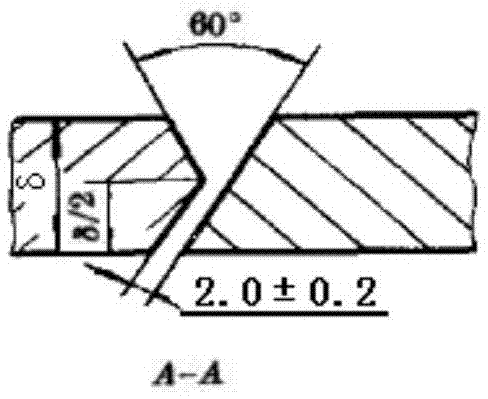
本案屬于焊接領(lǐng)域,涉及氣體保護電弧焊之實芯焊絲的制備方法及其中間成品和產(chǎn)成品及其工藝設(shè)備。特別是拉拔的工藝,及其配模的工藝單元。拉拔單元的絲材構(gòu)造,
背景技術(shù):
:不銹鋼焊絲、焊條在自動化技術(shù)中的應(yīng)用越來越多,但是已有技術(shù)制備的不銹鋼焊絲常見的質(zhì)量問題是焊絲外觀不好、送絲不夠穩(wěn)定,因此難以滿足高自動化焊接設(shè)備的要求。一般可知,焊絲質(zhì)量與煉鋼引起的化學(xué)成分的細微變化有著緊密的關(guān)系,與材料成分的雜質(zhì)含量有著緊密的關(guān)系,重要的是焊絲制備的工藝方法和工藝設(shè)備關(guān)系著焊絲的半成品、產(chǎn)成品的品質(zhì)。為此業(yè)界在這方面做過很多努力,已有技術(shù)包括但不限于:如中國專利公開了“03110146.1未鍍覆的焊接用實芯焊絲”,其中含有c、si、mn、ti,文件提供了將si、mn、ti作為各元素在焊絲中的含量時的條件等等工藝構(gòu)成,闡述能夠提高焊絲的送進性和引弧性。又如中國專利公開了“200410057630.9實心焊絲的生產(chǎn)方法”步驟包括:在用于拉絲的干燥固體潤滑劑幫助下用輥模拉絲,用于拉絲的干燥固體潤滑劑至少含有硬脂酸鈉或硬脂酸鉀;將用于焊絲進料的潤滑劑涂布在已經(jīng)用上油設(shè)備拉拔的焊絲表面上。用輥模高速拉絲。再如中國專利公開了“200410057948.7用于制造有縫焊劑芯焊絲的方法”,步驟包括:利用潤滑劑拉伸包括在其中填充焊劑形成的管狀焊絲;通過物理方法從拉伸的焊絲上去除潤滑劑;以及在焊絲表面上涂覆用于進給的焊絲潤滑劑(涂覆油)。在焊絲拉伸步驟中,使用包含含硫高壓潤滑劑的焊絲拉伸潤滑劑。如中國專利公開了“98800383.x一種焊絲的制造方法”,其中,在對焊絲原材料線拉絲以制造焊絲的方法中的拉絲工序的至少一部分,依次進行一邊供給粉體潤滑劑一邊實施的干式孔模拉絲、輥輪拉絲模式拉絲、以及濕式孔模拉絲。用上述干式孔模拉絲將粉末潤滑劑強力壓入焊絲表面,目的是令焊絲表面成為粗糙面。還有,中國專利200910052322.x公開了一種不銹鋼的制備方法。中國專利200910223502.x公開了適合于時效馬氏體不銹鋼焊接用焊絲。還有已有技術(shù)h1cr21ni10mn6焊絲,主要用于重型、大型車輛等自動焊接,本案也是以此為研發(fā)背景的進一步改進,目的在于進一步提高焊絲的抗拉強度,提高其熔敷金屬的抗拉強度,為此還有包括但不限于下述公開:如中國專利201110104281.1公開了一種焊絲、盤條及其應(yīng)用它涉及盤條和焊絲。還有,本案申請人在先提出的中國專利申請“21-10mn7mo鋼錠及其冶煉工藝,申請?zhí)枮?01310756138x”,以及它提述的已有技術(shù)背景,在此引用,不再贅述。已有的技術(shù)存在下述問題亟待解決。本案焊絲是在已有的h1cr21ni10mn6焊絲的基礎(chǔ)上的創(chuàng)新,包括添加適量的mo,同時相應(yīng)的提高mn的含量,問題在于由此材料成分的改變會對后期的生產(chǎn)帶來工藝困難。一般可知,鉬在合金鋼中的含量在一定范圍時,鉬會使合金鋼的塑性和韌性下降,由于本案所述21-10mn7mo材料成分的因素,強度高,其拔制過程中易產(chǎn)生裂紋。已有技術(shù)存在的問題包括高強度焊絲拔制過程中裂紋較多,成材率很低。高強度焊絲在使用過程中存在送絲不暢,容易堵焊嘴的問題。因此業(yè)界亟待通過包括拉拔在內(nèi)的工藝方法的改善來解決這樣的問題。已有的技術(shù)因由焊絲的組分、焊絲的制備方法以及工藝設(shè)備的原因,不能很好的克服上述的問題。技術(shù)實現(xiàn)要素:本發(fā)明所要解決的問題在于克服前述技術(shù)存在的上述缺陷,而提供一種針對制備21-10mn7mo焊絲的拉拔方法及其配模的工藝單元及其產(chǎn)成品和中間品。