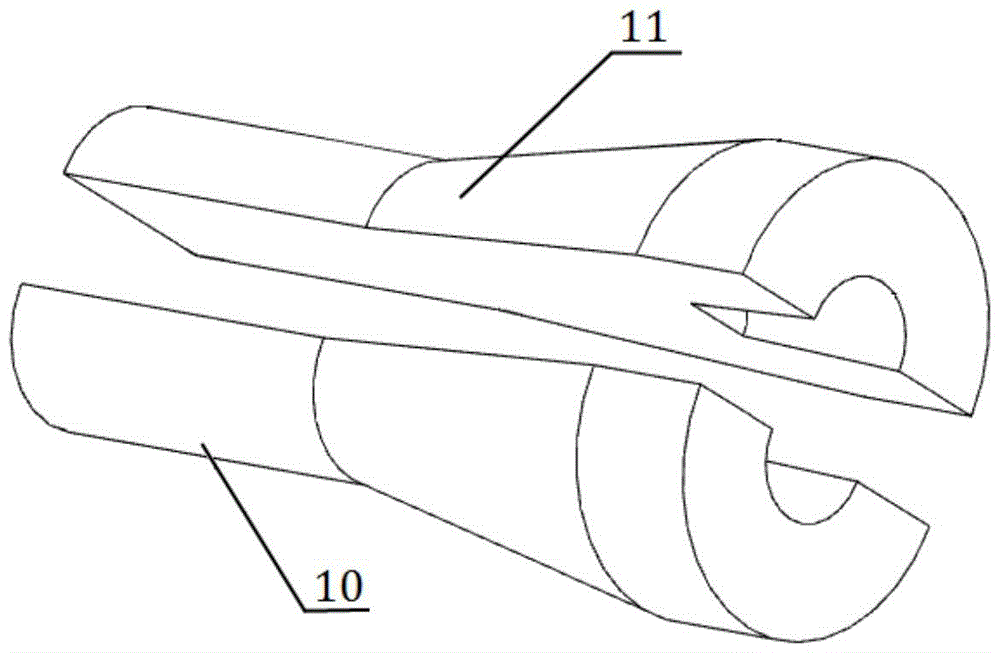
本發(fā)明涉及的是一種管材精密成形領域的技術,具體是一種管形件局部加厚成形裝置及其方法。
背景技術:管形件在機械行業(yè)中是一種十分常見的零部件,管形件之間一般采用螺紋連接,為保證連接處的強度,需要將其進行局部加厚處理,因此管形件的局部加厚工藝一直受到關注。管形件局部鐓鍛是一種典型的加厚方法,局部加厚處容易出現(xiàn)一系列問題,如加厚的尺寸不滿足要求,內(nèi)表面凹凸不平,平滑度較差,影響后續(xù)裝配和服役性能。因此,如何提高管形件加厚質量是急需解決的問題。目前,對于管形件局部加厚,利用不同凸凹模多道次鐓鍛成形,雖然多道次鐓鍛可以增大加厚程度,降低形成折疊缺陷的風險,但是工藝過程參數(shù)不易控制,所得局部加厚零件內(nèi)表面質量難以保證。經(jīng)過對現(xiàn)有技術的檢索發(fā)現(xiàn),中國專利文獻號CN104439011A,公告日2015.3.25,公開了一種石油鉆桿加厚端成形凸模及其應用,凸模包括凸模桿與三個凸模塊,凸模桿的前端開設有外螺紋,凸模塊內(nèi)側開設有內(nèi)螺紋段,凸模塊共設有三個,三個凸模塊圍合成完整的凸模環(huán),且三個凸模塊上的內(nèi)螺紋段圍合成與外螺紋配合的內(nèi)螺紋,凸模環(huán)為中空圓錐臺結構,有利于控制石油鉆桿的內(nèi)表面質量。但該技術要求每次鐓鍛時都需要重新組裝凸模,鐓粗完成后還要將凸模拆卸下來,整個操作過程相對繁鎖,直接影響生產(chǎn)效率。
技術實現(xiàn)要素:本發(fā)明針對現(xiàn)有技術存在的上述不足,提出一種管形件局部加厚成形裝置及其方法,所述成形裝置由凸模組件、活動芯軸、凹模、滑塊和頂桿組成,成形過程中,凸模組件與活動芯軸剛性接觸,并與凹模形成管件加厚部分的模具型腔,逐步鐓擠壓管料完成管件端部加厚,內(nèi)表面由活動芯軸控制,形成的加厚過渡區(qū)表面質量良好;活動芯軸通過滑塊與頂桿連為一體,取出方便,大幅提高生產(chǎn)效率。本發(fā)明是通過以下技術方案實現(xiàn)的:本發(fā)明涉及一種管形件局部加厚成形裝置,包括:依次相連的頂桿、滑塊、活動芯軸、凸模組件和套接于凸模組件外側的凹模,其中:頂桿、滑塊和活動芯軸分別與凹模間隙配合。所述的凸模組件包括:套接的內(nèi)凸模和外凸模。所述的內(nèi)凸模與活動芯軸剛性接觸。所述的活動芯軸包括:彈性連接并且彼此對稱的左半芯軸和右半芯軸。