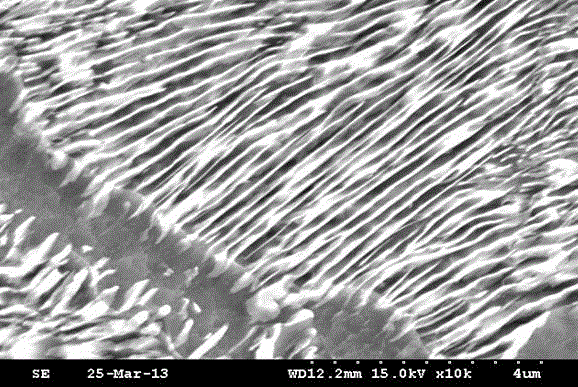
本發(fā)明涉及一種高強(qiáng)韌性轉(zhuǎn)向節(jié)用非調(diào)質(zhì)鋼的領(lǐng)域,具體涉及一種代替40Cr調(diào)質(zhì)鋼的轉(zhuǎn)向節(jié)用非調(diào)質(zhì)鋼及其生產(chǎn)方法。
背景技術(shù):
:轉(zhuǎn)向節(jié)(SteeringKnuckle)又稱(chēng)“羊角”,是汽車(chē)轉(zhuǎn)向橋中的重要零件之一,能夠使汽車(chē)穩(wěn)定行駛并靈敏傳遞行駛方向。它的功用是傳遞并承受汽車(chē)前部載荷,支承并帶動(dòng)前輪繞主銷(xiāo)轉(zhuǎn)動(dòng)而使汽車(chē)轉(zhuǎn)向。在汽車(chē)行駛狀態(tài)下,它承受著多變的沖擊載荷,因此,要求其具有很高的強(qiáng)度。轉(zhuǎn)向節(jié)是汽車(chē)車(chē)輪與車(chē)軸之間的關(guān)鍵連接件,它既要承受汽車(chē)在行駛中顛簸的彎曲應(yīng)力,轉(zhuǎn)向時(shí)的扭曲力,還要保證汽車(chē)在剎車(chē)時(shí)有足夠的沖擊韌性,同時(shí)還得具有良好的切削加工性,便于制造生產(chǎn)。因此要求生產(chǎn)轉(zhuǎn)向節(jié)的材料在機(jī)械性能、組織結(jié)構(gòu)和切削加工性等方面有較高的技術(shù)要求。球墨鑄鐵和調(diào)質(zhì)40Cr是目前我國(guó)汽車(chē)通用轉(zhuǎn)向節(jié)材料,然后伴隨汽車(chē)輕量化、發(fā)動(dòng)機(jī)小型化和高功率大馬力的渦輪增壓技術(shù)的發(fā)展,對(duì)轉(zhuǎn)向節(jié)的高強(qiáng)韌性、耐扭曲、抗彎曲應(yīng)力及尺寸截面性能的均勻性的要求越來(lái)越高,然而在機(jī)械加工過(guò)程中又對(duì)長(zhǎng)細(xì)、截面復(fù)雜的轉(zhuǎn)向節(jié)的車(chē)削加工和配合面的精度要求也更加苛刻。傳統(tǒng)轉(zhuǎn)向節(jié):球墨鑄鐵和調(diào)質(zhì)40Cr的缺點(diǎn):球墨鑄鐵轉(zhuǎn)向節(jié):鑄鐵件零件材質(zhì)疏松且抗拉強(qiáng)度和屈服強(qiáng)度低,易脆性斷裂,福特翼虎“羊角”斷軸事件就是因?yàn)椴捎们蚰T鐵轉(zhuǎn)向節(jié)制造,在行駛過(guò)程中顛簸的彎曲應(yīng)力,轉(zhuǎn)向時(shí)的高扭曲力承載不足而導(dǎo)致轉(zhuǎn)向節(jié)斷軸,因此球墨鑄鐵轉(zhuǎn)向節(jié)越來(lái)越不適應(yīng)今天汽車(chē)工業(yè)發(fā)展的需求。40Cr轉(zhuǎn)向節(jié):調(diào)質(zhì)鍛鋼轉(zhuǎn)向節(jié)抗拉強(qiáng)度和屈服強(qiáng)度相比球墨鑄鐵要大大提高,且抗沖擊載荷和疲勞強(qiáng)度也要高出二個(gè)檔次。使用40Cr制造的轉(zhuǎn)向節(jié)應(yīng)用于中低端工程機(jī)械、乘用車(chē)、商用車(chē)、皮卡車(chē)還是比較滿(mǎn)足使用要求的。但是調(diào)質(zhì)40Cr淬火開(kāi)裂、彎曲變形需矯直等缺點(diǎn)是與生俱來(lái)不可避免的,因此零件的加工精度和裝配精度得不到強(qiáng)有力的保證。調(diào)質(zhì)結(jié)構(gòu)鋼還有一個(gè)顯著的缺陷就是其機(jī)械性能是由調(diào)質(zhì)熱處理來(lái)保證,但是轉(zhuǎn)向節(jié)形狀復(fù)雜、厚薄不均導(dǎo)致調(diào)質(zhì)后的零件的截面性能不均勻,往往使其在服役過(guò)程中在薄弱環(huán)節(jié)部位發(fā)生失效。技術(shù)實(shí)現(xiàn)要素:本發(fā)明的目的在于:克服現(xiàn)有技術(shù)的不足,提供一種代替40Cr調(diào)質(zhì)鋼的轉(zhuǎn)向節(jié)用非調(diào)質(zhì)鋼及其生產(chǎn)方法,通過(guò)化學(xué)成分的優(yōu)化設(shè)計(jì)和控軋控冷工藝技術(shù)(軋制參數(shù))的完美結(jié)合,嚴(yán)格控制該配方的冶煉工藝及開(kāi)、終軋溫度及冷卻方式,實(shí)現(xiàn)易車(chē)削高強(qiáng)韌性轉(zhuǎn)向節(jié)用非調(diào)質(zhì)鋼的生產(chǎn);采用非調(diào)質(zhì)鋼生產(chǎn)工藝制造,可以有效的避開(kāi)調(diào)質(zhì)熱處理,從而省去了調(diào)質(zhì)后的矯直、應(yīng)力消除等工序,依靠微合金化技術(shù)以及控鍛(軋)控冷來(lái)確保零件組織性能,因此非調(diào)質(zhì)鋼轉(zhuǎn)向節(jié)具有經(jīng)濟(jì)、節(jié)能和環(huán)保等優(yōu)點(diǎn),能很好的克服傳統(tǒng)轉(zhuǎn)向節(jié)的缺點(diǎn),且降本增效,提高成材率和縮短加工周期;通過(guò)該方法生產(chǎn)出的工件的截面性能更均勻、整體承受載荷能力更強(qiáng)、優(yōu)良的切削加工性能和裝配精度越來(lái)越受到汽車(chē)配套企業(yè)的青睞;因此在中國(guó)工程機(jī)械及汽車(chē)市場(chǎng)的應(yīng)用前景是十分廣闊的;控制細(xì)小微合金化元素碳氮化物相的析出而強(qiáng)化鐵素體軟相;控制細(xì)小微合金化元素鈮、釩碳氮化物相的析出并強(qiáng)化鐵素體軟相;增加Si元素含量,使鐵素體相固溶強(qiáng)化,同時(shí)提高鋼材屈強(qiáng)比;鋼中高氮促進(jìn)VN粒子大量析出,VN能有效細(xì)化奧氏體晶粒,促進(jìn)晶內(nèi)鐵素體的析出,有效的分割粗大的珠光體團(tuán),提高非調(diào)質(zhì)鋼的沖擊韌性,并且鋼中增氮還能進(jìn)一步促進(jìn)鋼中碳氮化釩的析出,顯著發(fā)揮V的析出強(qiáng)化作用;為了進(jìn)一步改善切削加工性,還增加鋼中S元素含量;V-Nb-Ti微合金化技術(shù)的應(yīng)用,使其可以實(shí)現(xiàn)再結(jié)晶+未再結(jié)晶區(qū)進(jìn)行控軋控冷,顯著提高非調(diào)質(zhì)鋼的強(qiáng)韌性;通過(guò)各成分的合理配比,實(shí)現(xiàn)了鋼的物理指標(biāo)以及各性能指標(biāo)均達(dá)到并超過(guò)設(shè)計(jì)要求的前提下,盡可能降低了鋼的生產(chǎn)成本,提高了市場(chǎng)競(jìng)爭(zhēng)力。本發(fā)明所采取的技術(shù)方案是:代替40Cr調(diào)質(zhì)鋼的轉(zhuǎn)向節(jié)用非調(diào)質(zhì)鋼,其按照重量百分比(%)包括以下成分:C:0.35-0.42、Si:0.50-0.80、Mn:1.20-1.40、P:≤0.013、S:0.030-0.050、Cu:≤0.20、Cr:0.20-0.35、Mo:≤0.05、Al:0.010-0.035、V:0.12-0.20、Nb:≤0.035、Ti:0.007-0.020、N:0.014-0.02,其余原來(lái)Fe。本發(fā)明進(jìn)一步改進(jìn)方案是,所述代替40Cr調(diào)質(zhì)鋼的高強(qiáng)韌性轉(zhuǎn)向節(jié)用非調(diào)質(zhì)鋼,其成分還包括H和O,并且根據(jù)重量百分比,保證[H]≤2.5ppm、[O]≤20ppm。C:0.35%-0.42%C:決定鋼強(qiáng)度的重要元素。C與其它合金元素相比,成本廉價(jià),如果能夠大量添加C則能夠降低鋼材的合金成本,而且能夠與強(qiáng)碳化物形成元素V、Ti、Mo、等結(jié)合形成碳化物,這些碳化物起到沉淀強(qiáng)化和細(xì)晶強(qiáng)化作用,一方面有利于強(qiáng)度增加,另一方面能夠拖拽基體晶界而阻止再結(jié)晶,提高再結(jié)晶溫度;但是,如果添加大量的C,則會(huì)導(dǎo)致珠光體的片層化明顯,而珠光體的片層具有一定的方向性,會(huì)導(dǎo)致工件對(duì)于不同方向的抗拉抗壓能力差異較大,還會(huì)導(dǎo)致韌性下降,當(dāng)C含量高于0.40%,工件的(低溫)韌性降低,導(dǎo)致不適用于轉(zhuǎn)向節(jié);因此綜合考慮成本和工件的性能,從而將C的含量限定在0.35%-0.42%的范圍內(nèi)。Si:0.50%-0.80%Si:顯著強(qiáng)化鐵素體,具有較強(qiáng)的固溶強(qiáng)化效果,又可增加鐵素體的體積分?jǐn)?shù),有利于提高韌性,另外Si與其它合金元素相比,成本廉價(jià),如果能夠大量添加Si則能夠降低鋼材的合金成本;但Si含量過(guò)高,將降低鋼的抗疲勞強(qiáng)度和耐久度會(huì)降低,對(duì)于應(yīng)用于轉(zhuǎn)向節(jié)這種受力頻繁并且受力方向不同的工件而言,對(duì)于抗疲勞強(qiáng)度和耐久度的要求比普通的鋼要求更高;所以綜合考慮成本和工件的性能,從而將Si的含量限定在0.50%-0.80%。Mn:1.20%-1.40%Mn:是提高非調(diào)質(zhì)鋼強(qiáng)度,改善韌性的重要合金元素。Mn元素還可以提高VC和VN在奧氏體中的溶解度,有助于其在鐵素體中析出,一般Mn含量低于1.0%時(shí),其強(qiáng)韌化效果不明顯,增加Mn的含量,有利于珠光體團(tuán)變細(xì)小,并減小珠光體片層間距,還使珠光體中滲碳體片的厚度減??;但是當(dāng)Mn的含量過(guò)高的時(shí)候,尤其是大于等于2.0%的時(shí)候,將提高珠光體的體積分?jǐn)?shù),降低工件的韌性,這對(duì)于應(yīng)用于轉(zhuǎn)向節(jié)這種受力頻繁并且受力方向不同的工件而言是不利的;另外Mn具有與S結(jié)合形成硫化物、提高切削性的效果,但Mn與其它合金元素相比,成本相對(duì)而言較高;因此綜合考慮成本和工件的性能,從而將Mn的含量限定在1.20%-1.40%。