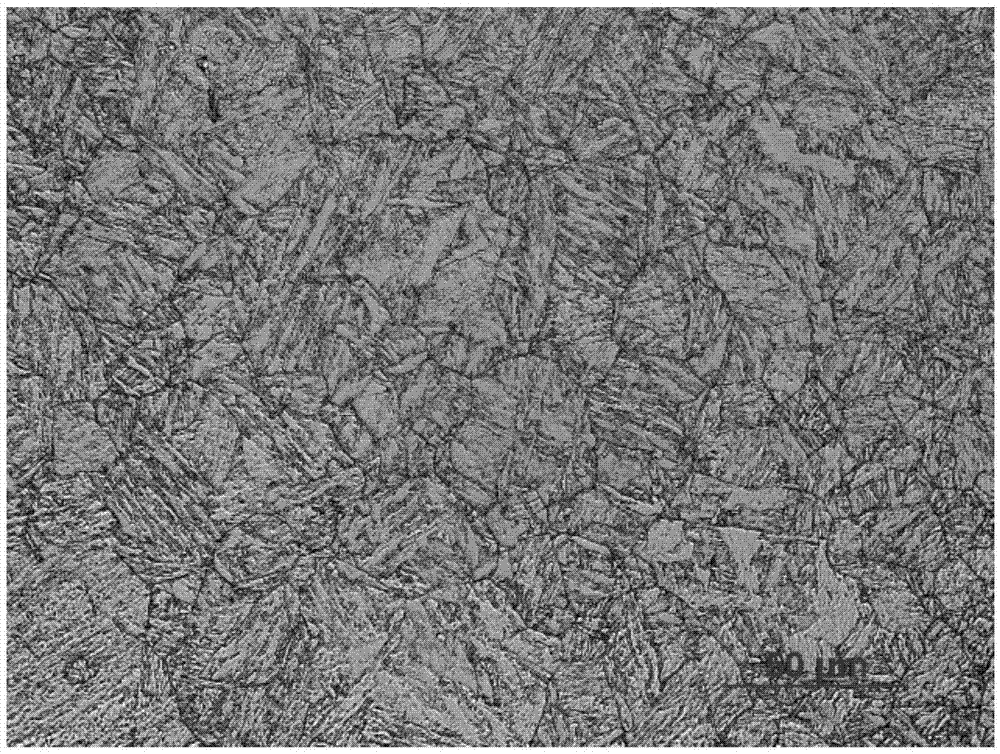
本發(fā)明涉及冶金行業(yè)結(jié)構(gòu)鋼的成分設計及其制造方法,尤其是指一種抗氯離子腐蝕抽油桿鋼材的成分設計及其棒線材的制造技術(shù),屬黑色金屬材料制造加工
技術(shù)領(lǐng)域:
。
背景技術(shù):
:機械采油是油田開發(fā)的主要手段,有桿抽油系統(tǒng)在機械采油中占有舉足輕重的地位。抽油桿是有桿抽油設備的重要零件,其功能是將抽油機的動力傳遞給井下抽油泵,通過油井管采出石油。抽油桿在抽油過程中將承受各種交變載荷、振動載荷和沖擊載荷及與油管相對運動所產(chǎn)生的摩擦作用。同時抽油桿還直接與油井中的鹽離子、氯離子、co2、h2s等多種腐蝕性介質(zhì)及砂粒相接觸而受到強烈的腐蝕和磨損作用。所以,抽油桿不僅需要良好的強韌性,還要求具有優(yōu)良的耐腐蝕性能。抽油桿一般采用鋼質(zhì)線材制造,其按強度級別可分為d級桿、h級桿兩種,其中,后者強度較高。制造d級桿采用的鋼種有35mn2、35crmo、42crmo鋼等,美國石油協(xié)會推薦的d級抽油桿有:1536和4142(分別相當于35mn2和42crmo鋼)。制造h級桿主要采用12mn2sicr、16mn2sicr、20cr2moni鋼等。大量實際應用表明,盡管h級抽油桿強度較高,但其使用壽命并不一定高于d級桿。原因在于,盡管隨著鋼的強度提高,抽油桿的疲勞強度、耐磨損性能提高,但在co2、h2s、cl-等油井腐蝕性介質(zhì)條件下,抽油桿的耐侵蝕、耐腐蝕疲勞性能并沒有得到改善。而且,單純提高抽油桿強度時,往往伴隨著韌性的降低,抽油桿早期突然斷裂的概率上升。隨著采油工業(yè)的迅速發(fā)展,各種高腐蝕油井的開發(fā)要求有新的解決方案,以降低腐蝕速率、裂紋擴展速率,降低早期斷桿概率,提高抽油桿的使用壽命和可靠性。近年來,解決腐蝕問題的主要方案有(1)對抽油桿桿體或接箍的表面進行熱噴涂,如申請?zhí)朿n200510083018.3:對抽油桿桿體或接箍的表面噴涂成份為碳0.3~0.6%,硅3.5~4%,硼3.5~4%,鉻15~16%,銅3~3.5%,鉬3~3.5%,鐵3~5%,鎳63.9~68.7%,厚度為0.26~0.6mm的涂層。申請?zhí)朿n200710118049.7噴涂一種鎳基合,申請?zhí)朿n200710188006.6噴涂一種耐腐蝕合金涂層。(2)采用碳纖維新型材料(3)開發(fā)新型抗腐蝕鋼材,表1中對檢索到的相關(guān)新型抽油桿鋼方面的專利進行比較。表1近年來發(fā)明專利檢索結(jié)果現(xiàn)有解決抽油桿腐蝕問題的不足:(1)表面噴涂防腐介質(zhì)這一方法能阻止鋼質(zhì)抽油桿進一步腐蝕,但是由于抽油桿在工作時不可避免地與油井管等進行接觸摩擦,表面的涂層容易磨掉。局部裸露的鋼質(zhì)抽油桿由于電極電位差的原因更容易成為腐蝕點,從而引起抽油桿的斷裂。(2)碳纖維材料韌性和抗腐蝕性能優(yōu)良,在部分油田得到了試用,但實際效果并不理想。由于碳纖維材質(zhì)較輕,碳纖維抽油桿下端必須加裝鋼質(zhì)加重抽油桿,鋼種加重抽油桿的腐蝕問題仍然沒有解決。