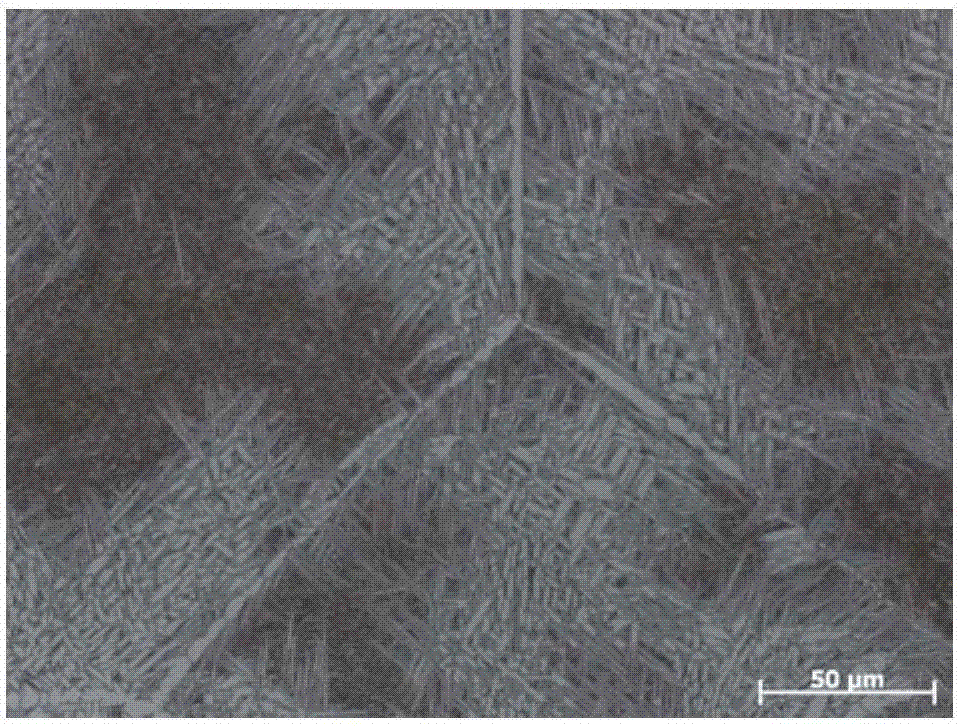
本發(fā)明屬于ti-al金屬間化合物領(lǐng)域,具體涉及到一種在600℃~700℃下長時使用(≥500小時)或在650℃~750℃范圍內(nèi)短時使用的新型鑄態(tài)強韌ti3al金屬間化合物其制造方法和應(yīng)用。
背景技術(shù):
:為了提高航空發(fā)動機的推重比,需要重點突破發(fā)動機部件的氣動設(shè)計、結(jié)構(gòu)設(shè)計、材料、工藝等方面的關(guān)鍵技術(shù),減輕發(fā)動機結(jié)構(gòu)重量的主要途徑之一是盡可能多的采用輕質(zhì)材料,但是目前變形鈦合金最高使用溫度為600℃,鑄造鈦合金最高使用溫度僅為500℃,使用溫度限制了鈦合金使用范圍的擴大。ti3al合金密度較低(小于5g/cm3)、比強度和比剛度較高,工作溫度可達650℃,以ti3al基合金代替高溫合金合金,并采用精密鑄造的工藝路線制備復(fù)雜形狀高溫部件可以從重量和結(jié)構(gòu)上同時減輕航空發(fā)動機重量,實現(xiàn)航空發(fā)動機驗證機高推重比的技術(shù)指標,具有十分重要的現(xiàn)實意義。目前,航空發(fā)動機高溫構(gòu)件主要采用工藝性能優(yōu)異的gh4169合金制備。然而gh4169合金的密度大,不能滿足高推重比發(fā)動機對減重的要求。ti3al合金是一種新材料,經(jīng)近二十年的研發(fā),變形ti3al合金已接近實用化程度,而鑄造ti3al合金的研究起步較晚。ti3al金屬間化合物因密度低,可望拓展鈦合金的使用溫度,因此在20世紀70年代即受到美歐和前蘇聯(lián)等國的普遍重視。經(jīng)近二十幾年的研究,在合金研制方面,合金的塑性得到了明顯改善,先后發(fā)展了ti-24al-11nb(at.%)、ti-25al-10nb-3v-1mo、ti-25al-17nb-1mo、ti-24.5al-12.5nb-1.5mo等ti3al基合金。在成型工藝方面,已制備出合金的棒材、餅材、板材和箔材等工業(yè)半成品,并用其制作了高壓壓氣機機匣、高壓渦輪靜止支撐環(huán)等。在應(yīng)用考核方面,高壓壓氣機匣成功地試車了65小時,高壓渦輪靜止支撐環(huán)也在ge29發(fā)動機上成功地經(jīng)受了試車考核,而加力燃燒室噴口密封片在f100和f404發(fā)動機進行了運轉(zhuǎn)試驗。在國內(nèi),自80年代中期以來,在國家“863”計劃和國家軍品配套項目的支持下,在ti3al合金研制、熱加工工藝和構(gòu)件成型等方面均取得長足的進展,目前已接近實用化程度。國內(nèi)在ti-24al-10nb-3v-1mo合金的基礎(chǔ)上,研制出具有優(yōu)異綜合性能和自主知識產(chǎn)權(quán)的ti3al合金;研發(fā)出適于ti3al合金大尺寸鑄錠真空自耗熔煉技術(shù),建立了相應(yīng)的技術(shù)裝備,具備了熔煉大尺寸ti3al合金鑄錠的能力,研發(fā)出了適于ti3al合金大尺寸鑄錠開坯和鍛造、環(huán)材軋制、板材軋制和構(gòu)件熱模鍛造等技術(shù),成功制備出先進航空發(fā)動機用ti3al合金級間封嚴環(huán)構(gòu)件,模鍛出先進航空發(fā)動機用ti3al合金鍛件,軋制出ti3al合金薄板材和厚度分別為0.7mm、0.5mm和0.1mm的箔材,其中0.5mm厚的ti3al基合金箔材已用于豐田和印度力量一級方程式賽車發(fā)動機排氣系統(tǒng)。技術(shù)實現(xiàn)要素:本發(fā)明的目的在于提供一種新型鑄態(tài)強韌ti3al金屬間化合物其制造方法和應(yīng)用,該合金在具有高拉伸強度、高疲勞強度的同時,還具有高塑性、可接受的熱穩(wěn)定性及優(yōu)良的抗氧化性能。本發(fā)明的技術(shù)方案是:一種鑄態(tài)強韌ti3al金屬間化合物,按重量百分比計,所說的合金成分為:al:10.2%~11.8%,nb:26.0%~29.0%,mo:1.0%~3.0%,余量為ti和不可避免的雜質(zhì)元素;其中,不可避免的雜質(zhì)元素為fe、si、o、n、h,fe≤0.3%,si≤0.3%,o≤0.15%,n≤0.04%,h≤0.01%。