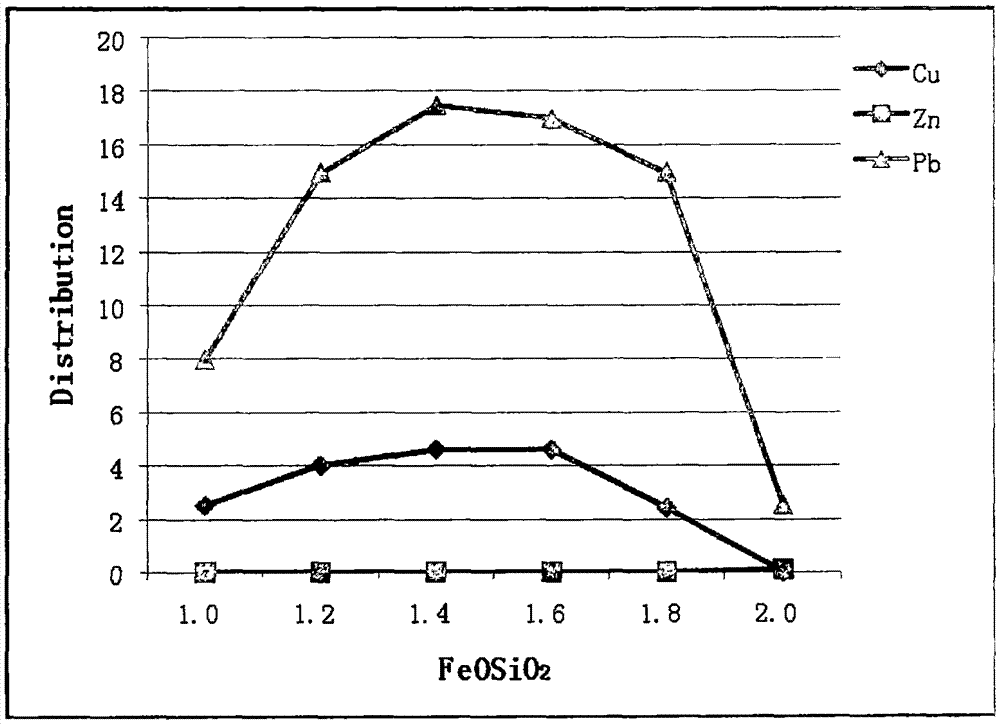
本發(fā)明涉及冶金
技術(shù)領(lǐng)域:
,具體是熔融液態(tài)高鉛渣節(jié)能還原熔煉方法。
背景技術(shù):
:我國的鉛生產(chǎn)量和消費(fèi)量居世界第一。鉛渣一般是火法煉鉛的冶煉渣,鉛渣中含鐵21-31%、含鋅2-15%、含鉛0.02-3%。目前鉛渣大量堆存,占用土地資源并污染環(huán)境。鉛渣的處理主要集中于回收鉛渣中鉛鋅和稀散金屬、將鉛渣作井下礦坑的充填材料、生產(chǎn)玻璃及陶瓷、生產(chǎn)磚和砌塊水泥等建材等,但鉛渣中大量的鉛與鋅資源未得到回收。鋅的用途十分廣泛,在國民經(jīng)濟(jì)中占有重要的地位,鋅的熔點(diǎn)較低,熔體流動(dòng)性好,有較好的抗腐蝕性能,主要用于鍍鋅工業(yè),常作為鋼鐵的保護(hù)層,如鍍鋅的板材管件等,其消耗量占世界鋅消耗量的50%。而我國鉛渣量大,渣中的鉛、鋅含量高,因此將鉛渣中的鉛、鋅資源作為原料不失為彌補(bǔ)我國礦石資源長期短缺的一種途徑。目前鉛渣中鉛、鋅資源的回收利用缺乏有效的方法,使得鉛渣中鉛、鋅資源得不到高效回收利用??梢哉f鉛渣中的鉛、鋅資源的回收利用是冶金和環(huán)境領(lǐng)域啞待解決的難題,迫切需要一種節(jié)能、高效、流程短的工藝方法回收鉛渣中伴生的資源。技術(shù)實(shí)現(xiàn)要素:本發(fā)明的目的在于提供流程簡單、處理效果好、成本低熔融液態(tài)高鉛渣節(jié)能還原熔煉方法,以解決上述
背景技術(shù):
中提出的問題。為實(shí)現(xiàn)上述目的,本發(fā)明提供如下技術(shù)方案:熔融液態(tài)高鉛渣節(jié)能還原熔煉方法,利用還原劑對熔融液態(tài)鉛渣進(jìn)行直接還原,還原劑的加入量是熔融液態(tài)鉛渣質(zhì)量的3.25~3.5%;還原溫度為1200~1225℃;還原時(shí)間為30~60min。作為本發(fā)明進(jìn)一步的方案:還原劑采用co、c、固體煤、h2或ch4。作為本發(fā)明進(jìn)一步的方案:還原劑采用固體煤。作為本發(fā)明進(jìn)一步的方案:還原劑采用固體無煙煤。作為本發(fā)明進(jìn)一步的方案:熔融液態(tài)鉛渣采用的渣型是cao/sio2在0.4~0.8之間,feo/sio2在1.2~1.8之間。作為本發(fā)明進(jìn)一步的方案:feo/sio2=1.5。與現(xiàn)有技術(shù)相比,本發(fā)明的有益效果是:本發(fā)明克服了高鉛體系下鉛、鋅回收率低的難題,流程簡單,處理效果好,能高效回收鋅等有價(jià)金屬,解決大量廢棄渣堆存造成的環(huán)境污染及資源浪費(fèi)問題。本發(fā)明直接冶煉處理熔融鉛渣,充分利用熔融鉛氧化渣的熱焓,節(jié)省能源。本發(fā)明的冶煉方法采用直接還原方法,提高碳質(zhì)還原劑的利用率,節(jié)省冶煉成本。附圖說明圖1是鐵硅比對鉛鋅銅的回收率的影響;圖2是鐵硅比對鉛鋅銅分配的影響;圖3是鈣硅比對鉛鋅銅回收率的影響;圖4是鈣硅比對鉛鋅銅分配的影響;圖5是溫度對無煙煤的co2還原率的影響;圖6是還原劑煤比對試驗(yàn)的影響效果;圖7是還原劑煤比對金屬回收率的影響;圖8是還原溫度對金屬回收率的影響(時(shí)間60min);圖9是還原溫度對金屬回收率的影響(時(shí)間30min);圖10是還原時(shí)間對金屬回收率的影響(溫度1200℃);圖11是還原時(shí)間對金屬回收率的影響(溫度1225℃);圖12是還原時(shí)間對金屬回收率的影響(溫度1250℃);圖13是鈣硅比0.45還原溫度對金屬回收率的影響;圖14是不同鈣硅比對金屬回收率的影響;圖15是不同鐵硅比對金屬回收率的影響。