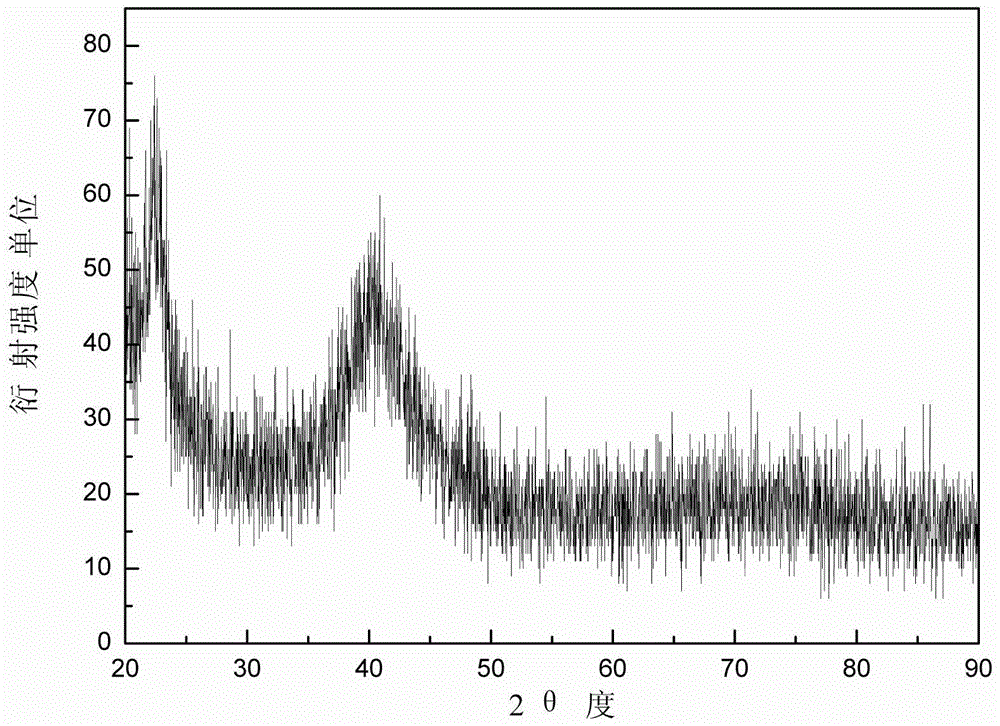
本發(fā)明涉及材料制備技術領域,尤其涉及一種鈦基非晶纖維及其制備方法。
背景技術:非晶合金有著與液態(tài)近似的結構而且晶體中不存在位錯、晶界等缺陷,這使得非晶合金具有一些優(yōu)異的力學性能。如高強度、高硬度、高彈性應變等特性,非晶合金還能夠像塑料一樣易于鑄造,這種優(yōu)異的性能和成型能力使其可以替代某些傳統(tǒng)材料。Ti基非晶合金由于比強度高、價格低廉而逐漸受到各國學者的重視,其中,鈦-鋯-鎳-銅-鈹(Ti-Zr-Ni-Cu-Be)系合金由于Be元素的存在具有較高的非晶形成能力而備受關注,但是體系中的Be是劇毒元素,限制了這類非晶合金的廣泛應用。金屬纖維同有機和無機纖維一樣具有獨特的性能和廣泛的用途。金屬纖維具有良好的導電、導熱、導磁和耐高溫性能,而且制造方法較簡單,成本價格便宜。以金屬纖維為填充劑的復合材料在民用行業(yè)如電子、化工、機械、紡織、食品、醫(yī)藥部門開拓了廣闊的應用前景。在民用工業(yè)上應用金屬纖維復合材料也勢在必行。金屬纖維作為一種新興的纖維材料已經受到各行各業(yè)的重視。熔體抽拉技術成為制備金屬纖維的一種直接或者近凈成形方法。其他制備金屬纖維的方法主要有水紡法、玻璃包裹。水紡法冷卻能力較差,而且冷卻液會與Ti、Al等金屬發(fā)生發(fā)硬,因此不適合Ti基合金纖維的制備。玻璃包裹法,要求合金熔體熔化溫度與玻璃軟化溫度一致,合金與玻璃的熱膨脹系數也必須相似,否則合金絲的連續(xù)性受到限制,Ti基合金熔點相對高,而且Ti易于石英發(fā)生反應。與玻璃包裹法和水紡法相比,熔體抽拉技術可以作為TiZr非晶態(tài)合金直接成形方法,對合金的熔煉要求較低,普適性高。熔體抽拉技術中采用石英坩堝存放塊體母合金,再將母合金制成纖維,制作塊體合金采用的一般是銅模,直接通過感應線圈加熱澆注到銅模中快速冷卻,但制備纖維通常采用石英制的坩堝,Ti是高活性、親氧性的,Ti基合金會和石英制成的坩堝發(fā)生反應,一旦發(fā)生反應,無法制成Ti基纖維。
技術實現(xiàn)要素:本發(fā)明實施例提供一種鈦基非晶纖維及其制備方法,用以解決現(xiàn)有技術中存在制備不含有Be的Ti基非晶纖維時容易與石英坩堝發(fā)生反應,無法制成Ti基纖維的問題。本發(fā)明實施例提供一種鈦基非晶纖維及其制備方法,包括以下兩個方面:第一方面,一種鈦基非晶纖維,該鈦基非晶纖維的化學通式以及原子百分數包括:Ti(58-x)Zr(20+x1)Cu(8+x2)Ni(9+x3),其中,0≤x≤8,0≤x1≤10,0≤x2≤5,0≤x3≤3,且58-x、20+x1、8+x2、9+x3之和為100。