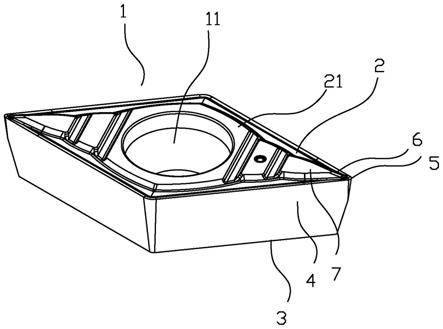
1.本發(fā)明涉及刀具技術(shù)領(lǐng)域,特別是涉及一種小零件加工用車削刀片。
背景技術(shù):2.刀具是機(jī)械制造中用于切削加工的工具,又稱切削工具。刀具的種類繁多,有用于加工各種外表面的刀具,用于孔加工的刀具,用于螺紋加工的刀具,用于齒輪加工的刀具,用于切斷的刀具等等。車削刀片是一種對(duì)旋轉(zhuǎn)的工件進(jìn)行車削加工的刀具,小直徑零部件是3c、汽車、醫(yī)療、液壓等行業(yè)的典型工件,在3c、醫(yī)療行業(yè),小直徑零部件是屬于高精密、小尺寸產(chǎn)品,對(duì)產(chǎn)品尺寸精度和表面質(zhì)量要求異常高,加工時(shí)往往采用小進(jìn)給小切深工況,且加工難度大,故對(duì)刀具性能提出更高的要求。
3.現(xiàn)階段刀具大部分采用高強(qiáng)度三維槽設(shè)計(jì)或是二維槽設(shè)計(jì)。高強(qiáng)度三維槽設(shè)計(jì)帶有刃寬及大容屑槽,以增強(qiáng)刀具的強(qiáng)度和大切深時(shí)降低切削阻力,難以滿足小直徑零部件在小切深,小進(jìn)給工況下的排屑及斷屑要求。而二維槽設(shè)計(jì)的容屑槽結(jié)構(gòu)簡(jiǎn)單,難以滿足小直徑零部件變切深工況下的排屑及斷屑要求。眾所周知,若是排屑良好,鐵屑可以帶走加工時(shí)產(chǎn)生大部分熱量,降低切削熱對(duì)刀具影響,延緩刀具的磨損。良好的斷屑,可以防止切屑纏繞或者由激烈振動(dòng)造成刀具損傷,滿足自動(dòng)化加工需求。因此,設(shè)計(jì)一種能夠?qū)崿F(xiàn)小直徑工件的小切深、小進(jìn)給穩(wěn)定加工的小零件車削刀片成了急迫需要解決的問(wèn)題。
技術(shù)實(shí)現(xiàn)要素:4.本發(fā)明的目的在于克服現(xiàn)有技術(shù)之不足,提供一種小零件加工用車削刀片,通過(guò)在容屑槽里設(shè)計(jì)特定的凸起結(jié)構(gòu),來(lái)保證足夠的容屑空間同時(shí)增強(qiáng)刀具的鋒利性,加強(qiáng)其對(duì)切屑的作用,能夠?qū)崿F(xiàn)在小型零部件的小進(jìn)給小切深加工及切深變化時(shí)能夠?qū)η行歼M(jìn)行有效地控制,從而提高刀具壽命以及工件表面質(zhì)量。
5.本發(fā)明解決其技術(shù)問(wèn)題所采用的技術(shù)方案是:一種小零件加工用車削刀片,包括刀片本體;所述刀片本體的輪廓投影為多邊形形狀;所述刀片本體具有上表面、下表面和連接在上、下表面之間的側(cè)面;所述刀片本體的中部設(shè)有貫穿上、下表面的螺釘鎖接孔;所述刀片本體的各個(gè)角部中,至少有一個(gè)角部為銳角,在刀片本體的銳角角部中,所述上表面與所述側(cè)面相交形成切削刃;所述切削刃包括對(duì)應(yīng)于角尖處的圓弧切削刃和與圓弧切削刃的兩邊相接的線段切削刃;所述上表面中,由所述切削刃向刀片本體的中部方向,沿斜向下方向延伸形成前刀面;在對(duì)應(yīng)于圓弧切削刃,由前刀面向刀片本體的中部方向順序設(shè)有圓臺(tái)形狀的第一凸起和倒v形狀的第二凸起,且第一凸起和第二凸起分別沿著所述刀片本體的銳角角部的角平分線為對(duì)稱結(jié)構(gòu);所述第一凸起和第二凸起分別包括頂面和側(cè)面;所述第一凸起的頂面位置高于所述圓弧切削刃的位置,所述第二凸起的頂面位置高于所述第一凸起的頂面位置。
