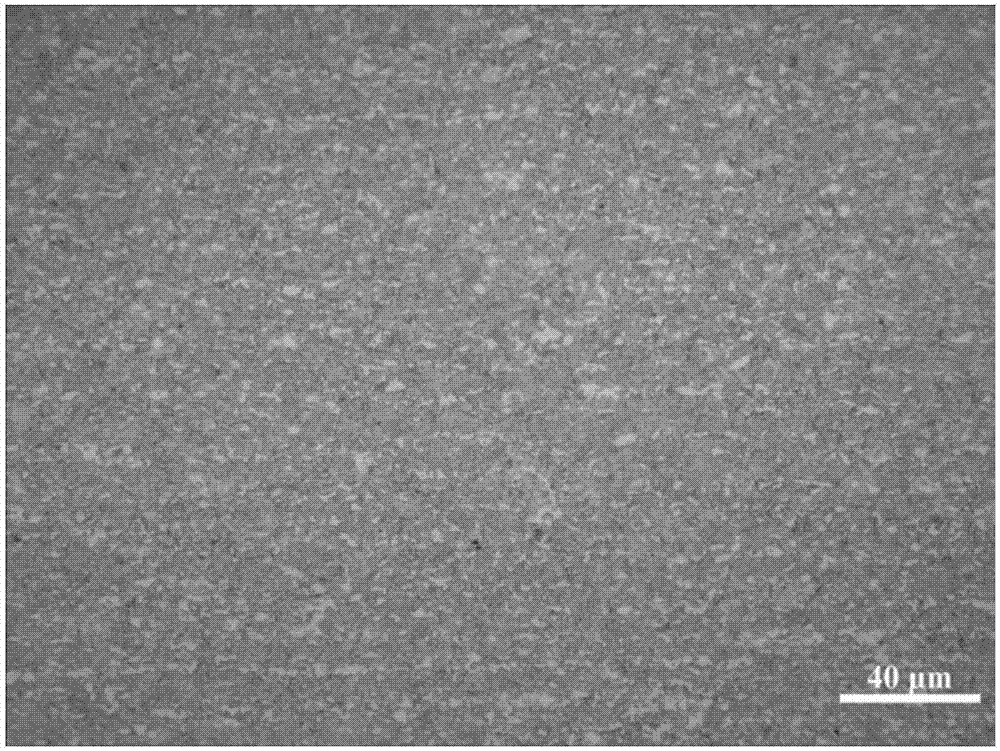
本發(fā)明涉及一種冷彎性能優(yōu)異的980mpa級冷軋雙相鋼鋼板及其制備方法。
背景技術(shù):
:隨著汽車輕量化的推動以及汽車用鋼的發(fā)展,高強鋼特別是先進高強鋼在汽車中的應(yīng)用越來越廣。其中以具有雙相組織的鐵素體/馬氏體雙相鋼最具代表性,目前研究和應(yīng)用最多、最成熟的雙相鋼大多集中在抗拉強度800mpa以下,其馬氏體含量一般不超過20%。而隨著汽車工業(yè)對減重要求的提高,應(yīng)用抗拉強度在980mpa及其以上級別的超高強度雙相鋼可在保證安全性能的前提下降低零部件厚度,從而達到減輕汽車車身重量的目的。通過合理的成分以及工藝設(shè)計,提高組織中馬氏體含量,細化晶粒,控制馬氏體和鐵素體彌散程度和分布狀態(tài)可以得到更高強度級別的雙相鋼產(chǎn)品。但在提高雙相鋼強度的同時也造成了成形性能的下降。而抗拉強度980mpa及以上高強度冷軋雙相鋼主要應(yīng)用在前后保險杠、車門防撞梁、座椅橫梁等梁狀安全件,其成形方式有沖壓和輥壓兩種,變形方式以冷彎為主。因此,應(yīng)用和變形方式?jīng)Q定了對于抗拉強度980mpa及以上高強度冷軋雙相鋼,其對局部變形能力要求很高,也就是擴孔率和冷彎性能。雙相鋼的組織特點決定了他優(yōu)良的綜合力學(xué)性能,即較低的屈強比和較好的延伸率,具備一定的拉延成形能力。但應(yīng)用于以冷彎為主的高強度安全件時容易在r角處發(fā)生開裂、頸縮等缺陷。這是由于為了達到需要的強度級別,高強度冷軋雙相鋼中必定會添加c、mn等合金元素,這些元素在澆注、熱軋過程中發(fā)生偏析造成成品組織不均甚至帶狀組織,使材料局部變形能力下降,嚴重影響材料冷彎性能。技術(shù)實現(xiàn)要素:本發(fā)明提供了一種冷彎性能優(yōu)異的980mpa級冷軋雙相鋼鋼板及其制備方法,其組織形貌為馬氏體加鐵素體組織,晶粒度等級可達12級以上具有優(yōu)異的力學(xué)性能,其屈服強度為730mpa~850mpa,抗拉強度在980mpa以上,延伸率10~20%,180°冷彎性能≤2a,a為板厚,并具有成本較低、產(chǎn)品應(yīng)用性能好的特點。本發(fā)明采取的技術(shù)方案為:一種冷彎性能優(yōu)異的980mpa級冷軋雙相鋼鋼板,其化學(xué)成分及重量百分比為:c0.10~0.12%;si0.45~0.65%;mn2.4~2.6%;cr0.35~0.45%;nb0.05~0.075%;ti0.06~0.10%;als0.055-0.075%;p≤0.008%;s≤0.002%;n≤0.003%,余量為fe和不可避免的雜質(zhì)。進一步地,其化學(xué)成分及重量百分比優(yōu)選為:c0.11%;si0.50%;mn2.5%;cr0.40%;nb0.06%;ti0.08%;als0.060%;p0.005%;s0.001%;n0.001%,余量為fe和不可避免的雜質(zhì)。進一步地,其化學(xué)成分及重量百分比優(yōu)選為:c0.12%;si0.46%;mn2.49%;cr0.36%;nb0.06%;ti0.09%;als0.065%;p0.006%;s0.002%;n0.001%,余量為fe和不可避免的雜質(zhì)。