所述的鑄態(tài)強韌ti3al金屬間化合物的制造方法,冶煉工藝如下:原材料采用0~1級海綿鈦,合金元素mo、nb以中間合金形式加入;合金元素al部分由中間合金帶入,不足部分以純al加入;中間合金與海綿鈦經(jīng)配料、混料后,用壓機壓制成電極;將電極組焊在一起,在真空自耗電弧爐中熔煉1~3次,制成合金鑄錠;合金鑄錠再經(jīng)一次真空凝殼熔煉和一次真空懸浮熔煉,澆鑄成合金母材或精密鑄件;或者,合金鑄錠直接進入真空懸浮熔煉,澆鑄成合金母材或精密鑄件。所述的鑄態(tài)強韌ti3al金屬間化合物的制造方法,采用鑄造成形后進行熱處理,熱處理工藝為:熱等靜壓壓力110~150mpa,溫度為1020±20℃,時間為1~3小時,隨爐冷至300℃以下出爐;然后,在980~1040℃固溶熱處理0.5~2h,冷速根據(jù)性能要求在爐冷至空冷冷速范圍內(nèi)變化。所述的鑄態(tài)強韌ti3al金屬間化合物的制造方法,固溶熱處理后進行時效處理,在700℃~800℃保溫2~8h,隨后空冷或爐冷。所述的鑄態(tài)強韌ti3al金屬間化合物的應(yīng)用,通過成分優(yōu)化和熱處理工藝組合,獲得拉伸強度與塑性、疲勞強度強度與熱穩(wěn)定性的不同匹配,該合金用于制作先進航空發(fā)動機高溫部位的精密鑄件,在600~700℃范圍內(nèi)長時使用;或者,該合金用于制作航天飛行器耐高溫結(jié)構(gòu)件,在650℃~750℃范圍內(nèi)短時使用。本發(fā)明的耐熱鈦合金中合金元素種類及其成分范圍的選擇,是經(jīng)過多年的深入研究和反復(fù)實驗而得出的,其設(shè)計思想分別說明如下:鋁(al):10.2wt%~11.8wt%。al是耐熱鈦合金最常用的一種強化元素,具有穩(wěn)定α相和提高α→β相轉(zhuǎn)變溫度的作用,提高al含量可明顯提高鈦合金的室溫、高溫、蠕變和持久強度,但對鈦合金塑性和熱穩(wěn)定性有不利影響;當(dāng)al含量增加導(dǎo)致ti3al脆性有序相析出時,材料塑性(包括工藝塑性)、韌性尤其是熱穩(wěn)定性會顯著降低,最后可能導(dǎo)致材料不適于在航空下長時使用。對于ti3al基金屬間化合物,降低al含量可提高合金強度,但對合金的抗氧化性和熱定性有不利影響。本發(fā)明鈦合金成分體系內(nèi),將al含量嚴格控制在10.2wt%~11.8wt%之間,可獲得本發(fā)明所主張的高耐熱性,同時保證材料有可接受的塑性。鈮(nb):26.0%~29.0%。在ti-al-nb系合金中,nb元素既是重要的β相穩(wěn)定元素,又是ti3al合金中o相的析出的主要參與元素。當(dāng)α2相中nb含量過飽和時,在固溶引起的應(yīng)變能驅(qū)動下,α2相將分解為nb元素的富集區(qū)和貧乏區(qū),通過其富集區(qū)中α2相點陣常數(shù)發(fā)生變化,原子排列可進一步有序化進而形成o相。鉬(mo):1.5%~2.2%。mo是鈦合金中最常用的強β穩(wěn)定元素,也是有效的強化元素。ti3al金屬間化合物中加入少量mo可使其在提高基體強度的同時,提高合金的蠕變和持久性能;mo元素的存在還可改善材料的熱加工工藝性能。研究表明,在0.96wt%以下時,mo含量增加可明顯提高鈦合金的拉伸強度,對熱穩(wěn)定性總體來看沒有明顯不利影響,還可降低熱穩(wěn)定性對熱處理制度的敏感度;在0.64wt%以下,含mo元素的合金還可通過熱處理使蠕變和持久性能在一個比較寬的范圍內(nèi)變化,滿足不同的使用需求。鐵(fe)、硅(si)、氧(o)、氮(n)、氫(h)等雜質(zhì)元素在鈦合金中以間隙原子的形式存在,它們對鈦合金基體有顯著的強化效果,但對合金的塑性、韌性及熱穩(wěn)定性有明顯的不利影響。但o元素是一種強α穩(wěn)定元素,其含量會隨原材料、熔煉方法、工藝及熔煉次數(shù)有較大變化,該元素對高溫鈦合金塑性、韌性和熱穩(wěn)定性有非常不利的影響。研究發(fā)現(xiàn),要實現(xiàn)本發(fā)明所主張的高塑性、韌性及熱穩(wěn)定性,o含量必須在0.15wt%以下,低于其它常規(guī)鈦合金要求的控制水平。