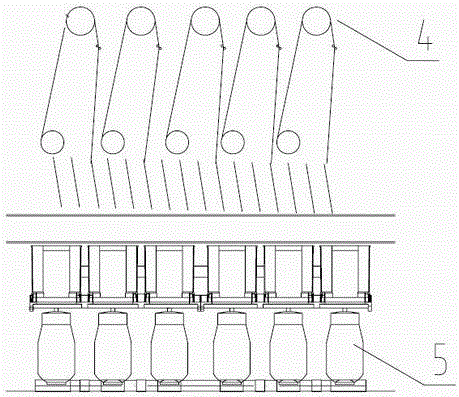
本發(fā)明涉及粘膠長(zhǎng)絲紡絲生產(chǎn)技術(shù)領(lǐng)域,具體涉及一種適用于卷繞裝置外置的紡絲機(jī)的紡絲工藝。
背景技術(shù):由纖維素原料提取出純凈的甲纖維素,稱為漿粕。用燒堿、二硫化碳處理,得到橙黃色的纖維素黃原酸鈉,再溶解在稀氫氧化鈉溶液中,成為粘稠的紡絲原液,稱為粘膠。粘膠經(jīng)過(guò)濾、熟成、脫泡后,進(jìn)行濕法紡絲,凝固浴由硫酸、硫酸鈉和硫酸鋅組成。粘膠中的纖維素黃原酸鈉與凝固浴中的硫酸作用而分解,纖維素再生而析出,所得纖維素纖維經(jīng)水洗、脫硫、漂白、干燥后成為粘膠纖維。粘膠長(zhǎng)絲即粘膠纖維的一種,也是由上述工藝制得。在紡絲及紡絲后處理過(guò)程中,紡絲機(jī)的選擇有半連續(xù)紡織機(jī)和連續(xù)紡織機(jī),從工藝和設(shè)備兩方面來(lái)說(shuō),這兩種紡絲機(jī)存在以下區(qū)別:1、從生產(chǎn)工藝的角度來(lái)說(shuō),半連續(xù)紡絲機(jī)是將紡絲和后處理(后處理包括洗滌、烘干、成筒等步驟)分開(kāi),單獨(dú)完成,半連續(xù)紡絲機(jī)主要負(fù)責(zé)紡絲部分;而連續(xù)紡絲機(jī)是將紡絲和后處理(后處理包括洗滌、烘干、成筒等步驟)工序集中在一起連續(xù)完成,連續(xù)紡絲負(fù)責(zé)從紡絲到后處理的所有步驟。2、從設(shè)備結(jié)構(gòu)的角度來(lái)說(shuō),半連續(xù)紡絲機(jī)包括供膠機(jī)構(gòu)、噴絲機(jī)構(gòu)、絲條成型機(jī)構(gòu)、紡絲輥機(jī)構(gòu)、清洗機(jī)構(gòu)以及卷繞機(jī)構(gòu),得到的產(chǎn)品為落入離心缸中的絲餅;而連續(xù)紡絲機(jī)具有供膠機(jī)構(gòu)、噴絲機(jī)構(gòu)、絲條成型機(jī)構(gòu)、紡絲輥機(jī)構(gòu)、清洗機(jī)構(gòu),沒(méi)有卷繞機(jī)構(gòu),絲條直接進(jìn)入淋洗、烘干等機(jī)構(gòu),最后得到卷繞成型的絲筒?;谝陨蟽煞N紡絲機(jī)的區(qū)別,其各自的優(yōu)缺點(diǎn)如下:1、半連續(xù)紡絲機(jī)(如圖1-圖3所示):優(yōu)點(diǎn):由于有單獨(dú)進(jìn)行的后處理步驟,且后處理步驟中還有低溫脫硫、低溫長(zhǎng)時(shí)間烘干的過(guò)程,產(chǎn)品具有強(qiáng)度高、白度高,絲條柔軟亮麗的特點(diǎn);缺點(diǎn):紡速低,后處理費(fèi)用高,增加生產(chǎn)成本。2、連續(xù)紡絲機(jī):優(yōu)點(diǎn):紡速高,產(chǎn)量提高;紡絲與后處理集中在一起進(jìn)行,生產(chǎn)成本降低;缺點(diǎn):由于絲條是即洗即烘,絲條強(qiáng)度低,白度低,絲條粗糙,質(zhì)量不如半連續(xù)紡絲機(jī)的產(chǎn)品;為增加絲條抱合上漿,繡花線染色時(shí)漿料需去除,增加下游產(chǎn)品生產(chǎn)成本;對(duì)原料(粘膠)質(zhì)量要求高?,F(xiàn)有技術(shù)中最常見(jiàn)的半連續(xù)紡絲機(jī)為R535半連續(xù)紡絲機(jī)(如圖1-圖3所示,包括機(jī)架1、供膠裝置2、絲條成型裝置3、紡絲裝置4和卷繞裝置5,紡絲裝置4中紡絲輥相對(duì)于紡面101的操作面為縱向設(shè)置),其紡絲的主要流程為:粘膠通過(guò)濾器過(guò)濾后用噴絲頭噴入酸浴槽內(nèi)經(jīng)過(guò)反應(yīng)成型為絲條,絲條通過(guò)牽伸盤(pán)牽伸至凝固輥,絲條在凝固輥上卷繞一定圈數(shù)的距離進(jìn)行一段時(shí)間的反應(yīng)后再升頭至捻面去酸輥,去酸輥上方采用滴水淋洗的方式對(duì)絲條進(jìn)行去酸洗滌,絲條在去酸輥上卷繞一定圈數(shù)的距離再導(dǎo)入離心缸,最后得到絲餅。其中,紡絲輥體主要分為去酸輥和凝固輥,紡絲機(jī)的每個(gè)錠位分別使用一對(duì)凝固輥和一對(duì)去酸輥,凝固輥安裝在紡面,去酸輥安裝在捻面,相互背離,輥體的固定方式均為一端固定,安裝方向相對(duì)紡絲機(jī)紡面的操作面位置成縱向安裝。另現(xiàn)R535三缸絲紡絲機(jī)的三圓筒排風(fēng)采用三缸同風(fēng)道排風(fēng)方式?,F(xiàn)有R535A半連續(xù)紡絲機(jī)其絲條成型部分及紡絲輥結(jié)構(gòu)和安裝方式無(wú)法進(jìn)行高速紡絲,其紡絲紡速在70-90m/min左右。同時(shí)其設(shè)備結(jié)構(gòu)及安裝方式等造成紡絲機(jī)設(shè)備占地面積大、能耗高、工藝流程復(fù)雜、維護(hù)點(diǎn)多,配件消耗大、產(chǎn)品成本高等缺點(diǎn)。另R535三缸絲的三圓筒三缸同風(fēng)道排風(fēng)方式在排風(fēng)過(guò)程中相互形成干擾,造成排風(fēng)效果差?,F(xiàn)有技術(shù)中最常見(jiàn)的連續(xù)紡絲機(jī)結(jié)構(gòu)如圖4-圖6所示,其前半部分包括機(jī)架1、供膠裝置2、絲條成型裝置3和紡絲裝置4,紡絲裝置4中紡絲輥相對(duì)于紡面101的操作面也為縱向設(shè)置。蘇聯(lián)制的連續(xù)紡絲機(jī)對(duì)于紡絲輥部分進(jìn)行了改進(jìn),但是由于其生產(chǎn)得到的是絲束,不能得到絲餅,所以不能直接應(yīng)用在半連續(xù)紡絲機(jī)中。