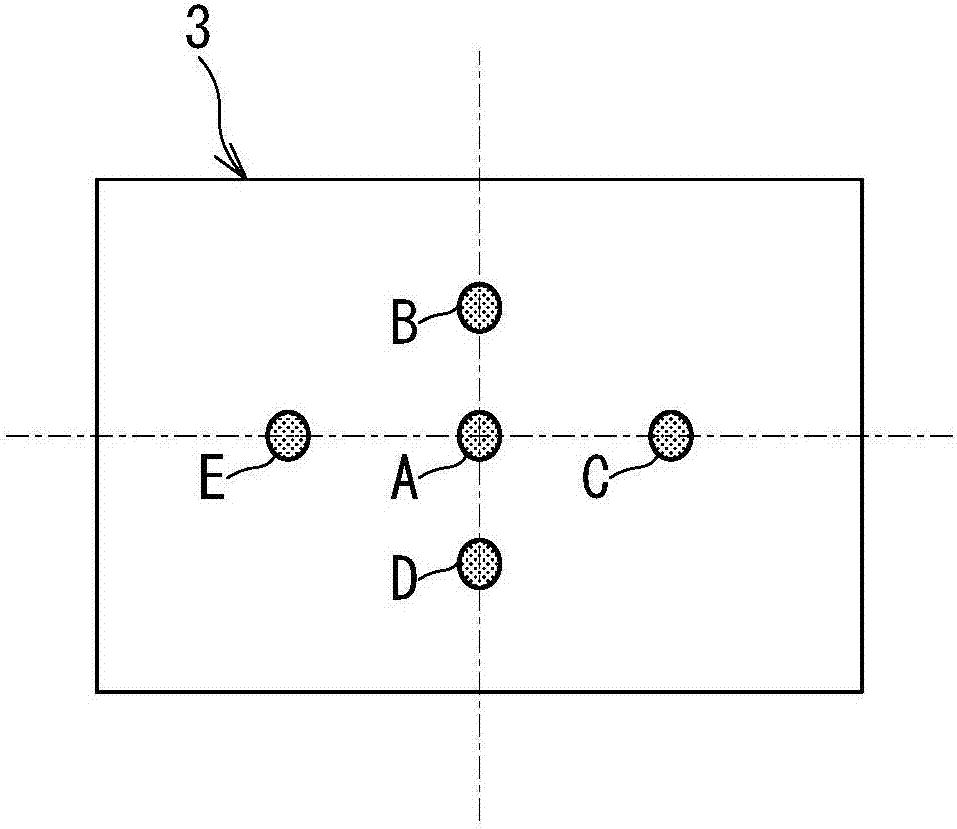
本申請(qǐng)是國(guó)際申請(qǐng)日為2011年2月10日國(guó)際申請(qǐng)?zhí)枮閜ct/jp2011/052910、中國(guó)國(guó)家申請(qǐng)?zhí)枮?0118009729.x,名稱為“耐磨元件以及制造該耐磨元件的方法”的申請(qǐng)的分案申請(qǐng)。本發(fā)明涉及一種耐磨(耐磨損)元件以及制造該元件的方法,并且更具體地涉及一種包含主要由氮化硅所形成的陶瓷燒結(jié)體的耐磨元件,以及制造該耐磨元件的方法。
背景技術(shù):
:陶瓷燒結(jié)體具有輕、高硬度、高耐磨性、高耐腐蝕性和低熱膨脹系數(shù)的性能,使得陶瓷燒結(jié)體廣泛地作為元件用于構(gòu)成精制的裝置。具體地,從優(yōu)異的高硬度和耐磨性的觀點(diǎn)來(lái)說(shuō),陶瓷燒結(jié)體已經(jīng)被優(yōu)選作為耐磨元件用于構(gòu)成軸承。在不同的陶瓷燒結(jié)體中,氮化硅(si3n4)燒結(jié)體具有高硬度和優(yōu)異的耐磨性,使得氮化硅燒結(jié)體優(yōu)選作為元件用于構(gòu)成軸承等。關(guān)于這種氮化硅燒結(jié)體,為了改進(jìn)作為構(gòu)成軸承等的耐磨元件的可靠性,一段時(shí)間以來(lái)已經(jīng)進(jìn)一步改進(jìn)了性能。例如,已經(jīng)提出了一種制造氮化硅燒結(jié)體的方法,包含步驟:通過(guò)將釔氧化物、尖晶石、氧化鋁和/或氮化鋁以規(guī)定的金屬元素的預(yù)定摩爾比和預(yù)定的含量比加入到氮化硅材料粉末,來(lái)制備材料粉末混合物;制備由該材料粉末混合物所形成的壓實(shí)體(模制體);在1400-1500℃的溫度燒結(jié)該壓實(shí)體;在1500-1650℃的溫度進(jìn)一步燒結(jié)該壓實(shí)體,由此來(lái)獲得相對(duì)密度為大約98%的燒結(jié)體;和在10atm或者更大的氮?dú)夥罩?,?400-1650℃的溫度對(duì)該燒結(jié)體進(jìn)行次級(jí)燒結(jié)(主燒結(jié))操作,由此來(lái)將相對(duì)密度提高到大約99%,以便能夠制造強(qiáng)度優(yōu)異,并且在強(qiáng)度性能方面具有較低分散的氮化硅燒結(jié)體(例如參考專利文獻(xiàn)1)。另外,作為用于制造這種類型的氮化硅燒結(jié)體所用的氮化硅原料粉末,通常已知的是優(yōu)選使用高純材料粉末。例如,通過(guò)酰亞胺熱分解方法所合成的高純度材料粉末是適用的。但是,這種高純度材料粉末是非常昂貴的,并且因此所制造的氮化硅燒結(jié)體的機(jī)械強(qiáng)度和斷裂韌性值傾向于變得過(guò)大,因此產(chǎn)生了這樣的問(wèn)題,即,所形成的燒結(jié)體的可加工性是不足的。為了解決這個(gè)問(wèn)題,已經(jīng)論述了一種通過(guò)使用廉價(jià)的氮化硅原料粉末來(lái)制造氮化硅燒結(jié)體的方法,該氮化硅原料粉末是通過(guò)將金屬si直接氮化的直接氮化方法來(lái)制造的。該通過(guò)直接氮化方法所制造的氮化硅原料粉末具有相對(duì)大的fe和ca含量。