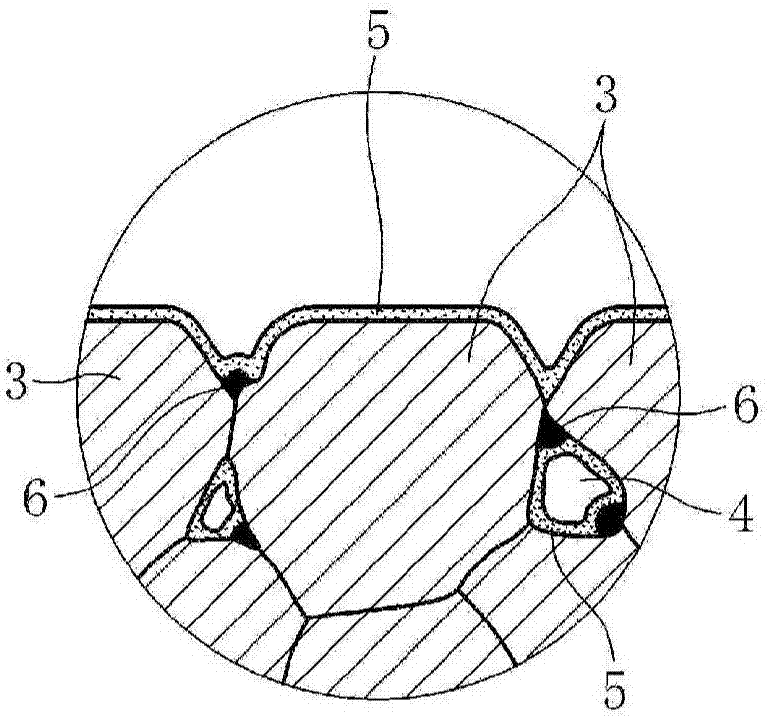
本發(fā)明涉及燒結(jié)軸承,特別是涉及al-cu合金(也被稱為鋁青銅)系燒結(jié)軸承。
背景技術(shù):
:作為發(fā)動(dòng)機(jī)的燃料使用的汽油、輕油等的品質(zhì)在世界各地有所不同,有的地區(qū)也使用粗劣的燃料(汽油、輕油等)、生物燃料等。對(duì)于設(shè)置在可能與這樣的燃料接觸的位置(例如電動(dòng)燃料泵、egr閥)的軸承來(lái)說(shuō),要求具有針對(duì)粗劣燃料、生物燃料中含有的硫化物、有機(jī)酸的耐腐蝕性。另一方面,隨著發(fā)動(dòng)機(jī)的小型化和輕量化,對(duì)于電動(dòng)燃料泵等要求小型化和輕量化,對(duì)于其中所安裝的軸承也要求小型化。例如在電動(dòng)燃料泵中,為了在確保噴出性能的同時(shí)達(dá)成小型化,需要提高轉(zhuǎn)速。對(duì)于支承這樣高速旋轉(zhuǎn)的軸的軸承來(lái)說(shuō),在要求小型化的同時(shí),還要求耐腐蝕性、耐磨耗性(低摩擦特性)。例如,作為耐磨耗性優(yōu)異的軸承,已知有銅系燒結(jié)軸承。但是,銅系燒結(jié)軸承與粗劣燃料、生物燃料中含有的硫化物、有機(jī)酸接觸時(shí),銅容易發(fā)生腐蝕。例如,在硫化物與銅系燒結(jié)軸承接觸時(shí),在表面(特別是軸承面)生成硫化銅,從而使軸承面與軸之間的間隙減少,可能招致旋轉(zhuǎn)扭矩的上升。另外,在有機(jī)酸與銅系燒結(jié)軸承接觸時(shí),銅會(huì)發(fā)生溶出,因而可能使耐磨耗性降低、制品壽命縮短。根據(jù)以上所述,銅系燒結(jié)軸承的耐磨耗性優(yōu)異,但耐腐蝕性差,因而不適于與粗劣燃料、生物燃料接觸的用途。例如在專利文獻(xiàn)1中示出了al-cu合金系燒結(jié)軸承。al-cu合金系燒結(jié)軸承的滑動(dòng)性優(yōu)異,同時(shí)由于在表面生成氧化鋁膜,因而耐腐蝕性也優(yōu)異?,F(xiàn)有技術(shù)文獻(xiàn)專利文獻(xiàn)專利文獻(xiàn)1:日本特開2009-7650號(hào)公報(bào)技術(shù)實(shí)現(xiàn)要素:發(fā)明所要解決的課題在上述專利文獻(xiàn)1中揭示了調(diào)整al-cu合金系燒結(jié)軸承中的各成分的混配比的技術(shù)。但是,即使應(yīng)用這樣的技術(shù),也不能說(shuō)耐腐蝕性得到了充分提高,要求進(jìn)行進(jìn)一步的研究。鑒于以上的情況,本發(fā)明的目的在于提高al-cu合金系燒結(jié)軸承的耐腐蝕性。用于解決課題的手段為了達(dá)成上述目的,本發(fā)明提供一種燒結(jié)軸承,該燒結(jié)軸承含有al、cu以及ni,并且al-cu-ni合金組織彼此被燒結(jié),上述al-cu-ni合金組織具有al-cu-ni母相和al-ni化合物相、不具有al-cu化合物相。如此,通過在al-cu合金系燒結(jié)軸承中混配ni并使al-cu-ni母相(固溶體合金相)在合金組織中析出,耐腐蝕性提高。此時(shí),在al-cu-ni合金組織中,通常不僅母相析出,而且耐腐蝕性低于母相的化合物相也析出。具體地說(shuō),al-cu化合物相的耐腐蝕性特別低,al-ni化合物相的耐腐蝕性高于al-cu化合物相。因此,在al-cu-ni合金組織中,若調(diào)整原料粉末的成分、混配比以使得耐腐蝕性特別差的al-cu化合物相不發(fā)生析出、耐腐蝕性比較優(yōu)異的al-ni化合物相析出,則能夠得到具有非常優(yōu)異的耐腐蝕性的燒結(jié)軸承。上述的燒結(jié)軸承的組成例如含有7質(zhì)量%~11質(zhì)量%的al、1質(zhì)量%~6質(zhì)量%的ni,余部的主成分為cu。另外,在上述的燒結(jié)軸承中,即使混配si來(lái)替代ni,也能夠得到與上述同樣的效果。