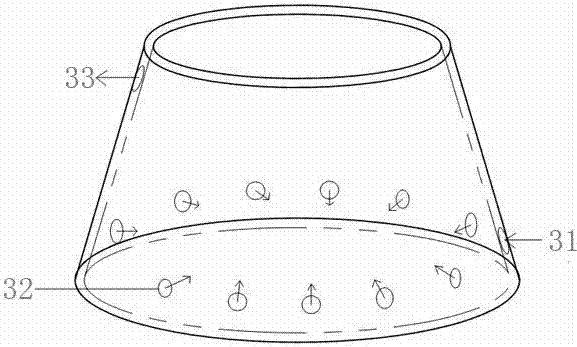
本發(fā)明涉及材料制備
技術(shù)領(lǐng)域:
,具體的說(shuō)是一種耐高溫濃硫酸用高硅不銹鋼制造方法及其設(shè)備。
背景技術(shù):
:硫酸是一種腐蝕性強(qiáng)、腐蝕過(guò)程復(fù)雜的基本化工原料,高溫濃硫酸產(chǎn)生氫去極化腐蝕和氧去極化腐蝕。在高溫濃硫酸中,高硅不銹鋼具有極其優(yōu)異的耐腐蝕性能,是硫酸工業(yè)中的首選材料。由于高硅不銹鋼的特殊應(yīng)用環(huán)境,不僅要求材料在高溫濃硫酸中具有優(yōu)良的耐點(diǎn)腐蝕縫隙腐蝕和應(yīng)力腐蝕開(kāi)裂性能,而且要求其具有優(yōu)良的塑性變形性能,可用于鍛造開(kāi)坯、熱軋、冷軋等加工變形工藝,滿足低成本生產(chǎn)和工業(yè)應(yīng)用。通過(guò)對(duì)高硅鋼相關(guān)專(zhuān)利進(jìn)行檢索,分析如下:專(zhuān)利“cn101228287a”公開(kāi)了一種高硅不銹鋼及其材料與高硅不銹鋼的制造方法,該專(zhuān)利所描述的高硅鋼的特征在于,各元素的重量百分比為:c:0.02;si:4;cr:12;ni:7;余量為fe。該專(zhuān)利的優(yōu)點(diǎn)是:通過(guò)細(xì)化晶粒的方法,使材料具有較高斷裂延伸率,以此材料可以制作長(zhǎng)壽命、高耐磨的彈簧,應(yīng)用于高荷重的負(fù)荷環(huán)境中。專(zhuān)利“cn1544680a”公開(kāi)了一種高硅鋼及其制造方法,該專(zhuān)利所描述的高硅鋼的特征在于,各元素的重量百分比為:c:0.007-1;si:5-10;cr≤0.01;ni≤0.01;mn≤0.01;p≤0.01;s≤0.01;余量為fe。該專(zhuān)利的優(yōu)點(diǎn)是:改善了硅鋼的拉伸塑性和加工性能,有利于不同厚度高硅片大規(guī)模生產(chǎn),利用熱機(jī)械處理技術(shù),控制其顯微組織、碳含量和軟磁性能。專(zhuān)利“cn101985679a”公開(kāi)了一種高硅鋼板的短流程生產(chǎn)工藝,該專(zhuān)利所描述的高硅鋼的特征在于,各元素的重量百分比為:si:3.5-7;余量為fe。該專(zhuān)利的優(yōu)點(diǎn)是:采用離心澆注方法生產(chǎn)的三層復(fù)合金屬管坯,三層金屬為硅含量不同的高硅鋼,利用熱塑性變形與冷軋相結(jié)合的方法,生產(chǎn)出厚度為0.1-1mm的鋼板。專(zhuān)利“cn102139279a”公開(kāi)了一種利用定向凝固板坯制備取向高硅鋼冷軋薄板的方法,該專(zhuān)利所描述的高硅鋼的特征在于,各元素的重量百分比為:si:4.5-1.0;b:50-2000ppm;余量為fe。該專(zhuān)利的優(yōu)點(diǎn)是:采用重熔定向凝固技術(shù)制備<110>方向生長(zhǎng)的定向板坯,然后,再進(jìn)行軋制,獲得取向高硅鋼薄板,使高硅鋼的軟磁性能進(jìn)一步提高。專(zhuān)利“cn102321785a”公開(kāi)了一種高硅低氧潔凈鋼的冶煉方法,該專(zhuān)利所描述的高硅鋼牌號(hào)為60si2mna,該專(zhuān)利的優(yōu)點(diǎn)是:采用al粒+電石渣渣面擴(kuò)散脫氧,禁止使用硅鐵粉或者碳化硅,將鋼中的氧含量控制在6-10ppm,提高爐高硅鋼的疲勞性能。專(zhuān)利“cn103266215a”公開(kāi)了一種基于合金化的高硅鋼薄帶及其制造方法,該專(zhuān)利所描述的高硅鋼的特征在于,各元素的重量百分比為:si:5.5-7.0;cu:0.05-2.5;余量為fe及不可避免的雜質(zhì)。該專(zhuān)利的優(yōu)點(diǎn)是:采用合金化的方法不僅改善爐高硅鋼薄帶的低溫延展性,還保證爐其具有較好的軟磁性能,使高硅鋼薄帶可以通過(guò)傳統(tǒng)軋制方式進(jìn)行制備。專(zhuān)利“cn104372238a”公開(kāi)了一種取向高硅鋼的制備方法,該專(zhuān)利所描述的高硅鋼的特征在于,各元素的重量百分比為:c:0.001-0.003;si:5.0-6.6;mn:0.2-0.3;al:0.05-0.12;v:0.01-0.03;nb:0.03-0.06;s:0.02-0.03;n:0.009-0.02;o:≤0.002;余量為fe及不可避免的雜質(zhì)。該專(zhuān)利的優(yōu)點(diǎn)是:設(shè)計(jì)抑制劑,通過(guò)鑄帶晶粒凝固-長(zhǎng)大行為控制盒抑制劑元素固溶析出行為設(shè)計(jì),實(shí)現(xiàn)組織-織構(gòu)-析出柔性控制,得到高磁感取向高硅鋼。專(zhuān)利“cn104630619a”公開(kāi)了一種用于薄板坯連鑄連軋生產(chǎn)的高硅鋼及制備方法,該專(zhuān)利所描述的高硅鋼的特征在于,各元素的重量百分比為:c≤0.003;si:4.5-7.0;mn:0.25-1.0;al≤0.008;s≤0.005;n≤0.003;o:≤0.002;余量為fe及不可避免的雜質(zhì)。