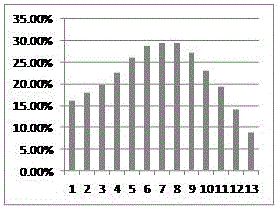
本發(fā)明屬于鋼鐵冶金領(lǐng)域,具體涉及一種在爐卷軋機上生產(chǎn)超長(150~220m)薄規(guī)格(5~8mm)海洋工程用EH36鋼的方法。
背景技術(shù):船板鋼是國民經(jīng)濟發(fā)展所依賴的重要鋼鐵材料,近年來中國造船業(yè)發(fā)展迅速,年造船量已經(jīng)占到世界造船總量比例突破10%。隨著船舶工業(yè)的快速發(fā)展,造船用鋼需求也在不斷增加,占造船用材料80%的船板鋼需求飛速增長。目前,為了節(jié)省下游企業(yè)的費用,船板軋件出現(xiàn)多元化需求,為了最大程度提高生產(chǎn)效益,降低成本,有利于更快更好的組批,節(jié)省船板排產(chǎn)時間,長、寬、薄等船板鋼軋件生產(chǎn)是目前生產(chǎn)船板鋼鐵企業(yè)長期努力方向。而生產(chǎn)這些極限規(guī)格的鋼板也是鋼鐵企業(yè)成分設(shè)計、工藝控制、現(xiàn)場生產(chǎn)水平綜合能力的體現(xiàn)。目前南鋼在爐卷軋機做了相當類似研究工作,在《寬厚板》上公開了(5~15)mm×3200mm寬薄規(guī)格Q345E鋼板的生產(chǎn),該鋼板的主要成分為,C:0.10~0.12%,Si:0.30~0.40%,Mn:1.40~1.50%,Nb+V+Ti:0.030~0.040%,碳當量Ceq目標值為0.40。中國專利CN102179406A公開了“單機架爐卷軋機薄規(guī)格高強度鋼板軋制工藝”,適用于長坯料(10~17m)生產(chǎn)薄規(guī)格≤10mm高強度(480MPa≤σs≤1000MPa)鋼板,通過控制出鋼溫度、卷取爐溫度、未道次壓下量等,減少鋼板頭、中、尾性能差,來保證鋼板的板形。然而,在該發(fā)明中沒有交代此類(480MPa≤σs≤1000MPa)鋼板的交貨狀態(tài),通常此類鋼板是在后期的調(diào)質(zhì)處理達到鋼板的強度性能。中國專利CN102699022A公開了“一種單機架爐卷軋機熱軋極限規(guī)格鋼卷控制方法”。通過結(jié)合成分,開發(fā)層流冷卻系統(tǒng)頭尾避讓功能、調(diào)整軋制工藝來獲得≥360MPa級別極限規(guī)格鋼卷性能合格。但是通過控制鋼板加熱爐火焰的調(diào)整會增加現(xiàn)場操作難度以及人工干攏因素,因而只適用于小批量試制,不適于大批量鋼板的生產(chǎn),且鋼材的性能穩(wěn)定性也得不到保證。成分設(shè)計中,碳當量較高,不適合作為低碳當量船板鋼的生產(chǎn)使用。該發(fā)明僅提及如何提高強度,而對影響鋼板非常重要的韌性沒有涉及。實際生產(chǎn)中,除了上述問題,生產(chǎn)薄規(guī)格EH36鋼板還存在如下技術(shù)難點:一、卷軋鋼板表面質(zhì)量控制,爐卷軋制生產(chǎn)超長薄規(guī)格鋼板,受爐內(nèi)氣氛的影響,鋼板表面易形成表面缺陷,如麻點,麻坑等;二、低碳當量爐卷軋制生產(chǎn)EH36鋼板強度的控制,為了保證船板具有良好的沖擊性能、焊接性能以及低成本控制,并且滿足TMCPEH36船規(guī)供貨要求;三、超長薄規(guī)格鋼板整板性能均勻性控制;四、超薄規(guī)格EH36船板正公差控制。為了克服現(xiàn)有技術(shù)的不足,克服相應(yīng)的技術(shù)難點,本發(fā)明通過成分設(shè)計及工藝優(yōu)化,提出了一種在爐卷軋機上生產(chǎn)超長薄規(guī)格EH36鋼的方法。
