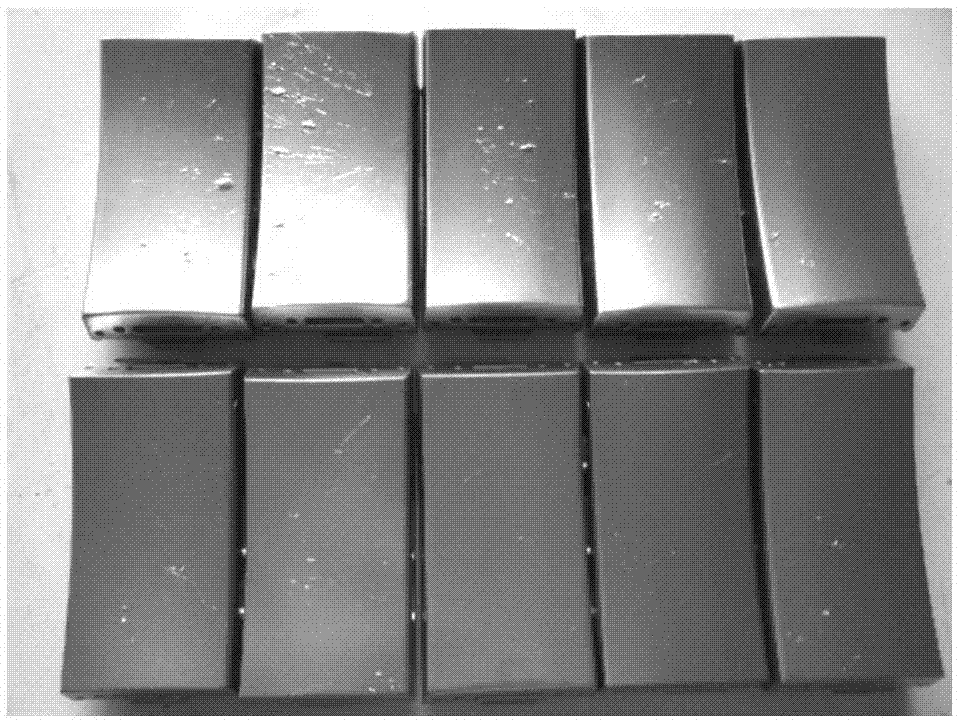
本發(fā)明涉及金屬加工領(lǐng)域,具體地,涉及一種加工壓鑄金屬件的方法。
背景技術(shù):
:壓鑄,全稱為壓力鑄造,是指將熔融合金在高壓、高速條件下填充模具型腔,并在高壓下冷卻成型的鑄造方法,是鑄造工藝中應(yīng)用最廣、發(fā)展速度最快的金屬熱加工成形工藝方法之一。壓鑄作為一種先進(jìn)的有色合金精密零部件成形技術(shù),適應(yīng)了現(xiàn)代制造業(yè)中產(chǎn)品復(fù)雜化、精密化、輕量化、節(jié)能化、綠色化的要求,應(yīng)用領(lǐng)域不斷拓寬。隨著壓鑄設(shè)備和工藝技術(shù)水平不斷提高,壓鑄產(chǎn)品的應(yīng)用范圍在現(xiàn)有基礎(chǔ)上仍將不斷擴(kuò)大。壓鑄金屬件的表面需要進(jìn)一步進(jìn)行噴砂加工,以利于噴漆、噴塑等后續(xù)處理。噴砂是指利用高速砂流的沖擊作用清理和粗化基體表面的過程。噴砂采用壓縮空氣為動(dòng)力,以形成高速噴射束將噴料(銅礦砂、石英砂、金剛砂、鐵砂、海南砂)高速噴射到需要處理的工件表面,使工件表面的外表面的外表或形狀發(fā)生變化,由于磨料對工件表面的沖擊和切削作用,使工件的表面獲得一定的清潔度和不同的粗糙度,使工件表面的機(jī)械性能得到改善,因此提高了工件的抗疲勞性,增加了它和涂層之間的附著力,延長了涂膜的耐久性,也有利于涂料的流平和裝飾。在應(yīng)用噴砂的方式對壓鑄金屬件進(jìn)行加工后,往往會(huì)出現(xiàn)起皮的現(xiàn)象。對于壓鑄件噴砂起皮現(xiàn)象,目前沒有很好的后處理方法。行業(yè)內(nèi)現(xiàn)有的后處理方法是通過控制噴砂工藝,減少噴砂壓力等參數(shù),或者通過更改模具設(shè)計(jì)等;但是,噴砂工藝參數(shù)改變會(huì)導(dǎo)致噴砂的外觀效果達(dá)不到要 求,噴砂效率降低,而且也仍然達(dá)不到很好的消除起皮現(xiàn)象;而改變模具設(shè)計(jì)一方面很難保證重新設(shè)計(jì)的模具不會(huì)再次出現(xiàn)起皮,另一方面,重新更改模具會(huì)大幅度地增加加工成本并且延長加工周期。因此,現(xiàn)有的通過噴砂處理來加工壓鑄金屬件的方法存在難以消除起皮的缺陷。技術(shù)實(shí)現(xiàn)要素:為了克服現(xiàn)有的通過噴砂處理來加工壓鑄金屬件的方法存在難以消除起皮的缺陷,本發(fā)明提供了一種加工壓鑄金屬件的方法。本發(fā)明的發(fā)明人發(fā)現(xiàn),如果在對壓鑄金屬件進(jìn)行噴砂處理之前,通過噴丸處理和拋光處理進(jìn)行表面的預(yù)處理,能夠顯著地降低噴砂處理后的起皮現(xiàn)象的發(fā)生率,由此得到了本發(fā)明。本發(fā)明提供了一種加工壓鑄金屬件的方法,其中,該方法包括如下步驟:(1)將壓鑄金屬件進(jìn)行噴丸處理,得到噴丸處理后的工件;(2)將噴丸處理后的工件進(jìn)行拋光處理,得到拋光處理后的工件;(3)將拋光處理后的工件進(jìn)行噴砂處理,得到噴砂處理后的工件。通過上述技術(shù)方案,本發(fā)明顯著地降低噴砂處理后的起皮現(xiàn)象的發(fā)生率,由此大大提高了加工壓鑄金屬件的成品率。本發(fā)明的其他特征和優(yōu)點(diǎn)將在隨后的具體實(shí)施方式部分予以詳細(xì)說明。