第二方面,一種鈦基非晶纖維的制備方法,該方法包括:在保護氣體或真空條件下,將塊體Ti(58-x)Zr(20+x1)Cu(8+x2)Ni(9+x3)合金通過激光加熱形成部分融化的Ti(58-x)Zr(20+x1)Cu(8+x2)Ni(9+x3)合金熔體,并連續(xù)進給;通過金屬輪盤切削Ti(58-x)Zr(20+x1)Cu(8+x2)Ni(9+x3)合金熔體,抽拉并快速冷卻形成鈦基非晶纖維Ti(58-x)Zr(20+x1)Cu(8+x2)Ni(9+x3)。本發(fā)明有益效果包括:克服了不含Be的鈦基非晶纖維難以成形的問題,通過激光部分加熱母合金,避免熔融合金與坩堝的直接接觸,避免鈦基非晶合金與石英管制的坩堝發(fā)生反應導致Ti基纖維制備失敗的問題,且采用消耗高純度氬的方式消耗制備設備中的氧氣,避免高活性,親氧性的Ti基纖維與氧氣發(fā)生反應。本發(fā)明制備出的Ti-Zr-Cu-Ni纖維為非晶態(tài),斷裂強度大于1100MPa,表現(xiàn)出了良好的力學性能,晶化起始溫度為431℃,表現(xiàn)出良好的熱穩(wěn)定性,且纖維連續(xù)長度大于40cm。附圖說明圖1為本發(fā)明實施例中的鈦基非晶纖維的制備方法流程圖;圖2為本發(fā)明實施例中的Ti58Zr25Cu8Ni9纖維X射線衍射(XRD)圖;圖3為本發(fā)明實施例中的Ti50Zr30Cu10Ni10纖維差熱分析曲線圖;圖4為本發(fā)明實施例中的Ti55Zr20Cu13Ni12合金纖維拉伸曲線。具體實施方式為了解決制備不含Be的鈦基非晶纖維難以形成非晶纖維的實現(xiàn)方案,本發(fā)明實施例提供了一種鈦基非晶纖維及其制備方法,以下結合說明書附圖對本發(fā)明的優(yōu)選實施例進行說明。本發(fā)明實施例提供一種鈦基非晶纖維,該鈦基非晶纖維的化學通式以及原子百分數包括:Ti(58-x)Zr(20+x1)Cu(8+x2)Ni(9+x3),其中,0≤x≤8,0≤x1≤10,0≤x2≤5,0≤x3≤3,且58-x、20+x1、8+x2、9+x3之和為100。本發(fā)明實施例制備出的這種鈦基纖維為非晶態(tài),直徑20微米至120微米的絲狀,其連續(xù)長度超過40厘米;斷裂強度大于1100MPa,表現(xiàn)出良好的力學性能,晶化起始溫度為431℃,表現(xiàn)出良好的熱穩(wěn)定性。參閱圖1所示,本發(fā)明實施例提供的上述鈦基非晶纖維的制備方法,具體包括以下步驟:步驟110:在保護氣體或真空條件下,將塊體Ti(58-x)Zr(20+x1)Cu(8+x2)Ni(9+x3)合金通過激光加熱形成部分融化的Ti(58-x)Zr(20+x1)Cu(8+x2)Ni(9+x3)合金熔體,并連續(xù)進給。