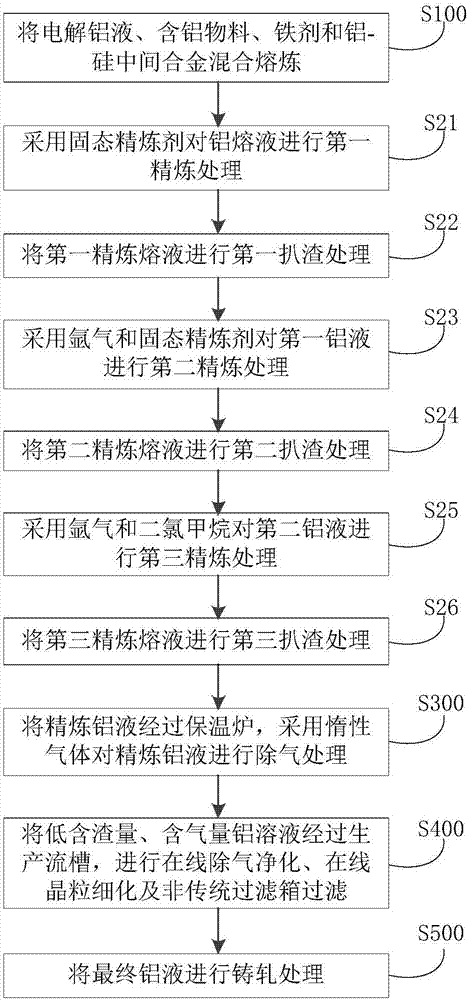
本發(fā)明屬于鋁板帶箔材加工
技術(shù)領(lǐng)域:
,具體而言,本發(fā)明涉及8079合金雙零箔坯料及其制備方法和8079合金雙零箔。
背景技術(shù):
:鋁箔因其自身的特性,被廣泛應(yīng)用于包裝、建筑、電力等領(lǐng)域。隨著經(jīng)濟技術(shù)的發(fā)展,市場對鋁箔品質(zhì)的要求越來越高,希望鋁箔的晶粒更加細(xì)膩均勻,厚度更薄,針孔更少,力學(xué)性能和表面質(zhì)量更高。目前,大部分雙零鋁箔采用的是1235合金或8079合金,由于1235合金的元素總含量少,其雙零箔成品的力學(xué)性能低,無法滿足現(xiàn)代高速復(fù)合機的生產(chǎn)要求;而8079合金雙零箔由于力學(xué)性能高,迎合了高速復(fù)合機的需求。同時,8079合金雙零箔的表面質(zhì)量比1235合金雙零箔的表面質(zhì)量更細(xì)膩,晶粒組織更加細(xì)密均勻,光澤度更均勻,針孔率更少,可以用于更高檔的產(chǎn)品。鋁箔坯料的生產(chǎn)方式主要有兩種:熱軋和鑄軋,由于8079合金自身的成分特點,低si高fe,目前國際上的8079合金雙零箔一般只采用熱軋坯料生產(chǎn),熱軋坯料箔坯晶粒細(xì)小均勻,其雙零箔成品表面細(xì)膩,光澤均勻。對于鑄軋,由于電解鋁液溫度過高,鋁液中非自發(fā)晶核較少,導(dǎo)致采用電解鋁液直接鑄軋制備雙零箔坯料難度更大,鑄軋板中經(jīng)常有夾雜、氣道、晶粒粗大、表面條紋等缺陷。但與熱軋坯料相比,鑄軋坯料具有流程短、成本低、軋制超薄鋁箔時針孔度少等一系列優(yōu)點。因此,現(xiàn)有開發(fā)電解鋁液直接鑄軋制備8079合金雙零箔坯料具有重要的意義。技術(shù)實現(xiàn)要素:本發(fā)明旨在至少在一定程度上解決相關(guān)技術(shù)中的技術(shù)問題之一。為此,本發(fā)明的一個目的在于提出一種8079合金雙零箔坯料及其制備方法和8079合金雙零箔,該方法可使得生產(chǎn)的8079合金雙零箔坯料的氫含量控制在0.1ml/100gal以下,ti吸收率達到85.75%~87.23%,鑄軋板晶粒達到1級(低倍晶粒度),鑄軋板表面質(zhì)量好且內(nèi)部組織均勻,8079合金雙零箔坯料軋制至0.0045㎜厚度時,針孔度小于100個/m2。本申請是基于發(fā)明人下列發(fā)現(xiàn)完成的:鋁箔坯料的生產(chǎn)方式主要有兩種:熱軋和鑄軋,目前國際上的8079合金雙零箔一般只采用熱軋坯料生產(chǎn),熱軋坯料箔坯晶粒細(xì)小均勻,其雙零箔成品表面細(xì)膩,光澤均勻。對于鑄軋,由于電解鋁液溫度過高,鋁液中非自發(fā)晶核較少,導(dǎo)致采用電解鋁液直接鑄軋制備雙零箔坯料難度更大,鑄軋板中經(jīng)常有夾雜、氣道、晶粒粗大、表面條紋等缺陷。但與熱軋坯料相比,鑄軋坯料具有流程短、成本低、軋制超薄鋁箔時針孔度少等一系列優(yōu)點。鑒于此,本申請的發(fā)明人通過對現(xiàn)有制備8079合金雙零箔的鑄軋技術(shù)進行積極探索,旨在解決現(xiàn)有技術(shù)中的缺陷,以期得到晶粒細(xì)小、表面質(zhì)量好的8079合金雙零箔坯料。為此,在本發(fā)明的一個方面,本發(fā)明提出了一種制備8079合金雙零箔坯料的方法。根據(jù)本發(fā)明的實施例,該方法包括:(1)將電解鋁液、含鋁物料、鐵劑和鋁-硅中間合金混合熔煉,以便得到鋁熔液;(2)將所述鋁熔液進行精煉和扒渣處理,以便得到精煉鋁液;(3)將所述精煉鋁液經(jīng)過保溫爐,采用惰性氣體對所述精煉鋁液進行除氣處理,以便得到低含渣量、低含氣量鋁溶液;(4)將所述低含渣量、含氣量鋁溶液經(jīng)過生產(chǎn)流槽,進行在線除氣凈化、在線晶粒細(xì)化及非傳統(tǒng)過濾箱過濾,以便得到最終鋁液;(5)將所述最終鋁液通過鑄軋工藝,以便得到8079鋁合金雙零箔坯料。由此,根據(jù)本發(fā)明實施例的制備8079合金雙零箔坯料的方法通過將電解鋁液、含鋁物料、鐵劑和鋁-硅中間合金混合熔煉,有利于得到符合8079合金的鋁熔液;通過將鋁熔液進行精煉和扒渣,可去除鋁熔液中的雜質(zhì),同時有利于細(xì)化晶粒;在除氣的過程中,惰性氣體對精煉鋁液起到保護作用,一方面可除去精煉鋁液中的氫,一方面可防止精煉鋁液被空氣污染;細(xì)化劑的加入可使得鋁溶液生成大量異質(zhì)晶核,有利于在整個鋁溶液內(nèi)部同時成核,形成細(xì)小的近似等軸晶的細(xì)晶粒組織,原來的粗大柱狀晶組織消失。