附圖說明附圖是用來提供對本發(fā)明的進(jìn)一步理解,并且構(gòu)成說明書的一部分,與下面的具體實(shí)施方式一起用于解釋本發(fā)明,但并不構(gòu)成對本發(fā)明的限制。在附圖中:圖1是實(shí)施例1中經(jīng)過噴丸、拋光和噴砂處理后的壓鑄金屬件的照片。圖2是對比例1中壓鑄金屬件直接進(jìn)行噴砂處理后的照片。圖3是對比例2中壓鑄金屬件經(jīng)過噴丸后直接進(jìn)行噴砂處理后的照片。具體實(shí)施方式以下結(jié)合附圖對本發(fā)明的具體實(shí)施方式進(jìn)行詳細(xì)說明。應(yīng)當(dāng)理解的是,此處所描述的具體實(shí)施方式僅用于說明和解釋本發(fā)明,并不用于限制本發(fā)明。本發(fā)明提供了一種加工壓鑄金屬件的方法,其中,該方法包括如下步驟:(1)將壓鑄金屬件進(jìn)行噴丸處理,得到噴丸處理后的工件;(2)將噴丸處理后的工件進(jìn)行拋光處理,得到拋光處理后的工件;(3)將拋光處理后的工件進(jìn)行噴砂處理,得到噴砂處理后的工件。其中,可能是由于通過噴丸對壓鑄金屬件的表面進(jìn)行了重整修剪,釋放壓鑄金屬件的表面的應(yīng)力,對于直接噴砂會(huì)起皮的地方經(jīng)噴丸會(huì)產(chǎn)生切削修剪而出現(xiàn)一些凹凸等缺陷,再經(jīng)過拋光后可以將噴丸引起的缺陷其去除而平整,最后進(jìn)行噴砂會(huì)顯著降低甚至消除起皮現(xiàn)象。其中,所述噴丸處理的條件沒有特別的要求,可以為本領(lǐng)域能夠用于加工壓鑄金屬件的常規(guī)條件,例如可以包括:噴丸壓力可以為0.1-1MPa,優(yōu)選為0.3-0.7MPa,噴丸時(shí)間為1-10分鐘,優(yōu)選為3-7分鐘。其中,所述噴丸處理所用的丸粒的硬度可以在較大的范圍內(nèi)變化,例如所述噴丸處理所用的丸粒的莫氏硬度可以處于不小于5的范圍,優(yōu)選莫氏硬度處于不小于5.5的范圍;其中,所述噴丸處理所用的丸粒的粒徑可以在較大的范圍內(nèi)變化,例如,所述噴丸處理所用的丸粒的粒徑能夠使得所述丸粒通過50-500目的篩網(wǎng),優(yōu)選通過100-400目的篩網(wǎng)。其中,所述壓鑄金屬件的材料可以為銅基合金、鋯基非晶合金、鈦基 非晶合金和銅基非晶合金中的至少一種。所述壓鑄金屬件的材料可以通過真空熔煉方法熔煉得到。所述壓鑄金屬件可以通過將金屬材料以真空壓鑄方法制備得到。其中,根據(jù)本發(fā)明特別優(yōu)選的一種實(shí)施方式,所述壓鑄金屬件的材料為銅基合金,所述噴丸處理所用的丸粒為鋯珠,所述鋯珠的莫氏硬度可以處于不小于5的范圍內(nèi),所述鋯珠的粒徑能夠使得所述鋯珠通過200-400目的篩網(wǎng)。其中,所述銅基合金的組成可以為各種鋯基非晶合金的組成,例如為含有45-75.9重量%的Cu、21-40重量%的Mn和3.1-15重量%的Al。其中,根據(jù)本發(fā)明特別優(yōu)選的一種實(shí)施方式,所述壓鑄金屬件的材料為鋯基非晶合金,所述噴丸處理所用的丸粒為鋯珠,所述鋯珠的莫氏硬度≥5.5,所述鋯珠的粒徑能夠使得所述鋯珠通過100-200目的篩網(wǎng)。其中,所述鋯基非晶合金的組成可以為各種鋯基非晶合金的組成,例如為含有50-70重量%的Zr、10-40重量%的Cu和1-10重量%的Ni。其中,所述拋光處理可以包括手工拋光、機(jī)械拋光和化學(xué)拋光中的至少一種。