具體實(shí)施方式下面將結(jié)合本發(fā)明實(shí)施例,對本發(fā)明實(shí)施例中的技術(shù)方案進(jìn)行清楚、完整地描述,顯然,所描述的實(shí)施例僅僅是本發(fā)明一部分實(shí)施例,而不是全部的實(shí)施例。基于本發(fā)明中的實(shí)施例,本領(lǐng)域普通技術(shù)人員在沒有做出創(chuàng)造性勞動(dòng)前提下所獲得的所有其他實(shí)施例,都屬于本發(fā)明保護(hù)的范圍。實(shí)施例11.1高鉛渣還原過程的渣型選擇的實(shí)驗(yàn)研究鉛渣是復(fù)雜的多元系,是由各種氧化物組成的,它們相互結(jié)合而形成化合物、固溶體、液熔體及共晶混合物。具體地說,爐渣是由各種金屬的硅酸鹽、亞鐵酸鹽及鋁酸鹽等所組成;此外,含有少量的金屬硫化物、金屬及氣體。sio2、feo和cao是鉛爐渣的主要成分,但相對其他有色金屬爐渣而言,高cao、高zno含量又是鉛爐渣的特點(diǎn)。對鉛冶煉爐渣的要求主要有:(1)爐渣成分必須符合熔煉時(shí)熔劑消耗量最少的要求;(2)爐渣的熔點(diǎn)合適;(3)爐渣的粘度要?。?4)爐渣比重要小;(5)爐渣的表面性質(zhì)(表面張力、界面張力等)對爐渣與金屬或锍的分離起著重要的作用,此外,爐渣對耐火材料的腐蝕也與爐渣的表面性質(zhì)有較大的關(guān)系。為了降低渣含鉛,提高原料綜合利用程度和處理高鋅物料,廣泛采用高鋅高鈣渣型。本發(fā)明中,爐渣擬采用鐵鈣硅酸鹽的熔合體,并選擇合適的鐵硅比和鈣硅比。1.1.1鐵硅比對高鉛渣還原過程有價(jià)金屬分布的影響圖1為feo/sio2比對高鉛渣還原過程中鉛鋅銅回收率的影響。由圖可知,鉛和銅主要存在于金屬相中,鋅則主要存在于渣中。鉛和銅的回收率均呈先增大后減小的趨勢,但兩者趨勢有明顯的不同。在feo/sio2比例為1.0-1.8的范圍內(nèi),pb回收率呈現(xiàn)平穩(wěn)增長的趨勢,在feo/sio2=1.8時(shí)達(dá)到最高的回收率84.8%,進(jìn)一步增加feo/sio2比例將導(dǎo)致pb回收率急劇下降。而cu回收率在feo/sio2=1.25時(shí)達(dá)到最高值(81.7%),增大或減小feo/sio2比均將導(dǎo)致回收率大幅度的下降,當(dāng)feo/sio2比增大至2.0時(shí)甚至將降低至20%。在金屬相中基本沒有檢出鋅,說明在實(shí)驗(yàn)所檢測的feo/sio2比例下鋅主要是進(jìn)入渣相中,因此鋅的回收率主要通過渣中鋅含量來考察。如圖1所示,其隨feo/sio2變化顯示出與pb、cu 相反的趨勢。鋅在feo/sio2為1.5時(shí)在渣中含量最少(75%)增大和降低feo/sio2將提高鋅的回收率,最高可達(dá)到90%。圖2為feo/sio2對高鉛渣還原過程中鉛鋅銅分配行為的影響。由圖可知,隨著feo/sio2的增加,鉛、銅的分布呈先增長后減小的趨勢,而鋅的則由于主要進(jìn)入渣相而在實(shí)驗(yàn)測試的feo/sio2范圍內(nèi)分配比平穩(wěn)地保持在0附近。值得注意的是,不同的feo/sio2比例下,pb的分配比均高于cu,且feo/sio2比對pb分配比的影響非常明顯。當(dāng)feo/sio2比從1增加到1.5時(shí),分配比從8.2增大到18.6,增長幅度達(dá)到1.2倍,進(jìn)一步增加feo/sio2比則導(dǎo)致分配比急劇下降,feo/sio2=2時(shí)分配比下降至最低(1.6)。cu分配比受feo/sio2比的影響相對較小,除feo/sio2=2.0時(shí)分配比為0.4外,其他比例下分配比均在2以上,且與最高分配比4.9(feo/sio2=1.5)差值不大。這些結(jié)果與圖1所示結(jié)果具有較好的對應(yīng)性,說明在feo/sio2=1.5的條件下pb、cu可以獲得在金屬相中最大的分配,而鋅則主要進(jìn)入渣中,因此feo/sio2=1.5為最佳條件。