本發(fā)明解決技術(shù)問題是采取以下技術(shù)方案來實現(xiàn)的,依據(jù)本發(fā)明提供的一種制備21-10mn7mo焊絲的拉拔方法,包括蘸涂層處理和配模工藝,其中:所述的配模工藝具有第一次拉拔的步驟:將預(yù)設(shè)直徑尺寸的盤條依次經(jīng)過固溶處理、酸洗處理、蘸涂層處理、拉拔,第一次拉拔處理的總減面率為56%,由此獲得預(yù)設(shè)直徑尺寸的第一道絲材;第二次拉拔的步驟:將第一道絲材依次經(jīng)過去油處理、光亮退火處理、蘸涂層處理、第二次拉拔處理,拉拔的總減面率為57%,由此獲得預(yù)設(shè)直徑尺寸的第二道絲材;第三次拉拔的步驟:將第二道絲材依次經(jīng)過去油處理、光亮退火處理、蘸涂層處理、第三次拉拔處理,拉拔的總減面率為75%,由此獲得預(yù)設(shè)直徑尺寸的第三道絲材。進一步,前述的制備21-10mn7mo焊絲的拉拔方法,其中:所述的配模工藝設(shè)置為:第一次拉拔的步驟為:φ5.5-φ4.9-φ4.41-φ4.04-φ3.80-φ3.65,退火處理為光亮退火,總減面率為56%;第二次拉拔的步驟為:φ3.65-φ3.2-φ2.93-φ2.68-φ2.52-φ2.4,退火處理為光亮退火,總減面率為57%;第三次拉拔的步驟為:φ2.4-φ2.06-φ1.79-φ1.55-φ1.35-φ1.2總減面率為75%。前述的方法制備的21-10mn7mo焊絲,其中,所述焊絲的化學(xué)成分質(zhì)量%應(yīng)滿足:碳c≤0.10、硅si≤0.8、錳mn5.5-8.0、磷p≤0.030、硫s≤0.020、鎳ni9.0-11.0、鉻cr19.0-22.0、鉬mo0.5-2.0,或/和余量為鐵fe和不可避免的雜質(zhì),或/和,mn/mo比控制在7-7.5之間。本發(fā)明解決技術(shù)問題是采取以下技術(shù)方案來實現(xiàn)的,依據(jù)本發(fā)明提供的一種21-10mn7mo焊絲的用途,所述21-10mn7mo焊絲用于裝甲鋼或合金鋼或調(diào)質(zhì)鋼或異種鋼的焊接,或/和,裝甲鋼或合金鋼或調(diào)質(zhì)鋼或異種鋼的自動化焊接、半自動化焊接。本發(fā)明解決技術(shù)問題是采取以下技術(shù)方案來實現(xiàn)的,依據(jù)本發(fā)明提供的一種應(yīng)用前述制備方法的21-10mn7mo焊絲拉絲機,包括模具裝置,其中,所述的模具裝置依次配置第一模具裝置、第二模具裝置、第三模具裝置、第四模具裝置、第五模具裝置。前述21-10mn7mo焊絲拉絲機,其中,相鄰的模具裝置之間設(shè)置拉絲機構(gòu)。前述21-10mn7mo焊絲拉絲機,其中,各模具裝置的輸入端配置導(dǎo)向機構(gòu)。前述的21-10mn7mo焊絲拉絲機,其中,相鄰的模具裝置之間,模具裝置的輸入端,配置張力機構(gòu)。前述的21-10mn7mo焊絲拉絲機,其中,各個模具裝置的輸出端,配置拉絲模具單元;模具裝置的輸出端與模具裝置的輸入端之間設(shè)置拉絲潤滑單元。前述的21-10mn7mo焊絲拉絲機,其中,所述的拉絲潤滑單元具有容絲材通過的第一進料孔和第二進料孔,第一進料孔位于模具裝置輸入端一側(cè),第二進料孔的模具裝置輸出端一側(cè),該第一進料孔和第二進料孔之間是容置潤滑劑的工作槽,用于為進入模具裝置的絲材提供潤滑劑;所述的拉絲模具單元具有冷卻槽,用于為模具提供冷卻水;拉絲模具主體借由拉絲模具活套的裝置在冷卻槽中;拉絲模具活套用于頂持拉絲模具主體。前述的21-10mn7mo焊絲拉絲機,其中,所述容置潤滑劑的工作槽內(nèi)的潤滑劑是鈉基潤滑劑。本發(fā)明解決技術(shù)問題是采取以下技術(shù)方案來實現(xiàn)的,依據(jù)本發(fā)明提供的一種21-10mn7mo絲材結(jié)構(gòu),它包括21-10mn7mo絲材本體,其中,絲材本體的化學(xué)成分質(zhì)量%應(yīng)滿足:碳c≤0.10、硅si≤0.8、錳mn5.5-8.0、磷p≤0.030、硫s≤0.020、鎳ni9.0-11.0、鉻cr19.0-22.0、鉬mo0.5-2.0,或/和余量為鐵fe和不可避免的雜質(zhì)。