對濕度60%的環(huán)境中,自然冷卻。得到的重組竹地板的導管或其他毛細結構中填充油介質,含油量為0、含水率為15.6%、防霉防變色性能(霉菌)被害值為2、吸水厚度膨脹率11.2%、吸水寬度膨脹率5.4%、水平剪切強度10.2MPa。對比實施例2:先將竹絲與熱固性酚醛膠粘劑以浸膠的方式混合,膠黏劑固含量為35%,施膠量為竹絲質量的20%;再將混合后的竹絲干燥至含水率12-17%,經冷壓熱固后成30mm厚度的型材;在容器內注入植物油,升溫至200℃、保溫;將型材的維管束與油熱蒸汽方向垂直,以此形式進行浸漬,并使油液表面浸沒型材,保持5h;處理后的型材出現了明顯的開裂、炸裂等質量問題,無法使用。對比實施例3:根據現有竹材熱處理技術,對竹絲進行220℃、處理時間為6h的熱處理,通過浸膠方式施以熱固型酚醛樹脂膠黏劑,干燥至含水率13-15%;再進行熱壓固化處理,熱壓溫度為140℃,保壓時間45min;最后經過冷卻和養(yǎng)生制成重組竹木材。附表1是對各實施例產品性能的對比表。表-1一種竹材油熱浸漬型材產品檢測物理化學性能對比表由表1可知,4個實施例中產品性能均遠優(yōu)于對比實施例1、3以及國家標準;與對比實施例1相比,可知本發(fā)明的技術方案是最優(yōu)技術方案,只有依照此技術方案內的工藝參數,才能獲得性能優(yōu)良的產品;與對比實施例2相比,重組竹型材的裝載方向在其維管束與油熱蒸汽平行的效果最佳,此裝載方法,可使處理效果均勻、處理過程安全;與對比實施例3、即現有工藝相比,產品的各項物理化學性能均優(yōu)于現有工藝,更增加了產品的膠合強度。