6.所述第一凸起的頂面為平面,并平行于所述下表面;所述第一凸起的側(cè)面為曲面。
7.所述第一凸起的頂面位置與所述圓弧切削刃的位置之間的高度差為0.025mm~
0.065mm;沿著所述刀片本體的銳角角部的角平分線方向,所述第一凸起的頂面與所述圓弧切削刃的最小距離為0.2mm~1mm。
8.所述第二凸起的頂面為平面,并平行于所述下表面;所述第二凸起的側(cè)面為曲面。
9.所述第二凸起的頂面位置與所述圓弧切削刃的位置之間的高度差為0.1mm~0.3mm;所述第一凸起的側(cè)面與下表面之間的夾角大于所述第二凸起的側(cè)面與下表面之間的夾角。
10.沿著所述刀片本體的銳角角部的角平分線方向,所述第一凸起的側(cè)面平緩過(guò)渡至所述第二凸起的側(cè)面;所述第二凸起的側(cè)面的長(zhǎng)度大于所述第一凸起的側(cè)面的長(zhǎng)度。
11.從垂直于所述線段切削刃的方向,所述線段切削刃到所述第二凸起的側(cè)面的距離大于位于所述線段切削刃到所述第一凸起的側(cè)面的距離。
12.所述圓弧切削刃的前刀面相對(duì)于下表面的傾斜角度為α,且2
°
≤α≤4
°
;所述線段切削刃的前刀面相對(duì)于下表面的傾斜角度為β,且5
°
≤β≤9
°
。
13.所述刀片本體的輪廓投影為菱形形狀,且在刀片本體的菱形形狀的四個(gè)角部中,有兩個(gè)角部為銳角。
14.所述側(cè)面相對(duì)于所述下表面的垂直面為斜面,且所述側(cè)面由上向下呈漸次向內(nèi)傾斜。
15.與現(xiàn)有技術(shù)相比較,本發(fā)明的有益效果是:
16.本發(fā)明由于采用了刀片本體的上表面中,由所述切削刃向刀片本體的中部方向,沿斜向下方向延伸形成前刀面;在對(duì)應(yīng)于圓弧切削刃,由前刀面向刀片本體的中部方向順序設(shè)有圓臺(tái)形狀的第一凸起和倒v形狀的第二凸起,且第一凸起和第二凸起分別沿著所述刀片本體的銳角角部的角平分線為對(duì)稱結(jié)構(gòu);所述第一凸起和第二凸起分別包括頂面和側(cè)面;所述第一凸起的頂面位置高于所述圓弧切削刃的位置,所述第二凸起的頂面位置高于所述第一凸起的頂面位置。本發(fā)明通過(guò)在容屑槽里設(shè)計(jì)特定的凸起結(jié)構(gòu)(即第一凸起和第二凸起),來(lái)保證足夠的容屑空間同時(shí)增強(qiáng)刀具的鋒利性,加強(qiáng)其對(duì)切屑的作用,能夠?qū)崿F(xiàn)在小型零部件的小進(jìn)給小切深加工及切深變化時(shí)能夠?qū)η行歼M(jìn)行有效地控制,從而提高刀具壽命以及工件表面質(zhì)量。
17.以下結(jié)合附圖及實(shí)施例對(duì)本發(fā)明作進(jìn)一步詳細(xì)說(shuō)明;但本發(fā)明的一種小零件加工用車削刀片不局限于實(shí)施例。
附圖說(shuō)明
18.圖1是本發(fā)明的實(shí)施例的立體構(gòu)造示意圖;
19.圖2是本發(fā)明的實(shí)施例的俯視圖;
20.圖3是沿圖2中的a-a線的剖視圖;
21.圖4是圖3中的b部放大示意圖;
22.圖5是沿圖2中的c-c線的剖視圖;
23.圖6是圖2中的d部放大示意圖。
24.圖中:1、刀片本體;11、螺釘鎖接孔;2、上表面;21、定位平面;3、下表面;4、側(cè)面;5、切削刃;51、圓弧切削刃;52、線段切削刃;6、前刀面;61、圓弧切削刃的前刀面;62、線段切削刃的前刀面;7、凸起;71、第一凸起;711、第一凸起的頂面;712、第一凸起的側(cè)面;72、第二凸
起;721、第二凸起的頂面;722、第二凸起的側(cè)面。
