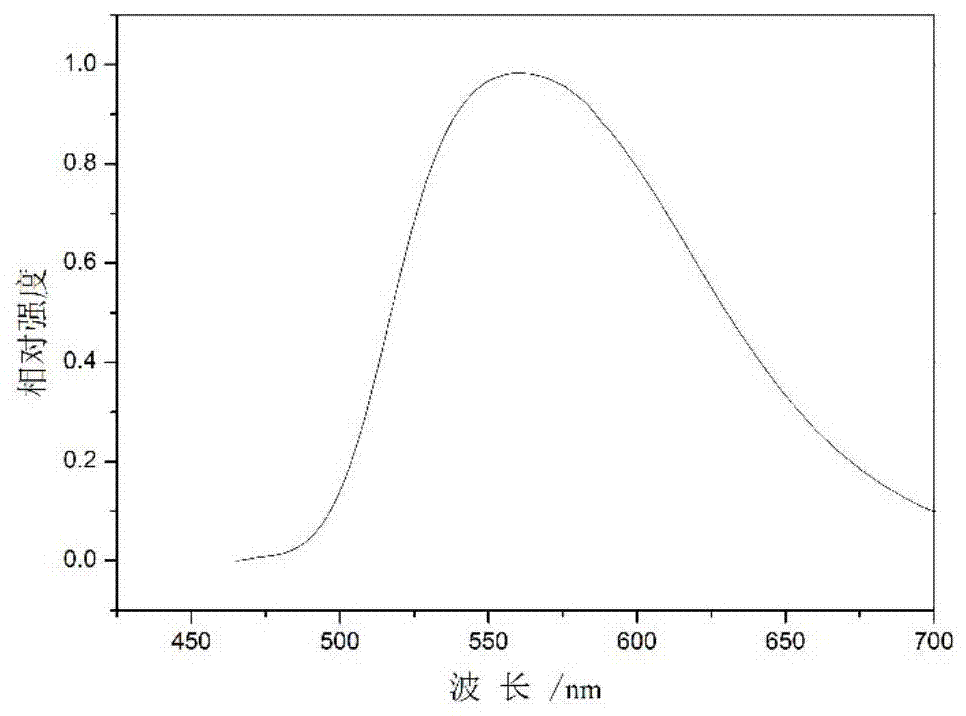
本發(fā)明屬于陶瓷制成工藝,涉及一種采用“造粒—模壓成型—燒結(jié)法”制作的熒光粉/玻璃復(fù)合發(fā)光陶瓷片。
背景技術(shù):當(dāng)前,各種類型的熒光粉廣泛的應(yīng)用在國民經(jīng)濟(jì)的各個領(lǐng)域,如在室內(nèi)LED照明領(lǐng)域的鈰釔鋁石榴石結(jié)構(gòu)的熒光粉(YAG:Ce熒光粉,化學(xué)式Y(jié)3Al5O12:Ce)和氮化物紅色熒光粉等,用于背光源的綠色硅酸鹽熒光粉等。熒光粉多為無機(jī)非金屬材料,且多制成具有一定粒度分布的粉體顆粒,本身不具有粘性,若需制作成特定形狀或與粘附于其他材料(基材)之上,則需其他材料配合。例如,廣泛的應(yīng)用于白光LED照明解決方案:YAG:Ce熒光粉分散于環(huán)氧樹脂(一類高分子材料)中,而后涂敷于藍(lán)光芯片之上的組合;以此為基礎(chǔ),商品化的遠(yuǎn)程激發(fā)熒光粉,其組成是熒光粉與環(huán)氧樹脂混合,通過注塑或其他方法制成需要的形狀從而得到發(fā)光樹脂片(“熒光粉+樹脂”)。在LED照明領(lǐng)域,將熒光粉與高分子材料混合制成塊體,將極大的簡化傳統(tǒng)封裝過程,且有利于實(shí)現(xiàn)了廣角發(fā)光。但是,發(fā)光樹脂片在復(fù)雜的戶外(長期陽光暴曬、紫外線、酸性雨水、冰雹、鳥類糞便酸堿腐蝕)或長期較高的溫度等條件下,存在容易老化等問題,這將嚴(yán)重的影響到采用此方案的器件使用壽命。采用無機(jī)非金屬材料替代高分子材料制作發(fā)光陶瓷片,可有效的解決容易老化的缺陷。目前,采用發(fā)光陶瓷片主要集中在以下幾種方式:(1)以釉料(漿料)方式涂敷于陶瓷基材表面,再經(jīng)過處理得到的表面發(fā)光的發(fā)光陶瓷片ZL98110318.9,該發(fā)明為一種發(fā)光陶瓷釉料,成分上除了含有熒光粉外,同時(shí)輔以粘土和/或長石、石英、氧化鋁之一或其混和物,屬于傳統(tǒng)陶瓷釉料(膏狀)。ZL99103523.2將熒光粉、陶瓷釉料(其組成SiO225-60%、B2O35-45%、K2O0-10%、Na2O0-15%、Li2O0-5%ZrO20-9%Al2O31-20%PbO1-50%CaO0-15%MgO0-5%ZnO0-9%BaO0-5%)混合均勻后制成發(fā)光陶瓷釉料,涂敷于陶瓷坯體表面,形成發(fā)光陶瓷的制品及其制作方法。類似的采用該種方法的還有ZL02257588.X、ZL200620063976.4、ZL200920129837.0、CN200610034866.X(公開號CN1837153)、CN200610155625.0(公開號CN101209930)、CN200910111267.7(公開號CN101503309A)、CN2009186068(公開號CN101570444)及CN200910213713.5(公開號CN102093088)等。