本發(fā)明的優(yōu)點及有益效果是:1、本發(fā)明的ti3al金屬間化合物用于航空發(fā)動機部件時要求具有靜強度、塑性、熱穩(wěn)定性、抗氧化性和疲勞性能的良好匹配,為此需要采用綜合性能較好的鑄態(tài)組織。而鑄態(tài)組織中初生α2相體積分數(shù)、尺寸、次生α2相厚度及長寬比等顯微組織特征參數(shù)與固溶溫度和隨后的冷速密切相關(guān)。研究發(fā)現(xiàn),控制α2相體積分數(shù)在25%~40%之間,根據(jù)坯料尺寸確定合適的冷卻方式,可以使上述性能獲得最佳匹配,因此確定了處于α2+β兩相區(qū)的960~1040℃固溶后緩冷的熱處理制度。2、本發(fā)明的合金所設(shè)計的強化方式是采用固溶和析出相強化,析出相為二次ti3al彌散強化相和少量o相,需要在較低溫度熱處理才能實現(xiàn)強化必須的“有效”析出。研究發(fā)現(xiàn),在700℃~800℃范圍內(nèi),本發(fā)明的合金中二次ti3al相析出緩慢且相對細小,力學(xué)性能波動也在允許和可控范圍內(nèi),因此確定了700~800℃保溫2~8h,隨后空冷或爐冷的時效熱處理制度。3、研究還發(fā)現(xiàn),本發(fā)明的合金采用鑄造+熱等靜壓+固溶時效態(tài)組織,固溶時效處理后可獲得原始晶粒尺寸≤1000μm的片層組織,具有良好的高溫力學(xué)性能(如:疲勞強度及高溫拉伸強度)。4、合金成分可以看作是材料的特性。本發(fā)明是一項選擇性的發(fā)明,其創(chuàng)新點就是在高溫鈦合金傳統(tǒng)ti-al-nb-mo合金體系基礎(chǔ)上,并通過對fe、si、c、o、n、h的嚴格控制來提高材料的室溫塑性,最終通過熱處理工藝合理控制獲得性能匹配的鑄件。附圖說明圖1為本發(fā)明實施例18制備的ti3al合金50倍的光學(xué)顯微鏡照片。圖2為本發(fā)明實施例18制備的ti3al合金200倍的光學(xué)顯微鏡照片。圖3為本發(fā)明實施例1~4制備的ti3al合金的掃描電鏡照片。其中,分別為①al:9.55wt%;②al:10.2wt%;③al:10.9wt%;④al:11.1wt%。圖4為本發(fā)明實施例18制備的ti3al合金20℃下高軸疲勞性能p-s-n曲線。圖5為本發(fā)明實施例18制備的ti3al合金400℃下高軸疲勞性能p-s-n曲線。圖6為本發(fā)明實施例18制備的ti3al合金600℃下高軸疲勞性能p-s-n曲線。圖7為本發(fā)明實施例18制備的ti3al合金650℃下高軸疲勞性能p-s-n曲線。具體實施方式在具體實施過程中,本發(fā)明ti3al金屬間化合物及其制備方法和應(yīng)用,包括合金成分、冶煉、熱加工和熱處理等組成要素。其中:按重量百分比計,所說的合金成分為al:10.2%~11.8%,nb:26.0%~29.0%,mo:1.0%~3.0%,余量為ti和不可避免的雜質(zhì)元素。其中,不可避免的雜質(zhì)元素為fe、si、o、n、h等,fe≤0.3%,si≤0.3%,o≤0.15%,n≤0.04%,h≤0.01%。為了獲得本發(fā)明所主張的強度、塑性、韌性、疲勞性能及熱穩(wěn)定性的良好匹配,本發(fā)明的新型ti3al金屬間化合物材料需采用以下方法制備:冶煉工藝:原材料采用0~1級海綿鈦,合金元素nb、mo以中間合金的形態(tài)加入,含mo中間合金為al-mo,含nb中間合金為al-nb;al除中間合金帶入部分外,不足部分以純al(如:鋁豆或鋁箔等)形態(tài)加入。中間合金與海綿鈦經(jīng)配料、混料后,用壓機壓制成電極。將若干支電極組焊在一起,在真空自耗電弧爐中熔煉1~3次,制成合金鑄錠。合金鑄錠再經(jīng)一次真空凝殼熔煉,一次真空懸浮熔煉,澆鑄成合金母材或精密鑄件。熱處理工藝:熱等靜壓壓力110~150mpa,溫度為1020±20℃,時間為1~3小時,隨爐冷至300℃以下出爐;然后,在960~1040℃固溶熱處理0.5~2h。且控制固溶后不同冷速和700~800℃不同時效熱處理,所述的新型耐熱t(yī)i3al金屬間化合物可獲得拉伸強度與塑性、持久和蠕變強度與熱穩(wěn)定性的不同匹配。經(jīng)過熱處理后,所發(fā)明ti3al金屬間化合物的室溫拉伸性能指標如下:抗拉強度為750~900mpa,屈服強度為600~750mpa,延伸率為2~8%。