其中,所述拋光處理對因噴丸產(chǎn)生的表面凹凸區(qū)域的拋除深度達(dá)到凹面以下。其中,所述噴砂處理的條件沒有特別的要求,可以按照本領(lǐng)域?qū)鸿T金屬件進(jìn)行噴砂加工的各種條件,例如可以包括:噴砂壓力可以為0.1-1MPa,優(yōu)選為0.3-0.7MPa,噴砂時(shí)間可以為1-10分鐘,優(yōu)選為2-7分鐘。其中,所述噴砂處理所用的砂粒為各種常用砂,例如陶瓷砂、玻璃珠和石英砂中的至少一種,硬度可以在較大的范圍內(nèi)變化,例如所述噴砂處理所用的砂粒的莫氏硬度可以處于不小于4的范圍內(nèi),優(yōu)選處于4.5-6的范圍 內(nèi)。其中,所述噴砂處理所用的砂粒的粒徑可以在較大的范圍內(nèi)變化,例如能夠使得所述砂粒通過100-800目的篩網(wǎng),優(yōu)選通過500-700目的篩網(wǎng)。其中,所述噴砂處理后的工件即可作為本發(fā)明的加工后的壓鑄金屬件,可以進(jìn)入后續(xù)工序。以下通過實(shí)施例進(jìn)一步詳細(xì)說明本發(fā)明。實(shí)施例1將銅基合金(組成為Cu75Mn21AL4)壓鑄得到的壓鑄金屬件,置于噴丸機(jī)中進(jìn)行噴丸處理,得到噴丸處理后的工件,其中,噴丸的壓力為0.5MPa,時(shí)間為5分鐘,噴丸處理所用的丸粒為鋯珠,莫氏硬度為5.5,大小為能夠通過300目的篩網(wǎng)。將噴丸處理后的工件進(jìn)行拋光,得到拋光后的工件,其中,所述拋光處理對因噴丸產(chǎn)生的表面凹凸區(qū)域的拋除深度達(dá)到凹面以下。將拋光后的工件置于噴砂機(jī)中進(jìn)行噴砂處理,得到噴砂處理后的工件,其中,噴砂的壓力為0.5MPa,時(shí)間為3分鐘,噴砂處理所用的砂粒為玻璃珠,莫氏硬度為5,大小為能夠通過600目的篩網(wǎng)。上述得到的噴砂處理后的工件即為本實(shí)施例的處理后的工件,本實(shí)施例的處理后的工件的表面照片如圖1所示。對比例1將銅基合金(組成為Cu75Mn21Al4)壓鑄得到的壓鑄金屬件,置于噴砂機(jī)中進(jìn)行噴砂處理,得到噴砂處理后的工件,其中,噴砂的壓力為0.5MPa,時(shí)間為3分鐘,噴砂處理所用的砂粒為玻璃珠,莫氏硬度為5,大 小為能夠通過600目的篩網(wǎng)。上述得到的噴砂處理后的工件即為本對比例的處理后的工件,本對比例的處理后的工件的表面照片如圖2所示。對比例2按照實(shí)施例1的方法對銅基合金進(jìn)行處理,區(qū)別在于:不含有拋光步驟。將銅基合金(組成為Cu75Mn21AL4)壓鑄得到的壓鑄金屬件,置于噴丸機(jī)中進(jìn)行噴丸處理,得到噴丸處理后的工件,其中,噴丸的壓力為0.5MPa,時(shí)間為5分鐘,噴丸處理所用的丸粒為鋯珠,莫氏硬度為5.5,大小為能夠通過300目的篩網(wǎng)。將噴丸處理后的工件直接置于噴砂機(jī)中進(jìn)行噴砂處理,得到噴砂處理后的工件,其中,噴砂的壓力為0.5MPa,時(shí)間為3分鐘,噴砂處理所用的砂粒為玻璃珠,莫氏硬度為5,大小為能夠通過600目的篩網(wǎng)。上述得到的噴砂處理后的工件即為本實(shí)施例的處理后的工件。本對比例的處理后的工件的表面照片如圖3所示。測試實(shí)施例1將實(shí)施例1、對比例1和對比例2各自進(jìn)行100次平行試驗(yàn),統(tǒng)計(jì)起皮個(gè)數(shù),結(jié)果如表1所示。