陶瓷釉,普遍的認(rèn)為是以石英、長石、粘土等礦物為原料(或上述礦物所體現(xiàn)的氧化物)為主要成分,經(jīng)研磨、加水調(diào)制后形成的,工藝操作中,將釉涂敷于坯體表面,經(jīng)一定溫度的焙燒而熔融從而粘附于陶瓷表面。上述發(fā)光陶瓷釉及其制品無論所用輔助原料的種類、發(fā)光部位和結(jié)構(gòu)還是具體成型工藝上,都將與本發(fā)明所述的內(nèi)容存在明顯的區(qū)別。同樣的,采用發(fā)光漿料涂敷與陶瓷或玻璃表面制作發(fā)光陶瓷片的方法,也與本發(fā)明方案存在不同。(2)采用流延法或類似于流延法的方法制作(多層)發(fā)光陶瓷片CN201180045076.0(公開號CN103228762A)提供了一種多層低共燒發(fā)光陶瓷的方案(YAG/Al2O3/YAG),大概方法為:將YAG或Al2O3粉體制成漿料,采用類似于流延法的方法(原文稱“澆注法”)形成“帶”干燥后再將所需要的層通過壓力結(jié)合在一起,最后通過燒結(jié)處理得到成品。上述方法,在成分、結(jié)構(gòu)與具體成型工藝上,都將與本
技術(shù)實(shí)現(xiàn)要素:存在本質(zhì)上的區(qū)別。CN201180054192.9(公開號CN103249803A)的采用“流延法”制備YAG:Ce陶瓷片,溫度制度為400-1150℃/4h、1150℃/2h、1745℃/1h(8%H2-N2保護(hù))。其從成分的相來說是十分單一的YAG:Ce晶相;從工藝上而言,本質(zhì)上是制作YAG:Ce熒光片,將與本發(fā)明內(nèi)容存在明顯的不同。(3)以氧化物為原料,在熱處理中發(fā)生燒結(jié)現(xiàn)象形成塊狀材料,并在還原氣氛中發(fā)生固相反應(yīng),從而制得發(fā)光陶瓷片US7902564所公布的一種發(fā)光陶瓷器件,在原料上,采用Y2O3、Al2O3與CeO2氧化物,及聚乙烯醇羧丁醛等試劑為原料;在工藝上,采用先制備YAG前驅(qū)體與YAG:Ce前驅(qū)體,而后通過混合方式制成混合物,再進(jìn)行造粒與壓制成型,經(jīng)過燒盡粘合劑(1000℃)、還原氣氛中燒結(jié)(CO,1675℃,2h)等步驟制備多晶發(fā)光陶瓷。此種方案中,在原料上,YAG:Ce前驅(qū)體并非能夠?qū)崿F(xiàn)光致發(fā)光的熒光粉,而是Y2O3、Al2O3與CeO2的按YAG:Ce的化學(xué)計(jì)量比組成的氧化物混合,該前驅(qū)體需要經(jīng)過還原氣氛燒結(jié)才能具備光致發(fā)光的條件;在工藝上,采取的燒結(jié)制度(1000℃燒盡粘結(jié)劑、1675℃還原氣氛燒結(jié))也將與本發(fā)明的方案存在明顯的不同。類似此方法的還有200680044724.X(公開號CN101366126A)、200780043097.2(公開號CN101657910A)和200880100852.0(公開號CN101821862A)、200780047857.7(CN101569021A)。