但是,已知的是當(dāng)將稀土元素、鋁成分和碳化硅等的含量控制到預(yù)定的范圍內(nèi)時(shí),可以獲得機(jī)械強(qiáng)度、耐磨性和滾動(dòng)壽命性能等于或者大于常規(guī)燒結(jié)體的燒結(jié)體,并且所形成的燒結(jié)體的可加工性也是優(yōu)異的(例如參見專利文獻(xiàn)2)。如上所述,當(dāng)由該含有氮化硅原料粉末的材料粉末的混合物所形成的壓實(shí)體(模制體)進(jìn)行初級(jí)燒結(jié)時(shí),獲得了相對(duì)密度為大約98%的燒結(jié)體。其后,將所形成的燒結(jié)體進(jìn)一步在壓力為10atm或者更大的氮?dú)夥罩羞M(jìn)行次級(jí)燒結(jié)操作,從而獲得相對(duì)密度高于98%、優(yōu)選99%或者更大的燒結(jié)體,由此來(lái)制造強(qiáng)度優(yōu)異,并且強(qiáng)度性能分散較小的氮化硅燒結(jié)體。但是,為了在初級(jí)燒結(jié)操作獲得大約98%的相對(duì)密度,必須嚴(yán)格的控制該制造方法,因此產(chǎn)生了這樣的問(wèn)題,即,制造氮化硅燒結(jié)體所需的生產(chǎn)成本不利地增加了。如上所述,通過(guò)直接氮化方法所制造的氮化硅材料粉末的成本是相對(duì)低的。此外,當(dāng)將包含在氮化硅材料粉末中的稀土元素、鋁成分和碳化硅等的量控制到預(yù)定的范圍內(nèi)時(shí),可以制造這樣的氮化硅燒結(jié)體,其具有優(yōu)異的機(jī)械強(qiáng)度、耐磨性和滾動(dòng)壽命(rollinglife)性能等,特別是優(yōu)異的加工性?,F(xiàn)有技術(shù)文獻(xiàn)專利文獻(xiàn)專利文獻(xiàn)1:日本專利申請(qǐng)(公開)no.06-080470專利文獻(xiàn)2:國(guó)際專利申請(qǐng)(公開)no.wo2005/030674技術(shù)實(shí)現(xiàn)要素:本發(fā)明所要解決的技術(shù)問(wèn)題但是,因此所制造的氮化硅燒結(jié)體表現(xiàn)出它特性的離差(分散性),因此當(dāng)這些氮化硅燒結(jié)體在更苛刻的條件下用作耐磨元件時(shí),產(chǎn)生了這樣的問(wèn)題,即,一些燒結(jié)體具有不足的特性。此外,因?yàn)榇嬖谏鲜鎏匦缘碾x差(dispersion),當(dāng)燒結(jié)體加工成耐磨元件時(shí),一些燒結(jié)體在加工過(guò)程等期間易于損壞,因此產(chǎn)生了在耐磨元件制造加工時(shí),產(chǎn)率降低的嚴(yán)重問(wèn)題。此外,在氮化硅燒結(jié)體用作耐磨元件的情況中,研磨加工是一個(gè)基本方法。但是,因?yàn)楦呙芏鹊牡锜Y(jié)體是一種硬質(zhì)材料,其難以進(jìn)行研磨加工,因此研磨加工的負(fù)荷很大,因此需要大量的人工-小時(shí)和加工時(shí)間。本發(fā)明已經(jīng)解決了上述問(wèn)題。因此,本發(fā)明的一個(gè)目標(biāo)是提供一種耐磨(磨損)元件,其包含能夠以低成本制造和同時(shí)能夠抑制特性的離差的氮化硅燒結(jié)體。