1.1.2鈣硅比對高鉛渣還原過程有價(jià)金屬分布的影響圖3為cao/sio2對有價(jià)金屬回收率以及在金屬、渣相中分配比的影響。實(shí)驗(yàn)結(jié)果如圖2所示。由圖可知,中可以看到在高鉛渣還原中不同鈣硅比時(shí)鉛鋅銅回收率的變化。當(dāng)cao/sio2在0.4~0.8之間變化時(shí),鉛、銅的回收率上升而鋅的回收率下降。在cao/sio2=0.8時(shí),pb達(dá)到最高的回收率84.9%,zn的回收率在此時(shí)則降低至最低。繼續(xù)提高cao/sio2比將使得pb的回收率降低,而銅和鋅的回收率則會(huì)繼續(xù)保持上升的趨勢,并分別達(dá)到最高點(diǎn)(81.3%,100%),在實(shí)驗(yàn)所用最高的cao/sio2(1.4)下,鉛和銅回收率均大幅降低,分別為51%和10%。鋅的回收率則繼續(xù)保持在最高點(diǎn)。圖4顯示了采用不同鈣硅比時(shí)鉛鋅銅在金屬相和渣相中的分配比??梢钥闯觯琧ao/sio2為0.8時(shí)鉛、銅的分配比均達(dá)到最大值,鋅的分配比則在整個(gè)測試范圍內(nèi)基本保持在0。在其他的cao/sio2比下,鉛、銅的分配分別在3.8和2左右波動(dòng),差別并不顯著。值得一提的是,當(dāng)cao/sio2比為1.4時(shí),鉛、銅分配比均下降至最低值。綜上所述,液態(tài)高鉛渣直接還原實(shí)驗(yàn)室所采用的渣型是cao/sio2在0.4~0.8,feo/sio2在1.2~1.8之間。1.2確定的渣型與傳統(tǒng)鼓風(fēng)爐熔煉渣的比較原來的常規(guī)鉛燒結(jié)塊為自熔疏松多孔的塊狀物,孔隙率一般為50%-60%,堆比重1.8-2.2,塊度一般為50~150mm。燒結(jié)塊中以硅酸鉛和游離氧化鉛形態(tài)存在的鉛約占總鉛量40%-60%,故在鼓風(fēng)爐還原熔煉時(shí),游離pbo在600℃時(shí)已大量被還原,各種硅酸鉛在700~900℃時(shí)開始熔化并還原,其它金屬氧化物熔體中鉛化合物在熔化區(qū)被上升氣流中的co及熔劑中的cao、feo所還原和置換,在焦點(diǎn)區(qū),c直接參與了從熔體中還原硅酸鉛中的鉛。由于鉛燒結(jié)塊表面積大,co氣固反應(yīng)和碳的直接還原反應(yīng)比較活躍,還原過程進(jìn)行得很徹底。氧氣底吹爐得到高鉛渣為一種含鉛高、致密的塊狀物料,堆比重3.05,比表面積小,氣(co)-固(固態(tài)高鉛渣)還原接觸面積小,還原能力弱,和燒結(jié)塊有很大的差別。鉛鼓風(fēng)爐還原熔煉所產(chǎn)爐渣特點(diǎn)是渣含zno較高,通常sio2、feo、cao和zno之和占渣總量的85%-90%。鼓風(fēng)爐渣含鉛一般為3%-5%,占熔煉過程總損失的60%-70%。鼓風(fēng)爐熔煉鉛在渣中的損失形態(tài)主要分為三類:①硅酸鉛形態(tài)的化學(xué)損失;②以硫化鉛溶解于渣中的物理損失;③以金屬鉛微粒夾雜的機(jī)械損失。一般來說,降低渣含鉛是提高金屬回收和企業(yè)經(jīng)濟(jì)效益的關(guān)鍵。一般爐渣中鈣硅比為w(cao)/w(sio2)=0.4-0.8,w(feo)/w(sio2)=0.6-1.3。液態(tài)還原爐渣鈣低鋅高的鐵硅渣型,且渣中鉛含量小于2%,綜合上面的實(shí)驗(yàn),初步確定液態(tài)還原渣中w(cao)/w(sio2)<0.8,w(feo)/w(sio2)=0.6-1.4,主要是cao含量較低,同時(shí)鐵含量較高。1.3還原終渣中氧化鉛和金屬鉛的溶解行為還原渣中的相別有氧化鉛相、砷酸鉛相、鐵酸鋅相、尖晶石相、硅酸鹽相、硫化物相及玻璃相。鉛在該還原渣中主要有三種損失狀態(tài),一是氧化鉛相、二是砷酸鉛相,三是玻璃相,后者是鉛的主要損失形式,而氧化鉛和砷酸鉛在該渣中的含量比較低。