具體的,在保護氣體或真空條件下,將連續(xù)進給的塊體Ti(58-x)Zr(20+x1)Cu(8+x2)Ni(9+x3)合金通過激光加熱形成部分融化的Ti(58-x)Zr(20+x1)Cu(8+x2)Ni(9+x3)合金熔體之前,還包括步驟:按照Ti單質為58-x、Zr單質為20+x1、Cu單質為8+x2以及Ni單質為9+x3的原子百分比進行混合。將混合后所得的混料在磁控鎢極電弧熔煉爐中反復熔煉三次,保證合金元素均勻混合,并吸鑄形成塊體Ti(58-x)Zr(20+x1)Cu(8+x2)Ni(9+x3)合金,這種塊體Ti(58-x)Zr(20+x1)Cu(8+x2)Ni(9+x3)合金為直徑9mm的棒狀材料。將直徑9mm的塊體Ti(58-x)Zr(20+x1)Cu(8+x2)Ni(9+x3)非晶合金用電火花線切割成3厘米至7厘米長的圓柱,并用砂紙打磨、超聲波清洗并干燥,放置于內徑為10毫米至15毫米的石英坩堝中。保護氣體或真空條件下,包括:將熔體抽拉裝置抽真空至10-3Pa時,充入高純度氬氣至熔體抽拉裝置內氣壓為-0.5MPa;繼續(xù)將熔體抽拉裝置內氣壓抽真空至10-3Pa,充入高純度氬氣。通常將熔體抽拉裝置抽真空至10-3Pa時即可充氬氣實驗,Ti基合金是高活性、親氧性的,制備Ti基纖維時,需要通過消耗氬氣來保證將裝置內的氧氣都抽走了。通過激光加熱裝置,將塊體Ti(58-x)Zr(20+x1)Cu(8+x2)Ni(9+x3)合金部分熔化,保持塊體Ti(58-x)Zr(20+x1)Cu(8+x2)Ni(9+x3)合金連續(xù)進給,將連續(xù)進給的塊體Ti(58-x)Zr(20+x1)Cu(8+x2)Ni(9+x3)非晶合金的進給速度設置為5-12毫米/分鐘。步驟120:通過金屬輪盤切削Ti(58-x)Zr(20+x1)Cu(8+x2)Ni(9+x3)合金熔體,抽拉并快速冷卻形成鈦基非晶纖維Ti(58-x)Zr(20+x1)Cu(8+x2)Ni(9+x3)。具體的,金屬輪盤切削Ti(58-x)Zr(20+x1)Cu(8+x2)Ni(9+x3)合金熔體時,將金屬輪盤的轉速設置為2000轉/分鐘(r/min)至3000r/min。金屬輪盤為銅合金制成,啟動滾輪,保持轉速為2000r/min至3000r/min。將Ti(58-x)Zr(20+x1)Cu(8+x2)Ni(9+x3)合金熔體與金屬輪盤接觸后,高速旋轉的金屬輪盤帶動Ti(58-x)Zr(20+x1)Cu(8+x2)Ni(9+x3)合金熔體甩出,并快速凝固形成纖維,制備過程中保持Ti(58-x)Zr(20+x1)Cu(8+x2)Ni(9+x3)合金熔體進給速度不變。待合金熔體消耗完成后,停止進給,關閉激光加熱,停止金屬滾輪轉動。通過調整工藝參數,可以制備出不同直徑的鈦基非晶纖維。下面結合附圖,用具體實施例對本發(fā)明提供的方法及裝置和相應系統(tǒng)進行詳細描述。