具體實(shí)施方式
25.實(shí)施例
26.參見(jiàn)圖1至圖6所示,本發(fā)明的一種小零件加工用車削刀片,包括刀片本體1;所述刀片本體1的輪廓投影為多邊形形狀;如圖2所示,本實(shí)施例的刀片本體的輪廓投影為菱形形狀,且在刀片本體的菱形形狀的四個(gè)角部中,有兩個(gè)角部為銳角;所述刀片本體1具有上表面2、下表面3和連接在上、下表面之間的側(cè)面4;所述刀片本體1的中部設(shè)有貫穿上、下表面的螺釘鎖接孔11;所述刀片本體中,在刀片本體1的銳角角部中,所述上表面2與所述側(cè)面4相交形成切削刃5;所述切削刃5包括對(duì)應(yīng)于角尖處的圓弧切削刃51和與圓弧切削刃的兩邊相接的線段切削刃52;本實(shí)施例中,線段切削刃52為構(gòu)成菱形上表面2的四條長(zhǎng)度相等的邊界;圓弧切削刃51,線段切削刃52均平行于所述下表面3,這種結(jié)構(gòu)能夠保證切削刃5的強(qiáng)度,使其在使用的過(guò)程中不易崩壞;所述上表面2中,由所述切削刃5向刀片本體1的中部方向,沿斜向下方向延伸形成前刀面6;需要說(shuō)明的是,往刀片本體1的中部方向指的是往本體內(nèi)的方向,而向下方向指的是從上表面2往下表面3的方向;上表面2的中部即對(duì)應(yīng)于螺釘鎖接孔11的周圍設(shè)為定位平面21,下表面3為平面,定位平面21與下表面3相平行;由前刀面6延伸至定位平面21形成容屑槽;在對(duì)應(yīng)于圓弧切削刃51,由前刀面6向刀片本體1的中部方向設(shè)有凸起7,具體的是順序設(shè)有圓臺(tái)形狀的第一凸起71和倒v形狀的第二凸起72,且第一凸起71和第二凸起72分別沿著所述刀片本體的銳角角部的角平分線為對(duì)稱結(jié)構(gòu);所述第一凸起71和第二凸起72分別包括頂面和側(cè)面;所述第一凸起71的最高點(diǎn)為第一凸起71的頂面711,第一凸起71的頂面711位置高于所述圓弧切削刃51的位置,所述第二凸起72的頂面721位置高于所述第一凸起71的頂面711位置。
27.本實(shí)施例中,所述第一凸起71的頂面711為平面,并平行于所述下表面3;所述第一凸起71的側(cè)面712為曲面,第一凸起71的側(cè)面712為朝第一凸起71中心斜向上延伸的曲面。
28.本實(shí)施例中,所述第一凸起71的頂面位置與所述圓弧切削刃51的位置之間的高度差為0.025mm~0.065mm;沿著所述刀片本體的銳角角部的角平分線方向,所述第一凸起71的頂面711與所述圓弧切削刃51的最小距離為0.2mm~1mm。這種最小距離設(shè)置能夠保證在切削過(guò)程,切屑能夠得到有效的處理。
29.本實(shí)施例中,所述第二凸起72的頂面721為平面,并平行于所述下表面3;所述第二凸起72的側(cè)面722為曲面,第二凸起72的側(cè)面722為朝第二凸起72中心線斜向上延伸的曲面,第二凸起72的頂面721是位于第二凸起72的側(cè)面722上方的平面。
30.本實(shí)施例中,所述第二凸起72的頂面位置與所述圓弧切削刃51的位置之間的高度差為0.1mm~0.3mm。
31.本實(shí)施例中,如圖4所示,所述第一凸起71的側(cè)面712與下表面3之間的夾角θ712大于所述第二凸起72的側(cè)面722與下表面3之間的夾角θ722。
32.如圖4所示,第一側(cè)面712與相對(duì)于下表面3的夾角θ712大于第二側(cè)面722相對(duì)于下表面3的夾角θ722。需要說(shuō)明的是,在此所描述的夾角均為通過(guò)圓弧切削刃52角平分線且垂直于下表面3的平面截圖所得到的。
