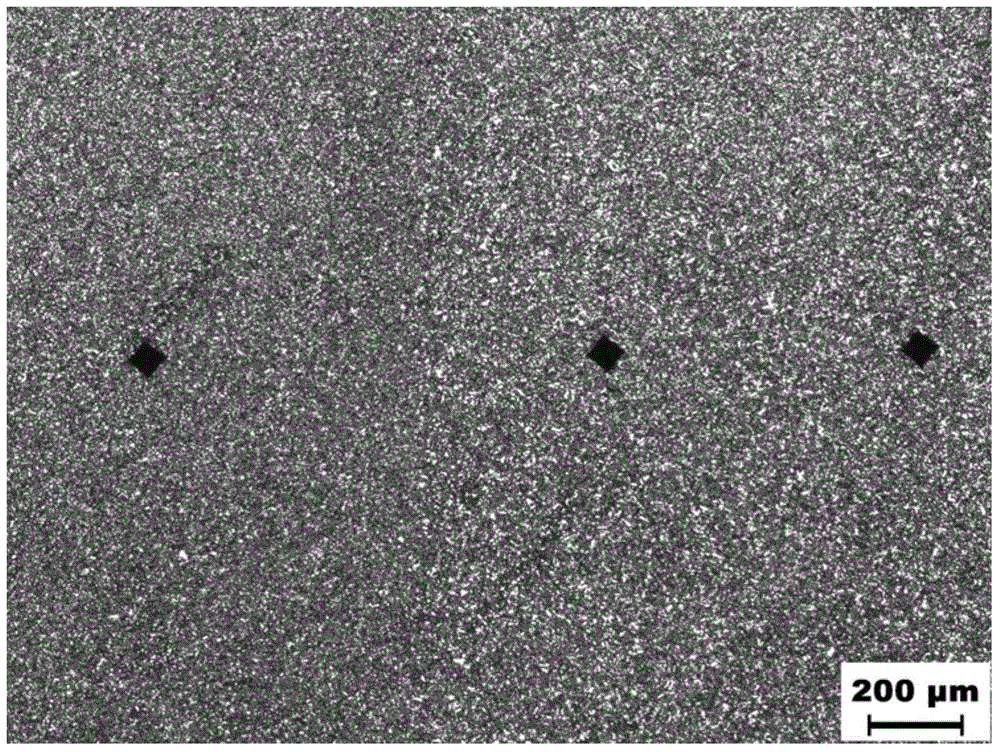
本發(fā)明屬于挖掘設(shè)備技術(shù)領(lǐng)域,尤其涉及一種梯度硬質(zhì)合金、制備方法及截齒頭。
背景技術(shù):礦用截齒是采煤及巷道掘進(jìn)機(jī)械中的易損件之一,是落煤及碎煤的主要工具,由于其工作條件的因素,礦用截齒也是礦山機(jī)械更換最頻繁的零部件之一。中國(guó)是煤礦消耗大國(guó),相應(yīng)的,礦用截齒的消耗量也非常大。大量的礦用截齒消耗不僅增加采煤成本、影響煤碳生產(chǎn)的經(jīng)濟(jì)效益,而且還會(huì)因?yàn)楦鼡Q截齒的時(shí)間增加而降低生產(chǎn)效率。因此,它的性能好壞直接影響采煤機(jī)械生產(chǎn)能力的發(fā)揮、功率的消耗、工作平穩(wěn)性和其他相關(guān)零部件的使用壽命。目前市場(chǎng)上所用的礦用截齒一般是由齒柄、齒體及齒頭構(gòu)成。截齒頭是礦用截齒的主要工作部位,它也是決定礦用截齒的機(jī)械性能及使用壽命的關(guān)鍵部位。礦用截齒的使用工況相當(dāng)復(fù)雜,環(huán)境惡劣,需要截齒頭既滿足耐磨性,又具有較好的韌性,能夠保證足夠長(zhǎng)的掘進(jìn)能力。即,要求截齒頭同時(shí)具有高強(qiáng)度和高硬度。目前,現(xiàn)有的截齒頭多為鍛造成型的30CrMn鋼、Si鋼、42CrM鋼。上述材料韌性較好,在采掘時(shí)很少發(fā)生斷裂,但是這些材料為了便于鍛造成型以鉆孔鑲焊硬質(zhì)合金,限制了合金元素加入量,其硬度受到影響,使其耐磨性能不好,限制了其在采掘作業(yè)時(shí)的工作效率。
技術(shù)實(shí)現(xiàn)要素:本發(fā)明的目的在于提供一種梯度硬質(zhì)合金、制備方法及截齒頭,本發(fā)明提供的梯度硬質(zhì)合金同時(shí)具有高硬度和高強(qiáng)度。本發(fā)明提供一種梯度硬質(zhì)合金,由硬度層單片模坯和強(qiáng)度層單片模坯交疊復(fù)合得到,所述硬度層單片模坯包括90~94wt%的WC,5~8wt%的Co,余量為TaC;所述強(qiáng)度層單片模坯包括84~88wt%的WC,10~15wt%的Co,余量為TaC。優(yōu)選的,所述硬度層單片模坯的厚度為0.1~10mm。優(yōu)選的,所述強(qiáng)度層單片模坯的厚度為0.1~10mm。優(yōu)選的,所述強(qiáng)度層單片模坯與硬度層單片模坯的厚度比為1:(0.5~2)。本發(fā)明提供一種梯度硬質(zhì)合金的制備方法,包括以下步驟:A)將硬度層混合料進(jìn)行注射成型,得到硬度層單片模坯,將強(qiáng)度層混合料進(jìn)行注射成型,得到強(qiáng)度層單片模坯,所述硬度層混合料包括90~94wt%的WC,5~8wt%的Co,余量的TaC,所述強(qiáng)度層混合料包括84~88wt%的WC,10~15wt%的Co,余量的TaC;B)將所述硬度層單片模坯和強(qiáng)度層單片模坯交疊,進(jìn)行溫壓成型,得到梯度硬質(zhì)合金坯體;C)將所述梯度硬質(zhì)合金坯體進(jìn)行燒結(jié),得到梯度硬質(zhì)合金。優(yōu)選的,所述步驟A)中注射成型的溫度為80~170℃。優(yōu)選的,所述步驟B)中溫壓成型的溫度為150~300℃。優(yōu)選的,所述步驟C)中燒結(jié)的溫度為1300~1450℃;所述燒結(jié)的時(shí)間為60~90min。本發(fā)明提供一種截齒頭,包括梯度和復(fù)合在所述基體上的梯度硬質(zhì)合金,所述梯度硬質(zhì)合金為上文所述的梯度硬質(zhì)合金或上文所述的制備方法得到的梯度硬質(zhì)合金;所述基體包括84~88wt%的WC,10~15wt%的Co,余量為TaC。優(yōu)選的,所述梯度硬質(zhì)合金的高度為所述截齒頭高度的1/3~1/2;所述基體的高度為所述截齒頭高度的1/2~2/3。