具體的,本發(fā)明的目標(biāo)是提供一種能夠降低其研磨加工的負(fù)荷的耐磨元件。本發(fā)明的另一目標(biāo)是提供一種有效制造這樣的耐磨元件的方法。解決問(wèn)題的手段為了實(shí)現(xiàn)上述目標(biāo),本發(fā)明的一種實(shí)施方案提供了一種由主要由氮化硅燒結(jié)體組成的陶瓷燒結(jié)體所形成的耐磨元件,該陶瓷燒結(jié)體含有10-3500ppm的按照f(shuō)e元素計(jì)的fe成分,大于1000ppm至2000ppm的按照ca元素計(jì)的ca成分,和1-2000ppm的按照mg元素計(jì)的mg成分,其中氮化硅晶粒的β-相比是95%或者更大,氮化硅晶粒的最大長(zhǎng)徑是40μm或者更低,通過(guò)xrd(x射線衍射方法)沒(méi)有檢測(cè)出存在于晶界相中的ca成分,并且該耐磨元件內(nèi)部的維氏(vicker)硬度、斷裂韌性和密度中每個(gè)的離差處于±10%的范圍。優(yōu)選的是通過(guò)xrd沒(méi)有檢測(cè)出存在于該陶瓷燒結(jié)體的晶界相中的mg成分。此外,還優(yōu)選的是該陶瓷燒結(jié)體包含0.1-5質(zhì)量%的選自下面的至少一種元素:ti,zr,hf,w,mo,ta,nb和cr。此外,還優(yōu)選的是前述陶瓷燒結(jié)體包含1-5質(zhì)量%的以稀土元素計(jì)的稀土成分,和1-5質(zhì)量%的以al元素計(jì)的al成分。另外,還優(yōu)選的是該陶瓷燒結(jié)體的維氏硬度是1400或者更大。此外,還優(yōu)選的是定義為構(gòu)成耐磨元件的氮化硅晶粒的各長(zhǎng)徑比的平均值的平均長(zhǎng)徑比是2或者更大。此外,還優(yōu)選的是該陶瓷燒結(jié)體包含表面粗糙度(ra)是1μm或者更低的研磨的表面。根據(jù)本發(fā)明的另外一種實(shí)施方案,這里提供了一種制造由主要由氮化硅形成的陶瓷燒結(jié)體所形成的耐磨元件的方法,該方法包含步驟:制備一種材料粉末混合物,其含有氮化硅材料粉末、燒結(jié)劑粉末、10-3500ppm的按照f(shuō)e元素計(jì)的fe成分、大于1000ppm至2000ppm的按照ca元素計(jì)的ca成分、和1-2000ppm的按照mg元素計(jì)的mg成分;模制該材料粉末混合物,由此來(lái)形成模制體;在1600-1950℃的燒結(jié)溫度對(duì)該模制體進(jìn)行初級(jí)燒結(jié)操作,由此來(lái)獲得相對(duì)密度為80%或者更高且小于98%的初級(jí)燒結(jié)體;冷卻該初級(jí)燒結(jié)體,其中在燒結(jié)溫度到1400℃的溫度范圍內(nèi),將冷卻速率控制到100℃/小時(shí)或者更大;在1600-1900℃的燒結(jié)溫度對(duì)該初級(jí)燒結(jié)體進(jìn)行次級(jí)燒結(jié)操作,由此來(lái)獲得相對(duì)密度為98%或者更大的次級(jí)燒結(jié)體;和冷卻該次級(jí)燒結(jié)體,其中在燒結(jié)溫度到1400℃的溫度范圍內(nèi),將冷卻速率控制到100℃/小時(shí)或者更大。