實施例1,(1)按照設定原子百分比為58、25、8、9的比例將單質Ti、Zr、Ni、Cu配置為Ti58Zr25Cu8Ni9合金,并在磁控鎢極電弧熔煉爐中吸鑄形成合金棒狀材料,在此實施例1中將Ti58Zr25Cu8Ni9合金稱為母合金。(2)將制備的母合金棒材用電火花線切割切成3-7cm長的小柱,并用砂紙打磨、超聲波清洗、干燥后,放置于熔體抽拉設備的坩堝中。(3)將熔體抽拉裝置抽真空至10-3Pa時,充入高純度氬氣至熔體抽拉裝置內氣壓為-0.5MPa;繼續(xù)將熔體抽拉裝置內氣壓抽真空至10-3Pa,充入高純度氬氣。(4)設置銅輪轉速為2800r/min,母合金進給速度為5mm/min。(5)金屬輥輪為銅合金,啟動輥輪,保持轉速為2800r/min。(6)啟動激光加熱裝置,將坩堝加熱,將合金融化,保持合金熔體溫度在合金熔點以上150℃-200℃,并保溫。母合金熔化后啟動進給,保持進給速度為5mm/min。(7)纖維成形。熔融母合金與銅輪接觸后,高速旋轉銅輪帶動母合金甩出,并快速凝固形成纖維,并保持母合金進給速度不變。(8)結束。合金熔體消耗完成后,停止進給,并關閉激光加熱,以及停止輥輪轉動,制備出連續(xù)Ti58Zr25Cu8Ni9合金纖維絲。參閱圖2所示,這一圖譜說明組織結構中不存在大的長程有序結構,可以初步斷定為非晶態(tài)結構,說明利用熔體抽拉工藝制備出了不含Be的Ti基非晶合金。實施例2,(1)按照設定原子百分比為50、30、10、10的比例將單質Ti、Zr、Ni、Cu配置為Ti50Zr30Cu10Ni10非晶合金,并在磁控鎢極電弧熔煉爐中吸鑄形成合金棒狀材料,在此實施例2中將Ti50Zr30Cu10Ni10非晶合金稱為母合金。(2)將制備的母合金棒材用電火花線切割切成3-7cm長的小柱,并用砂紙打磨、超聲波清洗、干燥后,放置于熔體抽拉設備的坩堝中。(3)將熔體抽拉裝置抽真空至10-3Pa時,充入高純度氬氣至熔體抽拉裝置內氣壓為-0.5MPa;繼續(xù)將熔體抽拉裝置內氣壓抽真空至10-3Pa,充入高純度氬氣。(4)設置銅輪轉速為3000r/min,母合金進給速度為7mm/min。(5)金屬輥輪為銅合金,啟動輥輪,保持轉速為3000r/min。(6)啟動激光加熱裝置,將坩堝加熱,將合金融化,保持合金熔體溫度在合金熔點以上150℃-200℃,并保溫。母合金熔化后啟動進給,保持進給速度為7mm/min。(7)纖維成形。熔融母合金與銅輪接觸后,高速旋轉銅輪帶動母合金甩出,并快速凝固形成纖維,并保持母合金進給速度不變。(8)結束。合金熔體消耗完成后,停止進給,并關閉激光加熱,以及停止輥輪轉動,制備出連續(xù)Ti50Zr30Cu10Ni10合金纖維絲,制備出的纖維表面光滑。參閱圖3所示,這類纖維的起始晶化溫度為431℃。