即,上述目的可利用下述燒結(jié)軸承來(lái)達(dá)成:該燒結(jié)軸承含有al、cu以及si,并且al-cu-si合金組織彼此被燒結(jié),上述al-cu-si合金組織具有al-cu-si母相和al-si化合物相、不具有al-cu化合物相。該燒結(jié)軸承的組成例如含有7質(zhì)量%~11質(zhì)量%的al、1質(zhì)量%~6質(zhì)量%的si,余部的主成分為cu。此外,在上述的燒結(jié)軸承中,即使混配zn來(lái)替代ni,也能夠得到與上述同樣的效果。即,上述目的可利用下述燒結(jié)軸承來(lái)達(dá)成:該燒結(jié)軸承含有al、cu以及zn,并且al-cu-zn合金組織彼此被燒結(jié),上述al-cu-zn合金組織具有al-cu-zn母相和al-zn化合物相、不具有al-cu化合物相。該燒結(jié)軸承的組成例如含有7質(zhì)量%~11質(zhì)量%的al、1質(zhì)量%~5質(zhì)量%的zn,余部的主成分為cu。另外,由于純銅容易附著硫化物,因而在燒結(jié)軸承中若存在純銅組織(cu相),則由于硫化物附著至cu相而容易發(fā)生硫化腐蝕。因此,在燒結(jié)軸承的原料中含有純銅粉末的情況下,需要使al在cu相中擴(kuò)散而進(jìn)行合金化,燒結(jié)工序的成本增高。因此,上述燒結(jié)軸承的原料粉末優(yōu)選不含有純銅粉末。在使游離石墨在上述那樣的燒結(jié)軸承的軸承面露出時(shí),能夠通過游離石墨自身的潤(rùn)滑性而使?jié)櫥院湍湍ズ男蕴岣?。?duì)于設(shè)置在燃料泵的用于支承軸的旋轉(zhuǎn)的軸承、或者設(shè)置在egr閥的用于支承閥在軸向的往復(fù)移動(dòng)的軸承來(lái)說(shuō),它們與燃料等中含有的硫化物、有機(jī)酸接觸,要求優(yōu)異的耐腐蝕性。作為在這樣的用途中所使用的軸承,能夠適當(dāng)?shù)厥褂蒙鲜龅臒Y(jié)軸承。發(fā)明效果如上所述,根據(jù)本發(fā)明,能夠提高al-cu合金系燒結(jié)軸承的耐腐蝕性。附圖說(shuō)明圖1是本發(fā)明的實(shí)施方式的燒結(jié)軸承的截面圖。圖2是上述燒結(jié)軸承的放大截面圖。圖3是上述燒結(jié)軸承的al-cu-ni合金組織的放大圖。圖4是其他實(shí)施方式的燒結(jié)軸承的al-cu-si合金組織的放大圖。圖5是其他實(shí)施方式的燒結(jié)軸承的al-cu-zn合金組織的放大圖。圖6是燃料泵的截面圖。圖7是egr閥的截面圖。圖8是比較例的試驗(yàn)片的al-cu合金組織的放大圖。圖9是表示腐蝕試驗(yàn)的結(jié)果的曲線圖。具體實(shí)施方式如圖1所示,本發(fā)明的一個(gè)實(shí)施方式的燒結(jié)軸承1形成圓筒狀,在內(nèi)周插入軸2。燒結(jié)軸承1的內(nèi)周面1a為圓筒面,作為滑動(dòng)支承軸2的外周面的軸承面發(fā)揮功能。燒結(jié)軸承1的外周面1b為圓筒面,作為安裝于其他部件的安裝面發(fā)揮功能。燒結(jié)軸承1由燒結(jié)金屬、特別是al-cu合金系燒結(jié)金屬形成,在本實(shí)施方式中,由包含al、cu和ni的燒結(jié)金屬形成。具體地說(shuō),燒結(jié)軸承1例如含有7質(zhì)量%~11質(zhì)量%的al、1質(zhì)量%~6質(zhì)量%的ni,余部的主成分為cu。在本實(shí)施方式中,除了上述成分以外,相對(duì)于al、cu、ni的總量100質(zhì)量%,還含有3質(zhì)量%~6質(zhì)量%的石墨(游離石墨)、以及0.1質(zhì)量%~0.4質(zhì)量%的p。在本實(shí)施方式中,燒結(jié)軸承1含有8.5質(zhì)量%的al、5質(zhì)量%的ni,余部的主成分為cu。