技術(shù)實現(xiàn)要素:本發(fā)明的目的在于根據(jù)上述現(xiàn)有現(xiàn)狀提供一種超長薄規(guī)格EH36鋼及其在卷爐卷軋機上的生產(chǎn)方法,通過化學成分設(shè)計,提高加熱爐溫度、合理分配平軋+卷軋軋制道次,以達到合適的終軋溫度,得到表面質(zhì)量良好,外形尺寸易于控制、性能良好的超長薄規(guī)格EH36鋼板。本發(fā)明解決上述問題所采用的技術(shù)方案為:一種超長薄規(guī)格EH36鋼,該鋼板的化學成分按質(zhì)量百分比計為C:0.05~0.09%,Mn:1.20~1.60%,Si:0.10~0.25%,Nb:0.015~0.030%,Ti:0.010~0.020%,Al:0.020~0.040%,Ceq≤0.38,余量為Fe及不可避免的雜質(zhì)元素。鋼板的主要晶相組織為先共析鐵素體以及彌散分布的珠光體,平均晶粒尺寸介于5~8μm。進一步地,鋼板的厚度為4.75mm~8mm,鋼板長度最長可達221m;鋼板的屈服強度介于358~405MPa,抗拉強度介于528~572MPa,延伸率為29.5~33.5%,屈強比≤71%,沖擊韌性滿足-40℃沖擊功>66J。本發(fā)明EH36鋼的化學成分是這樣確認的:C:影響鋼力學性能的主要元素,當碳含量低于0.05%則強度低,當碳含量介于0.09%~0.12%時,介于包晶區(qū)間,包晶區(qū)間鋼冶煉控制難度上升,當含量>0.12%時,因船板鋼對36Kg強度級的碳當量有限制,碳含量越高對焊接、耐蝕性都有負面影響。故本發(fā)明將C含量區(qū)間設(shè)定在0.05~0.09%。Mn:能夠推遲奧氏體向鐵素體的轉(zhuǎn)變,可以加大終軋溫度窗口,細化鐵素體,提高強度和韌性。通常,屈服強度介于235MPa級碳-錳中厚鋼板的錳含量通?!?.60wt%。與碳對Ae3溫度影響一樣,錳含量越高,Ae3溫度越低,當錳的含量高于1.50wt%時,Ae3溫度很容易低于820℃,這樣不利于鋼板軋制時終軋溫度的控制,特別是板形難以控制的薄規(guī)格鋼板的生產(chǎn)控制。因此,本發(fā)明軋制方法更適用于錳含量在1.20~1.50wt%范圍內(nèi)的中厚板。Si:硅是煉鋼脫氧的必要元素,也具有一定的固溶強化作用,在船級社規(guī)范與GB712中限定硅含量范圍是0.10~0.50%,為了改善鋼板表面質(zhì)量,將Si含量按下限控制,本發(fā)明中將硅限定在0.10~0.25%的范圍內(nèi)。Nb:微量鈮含量,便可在船板鋼中起到溶質(zhì)拖曳作用和Nb(C,N)對奧氏體晶界的釘扎作用,抑制形變奧氏體的再結(jié)晶,使得薄規(guī)格船板在軋制過程中,提高非再結(jié)晶區(qū)的溫度,減小部分再結(jié)晶區(qū)間,有利于熱連軋工藝的軋制。