ti3al金屬間化合物的600℃拉伸性能指標如下:抗拉強度為550~650mpa,屈服強度為400~500mpa,延伸率為10~23%。ti3al金屬間化合物的700℃拉伸性能指標如下:抗拉強度為500~550mpa,屈服強度為350~450mpa,延伸率為9~20%。在本發(fā)明成分范圍內(nèi)的ti3al金屬間化合物,通過上述熔煉和熱處理工藝獲得的顯微組織為層片狀組織,見圖1、2,其特征是原始晶粒尺寸≤1000μm,存在清晰完整的β/b2晶粒邊界,晶界α2相明顯;晶內(nèi)α2相在基體β/b2上呈層片狀析出,二次α2相和o相呈細長針狀,且α2相片片層大小隨著al含量及固溶冷卻速率的變化而改變,宏觀組織中顏色不同的斑點是由于鑄造偏析使α2相析出溫度和生長速率不同造成的。為了獲得更高的強度(屈服強度、抗拉強度),在本發(fā)明ti3al金屬間化合物成分范圍內(nèi)可通過降低al元素含量、提高o元素含量、提高固溶后冷卻速率等方式來實現(xiàn),但這些方式在提高合金強度同時會不同程度的降低合金斷后延伸率,使合金塑性降低;al含量的降低也會弱化合金的抗氧化性,且固溶冷卻速率從爐冷至空冷變化時,顯微組織從粗大片層轉(zhuǎn)變?yōu)榧毿♂槧钇瑢咏M織,合金塑性先升高后降低的變化規(guī)律。從而,通過成分微調(diào)與熱處理工藝組合,本發(fā)明合金獲得拉伸強度與塑性、疲勞強度與熱穩(wěn)定性的不同匹配;該合金用于制作先進航空發(fā)動機高溫部位的精密鑄件,在600~700℃范圍內(nèi)長時使用;該合金也用于制作航天飛行器耐高溫結(jié)構(gòu)件,在650℃~750℃范圍內(nèi)短時使用。下面結(jié)合附圖和實施例對本發(fā)明的新型鑄態(tài)強韌ti3al金屬間化合物及其制造方法作進一步的說明和補充。本發(fā)明所有實施例中的合金均采用的是表1所列出原材料,因此以后在每一實施例中不再一一贅述。但是必需指出的是,在滿足成分控制要求的前提下,還可選擇不限于表1中的其它原材料。表1:本發(fā)明實施例中合金采用的原材料本發(fā)明1#-13#實施例中的鈦合金按設(shè)計的成分配料、混料后,根據(jù)錠型不同,壓制成不同尺寸的電極。將這些電極焊在一起,采用真空自耗爐熔煉1~3次,制成合金鑄錠,合金鑄錠再經(jīng)一次真空凝殼熔煉,一次真空懸浮熔煉,澆鑄成合金母材或精密鑄件。成型后的母材或鑄件經(jīng)熱等靜壓處理,熱等靜壓壓力110~150mpa,溫度為1020±20℃,時間為1~3小時,隨爐冷至300℃以下出爐。經(jīng)熱等靜壓后對樣品進行化學(xué)分析和相變點測試,采用金相法獲得α2+β/β相變點,再按照相關(guān)的要求進行熱處理,制成最終的成品或半成品,進行各項性能測試,數(shù)據(jù)表中每一個數(shù)據(jù)均為2~3個平行試樣的平均值。原料的配置、電極壓型和真空熔煉的程序大都相同,在各實施例中就不再一一重復(fù)敘述了。實施例1#~4#實施例1#~4#的成分列于表2中。鑄錠的熔煉工藝為一次真空自耗熔煉,一次真空凝殼熔煉,一次真空懸浮熔煉,然后在鋼模中澆鑄成φ70mm的鑄棒。鑄棒經(jīng)固溶熱處理后加工試樣,進行力學(xué)性能測試。采用的熱處理制度為:固溶溫度1020℃,固溶時間1h,冷卻速率0.5℃/s。試樣掃描電鏡下顯微組織見圖3,室溫拉伸結(jié)果見表3。表2:實施例1#~4#合金成分實施例合金名義成分(at.%)實測al含量(wt.%)實測o含量(wt.%)1#ti-18.5al-15nb-1mo9.550.0682#ti-19.5al-15nb-1mo10.20.0693#ti-20.5al-15nb-1mo10.90.0674#ti-21al-15nb-1mo11.10.068表3:實施例1#~4#室溫拉伸性能實施例σ0.2,mpaσb,mpaδ,%1#1131.11178.402#959.61068.02.13#696.2932.810.04#711.1918.28.0從圖2可以看出:al含量對析出α2-ti3al相的形態(tài)、體積百分比和分布有很大的影響。當(dāng)al含量最低時(9.55wt.%),析出的初生針狀α2相非常細小,即使在1000倍掃描電鏡下也不易分辨清楚;al含量增大到10.2wt.