國(guó)家知識(shí)產(chǎn)權(quán)局于2000.12.6公開(kāi)了一件公開(kāi)號(hào)為CN1356409,名稱為“單路多絲離心紡和半連續(xù)紡絲機(jī)及其粘膠紡絲工藝”的發(fā)明專利,該發(fā)明公開(kāi)了一種離心式半連續(xù)紡絲機(jī),其包括粘膠輸送系統(tǒng)、搖擺管組件、刮酸、牽伸盤(pán)、凝固輥、去酸輥、升降架及漏斗、離心缸及電錠系統(tǒng),粘膠輸送系統(tǒng)由機(jī)頭和機(jī)尾兩端同時(shí)進(jìn)膠的多路粘膠管及其支撐機(jī)構(gòu)組成;搖擺管組件由與多路膠管串接的多路并聯(lián)的計(jì)量泵、慮套、曲管及噴頭組成;在雙凝固輥的上方絲條行走路徑上設(shè)有上下安裝的由兩個(gè)去酸輥組成的去酸輥組件;在機(jī)器升降架上,裝置與絲條數(shù)目相同的同步動(dòng)作的漏斗;其離心缸、電錠系統(tǒng)設(shè)置成為每錠多離心缸及與其配套的電錠和控制機(jī)構(gòu)。上述發(fā)明可同時(shí)生產(chǎn)多根絲,大幅度提高了粘膠長(zhǎng)絲的產(chǎn)量,但是該發(fā)明由于其紡絲機(jī)的每個(gè)錠位分別使用一對(duì)凝固輥和一對(duì)去酸輥,凝固輥安裝在紡面,去酸輥安裝在捻面,相互背離,輥體的固定方式均為一端固定,安裝方向相對(duì)紡絲機(jī)操作面位置成縱向安裝。上述結(jié)構(gòu)帶來(lái)的問(wèn)題如下:1、上述結(jié)構(gòu)限制了輥的長(zhǎng)度,粘膠長(zhǎng)絲在輥上行走的時(shí)間短,粘膠長(zhǎng)絲成形時(shí)間短,如果要提高紡速,必然會(huì)導(dǎo)致粘膠長(zhǎng)絲反應(yīng)時(shí)間不夠而降低產(chǎn)品質(zhì)量,所以采用傳統(tǒng)的半連續(xù)紡絲機(jī)效率降低;2、為了提高效率,通常會(huì)同時(shí)加工多根絲條,但是多根粘膠長(zhǎng)絲纏繞在現(xiàn)有的紡絲輥上時(shí)又容易絞絲,造成粘膠長(zhǎng)絲斷裂,影響粘膠長(zhǎng)絲的產(chǎn)品質(zhì)量;3、另外,所述的紡絲輥的固定方式為一端固定,這樣的固定形式為懸臂式,在紡絲輥轉(zhuǎn)動(dòng)時(shí),處于一種不穩(wěn)定的狀態(tài),容易發(fā)生故障;4、所有紡絲輥都為一端固定,勢(shì)必需要結(jié)構(gòu)極其復(fù)雜的傳動(dòng)機(jī)構(gòu)來(lái)帶動(dòng)紡絲輥的轉(zhuǎn)動(dòng),這樣也會(huì)導(dǎo)致故障率的上升,而且在更換絲線品種,改變轉(zhuǎn)動(dòng)速度時(shí),需要停車,再進(jìn)行傳動(dòng)系統(tǒng)中齒輪的更換,這樣使得生產(chǎn)效率降低,生產(chǎn)成本增加。國(guó)家知識(shí)產(chǎn)權(quán)局于1998.9.23公開(kāi)了一件公開(kāi)號(hào)為CN2292097,名稱為“粘膠長(zhǎng)絲連續(xù)紡絲機(jī)”的實(shí)用新型專利,該專利涉及一種粘膠長(zhǎng)絲連續(xù)紡絲機(jī),能連續(xù)完成紡絲、水洗、烘干、上油、卷繞等,其紡速可達(dá)120m/min,本實(shí)用新型在紡絲機(jī)機(jī)臺(tái)前設(shè)置粘膠過(guò)濾裝置,利用紡絲機(jī)泵軸帶動(dòng)計(jì)量泵運(yùn)轉(zhuǎn),其結(jié)構(gòu)簡(jiǎn)單,清洗維修方便,有效地過(guò)濾了粘膠中的雜質(zhì);紡絲浴盒中將噴絲頭置于擺管端部,保證了噴絲頭與玻璃管的同心度,能夠避免產(chǎn)生毛絲,操作靈活,工效高;玻璃管出口處采用絲條雙轉(zhuǎn)向裝置,減小了絲條與導(dǎo)絲輪之間的摩擦力,牽伸比分配合理,成絲質(zhì)量高。上述由于絲條是即洗即烘,絲條強(qiáng)度低,白度低,絲條粗糙,質(zhì)量不如半連續(xù)紡絲機(jī)的產(chǎn)品;為增加絲條抱合上漿,繡花線染色時(shí)漿料需去除,增加下游產(chǎn)品生產(chǎn)成本;對(duì)原料(粘膠)質(zhì)量要求高。另外,上述連續(xù)紡絲機(jī)的紡絲輥依然是相對(duì)于工人操作區(qū)域縱向設(shè)置,所以其安裝方式也是一端固定,還是存在第一篇現(xiàn)有技術(shù)專利中的問(wèn)題。國(guó)家知識(shí)產(chǎn)權(quán)局于2008.7.23公開(kāi)了一件公開(kāi)號(hào)為CN201089811,名稱為“粘膠人造絲深浴紡連續(xù)紡絲機(jī)”,該專利公開(kāi)了一種粘膠人造絲深浴紡連續(xù)紡絲機(jī),解決現(xiàn)有連續(xù)紡絲機(jī)絲條剩余脂化度高所帶來(lái)的問(wèn)題。本實(shí)用新型采用的方案是成型管與紡絲小輥之間設(shè)置有酸浴槽,從成型管伸出的絲條落入裝有酸液的酸浴槽內(nèi)浸浴后再行至紡絲小輥。本實(shí)用新型增加深浴紡,加強(qiáng)絲條的反應(yīng)程度,降低剩余脂化度,保證人絲品質(zhì),并適用于繡花線的生產(chǎn)。該工藝屬“二次浴”工藝,二次浴酸濃、酸溫比一次浴低,故需要增加一套獨(dú)立酸浴系統(tǒng),增加酸站投入成本。另外,上述連續(xù)紡絲機(jī)的紡絲輥依然是相對(duì)于工人操作區(qū)域縱向設(shè)置,所以其安裝方式也是一端固定,還是存在第一篇現(xiàn)有技術(shù)專利中的問(wèn)題。國(guó)家知識(shí)產(chǎn)權(quán)局于2005.8.31公開(kāi)了一件公開(kāi)號(hào)為CN2721660,名稱為“適用于粘膠長(zhǎng)絲一錠位同時(shí)紡三絲的半連續(xù)離心紡絲機(jī)”的實(shí)用新型專利,本實(shí)用新型公開(kāi)了一種適用于在半連續(xù)離心紡絲機(jī)的一個(gè)錠位上同時(shí)紡出三根絲條的連續(xù)離心紡絲機(jī),這種半連續(xù)離心紡絲機(jī)的每節(jié)內(nèi)能夠同時(shí)生產(chǎn)出18個(gè)絲餅的紡絲機(jī)。