申請(qǐng)人研究發(fā)現(xiàn),梯度功能復(fù)合材料(FGM)與均一材料、復(fù)合材料不同。它是選用兩種(或多種)性能不同的材料,通過連續(xù)地改變這兩種(或多種)材料的組成和結(jié)構(gòu),使其界面消失導(dǎo)致材料的性能隨著材料的組成和結(jié)構(gòu)的變化而緩慢變化。由于FGM的材料組分是在一定的空間方向上連續(xù)變化的特點(diǎn),因此它能有效地克服傳統(tǒng)復(fù)合材料的不足:1)將FGM用作界面層來連接不相容的兩種材料,可以大大地提高粘結(jié)強(qiáng)度;2)將FGM用作界面層可以減小殘余應(yīng)力和熱應(yīng)力;3)將FGM用作界面層可以消除連接材料中界面交叉點(diǎn)以及應(yīng)力自由端點(diǎn)的應(yīng)力奇異性;4)用FGM代替?zhèn)鹘y(tǒng)的均勻材料,既可以增強(qiáng)連接強(qiáng)度也可以減小裂紋驅(qū)動(dòng)力。有鑒于此,本發(fā)明提供了一種梯度硬質(zhì)合金,由硬度層單片模坯和強(qiáng)度層單片模坯交疊復(fù)合得到,所述硬度層單片模坯包括90~94wt%的WC,5~8wt%的Co,余量為TaC;所述強(qiáng)度層單片模坯包括84~88wt%的WC,10~15wt%的Co,余量為TaC。本發(fā)明利用兩種分別具有高強(qiáng)度和高硬度的混合料制備出硬度和強(qiáng)度呈梯度分布的材料,使本發(fā)明提供的梯度硬質(zhì)合金同時(shí)具有高強(qiáng)度和高硬度,實(shí)驗(yàn)結(jié)果表明,本發(fā)明提供的梯度硬質(zhì)合金的硬度大于91HRA,強(qiáng)度大于3600KN/mm2。本發(fā)明還提供了一種梯度硬質(zhì)合金的制備方法,本發(fā)明將注射成型和溫壓成型復(fù)合使用,使硬度層單片模坯和強(qiáng)度層單片模坯之間的結(jié)合自然過渡,融為一體,無任何孔隙等缺陷出現(xiàn)。附圖說明為了更清楚地說明本發(fā)明實(shí)施例或現(xiàn)有技術(shù)中的技術(shù)方案,下面將對(duì)實(shí)施例或現(xiàn)有技術(shù)描述中所需要使用的附圖作簡(jiǎn)單地介紹,顯而易見地,下面描述中的附圖僅僅是本發(fā)明的實(shí)施例,對(duì)于本領(lǐng)域普通技術(shù)人員來講,在不付出創(chuàng)造性勞動(dòng)的前提下,還可以根據(jù)提供的附圖獲得其他的附圖。圖1為本發(fā)明實(shí)施例1得到的截齒頭的結(jié)構(gòu)示意圖;圖2為本發(fā)明實(shí)施例1得到的截齒頭中強(qiáng)度層和硬度層交界處的金相圖(200μm);圖3為本發(fā)明實(shí)施例1得到的截齒頭中強(qiáng)度層和硬度層交界處的金相圖(10μm)。具體實(shí)施方式本發(fā)明提供了一種梯度硬質(zhì)合金,由硬度層單片模坯和強(qiáng)度層單片模坯交疊復(fù)合得到,所述硬度層單片模坯包括90~94wt%的WC,5~8wt%的Co,余量為TaC;所述強(qiáng)度層單片模坯包括84~88wt%的WC,10~15wt%的Co,余量為TaC。本發(fā)明提供的梯度硬質(zhì)合金同時(shí)具有高強(qiáng)度和高硬度。本發(fā)明提供的梯度硬質(zhì)合金由硬度層單片模坯和強(qiáng)度層單片模坯交疊復(fù)合得到,所述硬度層單片模坯包括90~94wt%的WC,5~8wt%的Co,余量為TaC,優(yōu)選包括91~93wt%的WC,6~7wt%的Co,余量為TaC,更優(yōu)選包括92wt%的WC,6.5wt%的Co,余量為TaC;所述硬度層單片模坯的厚度優(yōu)選為0.1~10mm,更優(yōu)選為0.5~8mm,最優(yōu)選為0.6~4mm。