如圖2中放大所示,燒結(jié)軸承1具有al-cu-ni合金組織3,相鄰的al-cu-ni合金組織3彼此燒結(jié)結(jié)合。在al-cu-ni合金組織3之間設(shè)有無(wú)數(shù)個(gè)內(nèi)部空孔4。內(nèi)部空孔4與燒結(jié)軸承1的表面連通。在al-cu-ni合金組織3的表面也即包含內(nèi)周面1a(軸承面)的燒結(jié)軸承1的表面和燒結(jié)軸承1的內(nèi)部空孔4的周圍形成有氧化鋁覆膜5。利用該氧化鋁覆膜5保護(hù)al-cu-ni合金組織3,因而耐腐蝕性和耐磨耗性提高。游離石墨6分布在燒結(jié)軸承1的表面和內(nèi)部。該游離石墨6的一部分在燒結(jié)軸承1的軸承面(內(nèi)周面1a)露出。在al-cu-ni合金組織3的晶界部存在p(磷)(省略圖示)。圖3中進(jìn)一步放大示出al-cu-ni合金組織3。如該圖所示,al-cu-ni合金組織3具有al-cu-ni母相(α相)、以及al-ni化合物相(κ相),另一方面,其不具有al-cu化合物相(γ相)。換言之,以下述范圍來(lái)設(shè)定al-cu-ni合金組織3的組成(al、cu、ni的混配比),該范圍為在al-cu-ni三元相圖中α相和κ相析出、且γ相不析出的范圍。如此,通過使耐腐蝕性非常高的al-cu-ni母相析出,能夠賦予燒結(jié)軸承1優(yōu)異的耐腐蝕性。另外,在燒結(jié)軸承1中生成al-cu-ni合金組織3時(shí),實(shí)際上無(wú)法避免耐腐蝕性差的化合物相的析出,但如上所述通過使耐腐蝕性比較高的al-ni化合物相析出、不使耐腐蝕性特別低的al-cu化合物相析出,燒結(jié)軸承1的耐腐蝕性進(jìn)一步提高。此時(shí),優(yōu)選al-cu-ni合金組織3中的al-cu-ni母相的比例高,例如以面積比計(jì)為50%以上、優(yōu)選為70%以上,在圖示例中大約為85%左右。燒結(jié)軸承1的密度比為80%~95%的范圍。燒結(jié)軸承1的密度比小于80%時(shí)強(qiáng)度不充分,密度比大于95%時(shí)含油量不足,因而不優(yōu)選。燒結(jié)軸承1的表層的密度比高于內(nèi)部的密度比。即,燒結(jié)軸承1的表面的空孔率(表面開孔率)小于燒結(jié)軸承1的內(nèi)部的空孔率。另外,燒結(jié)軸承1的外周面1b側(cè)的表層的密度比高于內(nèi)周面1a側(cè)的表層的密度比。即,燒結(jié)軸承1的外周面1b的表面開孔率小于燒結(jié)軸承1的內(nèi)周面1a的表面開孔率。需要說(shuō)明的是,密度比α由下式來(lái)表示。α(%)=(ρ1/ρ0)×100其中,ρ1:多孔質(zhì)體的密度、ρ0:假定該多孔質(zhì)體中不存在空孔時(shí)的密度另外,燒結(jié)軸承1的表層是指從燒結(jié)軸承1的表面到規(guī)定深度(例如,燒結(jié)軸承1的內(nèi)徑的1/100~1/15左右的深度)的區(qū)域。在燒結(jié)軸承1的內(nèi)部空孔浸滲有潤(rùn)滑油。作為潤(rùn)滑油,可以使用礦物油、聚α烯烴(pao)、酯、液態(tài)油脂等。其中,對(duì)于軸承的用途來(lái)說(shuō),不一定必須要浸滲潤(rùn)滑油,也可以在干燥狀態(tài)下使用。在插入到燒結(jié)軸承1的內(nèi)周的軸2進(jìn)行旋轉(zhuǎn)或軸向移動(dòng)或者進(jìn)行這兩種運(yùn)動(dòng)而使燒結(jié)軸承1的內(nèi)周面1a與軸2的外周面發(fā)生滑動(dòng)時(shí),保持在燒結(jié)軸承1的內(nèi)部空孔中的潤(rùn)滑油隨著溫度上升滲出到內(nèi)周面1a。利用該滲出到內(nèi)周面1a的潤(rùn)滑油,在燒結(jié)軸承1的內(nèi)周面1a與軸2的外周面之間的軸承間隙內(nèi)形成油膜,軸2被燒結(jié)軸承1支承。接下來(lái),對(duì)上述燒結(jié)軸承1的制造方法進(jìn)行說(shuō)明。