而CN201110430934.5(公開號CN102515751A)中選擇把HfO2、Y2O3、La2O3、Yb2O3和A2O3(Er2O3或Tm2O3)加無水乙醇混合后球磨,再干燥,過200目篩,得到陶瓷粉體,用模壓結(jié)合冷等靜壓成型工藝制備一定形狀的陶瓷坯體,陶瓷坯體經(jīng)過預(yù)燒(800~1100℃,2-4h),真空或氫氣氣氛下燒結(jié)(1800~2000℃,4-10h),空氣氣氛下退火處理(1400~1600℃,2-10h),得到透明的發(fā)光陶瓷材料。此方法也與本發(fā)明的方法也明顯不同。(4)采用熱處理使玻璃析出含有激活離子的微小晶體制備發(fā)光陶瓷的方法(微晶玻璃)CN200810120788.4(公開號CN101353229A)公布了一種制作發(fā)光微晶玻璃的方法,在原料上,將作為微晶玻璃組成成分的氟氧化物與作為摻雜離子混合均勻后,共同熔制而后迅速冷卻成型,再經(jīng)過析晶處理得到發(fā)光微晶玻璃。該種方法在原料與工藝上均與本發(fā)明的方法存在明顯不同。(5)采用絲網(wǎng)印刷的方法將發(fā)光粉制成花紙貼在陶瓷表面,施釉后燒結(jié)得到發(fā)光陶瓷CN200910086068.5(公開號CN101570444A)中將一定粒徑的長余輝熒光粉與陶瓷烤花專用顏料調(diào)配成絲網(wǎng)印刷油墨,通過絲網(wǎng)印刷制成花紙,將花紙貼于白坯陶瓷表面自然干燥24h,再在一定溫度的烤窯內(nèi)烘烤,出窯后在表面噴涂低溫透明釉,干燥2h后再入窯燒烤,最終得到發(fā)光陶瓷。此發(fā)明所用方法明顯區(qū)別于本發(fā)明的方法。(6)采用“熱等靜壓—燒結(jié)法”制備透明陶瓷ZL200910154360.6公布了一種“熒光粉/玻璃復(fù)合體”的制備方法,其采用鋁酸鹽熒光粉與玻璃粉在保護(hù)氣氛(氮?dú)饣驓鍤?或空氣氣氛中進(jìn)行熱等靜壓燒結(jié),而后通過磨削、拋光,制成半透明熒光粉/玻璃復(fù)合體。該發(fā)明所公布的玻璃粉為含有堿金屬的硼鋁酸鹽玻璃,根據(jù)該發(fā)明公布的玻璃配方,堿金屬氧化物(含量>25mol.%)作為網(wǎng)絡(luò)外體氧化物在玻璃中起到降低轉(zhuǎn)變溫度和軟化溫度的作用,將是其實(shí)現(xiàn)低轉(zhuǎn)變溫度的關(guān)鍵成分,為必不可少的成分,以此種方式實(shí)現(xiàn)低轉(zhuǎn)變溫度將與本發(fā)明公布的玻璃體系及成分上存在明顯不同;制成工藝上,該發(fā)明采用的方法為“熱等靜壓—燒結(jié)法”,與本發(fā)明更為簡單的“造?!撼尚汀獰Y(jié)法”存在本質(zhì)上的不同;值得注意的是,該發(fā)明雖然提出能夠在空氣氣氛中進(jìn)行燒結(jié),但并未在其實(shí)施例中進(jìn)行體現(xiàn);另外燒結(jié)完成后,根據(jù)本發(fā)明的方法無需進(jìn)行二次加工。(7)其他不透明的發(fā)光陶瓷CN201410058586.7(公開號CN103819091A)公布了一種用于激光激發(fā)LPD(LaserPhosphorDisplay)的“熒光粉/玻璃復(fù)合發(fā)光片層”的制備方法。成分中玻璃粉配比為(wt.