表1為對玻璃相進(jìn)行的掃描電鏡能譜分析,玻璃相中鉛的平均含量為2.31%。表1玻璃相的基本化學(xué)組成(%)測點(diǎn)naalsipsclkcamnfeznbapbo12.885.6618.501.040.410.295.557.470.8211.134.731.861.5838.0823.096.0218.390.880.040.454.935.890.799.576.205.291.3037.1632.756.2319.050.600.310.415.427.190.7310.774.272.521.5638.1943.765.9719.260.720.460.374.814.890.837.737.343.622.2537.9953.705.2419.360.730.290.464.455.590.598.686.774.572.0537.5263.664.4618.480.460.300.394.095.880.619.048.044.503.9936.1073.195.3818.560.570.230.444.856.880.8011.126.532.331.8337.2983.214.6019.710.660.040.314.014.740.889.658.853.312.9137.1293.713.8919.080.660.260.513.466.641.009.955.894.234.2336.49103.635.1519.870.730.330.464.585.350.827.866.024.003.5137.69113.574.8919.230.720.060.324.266.590.508.756.923.263.8737.06123.644.2619.230.560.070.414.405.860.869.237.543.943.5136.49133.334.9919.720.690.100.314.666.200.798.366.893.562.9137.49142.275.0418.960.400.260.234.428.741.4211.515.501.292.3837.58153.105.5019.560.510.230.304.845.860.879.725.763.162.9637.63163.385.5419.50.420.240.425.026.280.8810.34.763.691.8837.69173.846.0620.370.390.210.395.545.930.679.154.722.571.5238.64183.225.0218.980.710.340.474.685.600.718.378.653.642.4537.16193.515.4318.760.670.60.424.666.400.838.296.574.282.0237.56203.656.6219.80.570.350.405.434.790.847.725.263.702.5138.36214.085.4319.150.400.400.485.054.900.327.927.925.241.5037.21223.485.5319.950.810.270.325.674.690.617.497.044.551.5738.02233.397.1119.030.700.290.536.135.040.428.745.443.641.2738.27244.008.1619.250.450.230.136.125.740.618.243.863.880.3039.03253.995.1118.690.590.260.424.75.370.468.388.864.341.9836.85平均3.445.4919.220.620.260.394.875.940.759.116.413.642.3137.552突破了液態(tài)高鉛渣還原過程氣氛優(yōu)化控制關(guān)鍵技術(shù)2.1高鉛渣還原過程機(jī)制根據(jù)pb-s-o系氧位圖,熔煉時(shí)鉛液穩(wěn)定存在的溫度區(qū)域應(yīng)高于900℃,同時(shí)為保證氧氣底吹爐渣的過熱要求,冶煉的溫度區(qū)域一般控制在1000-1150℃,排出的高鉛渣溫度在900℃以上。