前述的21-10mn7mo絲材結(jié)構(gòu),其中,mn/mo比控制在7-7.5之間。前述的21-10mn7mo絲材結(jié)構(gòu),其中,所述絲材本體外表面為潤滑膜層,所述的潤滑膜層為鈉基潤滑劑形成的膜,在絲材本體表面與潤滑膜層之間具有蘸涂層。前述的21-10mn7mo絲材結(jié)構(gòu),其中,所述的蘸涂層是借由礦物鹽基料在絲材本體表面形成的用于攜帶潤滑粉(劑)的載體層。前述21-10mn7mo絲材結(jié)構(gòu),其中,所述的涂料是以礦物鹽為基料的涂料。前述的21-10mn7mo絲材結(jié)構(gòu),其中,涂層溶液滿足:當水溫達到90℃時,按150-200克/升的比例將礦物鹽為基料的涂料溶入水中全部溶解。前述的21-10mn7mo絲材結(jié)構(gòu),其中,所述蘸涂層的形成應(yīng)滿足被處理的絲材浸泡時間為5-6分鐘;絲材經(jīng)過浸泡后,烘干,烘干溫度應(yīng)滿足120℃至150℃,烘干時間應(yīng)大于3小時。本發(fā)明解決技術(shù)問題是采取以下技術(shù)方案來實現(xiàn)的,依據(jù)本發(fā)明提供的一種用前述的21-10mn7mo焊絲焊接的焊縫,包括焊接母材,其中,焊接母材為675鋼或685鋼,焊接的融合線一側(cè)的熱影響區(qū)組織為粗大的馬氏體和貝氏體以及殘余奧氏體;母材的金相組織為回火索氏體;焊縫區(qū)的金相組織為奧氏體以及鐵素體。前述的21-10mn7mo焊絲焊接的焊縫,其中,焊接工藝條件為:母材板厚為45mm或5mm;焊接電流:120-140a,焊接電壓:20-24v,焊接速度:150-200mm/min,保護氣體:95%ar+5%co2;氣體流量15-20l/min。本發(fā)明與現(xiàn)有技術(shù)相比具有顯著的優(yōu)點和有益效果,在前述
發(fā)明內(nèi)容中給出,并在實施例中更具體給出,不在此贅述。本發(fā)明的具體實施方式由以下實施例詳細給出。本發(fā)明的具體實施方式由以下實施例及其附圖詳細給出。附圖說明圖1是制備21-10mn7mo焊絲的五聯(lián)罐拉絲機俯視面結(jié)構(gòu)示意圖。圖1a是制備21-10mn7mo焊絲的五聯(lián)罐拉絲機正視、剖視面結(jié)構(gòu)示意圖。圖2是制備21-10mn7mo焊絲中,模具裝置的立體結(jié)構(gòu)示意圖。圖3是制備21-10mn7mo焊絲中,拉拔單元的絲材結(jié)構(gòu)示意圖。圖4是常溫斜y型坡口焊接裂紋試驗,試件坡口形狀及尺寸組焊示意圖。圖4a是圖4的a-a向剖視面結(jié)構(gòu)示意圖。圖4b是圖4的b-b向剖視面結(jié)構(gòu)示意圖。圖5a是21-10mn7mo焊接685鋼的焊縫及熱影響區(qū)的金相組織中,焊接的融合線示意圖,其中融合線左邊為熱影響區(qū),融合線右邊為焊縫。圖5b是21-10mn7mo焊接685鋼的焊縫及熱影響區(qū)的金相組織中,熱影響區(qū)組織示意圖,顯示組織為粗大的馬氏體+貝氏體+殘余奧氏體。圖5c是21-10mn7mo焊接685鋼的焊縫及熱影響區(qū)的金相組織中,母材的金相組織示意圖,顯示組織為回火索氏體。圖5d是21-10mn7mo焊接685鋼的焊縫及熱影響區(qū)的金相組織中,焊縫區(qū)的金相組織示意圖,顯示組織為奧氏體+鐵素體。圖6a-6d是已有對比技術(shù)焊接685鋼的焊縫及熱影響區(qū)的金相組織示意圖,其中,a是焊接的融合線示意圖、b是熱影響區(qū)組織示意圖,c是母材的金相組織示意圖,d焊縫區(qū)的金相組織示意圖。圖7是21-10mn7mo焊接用于機器人的試驗中,焊縫外形效果圖。圖8是制備21-10mn7mo焊絲其中的拉絲工藝路線示意圖。具體實施方式以下結(jié)合較佳實施例,對依據(jù)本發(fā)明提供的具體實施方式、特征及其功效,詳細說明如后;為了簡單和清楚的目的,下文恰當?shù)氖÷粤斯夹g(shù)的描述,以免那些不必要的細節(jié)影響對本技術(shù)方案的描述。