本發(fā)明還提供了上述冷彎性能優(yōu)異的980mpa級冷軋雙相鋼鋼板的制備方法,具體包括以下步驟:(1)冶煉工序;(2)lf精煉與rh精煉工序;(3)連鑄工序:在此工序中投入動態(tài)輕壓下和電磁攪拌系統(tǒng);(4)熱連軋工序:鑄坯經(jīng)1250~1350℃加熱,由粗軋機進行5~20道次軋制,熱軋到30~50mm厚度規(guī)格,由熱連軋機組進行5~7道次軋制,軋至6~10mm厚度后,以80~100℃/s的速度快速冷卻,在500~650℃范圍內(nèi)進行卷取成鋼卷;(5)酸洗冷軋工序:冷軋壓下率為40~50%,軋至0.8~2mm;(6)連續(xù)退火工序。進一步地,所述步驟(6)具體包括以下步驟:將酸洗冷軋步驟處理好的鋼板,以5-15℃/s加熱至170℃后,快速升溫至770-810℃,保溫90~160s,以6~10℃/s的速度冷至710~750℃后,以36-60℃/s的冷卻速度快速冷卻至在280~320℃,過時效處理410~700s后冷至20~30℃室溫。進一步地,所述步驟(6)具體包括以下步驟:將酸洗冷軋步驟處理好的鋼板,以12℃/s加熱至170℃后,快速升溫至780℃,保溫120s,以6℃/s的速度冷至740℃后,以55℃/s的冷卻速度快速冷卻至310℃,過時效處理500s后冷至20~30℃室溫。進一步地,所述的快速升溫是指以加熱爐最大功率進行升溫。進一步地,冶煉工序中,可采用轉(zhuǎn)爐、電爐或感應(yīng)爐冶煉。進一步地,酸洗冷軋工序中,熱軋帶鋼經(jīng)鹽酸槽酸洗。本發(fā)明所公開的冷彎性能優(yōu)異的980mpa級冷軋雙相鋼鋼板,其化學(xué)成分設(shè)計合理,未大量添加貴重金屬合金,極少的c含量與少量的合金元素,保證了良好的焊接性能,且成分可滿足大規(guī)模生產(chǎn)控制。本發(fā)明所公開的各元素的作用如下:c:最有效的強化元素之一,對于馬氏體的形成起關(guān)鍵作用,鋼中碳含量決定雙相鋼的強度級別和馬氏體的性能;由于馬氏體含量和淬透性的設(shè)計要求,本發(fā)明中c的成分控制在0.10~0.12%的范圍內(nèi);si:鐵素體形成元素,起到固溶強化的作用,在兩相區(qū)保溫時,有加速碳向奧氏體擴散的作用,對鐵素體有顯著的凈化作用,提高了雙相鋼中鐵素體純凈度,從而得到較低的屈強比;另一方面,si含量過高在鋼板表面形成的高熔點氧化物而影響鋼板表面質(zhì)量,盡量降低鋼中的硅含量,所以本發(fā)明si重量百分含量控制在0.45~0.65%;mn:提高了奧氏體的穩(wěn)定性,從而顯著增加淬透性,mn也起到固溶強化和細化鐵素體晶粒的作用,可以推遲珠光體轉(zhuǎn)變和貝氏體轉(zhuǎn)變;另一方面,mn是擴大γ區(qū)元素,當高的錳含量使珠光體轉(zhuǎn)變開始時間推遲的同時,也會減緩鐵素體的析出;而錳含量太低又滿足不了淬透性要求,所以本發(fā)明mn重量百分比含量控制在2.4~2.6%;cr:中強碳化物形成元素,和mn元素一樣能提高鋼的淬透性,與其他合金元素搭配加入鋼中,能大大提高鋼的淬透性,從而推遲珠光體轉(zhuǎn)變和貝氏體轉(zhuǎn)變,cr也是一種固溶強化元素,起到對基體的強化作用;另一方面,過高的cr含量,會使鋼的淬透性大大提高,從而使強度大大增加,但是惡化了鋼的成形性與焊接性,因此較佳的cr含量應(yīng)控制在0.35~0.45%以內(nèi)。