所述的滑塊分別與活動芯軸和頂桿彈性連接。本發(fā)明涉及一種基于上述裝置的管形件局部加厚成形方法,包括以下步驟:步驟1、定位管坯:沿徑向打開凹模,放入管坯至預定位置后合攏凹模并壓緊,完成管坯定位。步驟2、模具調整:連接活動芯軸、滑塊和頂桿,形成連接體;把凸模組件移入凹模,直至外凸模與管坯的一端接觸,再將連接體從管坯另一端移入凹模,直至活動芯軸與內(nèi)凸模接觸;推動頂桿,通過滑塊使活動芯軸的兩個半芯軸處于張開狀態(tài),形成內(nèi)模腔。步驟3、管形件鐓擠成形:保持頂桿的力不變,與凹模配合的外凸模進行軸向移動,使管坯沿軸向鐓擠成形,實現(xiàn)管形件的局部加厚。步驟4、取出管形件:將外凸模和內(nèi)凸模依次從管形件的一端沿軸向移出,此時兩個半芯軸合攏,通過頂桿將連接體從管形件的另一端沿軸向移出,打開凹模,取出已完成加厚成形的管形件。技術效果與現(xiàn)有技術相比,本發(fā)明采用了凸模組件、活動芯軸與可分凹模形成模具型腔,凸模組件的內(nèi)凸模和外凸模兩個部分可按順序動作;活動芯軸分為左半芯軸和右半芯軸,通過彈簧依次與滑塊和頂桿相連,便于從管件中取出;可分凹??裳貜较驅崿F(xiàn)開合,方便管坯的放入與管件的取出。本發(fā)明采用活動芯軸與可分凹模配合,并結合外凸模鐓擠成形,獲得了內(nèi)表面質量可控的局部加厚管件,且具有較高的生產(chǎn)效率,便于投入批量生產(chǎn)。附圖說明圖1為本發(fā)明示意圖;圖2為芯軸結構示意圖;圖3為滑塊結構示意圖;圖中:1和3為周向彈簧,2為完成加厚成形的管形件,4為凹模,5為頂桿,6和7為連接彈簧,8為滑塊,9為管坯,10為左半芯軸,11為右半芯軸,12為內(nèi)凸模,13為外凸模,14為縫隙。具體實施方式下面對本發(fā)明的實施例作詳細說明,本實施例在以本發(fā)明技術方案為前提下進行實施,給出了詳細的實施方式和具體的操作過程,但本發(fā)明的保護范圍不限于下述的實施例。實施例1如圖1所示,本實施例包括:管坯9、依次相連的頂桿5、滑塊8、活動芯軸、凸模組件和套接于凸模組件外側的凹模4,其中:頂桿5、滑塊8和活動芯軸通過連接彈簧6和7相連,并且通過管坯9與凹模4間隙配合。所述的凸模組件包括:套接的內(nèi)凸模12和外凸模13。所述的內(nèi)凸模12與活動芯軸剛性接觸。所述的凹模4為徑向可分凹模,便于加厚成形后的管形件取出。如圖2所示,所述的活動芯軸包括:彼此對稱的左半芯軸10和右半芯軸11,其中:左半芯軸10和右半芯軸11通過兩端的周向彈簧1、3連接。