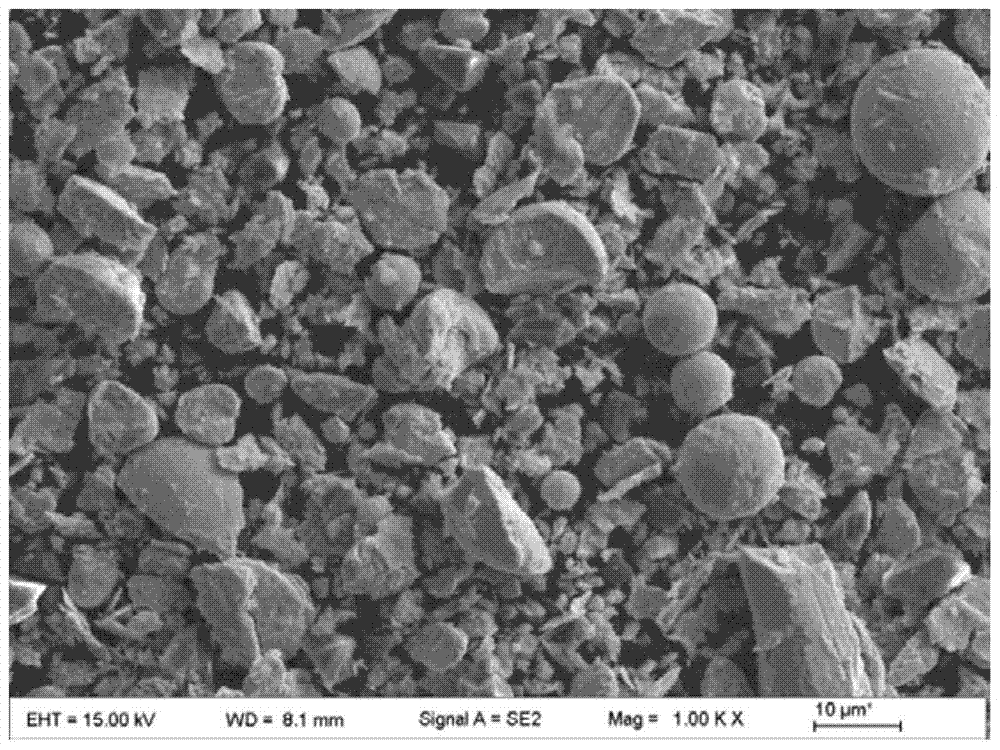
本發(fā)明涉及材料表面改性領(lǐng)域,具體涉及一種高硬度金屬基/金剛石復(fù)合涂層及其高效制備方法。
背景技術(shù):金屬陶瓷兼有金屬和陶瓷的優(yōu)點,它密度小、硬度高、耐磨、導(dǎo)熱性好,不會因為驟冷或驟熱而脆裂。金屬陶瓷既具有金屬的韌性、高導(dǎo)熱性和良好的熱穩(wěn)定性,又具有陶瓷的耐高溫、耐腐蝕和耐磨損等特性。主要有燒結(jié)鋁(鋁-氧化鋁)、燒結(jié)鈹(鈹-氧化鈹)、TD鎳(鎳-氧化釷)等。由一種或幾種陶瓷相與金屬相或合金所組成的復(fù)合材料,廣義的金屬陶瓷還包括難熔化合物合金、硬質(zhì)合金、金屬粘結(jié)的金剛石工具材料。制備金屬陶瓷復(fù)合涂層常用的方法有熱噴涂法、復(fù)合鍍法、激光原位合成法、自蔓延燃燒合成法、噴焊法及等離子堆焊法等,如利用超音速火焰噴涂已成功制備出WC系及Cr3C2系金屬陶瓷復(fù)合涂層,并在諸多工業(yè)領(lǐng)域得到了應(yīng)用。金剛石作為自然界中硬度最高的物質(zhì),其作為金屬陶瓷復(fù)合涂層的強化相已成為國內(nèi)外的研究熱點,各國學者在金屬基/金剛石復(fù)合涂層的制備方面開展了大量的探索研究。采用熱噴涂、噴焊、等離子堆焊、激光熔覆及自蔓延燃燒合成等方法制備金屬基/金剛石復(fù)合涂層時,固相金剛石顆粒會與高溫熔融液態(tài)金屬粘結(jié)相作用,產(chǎn)生熱分解與溶解,使金剛石顆粒難以保留在涂層中。因此,無法有效地制備金屬基/金剛石復(fù)合涂層。復(fù)合電鍍法和化學鍍法雖然避免了上述方法中出現(xiàn)的高溫化學反應(yīng),能夠?qū)⒔饎偸w粒保留在涂層中,且涂層中金剛石的體積含量可達45%,但是當涂層中金剛石體積含量超過25%時,金剛石與粘結(jié)相的界面結(jié)合顯著惡化,涂層的耐磨性難以提高,同時利用這些方法很難制備厚度超過200μm的金屬基/金剛石復(fù)合涂層,而且制備效率低、工藝復(fù)雜、污染環(huán)境,很難實現(xiàn)工業(yè)化。近幾十年發(fā)展起來的冷噴涂法,是一種依靠低溫固態(tài)顆粒高速碰撞基體后發(fā)生強烈塑性變形而沉積形成涂層的一種新型噴涂技術(shù),避免了熱噴涂高溫沉積過程中可能發(fā)生的成分、組織結(jié)構(gòu)的變化,因此適用于溫度敏感材料(如納米材料、非晶材料等)、易氧化材料(如鋁、銅、鈦等)和易相變材料(如碳基復(fù)合材料等)的涂層制備。雖然利用冷噴涂法可以制備金屬基/金剛石復(fù)合涂層,但復(fù)合涂層主要是通過在硬度較軟的金屬基體(如Al)中添加金剛石的方法來制備,難以制備高硬度的金屬基/金剛石復(fù)合涂層,且涂層中金剛石顆粒與金屬基結(jié)合較弱,容易脫落。此外,冷噴涂涂層與基體的結(jié)合機制主要是機械咬合,涂層/基體結(jié)合力較差,涂層容易剝落。綜上所述,目前金屬基/金剛石復(fù)合涂層的各種制備方法均存在以下一種或幾種問題:(1)涂層厚度薄;(2)涂層中金剛石含量低;(3)涂層中金剛石與金屬相結(jié)合差,容易脫落;(4)涂層中金剛石顆粒容易受熱分解;(5)涂層與基體結(jié)合力差;(6)難以制備高硬度金屬基/金剛石復(fù)合涂層。