%時,在晶界附近析出了粗大一些的初生α2相,這是因為晶界作為原子的快速擴散通道,很容易造成成分偏聚,從而優(yōu)先形核,析出粗大的α2相;其它大部分區(qū)域的α2相依然很細??;al含量繼續(xù)增加到10.9wt.%時,析出的粗大初生α2相所占比例增加,分布均勻;當(dāng)al含量為11.1wt.%時,析出的初生α2相尺寸粗大均勻,所占比例進一步增加?;w中固溶冷卻過程析出的次生α2/o相沒有明顯變化,只是在al含量在9.55wt.%時,初生α2相和次生α2/o相尺寸接近不易區(qū)分。經(jīng)能譜分析可知,四種成分的ti3al合金主要由α2相和β/b2相組成,此外還有少量的o相。隨著al含量增加,ti3al基合金中α2相的析出量增加,尺寸增大。由表3可以看到:al元素含量對本發(fā)明鑄態(tài)強韌ti3al金屬間化合物室溫拉伸性能影響非常大。當(dāng)al含量為9.55wt.%時,合金的強度極高,抗拉強度高達1178.4mpa,而延伸率卻極低,幾乎測不出塑性;增加al含量到10.2wt.%,合金的強度大幅度下降,抗拉強度為1068.0mpa,延伸率增加為2.1%;繼續(xù)增加al含量到10.9wt.%,合金的強度繼續(xù)大幅度下降,抗拉強度降到932.8mpa,而延伸率大幅度上升為10.0%;當(dāng)al含量增大到11.1wt.%時,抗拉強度降為918.2mpa,延伸率降低為8.0%,變化不大。因此,在本發(fā)明中一方面,al元素含量的調(diào)控是達到鑄態(tài)強韌ti3al金屬間化合物拉伸強度與塑性不同匹配的重要手段;另一方面,al元素含量的精確控制是本發(fā)明合金性能穩(wěn)定的重要保證。金屬間化合物最大的缺點之一是其室溫脆性,為保證本發(fā)明合金擁有一定的塑性,其al元素含量應(yīng)不低于10.2wt.%。實施例5#~6#實施例5#的名義成分為ti-22al-15nb-0.5mo(at.%),實施例6#的名義成分為ti-22al-15nb-1mo(at.%)。鑄錠的熔煉工藝為二次真空自耗熔煉,一次真空懸浮熔煉,然后在鋼模中澆鑄成φ70mm的鑄棒。鑄棒首先經(jīng)熱等靜壓(hip)處理:熱等靜壓壓力130mpa,溫度為1020±20℃,時間為3小時,隨爐冷至300℃以下出爐。熱等靜壓后對試樣進行不同固溶熱處理后進行力學(xué)性能測試,測試見表4、5。表4:實施例5#~6#室溫拉伸性能表5:實施例5#~6#600℃拉伸性能從表4、5的拉伸性能可以看出,mo含量從0.5at.%變化至1at.%時合金的拉伸強度有明顯的提高,尤其是600℃拉伸強度。因而從提高強度角度考慮,合金應(yīng)提高mo元素含量;但mo元素增加會提高合金的密度及制造成本,本發(fā)明中mo元素含量控制在1.5%~2.2wt.%。從固溶熱處理溫度來看,在較低固溶溫度處理可獲得較高的屈服強度;隨著固溶溫度的升高,合金的室溫抗拉強度先降低后升高,而高溫抗拉強度變化不大。因此,可根據(jù)實際合金的使用要求,固溶熱處理溫度在960~1040℃合理選擇。實施例7#~10#實施例7#~10#的實測成分列于表6中。合金配料中,梯度增加的o元素是以tio2形式加入的,其他合金制備工藝沒有變化。鑄錠的熔煉工藝為一次真空自耗熔煉,一次真空凝殼熔煉,一次真空懸浮熔煉,然后在鋼模中澆鑄成φ70mm的鑄棒。鑄棒經(jīng)固溶熱處理后加工試樣,進行力學(xué)性能測試。采用的熱處理制度為:固溶溫度1020℃,固溶時間1h,冷卻速率0.5℃/s。室溫拉伸結(jié)果見表7。表6:實施例7#~10#合金成分實施例合金名義成分(at.%)實測al含量(wt.%)實測o含量(wt.%)7#ti-21al-15nb-1mo11.10.0688#ti-21al-15nb-1mo11.10.0989#ti-21al-15nb-1mo11.10.12010#ti-21al-15nb-1mo11.10.150表7:實施例7#~10#室溫拉伸性能實施例σ0.2,mpaσb,mpaδ,%7#711.1918.28.08#725.7924.44.49#773.4946.66.110#814.3960.94.0從表7可以看到,o含量在0.068~0.15wt.%之間時,隨著o含量增加合金的強度逐漸增大,而延伸率總體趨勢是降低,只是在中間存在波動,不是單調(diào)下降。