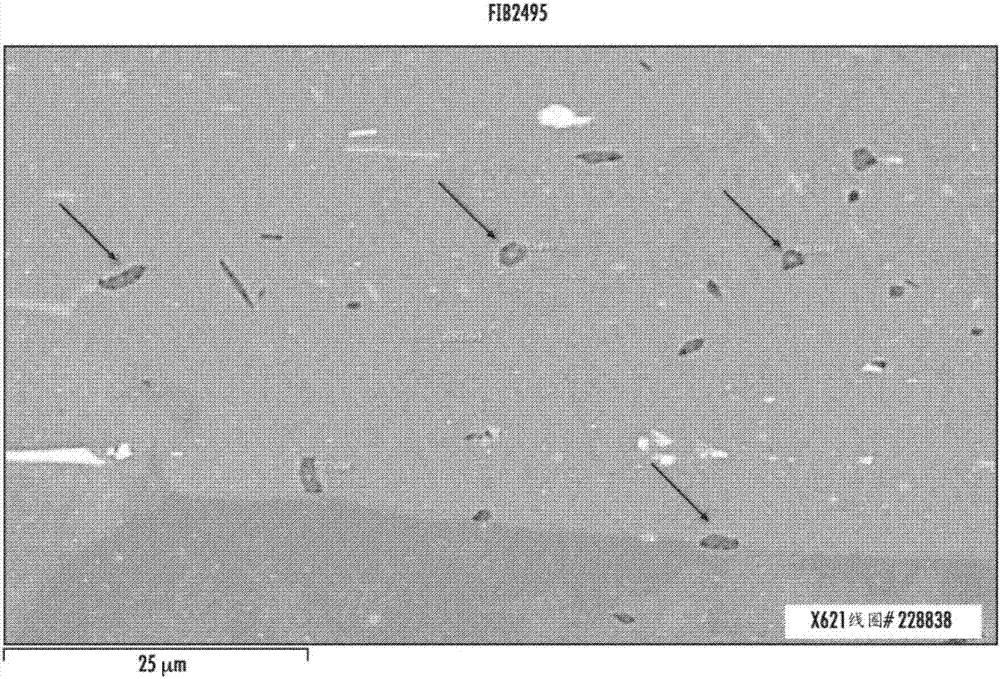
相關申請的交叉引用本申請要求2015年1月12日提交的第62/102,124號美國臨時申請的權益,所述美國臨時申請以全文引用的方式并入本文。本發(fā)明涉及材料科學、材料化學、冶金學、鋁合金、鋁制造、運輸行業(yè)、機動車輛行業(yè)、汽車行業(yè)、機動車輛制造的領域以及相關領域。本發(fā)明涉及條痕減少或無條痕的高度可成形的汽車鋁片材產品。本發(fā)明還涉及生產所述鋁片材產品的方法。特定來說,這些產品適用于汽車行業(yè)中。
背景技術:
:為了減少汽車的重量,汽車行業(yè)已經越來越多地用鋁合金面板代替鋼面板。較輕重量的面板幫助減少汽車重量,這減少了燃料消耗。然而,鋁合金面板的引入產生了其自己的多種需要。為了在汽車應用中有用,鋁合金片材產品必須擁有在常見的t4回火狀態(tài)條件中的良好成形特性,使得其可以按需要彎曲或塑形而不會開裂、撕裂或起皺。同時,合金面板在涂漆和烘烤之后必須具有足夠強度來抵抗凹痕且承受其它影響。除了上文論述的要求之外,另一要求是用于汽車組件的鋁合金不具有令人反感的和/或有害的表面缺陷,稱為隆脊、條痕或油漆刷線,所述表面缺陷出現于沖壓或成形的鋁片材組件的表面上。隆脊或條痕線僅在足夠橫向應變的施加后出現于輥軋方向上,例如在典型沖壓或成形操作中發(fā)生的情況。此條痕缺陷充分嚴重而使得在涂漆之后其在汽車組件中仍然可見。因此,這些鋁合金的成品表面外觀是令人反感的且不適合于汽車外部應用。此條痕缺陷可能還充當成形期間的應變集中位點,因此限制了可成形性。另外,用于制作適合于汽車外部面板的6xxx系列片材材料的已知工藝已經涉及一種相當復雜、昂貴且緩慢的程序,其大體上涉及以下步驟:熔融合金的半連續(xù)直接冷卻(dc)鑄造以形成鑄錠,鑄錠的刮修,使鑄錠在1到48小時之間的時間周期中均質化,熱軋,自退火,以及冷軋為所需規(guī)格。經輥軋的材料可隨后在連續(xù)熱處理作業(yè)線中被給予溶解熱處理,快速冷卻且接著老化。通常,用于汽車外部面板的自退火工藝包含高退出溫度,需要所述溫度來滿足條痕要求。高退出溫度促進了大的可溶粗糙顆粒,例如含有mg2si和銅的顆粒。為了實現在已供應和烤漆回火狀態(tài)中的所需強度組合,連續(xù)退火溶解熱處理(cash)作業(yè)線必須使用高固溶化溫度和長浸泡時間來溶解大的可溶顆粒。這些可溶顆粒已知影響在t4和烤漆回火狀態(tài)中的抗拉性質且還影響成形特性。大的可溶顆??勺罱K將cash作業(yè)線生產力降低到不可接受的水平。另外,自退火工藝減小了在t4和烤漆強度方面區(qū)分合金的能力,盡管合金化學性質存在顯著差異也是如此。汽車內部和結構產品一般是從在相對較低溫度下卷繞的再輥軋件生產的。這些產品滿足抗拉性質,但不滿足使用較低cash峰值金屬溫度和浸泡時間的外部產品的條痕要求。因此,用于內部/結構面板的金屬片材在cash作業(yè)線上運行往往比用于外部面板的金屬片材快25到50%之間。在此總體程序中,用于汽車應用的外部面板的處理會花費大體上長的固溶化時間,這降低了昂貴資產的生產力。因此需要具有減少的條痕缺陷的改進的鋁合金,以及用于從這些合金制造片材材料的更高效的工藝。技術實現要素:本發(fā)明的所涵蓋的實施例是由權利要求書而不是此
發(fā)明內容界定。此
發(fā)明內容是本發(fā)明的各種方面的高級概覽,且介紹了在下文的具體實施方式章節(jié)中進一步描述的一些概念。此
發(fā)明內容既定不識別所要求標的物的關鍵特征或本質特征,也既定不單獨地用以確定所要求標的物的范圍。應當通過參考整個說明書的適當部分、任何或全部附圖以及每一權利要求來理解所述標的物。本發(fā)明解決了上文關于在cash作業(yè)線上增加生產力的新工藝所描述的問題,且提供了具有高t4和烤漆后強度且條痕最少或無條痕的可熱處理的汽車鋁片材產品。作為非限制性實例,本發(fā)明的工藝尤其適用于汽車行業(yè)中。舉例來說,在卡車駕駛室中使用的外部面板需要良好的烤漆強度以及無條痕的表面外觀。然而,已知本發(fā)明的可熱處理的合金和工藝可適用于海洋、航空航天和運輸行業(yè),僅舉幾例。本發(fā)明的合金可用以制作呈擠壓件、板、片材和鍛件的形式的產品。附圖和表的說明圖1是處于熱軋條件(a)下的未再結晶晶粒結構和各自在375℃(b)、400℃(c)和425℃(d)下的批量退火1小時之后的再結晶晶粒結構的表示。圖2是使用標準生產實踐在自退火之后的較大mg2si顆粒大小的表示。掃描電子顯微鏡(sem)顯微照片示出了自退火線圈中的相對粗糙的mg2si沉淀物(由箭頭指示的暗顆粒)。圖3是在400℃下批量退火1小時之后的較小mg2si顆粒大小的表示。sem顯微照片示出了批量退火線圈中的精細mg2si顆粒(由箭頭指示的暗顆粒)。圖4是在自退火(sa)和批量退火(ba)之后示例性合金的t4抗拉屈服強度(以mpa計的tys)與最終屈服強度(以mpa計的uts)的比較。在插圖中,如下指示測試方向:l=縱向,t=橫向,d=對角線。標準sa是自退火再輥軋件,離開熱軋機的產品,其中溫度和輥軋條件使得產生再結晶片材。再輥軋件ba是其中批量退火工藝步驟以再輥軋厚度發(fā)生的產品。中間ba是其中批量退火工藝步驟在至少一個冷軋機通過之后但在最終冷軋機通過之前發(fā)生的產品。圖4中所示的線圈編號與圖5和6中的編號相同且呈相同次序。每一集合中的第一直方圖柱表示tys-l;每一集合中的第二直方圖柱表示tys-t;每一集合中的第三直方圖柱表示tys-d;每一集合中的第四直方圖柱表示uts-l;每一集合中的第五直方圖柱表示uts-t;且每一集合中的第六直方圖柱表示uts-d。圖5是所要求合金在自退火和批量退火之后針對180℃/20分鐘烤漆在橫向方向上測試的抗拉屈服強度結果(以mpa計)的表示。每一集合中的第一直方圖柱表示烤漆后屈服強度。