P:≤0.013%P:能夠提高基體強(qiáng)度。P與其它合金元素相比,雖然成本廉價(jià),但P在鍛造時(shí)對(duì)變形有明顯的抑制作用;但是與Cu聯(lián)合使用,提高低合金高強(qiáng)度鋼的耐大氣腐蝕性能。所以綜合考慮到工件的性能,從而將P的含量限定在≤0.013%。S:0.030%-0.050%S:由于會(huì)降低工件的韌性,原本屬于鋼中雜質(zhì)元素,應(yīng)當(dāng)盡量減少,一般應(yīng)嚴(yán)格控制在≤0.03%-0.05%。但是S由于其切屑發(fā)脆而可得到非常光澤的表面,尤其是S與Mn結(jié)合成的硫化物具有顯著提高切削性能的效果,而且S與Mn結(jié)合成的硫化物呈晶粒狀分布在晶粒內(nèi),且在在鍛造的高溫環(huán)境中有一定的塑性,從而避免熱脆,有利于鋼的鍛造;另外,工件在切削時(shí)工件微觀上不同的組織成分形成了韌窩結(jié)構(gòu),對(duì)于切削作用力的承受能力也不同,由于S的作用,使工件的切削時(shí),切削刀具切削到S含量較多部位處,便會(huì)由于受力不均而使切削屑斷落,產(chǎn)生的切削屑呈較短的“C”形結(jié)構(gòu),這樣就避免切削屑纏繞在切削刀上而導(dǎo)致切削刀的磨損;另外S與其它合金元素相比,成本廉價(jià),如果能夠大量添加S則能夠降低鋼材的合金成本。因此綜合考慮到工件的性能和成本,從而將S的含量限定在0.030%-0.050%。Cu:≤0.20%Cu:可以改善工件的耐蝕能力,Cu可以借助沉淀硬化來(lái)提高工件的抗拉強(qiáng)度,而在那些不發(fā)生沉淀硬化的鋼中Cu能夠提高屈服強(qiáng)度;但是當(dāng)Cu>0.2%時(shí),就會(huì)產(chǎn)生“銅脆”——當(dāng)Cu>0.2%時(shí),加熱過(guò)程由于表面發(fā)生選擇性氧化,使Fe先Cu而發(fā)生氧化,而表層Cu含量即相對(duì)增加形成一層薄膜,然后向擴(kuò)散形成含Cu網(wǎng)絡(luò),在1030℃即容易鍛裂;另外,Cu與其它合金元素相比,成本相對(duì)而言較高;因此綜合考慮成本和工件的性能,從而將Cu的含量限定在≤0.20%。Cr:0.20%-0.35%Cr:是有助于珠光體形成的重要元素,可以提高工件的強(qiáng)度以及韌性。Cr會(huì)形成安定而硬的碳化物,而且具抗蝕性、高硬度、高強(qiáng)度、屈服點(diǎn)、高耐磨性,同時(shí)對(duì)塑性、韌性影響又不大;另外,通過(guò)添加V、Nb與Cr反應(yīng)可得極細(xì)彌散相,對(duì)抗蠕強(qiáng)(耐熱性)改善極為有利。當(dāng)Cr的含量小于0.20%時(shí),得到上述效果相對(duì)較不明顯,甚至得不到上述效果,但是由于我國(guó)的Cr資源十分緊缺,應(yīng)盡量少用Cr;所以綜合考慮成本和工件的性能,從而將Cr的含量限定在0.20%-0.35%。Mo:≤0.05%Mo:細(xì)化晶粒的作用比W更強(qiáng),所以可降低鋼的過(guò)熱傾向性,提高強(qiáng)度、硬度、熱穩(wěn)定性;Mo在鋼中會(huì)使鍛件的抗拉強(qiáng)度、屈服強(qiáng)度、硬度有效提升;Mo與Cr結(jié)合可大大提高淬透性,可細(xì)化晶粒,提高韌性,使鍛造加工容易;同時(shí),Mo還可以提高鋼的沖擊韌性,非常適合于受力復(fù)雜、頻繁受到?jīng)_擊的轉(zhuǎn)向節(jié);而且Mo可以提高珠光體的熱強(qiáng)性。但是,Mo是鐵素體形成元素,所以為了得到奧氏體,應(yīng)相應(yīng)多加Mn等奧氏體形成元素,否則當(dāng)Mo含量較多時(shí)就易出現(xiàn)鐵素體δ相或其它脆性相而使韌性降低。另外,Mo與其它合金元素相比,成本非常昂貴。因此綜合考慮成本和工件的性能,從而將Mo的含量限定在≤0.05%。Al:0.010%-0.035%Al:當(dāng)鋼中其含量小于3~5%時(shí),可以提高鋼的抗氧化性。作為強(qiáng)烈脫氧劑加進(jìn)的Al,可生成高度細(xì)碎的、超顯微的氧化物,分散于鋼體積中;作為強(qiáng)烈脫氧劑加進(jìn)的Al,可生成高度細(xì)碎的、超顯微的氧化物,分散于鋼體積中;在改善鋼的抗氧化性的時(shí)候,鋁作為終脫氧劑,Al的含量一般限定在0.01%-0.03%,由于Al與其它合金元素相比,成本廉價(jià),而且還會(huì)與Cr反應(yīng),所以綜合考慮成本和工件的性能,從而將Al的含量限定在0.010%-0.035%。V:0.12%-0.20%V:能細(xì)化鋼的晶粒組織,提高鋼的強(qiáng)度,韌性和耐磨性,V還是鋼的優(yōu)良脫氧劑。V與O、N都有很大的親和力,亦是強(qiáng)碳化物元素。一般VC的彌散度很高,且極穩(wěn)定。所以它既利脫氧、脫氣得到致密細(xì)晶組織,提高塑性、韌性及高強(qiáng)度,其沖擊性能和疲勞強(qiáng)度都較無(wú)V鋼高,在高溫及低溫(<0℃)均有高強(qiáng)度、韌性。