該方法可使得生產(chǎn)的8079合金雙零箔坯料的氫含量控制在0.1ml/100gal以下,ti吸收率達到85.75%~87.23%,鑄軋板晶粒達到1級(低倍晶粒度),鑄軋板表面質(zhì)量好且內(nèi)部組織均勻,8079合金雙零箔坯料軋制至0.0045㎜厚度時,針孔度小于100個/m2。另外,根據(jù)本發(fā)明上述實施例的制備8079合金雙零箔坯料的方法還可以具有如下附加的技術(shù)特征:在本發(fā)明的實施例中,在步驟(1)中,所述含鋁物料為選自鑄軋廢料、冷軋廢料和工業(yè)重熔用鋁錠中的至少之一。由此,有利于實現(xiàn)含鋁資源的回收再利用,降低原材料成本。在本發(fā)明的實施例中,在步驟(1)中,將所述電解鋁液、所述含鋁物料、所述鐵劑和所述鋁-硅中間合金按照質(zhì)量比為(65~75):(25~35):(5~8):(3~6)進行所述混合熔煉,由此,有利于得到成分合格的8079合金熔液。在本發(fā)明的實施例中,在步驟(1)中,當(dāng)所述含鋁物料為鑄軋廢料或冷軋廢料時,將所述電解鋁液、所述含鋁物料、所述鐵劑和所述鋁-硅中間合金按照質(zhì)量比為。(60~65):(35~40:(5~8):(3~6)進行所述混合熔煉。由此,有利于得到成分合格的8079合金熔液。在本發(fā)明的實施例中,在步驟(1)中,當(dāng)所述含鋁物料為工業(yè)重熔用鋁錠時,將所述電解鋁液、所述含鋁物料、所述鐵劑和所述鋁-硅中間合金按照質(zhì)量比為(65~70):(25~30):(5~8):(3~6)進行所述混合熔煉。由此,有利于得到成分合格的8079合金熔液。在本發(fā)明的實施例中,步驟(2)是按照下列步驟進行的:(2-1)采用固態(tài)精煉劑對所述鋁熔液進行第一次精煉處理,以便得到第一次精煉熔液;(2-2)將所述第一次精煉熔液進行第一扒渣處理,以便得到第一鋁液;(2-3)采用氬氣和固態(tài)精煉劑對所述第一鋁液進行第二次精煉處理,以便得到第二精煉熔液;(2-4)將所述第二精煉熔液進行第二次扒渣處理,以便得到第二鋁液;(2-5)采用氬氣和二氯甲烷對所述第二鋁液進行第三次精煉處理,以便得到第三精煉熔液;(2-6)將所述第三精煉熔液進行第三扒渣處理,以便得到所述精煉鋁液。由此,有利于去除鋁熔液中的雜質(zhì)并細(xì)化晶粒。在本發(fā)明的實施例中,在步驟(2-1)中,基于20~23t的所述鋁熔液,所述固態(tài)精煉劑的加入量為3~3.5kg。由此,有利于去除鋁熔液中的氫和浮游的氧化夾渣。在本發(fā)明的實施例中,在步驟(2-3)中,所述氬氣的壓力為5~10mpa,并且基于20~23t的所述第一鋁液,所述固態(tài)精煉劑的加入量為2~2.5kg。由此,可進一步去除鋁熔液的氫和浮游的氧化夾渣。在本發(fā)明的實施例中,在步驟(2-5)中,所述氬氣的壓力為5~10mpa,并且基于20~23t的所述第二鋁液,所述二氯甲烷的加入量為2~3kg。由此,可進一步去除鋁熔液的氫和浮游的氧化夾渣。在本發(fā)明的實施例中,在步驟(3)中,所述惰性氣體的流量為2.5~3.0m3/h,所述惰性氣體的氣泡高度為3-5mm。由此,有利于去除精煉鋁液中的氫氣。在本發(fā)明的實施例中,在步驟(3)中,所述除氣鋁液中氫氣含量為不高于0.10ml/100g鋁。由此,可顯著提高8079合金雙零箔坯料的表面質(zhì)量。在本發(fā)明的實施例中,在步驟(4)中,所述細(xì)化劑為鋁鈦硼絲細(xì)化劑。由此,有利于細(xì)化8079合金雙零箔坯料的晶粒。在本發(fā)明的實施例中,在步驟(4)中,基于1t所述鋁溶液,所述細(xì)化劑的加入量為2~3kg。由此,可進一步細(xì)化8079合金雙零箔坯料的晶粒。在本發(fā)明的實施例中,在步驟(5)中,所述鑄軋過程中前箱溫度為695±3攝氏度。由此,可進一步細(xì)化8079合金雙零箔坯料的晶粒。在本發(fā)明的實施例中,在步驟(5)中,所述鑄軋?zhí)幚淼乃俣葹?50-900mm/min。由此,可進一步細(xì)化8079合金雙零箔坯料的晶粒。在本發(fā)明的實施例中,在步驟(5)中,所述鑄軋區(qū)長度為67~74mm。