als:als在雙相鋼中所起的作用與si相似,同時al還可形成aln析出,起到一定的細化晶粒的作用;少量al的存在,保證強度性能的前提下,可使雙相鋼的延伸性能提高,所以本發(fā)明al重量百分比含量控制在0.055-0.075%。ti:是強碳化物形成元素,具有細化晶粒的作用,另外,鈦可以固定碳元素,已消除鉻在晶界處的貧化,從而消除或減輕鋼的晶間腐蝕,微量的鈦還具有提高鋼的塑性和韌性的作用,但是過量的鈦會降低鋼件的強度和韌性,因此,本發(fā)明中鈦的含量限制在0.06~0.10%;nb:具有固溶強化、細化晶粒并提高鋼的淬透性,它能增加鋼的回火穩(wěn)定性,有二次硬化的作用,微量nb的加入,在不影響鋼的塑性或者韌性的情況下提高鋼的強度,本發(fā)明中nb的含量限制在0.05~0.075%。p、s、n:為減少鋼中有害雜質(zhì)對鋼的沖壓性能的不良影響,嚴格控制鋼中的p、s、n的含量,因此分別將三者的含量限制在0.008%以下、0.002%以下、0.003%以下。在其制備工藝中,lf精煉與rh精煉雙聯(lián)控制、連鑄過程中的動態(tài)輕壓下和電磁攪拌保證了板坯質(zhì)量和合金元素的精確命中,電磁攪拌使得雜質(zhì)上浮以獲得好的鑄坯內(nèi)部質(zhì)量;熱軋區(qū)域采用1250~1350℃高溫加熱制度、500-650℃低溫卷取的方式,80~100℃/s的速度快速冷卻,避免了熱軋區(qū)域帶狀組織的產(chǎn)生;同時,連續(xù)退火快冷段冷卻速度較快為36-60℃,有益于形成典型的馬氏體加鐵素體組織,避免貝氏體的過多生成,從而保證了雙相鋼的延性和低的屈強比;同時過時效保溫時間較長,保證了雙相鋼的綜合力學(xué)性能。各化學(xué)元素含量的控制結(jié)合上述對生產(chǎn)工藝的改進,根據(jù)本發(fā)明公開的方法得到了具有較高晶粒度級別的冷軋雙相鋼鋼板,其屈服強度、抗拉強度、冷彎性能均優(yōu)于同級別的冷軋雙相鋼鋼板。根據(jù)目前市場情況,980mpa級冷軋雙相鋼產(chǎn)品噸鋼利潤約為1000元,按照年銷售1000噸計算,可實現(xiàn)年新增利潤100萬元。因此本發(fā)明設(shè)計的鋼種性能優(yōu)異,具有良好的應(yīng)用前景,并且生產(chǎn)成本低廉,產(chǎn)品附加值高,適合市場推廣。附圖說明圖1為實施例1獲得的冷軋雙相鋼鋼板的金相組織照片;圖2為實施例2獲得的冷軋雙相鋼鋼板的金相組織照片。具體實施方式以下通過實施例結(jié)合附圖對本發(fā)明進行詳細說明。本實施例旨在提供一種冷彎性能優(yōu)異的980mpa級冷軋雙相鋼鋼板及其制備方法,冷軋雙相鋼鋼板的化學(xué)成分及重量百分比為:c0.10~0.12%;si0.45~0.65%;mn2.4~2.6%;cr0.35~0.45%;nb0.05~0.075%;ti0.06~0.10%;als0.055-0.075%;p≤0.008%;s≤0.002%;n≤0.003%,余量為fe和不可避免的雜質(zhì)。所述冷彎性能優(yōu)異的980mpa級冷軋雙相鋼鋼板采用如下的方法進行制備:(1)冶煉工序:可采用轉(zhuǎn)爐、電爐或感應(yīng)爐冶煉;(2)lf精煉與rh精煉工序;(3)連鑄工序:在此工序中投入動態(tài)輕壓下和電磁攪拌系統(tǒng),電磁攪拌使得雜質(zhì)上浮以獲得好的鑄坯內(nèi)部質(zhì)量;(4)熱連軋工序:鑄坯經(jīng)1250~1350℃加熱,由粗軋機進行5~20道次軋制,熱軋到30~50mm厚度規(guī)格,由熱連軋機