通過(guò)在半連續(xù)離心紡絲機(jī)的每節(jié)安裝18個(gè)電錠、18個(gè)離心缸的部件,能夠在不增加設(shè)備臺(tái)數(shù)、公用運(yùn)行成本、占地面積及投資的情況下,節(jié)約紡絲機(jī)的維修時(shí)間,降低單個(gè)絲餅的生產(chǎn)成本,提高紡絲機(jī)的利用率,且設(shè)備維護(hù)和操作方便,在系統(tǒng)設(shè)備改進(jìn)后使其生產(chǎn)能力達(dá)到原設(shè)計(jì)能力從原來(lái)的每節(jié)6個(gè)絲餅或12個(gè)絲餅達(dá)到18個(gè)絲餅;同時(shí)滿足生產(chǎn)質(zhì)量要求。雖然單機(jī)每節(jié)的產(chǎn)量由于增加電錠、離心缸裝置能夠提高產(chǎn)量,但是該紡絲機(jī)的紡速任然沒(méi)有提高,如果提高了紡速,又會(huì)因?yàn)榻z條反應(yīng)不充分影響最終產(chǎn)品的質(zhì)量。另外,上述半連續(xù)紡絲機(jī)的紡絲輥依然是相對(duì)于工人操作區(qū)域縱向設(shè)置,所以其安裝方式也是一端固定,還是存在第一篇現(xiàn)有技術(shù)專利中的問(wèn)題。又如申請(qǐng)?zhí)枮?00920297370.0,申請(qǐng)日為2009-12-18,名稱為“用于粘膠粗旦扁平絲的連續(xù)紡絲機(jī)”,其技術(shù)方案為:本實(shí)用新型公開(kāi)了一種用于粘膠粗旦絲扁平絲的連續(xù)紡絲機(jī),包括粘膠計(jì)量成型設(shè)備、洗滌設(shè)備、烘干設(shè)備和成筒設(shè)備,粘膠計(jì)量成型設(shè)備的成型裝置為玻璃成型管,洗滌設(shè)備由多級(jí)洗滌槽組成,玻璃成型管管中成型的絲條由多級(jí)洗滌槽的壓緊輥牽引至洗滌槽內(nèi);多級(jí)洗滌槽的下行設(shè)備為烘干設(shè)備,烘干設(shè)備為輸送帶和蒸汽烘干機(jī),多級(jí)洗滌槽末端的絲條由壓緊輥牽引至蒸汽烘干機(jī),蒸汽烘干機(jī)下行與成筒設(shè)備聯(lián)接。上述實(shí)用新型為連續(xù)紡絲機(jī),設(shè)置了烘干設(shè)備,并且烘干后的絲條直接成筒,其成筒設(shè)備位于烘干設(shè)備的外側(cè),但是由于紡絲輥上集成了去牽伸、水洗去酸、烘干和上油等結(jié)構(gòu),使得整機(jī)結(jié)構(gòu)復(fù)雜,并且增加了能耗。綜上所述,現(xiàn)有的半連續(xù)紡絲機(jī)存在卷繞裝置位于紡絲輥下方,由于紡絲輥上有水以及酸性溶液,因而會(huì)導(dǎo)致卷繞裝置易被紡絲輥上的水和酸性溶液污染的問(wèn)題;而現(xiàn)有的連續(xù)紡絲機(jī)為了最終得到成型的干絲條,紡絲輥上集成了去牽伸、水洗去酸、烘干和上油等結(jié)構(gòu),使得整機(jī)結(jié)構(gòu)復(fù)雜,增加了能耗,并且不能得到帶弱酸性的濕絲條。因此,針對(duì)上述問(wèn)題而進(jìn)行改進(jìn)的適用于卷繞裝置外置的紡絲機(jī),現(xiàn)有的工藝控制將無(wú)法滿足其提高紡速的要求,也無(wú)法滿足對(duì)直接卷繞成濕態(tài)的餅裝絲、和/或濕態(tài)的筒裝絲、和/或濕態(tài)的絞裝絲單一控制所帶來(lái)的品種或規(guī)格變化的技術(shù)要求。
技術(shù)實(shí)現(xiàn)要素:本發(fā)明旨在提供一種針對(duì)卷繞裝置外置的紡絲機(jī)的紡絲工藝,以達(dá)到紡絲機(jī)能夠在提高紡速的同時(shí),保證絲條在卷繞時(shí)不受紡絲輥上殘留溶液污染,可根據(jù)需要得到弱酸性濕絲條,整機(jī)能耗降低,進(jìn)而保證質(zhì)量,提高生產(chǎn)效率、降低成本的目的。為實(shí)現(xiàn)上述發(fā)明目的,本發(fā)明采用的技術(shù)方案如下:一種適用于卷繞裝置外置的紡絲機(jī)的紡絲工藝,其工序包括粘膠計(jì)量與供膠、紡前過(guò)濾、絲條成型、紡絲及卷繞,其特征在于:所述卷繞工序中,絲條經(jīng)卷繞裝置成型為可直接用于捻線的濕態(tài)的餅裝絲、和/或濕態(tài)的筒裝絲、和/或濕態(tài)的絞裝絲;所述濕態(tài)的餅裝絲、濕態(tài)的筒裝絲或者濕態(tài)的絞裝絲的含水率為30~80%;所述成型為濕態(tài)的餅裝絲的離心缸的轉(zhuǎn)速為7200~8400r/min;所述成型為濕態(tài)的絞裝絲的絞裝電機(jī)的轉(zhuǎn)速為500~1000r/min;所述成型為濕態(tài)的筒裝絲采取主動(dòng)卷繞和/或被動(dòng)卷繞方式,其中:所述主動(dòng)卷繞中,橫向電機(jī)的轉(zhuǎn)速為800~1200r/min,旋轉(zhuǎn)電機(jī)的轉(zhuǎn)速為1000~1500r/min;所述被動(dòng)卷繞中,橫向電機(jī)的轉(zhuǎn)速為800~1200r/min,旋轉(zhuǎn)電機(jī)的轉(zhuǎn)速為1000~1500r/min,油劑的pH值為7~12。所述被動(dòng)卷繞包括單錠被動(dòng)卷繞、三錠被動(dòng)卷繞或通軸被動(dòng)卷繞。所述粘膠計(jì)量與供膠工序中,粘膠管的表壓為0.1~0.5MPa。所述紡前過(guò)濾工序中,粘膠熟成度NH4Cl值控制在7.0~13ml,落球粘度28~38mPa?s,粘膠甲纖含量8.0~8.2%,粘膠含堿5.8~6.1%,500ml粘膠氣泡≤25個(gè),粘膠表面張力50~55dyne/cm,10μm以下粘膠粒子≤100個(gè)/ml。所述絲條成型工序中,酸浴的組成為:硫酸濃度135~145g/L,硫酸鈉濃度230~245g/L,硫酸鋅濃度11.0~12.5g/L,酸浴溫度55~57℃,酸浴表面張力小于粘膠表面張力;成型管內(nèi)徑Φ5±0.1mm,成型管長(zhǎng)800~1200mm;噴絲頭的孔徑為0.06~0.09mm,且形狀呈“一”字形、扇形或圓形。所述紡絲工序包括對(duì)絲條的凝固、牽伸、去酸及上油,紡絲輥長(zhǎng)度1000~1500mm,直徑Φ120~180mm,紡絲輥轉(zhuǎn)速為100~160米/分,凝固反應(yīng)時(shí)間33~68秒/根,絲條的牽伸率為10~25%,淋洗水量為240~480ml/min,淋洗1~3次,水洗去酸中的水溫為35~60℃,pH值為7~8,油劑用量為5~50ml/min;所述經(jīng)凝固、牽伸、去酸、上油后的絲條,其含酸量在5~30%,生絲條剩余酯化度小于3%,含油率為0.25~1.5%,pH值為6.5~8.5。