由于VC的高度分散阻止焊縫晶粒粗大,所以可改善鋼的可焊性能。但是當(dāng)V>0.3%時(shí),將使回火脆性凸突顯;并且V與其它合金元素相比,成本昂貴,因此綜合考慮成本和工件的性能,從而將V的含量限定在0.12%-0.20%。Nb:≤0.035%Nb:能細(xì)化晶粒和降低鋼的過(guò)熱敏感性及回火脆性,提高強(qiáng)度;并且Nb的固溶強(qiáng)化作用很明顯,提高鋼的淬透性(溶于奧氏體時(shí)),增加回火穩(wěn)定性,有二次硬化作用,提高鋼的強(qiáng)度、沖擊韌性。但是,鋼的硬度將隨著Nb含量的增加而降低,同時(shí)Nb雖可細(xì)化晶粒而提高鋼的韌性,但含量過(guò)高時(shí),亦將生成鐵素體δ相或其它脆性相,而使其韌性降低,熱加工性能變壞。另外,Nb的作用與V相近,并且相比于V而言,Nb與V相近作用的效果遠(yuǎn)優(yōu)于V,但是Nb與其它合金元素相比,成本昂貴,相比于V的價(jià)格高出很多,所以綜合考慮成本和工件的性能,從而將Nb的含量限定在≤0.035%。Ti:0.007%-0.020%Ti:能細(xì)化鋼的晶粒組織,從而提高鋼的強(qiáng)度和韌性,鈦是鋼中強(qiáng)脫氧劑。它能使鋼的內(nèi)部組織致密,細(xì)化晶粒力;降低時(shí)效敏感性和冷脆性;鈦在鋼中易與碳形成碳化物TiC,TiC可以降低鋼的過(guò)熱傾向性;Ti是強(qiáng)烈的鐵素體形成元素,Ti能與S作用,降低硫的熱脆作用;但是,含Ti鋼,特別是低碳之Ti鋼,往往因其鋼液粘度較大,而使其中非金屬加雜,不易分離浮出;鋼是硬度隨Ti含量的增加而降低;Ti與N、O有很大的親和力而極易成形TiN和TiO2,鋼在較低溫度時(shí),就形成了較多的非金屬夾雜和皮下多孔等缺陷;與V一樣,Ti含量達(dá)到0.05%的時(shí)就將使鋼的矯頑力降低。而且,Ti與其它合金元素相比,成本昂貴。因此,綜合考慮成本和工件的性能,從而將Ti的含量限定在0.007%-0.020%。N:0.014%-0.02%N:N能提高鋼的強(qiáng)度,低溫韌性和焊接性,增加時(shí)效敏感性。N亦是強(qiáng)烈的奧氏體形成元素,在這點(diǎn)上它與Ni相似,穩(wěn)定奧氏體效果更好,比Ni作用強(qiáng)27倍,所以N有可能是代替Ni的重要元素之一;N還可在復(fù)雜的奧氏體鋼中借氮化物的析出而產(chǎn)生彌散硬化;N能提高高鉻鋼,特別是含V的的高鉻鋼的熱硬性。但是,它與合金元素生成氮化物是非金屬夾雜,更重要的是降低了合金元素的作用。鋼中氮含量高時(shí),在250℃-450℃溫度范圍,其表面發(fā)藍(lán),鋼的強(qiáng)度升高,沖擊韌性降低,稱(chēng)之為“藍(lán)脆”;含N鋼在退火過(guò)程中因氮化物析出而會(huì)顯著降低它的塑性。鋼中加入適量的鋁,可生成穩(wěn)定的AlN,能夠壓抑Fe4N生成和析出,不僅改善鋼的時(shí)效性,還可以阻止奧氏體晶粒的長(zhǎng)大。氮可以作為合金元素起到細(xì)化晶粒的作用。在冶煉鉻鋼,鎳鉻系鋼或鉻錳系等高合金鋼時(shí),加入適量的氮,能夠改善塑性和高溫加工性能;在一定含量的Cr、N鋼中,必有一與其相適應(yīng)的最小Mn含量,如低于這一Mn含量,鋼在凝固時(shí)N就會(huì)逸出,而成氣孔。另外,鐵素體溶解氮的能力很低,在高壓高溫下將空氣中的N2加入鐵水,難度非常大、并且有一定的危險(xiǎn)性。當(dāng)鋼中溶有過(guò)飽和的N,在放置較長(zhǎng)一段時(shí)間后或隨后在200℃-300℃加熱就會(huì)發(fā)生N以氮化物形式的析出,并使鋼的硬度、強(qiáng)度提高,塑性下降。鋼液中加入Al、Ti或V進(jìn)行固N(yùn)處理,使N固定在AlN、TiN或VN中。所以,綜合考慮成本和工件的性能,從而將N的含量限定在0.014%-0.02%。生產(chǎn)一種上述的代替40Cr調(diào)質(zhì)鋼的轉(zhuǎn)向節(jié)用非調(diào)質(zhì)鋼的方法,包括以下步驟:鐵水脫硫→LD→LF→RH→連鑄→切割→冷卻→檢驗(yàn)→判定→加熱爐加熱→控軋→冷卻→超聲+漏磁探傷→判定→包裝→稱(chēng)重→入庫(kù)。本發(fā)明進(jìn)一步改進(jìn)方案是,鐵水脫硫→LD→LF→RH→連鑄→切割→冷卻→檢驗(yàn)→判定→加熱爐加熱→控軋→冷卻→超聲+漏磁探傷→精整→判定→包裝→稱(chēng)重→入庫(kù)。本發(fā)明更進(jìn)一步改進(jìn)方案是,經(jīng)過(guò)LD的高純凈度鋼精煉時(shí),LF冶煉時(shí)將Mn范圍控制在1.10%-1.35%,RH吊包時(shí)將S線(xiàn)一次性性補(bǔ)喂到目標(biāo)值,RH破空后定氫:[H]≤2.5ppm,然后取樣測(cè)溫,根據(jù)氧氮儀分析結(jié)果進(jìn)行N-Mn線(xiàn)的補(bǔ)喂,冶煉過(guò)程中不允許補(bǔ)喂Al線(xiàn),LF冶煉結(jié)束后根據(jù)光譜成分中Al含量來(lái)確定加入硅鈣線(xiàn)的含量,在RH真空過(guò)程中對(duì)Al2O3充分進(jìn)行變性處理;所述目標(biāo)值是指正常40Cr鋼生產(chǎn)工藝中RH吊包時(shí)S線(xiàn)補(bǔ)喂的目標(biāo)值。