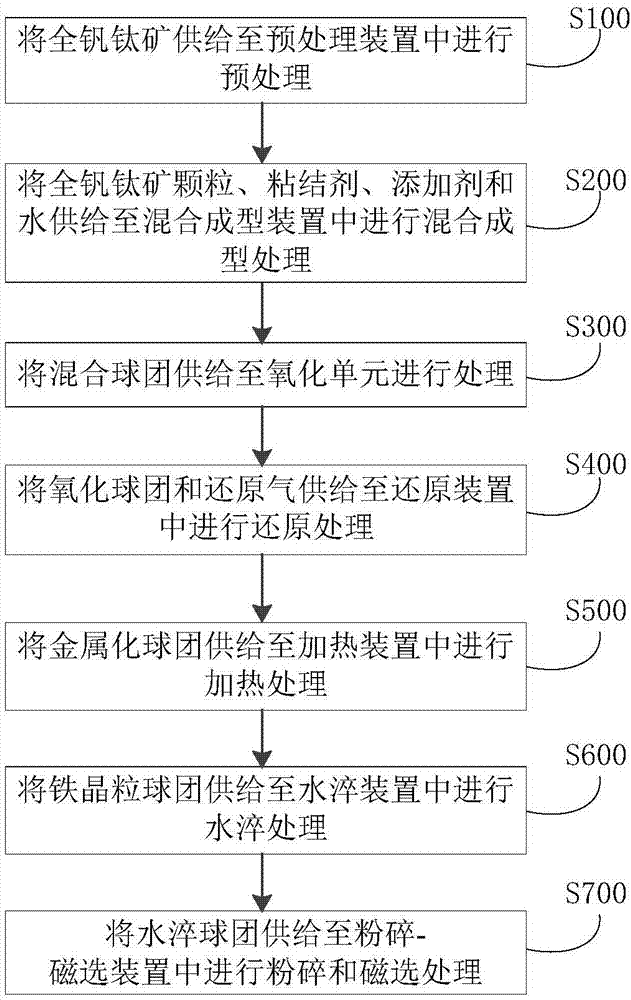
本發(fā)明屬于冶金
技術(shù)領(lǐng)域:
,具體而言,本發(fā)明涉及全釩鈦礦直接還原-磁選的系統(tǒng)和方法。
背景技術(shù):
:釩鈦礦作為一種復(fù)合鐵礦資源,具有極高的綜合利用價(jià)值,如何用好釩鈦礦,發(fā)揮資源的最大優(yōu)勢,全面回收鐵釩鈦一直是冶金界科研工作者努力的目標(biāo)。傳統(tǒng)高爐流程以及國外非高爐流程冶煉釩鈦礦,只回收了鐵和釩,鈦進(jìn)入高爐渣,由于鈦品位太低暫無經(jīng)濟(jì)合理的回收價(jià)值,造成鈦資源的大量流失。相關(guān)
技術(shù)領(lǐng)域:
中,利用煤粉、焦粉等顆粒作為還原劑直接與釩鈦礦顆粒混合制備球團(tuán)并進(jìn)行氧化、還原等處理,會因帶入灰分而影響高鈦爐渣二氧化鈦的富集,降低二氧化鈦品位。此外,現(xiàn)有技術(shù)釩鈦礦直接還原-磁選工藝,細(xì)磨效率低、生產(chǎn)率低、產(chǎn)品中非磁性物中脈石含量高,增加了釩鈦回收的原材料成本和能量的消耗,同時(shí)晶粒長大過程透氣性差,易粘結(jié),晶粒長大時(shí)間長。因此,現(xiàn)有釩鈦礦的處理技術(shù)有待進(jìn)一步改進(jìn)。技術(shù)實(shí)現(xiàn)要素:本發(fā)明旨在至少在一定程度上解決相關(guān)技術(shù)中的技術(shù)問題之一。為此,本發(fā)明的一個(gè)目的在于提出一種全釩鈦礦直接還原-磁選的系統(tǒng)和方法,采用該系統(tǒng)粉碎-磁選成本低,設(shè)備作業(yè)率高,且所得的磁性物中鐵回收率達(dá)95wt%以上,所得的非磁性物中含鈦渣二氧化鈦的回收率達(dá)96wt%以上,釩進(jìn)渣97wt%以上。在本發(fā)明的一個(gè)方面,本發(fā)明提出了一種全釩鈦礦直接還原-磁選的系統(tǒng),根據(jù)本發(fā)明的實(shí)施例,所述系統(tǒng)包括:預(yù)處理裝置,預(yù)處理裝置具有全釩鈦礦入口和全釩鈦礦顆粒出口;混合成型裝置,混合成型裝置具有全釩鈦顆粒入口、粘結(jié)劑入口、添加劑入口、水入口和混合球團(tuán)出口,全釩鈦礦顆粒入口與全釩鈦礦顆粒出口相連;氧化單元,氧化單元具有混合球團(tuán)入口和氧化球團(tuán)出口,混合球團(tuán)入口與混合球團(tuán)出口相連;還原裝置,還原裝置具有氧化球團(tuán)入口、還原氣入口和金屬化球團(tuán)出口,氧化球團(tuán)入口與氧化球團(tuán)出口相連;加熱裝置,加熱裝置具有金屬化球團(tuán)入口和鐵晶粒球團(tuán)出口,金屬化球團(tuán)入口與金屬化球團(tuán)出口相連;水淬裝置,水淬裝置具有鐵晶粒球團(tuán)入口和水淬球團(tuán)出口,鐵晶粒球團(tuán)入口與鐵晶粒球團(tuán)出口相連;粉碎-磁選裝置,粉碎裝置具有水淬球團(tuán)入口、磁性物出口和非磁性物出口,水淬球團(tuán)入口與水淬球團(tuán)出口相連。由此,根據(jù)本發(fā)明實(shí)施例的全釩鈦礦直接還原-磁選的系統(tǒng)通過將全釩鈦礦送至預(yù)處理裝置進(jìn)行預(yù)處理得到全釩鈦礦顆粒,可顯著增加全釩鈦礦顆粒的比表面積,從而增加后續(xù)在混合成型裝置中全釩鈦礦顆粒與粘結(jié)劑、添加劑和水的接觸面積,使得全釩鈦礦顆粒與粘結(jié)劑、添加劑和水充分接觸,得到混合球團(tuán);混合球團(tuán)經(jīng)過氧化單元的氧化作用后混合球團(tuán)中的低價(jià)鐵、釩和鈦被充分氧化成高價(jià)鐵氧化物、高價(jià)釩氧化物和高價(jià)鈦氧化物,得到氧化球團(tuán);接著氧化球團(tuán)在還原裝置中的還原氣作用下發(fā)生還原反應(yīng),使得大多數(shù)高價(jià)鐵化合物還原為金屬鐵及少量浮士體,得到疏松多孔、透氣性好且熱交換效率高的金屬化球團(tuán),將金屬化球團(tuán)進(jìn)一步加熱處理,使得鐵晶粒進(jìn)一步長大,得到鐵晶粒長大后的金屬化球團(tuán),經(jīng)水淬處理后,金屬化球團(tuán)性能變脆,成為水淬球團(tuán),可顯著降低后續(xù)粉碎-磁選處理的成本。由此,采用該系統(tǒng)粉碎-磁選成本低,設(shè)備作業(yè)率高,且所得的磁性物中鐵回收率達(dá)95wt%以上,所得的非磁性物中含鈦渣二氧化鈦的回收率達(dá)96wt%以上,釩進(jìn)渣97wt%以上。另外,根據(jù)本發(fā)明上述實(shí)施例的全釩鈦礦直接還原-磁選的系統(tǒng)還可以具有如下附加的技術(shù)特征:在本發(fā)明的一些實(shí)施例中,所述氧化單元包括依次相連的干燥裝置、預(yù)熱裝置和焙燒裝置。