高鉛渣中的鉛主要以氧化鉛和硅酸鉛存在,通過熱力學(xué)計(jì)算,co、c、h2、ch4都可作為還原劑,考慮加入固體煤作為還原劑。pbo+c=pb+copbo+co=pb+co2pbo·sio2+c=pb+co+sio2pbo·sio2+co=pb+co2+sio2在還原熔煉中,氧化鉛被co還原是其主要途徑,而硅酸鉛的還原一定是在有堿性氧化物(cao和feo)參與下,并且主要在爐料熔化后發(fā)生,其原因在于只有在熔融狀態(tài)下硅酸鉛才能與堿性氧化物、還原劑或co有良好接觸,從而完成還原反應(yīng)。pbo·sio2+cao+co=cao·sio2+pb+co22pbo·sio2+2cao+2co=2cao·sio2+2pb+2co2pbo·sio2+feo+co=feo·sio2+pb+co22pbo·sio2+2feo+2co=2feo·sio2+2pb+2co22pbo·sio2+cao+feo+2co=cao·feo·sio2+2pb+2co2pbo·fe2o3+co=pb+fe2o3+co2fe2o3+co=2feo+co2顯然,液態(tài)鉛渣直接還原與高鉛渣鑄塊鼓風(fēng)爐還原的不同是因?yàn)殂U渣入爐狀態(tài)和方式的不同造成的。在鼓風(fēng)爐還原高鉛渣鑄塊過程中,在以焦炭作還原劑時(shí),氧化鉛和硅酸鉛的還原是包含了與還原劑固(鉛的氧化物)一固(焦炭)或固(鉛的氧化物)-氣(co)接觸,到液(熔融的鉛的氧化物)一固(熾熱焦炭)或液(熔融的鉛的氧化物)-氣(co)接觸過程的。當(dāng)高鉛渣以液態(tài)方式進(jìn)入還原過程時(shí),由于不管是固體氧化鉛還是液體氧化鉛都是易還原的氧化物,而熔融的爐料又有利于硅酸鉛的還原,所以液態(tài)鉛渣的直接還原就顯而易見了。2.2高鉛渣還原還原氣氛的調(diào)控在煤比3.5%,還原溫度1250℃,時(shí)間60min時(shí),在管式爐中進(jìn)行鉛渣的還原反應(yīng)。在升溫過程以及保溫階段,進(jìn)行了氣體的取樣和成分測定,明確還原過程中氣氛的變化過程。利用奧氏氣體分析儀主要進(jìn)行了co2、co和o2的分析測定,氧氣的吸收劑為焦性沒食子酸的堿性溶液,二氧化碳為酸性氧化物,一般采用苛性堿(koh)為吸收劑,用氯化亞銅氨性溶液做一氧化碳的吸收劑。具體檢測結(jié)果如表2所示。由表可知,隨著溫度的升高,碳氧反應(yīng)發(fā)生,生成一氧化碳和二氧化碳。同時(shí)一氧化碳含量增加并趨于穩(wěn)定,二氧化碳含量降低并趨于穩(wěn)定,co/co2比值逐漸增加。氧氣和氮?dú)獾暮吭谶€原過程中基本穩(wěn)定。 溫度1100℃之后,還原氣氛的組成基本穩(wěn)定,co含量基本在體積百分比60%左右。表2鉛渣還原過程中氣體的組成及變化2.3開展了高鉛渣還原實(shí)驗(yàn)及鋅富集技術(shù)研究以高鉛渣為原料,于還原過程中考察主要金屬鉛、鋅、銅、鐵的走向,并確定合小試針對高鉛渣原料,進(jìn)行不同工藝參數(shù)研究,并考察主要金屬鉛、鋅、銅、鐵的走向。確定合理的還原參數(shù)并驗(yàn)證確定的確定的渣型。2.3.1還原劑煤的物化性能研究表3為試驗(yàn)所用還原劑為固體無煙煤的成分和物理性能分析結(jié)果由表可知該還原劑煤碳含量高,灰分低,孔隙度大。表3無煙煤物理化學(xué)分析表4為以co2作為氣體介質(zhì),煤對二氧化碳的化學(xué)反應(yīng)性分析結(jié)果。由表可知,各種 煤的反應(yīng)性隨煤化度的加深而減弱。因?yàn)樘己蚦o2反應(yīng)不僅在燃料的外表面進(jìn)行,而且也在燃料內(nèi)部微細(xì)孔隙的毛細(xì)管壁上進(jìn)行,孔隙率愈高,反應(yīng)的表面積愈大。