每一集合中的中間直方圖柱表示t4屈服強度。每一集合中的右直方圖柱表示烤漆后屈服強度與t4屈服強度之間的差異。圖6是所要求合金在自退火和批量退火之后針對180℃/60分鐘烤漆在橫向(t)、縱向(l)和對角線(d45°)方向上測試的抗拉屈服強度結果(以mpa計)的表示。每一集合中的第一直方圖柱表示縱向方向上的結果。每一集合中的中間直方圖柱表示橫向方向上的結果。每一集合中的右直方圖柱表示對角線方向上的結果。圖7示出了沿著生產試驗線圈的長度的t4屈服強度(以mpa計)。圖8示出了試驗線圈連同標準生產自退火線圈(sa再輥軋件)的條痕樣本及其分級的圖片。圖9a示出了在橫向方向上測試的從合金1到5制備的t4片材的屈服強度結果。圖9b示出了在橫向方向上測試的從合金1到5制備的t4片材的彎曲內部角度。圖10a示出了使用空氣驟冷且在橫向方向上測試的從合金1到5制備的t6片材的屈服強度結果。圖10b示出了使用水驟冷且在橫向方向上測試的從合金1到5制備的t6片材的屈服強度結果。圖10c示出了使用空氣驟冷且在橫向方向上測試的從合金1到5制備的t6片材的彎曲內部角度。圖10d示出了使用水驟冷且在橫向方向上測試的從合金1到5制備的t6片材的彎曲內部角度。圖11示出了從如本文描述的片材制備的栓接管的垂直碰撞測試結果。圖12示出了從如本文描述的片材制備的栓接管的水平碰撞測試結果。圖13a示出了在輥軋方向和輥軋方向的45°上線圈0127619的內徑和外徑的條痕樣本。圖13b示出了在輥軋方向上線圈0127622的內徑和外徑的條痕樣本。圖13c示出了在輥軋方向上線圈0127602的內徑和外徑以及在輥軋方向上線圈0127681的外徑的條痕樣本。圖14示出了對照通過空氣驟冷和水驟冷制備的樣本的線圈0127622的自然老化時間以及線圈的內徑和外徑繪制的橫向屈服強度。表1列出了在退火之后示例性合金的t4片材和烤漆后(180℃/20分鐘和180℃/60分鐘)的機械性質。表2列出了在自退火和批量退火之后示例性合金的t4片材的條痕評估。表3列出了針對550℃/15秒cash然后進行60天的自然老化,自退火線圈與t4中的批量退火材料相比的平包邊測試分級。表4列出了具有10%和15%預應變的處于t4中的批量退火材料的平包邊測試分級。表5列出了來自試驗線圈的t4片材的機械性質。表6列出了試驗線圈的烤漆后狀況的機械性質。表7列出了在4或5天的自然老化之后沿著試驗線圈的長度的片材的機械性質。表8列出了在0%預應變、5%預應變、10%預應變和15%預應變之后線圈0127619的彎曲分級。表9列出了在5%預應變、10%預應變和15%預應變之后線圈0127622的彎曲分級。表10列出了在5%預應變、10%預應變和15%預應變之后線圈0127602的彎曲分級。表11列出了在5%預應變、10%預應變和15%預應變之后線圈0127681的彎曲分級。表12列出了在24到45天的自然老化之后來自試驗線圈的片材的機械性質。表13列出了在24到45天的自然老化之后和烤漆后來自試驗線圈的片材的機械性質。表14列出了在0%預應變、5%預應變、10%預應變和15%預應變之后線圈0127619、0127622、0127681和0127602的彎曲分級。具體實施方式本發(fā)明是針對在cash作業(yè)線上對于展現可接受的條痕的具有高t4和烤漆后強度的可熱處理的鋁片材產品增加生產力的新工藝。作為非限制性實例,本發(fā)明的可熱處理的合金可以是6xxx鋁合金。作為另一非限制性實例,本發(fā)明的工藝可在汽車行業(yè)中使用。定義和描述:如本文使用,術語“發(fā)明”、“本發(fā)明”、“此發(fā)明”和“當前發(fā)明”旨在廣泛地指代本專利申請和所附權利要求書的全部標的物。含有這些術語的語句應當理解為并不限制本文描述的標的物或者并不限制所附專利權利要求書的意義或范圍。在此描述中,參考由aa數字和例如“系列”或“6xxx”等其它相關標示所識別的合金。為了理解在命名和識別鋁及其合金時最常用的數字標示系統(tǒng),參見《鍛鋁和鍛鋁合金的國際合金標示和化學成分限制(internationalalloydesignationsandchemicalcompositionlimitsforwroughtaluminumandwroughtaluminumalloys)》或《呈鑄件和鑄錠形式的鋁合金的鋁業(yè)協會合金標示和化學成分限制的注冊記錄(registrationrecordofaluminumassociationalloydesignationsandchemicalcompositionslimitsforaluminumalloysintheformofcastingsandingot)》,兩者均由鋁業(yè)協會發(fā)布。如本文使用,術語“可熱處理的合金”既定廣泛地指代任何2xxx、6xxx和7xxx鋁合金。如本文使用,“一”和“所述”的意義包含單數和復數參考,除非上下文清楚地另外規(guī)定。在以下實例中,鋁合金是在其元素組成方面以重量百分比(重量%)來描述。在每一合金中,剩余部分是鋁,且所有雜質的最大重量%為0.15%。合金:本文描述新穎的6xxx鋁合金。在一個實例中,提供一種鋁合金,其包括0.20到1.0重量%的si、0.11到0.40重量%的fe、0.0到0.23重量%的cu、0.0到0.22重量%的mn、0.50到0.83重量%的mg、0.0到0.25重量%的cr、0.0到0.006重量%的ni、0.0到0.15重量%的zn、0.0到0.17重量%的ti、0.0到0.05重量%的pb、0.0到0.005重量%的be、多達0.15重量%的雜質,剩余部分為al。