此外,還優(yōu)選的是該次級(jí)燒結(jié)操作是通過(guò)對(duì)初級(jí)燒結(jié)體進(jìn)行高溫等靜壓(hip)方法來(lái)實(shí)施。此外,還優(yōu)選的是該陶瓷燒結(jié)體包含1-5質(zhì)量%的以稀土元素計(jì)的稀土成分和1-5質(zhì)量%的以al元素計(jì)的al成分作為燒結(jié)劑。仍然的另外,還優(yōu)選的是該方法進(jìn)一步包含研磨該陶瓷燒結(jié)體的步驟,從而將該陶瓷燒結(jié)體的表面粗糙度ra控制到1μm或者更低。本發(fā)明的效果根據(jù)本發(fā)明由主要由氮化硅燒結(jié)體組成的陶瓷燒結(jié)體所形成的耐磨元件,該陶瓷燒結(jié)體含有10-3500ppm的按照f(shuō)e元素計(jì)的fe成分、大于1000ppm至2000ppm或者更低的按照ca元素計(jì)的ca成分、和1-2000ppm的按照mg元素計(jì)的mg成分,來(lái)提供耐磨元件,在其中將該耐磨元件的密度、硬度和斷裂韌性中每個(gè)的離差抑制到±10%的范圍,并且該耐磨元件還具有優(yōu)異的可靠性和低成本性。此外,根據(jù)本發(fā)明,可以獲得燒結(jié)的表面(燒結(jié)完成面),其是易于研磨的。另外,根據(jù)該制造耐磨元件的方法,該耐磨元件是如下來(lái)制造的:制備一種材料粉末混合物,其含有氮化硅材料粉末、燒結(jié)劑粉末、10-3500ppm的按照f(shuō)e元素計(jì)的fe成分、大于1000ppm至2000ppm的按照ca元素計(jì)的ca成分、和1-2000ppm的按照mg元素計(jì)的mg成分;模制該材料粉末混合物,由此來(lái)形成模制體;對(duì)該模制體進(jìn)行初級(jí)燒結(jié)操作,由此來(lái)獲得相對(duì)密度為80%或者更高且小于98%的初級(jí)燒結(jié)體;對(duì)該初級(jí)燒結(jié)體進(jìn)行次級(jí)燒結(jié)操作,由此來(lái)獲得相對(duì)密度為98%或者更大的次級(jí)燒結(jié)體,以使得能夠容易地制造這樣的耐磨元件,其含有10-3500ppm的fe成分、大于1000ppm至2000ppm的ca成分、和1-2000ppm的mg成分,并且具有抑制到±10%的范圍的密度、硬度和斷裂韌性的離差。附圖說(shuō)明圖1是一橫截面圖,表示在球形耐磨元件的情況中本發(fā)明的一種實(shí)施方案的耐磨元件,并且表示出測(cè)量該耐磨元件的維氏硬度、斷裂韌性和密度的點(diǎn)。圖2是一平面圖,表示了在矩形耐磨元件的情況中本發(fā)明的另外一種實(shí)施方案的耐磨元件,并且表示出測(cè)量該耐磨元件的維氏硬度、斷裂韌性和密度的點(diǎn)。圖3是一橫截面圖,表示用于測(cè)量本發(fā)明的耐磨(磨損)元件的滾動(dòng)壽命特性的推力(thrust)類型滾動(dòng)磨損(磨損)測(cè)試設(shè)備的結(jié)構(gòu)。具體實(shí)施方式接下來(lái),在下面解釋根據(jù)本發(fā)明一種實(shí)施方案的耐磨(磨損)元件的實(shí)施方案。