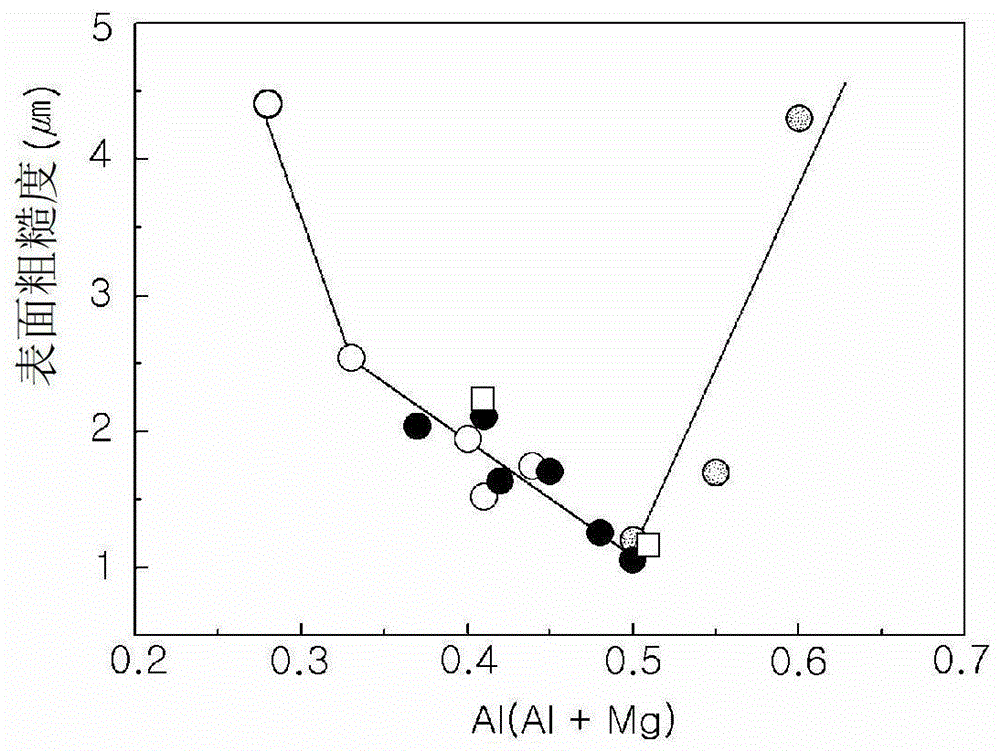
本發(fā)明涉及用于建筑材料、家用電器或汽車的鍍鋅(Zn)合金鋼板,更具體而言,涉及具有優(yōu)異的耐腐蝕性和表面品質(zhì)的熱浸鍍Zn合金鋼板,及其制造方法,該方法使用包含鋁(Al)、鎂(Mg)等的熱浸Zn合金鍍浴。
背景技術:由于熱浸鍍Zn鋼板的制造方法比電鍍鋅鋼板更簡單、價格更低,因此對其的需求已經(jīng)擴展到建筑材料、家用電器或汽車領域。特別是,根據(jù)Zn價格近期的提高,已經(jīng)開發(fā)了涉及與熱浸鍍Zn鋼板相比在較低涂層重量下具有更好的耐腐蝕性的熱浸鍍鋅-鋁(在下文中稱作Zn-Al體系)或熱浸鍍鋅-鋁-鎂(在下文中稱作Zn-Al-Mg體系)合金鋼板的技術,且對Zn-Al和Zn-Al-Mg體系的需求也已經(jīng)增加。常用的Zn-Al體系產(chǎn)品可為鍍Zn-55%Al的鋼板。然而,鑒于鍍層中的鋁含量,存在以下限制:犧牲腐蝕保護能力降低,并且腐蝕優(yōu)選發(fā)生在暴露于底層金屬的部分例如切削表面。而且,對于熱浸鍍Zn-55%Al,在鍍浴中渣滓的產(chǎn)生可能非常嚴重,因為鍍浴的溫度可高至約600℃,電鍍可加工性可能降低,且設備的壽命可能縮短,這是由于在鍍浴中對設備組件(如導輥)的腐蝕。關于Zn-Al-Mg體系,第3505043號美國專利中有提及,并且此后第64-8702號日本專利申請公開文本、第64-11112號日本專利申請公開文本、第8-60324號日本專利申請公開文本、第10-226865號日本專利申請公開文本、以及第3201469號日本專利中均有提及。前述日本專利公開了在鍍層中鋁和鎂的總含量在9重量%-14重量%的范圍內(nèi),并且由于優(yōu)異的耐腐蝕性,所述鍍層展示出用于建筑材料的合適的品質(zhì)特性。然而,該鍍層用于汽車可能是困難的,這是因為其表面品質(zhì)可能由于在鍍層中高水平的合金組分(如鋁和鎂)而劣化。而且,在歐洲存在一種技術,其中鍍層中鋁和鎂的總含量可以控制在比日本技術更低的水平。然而,在這種情況下,耐腐蝕性可能會有些許下降。同時,就制造而言,當鋁和鎂的含量被控制在低水平時,Zn-Al-Mg合金鍍層的凝固起始溫度可為400-420℃的范圍,但根據(jù)鋁和鎂的含量,該溫度可能會有些許不同。Zn-Al-Mg三元共晶體結(jié)構的最終凝固結(jié)束溫度為約340℃,并且其表面品質(zhì)可能由于在液相-固相溫度范圍內(nèi)鎂的選擇性氧化引起的波痕的產(chǎn)生而劣化。即,鋁和鎂富集于在鍍層凝固過程中未凝固的熔融金屬池中。鎂濃度越高,越易發(fā)生氧化,且流動性越不均勻。因此,需要一種用于熱浸鍍Zn-Al-Mg體系的鋼板的技術,所述技術在將鍍層中鋁和鎂的含量控制在盡可能低的同時,可以確保優(yōu)異的耐腐蝕性和均勻的表面品質(zhì)。