本發(fā)明所述的濕態(tài)的餅裝絲、濕態(tài)的筒裝絲或者濕態(tài)的絞裝絲可實(shí)現(xiàn)的主要技術(shù)指標(biāo)如下:1)濕斷裂強(qiáng)度(CN/dtex):≥0.852)濕斷裂伸長(zhǎng):≥15~30%3)線密度(纖度)偏差:±3.0%4)線密度變異系數(shù)(CV值):≤5.00%5)捻度變異系數(shù)(CV值):≤5%6)單絲根數(shù)偏差:≤5.0%7)殘硫量(Mg/100g纖維):≤20.0本發(fā)明的優(yōu)點(diǎn)在于:1、由于本發(fā)明卷繞裝置的外置,因此在酸性環(huán)境下,對(duì)絲條、卷繞設(shè)備及其控制系統(tǒng)的腐蝕性小,便于維修和工人操作,由于現(xiàn)有的離心缸需高速旋轉(zhuǎn),所以能耗高,而本發(fā)明卷繞裝置只需要滿足紡絲輥的速度,無(wú)其他能耗,所以整機(jī)功率小。2、現(xiàn)有的半連續(xù)紡絲機(jī)和連續(xù)紡絲機(jī)不能過(guò)度提高紡速,是因?yàn)楫?dāng)紡絲輥的轉(zhuǎn)速提高后,還需要提高升降機(jī)構(gòu)的速度與之匹配,而升降機(jī)構(gòu)速度提高有限,同時(shí)離心缸的轉(zhuǎn)速也需與之匹配,但其轉(zhuǎn)速過(guò)高,穩(wěn)定性降低,導(dǎo)致絲餅成型不好。而本發(fā)明由于采用筒裝卷繞方式,轉(zhuǎn)速可大幅提高,并且本發(fā)明取消了升降機(jī)構(gòu),因此改變了絲條成型的方式,當(dāng)紡絲輥的速度提高后,只需要相應(yīng)提高卷繞裝置的速度即可。3、本發(fā)明能夠根據(jù)需要得到弱酸性的濕絲條,得到弱酸性的濕絲條不在紡絲機(jī)上進(jìn)行烘干,如果后續(xù)步驟需要烘干濕絲條,則可以將弱酸性的濕絲條取出放入至烘干設(shè)備進(jìn)行烘干,避免了直接在紡絲輥上進(jìn)行烘干而產(chǎn)生的能耗增加、烘干程度不易控制等問(wèn)題。明由于紡絲輥的兩端均固定,所以紡絲輥的轉(zhuǎn)速能夠比現(xiàn)有的紡絲機(jī)懸空的紡絲輥轉(zhuǎn)速提升更多,并且更穩(wěn)定,不會(huì)造成紡絲輥在高速下發(fā)生搖擺,降低了紡絲機(jī)高速下的故障率。5、本發(fā)明紡絲機(jī)結(jié)構(gòu)緊湊,占地面積小。6、本發(fā)明紡絲機(jī)操作方便,且便于在高速紡絲下的質(zhì)量控制。7、本發(fā)明通過(guò)對(duì)粘膠計(jì)量與供膠、紡前過(guò)濾、絲條成型、紡絲及卷繞各工序的順序控制和參數(shù)控制,尤其是卷繞工序中,濕態(tài)的餅裝絲或者筒裝絲或者絞絲的含水率控制在30~80%,離心缸的轉(zhuǎn)速為7200~8400r/min,絞裝電機(jī)的轉(zhuǎn)速為500~1000r/min,主動(dòng)卷繞中,橫向電機(jī)的轉(zhuǎn)速為800~1200r/min,旋轉(zhuǎn)電機(jī)的轉(zhuǎn)速為1000~1500r/min,被動(dòng)卷繞中,橫向電機(jī)的轉(zhuǎn)速為800~1200r/min,旋轉(zhuǎn)電機(jī)的轉(zhuǎn)速為1000~1500r/min,油劑的pH值為7~12,可實(shí)現(xiàn)絲條在外置卷繞裝置中卷繞成可直接用于捻線的濕態(tài)的餅裝絲、和/或濕態(tài)的筒裝絲、和/或濕態(tài)的絞裝絲,并可滿足紡速穩(wěn)定提高到140m/min以上。本發(fā)明提供的卷繞工藝除可確保紡絲機(jī)能達(dá)到高紡速外,更突出的是還保證了產(chǎn)品品質(zhì),絲條在最后的卷繞成型工序中不會(huì)因水洗去酸液及油劑的滴落而受到污染,確保了后續(xù)的染色工藝,且工人操作更為簡(jiǎn)便,設(shè)備維護(hù)更容易,能耗降低,這使得在有效提高生產(chǎn)效率的同時(shí),產(chǎn)品成本大大降低。具體體現(xiàn)在以下各工序步驟中:1)在粘膠計(jì)量與供膠工序中,粘膠管的表壓控制在0.1~0.5MPa,充分保證了供膠的均勻性及紡絲速度。2)在紡前過(guò)濾工序中,將粘膠熟成度NH4Cl值控制在7.0~13ml,落球粘度28~38mPa?s,粘膠甲纖含量8.0~8.2%,粘膠含堿5.8~6.1%,500ml粘膠氣泡≤25個(gè),粘膠表面張力50~55dyne/cm,10μm以下粘膠粒子≤100個(gè)/ml,在粘膠熟成度低、膠老的條件下,確保了絲條強(qiáng)度的提高。3)在絲條成型工序中,采用與粘膠熟成度相匹配的酸浴工藝,即酸浴采用高酸低鹽、高酸溫,具體指標(biāo):酸浴的組成為:硫酸濃度135~145g/L,硫酸鈉濃度230~245g/L,硫酸鋅濃度11.0~12.5g/L,酸浴溫度55~57℃,酸浴表面張力小于粘膠表面張力,成型管內(nèi)徑Φ5±0.1mm,成型管長(zhǎng)800~1200mm,噴絲頭的孔徑為0.06~0.09mm,可確保在實(shí)現(xiàn)劇烈酸浴反應(yīng)的同時(shí),加快絲條反應(yīng)速度。4)在紡絲工序的凝固、牽伸、去酸及上油過(guò)程中,在紡絲輥長(zhǎng)度1000~1500mm,直徑Φ120~180mm,紡絲輥轉(zhuǎn)速為100~160m/分,凝固反應(yīng)時(shí)間33~68秒/根,絲條的牽伸率為10~25%,淋洗水量為240~480ml/min,淋洗1~3次,水洗去酸中的水溫為35~60℃,pH值為7~8,油劑用量為5~50ml/min的工藝條件下,可實(shí)現(xiàn)絲條的含酸量在5~30%,生絲條剩余酯化度小于3%,含油率為0.25~1.5%,pH值為6.5~8.5,水洗效果更好,去酸更徹底,絲條的均勻性好,同時(shí),絲條上油飽滿、均勻,上油率高,上油后的絲條滑爽好,卷繞時(shí)摩擦力少,不需要如連續(xù)紡上漿,因而絲條毛絲少,不易斷絲,充分保證了后續(xù)的染色工藝及染色的均勻性。