由此,可進一步細(xì)化8079合金雙零箔坯料的晶粒。在本發(fā)明的再一個方面,本發(fā)明提出了一種8079合金雙零箔坯料,所述8079合金雙零箔坯料是采用上述制備8079合金雙零箔坯料的方法制備得到的。由此,可獲得表面質(zhì)量好且內(nèi)部組織均勻的8079合金雙零箔坯料。在本發(fā)明的又一個方面,本發(fā)明提出了一種8079合金雙零箔,所述8079合金雙零箔是采用上述制備8079合金雙零箔坯料的方法制備得到的。由此,可獲得表面質(zhì)量好且內(nèi)部組織均勻的8079合金雙零箔。本發(fā)明的附加方面和優(yōu)點將在下面的描述中部分給出,部分將從下面的描述中變得明顯,或通過本發(fā)明的實踐了解到。附圖說明本發(fā)明的上述和/或附加的方面和優(yōu)點從結(jié)合下面附圖對實施例的描述中將變得明顯和容易理解,其中:圖1是根據(jù)本發(fā)明一個實施例的制備8079合金雙零箔坯料的方法流程示意圖;圖2是根據(jù)本發(fā)明再一個實施例的制備8079合金雙零箔坯料的方法流程示意圖。具體實施方式下面詳細(xì)描述本發(fā)明的實施例,所述實施例的示例在附圖中示出,其中自始至終相同或類似的標(biāo)號表示相同或類似的元件或具有相同或類似功能的元件。下面通過參考附圖描述的實施例是示例性的,旨在用于解釋本發(fā)明,而不能理解為對本發(fā)明的限制。此外,術(shù)語“第一”、“第二”僅用于描述目的,而不能理解為指示或暗示相對重要性或者隱含指明所指示的技術(shù)特征的數(shù)量。由此,限定有“第一”、“第二”的特征可以明示或者隱含地包括至少一個該特征。在本發(fā)明的描述中,“多個”的含義是至少兩個,例如兩個,三個等,除非另有明確具體的限定。在本發(fā)明的一個方面,本發(fā)明提出了一種制備8079合金雙零箔坯料的方法。根據(jù)本發(fā)明的實施例,該方法包括:(1)將電解鋁液、含鋁物料、鐵劑和鋁-硅中間合金混合熔煉,以便得到鋁熔液;(2)將鋁熔液進行精煉和扒渣處理,以便得到精煉鋁液;(3)將精煉鋁液經(jīng)過保溫爐,采用惰性氣體對精煉鋁液進行除氣處理,以便得到低含渣量、低含氣量鋁溶液;(4)將低含渣量、含氣量鋁溶液經(jīng)過生產(chǎn)流槽,進行在線除氣凈化、在線晶粒細(xì)化及非傳統(tǒng)過濾箱過濾,以便得到最終鋁液;(5)將最終鋁液通過鑄軋工藝,以便得到8079鋁合金雙零箔坯料。由此,根據(jù)本發(fā)明實施例的制備8079合金雙零箔坯料的方法通過將電解鋁液、含鋁物料、鐵劑和鋁-硅中間合金混合熔煉,有利于得到符合8079合金的鋁熔液;通過將鋁熔液進行精煉和扒渣,可去除鋁熔液中的雜質(zhì),同時有利于細(xì)化晶粒;在除氣的過程中,惰性氣體對精煉鋁液起到保護作用,一方面可除去精煉鋁液中的氫,一方面可防止精煉鋁液被空氣污染;細(xì)化劑的加入可使得鋁溶液生成大量異質(zhì)晶核,有利于在整個鋁溶液內(nèi)部同時成核,形成細(xì)小的近似等軸晶的細(xì)晶粒組織,原來的粗大柱狀晶組織消失。該方法可使得生產(chǎn)的8079合金雙零箔坯料的氫含量控制在0.1ml/100gal以下,ti吸收率達到85.75%~87.23%,鑄軋板晶粒達到1級(低倍晶粒度),鑄軋板表面質(zhì)量好且內(nèi)部組織均勻,8079合金雙零箔坯料軋制至0.0045㎜厚度時,針孔度小于100個/m2。下面參考圖1對本發(fā)明實施例的制備8079合金雙零箔坯料的方法進行詳細(xì)描述。根據(jù)本發(fā)明的實施例,該方法包括:s100:將電解鋁液、含鋁物料、鐵劑和鋁-硅中間合金混合熔煉該步驟中,將電解鋁液、含鋁物料、鐵劑和鋁-硅中間合金混合熔煉,以便得到鋁熔液。由此,有利于得到符合8079合金的鋁熔液。發(fā)明人發(fā)現(xiàn),在制備8079合金雙零箔坯料時,化學(xué)成分需嚴(yán)格按照8079合金執(zhí)行。8079合金的化學(xué)成分為:1.1wt%~1.3wt%fe,0.05wt%~0.08wt%si,0.02wt%cu,0.05wt%zn,0.035wt%ti,余量的鋁。通過在電解鋁液中加入一定比列的含鋁物料、鐵劑和鋁-硅中間合金,通過熔煉工藝,可得到符合8079合金成分的鋁熔液。其中,鋁-硅中間合金的具體組成為:11wt%~13wt%si,0.03wt%cu,0.03wt%zn,0.03wt%ti,0.01wt%mn,0.01wt%mg,al余量。