技術(shù)實現(xiàn)要素:本發(fā)明針對現(xiàn)有的金屬基/金剛石復(fù)合涂層制備技術(shù)存在的上述不足,提供一種采用硬度>50HRC的金屬粉末作為金剛石粘結(jié)相的復(fù)合涂層及其高效制備方法,解決現(xiàn)有技術(shù)制備高硬度金屬基/金剛石復(fù)合涂層厚度薄、涂層中金剛石顆粒容易脫落、復(fù)合涂層中金剛石容易分解、涂層中金剛石體積含量難以超過45%、涂層與基體結(jié)合力差等問題。為了達到上述的目的,本發(fā)明采用了以下的技術(shù)方案:一種金屬基/金剛石激光復(fù)合涂層的制備方法,包括如下步驟:1)利用球磨法將高硬度金屬粉末和金剛石粉末混合均勻形成復(fù)合粉末;所述高硬度金屬粉末的硬度>50HRC,高硬度金屬粉末形狀為球形或類球形,粉末粒度為10~20μm;金剛石粉末為不規(guī)則形狀,粉末粒度為30~50μm;2)將球磨好的復(fù)合粉末在還原爐中還原;3)對基體進行預(yù)處理;4)利用脈沖激光毛化技術(shù)對基體表面進行處理以提高表面粗糙度;采用連續(xù)激光輔助冷噴涂的方法在經(jīng)過脈沖激光毛化處理的基體上同步沉積高硬度金屬基/金剛石復(fù)合涂層。本發(fā)明利用激光毛化技術(shù)、激光熱處理技術(shù)、冷噴涂技術(shù)高效制備這種高硬度金屬基/金剛石復(fù)合涂層,該復(fù)合涂層的特征在于高硬度金屬基的硬度>50HRC,復(fù)合涂層厚度超過1mm,涂層中的金剛石體積含量大于45%。本發(fā)明既實現(xiàn)了以高硬度金屬粉末作為金剛石粘結(jié)相的復(fù)合涂層的制備,又通過脈沖激光毛化處理提高了復(fù)合涂層與基體的結(jié)合強度,最終制備出穩(wěn)定、優(yōu)質(zhì)的高硬度金屬基/金剛石復(fù)合高耐磨涂層,并實現(xiàn)了基材表面處理與涂層沉積制備的集成化、自動化和高效化。作為優(yōu)選,所述高硬度金屬粉末為鎳基粉末、鈷基粉末中的一種或多種。進一步優(yōu)選,所述高硬度金屬粉末為Ni55、Ni50、Ni60或stellite20。作為優(yōu)選,所述步驟1)中,球磨法采用行星式球磨混合,球料比為30~100:1,球磨轉(zhuǎn)速為200~600r/min,球磨時間為2~24h,球磨氣氛為氮氣或氬氣?;蛘邇?yōu)選,所述步驟1)中,球磨法采用振動式球磨混合,球料比為30~100:1,振動頻率為1200r/min,球磨時間為20~60min,球磨氣氛為氮氣或氬氣。