燒結(jié)軸承1經(jīng)下述工序形成:混合工序,將各種粉末混合得到原料粉末;壓粉工序,將原料粉末利用模具壓縮得到粉體壓坯(壓粉體);燒結(jié)工序,將粉體壓坯燒結(jié)得到燒結(jié)體;以及精整工序,將燒結(jié)體利用模具壓縮進(jìn)行成型修整。下面對(duì)各工序進(jìn)行詳細(xì)說(shuō)明。[混合工序]在混合工序中,通過利用混合機(jī)將各種粉末混合,生成原料粉末。原料粉末包含作為al源、cu源、ni源、p源以及固體潤(rùn)滑劑的粉末。在原料粉末中不包含純cu粉末和純al粉末。在原料粉末中根據(jù)需要進(jìn)一步混合燒結(jié)助劑(例如氟化鋁粉末或氟化鈣粉末)、脫模用潤(rùn)滑劑(例如硬脂酸鋅粉末或硬脂酸鈣粉末)。下面對(duì)各粉末進(jìn)行詳細(xì)說(shuō)明。作為al和cu源,可以使用例如al-cu-ni合金粉末、al-cu合金粉末。作為ni源,可以使用例如al-cu-ni合金粉末、cu-ni合金粉末。在本實(shí)施方式中,使用al-cu-ni合金粉末(預(yù)合金粉末)作為al、cu、ni源。al-cu-ni合金粉末包含7質(zhì)量%~11質(zhì)量%的al。al-cu-ni合金粉末可以使用例如通過霧化法制造的粉末。al-cu-ni合金粉末的粒徑為106μm以下、平均粒徑為20μm~50μm。需要說(shuō)明的是,平均粒徑是指通過激光衍射測(cè)定的粒徑的平均值。具體地說(shuō),是利用(株)島津制作所制造的sald-3100通過激光衍射對(duì)5000個(gè)粉末進(jìn)行測(cè)定時(shí)的粒徑的平均值(以下相同)。作為p源,可以使用p合金粉末。p合金粉末可以使用例如p-cu合金粉末,在本實(shí)施方式中使用7質(zhì)量%~10質(zhì)量%p-cu合金粉末。p具有提高燒結(jié)時(shí)的固液相間的潤(rùn)濕性的效果。p成分過少時(shí),固液相間的燒結(jié)促進(jìn)效果較差。另一方面,p成分過多時(shí),燒結(jié)過度進(jìn)行,al容易偏析。因此,p合金粉末的混合量例如如下進(jìn)行設(shè)定:相對(duì)于al、cu以及ni的總量100質(zhì)量%,使原料粉末中的p成分為0.1質(zhì)量%~0.6質(zhì)量%、優(yōu)選為0.1質(zhì)量%~0.4質(zhì)量%。作為固體潤(rùn)滑劑,可以使用例如石墨粉末。石墨粉末主要以游離石墨的形式存在于燒結(jié)軸承1的空孔內(nèi)和表面。特別是在軸承面(內(nèi)周面1a)露出的石墨粉末賦予燒結(jié)軸承1優(yōu)異的潤(rùn)滑性,有助于耐磨耗性的提高。相對(duì)于原料粉末中的al、cu、ni的總量100質(zhì)量%,石墨粉末的混合量例如為3質(zhì)量%~6質(zhì)量%。石墨的混合量小于3質(zhì)量%時(shí),得不到添加石墨所帶來(lái)的潤(rùn)滑性、耐磨耗性的提高效果。另一方面,石墨的混合量大于6質(zhì)量%時(shí),擔(dān)心會(huì)開始阻礙例如al向cu中的擴(kuò)散。石墨的混合量大于10質(zhì)量%時(shí),材料強(qiáng)度降低,會(huì)阻礙al向cu中的擴(kuò)散,因而不優(yōu)選。需要說(shuō)明的是,通常若相對(duì)于原料粉末的主成分添加4質(zhì)量%以上的石墨,則成型變得困難,但通過使用造粒石墨作為石墨粉末則能夠進(jìn)行成型。在本實(shí)施方式中,石墨粉末使用將天然石墨或人造石墨的微粉利用樹脂粘結(jié)劑造粒后進(jìn)行粉碎得到的粒徑為145目以下的石墨粉末。氟化鋁和氟化鈣作為燒結(jié)助劑發(fā)揮功能。具體地說(shuō),氟化鋁和氟化鈣在850℃~900℃(該溫度為al-cu-ni合金粉末的燒結(jié)溫度)發(fā)生熔融同時(shí)緩慢地蒸發(fā),保護(hù)al-cu-ni合金粉末的表面,抑制氧化鋁的生成,從而促進(jìn)燒結(jié)、增進(jìn)鋁的擴(kuò)散。