根據(jù)本發(fā)明的一個實施例,含鋁物料并不受特別限制,本領(lǐng)域技術(shù)人員可以根據(jù)實際需要進行選擇,根據(jù)本發(fā)明的一個具體實施例,含鋁物料可以為選自鑄軋廢料、冷軋廢料和工業(yè)重熔用鋁錠中的至少之一。由此,有利于實現(xiàn)含鋁資源的回收再利用,降低原材料成本。根據(jù)本發(fā)明的再一個實施例,電解鋁液、含鋁物料、鐵劑和鋁-硅中間合金的混合質(zhì)量比為:(65~75):(25~35):(5~8):(3~6)。發(fā)明人發(fā)現(xiàn),電解鋁液、含鋁物料、鐵劑和鋁-硅中間合金的質(zhì)量比必須嚴(yán)格按照上述質(zhì)量比,各組分含量過高或過低,都將直接影響8079合金雙零箔坯料內(nèi)部的晶粒組織。根據(jù)本發(fā)明的又一個實施例,當(dāng)含鋁物料為鑄軋廢料或冷軋廢料時,電解鋁液、含鋁物料、鐵劑和鋁-硅中間合金的混合質(zhì)量比為(60~65):(35~40):(5~8):(3~6)。發(fā)明人發(fā)現(xiàn),電解鋁液、含鋁物料、鐵劑和鋁-硅中間合金的質(zhì)量比必須嚴(yán)格按照上述質(zhì)量比,各組分含量過高或過低,都將直接影響8079合金雙零箔坯料內(nèi)部的晶粒組織。根據(jù)本發(fā)明的又一個實施例,當(dāng)含鋁物料為工業(yè)重熔用鋁錠時,電解鋁液、含鋁物料、鐵劑和鋁-硅中間合金的混合質(zhì)量比為(65~70):(25~30):(5~8):(3~6)進行混合熔煉。發(fā)明人發(fā)現(xiàn),電解鋁液、含鋁物料、鐵劑和鋁-硅中間合金的質(zhì)量比必須嚴(yán)格按照上述質(zhì)量比,各組分含量過高或過低,都將直接影響8079合金雙零箔坯料內(nèi)部的晶粒組織。且只有當(dāng)工業(yè)重熔用鋁錠的質(zhì)量比為上述比例時,才能有效提高8079合金雙零鋁箔的內(nèi)部質(zhì)量。s200:將鋁熔液進行精煉和扒渣處理該步驟中,將鋁熔液進行精煉和扒渣處理,以便得到精煉鋁液。由此,可去除鋁熔液中的雜質(zhì),同時有利于細(xì)化晶粒。參考圖2,根據(jù)本發(fā)明的實施例,s200是按照下列步驟進行的:s21:采用固態(tài)精煉劑對鋁熔液進行第一精煉處理該步驟中,采用固態(tài)精煉劑對鋁熔液進行第一精煉處理,以便得到第一精煉熔液。由此,有利于細(xì)化晶粒。根據(jù)本發(fā)明的一個實施例,固態(tài)精煉劑的加入量并不受特別限制,本領(lǐng)域技術(shù)人員可以根據(jù)實際需要進行選擇,根據(jù)本發(fā)明的一個具體實施例,基于20~23t的鋁熔液,固態(tài)精煉劑的加入量可以為3~3.5kg。發(fā)明人發(fā)現(xiàn),固態(tài)精煉劑的加入量過高過低都會直接影響鋁熔液精煉效果。s22:將第一精煉熔液進行第一扒渣處理該步驟中,將第一精煉熔液進行第一扒渣處理,以便得到第一鋁液和第一浮渣。由此,可去除第一精煉熔液中的雜質(zhì)。s23:采用氬氣和固態(tài)精煉劑對第一鋁液進行第二精煉處理該步驟中,采用氬氣和固態(tài)精煉劑對第一鋁液進行第二精煉處理,以便得到第二精煉熔液。由此,可進一步細(xì)化晶粒。根據(jù)本發(fā)明的一個實施例,氬氣的壓力和固態(tài)精煉劑的加入量并不受特別限制,本領(lǐng)域技術(shù)人員可以根據(jù)實際需要進行選擇,根據(jù)本發(fā)明的一個具體實施例,氬氣的壓力可以為5~10mpa,并且基于20~23t的第一鋁液,固態(tài)精煉劑的加入量可以為2~2.5kg。發(fā)明人發(fā)現(xiàn),氬氣的壓力以及固態(tài)精煉劑的加入量過高過低都會對第一鋁液的精煉效果產(chǎn)生巨大的影響。經(jīng)過第一次精煉后,第一鋁液在第二次精煉時,固態(tài)精煉劑的加入量必須嚴(yán)格控制,才能達到有效減少第一鋁液的含氣和含渣量,從而達到精煉效果。s24:將第二精煉熔液進行第二扒渣處理該步驟中,將第二精煉熔液進行第二扒渣處理,以便得到第二鋁液和第二浮渣。由此,可去除第二精煉熔液中的雜質(zhì)。s25:采用氬氣和二氯甲烷對第二鋁液進行第三精煉處理該步驟中,采用氬氣和二氯甲烷對第二鋁液進行第三精煉處理,以便得到第三精煉熔液。