由此,有利于混合球團(tuán)充分氧化,從而提高后續(xù)鐵、釩、鈦的回收率。在本發(fā)明的再一個(gè)方面,本發(fā)明還提出了一種采用上述全釩鈦礦直接還原-磁選的系統(tǒng)實(shí)施全釩鈦礦直接還原-磁選的方法。根據(jù)本發(fā)明的實(shí)施例,該方法包括:(1)將全釩鈦礦供給至所述預(yù)處理裝置中進(jìn)行預(yù)處理,以便得到全釩鈦礦顆粒;(2)將所述全釩鈦礦顆粒、粘結(jié)劑、添加劑和水供給至所述混合成型裝置中進(jìn)行混合成型處理,以便得到混合球團(tuán);(3)將所述混合球團(tuán)供給至所述氧化單元進(jìn)行處理,以便得到氧化球團(tuán);(4)將所述氧化球團(tuán)和還原氣供給至所述還原裝置中進(jìn)行還原處理,以便得到金屬化球團(tuán);(5)將所述金屬化球團(tuán)供給至加熱裝置中進(jìn)行加熱處理,以便得到鐵晶粒球團(tuán);(6)將所述鐵晶粒球團(tuán)供給至所述水淬裝置中進(jìn)行水淬處理,以便得到水淬球團(tuán);(7)將所述水淬球團(tuán)供給至所述粉碎-磁選裝置中進(jìn)行粉碎和磁選處理,以便得到磁性物和非磁性物。由此,根據(jù)本發(fā)明實(shí)施例的全釩鈦礦直接還原-磁選的方法通過將全釩鈦礦送至預(yù)處理裝置進(jìn)行預(yù)處理得到全釩鈦礦顆粒,可顯著增加全釩鈦礦顆粒的比表面積,從而增加后續(xù)在混合成型裝置中全釩鈦礦顆粒與粘結(jié)劑、添加劑和水的接觸面積,使得全釩鈦礦顆粒與粘結(jié)劑、添加劑和水充分接觸,得到混合球團(tuán);混合球團(tuán)經(jīng)過氧化單元的氧化作用后混合球團(tuán)中的低價(jià)鐵、釩和鈦被充分氧化成高價(jià)鐵氧化物、高價(jià)釩氧化物和高價(jià)鈦氧化物,得到氧化球團(tuán);接著氧化球團(tuán)在還原裝置中的還原氣作用下發(fā)生還原反應(yīng),使得大多數(shù)高價(jià)鐵化合物還原為金屬鐵及少量浮士體,得到疏松多孔、透氣性好且熱交換效率高的金屬化球團(tuán),將金屬化球團(tuán)進(jìn)一步加熱處理,使得鐵晶粒進(jìn)一步長大,得到鐵晶粒長大后的金屬化球團(tuán),經(jīng)水淬處理后,金屬化球團(tuán)性能變脆,成為水淬球團(tuán),可顯著降低后續(xù)粉碎-磁選處理的成本。由此,采用該方法粉碎-磁選成本低,設(shè)備作業(yè)率高,且所得的磁性物中鐵回收率達(dá)95wt%以上,所得的非磁性物中含鈦渣二氧化鈦的回收率達(dá)96wt%以上,釩進(jìn)渣97wt%以上。另外,根據(jù)本發(fā)明上述實(shí)施例的全釩鈦礦直接還原-磁選的方法還可以具有如下附加的技術(shù)特征:在本發(fā)明的一些實(shí)施例中,在步驟(1)中,所述全釩鈦礦為釩鈦鐵精礦、鈦精礦中的至少之一。由此,有利于提高鐵、釩、鈦的回收率。在本發(fā)明的一些實(shí)施例中,在步驟(1)中,所述全釩鈦礦顆粒中粒度不大于200目的占比50重量%以上。由此,可進(jìn)一步提高鐵、釩、鈦的回收率。在本發(fā)明的一些實(shí)施例中,在步驟(2)中,所述全釩鈦礦顆粒、所述粘結(jié)劑、所述添加劑和所述水的混合質(zhì)量比為(100):(0.5-1.5):(0.5-2):(5.5-8.5)。由此,可進(jìn)一步提高鐵、釩、鈦的回收率。在本發(fā)明的一些實(shí)施例中,在步驟(2)中,所述混合球團(tuán)的粒徑為10-18mm。由此,可進(jìn)一步提高鐵、釩、鈦的回收率。在本發(fā)明的一些實(shí)施例中,在步驟(4)中,所述還原氣中一氧化碳和氫氣的體積總量占80%以上。由此,可進(jìn)一步提高鐵、釩、鈦的回收率。在本發(fā)明的一些實(shí)施例中,在步驟(5)中,所述加熱處理的溫度為1100-1200攝氏度,時(shí)間為15-30min。由此,可進(jìn)一步提高鐵、釩、鈦的回收率。本發(fā)明的附加方面和優(yōu)點(diǎn)將在下面的描述中部分給出,部分將從下面的描述中變得明顯,或通過本發(fā)明的實(shí)踐了解到。附圖說明本發(fā)明的上述和/或附加的方面和優(yōu)點(diǎn)從結(jié)合下面附圖對實(shí)施例的描述中將變得明顯和容易理解,其中:圖1是根據(jù)本發(fā)明一個(gè)實(shí)施例的全釩鈦礦直接還原-磁選的系統(tǒng)結(jié)構(gòu)示意圖;圖2是根據(jù)本發(fā)明一個(gè)實(shí)施例的全釩鈦礦直接還原-磁選的方法流程示意圖;圖3是根據(jù)本發(fā)明再一個(gè)實(shí)施例的全釩鈦礦直接還原-磁選的系統(tǒng)結(jié)構(gòu)示意圖。