組進行5~7道次軋制,軋至6~10mm厚度后,以80~100℃/s的速度快速冷卻,在500-650℃范圍內(nèi)進行卷取成鋼卷;(5)酸洗冷軋工序:將熱軋帶鋼經(jīng)鹽酸槽酸洗,去除表面氧化鐵皮后,進行冷連軋或冷軋,冷軋壓下率為40~50%,軋至0.8~2mm;(6)連續(xù)退火工序:將酸洗冷軋步驟處理好的鋼板,以5-15℃/s加熱至170℃后,快速升溫至770~810℃,保溫90~160s,以6~10℃/s的速度冷至725~750℃后,以36~60℃/s的冷卻速度快速冷卻至在280~320℃,過時效處理410~700s后,冷至20~30℃室溫。實施例1一種冷彎性能優(yōu)異的980mpa級冷軋雙相鋼鋼板,其化學(xué)成分及重量百分比如表1中的實施例1所示。其制備方法如下:(1)冶煉工序:采用轉(zhuǎn)爐冶煉;(2)lf精煉與rh精煉工序;(3)連鑄工序:在此工序中投入動態(tài)輕壓下和電磁攪拌系統(tǒng),電磁攪拌使得雜質(zhì)上浮以獲得好的鑄坯內(nèi)部質(zhì)量;(4)熱連軋工序:鑄坯經(jīng)1300℃加熱,由粗軋機進行8道次軋制,熱軋到50mm厚度規(guī)格,由熱連軋機組進行7道次軋制,軋至10mm厚度后,以85℃/s的速度快速冷卻,在635℃進行卷取成鋼卷;(5)酸洗冷軋工序:將熱軋帶鋼經(jīng)鹽酸槽酸洗,去除表面氧化鐵皮后,進行冷連軋或冷軋,冷軋壓下率為49%,軋至1.8mm;(6)連續(xù)退火工序:將酸洗冷軋步驟處理好的鋼板,以12℃/s加熱至170℃后,快速升溫至780℃,保溫120s,以6℃/s的速度冷至740℃后,以55℃/s的冷卻速度快速冷卻至310℃,過時效處理500s后,冷至20~30℃室溫。依照上述制備方法得到的冷軋雙相鋼鋼板為馬氏體加鐵素體組織,如圖1所示,其晶粒度等級為12級。表1各實施例冷軋雙相鋼鋼板的化學(xué)成分實施例1實施例2實施例3實施例4c0.11%0.12%0.10%0.12%si0.50%0.46%0.60%0.62%mn2.5%2.49%2.6%2.55%cr0.40%0.36%0.43%0.38%nb0.06%0.06%0.07%0.065%ti0.08%0.09%0.07%0.10%als0.060%0.065%0.057%0.074%p0.005%0.006%0.007%0.008%s0.001%0.0020.0015%0.002%n0.001%0.0010.002%0.003%實施例2一種冷彎性能優(yōu)異的980mpa級冷軋雙相鋼鋼板,其化學(xué)成分及重量百分比如表1中的實施例1所示。其制備方法如下:(1)冶煉工序:采用轉(zhuǎn)爐冶煉;(2)lf精煉與rh精煉工序;(3)連鑄工序:在此工序中投入動態(tài)輕壓下和電磁攪拌系統(tǒng),電磁攪拌使得雜質(zhì)上浮以獲得好的鑄坯內(nèi)部質(zhì)量;(4)熱連軋工序:鑄坯經(jīng)1250℃加熱,由粗軋機進行10道次軋制,熱軋到45mm厚度規(guī)格,由熱連軋機組進行7道次軋制,軋至8mm厚度后,以85℃/s的速度快速冷卻,在550℃進行卷取成鋼卷;(5)酸洗冷軋工序:將熱軋帶鋼經(jīng)鹽酸槽酸洗,去除表面氧化鐵皮后,進行冷連軋或冷軋,冷軋壓下率為47%,軋至1.8mm;(6)連續(xù)退火工序:將酸洗冷軋步驟處理好的鋼板,以6℃/s加熱至170℃后,快速升溫至790℃,保溫90s,以7℃/s的速度冷至730℃后,以40℃/s的冷卻速度快速冷卻至在290℃,過時效處理420s后,冷至20~30℃室溫。