技術實現(xiàn)要素:技術問題本發(fā)明一方面提供了一種熱浸鍍Zn合金鋼板,其通過使用熱浸Zn-Al-Mg體系鍍浴而制造且具有優(yōu)異的耐腐蝕性和表面品質(zhì),以及一種制造該熱浸鍍Zn合金鋼板的方法。技術方案根據(jù)本發(fā)明的一方面,提供了一種高耐腐蝕性的熱浸鍍鋅(Zn)合金鋼板,包括:底層鋼板;和熱浸Zn合金鍍層,其中熱浸Zn合金鍍層的組成包括約1重量%至約3重量%的鋁(Al),約1.5重量%至約4.0重量%的鎂(Mg),和余量的Zn以及不可避免的雜質(zhì),其中Al+Mg為約2.5重量%至約7.0重量%的范圍并且Al:(Al+Mg)為約0.38至約0.48的范圍。根據(jù)本發(fā)明的另一方面,提供了一種制造高耐腐蝕性的熱浸鍍Zn合金鋼板的方法,包括:制備熱浸Zn合金鍍浴,其包括約1重量%至約3重量%的Al,約1.5重量%至約4.0重量%的Mg和余量的Zn以及不可避免的雜質(zhì),其中Al+Mg為約2.5重量%至約7.0重量%的范圍并且Al:(Al+Mg)為約0.38至約0.48的范圍;將底層鋼板浸入熱浸Zn合金鍍浴,以通過進行電鍍而制造電鍍鋼板;以及在氣體吹掃后冷卻該電鍍鋼板。發(fā)明的有益效果本發(fā)明提供了一種鍍浴,其使得能夠制備具有電鍍結(jié)構的熱浸鍍Zn合金鋼板,在所述電鍍結(jié)構中二元Zn-MgZn2共晶體結(jié)構主要分布于三元Al-Zn-MgZn2共晶體結(jié)構的基體中,并且提供了一種制造所述熱浸鍍Zn合金鋼板的方法,還提供了一種通過所述方法而得到的熱浸鍍Zn合金鋼板,其具有精細的表面外觀以及優(yōu)異的耐腐蝕性。因此,可期望得到高適用性材料,例如作為用于建筑材料、家用電器或汽車的防銹鋼板。附圖說明由以下詳細描述結(jié)合附圖可更清楚地理解本發(fā)明以上和其他方面、特征以及其他優(yōu)勢,在所述附圖中:圖1為根據(jù)鋁(Al)和鎂(Mg)的變化說明鍍層的示意圖;圖2為根據(jù)Al:(Al+Mg)的變化示出熱浸鍍鋅(Zn)合金鋼板表面粗糙度變化的圖;并且圖3是示出實施例1結(jié)果的圖。本發(fā)明最佳實施方式在下文中,將更加詳細地描述本發(fā)明。首先,詳細描述本發(fā)明中使用的熱浸鋅(Zn)合金鍍浴。本發(fā)明使用的熱浸Zn合金鍍浴可包括1重量%至3重量%的鋁(Al),1.5重量%至4.0重量%的鎂(Mg)和余量的Zn以及不可避免的雜質(zhì),其中Al+Mg可為2.5重量%至7.0重量%的范圍并且Al:(Al+Mg)可為0.38至0.48的范圍。當Al的含量小于1重量%時,改進耐腐蝕性的效果可能不足并且在鍍浴表面部分防止氧化的效果(由于加入Mg而變嚴重)可能不足。當Al的含量大于3重量%時,底層鋼板中的鐵(Fe)溶解可能增加,并且鍍層的可焊性和磷酸化作用性能可能劣化。因此,Al的含量可在1重量%-3重量%的范圍。當Mg的含量小于1.5重量%時,改進耐腐蝕性的效果可能不足,并且當Mg的含量大于4.0重量%時,對鍍浴的管理可能會困難,這是因為在后面將要描述的鍍浴的溫度范圍內(nèi)鍍浴的氧化和渣滓的產(chǎn)生都增加。因此Mg的含量可在1.5重量%-4.0重量%的范圍。鋁和鎂均是可提高鍍層耐腐蝕性的元素,這些元素的總量越大,可越大地提高鍍層的耐腐蝕性。