具體實(shí)施方式下面詳細(xì)描述本發(fā)明的實(shí)施例,所述實(shí)施例的示例在附圖中示出,其中自始至終相同或類似的標(biāo)號表示相同或類似的元件或具有相同或類似功能的元件。下面通過參考附圖描述的實(shí)施例是示例性的,旨在用于解釋本發(fā)明,而不能理解為對本發(fā)明的限制。在本發(fā)明中,除非另有明確的規(guī)定和限定,術(shù)語“安裝”、“相連”、“連接”、“固定”等術(shù)語應(yīng)做廣義理解,例如,可以是固定連接,也可以是可拆卸連接,或成一體;可以是機(jī)械連接,也可以是電連接;可以是直接相連,也可以通過中間媒介間接相連,可以是兩個(gè)元件內(nèi)部的連通或兩個(gè)元件的相互作用關(guān)系,除非另有明確的限定。對于本領(lǐng)域的普通技術(shù)人員而言,可以根據(jù)具體情況理解上述術(shù)語在本發(fā)明中的具體含義。在本發(fā)明的一個(gè)方面,本發(fā)明提出了一種全釩鈦礦直接還原-磁選的系統(tǒng),根據(jù)本發(fā)明的實(shí)施例,參考圖1,該系統(tǒng)包括:預(yù)處理裝置100、混合成型裝置200、氧化單元300、還原裝置400、加熱裝置500、水淬裝置600和粉碎-磁選裝置700。根據(jù)本發(fā)明的實(shí)施例,預(yù)處理裝置100具有全釩鈦礦入口101和全釩鈦礦顆粒出口102,且適于將全釩鈦礦進(jìn)行預(yù)處理,以便得到全釩鈦礦顆粒。由此,可顯著增加全釩鈦礦顆粒的比表面積,有利于提高鐵、釩、鈦的回收率。具體的,預(yù)處理裝置包括依次相連的細(xì)磨裝置和烘干裝置。根據(jù)本發(fā)明的一個(gè)實(shí)施例,全釩鈦礦并不受特別限制,本領(lǐng)域技術(shù)人員可以根據(jù)實(shí)際需要進(jìn)行選擇,根據(jù)本發(fā)明的一個(gè)具體實(shí)施例,全釩鈦礦可以為釩鈦鐵精礦、鈦精礦中的至少之一。由此,可進(jìn)一步提高鐵、釩、鈦的回收率。根據(jù)本發(fā)明的再一個(gè)實(shí)施例,全釩鈦礦顆粒的粒度并不受特別限制,本領(lǐng)域技術(shù)人員可以根據(jù)實(shí)際需要進(jìn)行選擇,根據(jù)本發(fā)明的一個(gè)具體實(shí)施例,全釩鈦礦顆粒中粒度不大于200目的占比50%重量以上。發(fā)明人發(fā)現(xiàn),釩鈦礦顆粒過大或過小均會導(dǎo)致成球性能差,破損率高,能耗高、生產(chǎn)率低等缺點(diǎn)。根據(jù)本發(fā)明的實(shí)施例,混合成型裝置200具有全釩鈦顆粒入口201、粘結(jié)劑入口202、添加劑入口203、水入口204和混合球團(tuán)出口205,全釩鈦礦顆粒入口201與全釩鈦礦顆粒出口102相連,且適于將全釩鈦礦顆粒、粘結(jié)劑、添加劑和水進(jìn)行混合成型處理,以便得到混合球團(tuán)。由此,有利于增加全釩鈦礦顆粒與粘結(jié)劑、添加劑和水的接觸面積,使得全釩鈦礦顆粒與粘結(jié)劑、添加劑和水充分接觸,從而進(jìn)一步提高鐵、釩、鈦的回收率。需要說明的是,粘結(jié)劑的類型并不受特別限制,本領(lǐng)域技術(shù)人員可以根據(jù)實(shí)際需要進(jìn)行選擇,例如可以為膨潤土。根據(jù)本發(fā)明的一個(gè)實(shí)施例,全釩鈦礦顆粒和粘結(jié)劑、添加劑、水的混合質(zhì)量比并不受特別限制,本領(lǐng)域技術(shù)人員可以根據(jù)實(shí)際需要進(jìn)行選擇,根據(jù)本發(fā)明的一個(gè)具體實(shí)施例,全釩鈦礦顆粒和粘結(jié)劑、添加劑、水的混合質(zhì)量比可以為(100):(0.5-1.5):(0.5-2):(5.5-8.5)。發(fā)明人發(fā)現(xiàn),水分過低或過高都將導(dǎo)致成球性差,破損率高,電耗高,生產(chǎn)率低;而且水分過高還將導(dǎo)致烘干預(yù)熱的熱量供應(yīng)增加,能耗增加;粘結(jié)劑、添加劑過高將增加生產(chǎn)成本,過低成球性差,冶金性能差。根據(jù)本發(fā)明的再一個(gè)實(shí)施例,混合球團(tuán)的粒徑并不受特別限制,本領(lǐng)域技術(shù)人員可以根據(jù)實(shí)際需要進(jìn)行選擇,根據(jù)本發(fā)明的一個(gè)具體實(shí)施例,混合球團(tuán)的粒徑可以為10-18mm。發(fā)明人發(fā)現(xiàn),如球團(tuán)粒徑過大,球團(tuán)內(nèi)部傳熱慢,球團(tuán)干燥、預(yù)熱、氧化焙燒過程容易出現(xiàn)外部過熱,內(nèi)部不熱及“燒不透,煮不熟”的狀態(tài);而若球團(tuán)粒徑過小,球團(tuán)之間透氣性差,增加能耗及生產(chǎn)成本。