圖1是實(shí)施例1未發(fā)生起皮的工件的照片。圖2是對比例1發(fā)生起皮的工件的照片。圖3是對比例2樣品表面發(fā)生起皮并產(chǎn)生很多坑點(diǎn)的照片。表1組別起皮個(gè)數(shù)未起皮個(gè)數(shù)良率對比例1(未噴丸)673333%實(shí)施例1(有噴丸5min)59595%對比例2(未拋光)554545%根據(jù)表1的數(shù)據(jù)可見,本發(fā)明顯著地降低噴砂處理后的起皮現(xiàn)象的發(fā)生率,由此大大提高了加工壓鑄金屬件的成品率。實(shí)施例2將鋯基非晶合金(組成為Zr55All0Ni5Cu30)壓鑄得到的壓鑄金屬件,置于噴丸機(jī)中進(jìn)行噴丸處理,得到噴丸處理后的工件,其中,噴丸的壓力為0.5MPa,時(shí)間為5分鐘,噴丸處理所用的丸粒為鋯珠,莫氏硬度為6,大小為能夠通過150目的篩網(wǎng)。將噴丸處理后的工件進(jìn)行拋光,得到拋光后的工件,其中,所述拋光處理對因噴丸產(chǎn)生的表面凹凸區(qū)域的拋除深度達(dá)到凹面以下。。將拋光后的工件置于噴砂機(jī)中進(jìn)行噴砂處理,得到噴砂處理后的工件,其中,噴砂的壓力為0.5MPa,時(shí)間為3分鐘,噴砂處理所用的砂粒為陶瓷砂,莫氏硬度為5.5,大小為能夠通過500目的篩網(wǎng)。上述得到的噴砂處理后的工件即為本實(shí)施例的處理后的工件。對比例3將鋯基非晶合金(組成為Zr55All0Ni5Cu30)壓鑄得到的壓鑄金屬件,置于噴砂機(jī)中進(jìn)行噴砂處理,得到噴砂處理后的工件,其中,噴砂的壓力為0.5MPa,時(shí)間為3分鐘,噴砂處理所用的砂粒為陶瓷砂,莫氏硬度為5.5,大小為能夠通過500目的篩網(wǎng)。上述得到的噴砂處理后的工件即為本對比例的處理后的工件。對比例4按照實(shí)施例2的方法對鋯基非晶合金進(jìn)行處理,區(qū)別在于:不含有拋光 步驟。測試實(shí)施例2將實(shí)施例2、對比例3和對比例4各自進(jìn)行100次平行試驗(yàn),統(tǒng)計(jì)起皮個(gè)數(shù),結(jié)果如表2所示。表2組別起皮個(gè)數(shù)未起皮個(gè)數(shù)良率對比例3(未噴丸)792121%實(shí)施例2(有噴丸5min)188280%對比例4(未拋光)653535%根據(jù)表2的數(shù)據(jù)可見,本發(fā)明顯著地降低噴砂處理后的起皮現(xiàn)象的發(fā)生率,由此大大提高了加工壓鑄金屬件的成品率。以上結(jié)合附圖詳細(xì)描述了本發(fā)明的優(yōu)選實(shí)施方式,但是,本發(fā)明并不限于上述實(shí)施方式中的具體細(xì)節(jié),在本發(fā)明的技術(shù)構(gòu)思范圍內(nèi),可以對本發(fā)明的技術(shù)方案進(jìn)行多種簡單變型,這些簡單變型均屬于本發(fā)明的保護(hù)范圍。另外需要說明的是,在上述具體實(shí)施方式中所描述的各個(gè)具體技術(shù)特征,在不矛盾的情況下,可以通過任何合適的方式進(jìn)行組合,為了避免不必要的重復(fù),本發(fā)明對各種可能的組合方式不再另行說明。此外,本發(fā)明的各種不同的實(shí)施方式之間也可以進(jìn)行任意組合,只要其不違背本發(fā)明的思想,其同樣應(yīng)當(dāng)視為本發(fā)明所公開的內(nèi)容。當(dāng)前第1頁1 2 3