該實(shí)施方案提供了一種由主要由氮化硅組成的陶瓷燒結(jié)體所形成的耐磨元件,該陶瓷燒結(jié)體的特征在于含有10-3500ppm的按照f(shuō)e元素計(jì)的fe成分、大于1000ppm至2000ppm的按照ca元素計(jì)的ca成分、和1-2000ppm的按照mg元素計(jì)的mg成分,其中氮化硅晶粒的β-相比是95%或者更大,氮化硅晶粒的最大長(zhǎng)徑是40μm或者更低,通過(guò)xrd(x射線衍射方法)沒(méi)有檢測(cè)出存在于晶界相中的ca成分,并且該耐磨元件內(nèi)部的維氏硬度、斷裂韌性和密度中每個(gè)的離差處于±10%的范圍。在耐磨元件的fe成分、ca成分或者mg成分的含量超過(guò)上述范圍的情況中,不利的產(chǎn)生了作為破裂起始點(diǎn)的脆性隔離部分,因此容易降低耐磨元件的特性例如硬度、斷裂韌性等。所以,當(dāng)該耐磨元件進(jìn)行表面加工來(lái)制造耐磨裝置或者當(dāng)該耐磨元件實(shí)際上用作耐磨元件時(shí),易于發(fā)生脫落和破裂。另一方面,在fe成分、ca成分和mg成分小于上述范圍的情況中,必需使用高純度的氮化硅材料粉末來(lái)制造該耐磨元件,這樣材料成本大幅升高,因此在經(jīng)濟(jì)上是不利的。為了提高后述的易磨性(研磨加工的容易性),優(yōu)選的是將fe成分的含量設(shè)定到以fe元素計(jì)100-2000ppm的范圍內(nèi)、ca成分的含量設(shè)定到以ca元素計(jì)為1100ppm-1600ppm的范圍內(nèi)、和mg成分的含量設(shè)定到以mg元素計(jì)為100ppm-1000ppm的范圍內(nèi)。就此而言,在本發(fā)明中“ppm”的單位表示“質(zhì)量%”。即,在本發(fā)明中,因?yàn)殡s質(zhì)含量例如fe成分、ca成分和mg成分被控制到上述范圍內(nèi),因此可以使用廉價(jià)的氮化硅原料粉末,其含有相對(duì)大量的fe成分、ca成分和mg成分作為雜質(zhì)。該廉價(jià)的氮化硅原料粉末是通過(guò)將金屬si直接氮化的直接氮化方法來(lái)制造的。使用這樣的低成本原料是非常有利的,結(jié)果是極大地降低了耐磨元件的制造成本。另外,在本發(fā)明中,雖然耐磨元件中包含了作為雜質(zhì)的大量的fe成分、ca成分和mg成分,但是硬度、斷裂韌性和密度的離差被抑制到±10%的范圍內(nèi)。所以,甚至在該耐磨元件長(zhǎng)期使用的情況中,引起脫落或者破裂的耐磨元件的數(shù)量很小,因此可以獲得具有優(yōu)異可靠性的耐磨元件。此外,即使該陶瓷燒結(jié)體包含大于1000ppm且2000ppm或者更小的量的ca,當(dāng)進(jìn)行xrd分析時(shí),沒(méi)有檢測(cè)出ca的化合物?!巴ㄟ^(guò)xrd分析沒(méi)有檢測(cè)出ca的化合物”表示沒(méi)有檢測(cè)到ca的化合物的峰,并且ca的化合物基本上變成無(wú)定形相。上述ca的化合物的例子可以包括單物質(zhì)的ca、ca的氧化物、ca和燒結(jié)劑的反應(yīng)產(chǎn)物等。此外,該xrd分析是在使用cu靶(cukα)的條件下進(jìn)行的,x射線管電壓是40kv,x射線管電流是100ma。此外,ca成分含量可以通過(guò)icp分析(誘導(dǎo)性偶合的等離子體質(zhì)譜法)來(lái)檢測(cè)。