在本發(fā)明中,所述強(qiáng)度層單片模坯包括84~88wt%的WC,10~15wt%的Co,余量為TaC,優(yōu)選包括85~87wt%的WC,11~14wt%的Co,余量的TaC,更優(yōu)選包括86wt%的WC,12~13wt%的Co,余量的TaC;所述強(qiáng)度層單片模坯的厚度優(yōu)選為0.1~10mm,更優(yōu)選為0.5~8mm,最優(yōu)選為0.6~4mm。本發(fā)明優(yōu)選將若干個(gè)強(qiáng)度層單片模坯和若干個(gè)硬度層單片模坯依次交疊,進(jìn)行復(fù)合,形成硬度層和強(qiáng)度層依次交疊的梯度硬質(zhì)合金。在本發(fā)明中,所述強(qiáng)度層單片模坯和硬度層單片模坯的厚度比優(yōu)選為1:(0.5~2),更優(yōu)選為1:1;本發(fā)明對(duì)所述強(qiáng)度層單片模坯和硬度層單片模坯的個(gè)數(shù)沒有特殊的限制,根據(jù)實(shí)際需要選擇合適的個(gè)數(shù)即可,本發(fā)明優(yōu)選采用一個(gè)強(qiáng)度層單片模坯疊放一個(gè)硬度層單片模坯,依次類推,得到一層強(qiáng)度層和一層硬度層均勻交替疊加的梯度硬質(zhì)合金,也就是說,在所述梯度硬質(zhì)合金中的硬度層和強(qiáng)度層的厚度相同的情況下,得到的梯度硬質(zhì)合金能夠具有更好的性能,因?yàn)檫@樣的梯度硬質(zhì)合金的梯度分布均勻,不會(huì)造成實(shí)際作業(yè)中局部出現(xiàn)脫落或崩裂的情況。在能保證其耐磨的同時(shí),又具有好的沖擊韌性。本發(fā)明提供了一種梯度硬質(zhì)合金的制備方法,包括以下步驟:A)將硬度層混合料進(jìn)行注射成型,得到硬度層單片模坯,將強(qiáng)度層混合料進(jìn)行注射成型,得到強(qiáng)度層單片模坯,所述硬度層混合料包括90~94wt%的WC,5~8wt%的Co,余量的TaC,所述強(qiáng)度層混合料包括84~88wt%的WC,10~15wt%的Co,余量的TaC;B)將所述硬度層單片模坯和強(qiáng)度層單片模坯交疊,進(jìn)行溫壓成型,得到梯度硬質(zhì)合金坯體;C)將所述梯度硬質(zhì)合金坯體進(jìn)行燒結(jié),得到梯度硬質(zhì)合金。本發(fā)明將硬度層混合料進(jìn)行注射成型,得到硬度層單片模坯,所述硬度層混合料包括90~94wt%的WC,5~8wt%的Co,余量的TaC,優(yōu)選包括91~93wt%的WC,6~7wt%的Co,余量為TaC,更優(yōu)選包括92wt%的WC,6.5wt%的Co,余量為TaC;在本發(fā)明中,所述硬度層混合料優(yōu)選還包括發(fā)泡劑和成型劑,所述發(fā)泡劑優(yōu)選包括高密度聚乙烯和/或聚乙二醇,所述成型劑優(yōu)選包括高溫蠟和/或低溫蠟,所述WC、Co和TaC的質(zhì)量之和與所述發(fā)泡劑和成型劑的質(zhì)量之比優(yōu)選為(75~85):(5~15):(1~10)。本發(fā)明對(duì)所述發(fā)泡劑和成型劑的來源沒有特殊的限制,采用普通市售商品即可。在本發(fā)明中,所述硬度層混合料注射成型的溫度優(yōu)選為80~170℃,更優(yōu)選為90~160℃,最優(yōu)選為100~150℃;本發(fā)明對(duì)所述注射成型的壓力沒有特殊的限制,根據(jù)產(chǎn)品的尺寸和密度進(jìn)行相應(yīng)的調(diào)整;具體的,本發(fā)明優(yōu)選將所述硬度層混合料倒入粉末冶金注塑機(jī)的進(jìn)料口,設(shè)定分段加熱的程序,使得混合料在注塑機(jī)模腔中熔化、排氣及碾壓破碎,最后從出料口出來,進(jìn)入通過三維軟件設(shè)計(jì)好的組合模具中,根據(jù)產(chǎn)品的尺寸和密度,配以一定的壓力,如,直徑為50mm,高度為30mm的產(chǎn)品,在注塑擠壓成型過程中需要的壓力為14MPa。