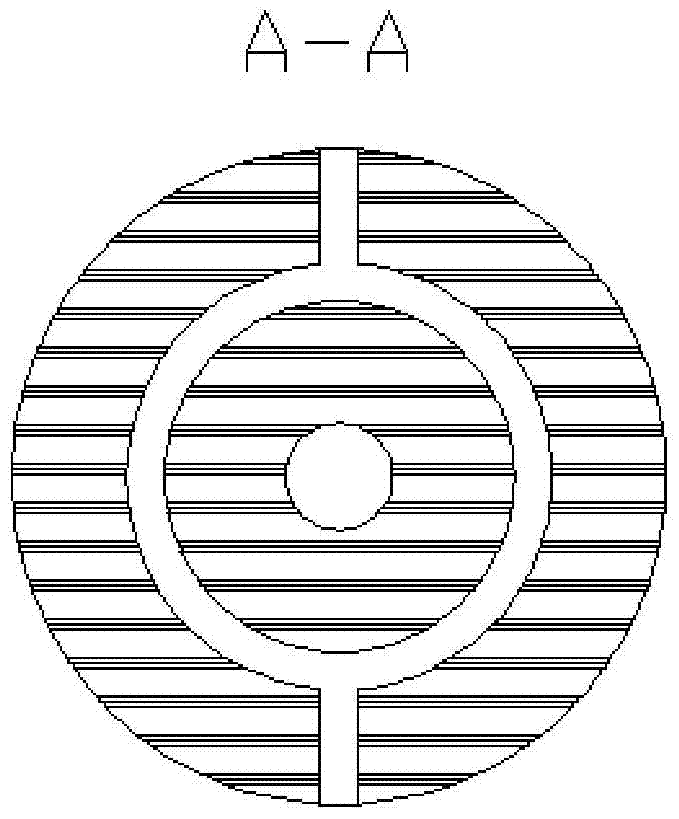
一種加熱-拉絲-精拉整形-冷卻的絲材制備方法技術(shù)領(lǐng)域本發(fā)明屬于絲材制備技術(shù)領(lǐng)域,具體為一種加熱-拉絲-精拉整形-冷卻的絲材制備方法和裝置,適用于高強難拉焊絲和金屬導(dǎo)線等絲材的生產(chǎn)。
背景技術(shù):高強焊絲在拉拔過程中,由于其強度硬度高,容易發(fā)生脆斷、粗細不均、損壞擠壓模等問題。同時需要多次的拉拔,才能獲得一定直徑的焊絲,生產(chǎn)效率低下。而本發(fā)明可提供感應(yīng)加熱和精拉整形功能,可在短時間內(nèi)將棒材加熱至所需溫度,提高棒材的塑韌性,也減小了桿材對擠壓模的摩擦破壞,提高了拉絲效率和表面成形質(zhì)量。金屬導(dǎo)線,如銅桿和鋁桿在拉絲機上拉拔的過程中,會發(fā)生硬化、變脆,為了恢復(fù)單絲的塑性,保持良好的電氣性能,因此需要將線材在一定的溫度下進行熱處理即退火處理。目前常見的退火拉絲機的退火設(shè)備主要由退火罐、加熱絲等組成,它通過把單絲放置在一個加熱的容器內(nèi)達到退火的目的,該設(shè)備的主要優(yōu)點是設(shè)備簡單、易維護,缺點是耗電大、單絲性能不穩(wěn)定,退火周期長、效率低。而本發(fā)明提供的裝置具有加熱和冷卻功能,可以實現(xiàn)拉拔與組織控制一體化的功能。查閱現(xiàn)有的焊絲及導(dǎo)線等絲材制造技術(shù),大多采用分步加熱、拉絲、整形、熱處理等措施,來保證獲得高質(zhì)量的焊絲和導(dǎo)線等絲材,并沒有發(fā)現(xiàn)具有集原位加熱-拉絲-精拉整形-冷卻功能于一體的方法及裝置。而本發(fā)明提供了一種集感應(yīng)加熱、拉絲、精拉整形、組織控制等功能于一體的高質(zhì)高效的絲材制備方法與裝置,可用于高強難拉焊絲和金屬導(dǎo)線等絲材產(chǎn)品的生產(chǎn)。
技術(shù)實現(xiàn)要素:本發(fā)明的目的是提出了一種加熱-拉絲-精拉整形-冷卻的絲材制備方法,適用于高強難拉焊絲和金屬導(dǎo)線等絲材的生產(chǎn)。本發(fā)明的技術(shù)方案為:一種加熱-拉絲-精拉整形-冷卻的絲材制備裝置,在拉絲方向依次設(shè)置第一密封圈、感應(yīng)加熱機構(gòu)、拉絲模具、精拉整形處理機構(gòu)、冷卻機構(gòu)以及第二密封圈;所述的感應(yīng)加熱機構(gòu)包括陶瓷基體與感應(yīng)線圈,感應(yīng)線圈埋置在陶瓷基體上,所述的陶瓷基體內(nèi)設(shè)有第一保護氣槽,所述的冷卻機構(gòu)中設(shè)有保護第二氣槽。所述的感應(yīng)加熱線圈區(qū)域為加熱區(qū)域,所述的拉絲模具區(qū)域為拉絲變形區(qū)域,所述的精拉整形處理機構(gòu)區(qū)域為表面修復(fù)整形區(qū)域,所述的冷卻機構(gòu)區(qū)域為冷卻控溫區(qū)域。如上所述的感應(yīng)線圈與陶瓷基體的內(nèi)側(cè)之間鋪置絕熱綿。如上所述的保護氣槽的氣體流通方向為由外向內(nèi)。