依照上述制備方法得到的冷軋雙相鋼鋼板為馬氏體加鐵素體組織,如圖2所示,其晶粒度等級為12.5級。實施例3一種冷彎性能優(yōu)異的980mpa級冷軋雙相鋼鋼板,其化學(xué)成分及重量百分比如表1中的實施例1所示。其制備方法如下:(1)冶煉工序:采用轉(zhuǎn)爐冶煉;(2)lf精煉與rh精煉工序;(3)連鑄工序:在此工序中投入動態(tài)輕壓下和電磁攪拌系統(tǒng),電磁攪拌使得雜質(zhì)上浮以獲得好的鑄坯內(nèi)部質(zhì)量;(4)熱連軋工序:鑄坯經(jīng)1350℃加熱,由粗軋機進行14道次軋制,熱軋到40mm厚度規(guī)格,由熱連軋機組進行6道次軋制,軋至6mm厚度后,以90℃/s的速度快速冷卻,在580℃進行卷取成鋼卷;(5)酸洗冷軋工序:將熱軋帶鋼經(jīng)鹽酸槽酸洗,去除表面氧化鐵皮后,進行冷連軋或冷軋,冷軋壓下率為45%,軋至1.6mm;(6)連續(xù)退火工序:將酸洗冷軋步驟處理好的鋼板,以9℃/s加熱至170℃后,快速升溫至805℃,保溫100s,以9℃/s的速度冷至745℃后,以45℃/s的冷卻速度快速冷卻至在300℃,過時效處理450s后,冷至20~30℃室溫。實施例4一種冷彎性能優(yōu)異的980mpa級冷軋雙相鋼鋼板,其化學(xué)成分及重量百分比如表1中的實施例1所示。其制備方法如下:(1)冶煉工序:采用轉(zhuǎn)爐冶煉;(2)lf精煉與rh精煉工序;(3)連鑄工序:在此工序中投入動態(tài)輕壓下和電磁攪拌系統(tǒng),電磁攪拌使得雜質(zhì)上浮以獲得好的鑄坯內(nèi)部質(zhì)量;(4)熱連軋工序:鑄坯經(jīng)1300℃加熱,由粗軋機進行20道次軋制,熱軋到30mm厚度規(guī)格,由熱連軋機組進行5道次軋制,軋至6mm厚度后,以98℃/s的速度快速冷卻,在575℃進行卷取成鋼卷;(5)酸洗冷軋工序:將熱軋帶鋼經(jīng)鹽酸槽酸洗,去除表面氧化鐵皮后,進行冷連軋或冷軋,冷軋壓下率為42%,軋至1.4mm;(6)連續(xù)退火工序:將酸洗冷軋步驟處理好的鋼板,以15℃/s加熱至170℃后,快速升溫至765℃,保溫150s,以10℃/s的速度冷至780℃后,以50℃/s的冷卻速度快速冷卻至在315℃,過時效處理600s后,冷至20~30℃室溫。以上各實施例公開的冷軋雙相鋼鋼板的力學(xué)性能參數(shù)如表2所示。從表2可以看出,根據(jù)本發(fā)明公開的方法制備得到的冷軋雙相鋼鋼板在具有較薄厚度的同時,具有較高的強度,其屈服強度可以達到810~850mpa,抗拉強度在980mpa以上,延伸率20%~30%,冷彎性能在2a以下。表2各實施例冷軋雙相鋼鋼板的力學(xué)性能參數(shù)實施例1實施例2實施例3實施例4成品厚度(mm)1.81.81.61.4屈服強度(mpa)825810830850抗拉強度(mpa)1080109610851025延伸率(%)15131817180°冷彎0.5a1a1.5a1a擴孔率(%)55585659上述參照實施例對冷彎性能優(yōu)異的980mpa級冷軋雙相鋼鋼板進行的詳細描述,是說明性的而不是限定性的,可按照所限定范圍列舉出若干個實施例,因此在不脫離本發(fā)明總體構(gòu)思下的變化和修改,應(yīng)屬本發(fā)明的保護范圍之內(nèi)。當前第1頁12