氟化鋁和氟化鈣在燒結(jié)時(shí)發(fā)生蒸發(fā)、揮散,因而在燒結(jié)軸承1的完成品中幾乎無(wú)殘留。相對(duì)于原料粉末中的al、cu、ni的總量100質(zhì)量%,氟化鋁和氟化鈣優(yōu)選共添加0.05質(zhì)量%~0.2質(zhì)量%的程度。氟化鋁和氟化鈣小于0.05質(zhì)量%時(shí),作為燒結(jié)助劑的效果不充分,得不到致密且具有高強(qiáng)度的燒結(jié)體。另一方面,氟化鋁和氟化鈣大于0.2質(zhì)量%時(shí),即使添加更多量,作為燒結(jié)助劑的效果也達(dá)到極限,因此從成本的方面考慮,優(yōu)選限制在0.2質(zhì)量%以下。需要說(shuō)明的是,若無(wú)特別需要,則也可以不在原料粉末中混配p合金粉末、氟化鋁和氟化鈣等燒結(jié)助劑、石墨粉末等固體潤(rùn)滑劑以及硬脂酸鋅等脫模用潤(rùn)滑劑中的一種或兩種以上。[壓粉工序]在壓粉工序中,將上述的原料粉末填充到壓粉模具中進(jìn)行壓縮,從而形成與燒結(jié)軸承1大致相同形狀的粉體壓坯。在本實(shí)施方式中,通過在200mpa~700mpa的壓力下對(duì)填充在壓粉模具中的原料粉末進(jìn)行壓縮來(lái)進(jìn)行粉體壓坯的成型。需要說(shuō)明的是,也可以在將壓粉模具加熱到70℃以上的狀態(tài)下進(jìn)行粉體壓坯的成型。在本實(shí)施方式的燒結(jié)軸承1中,al源僅由al-cu-ni合金粉末構(gòu)成,原料粉末中不包含純al粉末。由此可解決由于相對(duì)密度小的純al粉末所引起的原料粉末流動(dòng)性的劣化以及與純al顆粒的飛散相伴的處理上的問題。據(jù)此,原料粉末在壓粉模具中的填充性增高,因而能夠避免成型性的降低或粉體壓坯的強(qiáng)度不足。[燒結(jié)工序]在燒結(jié)工序中,在規(guī)定的燒結(jié)溫度下對(duì)粉體壓坯進(jìn)行加熱,使相鄰的原料粉末彼此燒結(jié)結(jié)合,從而形成燒結(jié)體。燒結(jié)工序例如使用網(wǎng)帶式連續(xù)爐來(lái)進(jìn)行。通過對(duì)粉體壓坯進(jìn)行加熱,相鄰的al-ni-cu合金粉末(al-cu-ni合金組織)彼此燒結(jié)結(jié)合(擴(kuò)散接合),形成燒結(jié)體。此時(shí),利用原料粉末中含有的p成分促進(jìn)al-cu-ni合金組織彼此的燒結(jié)、提高燒結(jié)體的強(qiáng)度。另外,原料粉末中的石墨粉末以游離石墨的形式殘留在燒結(jié)體的內(nèi)部和表面。在像這樣得到的燒結(jié)體的al-cu-ni合金組織中,析出有al-cu-ni母相(α相)與al-ni化合粒相(κ相)析出,另一方面,未析出al-cu化合物相(γ相)(參照?qǐng)D2)。通過以得到這樣的合金組織的方式來(lái)設(shè)定原料粉末的成分、混配比,可得到非常優(yōu)異的耐腐蝕性。具體地說(shuō),例如,預(yù)先獲取該燒結(jié)溫度下的al-cu-ni的三元相圖,根據(jù)該三元相圖設(shè)定得到上述那樣的組織的成分及其混配比,從而能夠得到上述那樣的燒結(jié)體。燒結(jié)溫度優(yōu)選為900℃~950℃、更優(yōu)選為900℃~920℃。另外,氣氛氣體可以使用氫氣、氮?dú)饣蛘咚鼈兊幕旌蠚怏w。燒結(jié)時(shí)間增長(zhǎng)則耐腐蝕性提高,例如對(duì)于燃料泵中使用的燒結(jié)軸承1來(lái)說(shuō),燒結(jié)時(shí)間優(yōu)選為20分鐘~60分鐘(例如30分鐘)。若al-cu-ni合金粉末的共晶溫度達(dá)到548℃以上,則產(chǎn)生各種液相。在產(chǎn)生液相時(shí),粉體壓坯發(fā)生膨脹,利用所產(chǎn)生的液相形成燒結(jié)頸后,收縮達(dá)到致密化,從而得到燒結(jié)體。