參見圖1-8所示,一種制備21-10mn7mo焊絲的拉拔方法及其中間工藝,及其產(chǎn)成品及中間產(chǎn)品。一、焊絲拉拔的工藝路線制備21-10mn7mo焊絲其中拉拔工藝的前序工藝包括冶煉鑄錠的工藝,鍛造制備鍛坯件(也稱坯料)的工藝、熱軋盤條的工藝。優(yōu)選的可以引用下述專利申請?zhí)峁┑墓に噯卧?,借此工藝方法獲得更好的鋼錠、鍛坯件、盤條等中間產(chǎn)品,為焊絲的拉拔工序提供更好的工藝條件。制備21-10mn7mo焊絲其中的冶煉工藝,包括并不限于但可以優(yōu)選本申請人已公開的中國專利申請“201310756138x,名為21-10mn7mo鋼錠及其冶煉工藝”。由此可以獲得制備焊絲的鋼錠。制備21-10mn7mo焊絲其中的鍛造的方法、熱軋的方法包括并不限于但可以優(yōu)選本申請人已經(jīng)在先申請,但尚未公開的如下中國專利申請:申請?zhí)?014108478543制備21-10mn7mo焊絲的鍛造方法及其鍛坯件;申請?zhí)?014108494813制備21-10mn7mo焊絲的坯件及熱軋方法。由此可以獲得制備焊絲的鍛坯件和盤條。制備21-10mn7mo焊絲其中的拉絲工藝路線可以如圖8所示。從圖8所示的拉絲工藝路線可知,在焊絲拉拔之前,首先要對盤條涂潤滑載體,也就是蘸涂層處理。蘸涂層處理可以讓盤條或處理過程中的絲材表面形成一層粗糙、多孔、能吸附和攜帶潤滑粉(劑)的載體,拉絲時借助這層載體將拉絲粉(劑)帶入模具中,從而起到潤滑的作用。蘸涂層處理的方法包括并不限于但可以優(yōu)選本申請人已經(jīng)在先申請,但尚未公開的如下中國專利申請:申請?zhí)?015102893481制備21-10mn7mo焊絲的拉拔方法及其蘸涂層處理的工藝單元。制備21-10mn7mo焊絲其中拉拔的工藝,以直徑5.5毫米盤條的拉絲工藝流程為例,如下示意:φ5.5盤條→固溶處理→酸洗→蘸涂層→拉拔φ3.55→去油→光亮退火蘸涂層→拉拔φ2.4→去油→光亮退火→蘸涂層→拉拔φ1.2→去油→涂潤滑油→打軸→檢驗→包裝入庫二、焊絲拉拔的材料條件2.1引述的材料成分單位統(tǒng)一為質(zhì)量%。未予特別描述的量、值單位符合行業(yè)一般規(guī)定和慣常用法,不予贅述。制備21-10mn7mo焊絲的拉拔方法,其中,21-10mn7mo盤條的化學(xué)成分質(zhì)量%應(yīng)滿足:碳c≤0.10、硅si≤0.8、錳mn5.5-8.0、磷p≤0.030、硫s≤0.020、鎳ni9.0-11.0、鉻cr19.0-22.0、鉬mo0.5-2.0,或/和余量為鐵fe和不可避免的雜質(zhì),或/和,mn/mo比控制在7-7.5之間。在此合理配置鉬、錳成分比的效果包括有效避免金屬錳在重熔過程容易燒損的問題。2.2具體描述金屬鉬、錳元素在不銹鋼中的作用,其他成分的作用為一般可知,不再贅述。2.2.1.金屬鉬mo元素的作用。a.鉬對不銹鋼的顯微組織及熱處理的作用鉬作為合金元素對鋼和其他合金有兩個重要的作用,即提高強度和耐腐蝕性。鉬在鋼中可固溶于鐵素體、奧氏體和碳化物中,它是縮小奧氏體相區(qū)的元素;具有細化鋼微觀晶粒而達到細晶強化的作用,當鉬含量較低時,與鐵、碳形成復(fù)合的滲碳體;含量較高時則形成它自己的高硬度特殊碳化物6-moc/mo2c,是鋼中的強化相;鉬提高鋼的淬透性,其作用較鉻強,而稍遜于錳;鉬提高鋼的回火穩(wěn)定性。作為單一合金元素存在時,增加鋼的回火脆性;與鉻或錳等并存時,鉬又降低或抑止因其他元素所導(dǎo)致的回火脆性。b.鉬對不銹鋼的力學(xué)性能的作用鉬對鐵素體有固溶強化作用,在不銹鋼中還能形成沉淀析出相,提高鋼的強度,同時也提高碳化物的穩(wěn)定性,從而提高鋼的強度;鉬對改善鋼的延展性和韌性以及耐磨性起到有利作用;由于鉬使形變強化后的軟化和恢復(fù)溫度以及再結(jié)晶溫度提高,并強烈提高鐵素體的蠕變抗力,有效抑制滲碳體在下的聚集,促進特殊碳化物的析出,因而成為提高鋼熱強性的特別有效的合金元素,鉬能改善奧氏體不銹鋼的高溫力學(xué)性能,比如持久、蠕變等性能均可獲較大改善。c.