張開狀態(tài)時,所述的左半芯軸10和右半芯軸11形成縫隙14。如圖3所示,所述的滑塊8的一端設有圓臺形的凸起,另一端設有凹槽。所述的頂桿5的頂端設有與凹槽相配合的凸緣,活動芯軸的底部設有與凸起相配合的圓臺形凹槽。本實施例通過以下步驟對管形件進行局部加厚成形:步驟1、步驟1、定位管坯9:沿徑向打開凹模4,放入管坯9至預定位置后合攏凹模4并壓緊,完成管坯9定位。步驟2、模具調整:連接活動芯軸、滑塊8和頂桿5,形成連接體;把凸模組件移入凹模4,直至外凸模13與管坯9的一端接觸,再將連接體從管坯9的另一端移入凹模4,直至活動芯軸與內(nèi)凸模12接觸;推動頂桿5,通過滑塊8使活動芯軸的兩個半芯軸10和11克服周向彈簧3的約束力微微張開,形成內(nèi)模腔,中間保有縫隙14。步驟3、管形件鐓擠成形:保持頂桿5的力不變,與凹模4配合的外凸模13進行軸向移動,使管坯9沿軸向鐓擠成形,實現(xiàn)管形件的局部加厚。所述的管形件為難變形材料時,可采用熱鐓擠壓成形;管形件為易變材料時,可采用冷鐓擠成形。步驟4、取出管形件:將外凸模13和內(nèi)凸模12依次從完成加厚成形的管形件2的一端沿軸向移出,此時兩個半芯軸10和11由于周向彈簧3收緊而無縫合攏,與完成加厚成形的管形件2的內(nèi)表面分離,移動方便;通過頂桿5將連接體從完成加厚成形的管形件2的另一端沿軸向移出,打開凹模4,取出已完成加厚成形的管形件2。所述的縫隙14的寬度小于1mm,優(yōu)選為0.4mm。所述的活動芯軸的外表面與管坯9的內(nèi)表面形狀相匹配,活動芯軸的外側錐度與完成加厚成形的管形件2的加厚端過渡區(qū)內(nèi)表面錐度相同,以保證加厚端過渡區(qū)是由活動芯軸控制其成形過程。所述的活動芯軸結構簡單,使用方便,易于取出。所述的周向彈簧1和3的作用力可保證左半芯軸10和右半芯軸11不會發(fā)生分離。所述的凸模組件與活動芯軸、凹模配合,形成用于管坯9加厚的模具型腔,便于控制管形件的內(nèi)表面質量。所述的外凸模13用于對管坯9進行鐓擠成形。所述的滑塊8一端的連接彈簧6保證頂桿5與滑塊8始終連接。所述的滑塊8和頂桿5的外表面與管坯9的內(nèi)表面有一定距離,以保證頂桿5帶動滑塊8和活動芯軸移入與移出時不會與管坯9產(chǎn)生接觸,減小阻力。本實施例管形件內(nèi)表面的成形過程由活動芯軸控制,獲得了良好的加厚區(qū)內(nèi)表面質量,過渡光滑;活動芯軸與頂桿5通過滑塊8連為一體,取出方便,大幅提高生產(chǎn)效率。