由此,可進一步細(xì)化晶粒。根據(jù)本發(fā)明的一個實施例,氬氣的壓力和二氯甲烷的加入量并不受特別限制,本領(lǐng)域技術(shù)人員可以根據(jù)實際需要進行選擇,根據(jù)本發(fā)明的一個具體實施例,氬氣的壓力可以為5~10mpa,并且基于20~23t的第二鋁液,二氯甲烷的加入量可以為2~3kg。發(fā)明人發(fā)現(xiàn),氬氣的壓力和二氯甲烷的加入量過高或過低都會直接影響鋁液的精煉效果,從而無法滿足后續(xù)生產(chǎn)。s26:將第三精煉熔液進行第三扒渣處理該步驟中,將第三精煉熔液進行第三扒渣處理,以便得到精煉鋁液和第三浮渣。由此,可去除第三精煉熔液中的雜質(zhì)。具體的,在鋁熔液進行精煉的過程中,采用3次扒渣工藝。當(dāng)鋁熔液溫度達到700~710攝氏度時,基于20~23t的鋁熔液,加入3~3.5kg固態(tài)精煉劑,進行第一精煉處理,得到第一精煉熔液,精煉3h后,進行第一扒渣處理,去除鋁熔液表面的浮渣,得到第一鋁液和第一浮渣。然后進行合金配制,使得合金的成分落在8079合金成分內(nèi)。接著采用氬氣和固態(tài)精煉劑對第一鋁液進行第二精煉處理,得到第二精煉熔液。其中氬氣壓力控制在5~10mpa,基于20~23t的第一鋁液,固態(tài)精煉劑加入量為2~2.5kg,精煉時間為12min。第二精煉熔液靜置5min后,對第二精煉熔液進行第二扒渣處理,得到第二鋁液和第二浮渣。根據(jù)前箱溫度需要,控制熔煉爐轉(zhuǎn)爐溫度,并將熔煉爐中的第二鋁液靜置30min后轉(zhuǎn)爐。靜置爐轉(zhuǎn)爐1h后,采用氬氣和二氯甲烷對第二鋁液進行第三精煉處理,氬氣壓力控制在5~10mpa,基于20~23t的第二鋁液,二氯甲烷的加入量為2~3kg,并進行第三扒渣處理,靜置爐第二鋁液溫度控制在750~755攝氏度。s300:將精煉鋁液經(jīng)過保溫爐,采用惰性氣體對精煉鋁液進行除氣處理該步驟中,將精煉鋁液經(jīng)過保溫爐,采用惰性氣體對精煉鋁液進行除氣處理,以便得到低含渣量、低含氣量鋁溶液;由此,有利于凈化精煉鋁液。具體的,將精煉鋁液經(jīng)過保溫爐,采用惰性氣體對精煉鋁液進行除氣處理,精煉鋁液流經(jīng)除氣箱,除氣箱惰性氣體流量設(shè)置在2.5~3.0m3/h,氣泡高度控制在3~5mm,得到氫含量控制在0.10ml/100g鋁以下的低含渣量、低含氣量鋁溶液。根據(jù)本發(fā)明的一個實施例,惰性氣體的流量為2.5~3.0m3/h,惰性氣體的氣泡高度可以為3-5mm。發(fā)明人發(fā)現(xiàn),惰性氣體的流量和惰性氣體的氣泡高度過高或過低直接影響精煉鋁液的除氣效果。需要說明的是,惰性氣體并不受特別限制,本領(lǐng)域技術(shù)人員可以根據(jù)實際需要進行選擇,例如可以為氮氣和氬氣等。根據(jù)本發(fā)明的再一個實施例,除氣鋁液中氫氣的含量為不高于0.10ml/100g鋁。發(fā)明人發(fā)現(xiàn),除氣鋁液中氫氣的含量過高將使8079雙零箔坯料針孔超標(biāo),無法滿足后續(xù)使用。s400:將低含渣量、含氣量鋁溶液經(jīng)過生產(chǎn)流槽,進行在線除氣凈化、在線晶粒細(xì)化及非傳統(tǒng)過濾箱過濾該步驟中,將低含渣量、含氣量鋁溶液經(jīng)過生產(chǎn)流槽,進行在線除氣凈化、在線晶粒細(xì)化及非傳統(tǒng)過濾箱過濾,以便得到最終鋁液。具體的,在除氣箱的入口逆向加入細(xì)化劑,加入時鋁溶液的溫度為720~730攝氏度,基于1t的鋁溶液,細(xì)化劑的加入量為2~3kg,優(yōu)選2.5kg,細(xì)化劑的添加點至前箱的距離為2m,可使ti的吸收率達到85.75%~87.23%,可使得后續(xù)8079合金雙零箔坯料的晶粒更加細(xì)密均勻,且為1級晶粒。鋁溶液流經(jīng)過濾箱時,采用非傳統(tǒng)過濾方式,使鋁溶液從下至上,先后經(jīng)過2級陶瓷過濾板,陶瓷板上板面采用60ppi,下板面采用30ppi,有效去除夾雜。根據(jù)本發(fā)明的再一個實施例,細(xì)化劑的加入量并不受特別限制,本領(lǐng)域技術(shù)人員可以根據(jù)實際需要進行選擇,根據(jù)本發(fā)明的一個具體實施例,基于20~23t的鋁溶液,細(xì)化劑的加入量可以為2~3kg,優(yōu)選2.5kg。