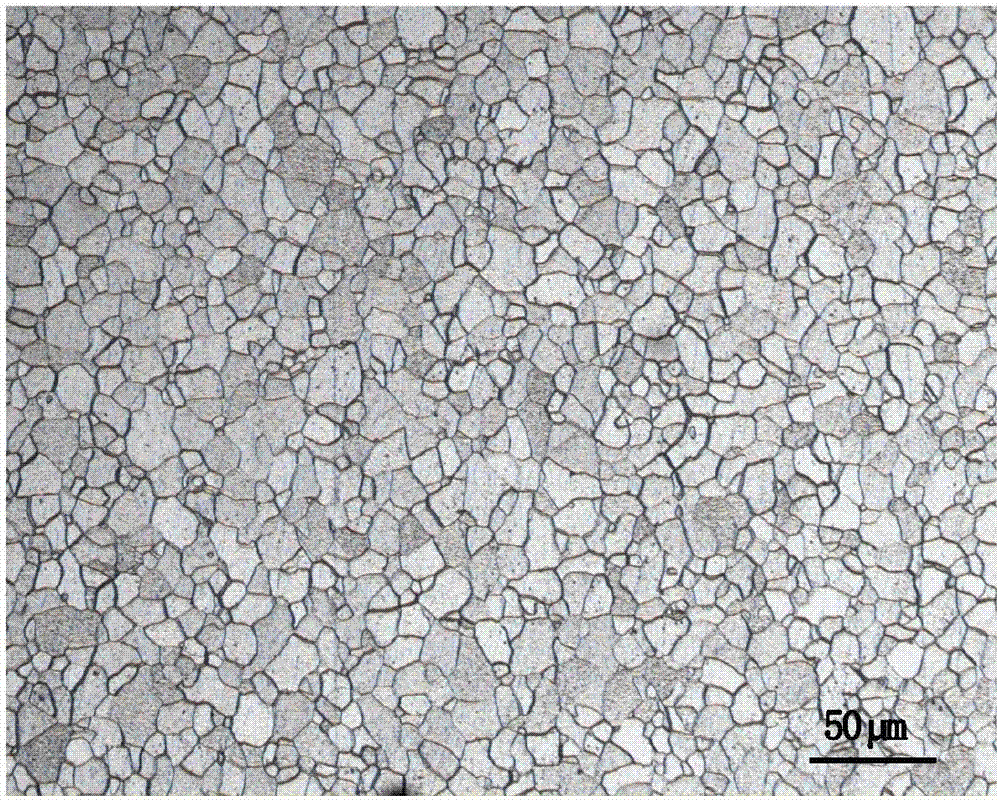
本發(fā)明屬于超低碳鋼板生產(chǎn)
技術(shù)領(lǐng)域:
,具體涉及一種極低屈服強(qiáng)度鋼板及其生產(chǎn)方法。
背景技術(shù):
:眾所周知,冷軋?zhí)妓亟Y(jié)構(gòu)鋼板是重要的工程結(jié)構(gòu)材料之一,其成形后主要用于汽車工業(yè)、建筑結(jié)構(gòu)、壓力容器、橋梁結(jié)構(gòu)及機(jī)械制造之中。影響工程結(jié)構(gòu)安全的因素主要包括兩方面,一方面是結(jié)構(gòu)設(shè)計(jì),另一方面是材料性能。工程結(jié)構(gòu)在遭受震動、撞擊或者其他意外工況時,如果結(jié)構(gòu)設(shè)計(jì)連接強(qiáng)度不能承載變形,那么就需要材料強(qiáng)度的協(xié)同承載力。提高結(jié)構(gòu)設(shè)計(jì)承載強(qiáng)度的最有效方法就是增加結(jié)構(gòu)件尺寸,然而這會增加成本。因此增加材料的使用性能成為了現(xiàn)行工程結(jié)構(gòu)材料最大的發(fā)展趨勢,這就對其的強(qiáng)度、塑性提出了更高的要求。目前,在冷軋汽車用鋼市場上,客戶為了保證成形性能節(jié)約成本,逐步將多步成形工藝簡化,力求一步成形。屈強(qiáng)比是衡量金屬材料成型性的關(guān)鍵指標(biāo),金屬材料塑性變形時,屈強(qiáng)比越低,材料從開始塑性變形到斷裂所需要的形變能就越大,從而其協(xié)調(diào)變形的能力越強(qiáng)。因此客戶對屈強(qiáng)比提出了更高的要求,隨著鋼材的品質(zhì)改進(jìn)和市場需求,低屈強(qiáng)比成為一些工程材料的重要技術(shù)指標(biāo)之一。為了保證較低的屈強(qiáng)比,生產(chǎn)上對鋼的化學(xué)成分和生產(chǎn)工藝做了多方面的改進(jìn),主要途徑通常有兩方面:一方面是提高碳含量,但是這樣會使碳當(dāng)量增加,影響焊接性能;另一方面是提高終軋溫度或者卷取溫度,這會使晶粒尺寸增大,但是會同時降低抗拉強(qiáng)度。因此,優(yōu)化成分和生產(chǎn)工藝,生產(chǎn)出在保證強(qiáng)度和焊接性能的前提下,極低屈強(qiáng)比的產(chǎn)品具有實(shí)際而重要的意義。日本是首先研發(fā)低屈服強(qiáng)度鋼的國家,國內(nèi)的研發(fā)企業(yè)主要有寶鋼、首鋼、鞍鋼、武鋼等等,具體專利如下:公開號為“jp55104429a”和“jp2004339548”等專利,公開的都是屈服強(qiáng)度較低、延伸率較高的低合金結(jié)構(gòu)鋼。在成分設(shè)計(jì)上以c-si-mn為基礎(chǔ)添加了cr、mo、ni、cu、b等合金中的一種或者多種,屈服強(qiáng)度范圍在180-260mpa。公開號為“jp05214442a”和“jp06235042a”等專利,公開的低屈服點(diǎn)鋼板屈服強(qiáng)度在130mpa以下。就成分設(shè)計(jì)而言,都采用在低c-si-mn的基礎(chǔ)上添加微合金元素設(shè)計(jì),同時還加入了b、nb等成分,就生產(chǎn)工藝而言,均較復(fù)雜。