然而,當鍍浴中鋁和鎂的重量百分比(重量%)總和小于2.5重量%時,改進耐腐蝕性的效果可能不足,且當總和大于7.0重量%時,由于鍍層硬度的提高可能促進產(chǎn)生加工裂縫,并且盡管耐腐蝕性提高,但是可焊性和涂覆性可能劣化或者需要改進處理方法。因此,鋁和鎂的重量百分比總和可在2.5重量%-7.0重量%的范圍。通過實驗,發(fā)明人發(fā)現(xiàn)形成三類電鍍結(jié)構且鍍層的耐腐蝕性可根據(jù)Al:(Al+Mg)比值變化,該Al:(Al+Mg)比值通過上述Al和Mg范圍中的Mg:Al的濃度比確定,并且其三個實例在圖1中示出。在本發(fā)明前述組成范圍可產(chǎn)生晶體結(jié)構,其可包括Zn單相、MgZn2單相、Zn-MgZn2二元共晶體結(jié)構或在Zn-AI-MgZn2三元共晶體結(jié)構基體中的Zn-Al二元共晶體結(jié)構。上述合金鍍層結(jié)構類型可因鍍浴組分的組成比例和冷卻方法而不同,根據(jù)不同的結(jié)構類型也可產(chǎn)生不同的耐腐蝕性。圖1(a)示出,當鍍浴的組成為Zn-2Al-2Mg,其中Mg+Al=4重量%,且Al:(Mg+Al)=0.5時,在Zn-AI-MgZn2三元共晶體結(jié)構基體中形成粗Zn單相結(jié)構。圖1(b)示出,當鍍浴的組成為Zn-3Al-2Mg,其中Mg+Al=5重量%,且Al:(Mg+Al)=0.6時,還形成了Zn-Al二元共晶體結(jié)構,這是因為鋁含量略微高于圖1(a)中組成的鋁含量。另一方面,圖1(c)示出,當鍍浴的組成為Zn-2Al-3Mg,其中Mg+Al=5重量%,且Al:(Mg+Al)=0.4時,可觀察到含量少于10%的Zn單相結(jié)構,鍍浴中的一部分MgZn2可能不可避免地包含在鍍層中,并且在Zn-AI-MgZn2三元共晶體結(jié)構基體中形成了Zn-MgZn2二元共晶體結(jié)構。當Al:(Mg+Al)在0.38-0.48的范圍時,形成了圖1(c)的電鍍結(jié)構。在(c)的情況下(其中Al:(Mg+Al)滿足0.38-0.48的范圍),與其中如圖1(a)形成Zn初晶相的情況或其中如圖1(b)形成Zn-Al二元共晶體結(jié)構的情況相比,當形成MgZn2時耐腐蝕性優(yōu)異,并且鍍層中的Mg促進堿式氯化鋅(simonkolleite)(Zn5(OH)8Cl2)的形成,其為一種致密的腐蝕產(chǎn)物,因此可提高耐腐蝕性。當Al:(Mg+Al)小于0.38時,鍍浴的氧化可能很嚴重,由于在鍍浴中浮選具有渣滓形式的MgZn2金屬間顆粒,所以可能產(chǎn)生鍍層的缺陷,并且由于在鍍層中形成粗MgZn2相,電鍍表面可能是粗糙的。而且,當Al:(Mg+Al)大于0.48時,由于如圖1(a)和1(b)中所示在鍍層中形成大量Zn單相,因此耐腐蝕性可能劣化。本發(fā)明的熱浸Zn合金鍍浴可包括一種或多種選自以下的物質(zhì):硅(Si)、鋰(Li)、鈦(Ti)、鑭(La)、鈰(Ce)、硼(B)和磷(P),含量為0.1%以下。