如上所述的冷卻機構(gòu)中也設(shè)有保護氣槽對打磨后的絲材冷卻過程提供氣體保護。如上所述的拉絲模具中設(shè)有冷卻水槽。如上所述的精拉整形處理機構(gòu)為管狀結(jié)構(gòu),其內(nèi)徑和拉絲模具出口端直徑相等;精拉整形處理機構(gòu)需經(jīng)淬火處理增加表面耐磨性;精拉整形處理機構(gòu)工作時,與拉絲模具配合,拉絲模具將絲材在圓周方向固定,精拉整形處理機構(gòu)旋轉(zhuǎn),對拉完的絲材進行整形修復(fù)處理。一種基于加熱-拉絲-精拉整形-冷卻的絲材裝置的制備方法,其特征在于,包括具體步驟如下:第一步,根據(jù)待拉絲材的直徑Φ0和目標(biāo)絲材的直徑Φ目標(biāo),選擇孔徑為Φ1,Φ2、Φ3,……,Φn的拉絲模具和精拉整形機構(gòu),其中Φ0>Φ1>Φ2>Φ3>……>Φn=Φ目標(biāo),且Φi—Φi+1≤ξ·Ψ·Φi,i=0,1,2…n-1,其中ξ為常數(shù),為0.2~0.6,Ψ為材料斷面收縮率,n為拉絲次數(shù);第二步,待拉絲材進入感應(yīng)加熱線圈區(qū)域,調(diào)節(jié)感應(yīng)加熱電流,將待拉絲材加熱至預(yù)熱溫度區(qū)間;感應(yīng)加熱機構(gòu)內(nèi)的保護氣槽通入保護氣;第三步,預(yù)熱后的待拉絲材進入拉絲模具,拉壓成Φ1的絲材,同時拉絲模具中通有冷卻水;第四步,拉壓處理后的絲材進入精拉整形處理機構(gòu),與拉絲模具配合,拉絲模具將絲材在圓周方向固定,精拉整形處理機構(gòu)旋轉(zhuǎn),對拉完的絲材進行整形修復(fù)處理;第五步,精拉整形處理后的絲材進入冷卻機構(gòu)。在冷卻機構(gòu)中的水冷槽和氣保槽分別通入冷卻水和保護氣,將精拉整形處理后的絲材冷卻至室溫后拉出冷卻裝置;第六步,將冷卻后直徑為Φ1絲材依次進入直徑為Φ2、Φ3…、Φ目標(biāo)的拉絲模具和精拉整形處理機構(gòu)的拉絲機構(gòu)中,重復(fù)上述步驟,最終獲得直徑為Φ目標(biāo)的絲材或線材精拉整形處理機構(gòu)工作時,與拉絲模具配合,拉絲模具將絲材在圓周方向固定,精拉整形處理機構(gòu)旋轉(zhuǎn),對拉完的絲材進行整形修復(fù)處理。第二步中,保護氣流速為10L/min~35L/min。第五步中,保護氣流速為10L/min~35L/min。其中,預(yù)熱溫度區(qū)間為待拉絲材的塑性溫度的20%至50%。本發(fā)明提供的方法及裝置還可以對棒材進行拉絲。本發(fā)明相對于現(xiàn)有技術(shù)相比具有如下顯著優(yōu)點:1)該裝置采用非接觸式的高頻感應(yīng)加熱方法加熱待拉棒材(或絲材),可以在短時間內(nèi)將待拉棒材(或絲材)加熱至一定溫度以提高其塑性,避免長時間加熱引起待拉棒材(或絲材)晶粒長大造成性能下降的影響。2)陶瓷感應(yīng)加熱機構(gòu)中靠陶瓷環(huán)內(nèi)側(cè)安置有保護氣槽,可以提供氣體保護,且保護氣槽的流通方向為由外向內(nèi),由于熱焊絲的熱輻射作用,可以預(yù)熱保護氣,提高保護氣的分壓和在加熱腔里的停留時間。