公開號為“cn104233061”的專利公開了一種屈服強(qiáng)度在225mpa的低屈服鋼及其制造方法,該發(fā)明采用c-si-mn的成分設(shè)計(jì),無其他合金元素的添加。該發(fā)明將成分設(shè)計(jì)和工藝控制較好的結(jié)合起來,生產(chǎn)經(jīng)濟(jì)型的低屈服鋼板。但是該種方法容易出現(xiàn)混晶、軋制溫度窗口窄等問題,并且其屈強(qiáng)比為60%,較高。公開號為“cn101845589”和“jp10324918a”的專利,均公布了一種極低屈服點(diǎn)鋼板及其制造方法,其屈服強(qiáng)度在140mpa左右。發(fā)明均在低c-si-mn的基礎(chǔ)上添加n、ti、nb中的一種或者多種,并含有b元素。然而b的添加不僅提高了鋼板的制造成本、增加了冶煉難度,并且不利于鋼板的焊接和沖擊性能。公開號為“101514426a”的專利公開了一種屈服強(qiáng)度100mpa級的低屈服鋼及其制造方法,該發(fā)明采用c-si-mn的成分設(shè)計(jì),添加微量ti元素合金化。有本發(fā)明相比,專利101514426a”的碳當(dāng)量較高,焊接性能較差。。技術(shù)實(shí)現(xiàn)要素:本發(fā)明提供一種極低屈服強(qiáng)度鋼板及其生產(chǎn)方法,該鋼板極低屈服強(qiáng)度鋼板具有優(yōu)良的綜合力學(xué)性能,本發(fā)明方法生產(chǎn)成本低、工藝簡單、產(chǎn)品成形性能好,能夠帶來可觀的經(jīng)濟(jì)效益。為解決上述技術(shù)問題,本發(fā)明采用如下技術(shù)方案:一種極低屈服強(qiáng)度鋼板,其特征在于,所述鋼板的化學(xué)質(zhì)量百分比為:c≤0.0050%,si≤0.03%,mn:0.10~0.20%,p≤0.013%,s≤0.012%,als:0.020~0.050%,ti:0.055~0.070%,n≤0.0050%,余量為fe及不可避免雜質(zhì)。本發(fā)明所述鋼板的冷軋卷顯微組織為單一的等軸鐵素體,晶粒尺寸為8~10級。本發(fā)明所述鋼板屈服強(qiáng)度≤110mpa;抗拉強(qiáng)度≥280mpa;斷后伸長率a80≥55%。本發(fā)明所述的成品鋼板的厚度1.5~12mm。本發(fā)明的鋼板化學(xué)成分設(shè)計(jì)思路如下:c通過固溶強(qiáng)化會使屈服強(qiáng)度升高、延伸率降低,并且過多的c會影響焊接性能,控制其含量≤0.005%。si為脫氧元素,也是固溶強(qiáng)化元素,使屈服強(qiáng)度升高、延伸率降低,控制其含量在0.02%以下。mn是鋼中常見的強(qiáng)化元素,通過固溶強(qiáng)化提高屈服強(qiáng)度、使延伸率降低,控制其含量在0.1-0.2%。p、s能夠提高強(qiáng)度,并使得鋼板變脆、影響韌性,作為雜質(zhì)元素控制其含量在0.012%以下。al是脫氧必需的元素,但也會提高鋼的強(qiáng)度,控制其含量在0.01-0.05%。n的固溶能夠顯著提高鋼的強(qiáng)度,控制其含量在0.005%以下。ti是強(qiáng)烈的鐵素體形成元素,也是強(qiáng)脫氧劑,使鋼中生成較多的ti的氮化物或碳化物。