第一次擠壓成型底部流道和凹型腔,隨后將模具冷卻到80~100℃后解壓;裝配型腔陰模和復(fù)合模,再次注入混合料,模體經(jīng)過二次感應(yīng)升溫至150~170℃,配以成型壓力第二次擠壓成型上部包覆蓋及型腔,冷卻后脫模獲得硬度層單片模坯。在本發(fā)明中,所述硬度層單片模坯的厚度優(yōu)選為0.1~10mm,更優(yōu)選為0.5~8mm,最優(yōu)選為0.6~4mm。本發(fā)明將強(qiáng)度層混合料進(jìn)行注射成型,得到強(qiáng)度層單片模坯,所述強(qiáng)度層混合料包括84~88wt%的WC,10~15wt%的Co,余量為TaC,優(yōu)選包括85~87wt%的WC,11~14wt%的Co,余量的TaC,更優(yōu)選包括86wt%的WC,12~13wt%的Co,余量的TaC。在本發(fā)明中,所述強(qiáng)度層混合料優(yōu)選還包括發(fā)泡劑和成型劑,所述發(fā)泡劑優(yōu)選包括高密度聚乙烯和/或聚乙二醇,所述成型劑優(yōu)選包括高溫蠟和/或低溫蠟,所述WC、Co和TaC的質(zhì)量之和與所述發(fā)泡劑和成型劑的質(zhì)量之比優(yōu)選為(70~80):(5~15):(5~15)。本發(fā)明對(duì)所述發(fā)泡劑和成型劑的來源沒有特殊的限制,采用普通市售商品即可。在本發(fā)明中,所述強(qiáng)度層混合料注射成型的溫度優(yōu)選為80~170℃,更優(yōu)選為90~160℃,最優(yōu)選為100~150℃;本發(fā)明對(duì)所述注射成型的壓力沒有限制,按照產(chǎn)品的尺寸和密度進(jìn)行調(diào)整即可;具體的,本發(fā)明優(yōu)選將所述強(qiáng)度層混合料倒入粉末冶金注塑機(jī)的進(jìn)料口,設(shè)定分段加熱的程序,使得混合料在注塑機(jī)模腔中熔化、排氣及碾壓破碎,最后從出料口出來,進(jìn)入通過三維軟件設(shè)計(jì)好的組合模具中,配以一定的壓力,第一次擠壓成型底部流道和凹型腔,隨后將模具冷卻到80~100℃后解壓;裝配型腔陰模和復(fù)合模,再次注入混合料,模體經(jīng)過二次感應(yīng)升溫至150~170℃,配以成型壓力第二次擠壓成型上部包覆蓋及型腔,冷卻后脫模獲得硬度層和強(qiáng)度層。所述強(qiáng)度層單片模坯的厚度優(yōu)選為0.1~10mm,更優(yōu)選為0.5~8mm,最優(yōu)選為0.6~4mm。得到所述硬度層單片模坯和強(qiáng)度層單片模坯后,本發(fā)明將所述硬度層單片模坯和強(qiáng)度層單片模坯依次交疊,進(jìn)行溫壓成型,得到梯度硬質(zhì)合金坯體。本發(fā)明優(yōu)選將所述硬度層單片模坯和強(qiáng)度層單片模坯交替疊放,即,一層硬度層單片模坯疊加一層強(qiáng)度層單片模坯,依次疊加若干層后,然后進(jìn)行溫壓成型,形成硬度層和強(qiáng)度層,得到梯度硬質(zhì)合金坯體,在本發(fā)明中,所述溫壓成型的溫度優(yōu)選為150~300℃,更優(yōu)選為160~280℃,最優(yōu)選為150~250℃;本發(fā)明對(duì)所述溫壓成型的壓力沒有特殊的限制。本發(fā)明對(duì)所述硬度層單片模坯和強(qiáng)度層單片模坯的層數(shù)沒有特殊的限制,根據(jù)實(shí)際需要進(jìn)行選擇即可。完成所述溫壓成型后,本發(fā)明優(yōu)選將所述梯度硬質(zhì)合金坯體放入真空干燥箱中進(jìn)行加熱處理,以鞏固各層膜坯之間的結(jié)合力。在本發(fā)明中,所述加熱處理的溫度優(yōu)選為200~260℃,更優(yōu)選為220~250℃;所述加熱處理的時(shí)間優(yōu)選為1~3小時(shí),更優(yōu)選為2小時(shí)。本發(fā)明將所述梯度硬質(zhì)合金坯體進(jìn)行燒結(jié),得到梯度硬質(zhì)合金。