碳纖維抽油桿使用中容易縱向劈裂,一旦發(fā)生更難于打撈。因此,新型的碳纖維抽油桿的應用一直難以得到推廣。(3)鋼質(zhì)抽油桿的抗腐蝕問題,近年來出現(xiàn)一批新的研究動向。比如:cn200710170721.7設計了一種微合金化的抽油桿鋼,通過成本較低的合金成分設計和控制軋制和冷卻工藝而獲得先共析鐵素體、貝氏體的組織,對于在含h2s、co2等油井氣的腐蝕井得到良好的應用,但對于含cl-的腐蝕井卻難以發(fā)揮抗腐蝕的相應作用。cn201210259053.6、cn200710099352.7、cn200710170721.7等專利,無不是采用nb、v、ti、b、re等細化晶粒元素獲得相應的組織,對解決油井氣腐蝕能起到相應的作用,但不能解決氯離子腐蝕。cn201010214315.8專利采用添加cu(0.20~0.30%)和ni(0.20~0.25%)的設計,不能解決氯離子的腐蝕問題,采用低碳的設計(0.06~0.10%)可能會造成強度不足。cn201110075772.8添加了(0.60~1.00%)的ni,對于改善鋼材的韌性起到良好的作用,由于ni合金價格較為昂貴不能解決氯離子的腐蝕問題。cn200410079237.x設計上采用碳含量為0.40-0.45%,ni含量為0.015-0.045%,碳當量偏高不利于連續(xù)抽油桿的焊接和改善韌性。綜上所述,目前耐腐蝕抽油桿用鋼尚存在以下不足之處:(1)現(xiàn)有的耐腐蝕抽油鋼成分設計上多采用微合金化+控制軋制和冷卻工藝獲得理想的顯微組織,一般可以解決油井氣腐蝕(包括co2、h2s等腐蝕介質(zhì)),對于氯離子腐蝕基本沒有效果。然而,從采油現(xiàn)場的水質(zhì)分析上看,許多 腐蝕井的腐蝕介質(zhì)多為氯離子腐蝕。以勝利油田某井的水樣分析報告為例,氯離子濃度為73647mg/l,總礦化度137739.4mg/l。(2)現(xiàn)有耐腐蝕抽油桿碳含量偏高,不能滿足連續(xù)抽油桿的焊接性能,強韌性匹配不良。技術(shù)實現(xiàn)要素:本發(fā)明的目的是:針對含cl-腐蝕環(huán)境,同時兼顧h2s、co2等復合腐蝕環(huán)境開發(fā)的一種成本較低的微合金化耐腐蝕抽油桿鋼。采用發(fā)明鋼制成的抽油桿具有抗cl-、h2s、co2等復合腐蝕環(huán)境能力,強韌性匹配良好、焊接性能優(yōu)良,從而提高抽油桿使用壽命和可靠性,提高抽油設備的整體穩(wěn)定性,進一步滿足石油工業(yè)的發(fā)展。重點解決現(xiàn)有抽油桿不耐cl-、h2s、co2等復合腐蝕環(huán)境、強塑性匹配不良,易發(fā)生疲勞斷裂的問題。為了實現(xiàn)上述目的,本發(fā)明的技術(shù)方案如下:一種抗氯離子腐蝕抽油桿鋼,其包括按重量百分數(shù)計的如下元素:碳:0.12~0.25%,硅:0.17~0.37%,錳:0.40~0.70%,鉬:0.15~0.25%,鎳:≤0.01%,鉻:4.50~6.10%,al:0.010~0.050%,鈮:0.02~0.06%,硫≤0.015%,磷≤0.020%,余為fe和不可避免的雜質(zhì)元素。