作為優(yōu)選,所述步驟2)中,復(fù)合粉末的還原在馬弗爐中進行,還原氣氛為氫氣,還原時間為30min,還原溫度為200~400℃。所述基體為任意形狀的鐵基材料,基體預(yù)處理方法為超聲波表面清洗或噴砂粗化。作為優(yōu)選,所述步驟4)中,脈沖激光光斑在前,噴涂粉斑在后,兩者間隔小于15mm,連續(xù)激光光斑與噴涂粉斑重合,連續(xù)激光光束與冷噴涂噴嘴之間的夾角為20~30°,脈沖激光光斑、連續(xù)激光光斑、噴涂粉斑三者保持同步移動,移動速度為30~50mm/s。進一步優(yōu)選,脈沖激光的能量密度為為104~108W/cm2,脈寬為0.5~2ms,波長為1460~1610nm,半導(dǎo)體連續(xù)激光的能量密度為3~5×105W/cm2,波長為960~1064nm,半導(dǎo)體連續(xù)激光的輸出功率通過閉環(huán)反饋控溫模式實時調(diào)整,沉積溫度依據(jù)高硬度金屬粉末的熔點來選擇,低于金屬粉末的熔點,使其軟化但不熔化。進一步優(yōu)選,冷噴涂工藝參數(shù)為載氣壓力2~3MPa,載氣預(yù)熱溫度300~600℃,噴涂距離15~40mm,送粉量40~80g/min,載氣為壓縮空氣或氮氣中的一種。一種金屬基/金剛石激光復(fù)合涂層,采用高硬度金屬粉末作為金剛石復(fù)合涂層粘結(jié)相;復(fù)合涂層厚度超過1mm,涂層中金剛石體積比超過45%。本發(fā)明與現(xiàn)有技術(shù)相比,具有的有益技術(shù)效果如下:(1)本發(fā)明涉及的高硬度金屬基/金剛石涂層是采用基于冷噴涂的技術(shù)制備的,保留了冷噴涂低溫沉積的特性,避免了高溫沉積技術(shù)導(dǎo)致的金剛石容易分解和溶解的問題,顯著提高了涂層中金剛石的含量;(2)本發(fā)明涉及的高硬度金屬基/金剛石涂層的制備方法是在冷噴涂的過程中同步引入激光輻照,激光的加熱作用使高硬度金屬粉末和基體材料得到軟化,實現(xiàn)了高硬度金屬基/金剛石復(fù)合涂層的有效沉積,而且由于高硬度金屬粉末塑性變形較充分,其作為粘結(jié)相與金剛石顆粒結(jié)合良好,涂層中的金剛石顆粒不易脫落;(3)本發(fā)明在冷噴涂的過程中引入激光,激光對高硬度金屬粉末的軟化作用,大大降低了其臨界沉積速度,提高了涂層沉積效率。此外,由于冷噴涂技術(shù)的低溫沉積特性,涂層中熱應(yīng)力較小,且涂層中的殘余應(yīng)力主要為壓應(yīng)力,涂層不易開裂。因此,綜合激光的軟化作用和冷噴涂的固有特性,實現(xiàn)了高硬度金屬基/金剛石的高效制備,涂層厚度顯著增加;(4)本發(fā)明采用脈沖激光毛化技術(shù)代替?zhèn)鹘y(tǒng)的噴砂技術(shù)對基材表面進行粗化處理,避免了噴砂處理時基材表面容易被雜質(zhì)污染的問題,從而提高了高硬度金屬基/金剛石復(fù)合涂層與基體的結(jié)合強度,涂層不易剝落。