本發(fā)明優(yōu)選將所述梯度硬質(zhì)合金坯體在汽油中浸泡,然后將浸泡過的梯度硬質(zhì)合金坯體進(jìn)行燒結(jié),得到梯度硬質(zhì)合金。在本發(fā)明中,所述浸泡的時(shí)間優(yōu)選為6~8小時(shí),更優(yōu)選為5~7小時(shí)。本發(fā)明對(duì)所述浸泡用的汽油的種類和來源沒有特殊的限制。傳統(tǒng)硬質(zhì)合金成型劑是石蠟、PEG或橡膠,一般通過預(yù)燒結(jié)進(jìn)行脫除,其過程漫長(zhǎng)且成本高。本發(fā)明在燒結(jié)前將所述梯度硬質(zhì)合金坯體在汽油中浸泡一段時(shí)間,然后再將浸泡過的坯體進(jìn)行燒結(jié),能夠有效脫除成型劑,并且其時(shí)間將大大縮短,節(jié)約制造成本。在本發(fā)明中,所述燒結(jié)的溫度優(yōu)選為1300~1450℃,更優(yōu)選為1350~1400℃;所述燒結(jié)的時(shí)間優(yōu)選為60~90min,更優(yōu)選為70~80min。本發(fā)明優(yōu)選采用真空脫蠟一體爐進(jìn)行所述燒結(jié)。本發(fā)明還提供了一種截齒頭,包括基體和復(fù)合在所述基體上的梯度硬質(zhì)合金,所述梯度硬質(zhì)合金為上述技術(shù)方案中所述的梯度硬質(zhì)合金;所述基體包括84~88wt%的WC,10~15wt%的Co,余量為TaC。參見圖1,圖1為本發(fā)明實(shí)施例1得到的截齒頭的結(jié)構(gòu)示意圖,圖1中,01為梯度硬質(zhì)合金,011為硬度層(黑色條狀部分),012為強(qiáng)度層(白色條狀部分),02為基體,03為應(yīng)力孔。在本發(fā)明中,所述梯度硬質(zhì)合金為上述技術(shù)方案中所述的梯度硬質(zhì)合金,將其打磨成實(shí)際所需的形狀即可,在此不再贅述。在本發(fā)明中,所述基體包括84~88wt%的WC,10~15wt%的Co,余量為TaC,優(yōu)選包括85~87wt%的WC,11~14wt%的Co,余量的TaC,更優(yōu)選包括86wt%的WC,12~13wt%的Co,余量的TaC。在本發(fā)明中,所述梯度硬質(zhì)合金的高度優(yōu)選為所述截齒頭高度的1/3~1/2;所述基體的高度優(yōu)選為所述截齒頭高度的1/2~2/3。本發(fā)明對(duì)所述截齒頭的尺寸及形狀沒有特殊的限制,按照實(shí)際需求選定即可。在本發(fā)明中,所述基體的底部?jī)?yōu)選設(shè)置有應(yīng)力孔,以釋放所述截齒頭工作中的應(yīng)力,所述應(yīng)力孔優(yōu)選設(shè)置在所述基體底部的正中間,所述應(yīng)力孔的直徑優(yōu)選為2~4mm,更優(yōu)選為3mm,所述應(yīng)力孔的高度優(yōu)選為1~3mm,更優(yōu)選為2mm。本發(fā)明優(yōu)選按照以下步驟制備得到截齒頭:1)將強(qiáng)度層混合料進(jìn)行注射成型,得到強(qiáng)度層單片模坯,所述強(qiáng)度層混合料包括84~88wt%的WC,10~15wt%的Co,余量的TaC;2)將所述強(qiáng)度層單片模坯堆疊,得到基體坯體,然后將梯度硬質(zhì)合金坯體與基體層坯體疊放,進(jìn)行溫壓成型,得到截齒頭坯體,所述梯度硬質(zhì)合金坯體為上述技術(shù)方案梯度硬質(zhì)合金的制備方法中步驟B)得到的梯度硬質(zhì)合金;3)將所述截齒頭坯體進(jìn)行燒結(jié),得到截齒頭。在本發(fā)明中,所述步驟1)中強(qiáng)度層混合料注射成型的方法與上述技術(shù)方案中梯度硬質(zhì)合金的制備方法中的步驟A)中的強(qiáng)度層混合料注射成型的方法一致,在此不再贅述。本發(fā)明將所述強(qiáng)度層單片模坯堆疊,得到基體坯體,然后將所述梯度硬質(zhì)合金坯體與基體坯體疊放,進(jìn)行溫壓成型,得到截齒頭坯體。