鉬對不銹鋼的物理化學(xué)及工藝性能的作用在還原性酸及強氧化性鹽溶液中都能使鋼表面鈍化,因此鉬可以普遍提高鋼的抗蝕性能,防止鋼在氯化物溶液中的點蝕;鉬含量較高(>3質(zhì)量%)時使鋼的抗氧化性惡化;含鉬不超過8質(zhì)量%的鋼仍可以鍛、軋,但含量較高時,鋼對熱加工的變形抗力增高。綜上可知,鉬是形成和穩(wěn)定鐵素體并擴大鐵素體相區(qū)的元素。但是,鉬的加入使鋼的高溫變形抗力增大,加之鋼中常常存在少量δ鐵素體因而含鉬不銹鋼的熱加工性比不含鉬鋼為差,而且鉬含量越高,熱加工性能越壞;鉬還促進奧氏體不銹鋼中金屬間相,比如σ相,κ相,和laves相等的沉淀,對鋼的耐蝕性和力學(xué)性能都會產(chǎn)生不利影響,特別是導(dǎo)致塑性,韌性下降。為使奧氏體不銹鋼保持單一的奧氏體組織,隨著鋼中鉬含量的增加,奧氏體形成元素的含量也要相應(yīng)提高,以保持鋼中鐵素體與奧氏體形成元素之間的平衡,因此本案在奧氏體不銹鋼中加鉬后,錳的含量也相應(yīng)提高。一般可知所述奧氏體形成元素是指鎳、氮、錳等。2.2.2金屬錳mn元素的控制錳對于奧氏體的作用與鎳相似。但錳的重要作用不在于形成奧氏體,而是在于它降低鋼的臨界淬火速度,在冷卻時增加奧氏體的穩(wěn)定性,抑制奧氏體的分解,使高溫下形成的奧氏體得以保持到常溫。在提高鋼的耐腐蝕性能方面,錳的作用不大,實驗表明,如鋼中的含錳量從0到10.4質(zhì)量%變化,也不能使鋼在空氣與酸中的耐腐蝕性能發(fā)生明顯的改變。還有,添加mn可以使更多的氮溶入奧氏體,而氮是強奧氏體形成元素,含0.25質(zhì)量%的氮,形成奧氏體的能力相當于7.5質(zhì)量%的鎳。提高焊絲中錳的含量,除了脫氧作用外,還能和硫化合生成了硫化錳(mns),并被除去(即:脫硫),故可降低由硫引起的熱裂紋的傾向,同時可以提高焊絲的強度。但錳的含量需要有效控制,錳的含量過高容易使材料凝固時或高溫使用過程中材料組織粗大,增加材料的脆性。2.3.本案21-10mn7mo與已有技術(shù)的材料化學(xué)成分質(zhì)量%對比,見表1。表1:兩種材料的化學(xué)成分試驗表明,適宜確定添加量,形成新合金,這樣的合金制成焊絲后,其強度會明顯提高。一般可知,鉬和錳的添加會給鍛造工序增加一定的困難。包括因由鉬和錳的添加使鋼的強度提高,塑性降低,由此,冷加工工序的加工變得更困難。三、焊絲拉拔中的蘸涂層工藝,鍛造處理后的鍛坯件處理形成熱軋盤條,進入具有蘸涂層處理的拉拔工藝單元。3.1蘸涂層工藝3.1.1涂層溶液的制備所述蘸涂層工藝引用的涂料較好的是以礦物鹽為基料的涂料,以礦物鹽為基料的涂料應(yīng)該能夠在金屬表面沉積形成晶體結(jié)構(gòu)層,也就是對盤條涂層形成潤滑載體,即蘸涂層,所述蘸涂層是借由所述礦物鹽基料在金屬表面沉積形成的一層粗糙而附著力強的晶體結(jié)構(gòu),由此可以有效提高潤滑材料在金屬表面的附著力。當水溫達到90℃時,按150-200克/升的比例將礦物鹽為基料的涂料溶入水中,并不斷攪拌至該涂料全部溶解。3.1.2.蘸涂層中的浸泡時間為5-6分鐘。3.1.3浸泡后烘干,烘干溫度120℃至150℃,烘干時間3小時以上。由此,一方面促使鋼絲表面形成載體粗膜,另一方面也可實現(xiàn)去除酸洗氫脆的技術(shù)效果。至此,鋼絲表面可形成一層粗糙、多孔、能吸附和攜帶潤滑粉(劑)的載體,拉絲時借助這層載體將拉絲粉(劑)帶入拉絲模具中,從而起到潤滑的作用。這種以礦物鹽為基料的涂料可以是市售品,或通過一般已有技術(shù)配制。3.1.4工藝要求:涂層要沾勻、粘牢、烘干、烘透。四、焊絲拉拔中的配模工藝,包括21-10mn7mo盤條的化學(xué)成分的確定,拉絲道次的確定,中間退火的確定,拉拔后絲材化學(xué)成分的確定,總減面率的確定,其中,制備21-10mn7mo焊絲優(yōu)選五聯(lián)罐拉絲機,參見圖1?!拔迓?lián)罐”是指配置五個模具裝置,實現(xiàn)五個道次的拉拔工藝。每個道次的拉拔都經(jīng)由模具裝置2-1至2-5,實現(xiàn)蘸涂層處理和拉拔。所述的五聯(lián)罐拉絲機,具有輸出線裝置1-1、回收線裝置1-2,完成絲材的收放。