此外,實現(xiàn)基材表面粗糙度處理和涂層沉積的一體化加工,提升了技術(shù)和設(shè)備的自動化、集成化和高效化。(5)本發(fā)明涉及的技術(shù)可以快速在金屬基體上獲得毫米級的高硬度金屬基/金剛石復(fù)合涂層,基體熱影響小,適合于薄壁類、精度要求高的零件的修復(fù)和強化。附圖說明圖1為涂層制備方法示意圖;圖2為Ni60粉末和金剛石粉末球磨混合后的SEM圖片;圖3為添加20wt%金剛石Ni60基復(fù)合涂層宏觀形貌;圖4為添加20wt%金剛石Ni60基復(fù)合涂層顯微組織;圖5為Ni60基/金剛石復(fù)合涂層中金剛石與Ni60的結(jié)合圖片;圖6為添加40wt%金剛石Ni60基復(fù)合涂層宏觀形貌;圖7為添加20wt%金剛石Ni60基激光熔覆涂層宏觀形貌;圖8為添加20wt%金剛石Ni60基激光熔覆涂層截面顯微組織。具體實施方式下面結(jié)合附圖對本發(fā)明的具體實施方式做一個詳細的說明。實例1:選用Ni60粉末作為粘結(jié)相與金剛石顆?;旌?,Ni60粉末平均粒度為18μm,金剛石選用-400目;Ni60粉末和金剛石粉末以4:1質(zhì)量比在行星式球磨機中混合,球料比為30:1,球磨速度500r/min,混合時間2h,球磨后復(fù)合粉末的微觀形貌如圖2所示;基材選用100×50×10mm的45#鋼板;利用激光毛化與激光輔助冷噴涂技術(shù)同步制備高硬度金屬基/金剛石復(fù)合涂層;激光毛化采用光纖激光器,激光脈沖能量密度為106W/cm2,脈寬為1ms,波長為1510nm;噴涂載氣為3MPa壓縮氮氣,載氣預(yù)熱溫度為500℃;采用閉環(huán)反饋控溫模式調(diào)整半導(dǎo)體激光功率,控制溫度為800℃;毛化處理激光光斑與噴涂區(qū)域間隔5mm,噴涂距離為40mm,復(fù)合噴涂移動速度30mm/s。20wt%金剛石含量的Ni60基/金剛石復(fù)合涂層宏觀形貌如圖3所示,復(fù)合涂層厚度超過1mm,涂層與基體結(jié)合很好。涂層中金剛石體積比超過45%,金剛石顆粒分布均勻,復(fù)合涂層致密無明顯的孔隙,如圖4所示;由于掃描速度快,激光加熱溫度低,涂層中金剛石沒有熱分解,最大限度地保持金剛石的硬度及形貌,金剛石顆粒與Ni60基體相結(jié)合良好,如圖5所示。實例2:選用Ni60粉末為粘結(jié)相與金剛石顆粒混合,Ni60粉末平均粒度為18μm,金剛石選用-400目;Ni60粉末和金剛石粉末以3:2質(zhì)量比在振動式球磨機中進行混合,球料比為30:1,球磨時間為60min,振動頻率為800r/min;基材選用100×50×10mm的不銹鋼板,利用激光毛化與激光輔助冷噴涂技術(shù)同步制備高硬度金屬基/金剛石復(fù)合涂層;激光毛化采用光纖激光器,激光脈沖能量密度為106W/cm2,脈寬為1ms,波長為1510nm;噴涂載氣為3MPa壓縮氮氣,載氣預(yù)熱溫度為550℃;采用閉環(huán)反饋控溫模式調(diào)整半導(dǎo)體激光功率,控制溫度為800℃;毛化處理激光光斑與噴涂區(qū)域間隔5mm,噴涂距離40mm,復(fù)合噴涂移動速度30mm/s。