本發(fā)明中各成分的設計理由或原理:碳:是提高鋼強度的主要元素,保證一定的強度必須一定的碳含量,但是碳元素對塑性不利,同時大于0.30%的碳含量不利焊接性能??刂?.15~0.25%的c含量可以保證獲得足夠的強度,同時使鋼具有良好的韌性和焊接性。錳:作為固溶強化元素,同時還可降低奧氏體-鐵素體相變溫度,有效提高鋼淬透性。但是錳在鋼中有促進奧氏體化晶粒長大缺點,錳的含量控制在0.40~0.70%能在本發(fā)明鋼中發(fā)揮良好的作用。硅:能顯著提高鐵素體的強度,能改變回火過程中碳化物的析出的形態(tài)、數(shù)量和尺寸,提高鋼的回火穩(wěn)定性,間接促進沉淀強化。硅在一定程度上對鋼的塑性和韌性有不良影響,但硅能促進相變過程中碳元素的再分配,提高殘余奧氏體的穩(wěn)定性,從而改善韌性??刂?.17~0.37%的硅含量,可以起到固溶強化的同時提高韌性。鉬:可以強烈推遲鐵素體轉(zhuǎn)變,顯著提高鋼的淬性??山档弯摰幕鼗鸫嘈?,改善熱處理工藝性能,提高鋼材的疲勞性能。鉬能降低鋼中氫的活度,大大降低鋼的吸氫傾向??梢詮娏业刈璧K碳化物的形核和長大,減少鋼中的儲氫陷阱。本發(fā)明鋼加入0.15~0.25%的鉬是最經(jīng)濟有效的含量。鉻:核心的合金元素。一般認為≥12%的cr能使鋼具有良好的抗氧化和腐蝕性能,可以提高鋼的熱強性,是不銹鋼和耐熱鋼的主要合金元素。同時,cr元素能提高耐磨性和硬度,但是對塑性和焊接性不利。針對油田的腐蝕介質(zhì)情況(cl-、na++k+、hco3-、mg2+、so42-、mg2+、ca2+),cr元素能改善抗腐蝕能力,但是考慮到焊接性能和強韌性的匹配以及成本的因素。經(jīng)過多輪次的50kg感應爐冶煉-鍛造-試驗優(yōu)選成分控制鉻為4.50~6.10%,同時與0.40~0.70%的mn共同使用效果良好。鈮、鋁:nb、v、ti、al都是常見的微合金元素,其作用是細化晶粒。在鋼種成分設計時,我們一般會有多種選擇,可以選用其中的一種或多種作為合金元素。然而,本鋼種選用nb+al,這是因為發(fā)明鋼在冶煉時采用al脫氧方式,鋼中有al的殘余,精煉結(jié)束前補充al能在較低的氧含量條件下保持鋼水酸熔鋁的0.010~0.050%,部分al與n生成aln顆粒(al/n≥3.5),可以細化晶粒尺寸。nb在鋼種也能形成細小的nbcn顆粒,鋼坯再加熱時未溶nbcn顆??梢宰柚箠W氏體晶粒的長大;nb能顯著提高鋼的再結(jié)晶溫度,使鋼在較高、較大的熱變形溫度范圍進行未再結(jié)晶控軋,促進晶粒的細化,提高鋼的強韌性,過量的nb往往形成降低焊接性和韌性,使鋼變脆。0.02~0.06%的鈮能起到上述的作用。鎳元素:鎳元素常常作為重要的合金元素添加到鋼中,因為鎳能提高強度和韌性。然而,在氯離子的腐蝕環(huán)境下,添加鎳具有不利影響。根據(jù)試驗室50kg的試驗爐數(shù)據(jù)表明,在≥70000mg/l的氯離子濃度時,0.02%的鎳有增加腐蝕速率的傾向。