在輸出線裝置和回收線裝置之間依次配置第一模具裝置2-1、第二模具裝置2-2、第三模具裝置2-3、第四模具裝置2-4、第五模具裝置2-5。所述五聯(lián)罐拉絲機上配置導(dǎo)向機構(gòu)和張力機構(gòu),用于實現(xiàn)引導(dǎo)絲材從輸出線裝置平穩(wěn)導(dǎo)向各個模具裝置,這可以按一般已有技術(shù),不予贅述。參見圖1,相鄰的模具裝置之間設(shè)置拉絲機構(gòu)3,各個模具裝置的輸入端2-n-1配置導(dǎo)向機構(gòu)2-n-14,相鄰的模具裝置之間,模具裝置的輸入端2-n-1,配置張力機構(gòu)2-n-15。這可以按一般已有技術(shù),不予贅述。各個模具裝置的輸出端2-n-2,配置拉絲模具單元2-n-26;模具裝置的輸出端2-n-2與模具裝置的輸入端2-n-1之間設(shè)置拉絲潤滑單元2-n-3,所述的拉絲潤滑單元具有容絲材通過的第一進料孔2-n-31和第二進料孔2-n-32,第一進料孔2-n-31位于模具裝置輸入端一側(cè),第二進料孔2-n-32的模具裝置輸出端一側(cè),該第一進料孔2-n-31和第二進料孔2-n-32之間是容置潤滑劑的工作槽2-n-30,為進入模具裝置的絲材提供潤滑劑;所述的拉絲模具單元2-n-26具有冷卻槽2-n-260,用于為模具提供冷卻水;拉絲模具主體2-n-261借由拉絲模具活套2-n-262的裝置在冷卻槽中;拉絲模具活套負責(zé)頂持拉絲模具主體,不偏不倚。至此經(jīng)過拉拔單元處理的絲材構(gòu)造借此實現(xiàn)。4.1潤滑劑選擇所述的潤滑劑可以是市售的,優(yōu)選的是干式鈉基潤滑劑。所述鈉基潤滑劑配合前述以礦物鹽為基料的蘸涂層涂料。由此潤滑的措施使得絲材表面形成鈉基潤滑膜的層構(gòu)造,與所述蘸涂層的工藝形成的潤滑載體層構(gòu)造形成重要匹配。由此進一步可有效提高潤滑材料在金屬表面的附著力。在被拉絲材與拉絲模具之間形成更好效果的潤滑膜,且殘余潤滑膜更容易清洗。不僅如此,由于21-10mn7mo焊絲強度高、壓下量大,引用鈉基潤滑劑配合以礦物鹽為基料的涂料涂層使用,經(jīng)拉拔后的絲材可以實現(xiàn)以下指標:當熔程為220℃~260℃,拔制速度為150m/min,抗拉強度≥1200mpa時,絲材表面性能依然良好,可實現(xiàn)總減面率≥75%。4.1.1拉拔單元的絲材的結(jié)構(gòu)至此形成拉拔單元的絲材4-1的結(jié)構(gòu),它包括21-10mn7mo絲材本體,其中,絲材本體的化學(xué)成分質(zhì)量%應(yīng)滿足:碳c≤0.10、硅si≤0.8、錳mn5.5-8.0、磷p≤0.030、硫s≤0.020、鎳ni9.0-11.0、鉻cr19.0-22.0、鉬mo0.5-2.0,或/和余量為鐵fe和不可避免的雜質(zhì),或/和,mn/mo比控制在7-7.5之間。參見圖3絲材本體4-1-0外表面為潤滑膜層4-1-2,所述的潤滑膜層為鈉基潤滑劑形成的膜,在絲材本體表面與潤滑膜層之間具有蘸涂層4-1-1,所述的蘸涂層是借由礦物鹽基料在絲材本體表面形成的一層粗糙、多孔、能吸附和攜帶潤滑材料的載體層。4.2配模工藝每次拉拔的道次設(shè)置為五次,以直徑5.5毫米盤條為例描述拉絲配模的設(shè)置為如下,直徑單位:毫米。第一次拉拔:將預(yù)設(shè)直徑尺寸的盤條依次經(jīng)過固溶處理、酸洗處理、蘸涂層處理、拉拔,第一次拉拔處理的總減面率為56%,由此獲得預(yù)設(shè)直徑尺寸的第一道絲材。φ5.5-φ4.9-φ4.41-φ4.04-φ3.80-φ3.65(光亮退火)總減面率56%。第二次拉拔:將第一道絲材依次經(jīng)過去油處理、光亮退火處理、蘸涂層處理、第二次拉拔處理,拉拔的總減面率為57%,由此獲得預(yù)設(shè)直徑尺寸的第二道絲材。φ3.65-φ3.2-φ2.93-φ2.68-φ2.52-φ2.4(光亮退火)總減面率57%第三次拉拔:將第二道絲材依次經(jīng)過去油處理、光亮退火處理、蘸涂層處理、第三次拉拔處理,拉拔的總減面率為75%,由此獲得預(yù)設(shè)直徑尺寸的第三道絲材。