該專(zhuān)利的優(yōu)點(diǎn)是:采用連鑄連軋短流程,獲得柱狀晶體積比例不低于90%,細(xì)纖維組織、磁性能良好的高硅鋼。這些專(zhuān)利所涉及的為合金含量低的高硅鋼,主要用來(lái)制作各種變壓器、電動(dòng)機(jī)和發(fā)電機(jī)的鐵芯,應(yīng)用于電力、電子和軍事工業(yè)的重軟磁性材料。但是,均不能應(yīng)用于高溫硫酸環(huán)境中。通過(guò)文獻(xiàn)檢索,20世紀(jì)80年代國(guó)外開(kāi)始研究應(yīng)用于高溫硫酸環(huán)境中的高硅不銹鋼,相繼開(kāi)發(fā)出多個(gè)牌號(hào)的高硅不銹鋼,但是,其生產(chǎn)制造工藝均未見(jiàn)報(bào)道公開(kāi),國(guó)內(nèi)在高硅不銹鋼的研究還處于起步階段。目前,生產(chǎn)高硅不銹鋼主要采用兩種制造工藝,第一種工藝為:電弧爐+aod(氬氧脫碳)或者vod(真空吹氧脫碳)爐外精煉工藝冶煉鋼錠,將鋼錠鍛造開(kāi)坯后進(jìn)行熱軋、冷軋。該工藝的優(yōu)點(diǎn)是:生產(chǎn)效率高,成本低。該工藝的缺點(diǎn)是:鋼錠的鍛造開(kāi)坯成材率低,最高75%,材料的純凈度低,夾雜物含量高,影響材料的耐腐蝕性能。第二種工藝為:電弧爐或者中頻感應(yīng)爐+aod(氬氧脫碳)+保護(hù)氣氛電渣爐工藝冶煉鋼錠,將鋼錠鍛造開(kāi)坯后進(jìn)行熱軋、冷軋。該工藝的優(yōu)點(diǎn)是:采用電渣重熔工藝提高鋼錠的利用率,可以將鋼錠鍛造開(kāi)坯成材率提高至95%。材料的成分均勻性、純凈度高,夾雜物含量低,材料具有更優(yōu)異的耐腐蝕性能。該工藝的缺點(diǎn)是:為了避免電渣重熔過(guò)程中si元素的燒損,采用全保護(hù)氣氛電渣重熔爐冶煉,避免大氣中的氧氣進(jìn)入鋼中燒損si元素,而全保護(hù)氣氛電渣重熔爐設(shè)備投資高,是常規(guī)電渣重熔爐的5-6倍,造成生產(chǎn)成本高,噸鋼生產(chǎn)成本是常規(guī)電渣重熔爐的2倍,難以推廣應(yīng)用。技術(shù)實(shí)現(xiàn)要素:本發(fā)明目的是為解決上述技術(shù)問(wèn)題的不足,提供一種耐高溫濃硫酸用高硅不銹鋼制造方法及其設(shè)備,該方法和設(shè)備所制備的高硅不銹鋼,在高溫環(huán)境下,耐濃硫酸腐蝕性強(qiáng)。本發(fā)明為解決上述技術(shù)問(wèn)題所采用的技術(shù)方案是:一種耐高溫濃硫酸用高硅不銹鋼制造方法,包括以下步驟:(1)通過(guò)模擬相圖,匹配各元素的含量,設(shè)計(jì)出鋼錠的化學(xué)成分組成,保證高硅不銹鋼處于穩(wěn)定的奧氏體區(qū),減少鋼錠中的δ鐵素體含量,獲得均勻的奧氏體組織;各元素組成及質(zhì)量百分比含量為:c≤0.03;si:5.2-5.8;mn≤1.0;p≤0.025;s≤0.01;cr:17.5-18.5;ni:21-22;mo:0.5-1.3;cu:2.0-2.5;al:≤0.05;ce:≤0.05;nb:0.02-0.05;o:≤0.006;n:≤0.01;其余為不可避免的雜質(zhì)和fe;(2)、通過(guò)中頻感應(yīng)爐初煉+氬氧脫碳(aod)爐精煉工藝冶煉圓形電極;所述電極的元素組成及重量百分比為:c≤0.03;si:5.8-6.0;mn≤1.0;p≤0.025;s≤0.01;cr:17.5-18.5;ni:21-22;mo:0.5-1.3;cu:2.0-2.5;al:0.04-0.06;ce≤0.05;nb:0.02-0.05;o:≤0.006;n:≤0.01;其余為不可避免的雜質(zhì)和fe;電極的直徑d與鋼錠的直徑d的比值為0.7-0.8;(3)、通過(guò)電渣重熔(esr)工藝冶煉鋼錠。所述電渣重熔(esr)工藝,包括以下步驟:(1)、將電極表面的氧化皮清理干凈,并將其焊接在假電極上,送入井式電阻加熱爐內(nèi),電極預(yù)熱至500-600℃,保溫5-6小時(shí),去除電極表面的水分;(2)、選用的渣料組元和重量百分比為:caf260%~70%,al2o315%~20%,cao10%~20%,sio22%~5%,渣料為50-200kg,渣料烘烤溫度為800℃,烘烤時(shí)間為8-10小時(shí);(3)、采用石墨電極引弧造渣,將烘烤好的渣系按照caf2、sio2、cao、al2o3的順序加入到結(jié)晶器中,將渣料熔化成液態(tài),液態(tài)渣溫度控制在1650-1700℃;(4)、將自耗電極移至液態(tài)渣池內(nèi),在大氣環(huán)境下,開(kāi)始電渣重熔,電渣錠的直徑用d表示,根據(jù)鋼錠直徑d的大小選擇相應(yīng)的電極熔化速度v,其中,v=(0.7-0.8)×d,電渣錠直徑d的單位為mm,電極熔化速度v的單位為kg/h;(5)、冶煉過(guò)程中向渣池中均勻