同時硫、磷、鉛、銻、鉍是鋼中的雜質(zhì)元素,在技術(shù)條件允許情況下應盡可能降低其含量,以減少原奧氏體晶界處的偏聚,提高韌性。殘余元素和氣體含量控制在相當?shù)秃克?,使鋼具有相當高的純凈度,溶于奧氏體中的碳元素與各元素之間達到理想的最佳配比含量,從而為提高材質(zhì) 的均勻性和強韌性奠定了基礎(chǔ)。硫、磷等有害元素會顯著降低鋼的塑性和韌性,必須控制在一定含量之下,其中硫≤0.015%,磷≤0.020%是必須的。作為優(yōu)選方案,所述各元素的重量百分數(shù)分別為:碳:0.12~0.22%,硅:0.17~0.33%,錳:0.40~0.59%,鉬:0.15~0.22%,鎳:≤0.01%,鉻:4.50~5.5%,al:0.010~0.035%,鈮:0.02~0.06%,硫≤0.015%,磷≤0.020%。一種如前述的抗氯離子腐蝕抽油桿鋼的制造方法,其包括如下步驟:轉(zhuǎn)爐或電弧爐初煉;鋼包爐爐外精煉;真空精煉;連鑄或模鑄;加工成棒材或盤條。作為優(yōu)選方案,所述轉(zhuǎn)爐/電弧爐熔煉,初煉爐(轉(zhuǎn)爐或電弧爐)出鋼溫度≥1620℃,氧活度≤900ppm,出鋼時加入石灰3.2~6kg/噸.作為優(yōu)選方案,所述鋼包爐爐外精煉,到精煉爐溫度≥1520℃,分批加入合金和石灰,采用渣面復合脫氧和碳化硅擴散脫氧,渣面變?yōu)辄S白色并保持≥15min,控制堿度3~7,加入鈮鐵(按收得率80~85%),成分全部進入規(guī)格后同時溫度達到≥1630℃后吊包。作為優(yōu)選方案,所述真空精煉的具體工藝參數(shù)為,采用rh或vd真空脫氣裝備,真空度≤66.7pa并保持≥20min。真空結(jié)束后,底軟吹ar(控制ar氣流量和壓力以鋼水液面微顫為原則)保持20~20min。作為優(yōu)選方案,所述連鑄或模鑄的具體工藝參數(shù)為,全程ar保護澆注,連鑄控制過熱度≤35℃,模鑄控制澆注溫度≤(液相線+40℃)控制。連鑄視鑄坯斷面控制澆注速度(以320×425mm為例,控制拉速0.5~0.6m/min),開澆溫度1515±15℃。模鑄鋼錠尺寸2.3t~5.7t。作為優(yōu)選方案,所述加工成棒材或盤條采用軋鋼機熱扎制的方法。作為優(yōu)選方案,所述軋鋼機熱軋制的方法的技術(shù)參數(shù)為:加熱爐加熱工藝:均熱溫度1130~1230℃,加熱保溫時間≥2:10小 時,鋼坯出爐溫度1130~1210℃,陰陽面溫差≤30℃;控制軋制工藝:加熱均勻的鋼坯出爐后,正常開啟高壓除鱗機,終軋溫度:780~850℃;控冷工藝:軋成盤條后在線緩冷,冷卻速度40~80℃/h,不得吹風因此,本發(fā)明的的優(yōu)點在于:1、發(fā)明鋼晶粒組織均勻細小,晶粒度9.5~12級,如圖1所示,。2、發(fā)明鋼經(jīng)調(diào)質(zhì)處理(調(diào)質(zhì)熱處理工藝為:850℃~910℃保溫45~60min淬火(油或水),550℃~680℃保溫45~90min空冷)后,得到的鋼的顯微組織照片如圖2所示,空冷獲得的顯微組織:塊狀鐵素體和顆粒狀碳化物,從組織圖中可看出,在鐵素體基體中出現(xiàn)了長條狀的析出物,而這類第二相的析出會產(chǎn)生析出強化作用。