發(fā)明人發(fā)現(xiàn),細(xì)化劑加入量過高或過低直接影響8079雙零箔坯料的內(nèi)部組織和表面質(zhì)量。需要說明是,細(xì)化劑為鋁鈦硼絲細(xì)化劑。s500:將最終鋁液進行鑄軋?zhí)幚碓摬襟E中,將最終鋁液通過鑄軋工藝,以便得到8079鋁合金雙零箔坯料。具體的,鑄軋過程中前箱最終鋁液溫度控制在695±3攝氏度,鑄軋?zhí)幚淼乃俣葹?50-900mm/min,鑄軋區(qū)長度為67~74mm,前箱液面波動控制在±0.1mm范圍內(nèi),從而保證得到的8079合金雙零箔坯料具有細(xì)密的內(nèi)部組織和良好的表面質(zhì)量。發(fā)明人發(fā)現(xiàn),當(dāng)鑄軋速度與冷卻強度不變時,如果前箱鋁液溫度過高,將造成結(jié)晶前沿前面的熔體溫度梯度增大,液相過冷度變小,形核率降低而長大速度提高,有利于胞狀晶生長,因而表面晶粒粗大。當(dāng)其它條件不變時,如果提高鑄軋速度,將增大鑄造區(qū),使液穴加長,而變形區(qū)變短,造成結(jié)晶前沿前面的熔體溫度梯度增大,液相過冷度變小,形核率降低而長大速度提高,因而晶粒粗大。當(dāng)其它條件不變時,在保證鑄軋正常生產(chǎn)前提下,如果前箱液面過低,會導(dǎo)致熔體靜壓力較小,鑄軋區(qū)上表面熔體與鑄軋輥接觸不充分,傳熱條件差,冷卻速度慢,上表面結(jié)晶前沿溫度梯度加大,該處液相過冷度變小,易使鑄軋帶坯上表面形成粗大晶粒。冷卻水的溫度、壓力和流量,鑄軋輥套厚度及其導(dǎo)熱性能均對冷卻強度產(chǎn)生影響。如果冷卻水溫度偏高、水壓較低或輥套過厚,會使冷卻強度降低,使鋁熔體液相過冷度變小,形核率降低,凝固時間增加,從而易使鑄軋帶坯表面產(chǎn)生粗大晶粒。在鑄軋輥徑和輥縫一定時,鑄軋區(qū)越長,進入到鑄軋區(qū)內(nèi)的鋁熔體越多,需要帶走的熱量也越多。如果冷卻強度、軋制速度等工藝參數(shù)不變時,則會導(dǎo)致輥套溫度上升,熔體過冷度變小,易使晶粒粗大。根據(jù)本發(fā)明的一個實施例,鑄軋過程中前箱鋁液的溫度為695±3攝氏度。發(fā)明人發(fā)現(xiàn),當(dāng)鑄軋速度與冷卻強度不變時,如果前箱鋁液溫度過高,將造成結(jié)晶前沿前面的熔體溫度梯度增大,液相過冷度變小,形核率降低而長大速度提高,有利于胞狀晶生長,因而表面晶粒粗大。根據(jù)本發(fā)明的再一個實施例,鑄軋?zhí)幚淼乃俣葹?50-900mm/min。發(fā)明人發(fā)現(xiàn),當(dāng)其它條件不變時,如果提高鑄軋?zhí)幚淼乃俣?,將增大鑄造區(qū),使液穴加長,而變形區(qū)變短,造成結(jié)晶前沿前面的熔體溫度梯度增大,液相過冷度變小,形核率降低而長大速度提高,因而晶粒粗大。根據(jù)本發(fā)明的又一個實施例,鑄軋區(qū)長度可以為67~74mm。發(fā)明人發(fā)現(xiàn),在鑄軋輥徑和輥縫一定時,鑄軋區(qū)越長,進入到鑄軋區(qū)內(nèi)的鋁熔體越多,需要帶走的熱量也越多。如果冷卻強度、軋制速度等工藝參數(shù)不變時,則會導(dǎo)致輥套溫度上升,熔體過冷度變小,易使晶粒粗大。在本發(fā)明的再一個方面,本發(fā)明提出了一種8079合金雙零箔坯料,根據(jù)本發(fā)明的實施例,上述8079合金雙零箔坯料是采用上述制備8079合金雙零箔坯料的方法制備得到的。由此,可獲得表面質(zhì)量好內(nèi)部組織均勻的8079合金雙零箔坯料。在本發(fā)明的又一個方面,本發(fā)明提出了一種8079合金雙零箔,根據(jù)本發(fā)明的實施例,上述8079合金雙零箔是上述制備8079合金雙零箔坯料的方法制備得到的8079合金雙零箔坯料制備得到的。由此,可獲得表面質(zhì)量好內(nèi)部組織均勻的8079合金雙零箔。下面參考具體實施例,對本發(fā)明進行描述,需要說明的是,這些實施例僅僅是描述性的,而不以任何方式限制本發(fā)明。實施例18079合金的化學(xué)成分及重量百分比如表1所示。表18079合金的化學(xué)成分及重量百分比合金fe(wt%)si(wt%)cu(wt%)zn(wt%)mn(wt%)ti(wt%)al(wt%)80791.20.060.020.05-0.035余量將電解鋁液、8079鑄軋廢料、鐵劑和鋁-硅中間合金按照質(zhì)量比65:35:6:4合熔煉,得到鋁熔液。