本發(fā)明更進(jìn)一步改進(jìn)方案是,破空后立即喂入鈦線(xiàn)、氮化錳包心線(xiàn)、硫線(xiàn)調(diào)整Ti、N、S的含量。本發(fā)明更進(jìn)一步改進(jìn)方案是,軟吹氬15分鐘以上待成分均勻后吊包。本發(fā)明更進(jìn)一步改進(jìn)方案是,鋼料軋制前加熱的爐溫如表1所示:表1各段爐溫控制本發(fā)明更進(jìn)一步改進(jìn)方案是,控軋時(shí)候的開(kāi)軋溫度:≤1000℃、終軋溫度:≤900℃、鋼材冷卻;軋制時(shí),工件表面溫度的溫差≤30℃。本發(fā)明更進(jìn)一步改進(jìn)方案是,所述開(kāi)軋溫度在930℃-980℃的范圍內(nèi)。本發(fā)明更進(jìn)一步改進(jìn)方案是,在終軋的時(shí)候,如果溫度高于900℃,可以在執(zhí)行終軋的軋機(jī)處等待工件溫度≤900℃之后再進(jìn)行軋制。本發(fā)明更進(jìn)一步改進(jìn)方案是,成品鋼快速下冷床后進(jìn)坑冷卻,軋鋼廠加強(qiáng)入坑平直擺放控制,防止壓彎。本發(fā)明更進(jìn)一步改進(jìn)方案是,成品鋼快速下冷床后進(jìn)坑緩冷,入坑溫度在300℃-400℃的范圍內(nèi),出坑溫度≤200℃。本發(fā)明更進(jìn)一步改進(jìn)方案是,控軋為正公差軋制,軋制后的工件有粗磨余量。本發(fā)明更進(jìn)一步改進(jìn)方案是,所述工件完成軋制并冷卻后,先進(jìn)行粗磨然后再對(duì)工件進(jìn)行超聲和漏磁探傷。本發(fā)明更進(jìn)一步改進(jìn)方案是,工件經(jīng)過(guò)渦流/漏磁、超聲波探傷之后的精整步驟為:通過(guò)檢查短尺、單倍尺及定尺。本發(fā)明的有益效果在于:第一、本發(fā)明的代替40Cr調(diào)質(zhì)鋼的轉(zhuǎn)向節(jié)用非調(diào)質(zhì)鋼及其生產(chǎn)方法,通過(guò)化學(xué)成分的優(yōu)化設(shè)計(jì)和控軋控冷工藝技術(shù)(軋制參數(shù))的完美結(jié)合,嚴(yán)格控制該配方的冶煉工藝及開(kāi)、終軋溫度及冷卻方式,實(shí)現(xiàn)易車(chē)削高強(qiáng)韌性轉(zhuǎn)向節(jié)用非調(diào)質(zhì)鋼的生產(chǎn)。第二、本發(fā)明的代替40Cr調(diào)質(zhì)鋼的轉(zhuǎn)向節(jié)用非調(diào)質(zhì)鋼及其生產(chǎn)方法,采用非調(diào)質(zhì)鋼生產(chǎn)工藝制造,可以有效的避開(kāi)調(diào)質(zhì)熱處理,從而省去了調(diào)質(zhì)后的矯直、應(yīng)力消除等工序,依靠微合金化技術(shù)以及控鍛(軋)控冷來(lái)確保零件組織性能,因此非調(diào)質(zhì)鋼轉(zhuǎn)向節(jié)具有經(jīng)濟(jì)、節(jié)能和環(huán)保等優(yōu)點(diǎn),能很好的克服傳統(tǒng)轉(zhuǎn)向節(jié)的缺點(diǎn),且降本增效,提高成材率和縮短加工周期。第三、本發(fā)明的代替40Cr調(diào)質(zhì)鋼的轉(zhuǎn)向節(jié)用非調(diào)質(zhì)鋼及其生產(chǎn)方法,通過(guò)該方法生產(chǎn)出的工件的截面性能更均勻、整體承受載荷能力更強(qiáng)、優(yōu)良的切削加工性能和裝配精度越來(lái)越受到汽車(chē)配套企業(yè)的青睞;因此在中國(guó)工程機(jī)械及汽車(chē)市場(chǎng)的應(yīng)用前景是十分廣闊的。第四、本發(fā)明的代替40Cr調(diào)質(zhì)鋼的轉(zhuǎn)向節(jié)用非調(diào)質(zhì)鋼及其生產(chǎn)方法,控制細(xì)小微合金化元素碳氮化物相的析出而強(qiáng)化鐵素體軟相。第五、本發(fā)明的代替40Cr調(diào)質(zhì)鋼的轉(zhuǎn)向節(jié)用非調(diào)質(zhì)鋼及其生產(chǎn)方法,控制細(xì)小微合金化元素鈮、釩碳氮化物相的析出并強(qiáng)化鐵素體軟相。第六、本發(fā)明的代替40Cr調(diào)質(zhì)鋼的轉(zhuǎn)向節(jié)用非調(diào)質(zhì)鋼及其生產(chǎn)方法,增加Si元素含量,使鐵素體相固溶強(qiáng)化,同時(shí)提高鋼材屈強(qiáng)比。第七、本發(fā)明的代替40Cr調(diào)質(zhì)鋼的轉(zhuǎn)向節(jié)用非調(diào)質(zhì)鋼及其生產(chǎn)方法,鋼中高氮促進(jìn)VN粒子大量析出,VN能有效細(xì)化奧氏體晶粒,促進(jìn)晶內(nèi)鐵素體的析出,有效的分割粗大的珠光體團(tuán),提高非調(diào)質(zhì)鋼的沖擊韌性,并且鋼中增氮還能進(jìn)一步促進(jìn)鋼中碳氮化釩的析出,顯著發(fā)揮V的析出強(qiáng)化作用。