雖然o元素是α2相穩(wěn)定元素,但o含量在0.15wt.%以下時,隨著o含量的增加,初生α2相、細小的次生α2/o相和b2相的形態(tài)、分布、所占的體積百分比沒有明顯變化;o元素主要固溶到α2相的八面體間隙中起固溶強化作用。o元素的固溶強化作用并不十分明顯,并會降低合金的塑性。為保證發(fā)明合金擁有一定的塑性,其o元素含量應(yīng)低于0.15wt.%。實施例11#~12#實施例11#的名義成分為ti-22al-15nb-0.5mo-0.4b(at.%),增加的b元素是以tib粉末形式加入的,實施例12#的名義成分為ti-22al-15nb-1mo-0.05si(at.%),增加的si元素是以sio2形式加入的,。鑄錠的熔煉工藝為二次真空自耗熔煉,一次真空懸浮熔煉,然后在鋼模中澆鑄成φ70mm的鑄棒。鑄棒首先經(jīng)熱等靜壓(hip)處理:熱等靜壓壓力130mpa,溫度為1020±20℃,時間為3小時,隨爐冷至300℃以下出爐。熱等靜壓后對試樣進行拉伸性能測試,測試見表8。表8:實施例11#~12#室溫拉伸性能實施例σ0.2,mpaσb,mpaδ,%11#6568292.512#9661073/實施例11#中b元素的添加顯著減小了晶粒尺寸,但根據(jù)表8的拉伸結(jié)果顯示,合金塑性和強度沒有明顯提高。這可能是由于晶界處富集的硼化物為裂紋提供了很好的擴展路徑,抵消了晶粒尺寸降低的效果。因此,b元素的添加雖然可以減小鑄造ti3al合金晶粒尺寸,但對于合金拉伸性能沒有明顯改善。實施例12#中si元素明顯提高了合金的強度,但卻大大降低了合金塑性。si元素雖然固溶強化效果明顯,但是在含量超出0.05at.%時使得合金呈嚴重的穿晶斷裂,塑性降低。因此,為保證合金良好的強度、塑性匹配,應(yīng)嚴格控制si<0.3wt.%。實施例13#實施例13#的名義成分為ti-22al-15nb-1mo(at.%),采用一次真空自耗熔煉,一次真空自耗凝殼熔煉,一次真空懸浮熔煉,然后在熔模中澆鑄成φ70mm的鑄棒。測試其al元素含量為11.8wt.%,o元素含量為0.12wt.%。采用金相法測得的13#合金(α2+b2)/b2相變點約為1095℃。對13#合金進行不同熱處理后室溫拉伸性能見表9。對熱處理制度中出現(xiàn)的符號說明如下:wc代表水淬,冷卻速率大概為120℃/s;ac代表空冷,冷卻速率大概為10℃/s;sc代表包耐火棉緩冷,冷卻速率大概為0.5℃/s;fc代表爐冷,冷卻速率大概為0.3℃/s。表9:13#合金進行不同熱處理后室溫拉伸性能從表9可以看出,不同熱處理制度下可以使本發(fā)明的新型鑄態(tài)強韌ti3al金屬間化合物得到不同的強度塑性匹配。研究不同冷卻速率對合金拉伸性能的影響。從熱處理制度ht1~ht4可以看出,實施例13#合金在相同固溶溫度(1020℃)下,冷卻速率緩慢時合金的強度低,延伸率高;隨著冷卻速率的加快,合金的強度增高,塑性降低。冷卻速率主要影響次生α2/o相的析出與生長形態(tài):冷卻速率較慢時,次生α2/o相析出充分且發(fā)生粗化;冷卻速率較快時,次生α2/o相析出減少或者不析出。析出充分且發(fā)生粗化的次生α2/o相增加了裂紋擴展路徑,合金表現(xiàn)為穿晶斷裂,塑性提高;次生α2/o相析出減少或者不析出時,基體b2相處于過飽和固溶狀態(tài),強度提高,但較高的應(yīng)力集中會使合金發(fā)生沿晶斷裂,塑性降低。為了保證合金一定的塑性,固溶熱處理的冷卻速率應(yīng)選擇適中的冷卻速率。研究不同固溶溫度對合金拉伸性能的影響。從熱處理制度ht2、ht5~ht7可以看出,固溶溫度的改變對合金的室溫拉伸性能沒有明顯的影響。當(dāng)固溶溫度升高時,合金中的初生α2相減少,尺寸增大,冷卻過程中析出的細小次生α2/o相數(shù)量增加尺寸增大,當(dāng)固溶溫度達到1150℃時合金處于β單相區(qū),初生α2相全部溶解到β基體中,其緩慢冷卻過程中析出大量α2/o相。在初生α2相和次生α2/o相共同作用下,使得固溶溫度的改變對合金的室溫拉伸性能沒有明顯的影響。研究不同固溶時間對合金拉伸性能的影響。從熱處理制度ht2、ht8~ht9可以看出,隨著固溶時間延長,合金的強度沒有明顯的變化,延伸率稍微降低。因此,在兩相區(qū)進行固溶熱處理時,固溶時間不宜過長。研究不同時效溫度對合金拉伸性能的影響。