5)在管中成型中,采用內(nèi)徑Φ5±0.1mm,長(zhǎng)800~1200mm的成型管,可有效避免單絲漂移現(xiàn)象,確保每束絲條單絲根數(shù)的均勻性,利于紡速的提高。6)在本發(fā)明的整個(gè)工藝中,由于各工序步驟的相互作用,以及卷繞速度、濕態(tài)的餅裝絲、筒裝絲或者絞裝絲的含水率、油劑的pH值、粘膠的參數(shù)性能、酸浴的溫度、水洗的用量及溫度、紡絲輥的長(zhǎng)度、油劑用量、成型管內(nèi)徑及長(zhǎng)度等的確定,使得在高紡速下的外置卷繞方式不但具有更加好的操作性、穩(wěn)定性及控制性,且濕絲條質(zhì)量好,后續(xù)染色效果佳。顯然,根據(jù)本發(fā)明的上述內(nèi)容,按照本領(lǐng)域的普通技術(shù)和慣用手段,在不脫離本發(fā)明上述基本技術(shù)思想前提下,還可以作出其它多種形式的修改、替換或變更。附圖說(shuō)明圖1現(xiàn)有半連續(xù)離心紡絲機(jī)的側(cè)視圖。圖2現(xiàn)有半連續(xù)離心紡絲機(jī)的主視圖。圖3現(xiàn)有半連續(xù)離心紡絲機(jī)紡面的俯視圖。圖4現(xiàn)有連續(xù)離心紡絲機(jī)的側(cè)視圖。圖5現(xiàn)有連續(xù)離心紡絲機(jī)的主視圖。圖6現(xiàn)有連續(xù)離心紡絲機(jī)紡面的俯視圖。圖7為本發(fā)明紡絲機(jī)的側(cè)視的結(jié)構(gòu)示意圖。圖8為本發(fā)明紡絲機(jī)的主視的結(jié)構(gòu)示意圖。圖9為本發(fā)明紡絲機(jī)紡面的俯視圖。圖10為本發(fā)明的水洗裝置的結(jié)構(gòu)示意圖之一。圖11為本發(fā)明的水洗裝置的結(jié)構(gòu)的示意圖之二。圖12為本發(fā)明的上油裝置的結(jié)構(gòu)示意圖之一。圖13為本發(fā)明的上油裝置的結(jié)構(gòu)示意圖之二。圖14為本發(fā)明的主動(dòng)濕態(tài)卷繞裝置的結(jié)構(gòu)示意圖。圖15為本發(fā)明的單錠被動(dòng)卷繞裝置的結(jié)構(gòu)示意圖之一。圖16為本發(fā)明的單錠被動(dòng)卷繞裝置的結(jié)構(gòu)示意圖之二。圖17為本發(fā)明的三錠被動(dòng)卷繞裝置的側(cè)視圖。圖18為本發(fā)明的三錠被動(dòng)卷繞裝置的俯視圖。圖19為本發(fā)明的通軸被動(dòng)卷繞裝置的結(jié)構(gòu)示意圖之一。圖20為本發(fā)明的通軸被動(dòng)卷繞裝置的結(jié)構(gòu)示意圖之二。圖21為發(fā)明的濕態(tài)餅裝卷繞裝置的結(jié)構(gòu)示意圖。圖22為本發(fā)明的濕態(tài)絞裝卷繞裝置的結(jié)構(gòu)示意圖。圖23為本發(fā)明卷繞裝置為濕態(tài)餅裝卷繞裝置時(shí)的分布示意圖。圖24為本發(fā)明卷繞裝置為濕態(tài)筒裝卷繞裝置時(shí)的分布示意圖。圖25為本發(fā)明卷繞裝置為濕態(tài)絞裝卷繞裝置時(shí)的分布示意圖。圖26為本發(fā)明卷繞裝置為濕態(tài)餅裝卷繞裝置和濕態(tài)筒裝卷繞裝置組合時(shí)的分布示意圖。圖27為本發(fā)明卷繞裝置為濕態(tài)餅裝卷繞裝置和濕態(tài)絞裝卷繞裝置組合時(shí)的分布示意圖。圖28為本發(fā)明卷繞裝置為濕態(tài)筒裝卷繞裝置和濕態(tài)絞裝卷繞裝置組合時(shí)的分布示意圖。圖29為本發(fā)明卷繞裝置為濕態(tài)餅裝卷繞裝置、濕態(tài)筒裝卷繞裝置和濕態(tài)絞裝卷繞裝置組合時(shí)的分布示意圖。圖30為本發(fā)明的工藝流程示意圖。附圖中:機(jī)架1、供膠裝置2、絲條成型裝置3、紡絲裝置4、卷繞裝置5、墻板6、卷繞面7。水洗裝置41、上油裝置42、濕態(tài)餅裝卷繞裝置51,濕態(tài)筒裝卷繞裝置52,濕態(tài)絞裝卷繞裝置53。紡面101、立柱1101。噴淋管4101、噴淋孔或噴嘴4102、導(dǎo)流管4103、導(dǎo)流篩4104、導(dǎo)流板4106,擋流板4107,導(dǎo)流槽4109。油槽4201、導(dǎo)絲輥4202、牽伸輥4203、油輪4204、油4205、海綿吸附裝置4206、通孔4207、刮油輪4208、絲條4209、噴油管4211、噴油孔4212、儲(chǔ)油槽4213。卷繞架5201、支架5202、松筒管5203、橫向連桿5204、橫向電機(jī)5205、旋轉(zhuǎn)電機(jī)5206、橫向架5207、導(dǎo)絲鉤5208、主軸5209、軸承5210、中和槽5211、頂盤(pán)5212、槽筒5213、軸承座5214、連接件5215、轉(zhuǎn)動(dòng)軸5216、被動(dòng)齒5217、從動(dòng)軸5218、主動(dòng)齒5219、主動(dòng)軸5220。離心缸5100,支承座5101,軸承體5102,迷宮外殼5103,離心軸5104,迷宮錠盤(pán)5105,上軸承5106,下軸承5107,阻尼5108,減震圈和減震墊5109,O型密封膠圈5110,轉(zhuǎn)子5111,定子5112,鐵心5113,繞組5114。絞裝電機(jī)5301、摩擦輪5302、絞框5303、絞軸5304、橫動(dòng)支架5305、橫動(dòng)連桿5306、轉(zhuǎn)動(dòng)軸5307、橫動(dòng)電機(jī)5308、軸承5309、導(dǎo)絲掛鉤5310。以下通過(guò)實(shí)施例的形式對(duì)本發(fā)明的上述內(nèi)容再作進(jìn)一步的詳細(xì)說(shuō)明。但不應(yīng)將此理解為本發(fā)明上述主題的范圍僅限于以下的實(shí)例,凡基于本發(fā)明上述內(nèi)容所實(shí)現(xiàn)的技術(shù)均屬于本發(fā)明的范圍。