實施例3,(1)按照設定原子百分比為55、20、13、12的比例將單質Ti、Zr、Ni、Cu配置為Ti55Zr20Cu13Ni12合金,并在磁控鎢極電弧熔煉爐中吸鑄形成合金棒狀材料,在此實施例3中將Ti55Zr20Cu13Ni12非晶合金稱為母合金。(2)將制備的母合金棒材用電火花線切割切成3-7cm長的小柱,并用砂紙打磨、超聲波清洗、干燥后,放置于熔體抽拉設備的坩堝中。(3)將熔體抽拉裝置抽真空至10-3Pa時,充入高純度氬氣至熔體抽拉裝置內氣壓為-0.5MPa;繼續(xù)將熔體抽拉裝置內氣壓抽真空至10-3Pa,充入高純度氬氣。(4)設置銅輪轉速為2600r/min,母合金進給速度為7mm/min。(5)金屬輥輪為銅合金,啟動輥輪,保持轉速為2600r/min。(6)啟動激光加熱裝置,將坩堝加熱,將合金融化,保持合金熔體溫度在合金熔點以上150℃-200℃,并保溫。母合金熔化后啟動進給,保持進給速度為7mm/min。(7)纖維成形。熔融母合金與銅輪接觸后,高速旋轉銅輪帶動母合金甩出,并快速凝固形成纖維,并保持母合金進給速度不變。(8)結束。合金熔體消耗完成后,停止進給,并關閉激光加熱,以及停止輥輪轉動,制備出連續(xù)Ti55Zr20Cu13Ni12合金纖維絲。這種纖維的拉伸斷口形貌,為明顯的剪切斷裂,微觀形貌上有脈狀花樣和細小的類似河流花樣的分支。參閱圖4所示,直徑為38微米的鈦基非晶纖維的抗拉強度為1130MPa,直徑為50微米的鈦基非晶纖維的抗拉強度為1190MPa。本發(fā)明實施例提供的方案,克服了不含Be的鈦基非晶纖維難以成形的問題,非晶塊體比非晶纖維容易成形,只要大于臨界冷卻速率都可以得到塊體非晶,做塊體非晶時采用銅模,通過感應加熱后澆注到銅模中快冷即可。而本發(fā)明實施例中的鈦基非晶纖維,采用石英管做坩堝,會發(fā)生化學反應,鈦基合金的熔點較高,熔化后容易與石英發(fā)生反應,但本發(fā)明采用激光加熱時鈦基合金只是局部熔化,不會像采用感應加熱時鈦基合金熔融成液體,液面與石英管壁接觸時容易與石英發(fā)生反應,因此做鈦基非晶纖維會失敗。綜上所述,本發(fā)明實施例提供的方案,克服了不含Be的鈦基非晶纖維難以成形的問題,避免鈦基非晶合金與石英制的坩堝發(fā)生反應導致Ti基纖維制備失敗的問題,且采用消耗高純度氬的方式消耗制備設備中的氧氣,避免高活性,親氧性的Ti與氧氣發(fā)生反應。本發(fā)明制備出的Ti-Zr-Cu-Ni纖維為非晶態(tài),斷裂強度大于1100MPa,表現(xiàn)出了良好的力學性能,晶化起始溫度為431℃,表現(xiàn)出良好的熱穩(wěn)定性,且纖維連續(xù)長度大學40cm。顯然,本領域的技術人員可以對本發(fā)明進行各種改動和變型而不脫離本發(fā)明的精神和范圍。這樣,倘若本發(fā)明的這些修改和變型屬于本發(fā)明權利要求及其等同技術的范圍之內,則本發(fā)明也意圖包含這些改動和變型在內。