的加入硅鈣粉進(jìn)行脫氧,硅鈣粉在渣面與大氣中的氧氣反應(yīng)生成cao和sio2,減少大氣中的氧氣進(jìn)入液態(tài)渣池中,氧化鋼液中的si元素;電極的重量表示為w,w的單位為kg,硅鈣粉的加入量表示為w1,w1的單位為g,硅鈣粉的加入量為:w1=(3-4)×w;將電渣重熔冶煉過(guò)程平均分成兩個(gè)階段,電渣重熔開(kāi)始,硅鈣粉的加入頻率表示為m1,m1的單位為g/min,硅鈣粉的加入頻率為:m1=(3-4)×v/60;當(dāng)電極重量冶煉至一半時(shí),硅鈣粉的加入頻率表示為m2,m2的單位為g/min,硅鈣粉的加入頻率為:m2=(1-3)×v/60;電渣重熔補(bǔ)縮期,硅鈣粉的加入頻率表示為m3,m3的單位為g/min,硅鈣粉的加入頻率為:m3=(0.5-2)×v/60;所述硅鈣粉si:ca=1:1;(6)、冶煉過(guò)程中,爐口放置保護(hù)罩,保護(hù)裝置內(nèi)通入氬氣,氬氣的流量控制在20-40m3/h;保護(hù)罩內(nèi)的氬氣通過(guò)其內(nèi)壁上的小孔流出,在爐口匯集形成保護(hù)層,減少了大氣中的氧氣進(jìn)入液態(tài)渣池內(nèi);(7)、電極熔化完畢后,鋼錠在結(jié)晶器內(nèi)緩慢冷卻40-90分鐘,保證液態(tài)金屬和熔渣凝固充分,鋼錠脫模后空冷至室溫。用于所述耐高溫濃硫酸用高硅不銹鋼制造方法的設(shè)備,包括電極和液態(tài)渣池;在液態(tài)渣池上方設(shè)有保護(hù)罩,所述保護(hù)罩設(shè)有內(nèi)腔,內(nèi)腔中設(shè)有電極;保護(hù)罩底部設(shè)有惰性氣體的內(nèi)壁出氣孔,側(cè)面下方設(shè)有惰性氣體的主進(jìn)氣孔,側(cè)面上方設(shè)有惰性氣體的主進(jìn)氣孔。有益效果是:(1)在大氣環(huán)境下,采用常規(guī)的電渣重熔爐冶煉鋼錠,降低了設(shè)備投資和鋼錠的制造成本,具有明顯的經(jīng)濟(jì)效益;(現(xiàn)有技術(shù):采用全密閉保護(hù)氣氛電渣重熔爐冶煉工藝。為什么不采用常規(guī)的電渣重熔爐冶煉鋼錠的原因:此材料含有大量的易氧化元素si,此工藝高溫鋼液與大氣中的氧始終接觸,容易在冶煉過(guò)程中發(fā)生氧化反應(yīng),生產(chǎn)sio2,造成材料中的si元素減少,甚至不合格,工藝穩(wěn)定性差,難以控制);(2)通過(guò)設(shè)計(jì)保護(hù)罩,冶煉過(guò)程中在電渣重熔爐口形成惰性氣體保護(hù)層,并在冶煉的不同階段,均勻的向渣中加入不同劑量的硅鈣粉脫氧劑,有效控制了硅元素的燒損,冶煉出低氮、低氧、成分均勻的高硅奧氏體不銹鋼鋼錠,通過(guò)優(yōu)于成分設(shè)計(jì),加入微量ce、nb、al等合金元素,提高了鋼的熱加工性能和耐腐蝕性能。(3)本發(fā)明制造工藝簡(jiǎn)單,生產(chǎn)成本低廉,鋼錠具有良好的成分均勻性,優(yōu)異的耐高溫硫酸腐蝕性能,能夠應(yīng)用在硫酸工業(yè)的惡略腐蝕環(huán)境中,大大延長(zhǎng)了產(chǎn)品的使用壽命,提高設(shè)備的安全性,具有良好的社會(huì)效益;耐高溫硫酸腐蝕性根據(jù)標(biāo)準(zhǔn)進(jìn)行實(shí)驗(yàn),以材料表面沒(méi)有腐蝕現(xiàn)象為標(biāo)準(zhǔn),現(xiàn)有技術(shù)的腐蝕數(shù)據(jù):在150℃的98%濃度的h2so4溶液中,平均腐蝕速率為0.09-0.125mm/年,本發(fā)明的腐蝕速率為小于0.08mm/年。附圖說(shuō)明圖1是本發(fā)明耐高溫濃硫酸用高硅不銹鋼制造方法的設(shè)備結(jié)構(gòu)示意圖;圖2是本發(fā)明耐高溫濃硫酸用高硅不銹鋼制造方法設(shè)備的保護(hù)罩結(jié)構(gòu)示意圖;圖中標(biāo)記是:1、電極升降機(jī)構(gòu),2、電極,3、保護(hù)罩,4、液態(tài)渣池,5、金屬熔池,6、結(jié)晶器,7、鋼錠,8、底水箱,9、控制系統(tǒng);31、主進(jìn)氣孔,32、內(nèi)壁出氣孔,33、主出氣孔。具體實(shí)施方式一種耐高溫濃硫酸用高硅不銹鋼制造方法,包括以下步驟:(一)通過(guò)模擬相圖,匹配各元素的含量,設(shè)計(jì)出鋼錠的化學(xué)成分組成,保證高硅不銹鋼處于穩(wěn)定的奧氏體區(qū),減少鋼錠中的δ鐵素體含量,獲得均勻的奧氏體組織;各元素組成及質(zhì)量百分比含量為:c≤0.03;si:5.2-5.8;mn≤1.0;p≤0.025;s≤0.01;cr:17.5-18.5;ni:21-22;mo:0.5-1.3;cu:2.0-2.5;al:≤0.05;ce:≤0.05;nb:0.02-0.05;o:≤0.006;n:≤0.01;其余為不可避免的雜質(zhì)和fe;(二)、通過(guò)中頻感應(yīng)爐初煉+氬氧脫碳(aod)爐精煉工藝冶煉圓形電極;所述電極的元素組成及重量百分比為:c≤0.03;si:5.8-6.0;mn≤1.0;p≤0.025;s≤0.01;cr:17.5-18.5;ni:21-22;mo:0.5-1.3;cu:2.0-2.5;al:0.04-0.06;ce≤0.05;nb:0.02-0.05;o:≤0.006;n:≤0.01;其余為不可避免的雜質(zhì)和fe;電極的直徑d與鋼錠的直徑d的比值為0.7-0.8;本發(fā)明增加了al、ce元素的含量,達(dá)到的效果:降低鋼錠中雜質(zhì)o元素的含量,提高鋼錠的熱加工性能。