因?yàn)閏a的化合物變成了無(wú)定形相,因此能夠降低耐磨元件的研磨加工負(fù)荷。因?yàn)樵撗心ゼ庸さ呢?fù)荷能夠降低至很小,因此容易獲得平的研磨的表面,該表面的表面粗糙度ra是1μm或者更低,進(jìn)一步的0.1μmra或者更低。此外,優(yōu)選的是通過(guò)xrd分析也沒(méi)有檢測(cè)出在陶瓷燒結(jié)體的晶界相中存在著mg成分的峰。特征“通過(guò)xrd分析沒(méi)有檢測(cè)出mg的化合物的峰”表示mg的化合物基本變成了無(wú)定形相。此外,上述mg的化合物的例子可以包括單物質(zhì)mg、mg的氧化物,mg和燒結(jié)劑的反應(yīng)產(chǎn)物,和mg和ca的反應(yīng)產(chǎn)物等。因?yàn)閙g的化合物變成了無(wú)定形相,因此耐磨元件的研磨加工負(fù)荷可以進(jìn)一步降低到很小。晶界相中是否存在ca的化合物和mg的化合物可以通過(guò)epma(電子探針微分析)方法,使用彩色成圖(colormapping)技術(shù)來(lái)確認(rèn)。此外,必需將上述陶瓷燒結(jié)體(氮化硅燒結(jié)體)的氮化硅晶粒的β-相比設(shè)定到95%或者更大。該β-相類型氮化硅晶粒具有三角系晶體,因?yàn)槟軌蛱岣吣湍ピ母邷貜?qiáng)度。當(dāng)上述氮化硅晶粒的β-相比小于95%時(shí),陶瓷燒結(jié)體的強(qiáng)度不利地降低了。在本發(fā)明中,耐磨元件中的氮化硅晶粒的最大長(zhǎng)徑優(yōu)選設(shè)定為40μm或者更小。換句話說(shuō),優(yōu)選的是在該耐磨元件中不存在長(zhǎng)徑超過(guò)40μm的粗氮化硅晶粒。在其中在該耐磨元件中存在長(zhǎng)徑超過(guò)40μm的粗氮化硅晶粒的情況中,該粗氮化硅晶粒充當(dāng)了破裂的開始點(diǎn),因此燒結(jié)體的斷裂韌性極大降低,并且機(jī)械強(qiáng)度也降低了,因此確實(shí)不是優(yōu)選的。就此而言,氮化硅晶粒的最大長(zhǎng)徑是通過(guò)下面的方式來(lái)測(cè)量的。即,將該耐磨元件切割,并且對(duì)切割表面進(jìn)行鏡面拋光。隨后,將該鏡面拋光的表面進(jìn)行蝕刻處理,由此除去晶界成分。然后,通過(guò)×5000或者更大放大倍率的掃描型電子顯微鏡(sem)對(duì)單位面積(100μm×100μm)進(jìn)行照相,該單位面積任意選自蝕刻的表面。氮化硅晶粒的最大長(zhǎng)徑是在照片上所觀察的各晶粒的最長(zhǎng)直徑。因此,當(dāng)在該耐磨元件的照片上沒(méi)有觀察到長(zhǎng)徑超過(guò)40μm的粗氮化硅晶粒時(shí),實(shí)現(xiàn)了本發(fā)明的要求。此外,在本發(fā)明的耐磨元件中,同樣優(yōu)選的是定義為氮化硅晶粒各長(zhǎng)徑比的平均值的平均長(zhǎng)徑比是2或者更大。在長(zhǎng)徑比小于2的情況中,耐磨元件的微結(jié)構(gòu)將不是其中氮化硅晶粒是以復(fù)雜的方式形成的并且彼此復(fù)雜纏繞的結(jié)構(gòu),因此耐磨元件的機(jī)械強(qiáng)度等易于變成不足的。