此時(shí),在燒結(jié)體的表層,al-cu-ni合金組織被氧化而阻礙燒結(jié),達(dá)不到致密化,尺寸處于膨脹狀態(tài),因而擔(dān)心燒結(jié)體的強(qiáng)度不足。但是,在燒結(jié)體的內(nèi)部,al-cu-ni合金組織不容易被氧化,可充分進(jìn)行燒結(jié),因而能夠充分確保燒結(jié)體的強(qiáng)度。[精整工序]在精整工序中,對(duì)于通過燒結(jié)而發(fā)生了膨脹的燒結(jié)體進(jìn)行壓縮來(lái)進(jìn)行尺寸成型修整。具體地說(shuō),將芯棒插入到燒結(jié)體的內(nèi)周,同時(shí)利用上下沖頭將燒結(jié)體的軸向?qū)挾认薅ㄔ谝?guī)定尺寸,在該狀態(tài)下將它們一體地壓入到模頭的內(nèi)周。由此,燒結(jié)體的外周面被模頭壓迫而進(jìn)行成型,同時(shí)燒結(jié)體的內(nèi)周面被芯棒的外周面擠壓而進(jìn)行成型。利用該精整工序,發(fā)生了膨脹的燒結(jié)體的表層被壓縮,表層的密度大于內(nèi)部的密度。另外,燒結(jié)體的外周面?zhèn)鹊谋韺拥膲嚎s量大于內(nèi)周面?zhèn)鹊谋韺拥膲嚎s量,因而外周面?zhèn)鹊谋韺拥拿芏却笥趦?nèi)周面?zhèn)鹊拿芏取P枰f(shuō)明的是,在精整工序后,通過進(jìn)一步對(duì)燒結(jié)體的內(nèi)周面1a旋轉(zhuǎn)精整,可以使在內(nèi)周面1a(軸承面)開孔的空孔進(jìn)一步減小。[含油工序]在含油工序中,潤(rùn)滑油浸滲到上述燒結(jié)體的內(nèi)部空孔中。具體地說(shuō),在減壓環(huán)境下將燒結(jié)體浸漬在潤(rùn)滑油中后,恢復(fù)常壓,從而使?jié)櫥徒B到燒結(jié)體的內(nèi)部空孔中。通過以上操作完成燒結(jié)軸承1。本發(fā)明并不限于上述的實(shí)施方式。例如,燒結(jié)軸承1的組成并不限于上述組成,也可以混配si來(lái)替代上述實(shí)施方式中的ni。具體地說(shuō),例如燒結(jié)軸承的組成可以為含有7質(zhì)量%~11質(zhì)量%的al、1質(zhì)量%~6質(zhì)量%的si,余部的主成分為cu。圖4中示出了含有8.5質(zhì)量%的al、2質(zhì)量%的si、余部的主成分為cu的燒結(jié)軸承的al-cu-si合金組織。在該al-cu-si合金組織中,析出有al-cu-si母相(α相)和al-si化合物相(κ相),未析出al-cu化合物相(γ相)。al-cu-si合金組織中的al-cu-si母相的比例例如以面積比計(jì)為50%以上、優(yōu)選為70%以上,在圖示例中大約為75%左右。其他成分、制法等與上述的實(shí)施方式相同,因而省略說(shuō)明。另外,也可以混配zn來(lái)替代上述實(shí)施方式中的ni。具體地說(shuō),例如燒結(jié)軸承1的組成可以為含有7質(zhì)量%~11質(zhì)量%的al、1質(zhì)量%~5質(zhì)量%(優(yōu)選為1質(zhì)量%~4質(zhì)量%)的zn,余部的主成分為cu。圖5中示出了含有8.5質(zhì)量%的al、3質(zhì)量%的zn,余部的主成分為cu的燒結(jié)軸承的al-cu-zn合金組織。在該al-cu-zn合金組織中,析出有al-cu-zn母相(α相)和al-zn化合物相(δ相),未析出al-cu化合物相(γ相)。al-cu-zn合金組織中的al-cu-zn母相的比例例如以面積比計(jì)為50%以上、優(yōu)選為70%以上,在圖示例中大約為80%左右。其他成分、制法等與上述的實(shí)施方式相同,因而省略說(shuō)明。另外,除了上述實(shí)施方式的ni以外,還可以混配si或zn、或者這兩者。另外,也可以混配si和zn來(lái)代替上述實(shí)施方式中的ni。