增加了nb元素的含量,達(dá)到的效果:提高材料的耐腐蝕性能。鋼錠化學(xué)成分設(shè)計(jì)原理如下:(1)c≤0.03%碳是強(qiáng)烈形成并穩(wěn)定奧氏體元素,并能提高材料的機(jī)械性能,但是,碳含量過(guò)高能明顯促進(jìn)碳化物cr23c6沿晶間析出,導(dǎo)致晶界貧鉻,使材料的耐晶間腐蝕性能下降。高硅不銹鋼在冶煉過(guò)程中盡量降低碳含量,但是,碳含量過(guò)低,會(huì)顯著地增加冶煉成本。因此,本發(fā)明的碳元素含量重量百分比為:c≤0.03%,碳元素含量重量百分比的優(yōu)選范圍為:c≤0.02%。(2)si:5.2-5.8si是重要的耐蝕合金元素之一,具有優(yōu)良的抗氧化性能,能夠在不銹鋼的表面生成sio2氧化膜。si≤5.2時(shí),不能與不銹鋼中的鉻、鎳元素形成一些陰極性的含硅復(fù)合化合物,促進(jìn)不銹鋼的鈍化,造成不銹鋼的耐蝕性降低。si≥5.8時(shí),過(guò)高的含硅量使鉻、鎳的鈍化作用減弱,反而減弱不銹鋼的耐蝕性。而且,過(guò)量的鐵素體形成元素硅會(huì)使鋼錠中產(chǎn)生大量的一次δ鐵素體,降低鋼錠的熱加工塑性。因此,本發(fā)明的硅元素含量重量百分比為:si:5.2-5.8,硅元素含量重量百分比的優(yōu)選范圍為:5.5-5.8。(3)mn≤1%mn對(duì)不銹鋼在濃硫酸中的耐蝕性影響不大,主要是作為脫氧劑帶入鋼中的,考慮到鋼在冶煉過(guò)程中的脫氧效果和冶煉經(jīng)濟(jì)性,本發(fā)明的mn元素含量重量百分比為:mn≤1%(4)s≤0.01%s是鋼中的雜質(zhì)元素,能夠降低材料的熱加工性能和耐腐蝕性能,因此,s在鋼中的含量越低越好,根據(jù)本發(fā)明所采取的冶煉工藝,在不增加生產(chǎn)成本的基礎(chǔ)上,s元素含量重量百分比為:s≤0.01%,s元素含量重量百分比的優(yōu)選范圍為:s≤0.006%。(5)p≤0.025%p是鋼中的雜質(zhì)元素,容易聚集在晶界惡化材料的性能,因此,p在鋼中的含量越低越好,根據(jù)本發(fā)明所采取的冶煉工藝,在不增加生產(chǎn)成本的基礎(chǔ)上,磷元素含量重量百分比為:p≤0.025%,硫元素含量重量百分比的優(yōu)選范圍為:p≤0.02%。(6)17.5%≤cr≤18.5%cr元素顯著提高材料的耐腐蝕性能,對(duì)提高不銹鋼在高溫濃硫酸中的耐腐蝕性能作用僅次于si。因此,cr元素是本發(fā)明高硅不銹鋼必不可缺的元素。當(dāng)cr≤17.5%時(shí),不能與硅、鎳元素形成足夠厚的含硅復(fù)合化合物薄膜,造成不銹鋼的耐蝕性降低。同時(shí),cr元素是強(qiáng)烈形成并穩(wěn)定鐵素體的元素,縮小單相奧氏體區(qū),隨著cr含量的增加,能夠促進(jìn)金屬間相的析出,從而降低材料的塑韌性。當(dāng)cr元素含量重量百分比大于18.5%時(shí),材料的奧氏體組織穩(wěn)定性變差,鋼中會(huì)保留一定數(shù)量的高溫鐵素體組織,降低材料的熱加工塑性。因此,本發(fā)明的cr元素含量重量百分比為:17.5%≤cr≤18.5%。(7)21%≤ni≤22%鎳對(duì)提高不銹鋼在高溫濃硫酸中的耐腐蝕性能有一定作用,但不十分明顯。在本發(fā)明中,鎳是強(qiáng)烈形成并穩(wěn)定奧氏體且擴(kuò)大單相奧氏體區(qū)的元素,其主要作用是維持鎳、鉻當(dāng)量的平衡,得到穩(wěn)定的奧氏體組織,保證變形性能。因此,本發(fā)明的ni元素含量重量百分比為:21%≤ni≤22%。(8)0.5%≤mo≤1.3%mo元素可以促進(jìn)不銹鋼鈍化。當(dāng)mo≤0.5%時(shí),通過(guò)鉻、鉬的復(fù)合作用提高不銹鋼在濃硫酸中的耐蝕性的作用不明顯;當(dāng)mo≥1.3%時(shí),鉬在氧化性介質(zhì)濃硫酸中極易產(chǎn)生過(guò)鈍化,對(duì)不銹鋼的耐蝕性不利。因此,本發(fā)明的mo元素含量重量百分比為:mo:0.5%≤mo≤1.3%,mo元素含量重量百分比的優(yōu)選范圍為:0.6%≤mo≤1.0%。(9)2.0%≤cu≤2.5%cu元素可以提高不銹鋼在濃硫酸中的耐腐蝕性。主要原因?yàn)椋恒~的電極電位比氫高,可抑制析氫腐蝕。但是,cu元素含量過(guò)高會(huì)降低鋼的熱加工塑性。因此,本發(fā)明的cu元素含量重量百分比為:mo:2%≤mo≤2.5%。