該ti的碳、氮化物的存在,可以在后期的軋制和熱處理過程中阻止奧氏體晶粒的長大,從而改善鋼的強(qiáng)度和沖擊韌性。并且ti的氮化物或碳化物的存在還可以通過阻止熱影響區(qū)的晶粒長大,進(jìn)而有效提高焊接性能??刂破浜?.055-0.070%。本發(fā)明的另一目的在于提供上述一種極低屈服強(qiáng)度鋼板的生產(chǎn)方法,所述生產(chǎn)方法包括冶煉工序、連鑄工序、熱軋工序和退火工序。本發(fā)明所述冶煉工序采用轉(zhuǎn)爐冶煉,通過頂?shù)讖?fù)吹,充分脫碳,使用lf精煉進(jìn)行脫氧脫硫合金化,采用rh精煉降低有害氣體n、h含量,最后上板坯連鑄。本發(fā)明所述熱軋工序,粗軋軋制道次5道次,中間坯厚度40~48mm;精軋軋制道次7道次,道次壓下率≥10%,總壓下率≥75%。本發(fā)明所述熱軋工序,在完全再結(jié)晶溫度范圍內(nèi)連續(xù)軋制,軋前連鑄坯加熱溫度1230~1270℃,駐爐時間120~160min,出爐溫度1130~1150℃;精軋進(jìn)口溫度1030~1070℃,終軋溫度885~915℃,卷取溫度705~735℃。本發(fā)明所述熱軋工序,卷取溫度層冷過程開啟u形卷取模式,帶鋼頭尾30米處高出卷取溫度20℃;軋后采用前段快冷,冷速10~20℃/s,上下水比控制在1:1。本發(fā)明所述退火工序,采用罩式退火爐,熱點(diǎn)/冷點(diǎn)溫度為680±20℃/620±20℃,延伸率控制1.0%。采用上述技術(shù)方案所產(chǎn)生的有益效果在于:1、本發(fā)明提供的極低屈服強(qiáng)度鋼板具有優(yōu)良的綜合力學(xué)性能,鋼板的晶粒尺寸達(dá)到8~10級,屈服強(qiáng)度≤110mpa,抗拉強(qiáng)度≥280mpa,斷后伸長率a80≥55%,具有優(yōu)良的塑性變形能力;2、本發(fā)明提供的極低屈服強(qiáng)度鋼板具有良好的焊接性能,其低碳當(dāng)量成分設(shè)計(jì)保證了鋼板具有良好的焊接性能;3、本發(fā)明方法以低c+mn的基本成分、單加微合金ti元素,采用控軋控冷軋制工藝和罩式退火工藝,生產(chǎn)工藝簡單投入小,適用于企業(yè)大規(guī)模低成本生產(chǎn)。附圖說明圖1實(shí)施例1鋼帶的邊部200倍顯微金相組織圖;圖2實(shí)施例1鋼帶的心部200倍顯微金相組織圖;圖3實(shí)施例2鋼帶的邊部200倍顯微金相組織圖;圖4實(shí)施例2鋼帶的心部200倍顯微金相組織圖;圖5實(shí)施例3鋼帶的邊部200倍顯微金相組織圖;圖6實(shí)施例3鋼帶的心部200倍顯微金相組織圖;圖7實(shí)施例4鋼帶的邊部200倍顯微金相組織圖;圖8實(shí)施例4鋼帶的心部200倍顯微金相組織圖。具體實(shí)施方式下面結(jié)合附圖和具體實(shí)施例對本發(fā)明作進(jìn)一步的詳細(xì)描述。實(shí)施例1一種極低屈服強(qiáng)度鋼板,厚度3mm,化學(xué)成分組成見表1,余量為fe和不可避免雜質(zhì)元素。上述極低屈服強(qiáng)度鋼板生產(chǎn)方法包括:冶煉工序、連鑄工序、熱軋工序和退火工序。