%)Bi2O360-70%,B2O320-30%,ZnO6-8%,Al2O32-4%;熒光粉為CaAlSiN3:Eu氮化物熒光粉(1113結(jié)構(gòu))含量20-80wt.%。將熒光粉與玻璃粉混合均勻,得到混合粉,然后在模具上鋪平,壓片,在500-600℃條件下熱處理0.5-1.5h,冷卻即得。該發(fā)明的特點(diǎn)在于:1)采用激光激發(fā),,故不需要“發(fā)光片層”本身具有對光的透過性,而是要求“發(fā)光片層”對激光完全的阻擋;2)玻璃粉的配比不同,其大量采用重金屬成分Bi2O3,這將與本發(fā)明即將公布的配方存在不同;3)采用的是氮化物熒光粉;(4)僅對混合粉體用壓機(jī)在30MPa條件下進(jìn)行壓實(shí)。該發(fā)明上述四項(xiàng),將與本發(fā)明的方法存在不同。發(fā)明內(nèi)容本發(fā)明的目的在于克服背景技術(shù)的以上問題,提供一種制備方法簡單的發(fā)光陶瓷片。本發(fā)明的技術(shù)方案如下一種發(fā)光陶瓷片,透過率≥20%,主要由熒光粉和玻璃粉制成,其中,所述熒光粉含量為30-85wt.%,玻璃粉15-70wt.%;所述熒光粉特點(diǎn)包括:1)光致發(fā)光;2)在<410℃,不發(fā)生分解或成分變化;3)成分含有氧;所述玻璃粉為低熔點(diǎn)玻璃,燒結(jié)前為單一的非晶態(tài)物質(zhì),其特點(diǎn)包括:1)軟化溫度在395-425℃;2)Pb和Cr含量為0wt.%;3)Na2O+K2O總含量<0.1wt.%。其中,玻璃粉優(yōu)選包括如下組分:其中,玻璃粉更優(yōu)選為包括如下組分:以上成分的重量比都是相對于玻璃粉總量計(jì)。其中(SiO2+B2O3+P2O5)<50wt.%、(Bi2O3+SnO)>30wt.%、(Bi2O3+ZnO)>30wt.%。熒光粉,其本質(zhì)為無機(jī)非金屬材料;本發(fā)明的熒光粉其特點(diǎn)包括:1)光致發(fā)光;2)溫度<410℃不發(fā)生分解或成分變化;3)成分中含有O。符合以上要求的熒光粉如,YAG:Ce、LuAG:Ce及蓄光型熒光粉(如長余輝熒光粉)等。本發(fā)明熒光粉需具有上述特點(diǎn)的原因是:1)由于是用在典型的“藍(lán)光激發(fā)”LED的基礎(chǔ)上,故熒光粉應(yīng)當(dāng)是光致發(fā)光;2)熒光粉與玻璃成型后需經(jīng)過最高410℃熱處理,故熒光粉在<410℃時(shí)應(yīng)不發(fā)生分解或成分變化;3)采用的是熒光粉與氧化物玻璃混合進(jìn)行熱處理,在處理溫度下,粉體表面間可能發(fā)生相互影響,主要是玻璃的成分對于熒光粉性能的影響,本發(fā)明實(shí)踐表明,氧化物玻璃與非氧化物體系熒光粉在共燒結(jié)過程中,容易出現(xiàn)非氧化物熒光粉基質(zhì)的氧化現(xiàn)象。低熔點(diǎn)玻璃粉,其本質(zhì)為無機(jī)非金屬材料,且燒結(jié)前為單一的非晶態(tài)物質(zhì);其特點(diǎn)包括:1)軟化溫度在395-425℃;2)Pb和Cr含量為0wt.