具體實(shí)施方式實(shí)施例1一種適用于卷繞裝置外置的紡絲機(jī)的紡絲工藝,其工序包括粘膠計(jì)量與供膠、紡前過(guò)濾、絲條成型、紡絲及卷繞,其中,卷繞工序中,絲條經(jīng)卷繞裝置成型為可直接用于捻線的濕態(tài)的餅裝絲、濕態(tài)的筒裝絲和濕態(tài)的絞裝絲;所述濕態(tài)的餅裝絲、濕態(tài)的筒裝絲或濕態(tài)的絞裝絲的含水率為50%;所述成型為濕態(tài)的餅裝絲的離心缸的轉(zhuǎn)速為7200r/min;所述成型為濕態(tài)的絞裝絲的絞裝電機(jī)的轉(zhuǎn)速為800r/min;所述成型為濕態(tài)的筒裝絲采取主動(dòng)卷繞和被動(dòng)卷繞方式,其中:主動(dòng)卷繞中橫向電機(jī)的轉(zhuǎn)速為1000r/min,旋轉(zhuǎn)電機(jī)的轉(zhuǎn)速為1200r/min;被動(dòng)卷繞中橫向電機(jī)的轉(zhuǎn)速為800r/min,旋轉(zhuǎn)電機(jī)的轉(zhuǎn)速為1000r/min,油劑的pH值為8.5;所述被動(dòng)卷繞為單錠被動(dòng)卷繞。在粘膠計(jì)量與供膠工序中,粘膠管的表壓為0.1MPa;在紡前過(guò)濾工序中,粘膠熟成度NH4Cl值控制在7.0ml,落球粘度30mPa?s,粘膠甲纖含量8.0%,粘膠含堿6.1%,500ml粘膠氣泡≤25個(gè),粘膠表面張力50dyne/cm,10μm以下粘膠粒子≤100個(gè)/ml;在絲條成型工序中,酸浴的組成為:硫酸濃度135g/L,硫酸鈉濃度230g/L,硫酸鋅濃度12g/L,酸浴溫度55℃,酸浴表面張力小于粘膠表面張力;成型管內(nèi)徑Φ5±0.1mm,成型管長(zhǎng)1000mm;噴絲頭的孔徑為0.06mm,且形狀呈扇形;紡絲工序包括對(duì)絲條的凝固、牽伸、去酸及上油,紡絲輥長(zhǎng)度1000mm,直徑Φ150mm,紡絲輥轉(zhuǎn)速為130米/分,凝固反應(yīng)時(shí)間50秒/根,絲條的牽伸率為15%,淋洗水量為300ml/min,淋洗2次,水洗去酸中的水溫為35℃,pH值為7,油劑用量為10ml/min;所述經(jīng)凝固、牽伸、去酸、上油后的絲條,其含酸量在5~10%,生絲條剩余酯化度小于3%,含油率為0.5%,pH值為6.5。同樣的上述工藝可對(duì)不同規(guī)格(如40D、60D、120D、150D、200D等)、不同品種的絲條(如有光絲,無(wú)光絲,含棉、竹、麻等的復(fù)合絲,異形絲、扁平絲等)進(jìn)行處置。實(shí)施例2一種適用于卷繞裝置外置的紡絲機(jī)的紡絲工藝,其工序包括粘膠計(jì)量與供膠、紡前過(guò)濾、絲條成型、紡絲及卷繞,其中,卷繞工序中絲條經(jīng)卷繞裝置成型為可直接用于捻線的濕態(tài)的餅裝絲和濕態(tài)的絞裝絲;所述濕態(tài)的餅裝絲或濕態(tài)的絞裝絲的含水率為40%;所述成型為濕態(tài)的餅裝絲的離心缸的轉(zhuǎn)速為8400r/min;所述成型為濕態(tài)的絞裝絲的絞裝電機(jī)的轉(zhuǎn)速為1000r/min。在粘膠計(jì)量與供膠工序中,粘膠管的表壓為0.3MPa;在紡前過(guò)濾工序中,粘膠熟成度NH4Cl值控制在13ml,落球粘度38mPa?s,粘膠甲纖含量8.1%,粘膠含堿5.8%,500ml粘膠氣泡≤25個(gè),粘膠表面張力55dyne/cm,10μm以下粘膠粒子≤100個(gè)/ml;在絲條成型工序中,酸浴的組成為:硫酸濃度140g/L,硫酸鈉濃度240g/L,硫酸鋅濃度11.0g/L,酸浴溫度57℃,酸浴表面張力小于粘膠表面張力;成型管內(nèi)徑Φ5±0.1mm,成型管長(zhǎng)800mm;噴絲頭的孔徑為0.08mm,且形狀呈圓形;紡絲工序包括對(duì)絲條的凝固、牽伸、去酸及上油,紡絲輥長(zhǎng)度1200mm,直徑Φ120mm,紡絲輥轉(zhuǎn)速為150米/分,凝固反應(yīng)時(shí)間40秒/根,絲條的牽伸率為25%,淋洗水量為240ml/min,淋洗3次,水洗去酸中的水溫為45℃,pH值為7.5,油劑用量為20ml/min;所述經(jīng)凝固、牽伸、去酸、上油后的絲條,其含酸量在10~15%,生絲條剩余酯化度小于3%,含油率為1.0%,pH值為7.5。同樣的上述工藝可對(duì)不同規(guī)格(如40D、60D、120D、150D、200D等)、不同品種的絲條(如有光絲,無(wú)光絲,含棉、竹、麻等的復(fù)合絲,異形絲、扁平絲等)進(jìn)行處置。實(shí)施例3一種適用于卷繞裝置外置的紡絲機(jī)的紡絲工藝,其工序包括粘膠計(jì)量與供膠、紡前過(guò)濾、絲條成型、紡絲及卷繞,其中,卷繞工序中,絲條經(jīng)卷繞裝置成型為可直接用于捻線的濕態(tài)的餅裝絲和濕態(tài)的筒裝絲;所述濕態(tài)的餅裝絲或濕態(tài)的筒裝絲的含水率為80%;所述成型為濕態(tài)的餅裝絲的離心缸的轉(zhuǎn)速為7500r/min;所述成型為濕態(tài)的筒裝絲采取主動(dòng)卷繞方式,其中:所述主動(dòng)卷繞中,橫向電機(jī)的轉(zhuǎn)速為800r/min,旋轉(zhuǎn)電機(jī)的轉(zhuǎn)速為1000r/min。在粘膠計(jì)量與供膠工序中,粘膠管的表壓為0.5MPa;在紡前過(guò)濾工序中,粘膠熟成度NH4Cl值控制在10ml,落球粘度28mPa?s,粘膠甲纖含量8.2%,粘膠含堿5.8%,500ml粘膠氣泡≤25個(gè),粘膠表面張力53dyne/cm,10μm以下粘膠粒子≤100個(gè)/ml;在絲條成型工序中,酸浴的組成為:硫酸濃度145g/L,硫酸鈉濃度245g/L,硫酸鋅濃度12.5g/L,酸浴溫度56℃,酸浴表面張力小于粘膠表面張力;成型管內(nèi)徑Φ5±0.1mm,成型管長(zhǎng)1200mm;噴絲頭的孔徑為0.09mm,且形狀呈“一”字形;紡絲工序包括對(duì)絲條的凝固、牽伸、去酸及上油,紡絲輥長(zhǎng)度1500mm,直徑Φ180mm,紡絲輥轉(zhuǎn)速為100米/分,凝固反應(yīng)時(shí)間68秒/根,絲條的牽伸率為10%,淋洗水量為480ml/min,淋洗1次,水洗去酸中的水溫為60℃,pH值為8,油劑用量為50ml/min;所述經(jīng)凝固、牽伸、去酸、上油后的絲條,其含酸量在20~30%,生絲條剩余酯化度小于3%,含油率為1.5%,pH值為8.5。