(10)0.02%≤nb≤0.05%鈮是穩(wěn)定化元素,鈮與碳的結(jié)合力強(qiáng)于鉻元素,鋼中加入鈮后,優(yōu)先與碳結(jié)合形成化合物在晶內(nèi)或者晶界析出,不僅可以抑制cr23c6析出,提高材料的抗腐蝕性能,而且鈮的析出物可以提高材料的強(qiáng)度,當(dāng)鈮的添加量重量百分比超過(guò)0.05%時(shí),強(qiáng)化作用達(dá)到飽和。當(dāng)鈮的添加量重量百分比低于0.02%時(shí),不能有效抑制cr23c6析出,影響耐腐蝕性能。因此,本發(fā)明的nb元素含量重量百分比為:0.02%≤nb≤0.05%。(11)ce:≤0.05稀土ce可以改變鋼中易于形成點(diǎn)蝕的硫化物夾雜的成分和形態(tài),降低鋼中的硫含量,提高鋼的耐點(diǎn)蝕能力。另外,稀土ce可以在晶界和碳化物-基體界面上富集,提高鋼錠的熱加工性能,當(dāng)ce的添加量重量百分比超過(guò)0.05%時(shí),生產(chǎn)成本提高。因此,本發(fā)明的ce元素含量重量百分比為:ce≤0.05%。(12)al≤0.05%al元素主要是作為脫氧劑帶入鋼中的,另外,鋼中適量的鋁可以抑制電渣重熔過(guò)程中硅元素的燒損。當(dāng)al≥0.05%時(shí),會(huì)形成粗大的晶粒,使鋼錠的熱加工性能降低??紤]到鋼在冶煉過(guò)程中的脫氧效果、電渣重熔冶煉過(guò)程中硅元素的燒損規(guī)律,本發(fā)明的al元素含量重量百分比為:al≤0.05%。(13)n≤0.01%n元素是鋼中的雜質(zhì)元素,會(huì)在鋼中形成氮化物,影響鋼的耐腐蝕性能,需要進(jìn)行嚴(yán)格控制。n元素含量控制的越低,鋼的使用性能越好,但是,會(huì)大大增加冶煉工藝的難度和生產(chǎn)成本,不適合批量生產(chǎn)應(yīng)用。因此,結(jié)合制造工藝的適應(yīng)性的生產(chǎn)成本,本發(fā)明的n元素含量重量百分比為:n≤0.01%。(14)o≤0.006%氧含量過(guò)高會(huì)惡化鋼的純凈度,降低鋼錠的熱加工性能,材料的耐腐蝕性能以及韌性,氧含量過(guò)低會(huì)增加冶煉成本。因此,綜合考慮冶煉成本和材料的使用性能,本發(fā)明的o元素含量重量百分比為:o≤0.006%。(三)、通過(guò)電渣重熔(esr)工藝冶煉鋼錠。所述電渣重熔(esr)工藝,包括以下步驟:(1)、將電極表面的氧化皮清理干凈,并將其焊接在假電極上,送入井式電阻加熱爐內(nèi),電極預(yù)熱至500-600℃,保溫5-6小時(shí),去除電極表面的水分;(2)、選用的渣料組元和重量百分比為:caf260%~70%,al2o315%~20%,cao10%~20%,sio22%~5%,渣料為50-200kg,渣料烘烤溫度為800℃,烘烤時(shí)間為8-10小時(shí);(3)、采用石墨電極引弧造渣,將烘烤好的渣系按照caf2、sio2、cao、al2o3的順序加入到結(jié)晶器中,將渣料熔化成液態(tài),液態(tài)渣溫度控制在1650-1700℃;(4)、將自耗電極移至液態(tài)渣池內(nèi),在大氣環(huán)境下,開(kāi)始電渣重熔,電渣錠的直徑用d表示,根據(jù)鋼錠直徑d的大小選擇相應(yīng)的電極熔化速度v,其中,v=(0.7-0.8)×d,電渣錠直徑d的單位為mm,電極熔化速度v的單位為kg/h;(5)、冶煉過(guò)程中向渣池中均勻的加入硅鈣粉進(jìn)行脫氧,硅鈣粉在渣面與大氣中的氧氣反應(yīng)生成cao和sio2,減少大氣中的氧氣進(jìn)入液態(tài)渣池中,氧化鋼液中的si元素;電極的重量表示為w,w的單位為kg,硅鈣粉的加入量表示為w1,w1的單位為g,硅鈣粉的加入量為:w1=(3-4)×w;將電渣重熔冶煉過(guò)程平均分成兩個(gè)階段,電渣重熔開(kāi)始,硅鈣粉的加入頻率表示為m1,m1的單位為g/min,硅鈣粉的加入頻率為:m1=(3-4)×v/60;當(dāng)電極重量冶煉至一半時(shí),硅鈣粉的加入頻率表示為m2,m2的單位為g/min,硅鈣粉的加入頻率為:m2=(1-3)×v/60;電渣重熔補(bǔ)縮期,硅鈣粉的加入頻率表示為m3,m3的單位為g/min,硅鈣粉的加入頻率為:m3=(0.5-2)×v/60;所述硅鈣粉si:ca=1:1;(6)、冶煉過(guò)程中,爐口放置保護(hù)罩,保護(hù)裝置內(nèi)通入氬氣,氬氣的流量控制在20-40m3/h;保護(hù)罩內(nèi)的氬氣通過(guò)其內(nèi)壁上的小孔流出,在爐口匯集形成保護(hù)層,減少了大氣中的氧氣進(jìn)入液態(tài)渣池內(nèi);(7)、電極熔化完畢后,鋼錠7在結(jié)晶器內(nèi)緩慢冷卻40-90分鐘,保證液態(tài)金屬和熔渣凝固充分,鋼錠脫模后空冷至室溫。用于所述耐高溫濃硫酸用高硅不銹鋼制造方法的設(shè)備,設(shè)備包括電極升降機(jī)構(gòu)1、電極2、結(jié)晶器6、底水箱8、保護(hù)罩3、液態(tài)渣池4、金屬熔池5和控制系統(tǒng)9等部分,如圖1所示;所述升降機(jī)構(gòu)的作用為:將電極夾持牢固后插入結(jié)晶器中,自上至下傳動(dòng)。