%;3)Na2O+K2O總含量<0.1wt.%。采用具有上述特征的低熔點(diǎn)玻璃的原因在于:1)控制軟化溫度上限(<425℃)能夠?qū)崿F(xiàn)低溫?zé)Y(jié),從而避免在高溫條件下熒光粉激活中心離子發(fā)生氧化,并且實(shí)現(xiàn)了不需要在保護(hù)氣氛(氮?dú)?、氬氣或氫?條件下燒結(jié)的目的,控制軟化溫度的下限(>395℃)又能充分的保證玻璃的熱穩(wěn)定性,以保證其能夠穩(wěn)定的長時(shí)間使用;2)符合歐盟RoHS要求;3)堿金屬離子(如Na+和K+)在加熱條件下容易發(fā)生遷移,這種遷移容易發(fā)生在非晶相(玻璃)與晶相(熒光粉晶體)的表面,從而破壞熒光粉的晶體結(jié)構(gòu)的完整性,故在玻璃中應(yīng)避免添加堿金屬離子,在本發(fā)明使用的玻璃中,其含量<0.1wt.%。其中(SiO2+B2O3+P2O5)<50wt.%;(Bi2O3+SnO)>30wt.%;(Bi2O3+ZnO)>30wt.%。這樣做的原因在于,作為網(wǎng)絡(luò)生成體氧化物(SiO2+B2O3+P2O5)其含量<50wt.%可制成逆性玻璃,能夠?qū)崿F(xiàn)低軟化溫度;保證網(wǎng)絡(luò)外體氧化物具有一定的量,能夠?qū)崿F(xiàn)低軟化溫度;為了獲得較高的光折射率,需保證成分中具有提高玻璃折射率能力的成分含量(Bi2O3+ZnO)>30wt.%。Bi2O3作為重金屬在低熔點(diǎn)玻璃中是最有可能替代PbO的材料,其在玻璃中的含量可以很高,可達(dá)85wt.%,但是高含量玻璃在較高溫度下容易腐蝕其他材料,包括Al2O3、ZrO2、Pt等,如采用高Bi2O3含量的玻璃與本發(fā)明所述的熒光粉進(jìn)行高燒結(jié),容易發(fā)生腐蝕熒光粉的現(xiàn)象,故本發(fā)明控制在10-35wt.%。本發(fā)明的又一技術(shù)方案為:一種發(fā)光陶瓷片的制備方法,包括如下步驟:1)根據(jù)前述的配比配備原料,將熒光粉和玻璃粉通過混合凝聚造粒,將熒光粉、低熔點(diǎn)玻璃粉在濕法混合機(jī)內(nèi)混合均勻,并以外加法加入0.5-5wt.%造粒與脫模助劑得到60-100目的造粒粉;2)模壓成型,在安裝有多套相應(yīng)模具的回轉(zhuǎn)式成型機(jī)上倒入一定量的造粒粉,采用15-20MPa的壓力,可制成發(fā)光陶瓷片坯體;3)熱處理,所述熱處理過程包括排膠和燒結(jié)兩個步驟,所述排膠溫度為300-395℃,燒結(jié)溫度為395-410℃。其中,步驟1)使用造粒與脫模助劑,主要作用為造粒用粘結(jié)劑與脫模劑;其特點(diǎn)是:1)質(zhì)量損失95%溫度為300-400℃;2)不含有除C、H、O、P及N外的其他成分。在較佳實(shí)施例中,造粒與脫模助劑包括PVB、乙基纖維素。其中,所述熱處理過程全程在空氣氣氛中進(jìn)行。1.