上述的燒結(jié)軸承1例如被組裝到圖6所示的燃料泵(電動(dòng)燃料泵10)中。電動(dòng)燃料泵10具有大致圓筒狀的金屬制外殼11、固定在外殼11的上端部的合成樹脂制馬達(dá)罩12、固定在外殼11的下端部的金屬制泵罩13和泵主體14。在外殼11的內(nèi)部配置有馬達(dá)的電樞15。設(shè)置于電樞15的軸2的軸向兩端部被安裝于馬達(dá)罩12和泵罩13的燒結(jié)軸承1旋轉(zhuǎn)自由地支承。在燒結(jié)軸承1的內(nèi)部空孔中預(yù)先浸滲有潤(rùn)滑油。磁體16被固定在外殼11的內(nèi)周面,該磁體16和電樞15以規(guī)定間隔在半徑方向?qū)χ?。在馬達(dá)罩12設(shè)置有與通到燃料噴射閥的燃料供給管(省略圖示)連接的噴出口17。在該噴出口17設(shè)置阻止燃料倒流的止回閥18。止回閥18利用彈簧19向關(guān)閉方向施力。在軸2的端部(圖中下端)固定泵輪20。在圖示例中,2個(gè)泵輪20設(shè)置在在軸向隔離開的2個(gè)位置。在泵主體14設(shè)置有吸入口21。在使電樞15和泵輪20一體旋轉(zhuǎn)時(shí),燃料箱內(nèi)的燃料由吸入口21汲上來(lái),通過外殼11的內(nèi)部,由噴出口17噴出。旋轉(zhuǎn)自由地支承電樞15的軸2的燒結(jié)軸承1處于經(jīng)常與燃料(例如汽油)接觸的環(huán)境下。另外,上述的燒結(jié)軸承1也可以安裝在圖7所示的egr閥30中。egr閥30具備:外殼31、配置在外殼31的內(nèi)部的閥32、向關(guān)閉閥32的方向施力的彈簧33、以及向?qū)㈤y32打開的方向進(jìn)行驅(qū)動(dòng)的驅(qū)動(dòng)部34(例如步進(jìn)馬達(dá))。在外殼31的內(nèi)部形成氣體流路35,在氣體流路35的中途設(shè)置閥座36。閥32的軸32a在軸向滑動(dòng)自由地被固定于外殼31的燒結(jié)軸承1支承。對(duì)于該燒結(jié)軸承1,在內(nèi)部空孔中未浸滲潤(rùn)滑油,以干燥狀態(tài)進(jìn)行使用。在驅(qū)動(dòng)部34停止的狀態(tài)下,閥32通過彈簧33的施加力而被擠壓到閥座36,由此構(gòu)成氣體流路35關(guān)閉的狀態(tài)。另一方面,在對(duì)驅(qū)動(dòng)部34進(jìn)行驅(qū)動(dòng)而使閥32向下方移動(dòng)時(shí),閥32從閥座36脫離,構(gòu)成氣體流路35打開的狀態(tài),由發(fā)動(dòng)機(jī)噴出的尾氣返回到發(fā)動(dòng)機(jī)的吸氣側(cè)。接下來(lái)制作由組成不同的燒結(jié)金屬構(gòu)成的多個(gè)試驗(yàn)片(實(shí)施例1~4、比較例1~4),對(duì)它們實(shí)施腐蝕試驗(yàn)。各試驗(yàn)片具有下述表1所示的組成,利用上述所示的制法進(jìn)行制作。下面對(duì)各試驗(yàn)片進(jìn)行詳細(xì)說(shuō)明?!颈?】alnisiznsncu實(shí)施例18.53.0---bal.實(shí)施例28.55.0---bal.實(shí)施例38.5-2.0--bal.實(shí)施例48.5--3.0-bal.比較例18.5--5.0-bal.比較例2-30~35---bal.比較例38.5----bal.比較例48.5---3.0bal.al-cu-ni系燒結(jié)體(實(shí)施例1、實(shí)施例2)其由使用含有al-cu-ni合金粉(其含有7質(zhì)量%~11質(zhì)量%al)的原料粉末制作的燒結(jié)體構(gòu)成,含有8.5質(zhì)量%的al、3.0質(zhì)量%(實(shí)施例1)或者5.0質(zhì)量%(實(shí)施例2)的ni,余部的主成分為cu。