3)拉絲模具中安設(shè)有冷卻水槽,可以及時降低拉絲模具的溫度,避免由于溫度過高出現(xiàn)粘刀的問題。4)冷卻機構(gòu)中也設(shè)有保護氣槽對整形修復(fù)后的絲材進行冷卻處理,同時可以提供氣體保護,避免了未冷卻到較低溫度而被空氣氧化的情況。對于在加熱拉拔過程中易逸出合金元素的絲材,可通入對應(yīng)保護氣體增大其分壓,減少加熱拉拔過程中絲材中合金元素的逸出。5)本發(fā)明提供了的一種集感應(yīng)加熱、拉絲、精拉整形、組織控制等功能于一體的高質(zhì)高效的絲材制備方法與裝置,可用于高強難拉焊絲和金屬導(dǎo)線等絲材產(chǎn)品的生產(chǎn),生產(chǎn)效率高,且棒材或絲材成型及性能好。附圖說明圖1是本發(fā)明的結(jié)構(gòu)示意圖。圖2是拉絲模具6沿A-A的截面圖。其中,1a-待拉絲材,2-第一密封圈,3-第一保護氣槽,4-陶瓷基體,5-感應(yīng)線圈,6-拉絲模具,7-精拉整形處理構(gòu)件,8-冷卻機構(gòu),9-第二保護氣槽,10-第二密封圈,1b-拉完的絲材。具體實施方式下面結(jié)合附圖對本發(fā)明作進一步的描述。以下實例僅用于更加清楚地說明本發(fā)明的技術(shù)方案,而不能以此來限制本發(fā)明的保護范圍。如圖1所示,本發(fā)明提供了一種加熱-拉絲-精拉整形-冷卻的絲材制備裝置:在拉絲方向依次設(shè)置第一密封圈2、感應(yīng)加熱機構(gòu)、拉絲模具6、精拉整形處理機構(gòu)7、冷卻機構(gòu)8以及第二密封圈10;所述的感應(yīng)加熱機構(gòu)包括陶瓷基體4與感應(yīng)線圈5,感應(yīng)線圈5埋置在陶瓷基體4上,所述的陶瓷基體4內(nèi)設(shè)有第一保護氣槽3,所述的冷卻機構(gòu)中設(shè)有第二保護氣槽9。所述的感應(yīng)線圈5與陶瓷基體4的內(nèi)側(cè)之間鋪置絕熱綿。所述的保護氣槽的氣體流通方向為由外向內(nèi)。冷卻機構(gòu)8中也設(shè)有保護氣槽對打磨后的絲材冷卻過程提供氣體保護。所述的拉絲模具6中設(shè)有冷卻水槽。精拉整形處理機構(gòu)7為管狀結(jié)構(gòu),其內(nèi)徑和拉絲模具出口端直徑相等;所述的精拉整形處理機構(gòu)7經(jīng)淬火處理增加表面耐磨性實施例一高氮鋼絲材的生產(chǎn)采用一種基于加熱-拉絲-精拉整形-冷卻的絲材裝置的制備方法生產(chǎn)高氮鋼絲材,包括具體步驟如下:第一步,根據(jù)待拉絲材的直徑Φ0和目標(biāo)絲材的直徑Φ目標(biāo),選擇孔徑為Φ1,Φ2、Φ3,……,Φn的拉絲模具和精拉整形機構(gòu),其中Φ0>Φ1>Φ2>Φ3>……>Φn=Φ目標(biāo),且Φi—Φi+1≤ξ·Ψ·Φi,(i=0,1,2…n-1),其中ξ為常數(shù),一般取0.2~0.6,Ψ為材料斷面收縮率,n為拉絲次數(shù)。高氮鋼預(yù)熱溫度區(qū)間為300℃~500℃,選用氮氣作為保護氣。根據(jù)待拉絲材種類確定預(yù)熱溫度區(qū)間和通保護氣的種類及通氣速率,對于在加熱拉拔過程中易逸出合金元素(如氮元素)的絲材,可通入對應(yīng)保護氣體增大其分壓,減少加熱拉拔過程中絲材中合金元素的逸出。