在另一實例中,提供一種鋁合金,其包括0.60到0.95重量%的si、0.20到0.35重量%的fe、0.05到0.20重量%的cu、0.05到0.20重量%的mn、0.55到0.75重量%的mg、0.0到0.15重量%的cr、0.0到0.006重量%的ni、0.0到0.15重量%的zn、0.0到0.15重量%的ti、0.0到0.05重量%的pb、0.0到0.005重量%的be、多達0.15重量%的雜質,剩余部分為al。在一些實例中,如本文描述的鋁合金包含基于合金的總重量為從0.20%到1.0%(例如,從0.30%到1.0%、從0.60%到0.95%或從0.65%到0.90%)的量的硅(si)。舉例來說,所述合金可包含0.20%、0.21%、0.22%、0.23%、0.24%、0.25%、0.26%、0.27%、0.28%、0.29%、0.30%、0.31%、0.32%、0.33%、0.34%、0.35%、0.36%、0.37%、0.38%、0.39%、0.40%、0.41%、0.42%、0.43%、0.44%、0.45%、0.46%、0.47%、0.48%、0.49%、0.50%、0.51%、0.52%、0.53%、0.54%、0.55%、0.56%、0.57%、0.58%、0.59%、0.60%、0.61%、0.62%、0.63%、0.64%、0.65%、0.66%、0.67%、0.68%、0.69%、0.70%、0.71%、0.72%、0.73%、0.74%、0.75%、0.76%、0.77%、0.78%、0.79%、0.80%、0.81%、0.82%、0.83%、0.84%、0.85%、0.86%、0.87%、0.88%、0.89%、0.90%、0.91%、0.92%、0.93%、0.94%、0.95%、0.96%、0.97%、0.98%、0.99%或1.0%的si。全部以重量%表達。在一些實例中,如本文描述的鋁合金包含基于合金的總重量為從0.11%到0.40%(例如,從0.20%到0.35%或從0.25%到0.30%)的量的鐵(fe)。舉例來說,所述合金可包含0.11%、0.12%、0.13%、0.14%、0.15%、0.16%、0.17%、0.18%、0.19%、0.20%、0.21%、0.22%、0.23%、0.24%、0.25%、0.26%、0.27%、0.28%、0.29%、0.30%、0.31%、0.32%、0.33%、0.34%、0.35%、0.36%、0.37%、0.38%、0.39%或0.40%的fe。全部以重量%表達。在一些實例中,如本文描述的鋁合金包含基于合金的總重量為從0%到0.23%(例如,從0.05%到0.20%或從0.1%到0.15%)的量的銅(cu)。舉例來說,所述合金可包含0.01%、0.02%、0.03%、0.04%、0.05%、0.06%、0.07%、0.08%、0.09%、0.10%、0.11%、0.12%、0.13%、0.14%、0.15%、0.16%、0.17%、0.18%、0.19%、0.20%、0.21%、0.22%或0.23%的cu。在一些情況下,合金中不存在cu(即,0%)。全部以重量%表達。在一些實例中,如本文描述的鋁合金包含基于合金的總重量為從0%到0.22%(例如,從0.05到0.20%或從0.1%到0.15%)的量的錳(mn)。舉例來說,所述合金可包含0.01%、0.02%、0.03%、0.04%、0.05%、0.06%、0.07%、0.08%、0.09%、0.10%、0.11%、0.12%、0.13%、0.14%、0.15%、0.16%、0.17%、0.18%、0.19%、0.20%、0.21%或0.22%的mn。在一些情況下,合金中不存在mn(即,0%)。全部以重量%表達。在一些實例中,如本文描述的鋁合金包含基于合金的總重量為從0.50%到0.83%(例如,從0.55%到0.75%或從0.60%到0.70%)的量的鎂(mg)。舉例來說,所述合金可包含0.50%、0.51%、0.52%、0.53%、0.54%、0.55%、0.56%、0.57%、0.58%、0.59%、0.60%、0.61%、0.62%、0.63%、0.64%、0.65%、0.66%、0.67%、0.68%、0.69%、0.70%、0.71%、0.72%、0.73%、0.74%、0.75%、0.76%、0.77%、0.78%、0.79%、0.80%、0.81%、0.82%或0.83%的mg。全部以重量%表達。在一些實例中,如本文描述的鋁合金包含基于合金的總重量為從0%到0.25%(例如,從0%到0.15%或從0.05%到0.20%)的量的鉻(cr)。舉例來說,所述合金可包含0.010%、0.011%、0.012%、0.013%、0.014%、0.015%、0.016%、0.017%、0.018%、0.019%、0.020%、0.021%、0.022%、0.023%、0.024%、0.025%、0.026%、0.027%、0.028%、0.029%、0.030%、0.031%、0.032%、0.033%、0.034%、0.035%、0.036%、0.037%、0.038%、0.039%、0.040%、0.041%、0.042%、0.043%、0.044%、0.045%、0.046%、0.047%、0.048%、0.049%、0.050%、0.051%、0.052%、0.053%、0.054%、0.055%、0.056%、0.057%、0.058%、0.059%、0.060%、0.061%、0.062%、0.063%、0.064%、0.065%、0.066%、0.067%、0.068%、0.069%、0.070%、0.071%、0.072%、0.073%、0.074%、0.075%、0.076%、0.077%、0.078%、0.079%、0.080%、0.081%、0.082%、0.083%、0.084%、0.085%、0.086%、0.087%、0.088%、0.089%、0.090%、0.091%、0.092%、0.093%、0.094%、0.095%、0.096%、0.097%、0.098%、0.099%、0.10%、0.11%、0.12%、0.13%、0.14%、0.15%、0.16%、0.17%、0.18%、0.19%、0.20%、0.21%、0.22%、0.23%、0.24%或0.25%的cr。在一些情況下,合金中不存在cr(即,0%)。全部以重量%表達。在一些實例中,如本文描述的鋁合金包含基于合金的總重量為從0%到0.006%(例如,從0%到0.005%或從0.001%到0.004%)的量的鎳(ni)。舉例來說,所述合金可包含0.001%、0.002%、0.003%、0.004%、0.005%或0.006%的ni。在一些情況下,合金中不存在ni(即,0%)。全部以重量%表達。在一些實例中,如本文描述的鋁合金包含基于合金的總重量為從0%到0.15%(例如,從0.01%到0.15%或從0.05%到0.1%)的量的鋅(zn)。舉例來說,所述合金可包含0.01%、0.011%、0.012%、0.013%、0.014%、0.015%、0.016%、0.017%、0.018%、0.019%、0.02%、0.03%、0.04%、0.05%、0.06%、0.07%、0.08%、0.09%、0.10%、0.11%、0.12%、0.13%、0.14%或0.15%的zn。在一些情況下,合金中不存在zn(即,0%)。全部以重量%表達。在一些實例中,如本文描述的鋁合金包含基于合金的總重量為從0%到0.17%(例如,從0.01%到0.15%或從0.05%到0.1%)的量的鈦(ti)。舉例來說,所述合金可包含0.01%、0.011%、0.012%、0.013%、0.014%、0.015%、0.016%、0.017%、0.018%、0.019%、0.02%、0.03%、0.04%、0.05%、0.06%、0.07%、0.08%、0.09%、0.10%、0.11%、0.12%、0.13%、0.14%、0.15%、0.16%或0.17%的ti。在一些情況下,合金中不存在ti(即,0%)。全部以重量%表達。在一些實例中,如本文描述的鋁合金包含基于合金的總重量為從0%到0.05%(例如,從0%到0.04%或從0.001%到0.01%)的量的鉛(pb)。舉例來說,所述合金可包含0.001%、0.002%、0.003%、0.004%、0.005%、0.006%、0.007%、0.008%、0.009%、0.010%、0.011%、0.012%、0.013%、0.014%、0.015%、0.016%、0.017%、0.018%、0.019%、0.020%、0.021%、0.022%、0.023%、0.024%、0.025%、0.026%、0.027%、0.028%、0.029%、0.030%、0.031%、0.032%、0.033%、0.034%、0.035%、0.036%、0.037%、0.038%、0.039%、0.040%、0.041%、0.042%、0.043%、0.044%、0.045%、0.046%、0.047%、0.048%、0.049%或0.050%的pb。在一些情況下,合金中不存在pb(即,0%)。全部以重量%表達。在一些實例中,如本文描述的鋁合金包含基于合金的總重量為從0%到0.005%(例如,從0%到0.004%或從0%到0.001%)的量的鈹(be)。舉例來說,所述合金可包含0.0001%、0.0002%、0.0003%、0.0004%、0.0005%、0.0006%、0.0007%、0.0008%、0.0009%、0.001%、0.002%、0.003%、0.004%或0.005%的be。在一些情況下,合金中不存在be(即,0%)。全部以重量%表達。6xxx鋁合金可以出于各種目的而包含多種第三元素(tertiaryelement),本文中有時稱為雜質,所述目的例如增強機械、物理或腐蝕性質(例如,強度、韌性、抗疲勞性和/或耐腐蝕性),增強在高溫下的性質,促進鑄造,控制鑄造或鍛造晶粒結構,和/或增強可加工性,以及其它目的。當存在時,這些第三元素可包含ag、li、sn、bi、sr、sb、v、zr、sc、hf、mo、co和稀土元素中的一種或多種。當存在時,第三元素通常以最多0.05重量%的量包含于合金中。所有第三元素的總和不超過0.15重量%。每一合金的其余百分比是鋁。下文列出如本文描述的鋁合金的示例性范圍。在隨后的6xxx鋁合金實例中,應理解,每一實例中未陳述的剩余部分是al。在一個實例中,本文描述6xxx鋁合金,其包括:成分范圍(重量%)標稱(重量%)cu0-0.220.10fe0.11-0.400.25mg0.50-0.830.65mn0-0.220.08si0.20-1.00.80ti0-0.17zn0-0.15cr0-0.25pb0-0.05be0-0.005痕量元素雜質0-0.15在另一實例中,本文描述6xxx鋁合金,其包括:在再一實例中,本文描述6xxx鋁合金,其包括:成分范圍(重量%)標稱(重量%)cu0.08-0.140.12fe0.27-0.340.31mg0.59-0.690.65mn0.10-0.160.12si0.74-0.840.82ti0-0.050.03zn0-0.050.01cr0-0.0500.042pb0-0.05be0-0.005痕量元素雜質0-0.15在又一實例中,本文描述6xxx鋁合金,其包括:在另一實例中,本文描述6xxx鋁合金,其包括:成分范圍(重量%)標稱(重量%)cu0.07-0.170.13fe0.19-0.270.22mg0.59-0.690.65mn0.05-0.140.08si0.56-0.650.62ti0-0.080.04zn0-0.050.02cr0-0.080.08pb0-0.05be0-0.005痕量元素雜質0-0.15在再一實例中,本文描述6xxx鋁合金,其包括:在又一實例中,本文描述6xxx鋁合金,其包括:成分范圍(重量%)標稱(重量%)cu0.19-0.230.19fe0.26-0.320.30mg0.61-0.690.67mn0.15-0.190.16si0.58-0.650.63ti0-0.080.04zn0-0.050.01cr0-0.10.081pb0-0.05be0-0.005痕量元素雜質0-0.15性質:已經出人意料地發(fā)現所描述的6xxx鋁合金擁有許多獨特且有利的性質。