φ2.4-φ2.06-φ1.79-φ1.55-φ1.35-φ1.2總減面率75%。4.2.1具體描述見圖1-1a,擇要描述每次拉拔中五個道次完成對絲材的拉拔的變形過程:將預(yù)設(shè)直徑尺寸的絲材從放線裝置1-1輸出,絲材通過第一模具裝置2-1,完成絲材從第一次拉拔的φ5.5mm或第二次拉拔的φ3.65mm或第三次拉拔的φ2.4mm到第一次拉拔的φ4.9mm或第二次拉拔的φ3.2mm或第三次拉拔的φ2.06mm的第一次減徑;第一次減徑后的絲材經(jīng)過模具裝置與模具裝置之間的拉絲機構(gòu)和導(dǎo)向機構(gòu)、張力機構(gòu)的矯正,定位導(dǎo)入第二模具裝置;絲材通過第二模具裝置,完成絲材從φ4.9mm或φ3.2mm或φ2.06mm到φ4.41mm或2.93mm或1.79mm的第二次減徑;……以此類推,當絲材經(jīng)過第五模具裝置時,完成絲材從φ3.80mm或φ2.52mm或φ1.35mm到φ3.65mm或φ2.4mm或φ1.2mm的第五次減徑,最后纏繞在回收線裝置1-2上面的絲材的直徑符合預(yù)設(shè)值。每一次拉拔,經(jīng)過5道次拉拔后,再經(jīng)過去油、去除絲材表面殘余的涂層及潤滑劑;再光亮退火,以消除加工硬化,提高絲材的塑性,絲材的總減面率符合預(yù)設(shè)值;然后再在絲材表面蘸上涂層進行下一次拉拔。由此拉絲配模的設(shè)置結(jié)合本案提供的蘸涂層工藝可有效提高絲材拉拔效果,而且絲材在拉拔過程中,可有效形成潤滑層,持續(xù)保持絲材表面的潤滑情況,為焊絲表面質(zhì)量提供保障。所述的模具裝置,具有潤滑劑槽2-n-13本案21-10mn7mo焊絲用途在于裝甲鋼或合金鋼或調(diào)質(zhì)鋼或異種鋼的焊接,包括裝甲鋼或合金鋼或調(diào)質(zhì)鋼或異種鋼的自動化焊接、半自動化焊接。五、本案21-10mn7mo焊絲與已有焊絲的性能比較5.1在化學(xué)成分及力學(xué)性能方面的比較21-10mn7mo不銹鋼焊絲是在已有焊絲h1cr21ni10mn6的基礎(chǔ)上添加mo和mn研制而成。加入mo后,在去除金屬焊接損耗的基礎(chǔ)上保證了焊絲的熔敷金屬成分和焊條焊接時熔敷金屬的一致性。同時金屬鉬還可以細化晶粒、提高再結(jié)晶溫度、顯著改善了鋼的韌性、高溫強度和蠕變性能。因此鉬便成為耐熱、耐蝕的各種結(jié)構(gòu)鋼的重要組分;提高焊絲中錳的含量,除了脫氧作用外,還能和硫化合生成硫化錳(mns),并被除去(脫硫)故可降低由硫引起的熱裂紋的傾向。兩種焊絲的化學(xué)成分見下表6表6兩種焊絲的化學(xué)成分一般可知,自動或半自動焊接對于焊絲的強度要求較高,如焊絲強度過低會或過高,在焊接送絲過程中或出現(xiàn)斷絲或出現(xiàn)打死彎等現(xiàn)象,導(dǎo)致焊接時送絲不順暢。21-10mn7mo焊絲有效提高了焊絲的強度,滿足自動或半自動焊接的要求。兩種焊絲力學(xué)性能比較見表7。表7兩種焊絲力學(xué)性能的比較表7說明本案21-10mn7mo焊絲的力學(xué)性能明顯優(yōu)越。5.2熔敷金屬的力學(xué)性能比較一般可知,焊絲用于母材力學(xué)性能較高的材料時,如裝甲鋼,焊絲的熔敷金屬的力學(xué)性能要求也相應(yīng)提高。由于本案焊絲應(yīng)用于裝甲鋼的焊接,因此對熔敷金屬的力學(xué)性能要求也比較高,焊絲用于裝甲鋼的熔敷金屬的力學(xué)性能指標要求,見表8。表8:抗拉強度σb(mpa)延伸率δ5(%)常溫沖擊功akv(j)≥550≥25≥7221-10mn7mo焊絲的熔敷金屬的力學(xué)性能能夠滿足上述要求,已有焊絲與本案21-10mn7mo焊絲熔敷金屬的力學(xué)性比較,見表9。實驗條件:焊絲焊接試驗采用不銹鋼富氬混合氣體保護焊接。表9:熔敷金屬的力學(xué)性能比較表9說明,本案抗拉強度和常溫沖擊功比已有技術(shù)的指標都明顯提高。5.3常溫斜y型坡口焊接裂紋試驗在焊接熱循環(huán)的作用下,焊縫及熱影響區(qū)金屬由于組織、性能發(fā)生變化,內(nèi)應(yīng)力作用及擴散氫的影響,主要焊接缺陷是可能發(fā)生冷裂紋。