第二步,待拉絲材進入感應(yīng)加熱區(qū)域,調(diào)節(jié)感應(yīng)加熱電流,將待拉絲材加熱至300℃~500℃;感應(yīng)加熱機構(gòu)內(nèi)的保護氣槽通入氮氣保護氣,保護氣流速一般為10L/min~35L/min。第三步,預(yù)熱后的待拉絲材進入拉絲模具,拉壓成Φ1的絲材,同時拉絲模具中通有冷卻水;第四步,拉壓處理后的絲材進入精拉整形處理機構(gòu),與拉絲模具配合,拉絲模具將絲材在圓周方向固定,精拉整形處理機構(gòu)旋轉(zhuǎn),對拉完的絲材進行整形修復(fù)處理。第五步,精拉整形處理后的絲材進入冷卻機構(gòu)。在冷卻機構(gòu)中的水冷槽和氣保槽分別通入冷卻水和氮氣保護氣,氮氣保護氣流速為10L/min~35L/min,將精拉整形處理后的絲材冷卻至室溫后拉出冷卻裝置;第六步,拉出的直徑為Φ1的絲材依次進入直徑為Φ2、Φ3…、Φ目標(biāo)的拉絲模具和精拉整形處理機構(gòu)的拉絲機構(gòu)中,重復(fù)上述步驟,最終獲得直徑為Φ目標(biāo)的高氮鋼絲材或線材。實施例二銅導(dǎo)線的生產(chǎn)與實例一不同是銅導(dǎo)線在拉絲過程中,對溫度的控制要求比較高。同時,所需的保護氣也不同,此處用氬氣作為保護氣。采用一種基于加熱-拉絲-精拉整形-冷卻的絲材裝置的制備方法生產(chǎn)銅導(dǎo)線,包括具體步驟如下:第一步,根據(jù)待拉絲材的直徑Φ0和目標(biāo)絲材的直徑Φ目標(biāo),選擇孔徑為Φ1,Φ2、Φ3,……,Φn的拉絲模具和精拉整形機構(gòu),其中Φ0>Φ1>Φ2>Φ3>……>Φn=Φ目標(biāo),且Φi—Φi+1≤ξ·Ψ·Φi,(i=0,1,2…n-1),其中ξ為常數(shù),一般取0.2~0.6,Ψ為材料斷面收縮率,n為拉絲次數(shù)。銅絲材預(yù)熱溫度區(qū)間為60℃~100℃,選用氬氣作為保護氣。第二步,待拉絲材進入感應(yīng)加熱區(qū)域,調(diào)節(jié)感應(yīng)加熱電流,將待拉絲材加熱至300℃~500℃;感應(yīng)加熱機構(gòu)內(nèi)的保護氣槽通入氬氣保護氣,保護氣流速一般為10L/min~35L/min。第三步,預(yù)熱后的待拉絲材進入拉絲模具,拉壓成Φ1的絲材,同時拉絲模具中通有冷卻水;第四步,拉壓處理后的絲材進入精拉整形處理機構(gòu),與拉絲模具配合,拉絲模具將絲材在圓周方向固定,精拉整形處理機構(gòu)旋轉(zhuǎn),對拉完的絲材進行整形修復(fù)處理。第五步,精拉整形處理后的絲材進入冷卻機構(gòu)。在冷卻機構(gòu)中的水冷槽和氣保槽分別通入冷卻水和氬氣保護氣,氬氣保護氣流速一般為10L/min~35L/min,將精拉整形處理后的棒材或絲材冷卻至室溫后拉出冷卻裝置;第六步,拉出的直徑為Φ1絲材依次進入直徑為Φ2、Φ3…、Φ目標(biāo)的拉絲模具和精拉整形處理機構(gòu)的拉絲機構(gòu)中,重復(fù)上述步驟,最終獲得直徑為Φ目標(biāo)的銅導(dǎo)線。