根據(jù)本發(fā)明的實(shí)施例,氧化單元300具有混合球團(tuán)入口301和氧化球團(tuán)出口302,混合球團(tuán)入口301與混合球團(tuán)出口205相連,且適于將混合球團(tuán)進(jìn)行處理,以便得到氧化球團(tuán)。根據(jù)本發(fā)明的一個(gè)實(shí)施例,氧化單元可以包括依次相連的干燥裝置、預(yù)熱裝置和焙燒裝置。例如,可以將上述所得的混合球團(tuán)送至豎爐或鏈篦機(jī)-回轉(zhuǎn)窯依次進(jìn)行干燥、預(yù)熱、氧化-焙燒處理,得到滿足豎爐生產(chǎn)的氧化球團(tuán),具體的,氧化球團(tuán)粒徑≥9mm,抗壓強(qiáng)度>2000n/個(gè),還原性大于60%等冶金性能可以滿足豎爐生產(chǎn)。根據(jù)本發(fā)明的實(shí)施例,還原裝置400具有氧化球團(tuán)入口401、還原氣入口402和金屬化球團(tuán)出口403,氧化球團(tuán)入口401與氧化球團(tuán)出口302相連,且適于采用還原氣對氧化球團(tuán)進(jìn)行還原處理,以便得到金屬化球團(tuán)。具體的,將上述所得氧化球團(tuán)送入豎爐車間,并吊運(yùn)至豎爐爐頂料倉,將料倉中的氧化球團(tuán)通過下料管連續(xù)下料至豎爐,與此同時(shí),還原氣從豎爐還原段下部輸入,還原氣溫度為800-1000攝氏度,還原氣氣量為每噸金屬球團(tuán)1700-2000nm3,還原氣中co和h2的體積總量占比大于80v%,h2與co的體積比為1.25-5.5,在豎爐內(nèi)下降的氧化球團(tuán)與上升的還原氣直接發(fā)生還原反應(yīng)生成金屬化球團(tuán),氧化球團(tuán)中的高價(jià)鐵化合物在還原氣的作用下被還原為低價(jià)鐵化合物,所得的金屬化球團(tuán)中鐵晶粒較大,且疏松多孔、透氣性好、熱交換效率高。根據(jù)本發(fā)明的一個(gè)實(shí)施例,還原氣中一氧化碳和氫氣的體積總量并不受特別限制,本領(lǐng)域技術(shù)人員可以根據(jù)實(shí)際需要進(jìn)行選擇,根據(jù)本發(fā)明的一個(gè)具體實(shí)施例,還原氣中一氧化碳和氫氣的體積總量可以為占80%以上。發(fā)明人發(fā)現(xiàn),若還原氣中一氧化碳和氫氣的體積總量低于80%,則球團(tuán)還原速度降低,從而導(dǎo)致生產(chǎn)能耗增加。根據(jù)本發(fā)明的實(shí)施例,加熱裝置500具有金屬化球團(tuán)入口501和鐵晶粒球團(tuán)出口502,金屬化球團(tuán)入口501與金屬化球團(tuán)出口403相連,且適于將金屬化球團(tuán)進(jìn)行加熱處理,以便得到鐵晶粒球團(tuán)。具體的,豎爐還原段以下設(shè)置下料溜槽,溜槽段使用循環(huán)豎爐爐頂氣以防止金屬化球團(tuán)被氧化,通過溜槽將還原后的金屬化球團(tuán)送至蓄熱式燃?xì)鉅t,爐內(nèi)呈弱還原氣氛,繼續(xù)加熱金屬化球團(tuán)使其溫度從700-850攝氏度升溫至1100-1200攝氏度,保溫15-30min,便于鐵晶粒長大,得到鐵晶粒球團(tuán)。根據(jù)本發(fā)明的實(shí)施例,水淬裝置600具有鐵晶粒球團(tuán)入口601和水淬球團(tuán)出口602,鐵晶粒球團(tuán)入口601與鐵晶粒球團(tuán)出口502相連,且適于將鐵晶粒球團(tuán)進(jìn)行水淬處理,以便得到水淬球團(tuán)。具體的,待鐵晶粒球團(tuán)保溫結(jié)束后出料水淬,通過水淬可改變鐵晶粒球團(tuán)的晶型結(jié)構(gòu),使其性能變脆,有利于后續(xù)粉碎-磁選處理,降低后續(xù)粉碎-磁選處理的成本,同時(shí)可克服現(xiàn)有技術(shù)中細(xì)晶粒在長大過程中物料粘結(jié)的問題,如此,有利于提高設(shè)備的作業(yè)率,促進(jìn)整個(gè)工藝順行。根據(jù)本發(fā)明的實(shí)施例,粉碎-磁選裝置700具有水淬球團(tuán)入口701、磁性物出口702和非磁性物出口703,水淬球團(tuán)入口701與水淬球團(tuán)出口602相連,且適于將水淬球團(tuán)進(jìn)行粉碎和磁選處理,以便得到磁性物和非磁性物。具體的,先將水淬后的水淬球團(tuán)粉碎細(xì)磨至200目以下占50%以上,然后進(jìn)行磁選,磁選時(shí)的磁場強(qiáng)度為450-800特斯拉,得到磁性物和非磁性物,磁性物中鐵回收率達(dá)95wt%以上,非磁性物是后續(xù)提釩提鈦的優(yōu)質(zhì)原料,非磁性物中含鈦渣二氧化鈦的回收率達(dá)96wt%以上,釩進(jìn)渣97wt%以上。