具體過程如下:1)冶煉及連鑄工序:按預(yù)定成分冶煉鋼水,冶煉工序采用轉(zhuǎn)爐冶煉,通過頂?shù)讖?fù)吹,充分脫碳,使用lf精煉進(jìn)行脫氧脫硫合金化,采用rh精煉降低有害氣體n、h含量,最后上板坯連鑄。連鑄獲得210mm厚度規(guī)格連鑄坯。2)熱軋工序:冷卻后的連鑄坯進(jìn)行加熱,均熱溫度1250℃,駐爐時間120min,出爐溫度1150℃;粗軋軋制道次5道次,中間坯厚度40mm;精軋軋制道次7道次,道次壓下率10%,總壓下率92%;精軋進(jìn)口溫度1070℃,終軋溫度900℃;卷取溫度730℃,卷取溫度層冷過程開啟u形卷取模式,帶鋼頭尾30米處高出卷取溫度20℃;軋后采用前段快冷,冷速10℃/s,上下水比控制在1:1。3)退火工序:熱點(diǎn)/冷點(diǎn)溫度690/630℃,拉矯機(jī)延伸率控制1.0%。獲得鋼板力學(xué)性能見表2。鋼板的冷軋卷顯微組織為等軸鐵素體,晶粒尺寸為8級。實(shí)施例2一種極低屈服強(qiáng)度鋼板,厚度9mm,化學(xué)成分組成見表1,余量為fe和不可避免雜質(zhì)元素。上述極低屈服強(qiáng)度鋼板生產(chǎn)方法包括:冶煉工序、連鑄工序、熱軋工序和退火工序。具體過程如下:1)冶煉及連鑄工序:按預(yù)定成分冶煉鋼水,冶煉工序采用轉(zhuǎn)爐冶煉,通過頂?shù)讖?fù)吹,充分脫碳,使用lf精煉進(jìn)行脫氧脫硫合金化,采用rh精煉降低有害氣體n、h含量,最后上板坯連鑄。連鑄獲得210mm厚度規(guī)格連鑄坯。2)熱軋工序:冷卻后的連鑄坯進(jìn)行加熱,均熱溫度1250℃,駐爐時間140min,出爐溫度1140℃。粗軋軋制道次5道次,中間坯厚度46mm;精軋軋制道次7道次,道次壓下率12%,總壓下率80%;控軋控冷軋制工序:精軋進(jìn)口溫度1040℃,終軋溫度885℃;卷取溫度705℃,卷取溫度層冷過程開啟u形卷取模式,帶鋼頭尾30米處高出卷取溫度20℃。軋后采用前段快冷,冷速12℃/s,上下水比控制在1:1。3)退火工序:罩退工序中,熱點(diǎn)/冷點(diǎn)溫度670/610℃,拉矯機(jī)延伸率控制0.7%。獲得鋼板力學(xué)性能見表2。鋼板的冷軋卷顯微組織為等軸鐵素體,晶粒尺寸為9級。實(shí)施例3一種極低屈服強(qiáng)度鋼板,厚度1.5mm,化學(xué)成分組成見表1,余量為fe和不可避免雜質(zhì)元素。上述極低屈服強(qiáng)度鋼板生產(chǎn)方法包括:冶煉工序、連鑄工序、熱軋工序和退火工序。具體過程如下:1)冶煉及連鑄工序:按預(yù)定成分冶煉鋼水,冶煉工序采用轉(zhuǎn)爐冶煉,通過頂?shù)讖?fù)吹,充分脫碳,使用lf精煉進(jìn)行脫氧脫硫合金化,采用rh精煉降低有害氣體n、h含量,最后上板坯連鑄。連鑄獲得210mm厚度規(guī)格連鑄坯。2)熱軋工序:冷卻后的連鑄坯進(jìn)行加熱,均熱溫度1270℃,駐爐時間120min,出爐溫度1150℃;粗軋軋制道次5道次,中間坯厚度40mm;精軋軋制道次7道次,軋制道次壓下率11%,總壓下率96%;精軋進(jìn)口溫度1070℃,終軋溫度890℃;卷取溫度735℃,卷取溫度層冷過程開啟u形卷取模式,帶鋼頭尾30米處高出卷取溫度20℃。軋后采用前段快冷,冷速20℃/s,上下水比控制在1:1。