不同煤化度煤的氣孔率、化學(xué)結(jié)構(gòu)不同,因此其反應(yīng)性不同。褐煤的反應(yīng)性最強(qiáng),但當(dāng)溫度較高(900℃以上)時(shí),反應(yīng)性增高減慢。無煙煤的反應(yīng)性最弱,但在較高溫度時(shí),隨溫度升高其反應(yīng)性顯著增強(qiáng)。煤的灰分組成與數(shù)量對其反應(yīng)性也有明顯的影響。堿金屬和堿土金屬對碳與co2的反應(yīng)起著催化作用,使煤的反應(yīng)性提高。圖5為溫度對無煙煤的co2還原率的影響,由圖可知,煤的co2還原率α隨著溫度升高而增加,表明生成co量增加,煤的化學(xué)反應(yīng)性隨反應(yīng)溫度的升高而增強(qiáng)。表4無煙煤對co2化學(xué)反應(yīng)性2.3.2還原劑煤用量圖6和圖7分別表示在高鉛渣400g,溫度1250℃,時(shí)間60min條件下,不同還原劑無煙煤用量對高鉛渣的還原效果和有價(jià)金屬回收率的影響,由圖可知隨著煤比的增加,鉛渣的失重率增大,表明高鉛渣中的各種氧化物被還原程度增強(qiáng)。渣中的鉛含量逐漸降低,同時(shí)鋅含量也逐漸降低。渣中的鐵含量先略有增加然后逐漸降低。由圖7可知,金屬塊中鉛和銅的回收率隨著煤比的增加而增加。而還原渣中鋅和鐵的回收率隨著煤比增加而降低,尤其是煤比在3.5%以后,鋅由于揮發(fā)進(jìn)入煙氣、鐵由于還原進(jìn)入金屬都使還原渣中鋅、鐵含量降低。高鉛渣原料中鈣硅比為0.17,不同煤比還原后的 鈣硅比大致還在0.17左右,表明還原劑煤中所含的cao和sio2對還原渣的渣型影響甚微,在后面研究中不考慮還原劑煤中所含化學(xué)成分的影響。試驗(yàn)表明,在煤比3.25%時(shí),還原渣中鉛含量2.41%,此時(shí)鉛的回收率為98.11%,而鋅的回收率為85.19%。在煤比3.5%時(shí),還原渣中鉛含量1.48%,此時(shí)鉛的回收率為98.86%,而鋅的回收率僅為82.91%。綜合考慮建議煤比在3.25~3.5%。2.3.3還原劑溫度的影響表5和表6分別為在煤比3.25%和3.5%,時(shí)間60min時(shí),不同還原溫度對高鉛渣的還原效果。表7在煤比3.25%和3.5%,時(shí)間30min時(shí),不同還原溫度對高鉛渣的還原效果。由表5、表6及圖8可知,還原時(shí)間60min時(shí),隨著還原溫度的升高,鉛的回收率稍有增加,且煤比3.5%比煤比3.25%的鉛回收率稍高,煤比高,則還原氣氛高,利于鉛的還原;鋅的回收率降低比較明顯,溫度升高增加了鋅的揮發(fā)。且煤比3.5%比煤比3.25%的鋅回收率低,煤比高,則還原氣氛高也增加了鋅的揮發(fā);銅的回收率呈現(xiàn)先增加再降低的趨勢,在1225℃時(shí)銅回收率最大,且煤比3.5%比煤比3.25%的銅回收率稍高;鐵的回收率隨還原溫度升高逐漸增加,鐵酸鉛溫度高時(shí)才能被還原,使鐵以feo和硅造渣進(jìn)入渣相,且煤比3.5%比煤比3.25%的鐵回收率低,煤比高則還原氣氛強(qiáng),會(huì)使鐵還原進(jìn)入金屬相。表5不同還原溫度的還原試驗(yàn)情況(時(shí)間60min,煤比3.25%)表6不同還原溫度的還原試驗(yàn)情況(時(shí)間60min,煤比3.5%)由表7及圖9可知,還原時(shí)間30min時(shí),隨著還原溫度的升高,鉛的回收率稍有增加,且煤比3.5%比煤比3.25%的鉛回收率稍高;鋅的回收率降低比較明顯,且煤比3.5%比煤比3.25%的鋅回收率低;銅的回收率影響不明顯,且煤比3.5%比煤比3.25%的銅回收率稍高;鐵的回收率隨還原溫度升高逐漸增加,且煤比3.5%比煤比3.25%的鐵回收率低。還原時(shí)間30min時(shí)試驗(yàn)現(xiàn)象與還原時(shí)間60min時(shí)相同,但還原時(shí)間較短時(shí),鋅的回收率相對較高,鐵的回收率相對較低。