根據(jù)本發(fā)明實(shí)施例的全釩鈦礦直接還原-磁選的系統(tǒng)通過將全釩鈦礦送至預(yù)處理裝置進(jìn)行預(yù)處理得到全釩鈦礦顆粒,可顯著增加全釩鈦礦顆粒的比表面積,從而增加后續(xù)在混合成型裝置中全釩鈦礦顆粒與粘結(jié)劑、添加劑和水的接觸面積,使得全釩鈦礦顆粒與粘結(jié)劑、添加劑和水充分接觸,得到混合球團(tuán);混合球團(tuán)經(jīng)過氧化單元的氧化作用后混合球團(tuán)中的低價(jià)鐵、釩和鈦被充分氧化成高價(jià)鐵氧化物、高價(jià)釩氧化物和高價(jià)鈦氧化物,得到氧化球團(tuán);接著氧化球團(tuán)在還原裝置中的還原氣作用下發(fā)生還原反應(yīng),使得大多數(shù)高價(jià)鐵化合物還原為金屬鐵及少量浮士體,得到疏松多孔、透氣性好且熱交換效率高的金屬化球團(tuán),將金屬化球團(tuán)進(jìn)一步加熱處理,使得鐵晶粒進(jìn)一步長大,得到鐵晶粒長大后的金屬化球團(tuán),經(jīng)水淬處理后,金屬化球團(tuán)性能變脆,成為水淬球團(tuán),可顯著降低后續(xù)粉碎-磁選處理的成本。由此,采用該系統(tǒng)粉碎-磁選成本低,設(shè)備作業(yè)率高,且所得的磁性物中鐵回收率達(dá)95wt%以上,所得的非磁性物中含鈦渣二氧化鈦的回收率達(dá)96wt%以上,釩進(jìn)渣97wt%以上。在本發(fā)明的再一個(gè)方面,本發(fā)明提出了一種利用上述全釩鈦礦直接還原-磁選的系統(tǒng)實(shí)施全釩鈦礦直接還原-磁選的方法。根據(jù)本發(fā)明的實(shí)施例,參考圖2,該方法包括:s100:將全釩鈦礦供給至預(yù)處理裝置中進(jìn)行預(yù)處理該步驟中,將全釩鈦礦供給至預(yù)處理裝置中進(jìn)行預(yù)處理,以便得到全釩鈦礦顆粒。由此,可顯著增加全釩鈦礦顆粒的比表面積,有利于提高鐵、釩、鈦的回收率。具體的,預(yù)處理過程包括細(xì)磨和烘干過程。根據(jù)本發(fā)明的一個(gè)實(shí)施例,全釩鈦礦并不受特別限制,本領(lǐng)域技術(shù)人員可以根據(jù)實(shí)際需要進(jìn)行選擇,根據(jù)本發(fā)明的一個(gè)具體實(shí)施例,全釩鈦礦可以為釩鈦鐵精礦、鈦精礦中的至少之一。由此,可進(jìn)一步提高鐵、釩、鈦的回收率。根據(jù)本發(fā)明的再一個(gè)實(shí)施例,全釩鈦礦顆粒的粒度并不受特別限制,本領(lǐng)域技術(shù)人員可以根據(jù)實(shí)際需要進(jìn)行選擇,根據(jù)本發(fā)明的一個(gè)具體實(shí)施例,全釩鈦礦顆粒中粒度不大于200目的占比50%重量以上。發(fā)明人發(fā)現(xiàn),釩鈦礦顆粒過大或過小均會導(dǎo)致成球性能差,破損率高,能耗高、生產(chǎn)率低等缺點(diǎn)。s200:將全釩鈦礦顆粒、粘結(jié)劑、添加劑和水供給至混合成型裝置中進(jìn)行混合成型處理該步驟中,將全釩鈦礦顆粒、粘結(jié)劑、添加劑和水供給至混合成型裝置中進(jìn)行混合成型處理,以便得到混合球團(tuán)。由此,有利于增加全釩鈦礦顆粒與粘結(jié)劑、添加劑和水的接觸面積,使得全釩鈦礦顆粒與粘結(jié)劑、添加劑和水充分接觸,從而進(jìn)一步提高鐵、釩、鈦的回收率。需要說明的是,粘結(jié)劑的類型并不受特別限制,本領(lǐng)域技術(shù)人員可以根據(jù)實(shí)際需要進(jìn)行選擇,例如可以為膨潤土。根據(jù)本發(fā)明的一個(gè)實(shí)施例,全釩鈦礦顆粒和粘結(jié)劑、添加劑、水的混合質(zhì)量比并不受特別限制,本領(lǐng)域技術(shù)人員可以根據(jù)實(shí)際需要進(jìn)行選擇,根據(jù)本發(fā)明的一個(gè)具體實(shí)施例,全釩鈦礦顆粒和粘結(jié)劑、添加劑、水的混合質(zhì)量比可以為(100):(0.5-1.5):(0.5-2):(5.5-8.5)。發(fā)明人發(fā)現(xiàn),水分過低或過高都將導(dǎo)致成球性差,破損率高,電耗高,生產(chǎn)率低;而且水分過高還將導(dǎo)致烘干預(yù)熱的熱量供應(yīng)增加,能耗增加;粘結(jié)劑、添加劑過高將增加生產(chǎn)成本,過低成球性差,冶金性能差。根據(jù)本發(fā)明的再一個(gè)實(shí)施例,混合球團(tuán)的粒徑并不受特別限制,本領(lǐng)域技術(shù)人員可以根據(jù)實(shí)際需要進(jìn)行選擇,根據(jù)本發(fā)明的一個(gè)具體實(shí)施例,混合球團(tuán)的粒徑可以為10-18mm。