第八、本發(fā)明的代替40Cr調(diào)質(zhì)鋼的轉(zhuǎn)向節(jié)用非調(diào)質(zhì)鋼及其生產(chǎn)方法,為了進(jìn)一步改善切削加工性,還增加鋼中S元素含量。第九、本發(fā)明的代替40Cr調(diào)質(zhì)鋼的轉(zhuǎn)向節(jié)用非調(diào)質(zhì)鋼及其生產(chǎn)方法,V-Nb-Ti微合金化技術(shù)的應(yīng)用,使其可以實(shí)現(xiàn)再結(jié)晶+未再結(jié)晶區(qū)進(jìn)行控軋控冷,顯著提高非調(diào)質(zhì)鋼的強(qiáng)韌性。第十、本發(fā)明的代替40Cr調(diào)質(zhì)鋼的轉(zhuǎn)向節(jié)用非調(diào)質(zhì)鋼及其生產(chǎn)方法,通過(guò)各成分的合理配比,實(shí)現(xiàn)了鋼的物理指標(biāo)以及各性能指標(biāo)均達(dá)到并超過(guò)設(shè)計(jì)要求的前提下,盡可能降低了鋼的生產(chǎn)成本,提高了市場(chǎng)競(jìng)爭(zhēng)力。附圖說(shuō)明圖1為本發(fā)明的金相結(jié)構(gòu)放大圖。圖2為本發(fā)明的珠光體結(jié)構(gòu)放大圖。圖3為本發(fā)明的沖擊斷口結(jié)構(gòu)放大圖。圖4為本發(fā)明的流線(xiàn)圖。圖5為本發(fā)明進(jìn)行切削加工后的切削屑圖。圖6為40Cr鋼調(diào)質(zhì)處理后工件進(jìn)行切削加工后的切削屑圖。具體實(shí)施方式實(shí)施例1代替40Cr調(diào)質(zhì)鋼的轉(zhuǎn)向節(jié)用非調(diào)質(zhì)鋼,其按照重量百分比(%)包括以下成分:C:0.38、Si:0.60、Mn:1.25、P:0.010、S:0.040、Cu:≤0.20、Cr:0.25、Mo:0.02、Al:0.010、V:0.15、Nb:0.015、Ti:0.010、N:0.017,另外,[H]為1.2ppm、[O]為9ppm,其余原來(lái)Fe。生產(chǎn)一種上述的代替40Cr調(diào)質(zhì)鋼的轉(zhuǎn)向節(jié)用非調(diào)質(zhì)鋼的方法,包括以下步驟:鐵水脫硫→LD→LF→RH→連鑄→切割→冷卻→檢驗(yàn)→判定→加熱爐加熱→控軋→冷卻→超聲+漏磁探傷→判定→包裝→稱(chēng)重→入庫(kù)。經(jīng)過(guò)LD的高純凈度鋼精煉時(shí),LF冶煉時(shí)Mn的含量以1.25%為目標(biāo),并且控制在1.20%-1.30%的范圍內(nèi),RH吊包時(shí)將S線(xiàn)一次性性補(bǔ)喂到目標(biāo)值,RH破空后定氫:[H]的含量以1.2ppm為目標(biāo),并且控制在≤2.5ppm的范圍內(nèi),然后取樣測(cè)溫,根據(jù)氧氮儀分析結(jié)果進(jìn)行N-Mn線(xiàn)的補(bǔ)喂,冶煉過(guò)程中不允許補(bǔ)喂Al線(xiàn),LF冶煉結(jié)束后根據(jù)光譜成分中Al含量來(lái)確定加入硅鈣線(xiàn)的含量,在RH真空過(guò)程中對(duì)Al2O3充分進(jìn)行變性處理;所述目標(biāo)值是指正常40Cr鋼生產(chǎn)工藝中RH吊包時(shí)S線(xiàn)補(bǔ)喂的目標(biāo)值。破空后立即喂入鈦線(xiàn)、氮化錳包心線(xiàn)、硫線(xiàn)調(diào)整Ti、N、S的含量;其中Ti的含量以0.010%為目標(biāo),并且控制在0.007%-0.015%的范圍內(nèi),其中N的含量以0.017%為目標(biāo),并且控制在0.015%-0.018%的范圍內(nèi),其中S的含量以0.040%為目標(biāo),并且控制在0.030%-0.050%的范圍內(nèi)。軟吹氬至成分均勻后吊包,并且控制吹氬流速,保證吹氬時(shí)間大于等于15分鐘。鋼料軋制前加熱的爐溫如下:第一加熱段爐溫:下加熱溫度為≤790℃、上加熱溫度為≤750℃,第二加熱段爐溫:下加熱溫度為810℃-890℃、上加熱溫度為790℃-870℃,均熱段爐溫:下加熱溫度為1010℃-1070℃、上加熱溫度為920℃-980℃,總加熱時(shí)間為2h-3h。控軋時(shí)候的開(kāi)軋溫度為950℃、終軋溫度為900℃、鋼材冷卻;軋制時(shí),工件表面溫度的溫差為≤30℃。在終軋的時(shí)候,如果溫度高于900℃,可以在執(zhí)行終軋的軋機(jī)處等待工件溫度為900℃之后再進(jìn)行軋制。成品鋼快速下冷床后進(jìn)坑緩冷,入坑溫度為380℃,出坑溫度為≤200℃軋鋼廠加強(qiáng)入坑平直擺放控制,防止壓彎。控軋為正公差軋制,軋制后的工件有粗磨余量。所述工件完成軋制并冷卻后,先進(jìn)行粗磨然后再對(duì)工件進(jìn)行超聲和漏磁探傷。工件經(jīng)過(guò)渦流/漏磁、超聲波探傷之后的精整步驟為:通過(guò)檢查短尺、單倍尺及定尺。