混合與凝聚造粒凝聚造粒通過在混合粉體中加入粘結(jié)劑,通過粘結(jié)劑的附著力能夠?qū)⒘捷^小的初始粉體團(tuán)聚成較大的顆粒;這樣做的目的是:首先,經(jīng)過凝聚造粒且干燥后的顆粒具有正態(tài)分布的特點(diǎn),在模具中能夠形成較大的堆積密度,有利于在壓制后獲得告致密度的坯體;其次,由于這種團(tuán)聚為軟團(tuán)聚,可以在壓力作用下釋放,從而能夠?qū)崿F(xiàn)顆粒間更為緊密的結(jié)合實(shí)現(xiàn)坯體的致密化;不僅如此,造粒能夠保證熒光粉與低熔點(diǎn)玻璃粉混合后成分的穩(wěn)定性,增加顆粒在模具中的流動性;而且,經(jīng)過造粒的粉末顆粒,具有流動性能夠適應(yīng)連續(xù)化的成型,提高工業(yè)生產(chǎn)的效率。2.模壓成型在工業(yè)化生產(chǎn)中,為了獲得高的生產(chǎn)效率,一般要求自動化生產(chǎn),這就要求進(jìn)行成型的粉體必須具有一定的流動性,而造粒步驟正是獲得這種流動性的關(guān)鍵。眾所周知,對于瘠性材料而言,不經(jīng)過造粒而壓制成型的坯體,由于粉體本身既不具有正態(tài)分布的特點(diǎn)而基本無流動性,材料本身也無粘性,成型后的坯體致密度小,氣孔率高,強(qiáng)度差,不易通過燒結(jié)法制得半透明的發(fā)光陶瓷片,同時(shí)也不易于進(jìn)行產(chǎn)業(yè)化生產(chǎn)。在壓制過程中初步實(shí)現(xiàn)致密化(低氣孔率)的發(fā)光陶瓷坯體,是獲得具有半透明的發(fā)光陶瓷片的基礎(chǔ)。3.熱處理包括排膠(300-395℃/2-4h)和燒結(jié)(395-410℃/1-2h);其中熱處理過程全程在空氣氣氛中進(jìn)行。燒結(jié)是一種致密化的物理過程,是實(shí)現(xiàn)陶瓷高致密和低氣孔率的過程。本發(fā)明的優(yōu)點(diǎn)如下1)解決了采用高分子材料制成的發(fā)光樹脂片(發(fā)光膠片)容易老化,在戶外復(fù)雜條件的使用壽命短等問題。2)采用陶瓷工業(yè)中簡單的模壓成型工藝,相比于“流延法”、“微晶玻璃法”及“熱等靜壓—燒結(jié)法”降低了工藝難度及減少了設(shè)備的投入。3)采用模壓法制得的發(fā)光陶瓷片,表面規(guī)則平整,不需要制成后的二次加工,如切割、打磨及拋光等。4)晶體(熒光粉晶體)含量可控,在封裝過程中,可通過不同配比的熒光粉/玻璃復(fù)合發(fā)光陶瓷片實(shí)現(xiàn)多層發(fā)光結(jié)構(gòu),實(shí)現(xiàn)高顯色、低色溫等要求。5)通過調(diào)整陶瓷坯體的厚度及成分中低熔點(diǎn)玻璃的含量,可實(shí)現(xiàn)調(diào)整該陶瓷制品的透光率,從而解決了在陶瓷基材上涂敷發(fā)光材料涂層只能實(shí)現(xiàn)表面發(fā)光的問題。6)通過本發(fā)明公布的工藝方法,制得的半透明發(fā)光陶瓷解決了不透明陶瓷不能用于LED藍(lán)光芯片發(fā)出藍(lán)光透過熒光粉層并與受藍(lán)光激發(fā)的黃色熒光粉層發(fā)出的黃色光混合形成白光;同樣的,在蓄光型熒光粉/玻璃陶瓷片中,陽光可透過白透明陶瓷,從而使更多的、在陶瓷內(nèi)部的蓄光型熒光粉接受陽光的激發(fā),從而大幅度提高蓄光型熒光粉/玻璃發(fā)光陶瓷的發(fā)光時(shí)間和亮度。