40wt%金剛石含量的Ni60基/金剛石復(fù)合涂層宏觀形貌如圖6所示,涂層厚度超過1mm,涂層與基體結(jié)合很好。涂層中金剛石體積比超過45%,且分布均勻;復(fù)合涂層相比冷噴涂致密,沒有明顯的孔隙;由于掃描速度快,激光熱量積累少,涂層中金剛石沒有出現(xiàn)熱分解,最大限度地保持金剛石的硬度及形貌,涂層耐磨性好。實例3:選用stellite20粉末為粘結(jié)相與金剛石顆?;旌?,stellite20粉末平均粒度為20μm,金剛石選用-400目;stellite20粉末和金剛石粉末以4:1質(zhì)量比在振動式球磨機中進行混合,球料比為60:1,球磨時間為60min,振動頻率為1200r/min;基材選用45#鋼棒;利用激光毛化與激光輔助冷噴涂技術(shù)同步制備高硬度金屬基/金剛石復(fù)合涂層;激光毛化采用光纖激光器,激光脈沖能量密度為106W/cm2,脈寬為1.5ms,波長為1640nm;噴涂載氣為3MPa壓縮氮氣,載氣預(yù)熱溫度為600℃;采用閉環(huán)反饋控溫模式調(diào)整半導(dǎo)體激光功率,控制溫度為900℃;毛化處理激光光斑與噴涂區(qū)域間隔5mm,噴涂距離30mm,復(fù)合噴涂移動速30mm/s。20wt%金剛石含量的stellite20基/金剛石復(fù)合涂層厚度超過1mm,涂層與基體結(jié)合很好,涂層中金剛石體積比超過45%,且分布均勻;復(fù)合涂層相比冷噴涂層致密,沒有明顯的孔隙和裂紋;由于掃描速度快,激光熱量累積較少,涂層中金剛石沒有出現(xiàn)熱分解,最大限度地保持了金剛石的硬度及形貌。實例4:選用stellite20粉末為粘結(jié)相與金剛石顆?;旌?,stellite20粉末平均粒度為20μm,金剛石選用-400目;stellite20粉末和金剛石粉末以3:2質(zhì)量比在行星式球磨機中混合,球料比為40:1,球磨速度600r/min,混合時間1h;基材選用100×50×10mm的17-4PH鋼板;利用激光毛化與激光輔助冷噴涂技術(shù)同步制備高硬度金屬基/金剛石復(fù)合涂層;激光毛化采用光纖激光器,激光脈沖能量密度為106W/cm2,脈寬為1.5ms,波長為1640nm;噴涂載氣為3MPa壓縮氮氣,載氣預(yù)熱溫度為600℃;采用閉環(huán)反饋控溫模式調(diào)整半導(dǎo)體激光功率,控制溫度為900℃;毛化處理激光光斑與噴涂區(qū)域間隔8mm,噴涂距離30mm,復(fù)合噴涂移動速度30mm/s。