當加入微量的上述組分時,鍍層的晶體結(jié)構精細化并且致密,使得表面粗糙度可能降低,在本發(fā)明所限定的Al:(Mg+Al)范圍內(nèi)可獲得均勻的表面粗糙度。上述添加元素的含量可在0.005%-0.1%的范圍內(nèi)。當其含量小于0.005%時,可能無法獲得添加的效果,當含量大于0.1%時,在鍍浴中可形成漂浮物或不再獲得進一步的效果。因此,上述添加元素的含量可在0.005%-0.1%的范圍內(nèi)。以下,將詳細描述本發(fā)明的熱浸鍍Zn合金鋼板。本發(fā)明的熱浸鍍Zn合金鋼板包括底層鋼板和熱浸Zn合金鍍層。熱浸Zn合金鍍層的組成可包括1重量%至3重量%的Al、1.5重量%至4.0重量%的Mg、和余量的Zn以及不可避免的雜質(zhì),其中Al+Mg可為2.5重量%至7.0重量%的范圍,Al:(Al+Mg)可為0.38-0.48的范圍。在本發(fā)明的熱浸鍍Zn合金鋼板中,熱浸Zn合金鍍層的合金相可包含作為主結(jié)構的Zn-AI-MgZn2三元共晶體結(jié)構和Zn-MgZn2二元共晶體結(jié)構,可包括含量為10%以下的Zn單相結(jié)構,并且可以包括余量的MgZn2結(jié)構。鋅可在腐蝕性環(huán)境中形成腐蝕產(chǎn)物,例如紅鋅礦(ZnO),水鋅礦(Zn5(CO3)2(OH)6)和堿式氯化鋅(Zn5(OH)8Cl2),作為致密的腐蝕產(chǎn)物的堿式氯化鋅具有優(yōu)異的腐蝕抑制作用。因為Zn-Al-Mg體系電鍍鋼板的鍍層中的Mg促進堿式氯化鋅的產(chǎn)生以提高鍍層的耐腐蝕性,因此本發(fā)明控制Zn單相結(jié)構的含量為10%以下。當所形成的Zn單相結(jié)構的含量大于10%時,耐腐蝕性可能由于在腐蝕性環(huán)境中堿式氯化鋅產(chǎn)生的降低而劣化。在熱浸電鍍方法中,通常在電鍍后通過進行表皮光軋(skinpass)來給予表面合適的粗糙度。鋼板的表面粗糙度是一個重要因素,其影響壓制成形過程可加工性的改進和涂布后圖像清晰度的改進,需要進行控制。為此,使用具有合適表面粗糙度的軋輥進行表皮光軋,以使通過轉(zhuǎn)移該軋輥的粗糙度而為鋼板表面提供粗糙度。當鍍層的表面粗糙時,難以將軋輥的粗糙度均勻地轉(zhuǎn)移至鋼板,因此在進行表皮光軋后,表面粗糙度也可能不均勻。即,鍍層的表面越光滑,可越容易地將表皮光軋輥的粗糙度均勻地轉(zhuǎn)移至鋼板。因此,進行表皮光軋前,鍍層的粗糙度可控制至盡可能的小。因此,本發(fā)明熱浸鍍Zn合金鋼板的表面粗糙度(Ra)可控制至2μm以下。圖2為根據(jù)Al:(Mg+Al)的變化的鍍層粗糙度的比較結(jié)果,并且應理解,當Al:(Mg+Al)小于0.38時,鍍層的表面粗糙度可能過于粗糙,而且由于鍍浴中的添加元素及冷卻速率,也可能難以控制表面粗糙度。磷(P)可以0.01mg/m2-500mg/m2的范圍粘附至本發(fā)明的熱浸鍍Zn合金鋼板的表面。在下文將要描述的制造熱浸鍍Zn合金鋼板方法中的冷卻過程中,通過噴射磷酸鹽水溶液而粘附磷。