發(fā)明人發(fā)現(xiàn),如球團(tuán)粒徑過大,球團(tuán)內(nèi)部傳熱慢,球團(tuán)干燥、預(yù)熱、氧化焙燒過程容易出現(xiàn)外部過熱,內(nèi)部不熱及“燒不透,煮不熟”的狀態(tài);而若球團(tuán)粒徑過小,球團(tuán)之間透氣性差,增加能耗及生產(chǎn)成本。s300:將混合球團(tuán)供給至氧化單元進(jìn)行處理該步驟中,將混合球團(tuán)供給至氧化單元進(jìn)行氧化處理,以便得到氧化球團(tuán)。具體的,氧化處理包括依次相連的干燥處理、預(yù)熱處理和焙燒處理。例如,將上述所得的混合球團(tuán)送至豎爐或鏈篦機(jī)-回轉(zhuǎn)窯依次進(jìn)行干燥、預(yù)熱、氧化-焙燒處理,得到滿足豎爐生產(chǎn)的氧化球團(tuán),具體的,氧化球團(tuán)粒徑≥9mm,抗壓強(qiáng)度>2000n/個(gè),還原性大于60%等冶金性能可以滿足豎爐生產(chǎn)。s400:將氧化球團(tuán)和還原氣供給至還原裝置中進(jìn)行還原處理該步驟中,將氧化球團(tuán)和還原氣供給至還原裝置中進(jìn)行還原處理,以便得到金屬化球團(tuán)。具體的,將上述所得氧化球團(tuán)送入豎爐車間,并吊運(yùn)至豎爐爐頂料倉,將料倉中的氧化球團(tuán)通過下料管連續(xù)下料至豎爐,與此同時(shí),還原氣從豎爐還原段下部輸入,還原氣溫度為800-1000攝氏度,還原氣氣量為每噸金屬球團(tuán)1700-2000nm3,還原氣中co和h2的體積總量占比大于80v%,h2與co的體積比為1.25-5.5,在豎爐內(nèi)下降的氧化球團(tuán)與上升的還原氣直接發(fā)生還原反應(yīng)生成金屬化球團(tuán),氧化球團(tuán)中的高價(jià)鐵化合物在還原氣的作用下被還原為低價(jià)鐵化合物,所得的金屬化球團(tuán)中鐵晶粒較大,且疏松多孔、透氣性好、熱交換效率高。根據(jù)本發(fā)明的一個(gè)實(shí)施例,還原氣中一氧化碳和氫氣的體積總量并不受特別限制,本領(lǐng)域技術(shù)人員可以根據(jù)實(shí)際需要進(jìn)行選擇,根據(jù)本發(fā)明的一個(gè)具體實(shí)施例,還原氣中一氧化碳和氫氣的體積總量可以為占80%以上。發(fā)明人發(fā)現(xiàn),若還原氣中一氧化碳和氫氣的體積總量低于80%,則球團(tuán)還原速度降低,從而導(dǎo)致生產(chǎn)能耗增加。s500:將金屬化球團(tuán)供給至加熱裝置中進(jìn)行加熱處理該步驟中,將金屬化球團(tuán)供給至加熱裝置中進(jìn)行加熱處理,以便得到鐵晶粒球團(tuán)。具體的,豎爐還原段以下設(shè)置下料溜槽,溜槽段使用循環(huán)豎爐爐頂氣以防止金屬化球團(tuán)被氧化,通過溜槽將還原后的金屬化球團(tuán)送至蓄熱式燃?xì)鉅t,爐內(nèi)呈弱還原氣氛,繼續(xù)加熱金屬化球團(tuán)使其溫度從700-850攝氏度升溫至1100-1200攝氏度,保溫15-30min,便于鐵晶粒長大,得到鐵晶粒球團(tuán)。s600:將鐵晶粒球團(tuán)供給至水淬裝置中進(jìn)行水淬處理該步驟中,將鐵晶粒球團(tuán)供給至水淬裝置中進(jìn)行水淬處理,以便得到水淬球團(tuán)。具體的,待鐵晶粒球團(tuán)保溫結(jié)束后出料水淬,通過水淬可改變鐵晶粒球團(tuán)的晶型結(jié)構(gòu),使其性能變脆,有利于后續(xù)粉碎-磁選處理,降低后續(xù)粉碎-磁選處理的成本,同時(shí)可克服現(xiàn)有技術(shù)中細(xì)晶粒在長大過程中物料粘結(jié)的問題,如此,有利于提高設(shè)備的作業(yè)率,促進(jìn)整個(gè)工藝順行。s700:將水淬球團(tuán)供給至粉碎-磁選裝置中進(jìn)行粉碎和磁選處理該步驟中,將水淬球團(tuán)供給至粉碎-磁選裝置中進(jìn)行粉碎和磁選處理,以便得到磁性物和非磁性物。具體的,先將水淬后的水淬球團(tuán)粉碎細(xì)磨至200目以下占50%以上,然后進(jìn)行磁選,磁選時(shí)的磁場強(qiáng)度為450-800特斯拉,得到磁性物和非磁性物,磁性物中鐵回收率達(dá)95wt%以上,非磁性物是后續(xù)提釩提鈦的優(yōu)質(zhì)原料,非磁性物中含鈦渣二氧化鈦的回收率達(dá)96wt%以上,釩進(jìn)渣97wt%以上。