在鋁熔液進行精煉的過程中,采用3次扒渣工藝。當(dāng)鋁熔液溫度達到700攝氏度時,基于20~23t的鋁熔液,加入3kg固態(tài)精煉劑,進行第一精煉處理,得到第一精煉熔液,精煉3h后,進行第一扒渣處理,去除鋁熔液表面的浮渣,得到第一鋁液和第一浮渣。然后進行合金配制,使得合金的成分落在8079合金成分內(nèi)。接著采用氬氣和固態(tài)精煉劑對第一鋁液進行第二精煉處理,得到第二精煉熔液。其中氬氣壓力控制在6mpa,基于20~23t的第一鋁液,固態(tài)精煉劑加入量為2kg,精煉時間為12min。鋁熔液靜置5min后,對第二精煉熔液進行第二扒渣處理,得到第二鋁液和第二浮渣。根據(jù)前箱溫度需要,控制熔煉爐轉(zhuǎn)爐溫度,并將熔煉爐鋁液靜置30min后轉(zhuǎn)爐。靜置爐轉(zhuǎn)爐1h后,采用氬氣和二氯甲烷對第二鋁液進行第三精煉處理,氬氣壓力控制在6mpa,基于20~23t的第二鋁液,二氯甲烷的加入量為2.5kg,并進行第三扒渣處理,得到精煉鋁液和浮渣。靜置爐鋁液溫度控制在750攝氏度。將精煉鋁液經(jīng)過保溫爐,采用惰性氣體對精煉鋁液進行除氣處理,精煉鋁液流經(jīng)除氣箱,除氣箱惰性氣體流量設(shè)置在2.5m3/h,氣泡高度控制在3mm,得到低含渣量、低含氣量鋁溶液。在除氣箱的入口逆向加入鋁鈦硼絲細(xì)化劑,加入時鋁溶液的溫度為720攝氏度,基于1t的鋁溶液,鋁鈦硼絲細(xì)化劑的加入量為2.5kg,鋁鈦硼絲細(xì)化劑的添加點至前箱的距離為2m,可使ti的吸收率達到85.75%,鋁溶液流經(jīng)過濾箱時,采用非傳統(tǒng)過濾方式,使鋁溶液從下至上,先后經(jīng)過2級陶瓷過濾板,陶瓷板上板面采用60ppi,下板面采用30ppi,有效去除夾雜,得到最終鋁液。鑄軋過程中前箱最終鋁液溫度控制在695攝氏度,鑄軋?zhí)幚淼乃俣葹?60mm/min,鑄軋區(qū)長度為67mm,前箱液面波動控制在±0.1mm范圍內(nèi),最終鋁液經(jīng)鑄軋?zhí)幚恚玫?079鋁合金雙零箔坯料。生產(chǎn)的8079合金雙零箔坯料鑄軋板滿足:氫含量為0.1ml/100g鋁,鑄軋板晶粒更加細(xì)密均勻,達到1級晶粒,鑄軋板表面條紋少,且8079合金雙零箔坯料軋制至0.0045㎜時,針孔度為100個/m2。實施例28079合金的化學(xué)成分及重量百分比如表2所示。表28079合金的化學(xué)成分及重量百分比合金fe(wt%)si(wt%)cu(wt%)zn(wt%)mn(wt%)ti(wt%)al(wt%)80791.10.050.020.05-0.035余量將電解鋁液、8079鑄軋廢料、鐵劑和鋁-硅中間合金按照質(zhì)量比60:35:5:4混合熔煉,得到鋁熔液。在鋁熔液進行精煉的過程中,采用3次扒渣工藝。當(dāng)鋁熔液溫度達到705攝氏度時,基于20~23t的鋁熔液,加入3.2kg固態(tài)精煉劑,進行第一精煉處理,得到第一精煉熔液,精煉3h后,進行第一扒渣處理,去除鋁熔液表面的浮渣,得到第一鋁液和第一浮渣。然后進行合金配制,使得合金的成分落在8079合金成分內(nèi)。接著采用氬氣和固態(tài)精煉劑對第一鋁液進行第二精煉處理,得到第二精煉熔液。其中氬氣壓力控制在8mpa,基于20~23t的第一鋁液,固態(tài)精煉劑加入量為2.2kg,精煉時間為12min。鋁熔液靜置5min后,對第二精煉熔液進行第二扒渣處理,得到第二鋁液和第二浮渣。根據(jù)前箱溫度需要,控制熔煉爐轉(zhuǎn)爐溫度,并將熔煉爐鋁液靜置30min后轉(zhuǎn)爐。靜置爐轉(zhuǎn)爐1h后,采用氬氣和二氯甲烷對第二鋁液進行第三精煉處理,氬氣壓力控制在8mpa,基于20~23t的第二鋁液,二氯甲烷的加入量為2.5kg,并進行第三扒渣處理,靜置爐鋁液溫度控制在753攝氏度。將精煉鋁液經(jīng)過保溫爐,采用惰性氣體對精煉鋁液進行除氣處理,精煉鋁液流經(jīng)除氣箱,除氣箱惰性氣體流量設(shè)置在2.8m3/h,氣泡高度控制在4mm,得到低含渣量、低含氣量鋁溶液。在除氣箱的入口逆向加入鋁鈦硼絲細(xì)化劑,加入時鋁溶液的溫度為725攝氏度,基于1t的鋁溶液,鋁鈦硼絲細(xì)化劑的加入量為2.5kg,鋁鈦硼絲細(xì)化劑的添加點至前箱的距離為2m,可使ti的吸收率達到86.0%。