本領域的普通技術人員已知通過制作鋁片材的工藝可以修整鋁性質,例如(但不限于)強度、伸長率、可彎曲性以及外觀。還已知生產具有若干這些性質的鋁片材是困難且不可預測的,因為增加一個性質可能降低另一性質。然而,所公開的合金展現有利性質的組合而不會有害地影響鋁片材的其它性質。舉例來說,所公開的合金出人意料地展現高強度和合適的可彎曲性。以下是所描述合金的非限制性增強性質。高t4強度:所公開的鋁合金可在批量退火之后具有至少100mpa的t4屈服強度(例如,至少105mpa、至少110mpa、至少115mpa、至少120mpa、至少125mpa、至少130mpa、至少135mpa、至少140mpa或至少145mpa)以及至少200mpa的t4抗拉強度(例如,至少205mpa、至少210mpa、至少215mpa、至少220mpa、至少225mpa、至少230mpa、至少235mpa、至少240mpa、至少245mpa、至少250mpa或至少255mpa)。在類似的固溶化條件下這等效于本發(fā)明的比自退火合金高約25mpa的屈服強度以及高約35mpa的抗拉強度,如圖4中所示。另外,另一優(yōu)點在于,批量退火的片材在多種固溶化條件下展現類似的屈服強度,表明mg2si顆粒足夠精細以在較低峰值金屬溫度下溶解,這不同于自退火的產品。本質上,本發(fā)明的工藝適合于比自退火產品更好地區(qū)分合金化學效應。高烤漆后強度:所公開的鋁合金可以在180℃的烤漆條件的批量退火20分鐘之后具有至少160mpa的烤漆后屈服強度(例如,至少165mpa、至少170mpa、至少175mpa、至少180mpa、至少185mpa、至少190mpa或至少200mpa)。這等效于比自退火合金高約45mpa到55mpa的屈服強度,如圖5中所示。通過如圖5中所示的本發(fā)明合金和工藝很容易滿足烤漆后條件與t4條件之間50mpa的屈服強度差異。類似地,圖6中示出180℃的烤漆條件達60分鐘的烤漆后強度。與標準自退火材料相比,可見本發(fā)明合金和工藝中對烤漆的顯著更高的響應。新的合金和工藝組合允許超過顧客要求的最小強度的材料。表1列出了用于標準和本發(fā)明合金和工藝的溶解熱處理(t4)和烤漆后條件的機械性質??蓮澢裕核_的鋁合金展現高可彎曲性??赏ㄟ^彎曲角度來估定可彎曲性。本文描述的鋁合金在t4回火狀態(tài)中可具有小于約10°的彎曲角度。舉例來說,本文描述的鋁合金在t4回火狀態(tài)中可具有小于約9°、小于約8°、小于約7°、小于約6°、小于約5°、小于約4°、小于約3°、小于約2°,或小于約1°的彎曲角度。減少的條痕:在550℃下的溶解熱處理15秒和45秒之后,所公開的鋁合金展示了與自退火合金相比顯著更好的條痕。通過首先將片材拉伸10%且隨后用磨石粗加工表面以突顯所關注的特征來測量條痕。隨后將片材樣本與標準進行比較。圖8和表2中示出了條痕測試和使用的條痕等級量表的結果。改進的平包邊性能:在550℃下的溶解熱處理15秒之后,所公開的鋁合金展示與自退火合金相比類似或更好的平包邊響應,如表3中所示。在全部三個方向上使片材預應變7%和15%之后進行包邊測試。隨后基于包邊外觀將包邊的樣本與標準和指派的額定值進行比較。更快的cash速度:如本文論述,在最后熱軋遍次之后的低退出溫度接著進行批量退火工藝產生了與自退火材料相比顯著更小的mg2si顆粒(參見圖2和3),這又允許更快的cash速度。本文描述的工藝使cash容量、速度和效率(僅舉幾例)增加至少10%、至少15%、至少20%或至少25%。工藝:還公開一種用于生產6xxx系列鋁合金產品的新穎工藝,其至少涉及處于再輥軋和中間規(guī)格的不大于300℃的熱軋退出溫度與退火(例如,批量退火)的組合。此外,本文描述的工藝提供具有顯著更高的t4和烤漆后強度、更好的條痕控制、更快的cash作業(yè)線速度以及改善的可包邊性的6xxx鋁合金產品。在一個實例中,本文描述的工藝涉及均質化、熱軋、冷軋、退火(例如,批量退火)、冷軋,以及cash。在另一實例中,本文描述的工藝涉及均質化、熱軋(a-在退出溫度卷繞之后,立即放置到退火爐中;b-在退出溫度卷繞之后,冷卻到室溫且隨后放置到退火爐中),退火(例如,批量退火),冷軋,以及cash。均質化:鑄錠均質化可以包含(但不限于)在500到600℃之間(例如,500℃、510℃、520℃、530℃、540℃、550℃、560℃、570℃、580℃、590℃或600℃)加熱鑄錠多達10小時。舉例來說,可將鑄錠加熱達10小時或更少、9小時或更少、8小時或更少、7小時或更少、6小時或更少、5小時或更少、4小時或更少、3小時或更少、2小時或更少或者1小時或更少。在一個實施例中,在560℃下加熱鑄錠大于6小時且隨后在540℃下加熱大于1小時??赏ㄟ^各種鑄造方法制備鑄錠,例如通過直接冷卻鑄造(dc)。熱軋:在熱軋期間,可以控制溫度和其它操作參數,使得鋁合金熱軋中間產品在從熱軋機退出時的溫度不大于300℃、不大于290℃、不大于280℃或不大于270℃。在一個實例中,退出溫度為約260℃。在一個實例中,退出溫度為約250℃。在另一實例中,退出溫度為約240℃。在又一實例中,退出溫度為約230℃。在再一實例中,退出溫度為約220℃。可在約200℃到500℃之間熱軋鑄錠。舉例來說,可在范圍從約225℃到475℃、從約250℃到450℃、從約275℃到425℃或從約300℃到400℃的溫度下熱軋鑄錠。