細化鐵素體晶粒,但過高的鈮,不光提高EH36鋼的生產(chǎn)成本,也會促進連鑄坯產(chǎn)生表面裂紋,因此,本發(fā)明鈮含量控制在0.015~0.030%的范圍內(nèi)。Ti:鈦是用來固定鋼中的氮元素,在適當條件下,鈦/氮形成氮化鈦,阻止鋼坯在加熱、軋制、焊接過程中晶粒長大,改善母材和焊接熱影響區(qū)的韌性。鈦低于0.006%時,固氮效果差,超過0.030%時,固氮效果達到飽和,過剩的鈦會使鋼的韌性惡化。當鋼中的Ti、N原子之比為1:1時,相于Ti、N重量之比為3.42,TiN粒子最為細小且分布彌散,對高溫奧氏體晶粒的細化作用最強,不僅可獲得優(yōu)良的韌性,而且能夠?qū)崿F(xiàn)30KJ/cm以上的大線能量焊接。故在本發(fā)明中,結(jié)合鋼中氮含量,將鈦含量控制在0.010%~0.020%。Al:鋁是煉鋼過程中一種重要的脫氧元素,即使在鋼水中加入微量的鋁,也可以有效減少鋼中的夾雜物含量,并細化晶粒。但過多的鋁會促進夾雜物以及連鑄坯產(chǎn)生表面裂紋的形成,降低連鑄工藝性能。因此,本發(fā)明中鋁含量控制在0.020~0.040%。Ceq:船級社對TMCP生產(chǎn)的船板鋼有碳當量限制,要求≤0.38,為了易于組爐生產(chǎn),一種成分多種交貨狀態(tài)生產(chǎn),故本發(fā)明將碳當量限制在Ceq≤0.38。以適應(yīng)多種厚度規(guī)格的EH36鋼板生產(chǎn),同樣,本發(fā)明適用于薄規(guī)格Q345E等鋼種的生產(chǎn)。本發(fā)明的另一目的是提供一種在卷爐卷軋機上制備所述超長薄規(guī)格EH36鋼的方法,具體步驟如下:(1)150mm連鑄坯軋制:將按組分配好的原料冶煉鋼水,鋼水依次經(jīng)過KR預(yù)脫硫→BOF轉(zhuǎn)爐冶煉→LF精煉→RH真空脫氣→連鑄→堆緩冷制備連鑄坯,連鑄坯的厚度為150mm±10mm;(2)加熱:軋前連鑄坯進加熱爐加熱,鋼坯出鋼時爐氣溫度為1240℃~1260℃,通常爐氣溫度高于鋼板實際溫度10~20℃,提高加熱爐溫度,減少材料在硅尖晶石形成溫度區(qū)間停留時間,改善鋼板表面質(zhì)量;(3)軋鋼:在3500爐卷軋機上采取平軋+卷軋的方式對鋼坯進行軋制,軋制目標厚度為4.75mm~8mm、最大長度為221m的EH36船板鋼,平軋+卷軋的總軋制道次數(shù)為11~13,其中,對于目標鋼板成品的寬度大于等于3m的鋼板,為了保證鋼板的板形,將鋼板的軋制設(shè)定為13道次,先平軋后卷軋,提高平軋道次數(shù),減少卷軋道次數(shù),卷軋前鋼坯的厚度控制在10~11mm,按照壓下率先低后高再低的原則控制單道次軋制的壓下率;平軋末道次鋼板的厚度為10~11mm,平軋開軋溫度介于1000~1100℃,平軋第3~6道次的單道次壓下量在20%~30%,卷軋的末道次壓下率≤8%,在平軋第1至3道次時對鋼坯表面高壓水除鱗,此時鋼板較厚,受高壓水除鱗降溫不均勻?qū)е碌挠绊戄^??;卷軋的開軋溫度為780~900℃,其中,對于厚度大于等于4.75mm小于6mm的鋼板的終軋溫度控制在750~800℃,對于厚度大于等于6mm小于等于8mm的鋼板的終軋溫度控制在850~900℃,平軋+卷軋的軋制總時間控制在5~8min,減少超長軋件在卷爐里的停留總時間,改善鋼板表面質(zhì)量。