對長條析出物進行能譜分析發(fā)現(xiàn),該析出物主要是以c、fe、cr元素形成的,其中fe原始占大部分,如圖4所示,c和cr元素原子百分比例占到22.23%和4.95%,比較接近m23c6的化學計量配比,故推測形成的第二相為cr23c6;按gb/t228.1、gb/t229檢測力學性能。規(guī)定塑性延伸強度rp0.2≥793mpa,抗拉強度rm≥910mpa,伸長率≥20%,斷面收縮率≥70%,aku2≥200j。3、發(fā)明鋼具有優(yōu)良的耐腐蝕性能:抽油桿腐蝕試驗模擬試驗采用勝利油田**井的工藝參數(shù)和介質(zhì)環(huán)境(即從現(xiàn)場提取油井采出液,并進行水質(zhì)分析:礦化度為137739.4mg/l,ph值為6.6見表2)。據(jù)此采用化學分析純試劑配制試驗用水溶液。在石油大學10l三電極腐蝕試驗磁力驅(qū)動反應釜測試平均腐蝕速率,發(fā)明鋼的平均腐蝕速率為0.8724mm/a,相同試驗條件下20crmoa鋼的平均腐蝕速率為7.2485mm/a。發(fā)明鋼的抗腐蝕性能是常規(guī)鋼的8.3倍。表2cl-oh-hco3-co32-so42-na++k+ca2+mg2+總礦化度ph值7364705009016815134311924868137739.46.64、發(fā)明鋼具有良好的焊接性能:發(fā)明鋼與發(fā)明鋼,發(fā)明鋼與對比鋼(20crmoa)采用壓力焊后加工成拉伸標準試驗,調(diào)質(zhì)處理(調(diào)質(zhì)熱處理工藝為:850℃~910℃保溫45~60min淬火(油或水),550℃~680℃保 溫45~90min空冷)后按gb/t228.1、gb/t229檢測力學性能,表3表明發(fā)明鋼能與其他材料友好焊接。表3附圖說明通過閱讀參照以下附圖對非限制性實施例所作的詳細描述,本發(fā)明的其它特征、目的和優(yōu)點將會變得更明顯:圖1為本發(fā)明制造的鋼的原始晶粒度組織照片;圖2為本發(fā)明制造的鋼在調(diào)制熱處理后的內(nèi)部組織照片;圖3為本發(fā)明制造的鋼在淬火空冷后的tem照片;圖4為本發(fā)明制造的鋼在淬火空冷后的光電子能譜圖。具體實施方式下面結(jié)合具體實施例對本發(fā)明進行詳細說明。以下實施例將有助于本領(lǐng)域的技術(shù)人員進一步理解本發(fā)明,但不以任何形式限制本發(fā)明。應當指出的是,對本領(lǐng)域的普通技術(shù)人員來說,在不脫離本發(fā)明構(gòu)思的前提下,還可以做出若干變形和改進。這些都屬于本發(fā)明的保護范圍。實施例1本實施例中各元素的配比如表4所示。本實施例的抗氯離子腐蝕抽油桿鋼的制造方法包括如下步驟:采用二步法工藝流程:第一步:轉(zhuǎn)爐或電弧爐初煉→鋼包爐爐外精煉-真空精煉→連鑄或模鑄;第二步:軋鋼機熱加工軋制成棒材或盤條。將鋼坯加熱至1130~1230℃。鋼坯均熱后出爐,經(jīng)除鱗后,在1050~1100℃溫度區(qū)間內(nèi)進入粗軋機組,初軋過程中,一方面使鋼坯均勻變形,一方面控制鋼坯的降溫速度,使鋼坯出初軋機組溫度控制在 1030~1000℃??