根據(jù)所粘附的磷,在冷卻期間可能存在提高冷卻能力的效果,但是當其含量大于500mg/m2時可能會產(chǎn)生表面缺陷。因此,其上限可以為500mg/m2。以下,詳細描述制造熱浸鍍Zn合金鋼板的方法。制造本發(fā)明的熱浸鍍Zn合金鋼板的方法包括:制備前述熱浸Zn合金鍍?。粚⒌讓愉摪褰朐摕峤n合金鍍浴以通過進行電鍍來制造電鍍鋼板;并且在氣體吹掃后冷卻該電鍍鋼板??稍?20℃-450℃的溫度范圍內(nèi)在熱浸Zn合金鍍浴中進行電鍍。一般而言,熱浸Zn鍍層的凝固反應在約420℃的溫度下結(jié)束。另一方面,因為本發(fā)明的熱浸鍍Zn合金鋼板的鍍層的凝固自400℃以下的溫度開始,并在約350℃的溫度下結(jié)束,因此所述熱浸鍍Zn合金鋼板的鍍層可具有寬范圍的凝固溫度,在該凝固溫度范圍內(nèi)的冷卻速率可影響鍍層的結(jié)構和表面品質(zhì)。因此,本發(fā)明的熱浸Zn合金鍍浴的溫度可設定在420℃-450℃的范圍,比常用的鍍浴的溫度低。電鍍后通過氣體吹掃處理來調(diào)節(jié)涂層重量。氣體吹掃處理可以通過使用空氣或氮氣而進行,例如可使用氮氣。這樣做的原因為當使用空氣時,通過在鍍層表面上鎂的優(yōu)先氧化而可能在鍍層中產(chǎn)生表面缺陷。氣體吹掃用于控制涂層重量且其方法無特別限制??稍?0℃/s以上的冷卻速率下進行冷卻??梢栽跉怏w吹掃后立即進行冷卻直至凝固結(jié)束,并且冷卻可以通過噴射空氣而進行。當冷卻速率低于10℃/s時,由于形成Zn單相,鍍層的晶體結(jié)構粗糙且耐腐蝕性和表面品質(zhì)劣化。因此,可在10℃/s以上的冷卻速率下進行冷卻。此時,噴射空氣的壓力可為300毫巴以下。這是為了在凝固過程中防止鍍層損壞,在所述凝固過程中液相和固相共存。同時,在冷卻過程中,可以通過將磷酸鹽水溶液與空氣一起噴射而進行冷卻。這樣做的原因為通過噴射磷酸鹽水溶液來提高冷卻速率至12℃/s以上,從而可以獲得具有精細的表面外觀的鍍層。噴射的磷酸鹽水溶液通過縮合反應而粘附在鋼板上的磷酸鹽組分的聚合反應是吸熱反應,因此可提高冷卻速率。此時使用的磷酸鹽可為磷酸氫銨、磷酸鈣銨或磷酸鈉銨,且水溶液中磷酸鹽的濃度可以為0.01%-5.0%的范圍。如上所述,這是為了將粘附在表面的磷酸鹽含量控制在0.01mg/m2-500mg/m2的范圍。噴射空氣和磷酸鹽水溶液的方法使用雙流體噴嘴,磷酸鹽水溶液的噴射壓力可在0.3kgf/cm2-5.0kgf/cm2的范圍,空氣的噴射壓力可在0.5kgf/cm2-7.0kgf/cm2的范圍。這樣的原因是當噴射壓力比合適的范圍低時,不足以噴射溶液,當噴射壓力比該合適的范圍高時,液滴的沖擊壓力提高,以致在鍍層上可產(chǎn)生具有圓點形狀的點蝕缺陷。同時,噴射的磷酸鹽水溶液的液滴可通過穿過充電至-1KV至-40KV的網(wǎng)狀電極而靜電充電。上述范圍用于獲得均勻且良好的液滴。當電壓為-1KV以下時,在鍍層上可產(chǎn)生點蝕印跡,這是因為不能獲得液滴的霧化效果而仍為大的液滴,當使用電壓為-40KV以上時,在充電電極和鋼板之間可產(chǎn)生電火花。