就此而言,氮化硅晶粒的長(zhǎng)徑比(=長(zhǎng)徑/短徑)是通過(guò)與上述用于測(cè)量氮化硅晶粒的最大長(zhǎng)徑的相同方法來(lái)獲得的。即,將該耐磨元件切割,并且對(duì)切割表面進(jìn)行鏡面拋光。隨后,將該鏡面拋光的表面進(jìn)行蝕刻處理,由此除去晶界成分。然后,通過(guò)掃描型電子顯微鏡(sem)對(duì)單位面積表面進(jìn)行照相。測(cè)量在照片上所觀察的氮化硅晶粒的長(zhǎng)徑和短徑。結(jié)果,長(zhǎng)徑比是作為長(zhǎng)直徑與短直徑之比來(lái)獲得的。另外,平均長(zhǎng)徑比是通過(guò)將照片上所顯示的在單位面積(100μm×100μm)中所觀察的全部氮化硅晶粒的各長(zhǎng)徑比的平均而獲得的。此外,還優(yōu)選的是該陶瓷燒結(jié)體包含1-5質(zhì)量%的以稀土計(jì)的稀土成分和1-5質(zhì)量%的以al元素計(jì)的al成分作為燒結(jié)劑。由于燒結(jié)劑的存在,可以獲得具有高密度的燒結(jié)體。稀土元素化合物的例子可以包括稀土氧化物,具體地,釔氧化物、鉺氧化物、鐿氧化物等。此外,作為al成分,使用氧化鋁、氮化鋁等。這些成分在陶瓷燒結(jié)體中與氮化硅等反應(yīng),由此來(lái)產(chǎn)生稀土元素-si-al-o-n類型化合物等作為構(gòu)成晶界相的成分而存在。稀土成分和al成分的量是通過(guò)分析各元素的含量來(lái)獲得的。此外,還優(yōu)選的是該陶瓷燒結(jié)體包含0.1-5質(zhì)量%的選自下面的至少一種元素:ti、zr、hf、w、mo、ta、nb和cr。這些元素能夠有效增強(qiáng)晶界相。在這些元素中,hf是最優(yōu)選的。hf與稀土元素反應(yīng),由此來(lái)形成晶體化合物,因此hf能夠有效增強(qiáng)晶界相。hf和稀土元素的結(jié)晶化合物可以通過(guò)xrd分析來(lái)鑒定和檢測(cè)。由于增強(qiáng)的晶界相,能夠進(jìn)一步提高燒結(jié)體的硬度和斷裂韌性。此外,本發(fā)明的耐磨元件具有優(yōu)異的性能,因此維氏硬度(hv)是1400或者更大,斷裂韌性是5.5mpa·m1/2或者更大。在這些耐磨元件具有高硬度和/或高斷裂韌性的情況中,各特性的離差受到抑制。此外,即使將維氏硬度(hv)設(shè)定為1430或者更高和將斷裂韌性設(shè)定為6.0mpa·m1/2或者更大,也可以抑制各特性的離差。就此而言,維氏硬度(hv)或者斷裂韌性或者密度的離差是按照如下方式來(lái)計(jì)算的。圖1是一橫截面圖,表示了球形耐磨元件的一個(gè)例子,和圖2是一平面圖,表示了矩形板狀耐磨元件的另一例子。在圖1所示的球形耐磨元件4的情況中,橫截面的中心部分表示為a點(diǎn),而直線的中間四個(gè)點(diǎn)(每個(gè)點(diǎn)連接到耐磨元件4的中心點(diǎn)a和周邊端點(diǎn))分別表示為b點(diǎn)、c點(diǎn)、d點(diǎn)和e點(diǎn)。維氏硬度(hv)、斷裂韌性和密度是分別在a-e點(diǎn)5個(gè)點(diǎn)測(cè)量的。將該測(cè)量值平均來(lái)獲得各平均值。