33.本實(shí)施例中,沿著所述刀片本體的銳角角部的角平分線方向,所述第一凸起71的
側(cè)面712平緩過(guò)渡至所述第二凸起72的側(cè)面722;所述第二凸起72的側(cè)面722的長(zhǎng)度大于所述第一凸起71的側(cè)面712的長(zhǎng)度,這種結(jié)構(gòu),能夠高度維持大切深的斷屑性能。
34.本實(shí)施例中,從垂直于所述線段切削刃52的方向,所述線段切削刃52到所述第二凸起72的側(cè)面722的距離大于位于所述線段切削刃52到所述第一凸起71的側(cè)面712的距離。
35.本發(fā)明的這種結(jié)構(gòu),隨著從圓弧切削刃51方向遠(yuǎn)離,線段切削刃52到凸起7的距離逐漸增大,作用于切屑的距離增大。
36.通過(guò)本實(shí)施方式,小切深加工時(shí),產(chǎn)生的切屑通過(guò)前刀面6在第一凸起71的側(cè)面712位置被有效處理。隨著切深增大,處理切屑的主要位置由第一凸起71的側(cè)面712漸漸地轉(zhuǎn)化成第二凸起72的側(cè)面722位置。這樣,在一定的切深范圍內(nèi),無(wú)論是小切深還是大切深,或是在切深變化的工況加工,都能夠妥善有效處理切屑,使得切屑能夠被穩(wěn)定卷曲,折斷并順暢排出。
37.如圖4所示,在本實(shí)施方式中,第一凸起71的側(cè)面712與第二凸起72的側(cè)面722之間存在第一凸起71的頂面711,第一凸起71的頂面711與下表面3平行,存在這一結(jié)構(gòu),可在小切深大進(jìn)給的工況下,突出第二凸起72的側(cè)面722的處理切屑作用,有效減少切屑在前刀面6及凸起7的堵塞情況。
38.另外,在本實(shí)施方式中,如圖4所示,在凸起7中的第一凸起71的側(cè)面712和第二凸起72的側(cè)面722。第一凸起71的側(cè)面712在前刀面6靠?jī)?nèi)位置開(kāi)始內(nèi)部斜上方向延伸終止于第一凸起71的頂面711。第二凸起72的側(cè)面722在第一凸起71的頂面711靠?jī)?nèi)部位置開(kāi)始往內(nèi)部斜上方向延伸終止于第二凸起72的頂面721。
39.通過(guò)以上描述的結(jié)構(gòu),在變化切深時(shí),可通過(guò)具有一定坡度,緩慢變化的第一凸起71的側(cè)面712及第二凸起72的側(cè)面722穩(wěn)定控制卷曲切屑。另外,在小切深大進(jìn)給的情況下,能夠充分發(fā)揮第二凸起72的側(cè)面722的處理切屑作用??傊诖私Y(jié)構(gòu)作用下,能夠在廣泛的工況下展現(xiàn)其優(yōu)異的排屑斷屑能力。
40.本實(shí)施例中,第一凸起71和第二凸起72均關(guān)于圓弧切削刃51的角平分線對(duì)稱。這樣,能夠在小切深情況下,使得產(chǎn)生的切屑能夠沿著圓弧切削刃51的角平分線較好地與第一凸起71的側(cè)面712及第二凸起72的側(cè)面722接觸,穩(wěn)定排屑。
41.通過(guò)這樣的結(jié)構(gòu),隨著切深的增大,作用于切屑的距離也隨之增大,能夠適應(yīng)切屑的卷曲直徑,從而使切屑穩(wěn)定卷曲??傊?,在此結(jié)構(gòu)作用下,能夠在廣泛的工況下展現(xiàn)其優(yōu)異的排屑斷屑能力。
42.本實(shí)施例中,如圖6所示,圓弧切削刃51與第一凸起71之間設(shè)置前刀面61與小部分前刀面62,線段切削刃52與第一凸起71或第二凸起72之間設(shè)置前刀面62。所述圓弧切削刃51的前刀面61相對(duì)于下表面3的傾斜角度為α,且2