從熱處理制度ht2、ht10~ht12可以看出,隨著時效溫度的升高,8#合金強度降低,塑性升高,但700~800℃時效時合金強度要低于固溶熱處理狀態(tài)。這是由于隨著時效溫度提高次生α2/o相尺寸增大,與基體的共格關(guān)系受到破壞并且在固溶冷卻過程中析出的次生α2/o相尺寸也會增大,所以次生α2/o相的強化作用就會減弱,使得合金的室溫強度降低,塑性提高。因此,根據(jù)構(gòu)件的服役溫度應(yīng)選取相應(yīng)的時效溫度保證其性能穩(wěn)定。實施例14#~16#實施例14#~16#的成分列于表10中。鑄錠的熔煉工藝為一次真空自耗熔煉,一次真空凝殼熔煉,一次真空懸浮熔煉,然后在鋼模中澆鑄成φ70mm的鑄棒。鑄棒首先經(jīng)熱等靜壓(hip)處理:熱等靜壓壓力130mpa,溫度為1020±20℃,時間為3小時,隨爐冷至300℃以下出爐,并對一部分熱等靜壓后鑄棒進行拉伸測試。熱等靜壓后另一部分試樣經(jīng)固溶熱處理后進行力學(xué)性能測試。采用的熱處理制度為:固溶溫度1020℃,固溶時間1h,冷卻速率0.5℃/s。鑄棒拉伸結(jié)果見表11。表10:實施例14#~16#合金成分實施例合金名義成分(at.%)實測al含量(wt.%)實測o含量(wt.%)14#ti-21al-15nb-1mo11.20.06815#ti-21al-15nb-1mo11.40.06816#ti-21al-15nb-1mo11.70.068表11:實施例14#~16#合金拉伸性能從表11可以看出,本發(fā)明的新型鑄態(tài)強韌ti3al金屬間化合物當(dāng)al含量在11.2~11.7wt.%變化時,合金的拉伸性能較為穩(wěn)定,只是略有起伏:隨al含量升高,合金的屈服強度略有升高。合金經(jīng)固溶熱處理后,由于冷速比熱等靜壓處理時的冷速大,合金的拉伸強度提高,塑性降低。實施例17#實施例17#的成分列于表12中。鑄錠的熔煉工藝為一次真空自耗熔煉,一次真空凝殼熔煉,一次真空懸浮熔煉,然后澆鑄成可應(yīng)用于航空器中的盤狀鑄件。鑄件首先經(jīng)熱等靜壓(hip)處理:熱等靜壓壓力130mpa,溫度為1020±20℃,時間為3小時,隨爐冷至300℃以下出爐,后切割其腹板部分(約5mm厚)進行不同固溶熱處理并進行拉伸測試。鑄件腹板部位拉伸試驗結(jié)果見表13。表12:實施例17#合金成分(質(zhì)量百分數(shù),wt.%)表13:實施例17#合金拉伸性能從表13可以看出,由本發(fā)明的新型鑄態(tài)強韌ti3al金屬間化合物的實際鑄件有良好的拉伸性能,并且通過不同熱處理可使實際鑄件得到不同力學(xué)性能匹配。其特定成分力學(xué)性能變化規(guī)律是:隨著固溶熱處理冷速的增大,合金的室溫、600℃拉伸強度增加,室溫塑性降低。實施例17鑄件室溫拉伸強度可達800mpa,斷后延伸率大于3.5%;600℃拉伸強度可達600mpa,該合金可用于制作先進航空發(fā)動機高溫部位的精密鑄件,在600~700℃范圍內(nèi)長時使用。實施例18#實施例18#的成分列于表14中。鑄錠的熔煉工藝為一次真空自耗熔煉,一次真空凝殼熔煉,一次真空懸浮熔煉,然后在鋼模中澆鑄成φ15×145mm的鑄棒。鑄棒經(jīng)熱等靜壓(hip)后進行固溶熱處理,隨后進行性能測試。采用的熱等靜壓制度為:熱等靜壓壓力130mpa,溫度為1020±20℃,時間為3小時,隨爐冷至300℃以下出爐;固溶熱處理制度為:固溶溫度1020℃,固溶時間1h,包耐火棉緩冷(sc)。性能測試結(jié)果見表15~20。表14:實施例18#合金成分(質(zhì)量百分數(shù),wt.%)表15:18#合金不同測試溫度下拉伸性能表16:18#合金長時間時效后室溫拉伸性能時效熱處理制度σ0.2,mpaσb,mpaδ,%600℃/100h6367932.4600℃/300h6397783.5600℃/500h6357893.8650℃/100h6337884.1650℃/300h6197754.3650℃/500h6107574.2700℃/100h6437673.8700℃/300h6027513.7700℃/500h6077432.9表17:18#合金高周疲勞不同溫度疲勞性能注:循環(huán)周次達到10000×103的樣品未斷,停止試驗。