在本發(fā)明中,所述強(qiáng)度層堆疊的層數(shù)和高度沒有具體的限制,使得最終得到的基體層的高度為所述截齒頭高度的1/2~2/3即可。在本發(fā)明中,所述溫壓成型的溫度優(yōu)選為150~300℃,更優(yōu)選為160~280℃,最優(yōu)選為150~250℃;本發(fā)明對(duì)所述溫壓成型的壓力沒有特殊限制。在本發(fā)明中,所述步驟4)中的燒結(jié)與上述技術(shù)方案中梯度硬質(zhì)合金的制備方法中步驟C)中的燒結(jié)的方法一致,在此不再贅述。本發(fā)明優(yōu)選在所述燒結(jié)結(jié)束后進(jìn)行冷卻,得到截齒頭毛坯,將所述毛坯進(jìn)行磨削加工,得到截齒頭。本發(fā)明采用MM2000型滑動(dòng)磨損試驗(yàn)機(jī)進(jìn)行常溫干滑動(dòng)磨損試驗(yàn)。試樣為本發(fā)明得到的截齒頭,尺寸為10mm×10mm×10mm,對(duì)磨環(huán)材料為淬火+低溫回火(硬度HRC53)的42CrMo,法向載荷20Kgf,對(duì)磨環(huán)轉(zhuǎn)速400r/min,磨損時(shí)間60min,總滑動(dòng)距離約3800m。以相對(duì)耐磨性(=標(biāo)樣磨損失重量/試樣磨損失重量)作為材料耐磨性的指標(biāo)。結(jié)果表明,本發(fā)明提供的截齒頭的相對(duì)耐磨性為84.9。本發(fā)明采用20℃恒溫浸泡腐蝕測(cè)試方法,在0.5mol/L鹽酸水溶液中測(cè)試材料的耐蝕性能,以316L不銹鋼為對(duì)比試樣,測(cè)試168小時(shí)浸泡后的腐蝕失重量,以相對(duì)耐蝕性(=標(biāo)樣腐蝕失重量/試樣腐蝕失重量)作為材料耐蝕性的指標(biāo)。結(jié)果表明,本發(fā)明提供的截齒頭的相對(duì)耐腐蝕性為31.4。本發(fā)明按照壓痕法測(cè)定了本發(fā)明得到的截齒頭的硬度,結(jié)果表明,本發(fā)明中截齒頭的硬度大于91HRA。本發(fā)明采用萬能試驗(yàn)機(jī)測(cè)定了本發(fā)明得到的截齒頭的強(qiáng)度,測(cè)試樣條尺寸為8mm×8mm×20mm。在本發(fā)明中,所述強(qiáng)度為抗彎強(qiáng)度,即待測(cè)材料在受到與材料軸線垂直荷載作用下,完全斷裂時(shí)的極限強(qiáng)度??箯潖?qiáng)度存在尺寸效應(yīng)。結(jié)果表明,本發(fā)明中截齒頭的強(qiáng)度大于3600kN/mm2。為了進(jìn)一步說明本發(fā)明,以下結(jié)合實(shí)施例對(duì)本發(fā)明提供的一種梯度硬質(zhì)合金、制備方法及截齒頭進(jìn)行詳細(xì)描述,但不能將其理解為對(duì)本發(fā)明保護(hù)范圍的限定。實(shí)施例1:將85g的牌號(hào)A料、10g的聚乙二醇和5g的高溫蠟混合,得到硬度層混合料;將80g的牌號(hào)B混合料、10g的聚乙二醇和10g的高溫蠟混合,得到強(qiáng)度層混合料;其中牌號(hào)A料中WC的質(zhì)量含量占比為90wt%,Co的質(zhì)量含量為5wt%,余量為TaC;牌號(hào)B料中WC的質(zhì)量含量占比為84wt%,Co的質(zhì)量含量占比為10wt%,余量為TaC。將硬度層混合料和強(qiáng)度層混合料分別進(jìn)行注射成型(將混合料分別倒入粉末冶金注塑機(jī)的進(jìn)料口,設(shè)定分段加熱的程序,在160℃下。