°
≤α≤4
°
,這種傾斜角度α的設(shè)置,能夠保證圓弧切削刃51的強(qiáng)度;所述線段切削刃52的前刀面62相對(duì)于下表面3的傾斜角度為β,且5
°
≤β≤9
°
;這種傾斜角度β的設(shè)置,能夠保證線段切削刃52的鋒利性。這種能夠保證線段切削刃52的鋒利性。
43.通過(guò)這種結(jié)構(gòu),在小切深的工況下,生成的切屑能夠首先被第一凸起71的前刀面61進(jìn)行卷曲,然后再被第一凸起71的側(cè)面712作用穩(wěn)定卷曲,順利將切屑排出。
44.本實(shí)施例中,所述側(cè)面4相對(duì)于所述下表面的垂直面為斜面即具有夾角γ,夾角γ為銳角,且所述側(cè)面4由上向下呈漸次向內(nèi)傾斜。這種結(jié)構(gòu)能夠避免刀具與工件的加工面發(fā)
生不必要的接觸。
45.本發(fā)明的一種小零件加工用車削刀片,采用了刀片本體1的上表面2中,由所述切削刃5向刀片本體1的中部方向,沿斜向下方向延伸形成前刀面6;在對(duì)應(yīng)于圓弧切削刃51,由前刀面6向刀片本體1的中部方向順序設(shè)有圓臺(tái)形狀的第一凸起71和倒v形狀的第二凸起72,且第一凸起71和第二凸起72分別沿著所述刀片本體的銳角角部的角平分線為對(duì)稱結(jié)構(gòu);所述第一凸起71和第二凸起72分別包括頂面711、721和側(cè)面712、722;所述第一凸起71的頂面711位置高于所述圓弧切削刃51的位置,所述第二凸起72的頂面721位置高于所述第一凸起71的頂面711位置。本發(fā)明通過(guò)在容屑槽里設(shè)計(jì)特定的凸起結(jié)構(gòu)(即第一凸起71和第二凸起72),來(lái)保證足夠的容屑空間同時(shí)增強(qiáng)刀具的鋒利性,加強(qiáng)其對(duì)切屑的作用,能夠?qū)崿F(xiàn)在小型零部件的小進(jìn)給小切深加工及切深變化時(shí)能夠?qū)η行歼M(jìn)行有效地控制,從而提高刀具壽命以及工件表面質(zhì)量。本發(fā)明可在小切深大進(jìn)給的工況下,突出第二凸起72的側(cè)面722的處理切屑作用,有效減少切屑在前刀面6及凸起7部位的堵塞情況。小切深加工時(shí),產(chǎn)生的切屑通過(guò)前刀面6在圓臺(tái)狀凸起71的第一側(cè)面712位置被有效處理。隨著切深增大,處理切屑的主要位置由第一凸起71的側(cè)面712漸漸地轉(zhuǎn)化成第二凸起72的側(cè)面722位置。這樣,在一定的切深范圍內(nèi),無(wú)論是小切深還是大切深,或是在切深變化的工況加工,都能夠妥善有效處理切屑,使得切屑能夠被穩(wěn)定卷曲,折斷并順暢排出。
46.上述只是本發(fā)明的較佳實(shí)施例,并非對(duì)本發(fā)明作任何形式上的限制。雖然本發(fā)明已以較佳實(shí)施例揭露如上,然而并非用以限定本發(fā)明。任何熟悉本領(lǐng)域的技術(shù)人員,在不脫離本發(fā)明技術(shù)方案范圍的情況下,都可利用上述揭示的技術(shù)內(nèi)容對(duì)本發(fā)明技術(shù)方案作出許多可能的變動(dòng)和修飾,或修改為等同化的等效實(shí)施例。因此,凡是未脫離本發(fā)明技術(shù)方案的內(nèi)容,依據(jù)本發(fā)明技術(shù)實(shí)質(zhì)對(duì)以上實(shí)施例所做的任何簡(jiǎn)單修改、等同變化及修飾,均應(yīng)落在本發(fā)明技術(shù)方案保護(hù)的范圍內(nèi)。