另外,還原溫度低時(shí),試驗(yàn)中渣金分離效果不好,使金屬相中夾雜有浮渣,還原溫度升高,鉛、鐵的回收率稍有增加,但鋅的回收率降低。綜合考慮,建議還原溫度為1200~1225℃。表7不同還原溫度的還原試驗(yàn)情況(時(shí)間30min)2.3.4還原劑時(shí)間的影響表8~表10分別為在1200℃、1225℃和1250℃時(shí),不同還原時(shí)間對高鉛渣還原效果的影響。由表8和圖10可知,在溫度1200℃時(shí),隨著還原時(shí)間的延長,鉛的回收率稍有增加,且煤比3.5%比煤比3.25%的鉛回收率稍高;鋅的回收率稍有降低,且煤比3.5%比煤比3.25%的鋅回收率低;銅的回收率略有降低,且煤比3.5%比煤比3.25%的銅回收率稍高;鐵的回收率隨還原時(shí)間延長逐漸增加,且煤比3.5%比煤比3.25%的鐵回收率低。由表9和圖11可知,在溫度1225℃時(shí),隨著還原時(shí)間的延長,鉛的回收率稍有增加,且煤比3.5%比煤比3.25%的鉛回收率稍高;鋅的回收率稍有降低,且煤比3.5%比煤比3.25%的鋅回收率低;銅的回收率變化不明顯,且煤比3.5%比煤比3.25%的銅回收率稍高;鐵的回收率隨還原時(shí)間延長逐漸增加,且煤比3.5%比煤比3.25%的鐵回收率低。表8不同還原時(shí)間的還原試驗(yàn)情況(溫度1200℃)由表10和圖12可知,在溫度1250℃時(shí),隨著還原時(shí)間的延長,對鉛、鋅、銅和鐵的回收率影響不明顯,鉛和銅回收率煤比3.5%比煤比3.25%的稍高。鋅和鐵回收率煤比3.5%比煤比3.25%的稍低。由此可見,在溫度1200℃和1225℃隨著還原時(shí)間延長,渣中鉛含量逐漸降低,鉛、鐵的回收率稍有增加,鋅的回收率隨著時(shí)間增加逐漸降低。在溫度1250℃時(shí),還原時(shí)間對鉛、鋅、銅和鐵的回收率影響不明顯。還原時(shí)間對鉛還原反應(yīng)影響不顯著,對鐵和鋅回收率略有影響。在煤比3.5%,1200℃溫度下還原時(shí)間為30min,渣含鉛為1.91%,鋅回收率為90.85%,鐵回收率為91.73%;還原時(shí)間為60min,渣含鉛為1.83%,鋅回收率為89.43%,鐵回收率為92.58%。1225℃溫度下還原時(shí)間為30min,渣含鉛為1.84%,鋅回收率為89.36%,鐵回收率為92.11%;還原時(shí)間為60min,渣含鉛為1.35%,鋅回收率為87.95%,鐵回收率為94.21%。綜合考慮建議還原時(shí)間為30~60min。表9不同還原時(shí)間的還原試驗(yàn)情況(溫度1225℃)表10不同還原時(shí)間的還原試驗(yàn)情況(溫度1250℃)2.3.5鈣硅比的影響高鉛渣中w(cao)/w(sio2)為0.17,w(feo)/w(sio2)為1.66,相對傳統(tǒng)渣型,鈣硅比較 低。配入碳酸鈣,提高還原渣的鈣硅比,考察不同渣型的影響。在高鉛渣400g,煤比3%,時(shí)間60min條件下,考察鈣硅比0.45時(shí)不同溫度對高鉛渣的還原效果。具體試驗(yàn)情況見表11。由表11和圖13可知,在鈣硅比0.45時(shí),隨著還原溫度升高,渣中鉛的含量降低,鉛和銅的回收率在1100℃前增加明顯,1100℃后隨著還原溫度升高緩慢增加,鋅的回收率逐漸降低,鐵的回收率略有波動(dòng)。表11鈣硅比0.45時(shí)不同還原溫度的試驗(yàn)情況表12為當(dāng)高鉛渣400g,煤比3.5%,溫度1250℃,時(shí)間60min,鉛渣中w(cao)/w(sio2)為0.17,w(feo)/w(sio2)為1.66時(shí),不同鈣硅比對高鉛渣的還原效果。由表12和圖14可知,在1250℃時(shí),隨著鈣硅比的增加,渣中鉛的含量逐漸升高,鉛和銅回收率稍有降低,同時(shí)鋅的回收率基本沒影響,鐵的回收率有所降低。