所述電極的作用為:電極熔化后在結(jié)晶器內(nèi)重新凝固成電渣錠。所述結(jié)晶器的作用為:電極被高溫液態(tài)渣池逐漸熔化后,金屬液滴滴到結(jié)晶器內(nèi)形成金屬熔池,金屬熔池在結(jié)晶器冷卻水的冷卻條件下,凝固成電渣錠。所述保護(hù)罩設(shè)在液態(tài)渣池上方,所述保護(hù)罩3設(shè)有內(nèi)腔,內(nèi)腔中設(shè)有電極2;保護(hù)罩3底部設(shè)有惰性氣體的內(nèi)壁出氣孔32,側(cè)面下方設(shè)有惰性氣體的主進(jìn)氣孔31,側(cè)面上方設(shè)有惰性氣體的主進(jìn)氣孔33。一定壓力的惰性氣體從31孔進(jìn)去,從32、33孔出去,其中從32出去的氣體在設(shè)備爐口形成一層惰性氣體,起與大氣中的氧隔離作用)所述保護(hù)罩3的作用為:在電渣重熔過(guò)程中,通入保護(hù)罩內(nèi)的氬氣從其內(nèi)壁四周的小孔內(nèi)流出,在結(jié)晶器上口形成氬氣保護(hù)層,阻止大氣中的氧進(jìn)入液態(tài)渣池中,氧化金屬液滴中的硅元素,如圖2所示。所述底水箱的作用為:在電渣重熔剛開(kāi)始階段,與結(jié)晶器形成封閉的空間,金屬熔滴滴落在該空間內(nèi)形成金屬熔池。所述控制系統(tǒng)的作用為:控制升降機(jī)構(gòu)下降速度。以下結(jié)合實(shí)施例對(duì)本發(fā)明加以詳細(xì)說(shuō)明:實(shí)施例1:φ360mm的高硅不銹鋼電渣重熔錠。第一步、采用“中頻感應(yīng)+aod精煉”工藝冶煉自耗電極,電極規(guī)格為φ260mm×2500mm,電極的化學(xué)成分如表1所示。表1電極化學(xué)成分(重量%)第二步、將自耗電極表面打磨干凈。第三步,根據(jù)熱力學(xué)原理,計(jì)算si燒損反應(yīng)達(dá)到平衡時(shí)出渣系中所需的sio2理論含量,然后由sio2理論含量選擇匹配的渣系,具體方法為:(1)電渣重熔階段,電極插入液態(tài)熔渣中逐漸熔化,金屬液滴穿過(guò)渣池的過(guò)程中,發(fā)生反應(yīng):[si]+2[o]=sio2公式1根據(jù)熱力學(xué)原理,當(dāng)反應(yīng)達(dá)到化學(xué)平衡時(shí):公式2-480626+213.389t公式3=公式4=公式5lg=公式6lg=公式7為1873k時(shí),鋼液中各個(gè)元素與si的相互作用系數(shù),為1873k時(shí),鋼液中各個(gè)元素與o的相互作用系數(shù)。t為化學(xué)反應(yīng)式的平衡溫度,1873k;r為氣體常數(shù),8.314。利用公式1~公式7,計(jì)算出的活度值為:=0.031,則設(shè)計(jì)渣系中的sio2的理論摩爾濃度為0.031,質(zhì)量百分比為2%。第三步、制備渣料。渣系采用caf2、al2o3、cao、sio2四元渣系,各組元的重量百分比分別為70%、15%、13%、2%,渣量50kg。將渣料分開(kāi)置入電爐內(nèi),溫度控制在850℃,烘烤8小時(shí)。第四步,將保護(hù)罩放置在結(jié)晶器上,接好氬氣的進(jìn)口和出口;第五步,將烘烤好的渣系按照caf2、sio2、cao、al2o3的順序加入結(jié)晶器內(nèi),采用石墨電極將渣料熔化成液態(tài),液態(tài)渣溫控制在1650-1700℃,保證渣系化開(kāi)、化清;第六步,將預(yù)熱好的自耗電極移至液態(tài)渣池內(nèi),開(kāi)始電渣重熔,電壓為38-52v,電流為0.4-0.8ka,電極熔化速度為290kg/h,氬氣的流量為20m3/h,保護(hù)罩內(nèi)的氬氣通過(guò)其內(nèi)壁上的小孔流出,在爐口匯集形成保護(hù)層,減少了大氣中的氧氣進(jìn)入液態(tài)渣池內(nèi)。電渣重熔開(kāi)始,硅鈣粉的加入頻率為m1=15g/min。當(dāng)電極重量冶煉至一半時(shí),硅鈣粉的加入頻率表為m2=10g/min。電渣重熔補(bǔ)縮期,硅鈣粉的加入頻率m3=5g/min;第七步,電極熔化完畢后,鋼錠在結(jié)晶器內(nèi)緩慢冷卻40分鐘,保證液態(tài)金屬和熔渣凝固充分,鋼錠脫模后空冷至室溫。直徑為φ360mm的高硅不銹鋼鋼錠表面質(zhì)量良好,沒(méi)有重皮、夾渣、波紋等缺陷。根據(jù)gb/t1979-2001《結(jié)構(gòu)鋼低倍組織缺陷評(píng)級(jí)圖》標(biāo)準(zhǔn),對(duì)實(shí)施例鋼錠內(nèi)部質(zhì)量進(jìn)行檢測(cè),未發(fā)現(xiàn)疏松、偏析、白亮帶、皮下氣泡、殘余縮孔、翻皮、白點(diǎn)、軸心晶間裂紋、內(nèi)部氣泡、非金屬夾雜物及夾渣、異金屬夾雜物等缺陷,鋼錠內(nèi)部質(zhì)量良好。