根據(jù)本發(fā)明實(shí)施例的全釩鈦礦直接還原-磁選的方法通過將全釩鈦礦送至預(yù)處理裝置進(jìn)行預(yù)處理得到全釩鈦礦顆粒,可顯著增加全釩鈦礦顆粒的比表面積,從而增加后續(xù)在混合成型裝置中全釩鈦礦顆粒與粘結(jié)劑、添加劑和水的接觸面積,使得全釩鈦礦顆粒與粘結(jié)劑、添加劑和水充分接觸,得到混合球團(tuán);混合球團(tuán)經(jīng)過氧化單元的氧化作用后混合球團(tuán)中的低價(jià)鐵、釩和鈦被充分氧化成高價(jià)鐵氧化物、高價(jià)釩氧化物和高價(jià)鈦氧化物,得到氧化球團(tuán);接著氧化球團(tuán)在還原裝置中的還原氣作用下發(fā)生還原反應(yīng),使得大多數(shù)高價(jià)鐵化合物還原為金屬鐵及少量浮士體,得到疏松多孔、透氣性好且熱交換效率高的金屬化球團(tuán),將金屬化球團(tuán)進(jìn)一步加熱處理,使得鐵晶粒進(jìn)一步長大,得到鐵晶粒長大后的金屬化球團(tuán),經(jīng)水淬處理后,金屬化球團(tuán)性能變脆,成為水淬球團(tuán),可顯著降低后續(xù)粉碎-磁選處理的成本。由此,采用該方法粉碎-磁選成本低,設(shè)備作業(yè)率高,且所得的磁性物中鐵回收率達(dá)95wt%以上,所得的非磁性物中含鈦渣二氧化鈦的回收率達(dá)96wt%以上,釩進(jìn)渣97wt%以上。下面參考具體實(shí)施例,對本發(fā)明進(jìn)行描述,需要說明的是,這些實(shí)施例僅僅是描述性的,而不以任何方式限制本發(fā)明。實(shí)施例1參考圖3,將全釩鈦礦(釩鈦鐵精礦)供給至預(yù)處理裝置中進(jìn)行預(yù)處理,得到粒度不大于200目的占比80%重量的全釩鈦礦(釩鈦鐵精礦或鈦精礦)顆粒,其主要成分及各成分的含量見表1,并將上述全釩鈦礦(釩鈦鐵精礦)顆粒與粘結(jié)劑(膨潤土)、添加劑(碳酸鈉)和水按照質(zhì)量比(100):(0.5-1.5):(0.5-2):(5.5-8.5)送至混合成型裝置中進(jìn)行混合成型,得到粒徑為10-18mm的混合球團(tuán),接著將該混合球團(tuán)供給至氧化單元(鏈篦機(jī)-回轉(zhuǎn)窯)依次進(jìn)行干燥、預(yù)熱、氧化-焙燒處理,得到滿足還原裝置(豎爐)生產(chǎn)的氧化球團(tuán),然后將該氧化球團(tuán)送入豎爐車間,并吊運(yùn)至豎爐爐頂料倉,將料倉中的氧化球團(tuán)通過下料管連續(xù)下料至豎爐,與此同時(shí),還原氣從豎爐還原段下部輸入,還原氣溫度為850攝氏度,還原氣氣量為每噸金屬球團(tuán)2000nm3,還原氣中co和h2的體積總量占比85v%,h2與co的體積比為4,在豎爐內(nèi)下降的氧化球團(tuán)與上升的還原氣直接發(fā)生還原反應(yīng)生成金屬化球團(tuán),氧化球團(tuán)中的高價(jià)鐵化合物在還原氣的作用下被還原為低價(jià)鐵化合物,所得的金屬化球團(tuán)中鐵晶粒較大,且疏松多孔、透氣性好、熱交換效率高。豎爐還原段以下設(shè)置下料溜槽,溜槽段使用循環(huán)豎爐爐頂氣以防止金屬化球團(tuán)被氧化,通過溜槽將還原后的金屬化球團(tuán)送至加熱裝置(蓄熱式燃?xì)鉅t),爐內(nèi)呈弱還原氣氛,繼續(xù)加熱金屬化球團(tuán)使其溫度從700-850攝氏度升溫至1100攝氏度,保溫15min,便于鐵晶粒長大,得到鐵晶粒球團(tuán)。待鐵晶粒球團(tuán)保溫結(jié)束后出料送至水淬裝置進(jìn)行水淬處理,打水量為350kg/t.dri,通過水淬可改變鐵晶粒球團(tuán)的晶型結(jié)構(gòu),使其性能變脆,有利于后續(xù)粉碎-磁選處理,降低后續(xù)粉碎-磁選處理的成本,同時(shí)可克服現(xiàn)有技術(shù)中細(xì)晶粒在長大過程中物料粘結(jié)的問題,如此,有利于提高設(shè)備的作業(yè)率,促進(jìn)整個(gè)工藝順行;最后將水淬球團(tuán)供給至粉碎-磁選裝置中進(jìn)行粉碎和磁選處理,具體的,將水淬后的水淬球團(tuán)粉碎細(xì)磨至150目以下占50%以上,然后進(jìn)行磁選,磁選時(shí)的磁場強(qiáng)度為600特斯拉,得到磁性物和非磁性物,磁性物的主要成分及各成分的含量見表2,非磁性物的主要成分及各成分的含量見表3,磁性物中鐵回收率達(dá)96.58wt%,非磁性物是后續(xù)提釩提鈦的優(yōu)質(zhì)原料,非磁性物中含鈦渣二氧化鈦的回收率達(dá)96wt%以上,釩進(jìn)渣97wt%以上。