表18:18#合金低周疲勞不同溫度疲勞性能試樣尺寸d=5mm應(yīng)力比0.1試驗頻率0.05~0.5hz測試環(huán)境空氣測試溫度20℃測試溫度650℃最大應(yīng)變εmax(%)循環(huán)周次nf最大應(yīng)變εmax(%)循環(huán)周次nf2.700621872.50033822032.50012922962.5001331.45242.4004291.45612.0001911.46692.000191114892.000246113081.999313113741.993690.829981.60014740.716661.60018770.732801.30040930.615511.30048130.653061.30022250.6173721.00053610.5614060161.00013692//1.00012023//0.80023880//0.600193183//表19:18#合金持久性能試驗數(shù)據(jù)試驗溫度應(yīng)力時間備注600℃280mpa>100h未斷650℃250mpa>100h未斷表20:18#合金抗氧化性能試驗數(shù)據(jù)從表15可以看出,本發(fā)明的新型鑄態(tài)強韌ti3al金屬間化合物從室溫直到700℃保持著較高的強度,性能波動性較小。600~700℃溫度范圍內(nèi),合金的屈服強度在470mpa~370mpa變化,合金的抗拉強度在790mpa~500mpa變化,其性能可達到先進航空發(fā)動機高溫部位的精密鑄件在600~700℃范圍內(nèi)使用要求。從表16可以看出,本發(fā)明的新型鑄態(tài)強韌ti3al金屬間化合物在600~700℃經(jīng)100~500h時效拉伸性能有較好的穩(wěn)定性。600℃長時間時效,合金拉伸強度穩(wěn)定,塑性有所提高;650℃長時間時效,合金塑性穩(wěn)定,拉伸強度略有降低;650℃長時間時效,合金塑性穩(wěn)定,拉伸強度略有降低;700℃長時間時效,拉伸強度和塑性均略有降低。表17給出了18#合金不同溫度下高周疲勞性能數(shù)據(jù),為便于分析,將結(jié)果制成圖4~7。圖4~7分別給出了20、400、600、650℃下18#合金高周疲勞性能數(shù)據(jù)及擬合出了s-n中值曲線及p-s-n中值曲線(置信度γ=95%,存活率p=99.87%)。根據(jù)擬合的p-s-n中值曲線,13#合金室溫、400、600、650℃下疲勞壽命nf>107對應(yīng)的應(yīng)力分別為362、408、216、323mpa。表18給出了18#合金不同溫度下低周疲勞性能數(shù)據(jù),室溫下最大應(yīng)變ε≤0.8時循環(huán)周次在20000次以上,600℃下最大應(yīng)變ε≤0.56時循環(huán)周次在20000次以上。從表19可以看出,18#合金600℃/100h持久強度在280mpa以上,650℃/100h持久強度在250mpa以上。從表20可以看出,本發(fā)明的新型鑄態(tài)強韌ti3al金屬間化合物在600~700℃溫度范圍內(nèi)氧化100h均屬于完全抗氧化級別,適合先進航空發(fā)動機高溫部位的精密鑄件在600~700℃范圍內(nèi)抗氧化使用要求。目前,變形ti3al合金已接近實用化程度,而鑄造ti3al合金的研究起步較晚。以ti3al基合金代替高溫合金合金采用精密鑄造的工藝路線制備復(fù)雜形狀高溫部件,可以從重量和結(jié)構(gòu)上同時減輕航空發(fā)動機重量,實現(xiàn)航空發(fā)動機驗證機高推重比的技術(shù)指標。實施例結(jié)果表明,本發(fā)明合金在600~700℃范圍內(nèi)具有高耐熱性(以拉伸強度、高軸疲勞強度和低周疲勞強度為衡量指標)、高抗氧化性,并可獲得良好的室溫塑性和可接受的熱穩(wěn)定性。從而,通過成分優(yōu)化和熱處理工藝組合,可獲得拉伸強度與塑性、疲勞強度與熱穩(wěn)定性的不同匹配,可用于制作先進航空發(fā)動機高溫部位的精密鑄件,在600~700℃范圍內(nèi)長時使用;該合金也用于制作航天飛行器耐高溫結(jié)構(gòu)件,在650℃~750℃范圍內(nèi)短時使用。當(dāng)前第1頁12