鋼錠經(jīng)鍛造后,具有良好的熱加工性能。根據(jù)gb/t4334.6-2015《不銹鋼5%硫酸腐蝕試驗(yàn)方法》、jb/t7901-1999《金屬材料實(shí)驗(yàn)室均勻腐蝕全浸試驗(yàn)方法》要求,將試樣放置在150℃的98%濃度的h2so4溶液中浸泡7天,試樣表面沒(méi)有明顯變化,沒(méi)有發(fā)生局部腐蝕現(xiàn)象,平均腐蝕速率為0.075mm/年,可見(jiàn),本發(fā)明高硅不銹鋼具有良好的耐腐蝕性能。實(shí)施例2:φ440mm的高硅不銹鋼電渣重熔錠。第一步、采用“中頻感應(yīng)+aod精煉”工藝冶煉自耗電極,電極規(guī)格為φ310mm×3500mm,電極的化學(xué)成分如表1所示。表2電極化學(xué)成分(重量%)第二步、將自耗電極表面打磨干凈。第三步,按照實(shí)施1的方法計(jì)算出的活度值為:=0.04,則設(shè)計(jì)渣系中的sio2的理論摩爾濃度為0.04,質(zhì)量百分比為3%。第三步、制備渣料。渣系采用caf2、al2o3、cao、sio2四元渣系,各組元的重量百分比分別為69%、15%、13%、3%,渣量80kg。將渣料分開(kāi)置入電爐內(nèi),溫度控制在850℃,烘烤8小時(shí)。第四步,將保護(hù)罩放置在結(jié)晶器上,接好氬氣的進(jìn)口和出口;第五步,將烘烤好的渣系按照caf2、sio2、cao、al2o3的順序加入結(jié)晶器內(nèi),采用石墨電極將渣料熔化成液態(tài),液態(tài)渣溫控制在1650-1700℃,保證渣系化開(kāi)、化清;第六步,將預(yù)熱好的自耗電極移至液態(tài)渣池內(nèi),開(kāi)始電渣重熔,電壓為60-40v,電流為0.5-11.5ka,電極熔化速度為360kg/h,氬氣的流量為25m3/h,保護(hù)罩內(nèi)的氬氣通過(guò)其內(nèi)壁上的小孔流出,在爐口匯集形成保護(hù)層,減少了大氣中的氧氣進(jìn)入液態(tài)渣池內(nèi)。電渣重熔開(kāi)始,硅鈣粉的加入頻率為m1=20g/min。當(dāng)電極重量冶煉至一半時(shí),硅鈣粉的加入頻率表為m2=12g/min。電渣重熔補(bǔ)縮期,硅鈣粉的加入頻率m3=6g/min;第七步,電極熔化完畢后,鋼錠在結(jié)晶器內(nèi)緩慢冷卻50分鐘,保證液態(tài)金屬和熔渣凝固充分,鋼錠脫模后空冷至室溫。直徑為φ440mm的高硅不銹鋼鋼錠表面質(zhì)量良好,沒(méi)有重皮、夾渣、波紋等缺陷。根據(jù)gb/t1979-2001《結(jié)構(gòu)鋼低倍組織缺陷評(píng)級(jí)圖》標(biāo)準(zhǔn),對(duì)實(shí)施例鋼錠內(nèi)部質(zhì)量進(jìn)行檢測(cè),未發(fā)現(xiàn)疏松、偏析、白亮帶、皮下氣泡、殘余縮孔、翻皮、白點(diǎn)、軸心晶間裂紋、內(nèi)部氣泡、非金屬夾雜物及夾渣、異金屬夾雜物等缺陷,鋼錠內(nèi)部質(zhì)量良好。鋼錠經(jīng)鍛造后,具有良好的熱加工性能。根據(jù)gb/t4334.6-2015《不銹鋼5%硫酸腐蝕試驗(yàn)方法》、jb/t7901-1999《金屬材料實(shí)驗(yàn)室均勻腐蝕全浸試驗(yàn)方法》要求,將試樣放置在150℃的98%濃度的h2so4溶液中浸泡7天,試樣表面沒(méi)有明顯變化,沒(méi)有發(fā)生局部腐蝕現(xiàn)象,平均腐蝕速率為0.064mm/年,可見(jiàn),本發(fā)明高硅不銹鋼具有良好的耐腐蝕性能。實(shí)施例3:φ560mm的高硅不銹鋼電渣重熔錠。第一步、采用“中頻感應(yīng)+aod精煉”工藝冶煉自耗電極,電極規(guī)格為φ420mm×3000mm,電極的化學(xué)成分如表3所示。表3電極化學(xué)成分(重量%)合金csimnspcrnimocualcenbon電極0.0155.50.60.010.01718.0521.50.662.20.040.040.040.0060.007第二步、將自耗電極表面打磨干凈。第三步,按照實(shí)施1的方法計(jì)算出的活度值為:=0.05,則設(shè)計(jì)渣系中的sio2的理論摩爾濃度為0.05,質(zhì)量百分比為4%。第三步、制備渣料。渣系采用caf2、al2o3、cao、sio2四元渣系,各組元的重量百分比分別為61%、20%、15%、4%,渣量120kg。將渣料分開(kāi)置入電爐內(nèi),溫度控制在850℃,烘烤8小時(shí)。第四步,將保護(hù)罩放置在結(jié)晶器上,接好氬氣的進(jìn)口和出口;第五步,將烘烤好的渣系按照caf2、sio2、cao、al2o3的順序加入結(jié)晶器內(nèi),采用石墨電極將渣料熔化成液態(tài),液態(tài)渣溫控制在1650-1700℃,保證渣系化開(kāi)、化清;第六步,將預(yù)熱好的自耗電極移至液態(tài)渣池內(nèi),開(kāi)始電渣重熔,電壓為54-62v,電流為7-16ka,電極熔化速度為450kg/h,氬氣的流量為35m3/h,保護(hù)罩內(nèi)的氬氣通過(guò)其內(nèi)壁上的小孔流出,在爐口匯集形成保護(hù)層,減少了大氣中的氧氣進(jìn)入液態(tài)渣池內(nèi)。