3)退火工序:罩退工序中,熱點(diǎn)/冷點(diǎn)溫度660/600℃,拉矯機(jī)延伸率控制0.6%。獲得鋼板力學(xué)性能見表2。鋼板的冷軋卷顯微組織為等軸鐵素體,晶粒尺寸為8級。實(shí)施例4一種極低屈服強(qiáng)度鋼板,厚度12mm,化學(xué)成分組成見表1,余量為fe和不可避免雜質(zhì)元素。上述極低屈服強(qiáng)度鋼板生產(chǎn)方法包括:冶煉工序、連鑄工序、熱軋工序和退火工序。具體過程如下:1)冶煉及連鑄工序:按預(yù)定成分冶煉鋼水,冶煉工序采用轉(zhuǎn)爐冶煉,通過頂?shù)讖?fù)吹,充分脫碳,使用lf精煉進(jìn)行脫氧脫硫合金化,采用rh精煉降低有害氣體n、h含量,最后上板坯連鑄。連鑄獲得210mm厚度規(guī)格連鑄坯。2)熱軋工序:冷卻后的連鑄坯進(jìn)行加熱,均熱溫度1230℃,駐爐時間160min,出爐溫度1130℃;粗軋軋制道次5道次,中間坯厚度48mm;精軋軋制道次7道次,道次壓下率10%,總壓下率75%;控軋控冷軋制工序:精軋進(jìn)口溫度1030℃,終軋溫度915℃;卷取溫度705℃,卷取溫度層冷過程開啟u形卷取模式,帶鋼頭尾30米處高出卷取溫度20℃。軋后采用前段快冷,冷速10℃/s,上下水比控制在1:1。3)退火工序:罩退工序中,熱點(diǎn)/冷點(diǎn)溫度700/640℃,拉矯機(jī)延伸率控制1.0%。獲得鋼板力學(xué)性能見表2。鋼板的冷軋卷顯微組織為等軸鐵素體,晶粒尺寸為10級。表1實(shí)施例1-4鋼的化學(xué)成分(wt%)序號csimnpsalstin實(shí)施例10.0040.0150.160.0100.0100.0360.0600.002實(shí)施例20.0030.0200.130.0090.0100.0330.0580.003實(shí)施例30.0050.0300.100.0080.0120.0500.0700.005實(shí)施例40.00450.0250.200.0130.0080.0200.0550.004表2實(shí)施例1-4鋼板的綜合力學(xué)性能序號位置屈服強(qiáng)度/mpa抗拉強(qiáng)度/mpa屈強(qiáng)比延伸率a80/%實(shí)施例11/41062980.3658實(shí)施例21/41002860.3561實(shí)施例31/41083030.3659實(shí)施例41/41102800.3955從上表可以看出,本發(fā)明提供的極低屈服強(qiáng)度鋼板具有穩(wěn)定的屈服強(qiáng)度,在不同的軋制工藝下,各種厚度鋼板的屈服強(qiáng)度均≤110mpa。本發(fā)明提供的極低屈服強(qiáng)度鋼板還具有很高的延伸率及良好的韌性。以上實(shí)施例僅用以說明而非限制本發(fā)明的技術(shù)方案,盡管參照上述實(shí)施例對本發(fā)明進(jìn)行了詳細(xì)說明,本領(lǐng)域的普通技術(shù)人員應(yīng)當(dāng)理解:依然可以對本發(fā)明進(jìn)行修改或者等同替換,而不脫離本發(fā)明的精神和范圍的任何修改或局部替換,其均應(yīng)涵蓋在本發(fā)明的權(quán)利要求范圍當(dāng)中。當(dāng)前第1頁12