(4)冷卻:對于厚度大于等于6mm小于等于8mm的鋼板,終冷溫度控制在680~720℃,對于厚度大于等于4.75mm小于6mm的鋼板,因為鋼板本身溫度下降較快,對鋼板終冷上限溫度不作要求,控制鋼坯的溫度下限不得低于600℃。本發(fā)明具有如下特點:1、本發(fā)明成分簡單,在普通C-Mn鋼的基礎(chǔ)上,僅添加了含量很少的微合金元素Nb,成本低廉,微合金元素Nb擴大奧氏體非再晶區(qū)間,可以使得卷軋時爐氣溫度設(shè)定較高,改善薄規(guī)格的板開。同時,低碳設(shè)計路線有利于鋼板沖擊韌性的提高。低硅含量的控制,結(jié)合加熱爐溫度的提高,改善鋼板的表面質(zhì)量。2、本發(fā)明通過提高加熱爐溫度、提高整個鋼板軋制時的道次溫度,使得鋼板中心偏析,微觀偏析得以有效改善,鋼板奧氏體組織得到充分均勻。3、本發(fā)明通過提高加熱爐溫度、卷取爐爐氣溫度,克服了150mm連鑄坯軋制8mm以下薄規(guī)格的鋼板時終軋溫度過低,鋼板頭、中、尾溫差過大而導(dǎo)致的板形問題以及性能不均的問題。本發(fā)明可以節(jié)省鋼板切頭、切尾量,提高成材率。4、本發(fā)明通過提高平軋道次數(shù),減少卷軋道次數(shù),并提高中間道次的壓下量(主要是平軋時的壓下量),有效的細化晶粒,最終長軋件鋼板組織晶粒細小均勻,鐵素體、珠光體彌散均勻分布,帶狀組織控制良好。本發(fā)明減少鋼坯在爐內(nèi)停留時間,改善鋼板表面質(zhì)量。本發(fā)明適用于采用150mm的鋼坯生產(chǎn)薄規(guī)格(厚度介于4.75~8mm)超長軋件(最長可達221m)EH36船板,也可以推廣至屈服強度36Kg級的橋梁、高層建筑、結(jié)構(gòu)用鋼超薄規(guī)格超長軋件以熱軋、TMCP狀態(tài)交貨的生產(chǎn)。附圖說明圖1為本發(fā)明實施例4的鋼的單道次軋制的壓下率分配示意圖;圖2為本發(fā)明實施例5的鋼的單道次軋制的壓下率分配示意圖;圖3為本發(fā)明實施例1的鋼板在正火狀態(tài)下的金相組織。具體實施方式以下結(jié)合附圖實施例對本發(fā)明作進一步詳細描述。本發(fā)明各實施例所對應(yīng)的超長薄規(guī)格EH36鋼的化學成分見表1,表中數(shù)據(jù)為各元素的質(zhì)量百分比含量,剩余為Fe及不可避免的雜質(zhì)元素。表1表中Ceq:%。鋼板的冶煉工藝如下:(1)150mm連鑄坯軋制:將按組分配好的原料冶煉鋼水,鋼水依次經(jīng)過KR預(yù)脫硫→BOF轉(zhuǎn)爐冶煉→LF精煉→RH真空脫氣→連鑄→堆緩冷制備連鑄坯,冶煉三爐鋼約450噸,連鑄坯的厚度為150mm。(2)加熱:軋前連鑄坯進加熱爐加熱,鋼坯出鋼時爐氣溫度為1240℃~1260℃,通常爐氣溫度高于鋼板實際溫度10~20℃,提高加熱爐溫度,減少材料在硅尖晶石形成溫度區(qū)間停留時間,改善鋼板表面質(zhì)量。