電渣重熔開(kāi)始,硅鈣粉的加入頻率為m1=30g/min。當(dāng)電極重量冶煉至一半時(shí),硅鈣粉的加入頻率表為m2=15g/min。電渣重熔補(bǔ)縮期,硅鈣粉的加入頻率m3=10g/min;第七步,電極熔化完畢后,鋼錠在結(jié)晶器內(nèi)緩慢冷卻70分鐘,保證液態(tài)金屬和熔渣凝固充分,鋼錠脫模后空冷至室溫。直徑為φ560mm的高硅不銹鋼鋼錠表面質(zhì)量良好,沒(méi)有重皮、夾渣、波紋等缺陷。根據(jù)gb/t1979-2001《結(jié)構(gòu)鋼低倍組織缺陷評(píng)級(jí)圖》標(biāo)準(zhǔn),對(duì)實(shí)施例鋼錠內(nèi)部質(zhì)量進(jìn)行檢測(cè),未發(fā)現(xiàn)疏松、偏析、白亮帶、皮下氣泡、殘余縮孔、翻皮、白點(diǎn)、軸心晶間裂紋、內(nèi)部氣泡、非金屬夾雜物及夾渣、異金屬夾雜物等缺陷,鋼錠內(nèi)部質(zhì)量良好。鋼錠經(jīng)鍛造后,具有良好的熱加工性能。根據(jù)gb/t4334.6-2015《不銹鋼5%硫酸腐蝕試驗(yàn)方法》、jb/t7901-1999《金屬材料實(shí)驗(yàn)室均勻腐蝕全浸試驗(yàn)方法》要求,將試樣放置在150℃的98%濃度的h2so4溶液中浸泡7天,試樣表面沒(méi)有明顯變化,沒(méi)有發(fā)生局部腐蝕現(xiàn)象,平均腐蝕速率為0.06mm/年,可見(jiàn),本發(fā)明高硅不銹鋼具有良好的耐腐蝕性能。實(shí)施例4:φ700mm的高硅不銹鋼電渣重熔錠。第一步、采用“中頻感應(yīng)+aod精煉”工藝冶煉自耗電極,電極規(guī)格為φ500mm×3200mm,電極的化學(xué)成分如表3所示。表3電極化學(xué)成分(重量%)合金csimnspcrnimocualcenbon電極0.0255.40.30.010.0217.821.60.92.30.050.030.030.0060.007第二步、將自耗電極表面打磨干凈。第三步,按照實(shí)施1的方法計(jì)算出的活度值為:=0.06,則設(shè)計(jì)渣系中的sio2的理論摩爾濃度為0.06,質(zhì)量百分比為5%。第三步、制備渣料。渣系采用caf2、al2o3、cao、sio2四元渣系,各組元的重量百分比分別為60%、20%、15%、5%,渣量200kg。將渣料分開(kāi)置入電爐內(nèi),溫度控制在850℃,烘烤8小時(shí)。第四步,將保護(hù)罩放置在結(jié)晶器上,接好氬氣的進(jìn)口和出口;第五步,將烘烤好的渣系按照caf2、sio2、cao、al2o3的順序加入結(jié)晶器內(nèi),采用石墨電極將渣料熔化成液態(tài),液態(tài)渣溫控制在1650-1700℃,保證渣系化開(kāi)、化清;第六步,將預(yù)熱好的自耗電極移至液態(tài)渣池內(nèi),開(kāi)始電渣重熔,電壓為33-78v,電流為8-17ka,電極熔化速度為560kg/h,氬氣的流量為38m3/h,保護(hù)罩內(nèi)的氬氣通過(guò)其內(nèi)壁上的小孔流出,在爐口匯集形成保護(hù)層,減少了大氣中的氧氣進(jìn)入液態(tài)渣池內(nèi)。電渣重熔開(kāi)始,硅鈣粉的加入頻率為m1=35g/min。當(dāng)電極重量冶煉至一半時(shí),硅鈣粉的加入頻率表為m2=20g/min。電渣重熔補(bǔ)縮期,硅鈣粉的加入頻率m3=10g/min;第七步,電極熔化完畢后,鋼錠在結(jié)晶器內(nèi)緩慢冷卻70分鐘,保證液態(tài)金屬和熔渣凝固充分,鋼錠脫模后空冷至室溫。直徑為φ700mm的高硅不銹鋼鋼錠表面質(zhì)量良好,沒(méi)有重皮、夾渣、波紋等缺陷。根據(jù)gb/t1979-2001《結(jié)構(gòu)鋼低倍組織缺陷評(píng)級(jí)圖》標(biāo)準(zhǔn),對(duì)實(shí)施例鋼錠內(nèi)部質(zhì)量進(jìn)行檢測(cè),未發(fā)現(xiàn)疏松、偏析、白亮帶、皮下氣泡、殘余縮孔、翻皮、白點(diǎn)、軸心晶間裂紋、內(nèi)部氣泡、非金屬夾雜物及夾渣、異金屬夾雜物等缺陷,鋼錠內(nèi)部質(zhì)量良好。鋼錠經(jīng)鍛造后,具有良好的熱加工性能。根據(jù)gb/t4334.6-2015《不銹鋼5%硫酸腐蝕試驗(yàn)方法》、jb/t7901-1999《金屬材料實(shí)驗(yàn)室均勻腐蝕全浸試驗(yàn)方法》要求,將試樣放置在150℃的98%濃度的h2so4溶液中浸泡7天,試樣表面沒(méi)有明顯變化,沒(méi)有發(fā)生局部腐蝕現(xiàn)象,平均腐蝕速率為0.068mm/年,可見(jiàn),本發(fā)明高硅不銹鋼具有良好的耐腐蝕性能。當(dāng)前第1頁(yè)12