通過上述試驗(yàn)結(jié)果,添加碳酸鈣調(diào)整渣型的鈣硅比,由于鈣硅比增加使渣的熔點(diǎn)增高,使鉛金屬回收率降低,同時(shí)也增加了還 原渣量。因此試驗(yàn)中建議不添加碳酸鈣,保持還原渣低的鈣硅比。表12不同鈣硅比的還原試驗(yàn)情況2.3.6鐵硅比的影響表13和圖15為不同鐵硅比對高鉛渣的還原效果的影響。由表13和圖15可知,在1250℃時(shí),隨著鐵硅比的增加,鉛、銅和鐵回收率基本不變,而鋅的回收率略有降低。表13不同鐵硅比的試驗(yàn)情況2.4鋅在還原渣中產(chǎn)出形式除了氧化鉛和砷酸鉛相外,鋅在該還原渣的各相中都有所分布。鋅主要是賦存在尖晶石、鐵酸鋅中,其次是賦存在硅酸鹽相中,當(dāng)硅酸鹽相中含鐵較高時(shí),含鈣亦較高時(shí),而鋅的含量一般較低,少量的鋅賦存在玻璃相中,而以硫化物相產(chǎn)出的鋅極少。鋅在該渣中典型的產(chǎn)出狀態(tài)如下所述。該還原渣中尖晶石以zn-fe尖晶石為主,其成分中平均含zn16.77%、al9.52%、fe40.26%、o31.44%;鐵酸鋅平均含zn9.57%、fe51.95%、o30.89%。硅酸鹽相按其成分可以分為以zn為主的硅酸鹽和fe為主硅酸鹽,以含鋅為主的硅酸鹽的平均成分中含zn34.87%、fe16.42%、si13.72%、o30.76%;以含鐵為主的硅酸鹽的平均成分中含fe35.53%、zn7.81%、ca4.40%、mn5.72%、si14.25%、o31.96%。該還原渣中主要相別典型產(chǎn)出特征。尖晶石和鐵酸鋅形成的溫度一般較高,在還原體系溫度下降時(shí)往往結(jié)晶較早,尤其是尖晶石多呈自形晶產(chǎn)出,且具有一定的反應(yīng)邊結(jié)構(gòu); 隨著體系溫度的降低,硅酸鹽相隨后形成,最后形成的是玻璃相,玻璃相成分較為復(fù)雜,不同程度地含zn、fe、pb、k、na、s、cl等元素。2.5液態(tài)高鉛渣還原綜合條件綜合上述還原試驗(yàn),確定高鉛渣還原的基本工藝參數(shù)為:還原劑煤比在3.25~3.5%;還原溫度為1200~1225℃;還原時(shí)間為30~60min。此時(shí),試驗(yàn)結(jié)果能滿足考核指標(biāo),渣中鉛含量小于2%,85%鋅在渣中。在試驗(yàn)y-111工藝下,即煤比3.5%,溫度1225℃,時(shí)間30min時(shí),渣中鉛含量1.84%,鉛的回收率98.57%,鋅的回收率89.36%。在試驗(yàn)y-97工藝下,即煤比3.5%,溫度1225℃,時(shí)間60min時(shí),渣中鉛含量1.35%,鉛的回收率98.97%,鋅的回收率87.95%。對于本領(lǐng)域技術(shù)人員而言,顯然本發(fā)明不限于上述示范性實(shí)施例的細(xì)節(jié),而且在不背離本發(fā)明的精神或基本特征的情況下,能夠以其他的具體形式實(shí)現(xiàn)本發(fā)明。因此,無論從哪一點(diǎn)來看,均應(yīng)將實(shí)施例看作是示范性的,而且是非限制性的,本發(fā)明的范圍由所附權(quán)利要求而不是上述說明限定,因此旨在將落在權(quán)利要求的等同要件的含義和范圍內(nèi)的所有變化囊括在本發(fā)明內(nèi)。此外,應(yīng)當(dāng)理解,雖然本說明書按照實(shí)施方式加以描述,但并非每個(gè)實(shí)施方式僅包含一個(gè)獨(dú)立的技術(shù)方案,說明書的這種敘述方式僅僅是為清楚起見,本領(lǐng)域技術(shù)人員應(yīng)當(dāng)將說明書作為一個(gè)整體,各實(shí)施例中的技術(shù)方案也可以經(jīng)適當(dāng)組合,形成本領(lǐng)域技術(shù)人員可以理解的其他實(shí)施方式。當(dāng)前第1頁12