7)解決了目前白光LED封裝領(lǐng)域內(nèi)熒光粉配膠過程中不一致的問題,同時(shí)為實(shí)現(xiàn)封裝的器件化和標(biāo)準(zhǔn)化提供了一條有效的途徑。附圖說明圖1為實(shí)施例一配方(1)熱膨脹系百分率與溫度圖譜;圖2為實(shí)施例二的發(fā)射光譜;圖3為實(shí)施例三的發(fā)射光譜;圖4為實(shí)施例三的衰減曲線。具體實(shí)施方式實(shí)施例一低熔點(diǎn)玻璃按下表1組成配合,混合均勻后熔制,溫度1000℃,保溫120min,熔制完成后用球磨機(jī)粉碎。按表1(1)配方制得的低熔點(diǎn)玻璃粉折射率1.8,按圖1的熱膨脹系百分率與溫度圖譜測得其軟化溫度413℃。表1低熔點(diǎn)玻璃配比(Wt.%)實(shí)施例二將85wt.%YAG:Ce熒光粉(Y3Al5O12:Ce,型號PAMYY4425,D50=20μm)與15wt.%低熔點(diǎn)玻璃粉(D50=10μm)混合均勻后加入5wt.%PVB粘結(jié)劑,制成80-60目的造粒粉,采用壓機(jī)制成具有相應(yīng)形狀的發(fā)光陶瓷片坯體。將發(fā)光陶瓷片坯體放入燒結(jié)爐中,設(shè)定排膠區(qū)(300-350℃)運(yùn)行3-4h、燒結(jié)區(qū)(400℃)運(yùn)行1.5h,制成發(fā)光陶瓷片。在365nm激發(fā)光下,其發(fā)射光譜如圖2(設(shè)定YAG熒光粉含量85wt.%與環(huán)氧樹脂制成的發(fā)光膠片強(qiáng)度為1);發(fā)光陶瓷片厚度0.6mm,透過率>20%。實(shí)施例三將50wt.%長余輝熒光粉(SrAl2O4:Eu)與50wt.%低熔點(diǎn)玻璃粉(D50=10μm))混合均勻后加入0.5wt.%PVB粘結(jié)劑,制成80-100目的造粒粉,采用壓機(jī)壓制成具有相應(yīng)形狀的發(fā)光陶瓷片坯體。將發(fā)光陶瓷片坯體放入燒結(jié)爐中,設(shè)定排膠區(qū)(350-395℃)運(yùn)行2-3h、燒結(jié)區(qū)(410℃)運(yùn)行1h,制成長余輝發(fā)光陶瓷片,在450nm激發(fā)光下,其發(fā)射光譜如圖3。將長余輝發(fā)光陶瓷片在太陽光下照射5min,測試其在30min內(nèi)的衰減,得到圖4所示曲線。實(shí)施例四將30wt.%YAG:Ce熒光粉(Y3Al5O12:Ce,型號PAMYY4425,D50=20μm)與70wt.%低熔點(diǎn)玻璃粉(D50=10μm)混合均勻后加入5wt.%PVB粘結(jié)劑,制成80-60目的造粒粉,采用壓機(jī)制成具有相應(yīng)形狀的發(fā)光陶瓷片坯體。將發(fā)光陶瓷片坯體放入燒結(jié)爐中,設(shè)定排膠區(qū)(300-350℃)運(yùn)行2-3h、燒結(jié)區(qū)(395℃)運(yùn)行2h,制成發(fā)光陶瓷片。