同樣的上述工藝可對(duì)不同規(guī)格(如40D、60D、120D、150D、200D等)、不同品種的絲條(如有光絲,無(wú)光絲,含棉、竹、麻等的復(fù)合絲,異形絲、扁平絲等)進(jìn)行處置。實(shí)施例4一種適用于卷繞裝置外置的紡絲機(jī)的紡絲工藝,其工序包括粘膠計(jì)量與供膠、紡前過(guò)濾、絲條成型、紡絲及卷繞,其中,卷繞工序中絲條經(jīng)卷繞裝置成型為可直接用于捻線的濕態(tài)的濕態(tài)的筒裝絲和濕態(tài)的絞裝絲;所述濕態(tài)的筒裝絲或濕態(tài)的絞裝絲的含水率為30%;所述成型為濕態(tài)的絞裝絲的絞裝電機(jī)的轉(zhuǎn)速為1000r/min;所述成型為濕態(tài)的筒裝絲采取被動(dòng)卷繞方式,其中:所述被動(dòng)卷繞中,橫向電機(jī)的轉(zhuǎn)速為1200r/min,旋轉(zhuǎn)電機(jī)的轉(zhuǎn)速為1500r/min,油劑的pH值為8;所述被動(dòng)卷繞包括單錠被動(dòng)卷繞、三錠被動(dòng)卷繞和通軸被動(dòng)卷繞。在粘膠計(jì)量與供膠工序中,粘膠管的表壓為0.4MPa;在紡前過(guò)濾工序中,粘膠熟成度NH4Cl值控制在8.0ml,落球粘度35mPa?s,粘膠甲纖含量8.2%,粘膠含堿5.9%,500ml粘膠氣泡≤25個(gè),粘膠表面張力52dyne/cm,10μm以下粘膠粒子≤100個(gè)/ml;在絲條成型工序中,酸浴的組成為:硫酸濃度138g/L,硫酸鈉濃度241g/L,硫酸鋅濃度11.5g/L,酸浴溫度55.5℃,酸浴表面張力小于粘膠表面張力;成型管內(nèi)徑Φ5±0.1mm,成型管長(zhǎng)900mm;噴絲頭的孔徑為0.07mm,且形狀呈扇形;紡絲工序包括對(duì)絲條的凝固、牽伸、去酸及上油,紡絲輥長(zhǎng)度1100mm,直徑Φ130mm,紡絲輥轉(zhuǎn)速為140米/分,凝固反應(yīng)時(shí)間55秒/根,絲條的牽伸率為25%,淋洗水量為400ml/min,淋洗2次,水洗去酸中的水溫為40℃,pH值為7.7,油劑用量為25ml/min;所述經(jīng)凝固、牽伸、去酸、上油后的絲條,其含酸量在15~25%,生絲條剩余酯化度小于3%,含油率為0.25%,pH值為6.5。同樣的上述工藝可對(duì)不同規(guī)格(如40D、60D、120D、150D、200D等)、不同品種的絲條(如有光絲,無(wú)光絲,含棉、竹、麻等的復(fù)合絲,異形絲、扁平絲等)進(jìn)行處置。實(shí)施例5一種適用于卷繞裝置外置的紡絲機(jī)的紡絲工藝,其工序包括粘膠計(jì)量與供膠、紡前過(guò)濾、絲條成型、紡絲及卷繞,其中,卷繞工序中,絲條經(jīng)卷繞裝置成型為可直接用于捻線的濕態(tài)的餅裝絲和濕態(tài)的筒裝絲;所述濕態(tài)的餅裝絲或濕態(tài)的筒裝絲的含水率為60%;所述成型為濕態(tài)的餅裝絲的離心缸的轉(zhuǎn)速為8000r/min;所述成型為濕態(tài)的筒裝絲采取主動(dòng)卷繞和被動(dòng)卷繞方式,其中:所述主動(dòng)卷繞中,橫向電機(jī)的轉(zhuǎn)速為900r/min,旋轉(zhuǎn)電機(jī)的轉(zhuǎn)速為1000r/min;所述被動(dòng)卷繞中,橫向電機(jī)的轉(zhuǎn)速為1100r/min,旋轉(zhuǎn)電機(jī)的轉(zhuǎn)速為1300r/min,油劑的pH值為7;所述被動(dòng)卷繞包括單錠被動(dòng)卷繞和通軸被動(dòng)卷繞。在粘膠計(jì)量與供膠工序中,粘膠管的表壓為0.2MPa;在紡前過(guò)濾工序中,粘膠熟成度NH4Cl值控制在11ml,落球粘度32mPa?s,粘膠甲纖含量8.1%,粘膠含堿6%,500ml粘膠氣泡≤25個(gè),粘膠表面張力51dyne/cm,10μm以下粘膠粒子≤100個(gè)/ml;在絲條成型工序中,酸浴的組成為:硫酸濃度137g/L,硫酸鈉濃度238g/L,硫酸鋅濃度11.8g/L,酸浴溫度56℃,酸浴表面張力小于粘膠表面張力;成型管內(nèi)徑Φ5±0.1mm,成型管長(zhǎng)1000mm;噴絲頭的孔徑為0.07mm,且形狀呈7圓形;紡絲工序包括對(duì)絲條的凝固、牽伸、去酸及上油,紡絲輥長(zhǎng)度1250mm,直徑Φ160mm,紡絲輥轉(zhuǎn)速為120米/分,凝固反應(yīng)時(shí)間58秒/根,絲條的牽伸率為18%,淋洗水量為280ml/min,淋洗3次,水洗去酸中的水溫為47℃,pH值為7.8,油劑用量為46ml/min;所述經(jīng)凝固、牽伸、去酸、上油后的絲條,其含酸量在25~30%,生絲條剩余酯化度小于3%,含油率為1.2%,pH值為7.6。同樣的上述工藝可對(duì)不同規(guī)格(如40D、60D、120D、150D、200D等)、不同品種的絲條(如有光絲,無(wú)光絲,含棉、竹、麻等的復(fù)合絲,異形絲、扁平絲等)進(jìn)行處置。上述實(shí)施例1-5所述的濕態(tài)的餅裝絲、濕態(tài)的筒裝絲或者濕態(tài)的絞裝絲具有的主要技術(shù)指標(biāo)如下表所示:實(shí)施例6(與實(shí)施例1-5基本相同)一種適用于卷繞裝置外置的紡絲機(jī)的紡絲工藝,在紡前過(guò)濾工序中,粘膠熟成度NH4Cl值控制在7.0ml,落球粘度29mPa?s,粘膠甲纖含量8.0%,粘膠含堿5.8%,500ml粘膠氣泡≤25個(gè),粘膠表面張力50dyne/cm,10μm以下粘膠粒子≤100個(gè)/ml。實(shí)施例7(與實(shí)施例1-5基本相同)一種適用于卷繞裝置外置的紡絲機(jī)的紡絲工藝,在紡前過(guò)濾工序中,粘膠熟成度NH4Cl值控制在9.0ml,落球粘度33mPa?s,粘膠甲纖含量8.1%,粘膠含堿5.9%,500ml粘膠氣泡≤25個(gè),粘膠表面張力51dyne/cm,10μm以下粘膠粒子≤100個(gè)/ml。