實(shí)施例2代替40Cr調(diào)質(zhì)鋼的轉(zhuǎn)向節(jié)用非調(diào)質(zhì)鋼,其按照重量百分比(%)包括以下成分:C:0.39、Si:0.62、Mn:1.23、P:0.008、S:0.045、Cu:≤0.20、Cr:0.24、Mo:0.01、Al:0.012、V:0.14、Nb:0.016、Ti:0.012、N:0.016,另外,[H]為1.0ppm、[O]為10ppm,其余原來(lái)Fe。生產(chǎn)上述的代替40Cr調(diào)質(zhì)鋼的轉(zhuǎn)向節(jié)用非調(diào)質(zhì)鋼的方法,包括以下步驟:鐵水脫硫→LD→LF→RH→連鑄→切割→冷卻→檢驗(yàn)→判定→加熱爐加熱→控軋→冷卻→超聲+漏磁探傷→判定→包裝→稱(chēng)重→入庫(kù)。經(jīng)過(guò)LD的高純凈度鋼精煉時(shí),LF冶煉時(shí)Mn的含量以1.23%為目標(biāo),并且控制在1.20%-1.30%的范圍內(nèi),RH吊包時(shí)將S線(xiàn)一次性性補(bǔ)喂到目標(biāo)值,RH破空后定氫:[H]的含量以1.0ppm為目標(biāo),并且控制在≤2.5ppm的范圍內(nèi),然后取樣測(cè)溫,根據(jù)氧氮儀分析結(jié)果進(jìn)行N-Mn線(xiàn)的補(bǔ)喂,冶煉過(guò)程中不允許補(bǔ)喂Al線(xiàn),LF冶煉結(jié)束后根據(jù)光譜成分中Al含量來(lái)確定加入硅鈣線(xiàn)的含量,在RH真空過(guò)程中對(duì)Al2O3充分進(jìn)行變性處理;所述目標(biāo)值是指正常40Cr鋼生產(chǎn)工藝中RH吊包時(shí)S線(xiàn)補(bǔ)喂的目標(biāo)值。破空后立即喂入鈦線(xiàn)、氮化錳包心線(xiàn)、硫線(xiàn)調(diào)整Ti、N、S的含量;其中Ti的含量以0.012%為目標(biāo),并且控制在0.007%-0.015%的范圍內(nèi),其中N的含量以0.016%為目標(biāo),并且控制在0.015%-0.018%的范圍內(nèi),其中S的含量以0.045%為目標(biāo),并且控制在0.030%-0.050%的范圍內(nèi)。軟吹氬至成分均勻后吊包,并且控制吹氬流速,保證吹氬時(shí)間大于等于15分鐘。鋼料軋制前加熱的爐溫如下:第一加熱段爐溫:下加熱溫度為≤790℃、上加熱溫度為≤750℃,第二加熱段爐溫:下加熱溫度為810℃-890℃、上加熱溫度為790℃-870℃,均熱段爐溫:下加熱溫度為1010℃-1070℃、上加熱溫度為920℃-980℃,總加熱時(shí)間為2h-3h??剀垥r(shí)候的開(kāi)軋溫度為960℃、終軋溫度為890℃、鋼材冷卻;軋制時(shí),工件表面溫度的溫差為≤30℃。在終軋的時(shí)候,如果溫度高于900℃,可以在執(zhí)行終軋的軋機(jī)處等待工件溫度為890℃之后再進(jìn)行軋制。成品鋼快速下冷床后進(jìn)坑緩冷,入坑溫度為360℃,出坑溫度為≤200℃軋鋼廠加強(qiáng)入坑平直擺放控制,防止壓彎。控軋為正公差軋制,軋制后的工件有粗磨余量。所述工件完成軋制并冷卻后,先進(jìn)行粗磨然后再對(duì)工件進(jìn)行超聲和漏磁探傷。工件經(jīng)過(guò)渦流/漏磁、超聲波探傷之后的精整步驟為:通過(guò)檢查短尺、單倍尺及定尺。實(shí)施例3代替40Cr調(diào)質(zhì)鋼的轉(zhuǎn)向節(jié)用非調(diào)質(zhì)鋼,其按照重量百分比(%)包括以下成分:C:0.37、Si:0.65、Mn:1.26、P:0.009、S:0.042、Cu:≤0.20、Cr:0.27、Mo:0.02、Al:0.008、V:0.17、Nb:0.017、Ti:0.008、N:0.016,另外,[H]為1.5ppm、[O]為11ppm,其余原來(lái)Fe。生產(chǎn)上述的代替40Cr調(diào)質(zhì)鋼的轉(zhuǎn)向節(jié)用非調(diào)質(zhì)鋼的方法,包括以下步驟:鐵水脫硫→LD→LF→RH→連鑄→切割→冷卻→檢驗(yàn)→判定→加熱爐加熱→控軋→冷卻→超聲+漏磁探傷→判定→包裝→稱(chēng)重→入庫(kù)。經(jīng)過(guò)LD的高純凈度鋼精煉時(shí),LF冶煉時(shí)Mn的含量以1.26%為目標(biāo),并且控制在1.20%-1.30%的范圍內(nèi),RH吊包時(shí)將S線(xiàn)一次性性補(bǔ)喂到目標(biāo)值,RH破空后定氫:[H]的含量以1.5ppm為目標(biāo),并且控制在≤2.5ppm的范圍內(nèi),然后取樣測(cè)溫,根據(jù)氧氮儀分析結(jié)果進(jìn)行N-Mn線(xiàn)的補(bǔ)喂,冶煉過(guò)程中不允許補(bǔ)喂Al線(xiàn),LF冶煉結(jié)束后根據(jù)光譜成分中Al含量來(lái)確定加入硅鈣線(xiàn)的含量,在RH真空過(guò)程中對(duì)Al2O3充分進(jìn)行變性處理;所述目標(biāo)值是指正常40Cr鋼生產(chǎn)工藝中RH吊包時(shí)S線(xiàn)補(bǔ)喂的目標(biāo)值。