使得混合料在注塑機(jī)模腔中熔化、排氣及碾壓破碎,最后從出料口出來,進(jìn)入通過三維軟件設(shè)計(jì)好的組合模具中,配以一定的壓力,第一次擠壓成型底部流道和凹型腔,隨后將模具冷卻到80℃后解壓;裝配型腔陰模和復(fù)合模,再次注入混合料,模體經(jīng)過二次感應(yīng)升溫至150℃,配以成型壓力第二次擠壓成型上部包覆蓋及型腔,冷卻后脫模獲得所需形狀的坯體),然后將得到0.5mm厚的硬度層單片膜坯和0.5mm厚的強(qiáng)度層單片膜坯相互依次交疊,得到具有3cm的梯度層,將所得的梯度層進(jìn)行溫壓處理,即放入真空干燥箱中進(jìn)行加熱處理,加熱溫度為200℃,保溫2h,以鞏固膜坯之間的結(jié)合力。將強(qiáng)度層混合料通過同樣的注射成型工藝制得強(qiáng)度層單片膜坯,然后將強(qiáng)度層單片膜坯堆疊制得基體層,基體高度為3cm。將梯度層與基體層疊在一起(基體層在下,梯度層在上),經(jīng)溫壓處理(溫壓工藝同上)后,獲得所需的復(fù)合坯體。將所述復(fù)合坯體在汽油中浸泡6h,然后將浸泡過的復(fù)合坯體在真空脫蠟一體爐中進(jìn)行燒結(jié),燒結(jié)溫度為1400℃,保溫時(shí)間為60min,燒結(jié)結(jié)束后進(jìn)行冷卻,得到毛坯,將毛坯進(jìn)行磨削加工,得到截齒頭。得到的截齒頭的結(jié)構(gòu)如圖1所示,圖1為本發(fā)明實(shí)施例1得到的截齒頭的結(jié)構(gòu)示意圖。本發(fā)明對(duì)本實(shí)施例得到的截齒頭進(jìn)行了金相分析,如圖2~3所示,圖2為本發(fā)明實(shí)施例1得到的截齒頭中強(qiáng)度層和硬度層交界處的金相圖(200μm);圖3為本發(fā)明實(shí)施例1得到的截齒頭中強(qiáng)度層和硬度層交界處的金相圖(10μm)。通過圖2可以明顯看出硬度層與強(qiáng)度層的顯微結(jié)構(gòu)的區(qū)別,左邊是細(xì)(或超細(xì))晶粒的強(qiáng)度層,它具有高強(qiáng)度,這就保證截齒良好的抗沖擊韌性;右邊為中(或粗)顆粒的硬度層,它具有高硬度,這便給予截齒頭好的耐磨性。通過圖3可以看出硬度層和強(qiáng)度層單片膜坯的交界處過度相當(dāng)自然,毫無違和感。分解處雖然能明顯看出晶粒度不同,但二者粘結(jié)相已經(jīng)融為一體,即單片膜坯之間已完美結(jié)合,無任何孔隙等缺陷出現(xiàn),燒結(jié)后毛坯已形成一個(gè)完整的、機(jī)械性能優(yōu)異的礦用截齒頭。本發(fā)明按照上述技術(shù)方案測(cè)定了截齒頭的相對(duì)耐磨性、相對(duì)耐腐蝕性、硬度和強(qiáng)度,結(jié)果表明,本實(shí)施例得到的截齒頭的相對(duì)耐磨性為84.9,相對(duì)耐腐蝕性為29.9,硬度為90.1HRA;強(qiáng)度為3600KN/mm2。實(shí)施例2:將75g的牌號(hào)A料、10g的聚乙二醇和10g的高溫蠟混合,得到硬度層混合料;將70g的牌號(hào)B混合料、15g的聚乙二醇和15g的高溫蠟混合,得到強(qiáng)度層混合料;其中牌號(hào)A料中WC的質(zhì)量含量占比為94wt%,Co的質(zhì)量含量為5wt%,余量為TaC;牌號(hào)B料中WC的質(zhì)量含量占比為80wt%,Co的質(zhì)量含量占比為15wt%,余量為TaC。將硬度層混合料和強(qiáng)度層混合料分別進(jìn)行注射成型(將混合料分別倒入粉末冶金注塑機(jī)的進(jìn)料口,設(shè)定分段加熱的程序,在150℃下,使得混合料在注塑機(jī)模腔中熔化、排氣及碾壓破碎,最后從出料口出來,進(jìn)入通過三維軟件設(shè)計(jì)好的組合模具中,配以一定的壓力,第一次擠壓成型底部流道和凹型腔,隨后將模具冷卻到100℃后解壓;裝配型腔陰模和復(fù)合模,再次注入混合料,模體經(jīng)過二次感應(yīng)升溫至170℃,配以成型壓力第二次擠壓成型上部包覆蓋及型腔,冷卻后脫模獲得所需形狀的坯體),然后將得到0.5mm厚的硬度層單片膜坯和0.5mm厚的強(qiáng)度層單片膜坯相互依次交疊,得到3cm的梯度層,將所得的梯度層在230℃下進(jìn)行溫壓處理,即放入真空干燥箱中進(jìn)行加熱處理,加熱溫度為260℃,保溫2h,以鞏固膜坯之間的結(jié)合力。