實(shí)施例8(與實(shí)施例1-5基本相同)一種適用于卷繞裝置外置的紡絲機(jī)的紡絲工藝,在絲條成型工序中,酸浴的組成為:硫酸濃度137g/L,硫酸鈉濃度235g/L,硫酸鋅濃度11.8g/L,酸浴溫度56.5℃,酸浴表面張力小于粘膠表面張力;成型管內(nèi)徑Φ5±0.1mm,成型管長(zhǎng)950mm;噴絲頭的孔徑為0.06mm,且形狀呈扇形。實(shí)施例9(與實(shí)施例1-5基本相同)一種適用于卷繞裝置外置的紡絲機(jī)的紡絲工藝,在絲條成型工序中,酸浴的組成為:硫酸濃度142g/L,硫酸鈉濃度240g/L,硫酸鋅濃度12.3g/L,酸浴溫度56.5℃,酸浴表面張力小于粘膠表面張力;成型管內(nèi)徑Φ5±0.1mm,成型管長(zhǎng)1050mm;噴絲頭的孔徑為0.085mm,且形狀呈圓形。實(shí)施例10(與實(shí)施例1-5基本相同)一種適用于卷繞裝置外置的紡絲機(jī)的紡絲工藝,在紡絲工序中,紡絲輥長(zhǎng)度1350mm,直徑Φ168mm,紡絲輥轉(zhuǎn)速為145米/分,凝固反應(yīng)時(shí)間47秒/根,絲條的牽伸率為18%,淋洗水量為370ml/min,淋洗1次,水洗去酸中的水溫為42℃,pH值為7.6,油劑用量為8ml/min。實(shí)施例11(與實(shí)施例1-5基本相同)一種適用于卷繞裝置外置的紡絲機(jī)的紡絲工藝,在紡絲工序中,紡絲輥長(zhǎng)度1285mm,直徑Φ146mm,紡絲輥轉(zhuǎn)速為115米/分,凝固反應(yīng)時(shí)間65秒/根,絲條的牽伸率為22%,淋洗水量為260ml/min,淋洗2次,水洗去酸中的水溫為52℃,pH值為7.7,油劑用量為35ml/min。實(shí)施例12(與實(shí)施例1-5基本相同)一種適用于卷繞裝置外置的紡絲機(jī)的紡絲工藝,在卷繞工序中,絲條經(jīng)卷繞裝置成型為可直接用于捻線的濕態(tài)的筒裝絲;所述濕態(tài)的筒裝絲的含水率為55%;所述成型為濕態(tài)的筒裝絲采取被動(dòng)卷繞方式,所述被動(dòng)卷繞中,橫向電機(jī)的轉(zhuǎn)速為1050r/min,旋轉(zhuǎn)電機(jī)的轉(zhuǎn)速為1250r/min,油劑的pH值為12;所述被動(dòng)卷繞包括單錠被動(dòng)卷繞和三錠被動(dòng)卷繞。實(shí)施例13(與實(shí)施例1-5基本相同)一種適用于卷繞裝置外置的紡絲機(jī)的紡絲工藝,在卷繞工序中,絲條經(jīng)卷繞裝置成型為可直接用于捻線的濕態(tài)的餅裝絲;所述濕態(tài)的餅裝絲為35%;所述成型為濕態(tài)的餅裝絲的離心缸的轉(zhuǎn)速為7800r/min。實(shí)施例14(與實(shí)施例1-5基本相同)一種適用于卷繞裝置外置的紡絲機(jī)的紡絲工藝,在卷繞工序中,絲條經(jīng)卷繞裝置成型為可直接用于捻線的濕態(tài)的濕態(tài)的絞裝絲;所述濕態(tài)的絞裝絲的含水率為57%;所述成型為濕態(tài)的絞裝絲的絞裝電機(jī)的轉(zhuǎn)速為500r/min。實(shí)施例15一種適用于卷繞裝置外置的紡絲機(jī)的紡絲工藝,在卷繞工序中,絲條經(jīng)卷繞裝置成型為可直接用于捻線的濕態(tài)的濕態(tài)的餅裝絲和濕態(tài)的筒裝絲;所述濕態(tài)的餅裝絲或濕態(tài)的筒裝絲的含水率為70%;所述成型為濕態(tài)的餅裝絲的離心缸的轉(zhuǎn)速為7400r/min;所述成型為濕態(tài)的筒裝絲采取主動(dòng)卷繞和被動(dòng)卷繞方式,其中:所述主動(dòng)卷繞中,橫向電機(jī)的轉(zhuǎn)速為950r/min,旋轉(zhuǎn)電機(jī)的轉(zhuǎn)速為1100r/min;所述被動(dòng)卷繞中,橫向電機(jī)的轉(zhuǎn)速為1100r/min,旋轉(zhuǎn)電機(jī)的轉(zhuǎn)速為1200r/min,油劑的pH值為9;所述被動(dòng)卷繞包括三錠被動(dòng)卷繞和通軸被動(dòng)卷繞。實(shí)現(xiàn)本發(fā)明工藝的紡絲機(jī)可以是如圖7-圖29所示的結(jié)構(gòu),具體說(shuō)明見(jiàn)實(shí)施例16~實(shí)施例21。實(shí)施例16一種紡絲機(jī),包括機(jī)架1、供膠裝置2、絲條成型裝置3、紡絲裝置4和卷繞裝置5,所述卷繞裝置5的成形部分位于機(jī)架1兩側(cè)墻板6之間所在區(qū)域的外側(cè)、與紡面101相對(duì)的另一側(cè),所述紡面101是指在機(jī)架1墻板6外側(cè)、設(shè)置有絲條成型裝置3的區(qū)域,與所述區(qū)域相對(duì)的另一側(cè)稱為卷繞面7,所述紡絲裝置4包括多根紡絲輥,所述紡絲輥的兩端固定,所述卷繞裝置5包括濕態(tài)餅裝卷繞裝置51、和/或濕態(tài)筒裝卷繞裝置52、和/或濕態(tài)絞裝卷繞裝置53。所述卷繞裝置5的松筒管5203形狀包括平行筒、錐形筒、菠蘿筒或紡錘筒。所述的卷繞裝置5位于紡絲輥的端面、且位于機(jī)架1的外側(cè)。所述機(jī)架1包括至少兩個(gè)立柱1101,所述墻板(6)分別安裝在立柱1101上。實(shí)施例17濕態(tài)筒裝卷繞裝置52包括主動(dòng)濕態(tài)卷繞裝置或\和被動(dòng)濕態(tài)卷繞裝置,所述濕態(tài)是指絲條的含水率在30~200%,其中當(dāng)絲條的含水率為30~80%時(shí),可直接用于捻線工序,所以本申請(qǐng)中的濕態(tài)筒裝卷繞裝置52、濕態(tài)餅裝卷繞裝置51或者濕態(tài)絞裝卷繞裝置53均是指適用于濕態(tài)絲條的卷繞裝置5。所述主動(dòng)濕態(tài)卷繞裝置的具體結(jié)構(gòu)如圖14所示。所述被動(dòng)濕態(tài)卷繞裝置的具體結(jié)構(gòu)如圖15-圖20所示。實(shí)施例18濕態(tài)餅裝卷繞裝置51如圖21所示。實(shí)施例19濕態(tài)絞裝卷繞裝置53如圖22所示。實(shí)施例20水洗裝置41如圖10-圖11所示。實(shí)施例21上油裝置42如圖12-圖13所示。