熱軋片材可具有10mm或更小(例如,3到10mm之間)的規(guī)格。舉例來說,熱軋片材可具有10mm或更小、9mm或更小、8mm或更小、7mm或更小、6mm或更小、5mm或更小、4mm或更小或者3mm或更小的規(guī)格。如本文描述,控制熱軋步驟的退出溫度提供所需的微結構,即抑制大的粗糙mg2si顆粒的沉淀,其在進一步處理時提供具有高t4和烤漆后強度、更好的條痕以及更快的cash速度的產品??刂茻彳堜X合金中間產品的退出溫度可以任何常規(guī)方式完成,例如通過熱軋機操作條件的控制,例如冷卻潤滑劑的程度、輥軋速度或典型熱軋機上的各種步驟之間的時間延遲。隨后可使用已知技術監(jiān)視熱軋中間產品的溫度,例如通過接觸式熱電偶或光學高溫計。所監(jiān)視的熱軋機退出溫度可以反饋控制方式與如上所述使用冷卻潤滑劑、軋機速度或類似者在熱軋期間冷卻板材或控制溫度結合使用。也就是說,軋機退出溫度可規(guī)定輥軋操作中的調整以將退出溫度維持于指定范圍內。批量退火:在冷軋工藝中的熱帶規(guī)格或某種中間規(guī)格的批量退火可產生幾乎不具有條痕或無條痕的產品的合適紋理。在批量退火步驟中的線圈加熱期間,微結構變?yōu)樘畛溆懈呙芏鹊南鄬^精細的可溶顆粒,例如mg2si。這些精細沉淀物產生最終產品中的所供應的回火狀態(tài)(t4)和烤漆回火狀態(tài)中的抗拉性質連同優(yōu)良的條痕和包邊特性的所需組合,與常規(guī)自退火產品相比在溶解熱處理作業(yè)線上具有相對較低的溫度和浸泡時間熱處理要求。在批量退火期間,可以從約40℃/小時到60℃/小時(例如,40℃/小時、45℃/小時、50℃/小時、55℃/小時或60℃/小時)的速率將卷繞的鋁片材加熱到約350℃到450℃之間(例如,350℃、360℃、370℃、380℃、390℃、400℃、410℃、420℃、430℃、440℃或450℃)的溫度。在一些情況下,可以約50℃/小時的速率將鋁片材加熱到約400℃的溫度。保持時間可多達1小時、多達2小時、多達3小時、多達4小時或多達5小時。在一個實例中,保持時間是2小時。在一個實例中,隨后可以從至少5℃/小時的速率將鋁片材冷卻到室溫。在另一實例中,可以至少7℃/小時的速率將鋁片材冷卻到室溫。在一個實例中,可以至少9℃/小時的速率將鋁片材冷卻到室溫。在另一實例中,可以至少10℃/小時的速率將鋁片材冷卻到室溫。應理解,退火工藝不應當限于批量退火。退火工藝也可包含連續(xù)退火。舉例來說,可通過使片材通過連續(xù)退火溶解熱(cash)作業(yè)線來對片材進行連續(xù)退火。冷軋:可使用常規(guī)冷軋機和技術對鋁片材進行冷軋。冷軋片材可具有0.5到4.5mm之間、0.7到4.0mm之間或0.9到3.5mm之間的規(guī)格。在一個實例中,冷軋片材具有約1.0mm的規(guī)格。在另一實例中,冷軋片材具有約0.8mm的規(guī)格。在又一實例中,冷軋片材具有約1.2mm的規(guī)格。冷加工減少的量可多達65%、多達70%、多達75%、多達80%或多達85%。連續(xù)退火溶解熱(cash)處理:溶解熱處理可為用于合金的導致可溶顆粒的固溶化的任何常規(guī)處理。可將鋁片材加熱到范圍從約500℃到580℃(例如,500℃、510℃、520℃、530℃、540℃、550℃、560℃、570℃或580℃)的峰值金屬溫度且在預定溫度以上浸泡(即,保持于指示的溫度)達一時間周期。在一些實例中,允許片材浸泡多達約10分鐘(例如,從1秒到10分鐘(包含性))。舉例來說,可將片材浸泡約5秒或更少、10秒或更少、15秒或更少、30秒或更少、45秒或更少、1分鐘或更少、2分鐘或更少、3分鐘或更少、4分鐘或更少、5分鐘或更少、6分鐘或更少、7分鐘或更少、8分鐘或更少、9分鐘或更少或者10分鐘或更少。用于溶解熱處理的示例性條件包含在高于540℃的溫度下30秒或60秒的浸泡時間。在一個實例中,將鋁合金加熱到550℃,其中條帶保持高于540℃達15或45秒。在加熱和浸泡之后,以大于10℃/s(例如,15℃/s或更大、20℃/s或更大或者25℃/s或更大)的速率將條帶快速冷卻到500到200℃之間的溫度。在一個實例中,鋁合金具有高于20℃/秒的驟冷速率,其中在450到250℃之間冷卻條帶。在其它實例中冷卻速率可能更快。在驟冷之后,鋁條帶可經受再加熱步驟,然后進行卷繞??赏ㄟ^使片材通過由輻射加熱、對流加熱、傳導加熱或紅外加熱等組成的加熱裝置來實行再加熱步驟。再加熱片材以允許條帶卷繞的步驟可在范圍從約55℃到110℃(例如,55℃、60℃、65℃、70℃、75℃、80℃、85℃、90℃、95℃、100℃、105℃或110℃)的溫度下執(zhí)行。本文描述的合金和方法可用于汽車、海洋、航空航天和/或運輸應用中,僅舉幾例。在一些情況下,所述合金和方法可用以制備機動車輛車身零件產品,包含外部面板。以下實例將用以進一步說明本發(fā)明,然而同時不構成對本發(fā)明的任何限制。相反,應清楚地理解,可以做出各種實施例、修改及其等效物,在閱讀本文的描述之后本領域的技術人員可以明了這些內容而不會脫離本發(fā)明的精神。在以下實例中描述的研究期間,遵循常規(guī)程序,除非另外陳述。下文出于說明性目的而描述一些程序。實例實例1鋁片材的制備dc鑄造含有98.03到98.06重量%的al、0.78到0.83重量%的si、0.22到0.24重量%的fe、0.10到0.11重量%的cu、0.08到0.09重量%的mn、0.64到0.65重量%的mg、0.015到0.019重量%的cr、0.006重量%的ni、0.011到0.016重量%的zn以及0.016重量%的ti的五個樣本。在560℃下使鑄錠均質化超過6小時,冷卻到540℃,且保持于所述溫度超過1小時。隨后從均質化坑熱拉動鑄錠且放置到用于熱軋的臺上。