在該燒結(jié)體中生成的al-cu-ni合金組織中,確認(rèn)到了al-cu-ni母相(α相)和al-ni化合物相(κ相)的析出(參照?qǐng)D3)。另外,未確認(rèn)到al-cu化合物相(γ相)的析出。al-cu-si系燒結(jié)體(實(shí)施例3)其由使用含有al-cu-si合金粉(其含有7質(zhì)量%~11質(zhì)量%al)的原料粉末制作的燒結(jié)體構(gòu)成,含有8.5質(zhì)量%的al、2.0質(zhì)量%的si,余部的主成分為cu。在該燒結(jié)體中生成的al-cu-si合金組織中,確認(rèn)到了al-cu-si母相(α相)和al-si化合物相(δ相、κ相)的析出(參照?qǐng)D4)。另外,未確認(rèn)到al-cu化合物相(γ相)的析出。al-cu-zn系燒結(jié)體(實(shí)施例4、比較例1)其由使用含有al-cu-zn合金粉(其含有7質(zhì)量%~11質(zhì)量%al)的原料粉末制作的燒結(jié)體構(gòu)成,含有8.5質(zhì)量%的al、3.0質(zhì)量%(實(shí)施例4)或者5.0質(zhì)量%(比較例1)的zn,余部的主成分為cu。在該燒結(jié)體中生成的al-cu-ni合金組織中,確認(rèn)到了al-cu-zn母相(α相)和al-zn化合物相(δ相)的析出(參照?qǐng)D5)。另外,未確認(rèn)到al-cu化合物相(γ相)的析出。銅鎳合金系燒結(jié)體(比較例2)其由使用主要含有cu粉末和ni粉末的原料粉末制作的燒結(jié)體構(gòu)成,含有30質(zhì)量%~35質(zhì)量%的ni。al-cu系燒結(jié)體(比較例3)其由使用含有al-cu合金粉(其含有7質(zhì)量%~11質(zhì)量%al)的原料粉末制作的燒結(jié)體構(gòu)成,含有8.5質(zhì)量%的al、余部的主成分為cu。在該燒結(jié)體中生成的al-cu合金組織中,確認(rèn)到了al-cu母相(α相)和al-cu化合物相(γ相)的析出(參照?qǐng)D8)。al-cu-sn系燒結(jié)體(比較例4)其由使用含有al-cu合金粉(其含有7質(zhì)量%~11質(zhì)量%al)和sn粉末的原料粉末制作的燒結(jié)體構(gòu)成,含有8.5質(zhì)量%的al、3.0質(zhì)量%的sn,余部的主成分為cu。在該燒結(jié)體中生成的al-cu-sn合金組織中,確認(rèn)到了al-cu-zn母相(α相)和al-cu化合物相(γ相)的析出。將上述各試驗(yàn)片在含有硫化物和有機(jī)酸的溶液中浸漬規(guī)定時(shí)間,測(cè)定浸漬前后的重量變化率。其結(jié)果,如圖9所示,實(shí)施例1~4在浸漬前后的重量幾乎沒有變化,與之相對(duì),比較例1~4在浸漬前后的重量變化很大。具體地說(shuō),在比較例1、2、4中,通過上述浸漬處理,重量大幅減少(比較例1:-45.13%、比較例2:-8.25%、比較例4:-28.49%)。據(jù)認(rèn)為,這是因?yàn)槿芤褐械挠袡C(jī)酸使得燒結(jié)體中的al成分發(fā)生溶出。另外,在比較例3中,通過上述浸漬處理,重量大幅增加(+10.21%)。據(jù)認(rèn)為,這是因?yàn)樵跓Y(jié)體上附著了硫化物。與之相對(duì),在實(shí)施例1~4中,由于上述浸漬處理所致的重量變化率均被抑制得極小(大約小于0.5%)。由這些結(jié)果確認(rèn)到,在實(shí)施例1~4中,在cu-al系燒結(jié)體中添加了適量的ni、si、zn中的任一種,該實(shí)施例1~4具有優(yōu)異的耐腐蝕性,特別是具有al-cu-ni合金組織的實(shí)施例1和2具有非常優(yōu)異的耐腐蝕性。符號(hào)說(shuō)明1燒結(jié)軸承2軸3al-cu-ni合金組織4內(nèi)部空孔5氧化鋁覆膜6游離石墨10電動(dòng)燃料泵30egr閥當(dāng)前第1頁(yè)12