因此,液滴在-1KV至-40KV范圍內(nèi)充電。本發(fā)明的實施方式在下文中,更詳細地描述本發(fā)明的實施例。提供以下實施例僅為更清楚地理解本發(fā)明,而不是限定其范圍。(實施例1)在熱浸電鍍設備中連續(xù)電鍍鋼帶,通過使用0.8mm厚的低碳冷軋鋼板作為底層鋼板在以下條件下進行熱浸Zn合金電鍍。此時,氮氣用于氣體吹掃以制造具有不同涂層重量的電鍍鋼板。通過鹽霧試驗(鹽霧標準試驗對應于KS-C-0223)測量直至在樣品表面的銹蝕產(chǎn)生區(qū)域為5%時所經(jīng)過的時間,并且其結(jié)果示于圖3。—連續(xù)還原爐的條件:鋼板最高溫度為780℃,露點溫度為-40℃—鍍浴組成:表1—鍍浴溫度和熱浸時間:440℃,3秒—電鍍后鋼板的冷卻速率:10℃/s(空氣噴射)[表1]如圖3中所示,可以確定滿足本發(fā)明Al和Mg濃度條件的發(fā)明實施例與對比實施例相比,具有優(yōu)異的耐鹽霧腐蝕性。(實施例2)同時,進行實施例2以通過鍍浴組成與電鍍結(jié)構之間的關系來確定熱浸鍍Zn合金鋼板的耐腐蝕性。在熱浸電鍍設備中連續(xù)電鍍鋼帶,通過使用0.8mm厚的低碳冷軋鋼板作為底層鋼板在以下條件下進行實施例2的熱浸Zn合金電鍍。此時,氮氣用于氣體吹掃以制造單面涂層重量為60g/m2的電鍍鋼板。通過鹽霧試驗(鹽霧標準試驗對應于KS-C-0223)測量直至在樣品表面的銹蝕產(chǎn)生區(qū)域為5%時所經(jīng)過的時間,并且其結(jié)果示于表2?!B續(xù)還原爐的條件:鋼板最高溫度為780℃,露點溫度為-40℃—鍍浴組成:表1—鍍浴溫度和熱浸時間:440℃,3秒—電鍍后鋼板的冷卻速率:10℃/s(空氣噴射)同時,鍍層剖面結(jié)構中的Zn單相所占面積示于2,且其他金屬相的存在用O/X表示。[表2]如表2所示,應理解滿足本發(fā)明鍍浴組成的鍍層主要由Zn-MgZn2二元相和Zn-Al-MgZn2三元相共晶體結(jié)構組成,并且此時,耐腐蝕性提高。對比實施例屬于Zn單相結(jié)構的含量大于10%的情況,并且可以確定其耐腐蝕性較差。盡管對于對比實施例2-7(Al和Mg的濃度分別為2.3重量%和5重量%),獲得了滿意的耐腐蝕性,但是表面粗糙度可能是粗糙的,這是因為當Al:(Mg濃度+Al濃度)比例小于0.38時鍍層中存在粗的MgZn2單相,其在本發(fā)明中已提及。因此,對比實施例2-7歸為對比實施例之一。特別地,關于使用添加劑的本發(fā)明實施例2-6至2-9,應理解,因為本發(fā)明實施例2-6至2-9中的Zn-MgZn2二元相共晶體結(jié)構相對于無添加劑的本發(fā)明實施例更精細,所以改進耐腐蝕性的效果提高。(實施例3)在實施例3中,不同于上述實施例2,通過使用2.6mm厚的低碳熱軋鋼板作為底層鋼板進行試驗。除了鍍浴組成外的處理條件與實施例2中的相同,在實施例3中制造了單面涂層重量為90g/m2的電鍍鋼板。同時,觀察構成鍍層的晶體結(jié)構,并且通過鹽霧試驗測定直至在樣品表面的銹蝕產(chǎn)生區(qū)域為5%時所經(jīng)過的時間,在表3中對比了其結(jié)果。