熱軋步驟包含使鑄錠運行通過可逆式軋機,然后在串列式軋機中熱軋,其中厚度進一步減少。熱軋材料的最終退出溫度是針對獲得在200到300℃的范圍中的卷繞溫度。進行批量退火步驟,其包含將線圈加熱到從375℃到425℃的所需溫度,然后浸泡最少60分鐘。在氮氣氣氛中實行退火,其中總批量退火熱處理循環(huán)時間為約8小時。將線圈從爐中拉出且允許其冷卻到室溫,然后進行冷軋。在線圈的完全退火之后進行冷軋。將所有線圈從熱帶規(guī)格冷軋為完成規(guī)格而無任何中間退火。在約550℃、約562℃和約575℃的峰值金屬溫度下實行cash,其中浸泡時間為15、30或45秒。在約450℃到約250℃之間在約18℃/秒到約50℃/秒的速率的驟冷速率下針對所有產品使用標準受迫空氣冷卻。重繞金屬溫度為約95℃。實例2最終抗拉強度和屈服強度的確定如上所述在實例1中制備線圈,且溶解熱處理為約550℃的峰值金屬溫度達15和45秒。使用本領域的普通技術人員已知的方法根據astmb557和astme8-11確定均勻和總伸長率和抗拉屈服強度。表4中示出了t4回火狀態(tài)片材中的5線圈工廠試驗測試的機械性質結果。圖4是在自退火(sa)和批量退火(ba)之后所要求合金的t4抗拉屈服強度(以mpa計的tys)與最終屈服強度(以mpa計的uts)的比較。與來自標準自退火生產線圈的平均屈服強度相比在本發(fā)明合金和工藝中獲得更高的t4屈服強度,如圖7中所示。實例3t4均勻和總伸長率的確定使用本領域的普通技術人員已知的方法根據astmb557和astme8-11確定來自上述線圈的片材的均勻和總伸長率。表5和6示出了工廠試驗測試的均勻和總伸長率結果。實例4烤漆抗拉屈服強度的確定使用本領域的普通技術人員已知的方法根據astmb557和astme8-11確定來自上述線圈的片材的烤漆抗拉屈服強度。圖5圖示了以2%預應變進行測試然后是180℃/20分鐘暴露而獲得的烤漆后屈服強度。與消費型典型屈服強度相比,在本發(fā)明合金和工藝中的烤漆后強度顯著更高。實例5mg2si大小分布使用sem觀察mg2si大小分布。從批量退火線圈取得的樣本展示了比從自退火線圈取得的那些樣本(圖2和3)更小的顆粒大小。實例6條痕的確定條痕是在6xxx合金中發(fā)現的導致帶狀表面拓撲的定向晶粒的大集合的集體變形。這些晶粒集合是在塑性變形期間激活且平行于輥軋方向而定向。這些帶在裸樣本上一般感覺不到,但因為這些晶粒集合具有不同的高度位置(峰和谷),所以它們例如在上漆或表面石磨之后可視覺上感覺到。對條痕準則進行視覺上分級,如表2中所示。圖8示出了試驗線圈連同標準生產自退火線圈的條痕樣本。在橫向于輥軋的方向上使樣本預應變10%,然后進行石磨以突顯條痕狀況。總體上,所公開的合金和工藝提供了可接受的表面條痕分級。實例7平包邊性能表3列出了與t4回火狀態(tài)中的批量退火線圈相比自退火線圈的平包邊測試結果。使材料在550℃下通過cash作業(yè)線達15秒,然后是60天的自然老化。表4列出了具有10%和15%預應變的處于t4回火狀態(tài)中的批量退火試驗線圈的平包邊性能分級??傮w上,所述分級是1s和2s,這視為可接受的(參見表3)。以15%預應變在l方向上測試的一個線圈樣本展示了3的分級。此較高的包邊分級歸因于針對所述線圈觀察到的高屈服強度。實例8cr和mn對合金抗拉性質和可碰撞性的影響根據實例1中描述的方法制備具有下表中所示的組成的鋁合金。合金1和合金2是參考合金。合金3是包含比參考合金更大量的mn且不包含銅的合金。合金4是包含比參考合金更大量的cr的合金。合金5是包含比參考合金更大量的mn和cr的合金。在合金1、2、3、4和5中的每一者中,組成的剩余部分是鋁。合金simgcufemncrtimn+cr合金10.880.670.080.180.070.0140.0250.08合金20.890.670.090.20.080.010.020.09合金30.870.650.000.180.130.0010.0160.13合金40.900.680.090.190.080.080.0190.16合金50.870.670.080.190.140.070.020.21通過在530℃下加熱8小時使合金1到5均質化。通過可逆式軋機對合金進行熱軋,隨后進行冷軋。從合金1到5制備的片材中的每一者的最終規(guī)格厚度是大約1mm。在550℃下使片材固溶化20秒(指示為“20s”)或60秒(指示為“60s”),且隨后使用水(指示為“wq”)或空氣(指示為“aq”)進行驟冷。通過在215℃下加熱t(yī)4片材30分鐘或者在225℃下加熱t(yī)4片材30分鐘而實現t6回火狀態(tài)。使用本領域的普通技術人員已知的方法在橫向方向上確定t4和t6片材的屈服強度和彎曲。根據iso/dis6892-1執(zhí)行抗拉測試,且根據vda238-100執(zhí)行彎曲角度測試。確定使用20秒固溶化步驟然后進行空氣驟冷和水驟冷以及60秒固溶化步驟然后進行水驟冷制備的從合金1到5制備的t4片材的屈服強度性質。參見圖9a。結果展示對于五個片材來說,t4強度是近似相同的。在10%的拉伸預應變之后確定t4片材的彎曲性質。參見圖9b。結果展示通過空氣驟冷制備的含有較大量cr和/或mn的片材(即,從合金3、4和5制備的片材)展現改進的彎曲性質。確定使用20秒固溶化步驟然后進行空氣驟冷和水驟冷制備的從合金1到5制備的t6片材的抗拉強度性質。參見圖10a和10b。結果展示含有較大量cr和/或mn的空氣驟冷t6片材(即,從合金3、4和5制備的片材)展現與從參考合金1和2制備的片材相比多大約10到20mpa的強度損失。參見圖10a。不包含cu的水驟冷片材(即,從合金3制備的片材)的強度比從參考合金1和2制備的片材低大約10mpa。確定t6片材的彎曲性質。參見圖10c和10d。結果展示含有較大量cr和/或mn的片材(即,從合金3、4和5制備的片材)展現優(yōu)于參考合金1和2的改進的彎曲性質。