將強(qiáng)度層混合料通過同樣的注射成型工藝制得強(qiáng)度層單片膜坯,然后將強(qiáng)度層單片膜坯堆疊制得基體層,基體高度為4cm。將梯度層與基體層疊在一起(基體層在下,梯度層在上),經(jīng)溫壓處理(溫壓工藝同上)后,獲得所需的復(fù)合坯體。將所述復(fù)合坯體在汽油中浸泡8h,然后將浸泡過的復(fù)合坯體在真空脫蠟一體爐中進(jìn)行燒結(jié),燒結(jié)溫度為1400℃,保溫時(shí)間為60min,燒結(jié)結(jié)束后進(jìn)行冷卻,得到毛坯,將毛坯進(jìn)行磨削加工,得到截齒頭。本發(fā)明按照上述技術(shù)方案測(cè)定了截齒頭的相對(duì)耐磨性、相對(duì)耐腐蝕性、硬度和強(qiáng)度,結(jié)果表明,本實(shí)施例得到的截齒頭的相對(duì)耐磨性為81.6,相對(duì)耐腐蝕性為31.4,硬度為89.5HRA;強(qiáng)度為3800KN/MM2。實(shí)施例3:將80g的牌號(hào)A料、14g的聚乙二醇和6g的高溫蠟混合,得到硬度層混合料;將88g的牌號(hào)B混合料、6g的聚乙二醇和6g的高溫蠟混合,得到強(qiáng)度層混合料;其中牌號(hào)A料中WC的質(zhì)量含量占比為93wt%,Co的質(zhì)量含量為5wt%,余量為TaC;牌號(hào)B料中WC的質(zhì)量含量占比為87wt%,Co的質(zhì)量含量占比為10wt%,余量為TaC。將硬度層混合料和強(qiáng)度層混合料分別進(jìn)行注射成型(將混合料分別倒入粉末冶金注塑機(jī)的進(jìn)料口,設(shè)定分段加熱的程序,在120℃下,使得混合料在注塑機(jī)模腔中熔化、排氣及碾壓破碎,最后從出料口出來,進(jìn)入通過三維軟件設(shè)計(jì)好的組合模具中,配以一定的壓力,第一次擠壓成型底部流道和凹型腔,隨后將模具冷卻到100℃后解壓;裝配型腔陰模和復(fù)合模,再次注入混合料,模體經(jīng)過二次感應(yīng)升溫至170℃,配以成型壓力第二次擠壓成型上部包覆蓋及型腔,冷卻后脫模獲得所需形狀的坯體),然后將得到0.5mm厚的硬度層單片膜坯和0.5mm厚的強(qiáng)度層單片膜坯相互依次交疊,得到4cm的梯度層,將所得的梯度層在230℃下進(jìn)行溫壓處理,即放入真空干燥箱中進(jìn)行加熱處理,加熱溫度為260℃,保溫2h,以鞏固膜坯之間的結(jié)合力。將強(qiáng)度層混合料通過同樣的注射成型工藝制得強(qiáng)度層單片膜坯,然后將強(qiáng)度層單片膜坯堆疊制得基體層,基體高度為4cm。將梯度層與基體層疊在一起(基體層在下,梯度層在上),經(jīng)溫壓處理(溫壓工藝同上)后,獲得所需的復(fù)合坯體。將所述復(fù)合坯體在汽油中浸泡7h,然后將浸泡過的復(fù)合坯體在真空脫蠟一體爐中進(jìn)行燒結(jié),燒結(jié)溫度為1400℃,保溫時(shí)間為60min,燒結(jié)結(jié)束后進(jìn)行冷卻,得到毛坯,將毛坯進(jìn)行磨削加工,得到截齒頭。本發(fā)明按照上述技術(shù)方案測(cè)定了截齒頭的相對(duì)耐磨性、相對(duì)耐腐蝕性、硬度和強(qiáng)度,結(jié)果表明,本實(shí)施例得到的截齒頭的相對(duì)耐磨性為79.5,相對(duì)耐腐蝕性為28.8,硬度為90.1HRA;強(qiáng)度為3600KN/MM2。以上所述僅是本發(fā)明的優(yōu)選實(shí)施方式,應(yīng)當(dāng)指出,對(duì)于本技術(shù)領(lǐng)域的普通技術(shù)人員來說,在不脫離本發(fā)明原理的前提下,還可以做出若干改進(jìn)和潤(rùn)飾,這些改進(jìn)和潤(rùn)飾也應(yīng)視為本發(fā)明的保護(hù)范圍。