[表3]如表3所示,通過使用低碳熱軋鋼板獲得的表3中的結(jié)果與通過使用冷軋鋼板獲得的表2中的結(jié)果相似,可以確定當滿足本發(fā)明鍍浴組成時獲得了優(yōu)異的耐腐蝕性。(實施例4)在實施例4中,為了揭示對電鍍后冷卻速度的影響而進行了實驗。在熱浸電鍍設備中連續(xù)電鍍鋼帶,通過使用如酸浸的方法去除2.6mm厚的低碳熱軋鋼條的鱗狀體(scales),然后在具有恒定電鍍組成的以下條件下進行實施例4的熱浸Zn合金電鍍。單面涂層重量調(diào)節(jié)至60g/m2,然后在鍍層凝固范圍內(nèi)的鋼板冷卻速率通過僅使用空氣噴射型冷卻或空氣噴射型冷卻室和靜電型磷酸鹽水溶液噴射二者而在1℃/s-15℃/s范圍內(nèi)變化。測量了電鍍鋼板的表面品質(zhì)和通過鹽霧試驗(鹽霧標準試驗對應于KS-C-0223)直至在樣品表面的銹蝕產(chǎn)生區(qū)域為5%時所經(jīng)過的時間,其結(jié)果示于表4。—連續(xù)還原爐的條件:鋼板最高溫度為550℃,露點為-40℃—鍍浴組成/溫度/熱浸時間:2.5重量%的Al,3.5重量%的Mg/450℃/3秒—磷酸鹽水溶液的噴射條件:磷酸鹽水溶液的噴射壓力為2.0kgf/cm2,空氣噴射壓力為3.0kgf/cm2,使用的高壓強度為-20KV。[表4]如表4中所示,應理解,當冷卻速率小于10℃/s時(比本發(fā)明的冷卻速率低),耐腐蝕性趨于降低,當冷卻速率為10℃/s以上時,耐腐蝕性提高。因此,可以確定本發(fā)明的冷卻速率可為10℃/s以上。(實施例5)為了確定在通過使用磷酸鹽水溶液噴射的冷卻過程中想要的條件而進行實施例5。通過使用0.8mm厚的低碳冷軋鋼帶在以下條件下進行實施例5的熱浸Zn合金電鍍,且通過氣體吹掃制造單面涂層重量為60g/m2的電鍍鋼板。測定電鍍鋼板的表面外觀和鍍層的黑化,其結(jié)果示于表5?!B續(xù)還原爐的條件:鋼板最高溫度為780℃,露點為-40℃—鍍浴組成:2重量%的Al,3重量%的Mg—鍍浴溫度和熱浸時間:440℃,3秒—溶液噴射和高壓條件:見表5目測觀察表面外觀,沒有外部的鍍層波紋和條狀印跡的均勻表面用○表示,細微的波紋或條狀印跡用△表示,明顯的波紋或條狀印跡用X表示。而且,通過測量制造鍍層后鍍層的白度和制造鍍層后三個月后的白度來確定黑化。當其差小于2,耐黑化性用○表示,當其差在2-5范圍,耐黑化性用△表示,當其差大于5,耐黑化性用X表示。[表5]如表5中所示,本發(fā)明實施例滿足本發(fā)明建議的磷酸鹽濃度的要求、使用的高壓強度和溶液噴射條件,其具有精細的表面外觀。另一方面,在具有超出本發(fā)明建議的范圍的條件的對比實施例中,可以確定鍍層的表面外觀較差,這是因為可觀察到波紋痕跡等且耐黑化性也更差。雖然已經(jīng)結(jié)合示例性的實施方案示出和描述了本發(fā)明,但是對本領域技術人員顯而易見的是,可以在不偏離所附權利要求書限定的本發(fā)明的主旨和范圍下做出改進和變化。