刂其撆鬟M精軋機組前的冷卻速度,在該過程中使鋼中的形變奧氏體完成再結(jié)晶。鋼坯在980~910℃之間進入多道次的精軋機組,在奧氏體未再結(jié)晶區(qū)軋制,軋制過程中控制線材的冷卻速度,使其在850~800℃溫度區(qū)間內(nèi)出精軋,在輸送線上冷卻至750~660℃后進入緩冷區(qū)緩慢冷卻。該抽油桿棒(線)材直徑為φ16~35mm,晶粒度9~12級。表4實施例鋼棒的化學成分,wt%實施例2本實施例中各元素的配比如表4所示。本實施例的抗氯離子腐蝕抽油桿鋼的制造方法同實施例1。實施例3本實施例中各元素的配比如表4所示。本實施例的抗氯離子腐蝕抽油桿鋼的制造方法同實施例1。實施例4本實施例中各元素的配比如表4所示。本實施例的抗氯離子腐蝕抽油桿鋼的制造方法同實施例1。實施例5本實施例中各元素的配比如表4所示。本實施例的抗氯離子腐蝕抽油桿鋼的制造方法同實施例1。實施例6本實施例中各元素的配比如表4所示。本實施例的抗氯離子腐蝕抽油桿鋼的制造方法同實施例1。實施例7本實施例中各元素的配比如表4所示。本實施例的抗氯離子腐蝕抽油桿鋼的制造方法同實施例1。實施例8本實施例中各元素的配比如表4所示。本實施例的抗氯離子腐蝕抽油桿鋼的制造方法同實施例1。上述各實施例制造的產(chǎn)品鋼在調(diào)質(zhì)處理后其力學性能達如表5所示,均達到或超過相應的技術(shù)標準。表5實施例鋼棒的力學性能注:調(diào)質(zhì)熱處理工藝為:850℃~910℃保溫45~60min淬火(油或水), 550℃~680℃保溫45~90min空冷。本發(fā)明制造的鋼具有優(yōu)良的耐腐蝕性能:抽油桿腐蝕試驗模擬試驗采用勝利油田**井的工藝參數(shù)和介質(zhì)環(huán)境(即從現(xiàn)場提取油井采出液,并進行水質(zhì)分析:礦化度為137739.4mg/l,ph值為6.6見表2)。據(jù)此采用化學分析純試劑配制試驗用水溶液。樣棒在美國cortest應力環(huán)測試系統(tǒng)內(nèi)20天后,在慢速率拉伸試驗機測試殘余拉伸強度,計算抗拉強度和斷面收縮率的損失比例,如表6所示,表6的說明:在美國cortest應力環(huán)測試系統(tǒng)內(nèi)(拉伸應力為70%σb)20天后,采用慢拉伸試驗機測試殘余拉伸性能發(fā)現(xiàn),發(fā)明鋼損失的強度和韌性均在7%以內(nèi),說明發(fā)明鋼具有良好的耐氯離子腐蝕性能。表6試樣的強度損失及塑性損失實施例抗拉強度損失率,%剩余斷面收縮率損失率,%10.844.3920.211.4931.476.1941.471.1651.443.4960.215.0970.000.1480.622.93綜上所述,僅為本發(fā)明的較佳實施例而已,并非用來限定本發(fā)明實施的范圍,凡依本發(fā)明權(quán)利要求范圍所述的形狀、構(gòu)造、特征及精神所為的均等變化與修飾,均應包括于本發(fā)明的權(quán)利要求范圍內(nèi)。當前第1頁12