另外,與空氣驟冷樣本相比,t6彎曲對于通過水驟冷制備的含有cr和/或mn的片材進一步改進。參見圖10c和10d。執(zhí)行測試以估定碾壓表現以確定樣本的可碰撞性。折疊且栓接片材(3mm厚)以形成碰撞管。在壓機中以恒定準靜態(tài)速度在垂直壓縮中(垂直碰撞測試)或者在準靜態(tài)3點彎曲設置中(水平碰撞測試)測試所述管。針對從類似于合金5的包含cr和mn的片材以及還從類似于合金1和2的參考片材制備的碰撞管確定可碰撞性。執(zhí)行垂直和水平測試。對于水平測試,在180℃下對用以制備碰撞管的片材進行熱處理達10小時。對于垂直測試,在185℃下對用以制備碰撞管的片材進行加熱15分鐘。如圖11中所示,含有增加量的cr和mn的碰撞管在垂直碰撞測試中在碾壓后成功地折疊而無撕裂,而參考碰撞管展現撕裂。與參考件相比,含有增加量的cr和mn的碰撞管還展示在水平碰撞測試中的改進可碰撞性。參見圖12。實例9強度、條痕和包邊性能線圈組成:從具有下表中所示的組成的鋁合金制備線圈。線圈alcusifetimgmncr012760298.050.100.790.260.020.630.080.01012762298.050.110.790.250.030.610.090.02012768198.040.100.780.240.020.630.100.01012761998.050.110.790.250.030.610.090.02樣本制備:以上所示的組成的鑄錠通過以下方式而各自均質化:將鑄錠加熱到560℃達6小時,將鑄錠冷卻到540℃,且允許鑄錠在540℃下浸泡2小時。隨后在范圍從209℃到256℃的溫度下熱軋和卷繞鑄錠。將線圈0127619熱軋到2.54mm規(guī)格且將其它線圈熱軋到5mm規(guī)格。線圈中的每一者的再輥軋件相對不含粗糙的mg2si/si顆粒,且晶粒結構未再結晶。在范圍從398℃到418℃的浸泡溫度下以100分鐘的浸泡時間對四個線圈進行再輥軋批量退火。再輥軋件完全再結晶且展現比常規(guī)自退火再輥軋件相對更精細的顆粒結構。以范圍從8到15秒的浸泡時間在范圍從約539℃到555℃的溫度下實行cash。使用水或空氣執(zhí)行驟冷。重繞金屬溫度范圍是從73℃到85℃。條痕分析:使用表2中提供的等級量表,在輥軋方向(90°)和輥軋方向的45°上針對條痕分析線圈的內徑(id)和外徑(od)。所有線圈展現合適的條痕結果且被指派1的分級。對于線圈0127619,參見圖13a;對于線圈0127622,參見圖13b;以及對于線圈0127602和0127681,參見圖13c。老化4到5天的樣本:抗拉性質和彎曲分級針對在4或5天的自然老化之后的線圈確定抗拉性質。具體來說,在4天的自然老化之后確定線圈0127619的抗拉性質,且在5天的自然老化之后確定線圈0127622、0127602和0127681的抗拉性質。在表7中示出了結果。所有線圈樣本展現大于215mpa的最終抗拉強度水平以及在100到155mpa的范圍內的屈服強度值。另外,每一線圈的平均伸長率大于27%。平均伸長率計算如下:平均伸長率=(橫向+2*對角線+縱向)/4。確定線圈的彎曲分級。在具有15mm輥的三點彎曲裝置上使用0.50mm沖頭和3.85mm的間隙將來自線圈0127622、0127602和0127681的樣本預彎曲到160°。在1噸手扳壓機上以0.82mm墊片對樣本進行包邊。將來自線圈0127619的樣本預彎曲到180°。表8到11列出了在0%、5%、10%和/或15%的預應變下在4或5天的自然老化之后批量退火試驗線圈0127619(表8)、0127622(表9)、0127602(表10)和0127681(表11)的平包邊性能分級。對線圈的內徑(id)和/或外徑(od)執(zhí)行測試。總體上,所述分級是1s和2s,這視為可接受的(參見表3)。老化24到45天的樣本:抗拉性質和彎曲分級針對在24到45天的自然老化之后的線圈確定抗拉性質。具體來說,在29天的自然老化之后確定線圈0127619的抗拉性質,在24天的自然老化之后確定線圈0127622的抗拉性質,且在45天的自然老化之后確定線圈0127602和0127681的抗拉性質。在表12中示出了結果。所有線圈樣本展現大于215mpa的最終抗拉強度水平以及在100到155mpa的范圍內的屈服強度值。另外,每一線圈的平均伸長率大于27%。平均伸長率計算如下:平均伸長率=(橫向+2*對角線+縱向)/4。還在烤漆之后確定上述線圈樣本的抗拉性質。在表13中示出了結果。所有線圈樣本展現大于280mpa的最終抗拉強度水平以及大于200mpa的屈服強度值。另外,每一線圈的平均伸長率為24%或更大。根據以上所示的等式計算平均伸長率。確定線圈的彎曲分級。樣本預彎曲到180°且具有0.45mm的mandrel半徑。表14列出在0%、5%、10%和/或15%預應變下在所指示天數的自然老化之后線圈0127619、0127622、0127602和0127681的包邊性能分級。對線圈的內徑(id)、中間和/或外徑(od)執(zhí)行測試??傮w上,經受5%和10%預應變的線圈的分級是1s和2s,其視為可接受的(參見表3)。將通過對來自線圈0127622的樣本進行水驟冷和空氣驟冷獲得的屈服強度以及從樣本的內徑和外徑獲得的屈服強度對比以天數計的自然老化時間而繪出。參見圖14。如圖14中所示,對于多達100天的自然老化將橫向屈服強度控制為100到135mpa之間的值。上文引用的所有專利、公開案以及摘要以全文引用的方式并入本文。已經在本發(fā)明的各種目標的實現方面描述了本發(fā)明的各種實施例。應當認識到,這些實施例僅說明本發(fā)明的原理。在不脫離如所附權利要求書中界定的本發(fā)明的精神和范圍的情況下,本領域的技術人員將容易了解對本發(fā)明的眾多修改和調適。當前第1頁12