表1釩鈦鐵精礦主要成分及各成分的含量(wt%)成分tfefeov2o5tio2含量56210.6513表2磁性物主要成分及各成分的含量(wt%)成分tfefeomfev2o5tio2含量93.257.0787.750.090.86表3非磁性物主要成分及各成分的含量(wt%)成分tfefeomfev2o5tio2含量5.563.053.192.3653.65實(shí)施例2參考圖3,將全釩鈦礦(釩鈦鐵精礦)供給至預(yù)處理裝置中進(jìn)行預(yù)處理,得到粒度不大于200目的占比80%重量的全釩鈦礦(釩鈦鐵精礦或鈦精礦)顆粒,其主要成分及各成分的含量見表4,并將上述全釩鈦礦(釩鈦鐵精礦或鈦精礦)顆粒與粘結(jié)劑(膨潤土)、添加劑(硝酸鉀)和水按照質(zhì)量比(100):(0.5-1.5):(0.5-2):(5.5-8.5)送至混合成型裝置中進(jìn)行混合成型,得到粒徑為10-18mm的混合球團(tuán),接著將該混合球團(tuán)供給至氧化單元(豎爐或鏈篦機(jī)-回轉(zhuǎn)窯)依次進(jìn)行干燥、預(yù)熱、氧化-焙燒處理,得到滿足還原裝置(豎爐)生產(chǎn)的氧化球團(tuán),然后將該氧化球團(tuán)送入豎爐車間,并吊運(yùn)至豎爐爐頂料倉,將料倉中的氧化球團(tuán)通過下料管連續(xù)下料至豎爐,與此同時(shí),還原氣從豎爐還原段下部輸入,還原氣溫度為950攝氏度,還原氣氣量為每噸金屬球團(tuán)1800nm3,還原氣中co和h2的體積總量占比90v%,h2與co的體積比為4,在豎爐內(nèi)下降的氧化球團(tuán)與上升的還原氣直接發(fā)生還原反應(yīng)生成金屬化球團(tuán),氧化球團(tuán)中的高價(jià)鐵化合物在還原氣的作用下被還原為低價(jià)鐵化合物,所得的金屬化球團(tuán)中鐵晶粒較大,且疏松多孔、透氣性好、熱交換效率高。豎爐還原段以下設(shè)置下料溜槽,溜槽段使用循環(huán)豎爐爐頂氣以防止金屬化球團(tuán)被氧化,通過溜槽將還原后的金屬化球團(tuán)送至加熱裝置(蓄熱式燃?xì)鉅t),爐內(nèi)呈弱還原氣氛,繼續(xù)加熱金屬化球團(tuán)使其溫度從700-850攝氏度升溫至1200攝氏度,保溫20min,便于鐵晶粒長大,得到鐵晶粒球團(tuán)。待鐵晶粒球團(tuán)保溫結(jié)束后出料送至水淬裝置進(jìn)行水淬處理,打水量為350kg/t.dri,通過水淬可改變鐵晶粒球團(tuán)的晶型結(jié)構(gòu),使其性能變脆,有利于后續(xù)粉碎-磁選處理,降低后續(xù)粉碎-磁選處理的成本,同時(shí)可克服現(xiàn)有技術(shù)中細(xì)晶粒在長大過程中物料粘結(jié)的問題,如此,有利于提高設(shè)備的作業(yè)率,促進(jìn)整個(gè)工藝順行;最后將水淬球團(tuán)供給至粉碎-磁選裝置中進(jìn)行粉碎和磁選處理,具體的,將水淬后的水淬球團(tuán)粉碎細(xì)磨至150目以下占50%以上,然后進(jìn)行磁選,磁選時(shí)的磁場強(qiáng)度為800特斯拉,得到磁性物和非磁性物,磁性物的主要成分及各成分的含量見表5,非磁性物的主要成分及各成分的含量見表6,磁性物中鐵回收率達(dá)96wt%以上,非磁性物是后續(xù)提釩提鈦的優(yōu)質(zhì)原料,非磁性物中含鈦渣二氧化鈦的回收率達(dá)98wt%,釩進(jìn)渣97wt%以上。表4釩鈦鐵精礦主要成分及各成分的含量(wt%)成分tfefeov2o5tio2含量38210.3146表5磁性物主要成分及各成分的含量(wt%)成分tfefeomfev2o5tio2含量94.735.4990.460.212.18表6非磁性物主要成分及各成分的含量(wt%)成分tfefeomfev2o5tio2含量2.422.330.610.6294.32在本說明書的描述中,參考術(shù)語“一個(gè)實(shí)施例”、“一些實(shí)施例”、“示例”、“具體示例”、或“一些示例”等的描述意指結(jié)合該實(shí)施例或示例描述的具體特征、結(jié)構(gòu)、材料或者特點(diǎn)包含于本發(fā)明的至少一個(gè)實(shí)施例或示例中。在本說明書中,對上述術(shù)語的示意性表述不必須針對的是相同的實(shí)施例或示例。而且,描述的具體特征、結(jié)構(gòu)、材料或者特點(diǎn)可以在任一個(gè)或多個(gè)實(shí)施例或示例中以合適的方式結(jié)合。此外,在不相互矛盾的情況下,本領(lǐng)域的技術(shù)人員可以將本說明書中描述的不同實(shí)施例或示例以及不同實(shí)施例或示例的特征進(jìn)行結(jié)合和組合。盡管上面已經(jīng)示出和描述了本發(fā)明的實(shí)施例,可以理解的是,上述實(shí)施例是示例性的,不能理解為對本發(fā)明的限制,本領(lǐng)域的普通技術(shù)人員在本發(fā)明的范圍內(nèi)可以對上述實(shí)施例進(jìn)行變化、修改、替換和變型。當(dāng)前第1頁12