目前廣泛用于評價焊縫金屬及熱影響區(qū)冷裂紋傾向的試驗方法,依據(jù)現(xiàn)用中國國家標準,用斜y型坡口焊接裂紋試驗法,通過計算表面裂紋和斷面裂紋率來衡量裂紋傾向。焊接條件:使用焊絲21-10mn7mo和h1cr21ni10mn6;焊絲直徑ф1.2mm;焊接電流120-140a;焊接電壓20-24v;焊接速度150-200mm/min;保護氣體95%ar+5%co2;氣體流量15-20l/min;直流反接,環(huán)境溫度20℃。焊接設(shè)備:市售氣保焊機。試樣制備及試驗方法:試件坡口以機械加工,參見圖4形狀及尺寸組焊。焊后48小時,觀察兩種焊絲用同種焊接工藝焊接同種材料的表面裂紋率和斷面裂紋率,試驗結(jié)果見下表10。表10說明,對于焊接高硬度的675鋼和中硬度的603鋼,兩種焊絲的表面裂紋率水平相當,但是在斷面裂紋率方面,本案21-10mn7mo焊絲要明顯優(yōu)于已有的h1cr21ni10mn6焊絲。表105.4.對接接頭力學(xué)性能試驗對比用兩種焊絲分別對高硬度鋼675和685鋼進行對接接頭焊接,板厚為45mm和5mm。焊接工藝:焊接電流:120-140a,焊接電壓:20-24v,焊接速度:150-200mm/min,保護氣體:95%ar+5%co2;氣體流量15-20l/min;并取沖擊試樣進行對比,試驗結(jié)果見下表11.表11表11說明,兩種焊絲焊接675鋼時,焊縫處的沖擊性能相當,但是熱影響區(qū)的沖擊性能本案21-10mn7mo焊絲明顯優(yōu)于已有的h1cr21ni10mn6焊絲;焊接685鋼時,無論是熱影響區(qū)還是焊縫處的沖擊性能都是21-10mn7mo焊絲明顯優(yōu)于h1cr21ni10mn6焊絲。5.5用兩種焊絲對685鋼對接接頭焊縫、熱影響區(qū)、母材的金相組織的比較。圖5a-5d是21-10mn7mo焊接685鋼的焊縫及熱影響區(qū)的金相組織,圖5a為焊接的融合線,融合線左邊為熱影響區(qū),融合線右邊為焊縫。圖5b為熱影響區(qū)組織為粗大的馬氏體+貝氏體+殘余奧氏體。圖5c為母材的金相組織,為回火索氏體。圖5d為焊縫區(qū)的金相組織,為奧氏體+鐵素體。圖6a-6dh1cr21ni10mn6焊接685鋼的焊縫及熱影響區(qū)的金相組織,圖6a為焊接的融合線,融合線左邊為熱影響區(qū),融合線右邊為焊縫。圖6b為熱影響區(qū)組織為粗大的馬氏體+貝氏體+殘余奧氏體。圖6c為母材的金相組織,為回火索氏體。圖6d為焊縫區(qū)的金相組織,為奧氏體+鐵素體。由圖5a-5d和圖6a-6d可以看出兩種焊絲焊接的各部位的金相組織基本相同。只是用h1cr21ni10mn6焊接的熱影響區(qū)的馬氏體組織更粗大些,焊縫的組織中有少量尺寸較大的夾雜物。而用21-10mn7mo焊絲焊接的焊縫的晶粒更細小些。5.6機器人適應(yīng)性試驗5.6.1試驗條件:使用焊絲21-10mn7mo,焊絲直徑ф1.2mm,焊接電流140-180a,焊接電壓20-24v,焊接速度150-200mm/min,保護氣體95%ar+5%co2;氣體流量15-20l/min,焊接設(shè)備選擇市售的全自動焊接機。5.6.2試驗方法:焊接603鋼板厚度45mm和g4鋼板厚度15mm各1對,對接焊接,焊接時記錄焊接參數(shù)、送絲狀態(tài)、飛濺情況、電弧穩(wěn)定性、焊縫成形及焊絲表面狀態(tài)。5.6.3試驗結(jié)論:(1)焊接參數(shù)在給定的焊接條件范圍中,即與h1cr21ni10mn6焊絲所使用的焊接參數(shù)相同。(2)送絲狀態(tài)均勻穩(wěn)定無抖動。(3)焊接過程中飛濺小、煙塵量較低,優(yōu)于使用h1cr21ni10mn6焊絲。(4)焊縫成形良好、焊絲表面光滑、無毛刺、凹坑、劃痕等缺陷。焊縫的外形如下圖7所示。在詳細說明的較佳實施例之后,熟悉該項技術(shù)人士可清楚的了解,在不脫本案所述申請專利范圍與精神下可進行各種變化與修改,且本發(fā)明亦不受限于說明書中所舉實施例的實施方式。當前第1頁12