破空后立即喂入鈦線(xiàn)、氮化錳包心線(xiàn)、硫線(xiàn)調(diào)整Ti、N、S的含量;其中Ti的含量以0.008%為目標(biāo),并且控制在0.007%-0.015%的范圍內(nèi),其中N的含量以0.016%為目標(biāo),并且控制在0.015%-0.018%的范圍內(nèi),其中S的含量以0.042%為目標(biāo),并且控制在0.030%-0.050%的范圍內(nèi)。軟吹氬至成分均勻后吊包,并且控制吹氬流速,保證吹氬時(shí)間大于等于15分鐘。鋼料軋制前加熱的爐溫如下:第一加熱段爐溫:下加熱溫度為≤790℃、上加熱溫度為≤750℃,第二加熱段爐溫:下加熱溫度為810℃-890℃、上加熱溫度為790℃-870℃,均熱段爐溫:下加熱溫度為1010℃-1070℃、上加熱溫度為920℃-980℃,總加熱時(shí)間為2h-3h。控軋時(shí)候的開(kāi)軋溫度為940℃、終軋溫度為880℃、鋼材冷卻;軋制時(shí),工件表面溫度的溫差為≤30℃。在終軋的時(shí)候,如果溫度高于900℃,可以在執(zhí)行終軋的軋機(jī)處等待工件溫度為880℃之后再進(jìn)行軋制。成品鋼快速下冷床后進(jìn)坑緩冷,入坑溫度為350℃,出坑溫度為≤200℃軋鋼廠加強(qiáng)入坑平直擺放控制,防止壓彎??剀垶檎钴堉?,軋制后的工件有粗磨余量。所述工件完成軋制并冷卻后,先進(jìn)行粗磨然后再對(duì)工件進(jìn)行超聲和漏磁探傷。工件經(jīng)過(guò)渦流/漏磁、超聲波探傷之后的精整步驟為:通過(guò)檢查短尺、單倍尺及定尺。根據(jù)實(shí)施例1、實(shí)施例2和實(shí)施例3的組分和工藝生產(chǎn)鍛造成的轉(zhuǎn)向節(jié)零件的機(jī)械性能如表2所示:表2各實(shí)施例轉(zhuǎn)向節(jié)的機(jī)械性能轉(zhuǎn)向節(jié)性能Rm/MPaRp0.2/MPaZ(%)A(%)AKU2/JHB標(biāo)準(zhǔn)值要求≥850≥580≥20≥10≥35250~298實(shí)施例1921628441255280實(shí)施例2911637551553278實(shí)施例3908623521758273由表2可知,用實(shí)施例1、實(shí)施例2和實(shí)施例3的組分配比的鋼各自通過(guò)實(shí)施例1、實(shí)施例2和實(shí)施例3的生產(chǎn)方法所生產(chǎn)制造出的工件,其各項(xiàng)性能都能超出客戶(hù)的要求,并且遠(yuǎn)超國(guó)家標(biāo)準(zhǔn);而且其成本控制合理,提高了產(chǎn)品的性?xún)r(jià)比和市場(chǎng)競(jìng)爭(zhēng)力。結(jié)合圖1和圖2可知,所開(kāi)發(fā)非調(diào)質(zhì)鋼的組織為珠光體+沿晶界分布的網(wǎng)狀鐵素體,珠光體片層間距(約0.2um)鐵素體晶粒度級(jí)別為14級(jí),并且非調(diào)質(zhì)鋼的珠光體形成如圖2中左下角所示的短片無(wú)序結(jié)構(gòu),這些短片無(wú)序結(jié)構(gòu)使得工件對(duì)于個(gè)方向的沖擊性能都能得到保證。結(jié)合圖3和圖4可知,沖擊斷口形貌可為解理斷裂特征以及少量韌窩。轉(zhuǎn)向節(jié)橫截面鍛后流線(xiàn)均勻,通過(guò)韌窩的作用進(jìn)一步保證了工件對(duì)于復(fù)雜受力情況的承受能力。結(jié)合圖5和圖6可知,本發(fā)明的鋼所生產(chǎn)的工件的切削屑呈現(xiàn)C狀,相較調(diào)質(zhì)處理的40Cr鋼所生產(chǎn)的工件的連續(xù)卷曲的切削屑而言不纏刀,在切削的時(shí)候,切削屑不會(huì)對(duì)刀具產(chǎn)生額外的磨損,從而延長(zhǎng)了刀具的使用壽命。疲勞耐久指標(biāo)是轉(zhuǎn)向節(jié)使用過(guò)程中的重要性能指標(biāo)之一。在長(zhǎng)城汽車(chē)技術(shù)中心采用型號(hào)為L(zhǎng)FH-50的動(dòng)態(tài)伺服試驗(yàn)系統(tǒng)ACT2對(duì)本發(fā)明的非調(diào)質(zhì)鋼轉(zhuǎn)向節(jié)進(jìn)行了疲勞耐久試驗(yàn)。按規(guī)定載荷和頻率對(duì)試樣加載100萬(wàn)次。實(shí)驗(yàn)結(jié)束后,進(jìn)行內(nèi)部缺陷探傷。結(jié)果表明,本發(fā)明的非調(diào)質(zhì)鋼轉(zhuǎn)向節(jié)100萬(wàn)次循環(huán)后試樣無(wú)疲勞損傷,其耐久性可滿(mǎn)足設(shè)計(jì)及使用要求。另外,隨著該種鋼所生產(chǎn)坯料直徑的增加,可以通過(guò)提高加熱爐各段爐溫的溫度、延長(zhǎng)加熱時(shí)間或提高軋制的溫度等方法來(lái)實(shí)現(xiàn)較大直徑坯料的軋制。當(dāng)前第1頁(yè)1 2 3