40wt%金剛石含量的stellite20基/金剛石復(fù)合涂層厚度超過1mm,涂層與基體結(jié)合很好,涂層中金剛石體積比超過45%,且分布均勻;復(fù)合涂層相比冷噴涂層致密,沒有明顯的孔隙和裂紋;由于掃描速度快,激光熱量累積較少,涂層中金剛石沒有明顯的熱分解,最大限度保持金剛石的硬度及形貌。實例5:選用Ni50粉末為粘結(jié)相與金剛石顆?;旌?,Ni50粉末平均粒度為20μm,金剛石選用-400目;Ni60粉末和金剛石粉末以7:3質(zhì)量比在行星式球磨機中混合,球料比為30:1,球磨時間為2h,轉(zhuǎn)速為400r/min,獲得混合均勻的復(fù)合粉末;基材選用100×50×10mm的2Cr13鋼板;利用激光毛化與激光輔助冷噴涂技術(shù)同步制備高硬度金屬基/金剛石復(fù)合涂層;激光毛化采用光纖激光器,激光脈沖能量密度為106W/cm2,脈寬為1.5ms,波長為1640nm;載氣為3MPa壓縮氮氣,載氣預(yù)熱溫度為500℃;采用閉環(huán)反饋控溫模式調(diào)整半導(dǎo)體激光功率,控制溫度為800℃;毛化處理激光光斑與噴涂區(qū)域間隔8mm,噴涂距離30mm,復(fù)合噴涂移動速度40mm/s。30wt%金剛石含量的Ni50基/金剛石復(fù)合涂層厚度超過1mm,涂層與基體結(jié)合很好,涂層中金剛石體積比超過45%,且分布均勻;復(fù)合涂層相比冷噴涂層致密,沒有明顯的孔隙和裂紋;由于掃描速度快,激光熱量累積較少,涂層中金剛石沒有明顯的熱分解,最大限度地保持金剛石的硬度及形貌。實例6(對比例):選用Ni60粉末作為粘結(jié)相與金剛石顆粒混合,Ni60粉末平均粒度為18μm,金剛石選用-400目;Ni60粉末和金剛石粉末以4:1質(zhì)量比在行星式球磨機中混合,球料比為30:1,球磨速率100r/min,混合時間0.5h;基材選用100×50×10mm的45#鋼板,表面利用噴砂技術(shù)除油除銹處理,噴砂使用24目白剛玉,噴砂壓力0.8MPa;利用激光熔覆技術(shù)制備金屬基/金剛石復(fù)合涂層;工藝參數(shù)為:激光功率1.2kW,熔覆速度10mm/s,送粉率15g/min,熔覆過程使用氬氣保護同軸送粉熔覆。20.wt%金剛石含量的Ni60基/金剛石復(fù)合熔覆涂層顯微組織如圖7所示,熔覆涂層表面形貌如圖8所示。顯然在熔覆過程中金剛石燒蝕和碳化嚴重,涂層表面有明顯的孔洞且疏松;相比激光毛化與激光輔助冷噴涂技術(shù)同步復(fù)合制備的20.wt%金剛石含量的涂層,熔覆涂層中金剛石含量明顯下降,金剛石在熔覆熔池中燒蝕成為球形,且涂層中金剛石碳化嚴重。需要強調(diào)的是:以上僅是本發(fā)明的較佳實施例而已,并非對本發(fā)明作任何形式上的限制,凡是依據(jù)本發(fā)明的技術(shù)實質(zhì)對以上實施例所作的任何簡單修改、等同變化與修飾,均仍屬于本發(fā)明技術(shù)方案的范圍內(nèi)。