鋁溶液流經(jīng)過濾箱時,采用非傳統(tǒng)過濾方式,使鋁溶液從下至上,先后經(jīng)過2級陶瓷過濾板,陶瓷板上板面采用60ppi,下板面采用30ppi。鑄軋過程中前箱最終鋁液溫度控制在696攝氏度,鑄軋?zhí)幚淼乃俣葹?70mm/min,鑄軋區(qū)長度為70mm,前箱液面波動控制在±0.1mm范圍內(nèi),最終鋁液經(jīng)鑄軋?zhí)幚?,得?079鋁合金雙零箔坯料。生產(chǎn)的8079合金雙零箔坯料鑄軋板滿足:氫含量為0.098ml/100g鋁,鑄軋板晶粒達到1級晶粒,鑄軋板表面條紋少,且8079合金雙零箔坯料軋制至0.0045㎜時,針孔度為98個/m2。實施例38079合金的化學(xué)成分及重量百分比如表1所示。表18079合金的化學(xué)成分及重量百分比合金fe(wt%)si(wt%)cu(wt%)zn(wt%)mn(wt%)ti(wt%)al(wt%)80791.30.070.020.05-0.035余量將電解鋁液、工業(yè)重熔用鋁錠、鐵劑和鋁-硅中間合金按照質(zhì)量比65:25:6:3混合熔煉,得到鋁熔液。在鋁熔液進行精煉的過程中,采用3次扒渣工藝。當(dāng)鋁熔液溫度達到710攝氏度時,基于20~23t的鋁熔液,加入3.5kg固態(tài)精煉劑,進行第一精煉處理,得到第一精煉熔液,精煉3h后,進行第一扒渣處理,去除鋁熔液表面的浮渣,得到第一鋁液和第一浮渣。然后進行合金配制,使得合金的成分落在8079合金成分內(nèi)。接著采用氬氣和固態(tài)精煉劑對第一鋁液進行第二精煉處理,得到第二精煉熔液。其中氬氣壓力控制在10mpa,基于20~23t的第一鋁液,固態(tài)精煉劑加入量為2.5kg,精煉時間為12min。鋁熔液靜置5min后,對第二精煉熔液進行第二扒渣處理,得到第二鋁液和第二浮渣。根據(jù)前箱溫度需要,控制熔煉爐轉(zhuǎn)爐溫度,并將熔煉爐鋁液靜置30min后轉(zhuǎn)爐。靜置爐轉(zhuǎn)爐1h后,采用氬氣和二氯甲烷對第二鋁液進行第三精煉處理,氬氣壓力控制在10mpa,基于20~23t的第二鋁液,二氯甲烷的加入量為2.5kg,并進行第三扒渣處理,靜置爐鋁液溫度控制在755攝氏度。將精煉鋁液經(jīng)過保溫爐,采用惰性氣體對精煉鋁液進行除氣處理,精煉鋁液流經(jīng)除氣箱,除氣箱惰性氣體流量設(shè)置在3m3/h,氣泡高度控制在5mm,得到低含渣量、低含氣量鋁溶液。在除氣箱的入口逆向加入鋁鈦硼絲細(xì)化劑,加入時鋁溶液的溫度為730攝氏度,基于1t的鋁溶液,鋁鈦硼絲細(xì)化劑的加入量為2.5kg,鋁鈦硼絲細(xì)化劑的添加點至前箱的距離為2m,可使ti的吸收率達到87.0%,鋁溶液流經(jīng)過濾箱時,采用非傳統(tǒng)過濾方式,使鋁溶液從下至上,先后經(jīng)過2級陶瓷過濾板,陶瓷板上板面采用60ppi,下板面采用30ppi,有效去除夾雜。鑄軋過程中前箱鋁液溫度控制在698攝氏度,鑄軋?zhí)幚淼乃俣葹?90mm/min,鑄軋區(qū)長度為72mm,前箱液面波動控制在±0.1mm范圍內(nèi),最終鋁液經(jīng)鑄軋?zhí)幚?,得?079鋁合金雙零箔坯料。生產(chǎn)的8079合金雙零箔坯料鑄軋板滿足:氫含量為0.01ml/100g鋁,鑄軋板晶粒更加細(xì)密均勻,達到1級晶粒,鑄軋板表面條紋少,且8079合金雙零箔坯料軋制至0.0045㎜時,針孔度為100個/m2。在本說明書的描述中,參考術(shù)語“一個實施例”、“一些實施例”、“示例”、“具體示例”、或“一些示例”等的描述意指結(jié)合該實施例或示例描述的具體特征、結(jié)構(gòu)、材料或者特點包含于本發(fā)明的至少一個實施例或示例中。在本說明書中,對上述術(shù)語的示意性表述不必須針對的是相同的實施例或示例。而且,描述的具體特征、結(jié)構(gòu)、材料或者特點可以在任一個或多個實施例或示例中以合適的方式結(jié)合。此外,在不相互矛盾的情況下,本領(lǐng)域的技術(shù)人員可以將本說明書中描述的不同實施例或示例以及不同實施例或示例的特征進行結(jié)合和組合。盡管上面已經(jīng)示出和描述了本發(fā)明的實施例,可以理解的是,上述實施例是示例性的,不能理解為對本發(fā)明的限制,本領(lǐng)域的普通技術(shù)人員在本發(fā)明的范圍內(nèi)可以對上述實施例進行變化、修改、替換和變型。當(dāng)前第1頁12