(3)軋鋼:在3500爐卷軋機上采取平軋+卷軋的方式對鋼坯進行軋制,軋制目標厚度為4.75mm~8mm、最大長度為221m的EH36船板鋼,平軋+卷軋的總軋制道次數(shù)為11~13,其中,對于目標鋼板成品的寬度大于等于3m的鋼板,為了保證鋼板的板形,將鋼板的軋制設(shè)定為13道次,先平軋后卷軋,提高平軋道次數(shù),減少卷軋道次數(shù),將將原5道次平軋+6道次卷軋優(yōu)化為6道次平軋+5道次卷軋;對于超3m寬的薄規(guī)格鋼板,原6道次平軋+7道次卷軋優(yōu)化為7道次平軋+6道次卷軋,提高平軋道次次數(shù),可以加快軋制過程中的溫度降低,特別是7~8mm鋼板的軋制,提高軋制效率,減少軋制道次,減少鋼坯在卷軋爐里的停留總時間,提高鋼材的表面質(zhì)量。卷軋前鋼坯的厚度控制在10~11mm,按照壓下率先低后高再低的原則控制單道次軋制的壓下率,最后一道次控制≤8%。本發(fā)明增加中間3~6道次的道次壓下量,降低最后一個道次的壓下量,細化組織晶粒,保證板形。高壓水除鱗系統(tǒng)在第1、3道次投用。軋制總時間控制在5~8min。提高中間道次的壓下量,圖1為實施例4的6mm鋼的單道次軋制的壓下率分配,其中第3、4、5平軋道次壓下率介于20~30%。圖2為實施例5的單道次壓下率分配。平軋末道次鋼板的厚度為10~11mm,平軋開軋溫度介于1000~1100℃,平軋第3~6道次的單道次壓下量在20%~30%。利用卷取爐在軋制過程中的保溫作用,同時在不影響最終產(chǎn)品性能的情況下,適當提高加熱爐溫度,提高卷軋時的爐溫,卷軋的開軋溫度為780~900℃,其中,對于厚度大于等于4.75mm小于6mm的鋼板的終軋溫度控制在750~800℃,對于厚度大于等于6mm小于等于8mm的鋼板的終軋溫度控制在850~900℃。具體軋制工藝參數(shù)如表2所示,表2(4)冷卻:對于厚度大于等于6mm小于等于8mm的鋼板,終冷溫度控制在680~720℃,對于厚度大于等于4.75mm小于6mm的鋼板,因為鋼板本身溫度下降較快,對鋼板終冷上限溫度不作要求,控制鋼坯的溫度下限不得低于600℃。本發(fā)明通過上述工藝控制,所得鋼板板形良好,表面光潔,無麻點麻坑現(xiàn)象。鋼板具體性能頭、中、尾強度性能差較小,具體如表3所示。從表3可以看出,按照本發(fā)明各實施例中鋼材拉伸性能中的屈服強度、抗拉強度、延伸率以及屈強比達到船級社規(guī)范要求以及GB712標準中EH36要求,屈服強度介于358~405MPa,抗拉強度介于528~572MPa,延伸率優(yōu)異為29.5~33.5%,屈強比≤71%。此外,-40℃低溫沖擊性能優(yōu)異,-40℃的沖擊值折合標準值>66J。鋼板表面質(zhì)量良好,板形優(yōu)異。鋼材的生產(chǎn)具有工藝穩(wěn)定,工藝窗口較大,易于生產(chǎn)控制的優(yōu)點。在本發(fā)明的化學成分體系與工藝下,獲得鋼材的組織主要由先共析鐵素體以及彌散分布的珠光體組織組成。典型組織如附圖3所示。粒組織細小均勻,平均晶粒尺寸介于5~8μm,珠光體未連成條帶狀,而是沿等軸鐵素體晶界處彌散分布,這種軟硬組織有利于在保證鋼材強度的前提下,獲得良好的低溫韌性,使得強韌性達到良好匹配。保證EH36在海洋工程中低溫條件下的使用性能。本發(fā)明各實施例鋼材熱處理前后的力學性能見表3表3注:薄規(guī)格鋼板采取5×10×10mm沖擊試樣,最小平均沖擊功為標準沖擊功的2/3。