另一方面,在圖2所示的矩形板狀耐磨元件3的情況中,平面的中心部分表示為a點(diǎn),而直線的中間四個(gè)點(diǎn)(每個(gè)點(diǎn)連接到耐磨元件3的中心點(diǎn)a和周邊端點(diǎn))分別表示為b點(diǎn)、c點(diǎn)、d點(diǎn)和e點(diǎn)。維氏硬度(hv)、斷裂韌性和密度是分別在a-e點(diǎn)5個(gè)點(diǎn)測(cè)量的。然后將該測(cè)量值平均來(lái)計(jì)算維氏硬度(hv)、斷裂韌性和密度的平均值。此外,在許多測(cè)量值中,在數(shù)字上偏離平均值最大(距離平均值最大的最遠(yuǎn)值)的最遠(yuǎn)值定義為“最大偏離值”。然后,將測(cè)量平均值和最大偏離值代入下文中的計(jì)算式(1)中,由此來(lái)計(jì)算各離差。離差[%]=[(平均值–最大偏離值)/平均值]×100---(1)就此而言,維氏硬度是根據(jù)日本工業(yè)標(biāo)準(zhǔn)(jisr1610)所規(guī)定的方法來(lái)測(cè)量的。另外,斷裂韌性是通過(guò)規(guī)定于日本工業(yè)標(biāo)準(zhǔn)(jisr1607)中的if方法測(cè)量的。此外,密度的離差是按照下面的方式來(lái)測(cè)量的。即,首先,從5個(gè)點(diǎn)(a-e點(diǎn))上切割下試樣。然后,對(duì)于各試樣,基于阿基米德原理來(lái)測(cè)量密度,并且對(duì)測(cè)量值進(jìn)行平均,由此來(lái)獲得平均密度。然后,按照與硬度和斷裂韌性相同的方式,基于計(jì)算式(1)來(lái)計(jì)算離差(%)。在本發(fā)明中,耐磨元件密度的離差也設(shè)定為±10%內(nèi)。就此而言,優(yōu)選的是該陶瓷燒結(jié)體的密度是3.18g/cm3或者更大。此外,更優(yōu)選的是該陶瓷燒結(jié)體的密度是3.25g/cm3或者更大。本發(fā)明的這些耐磨元件不僅可以用作構(gòu)成軸承等的滾珠,而且還可以用作需要耐磨(磨損)性的不同應(yīng)用所用的結(jié)構(gòu)元件。不同應(yīng)用的例子可以包括切割工具、旋轉(zhuǎn)夾具(rollingjig)、閥門的檢查球(checkball)、發(fā)動(dòng)機(jī)零件、各種夾具和工具、各種圍欄和各種輥?zhàn)?。具體的,本發(fā)明的耐磨元件能夠適用于直徑為3mm或者更大,進(jìn)一步的10mm或者更大的大球形(球)體,和短邊長(zhǎng)度為30mm或者更大,進(jìn)一步的100mm或者更大的大尺寸元件。本發(fā)明可以提供一種耐磨裝置。本發(fā)明的耐磨裝置包含上述耐磨元件,特別是包含許多上述本發(fā)明的耐磨元件。具體的,本發(fā)明的耐磨裝置包含例如使用該耐磨元件作為滾珠的軸承,或者包含這種軸承的裝置。在這些耐磨裝置中,因?yàn)槟湍ピ挠捕群蛿嗔秧g性的離差被限定到±10%的范圍內(nèi),因此造成損壞例如脫落或者破裂等的耐磨元件的量是非常小的,因此能夠長(zhǎng)期抑制振動(dòng)等的產(chǎn)生,并且該耐磨元件具有優(yōu)異的可靠性。此外,根據(jù)本發(fā)明的耐磨裝置,可以使用前述相對(duì)廉價(jià)的含有大量fe成分、ca成分和mg成分的氮化硅材料粉末用于構(gòu)建耐磨元件,以使得該耐磨裝置的成本能夠降低到相對(duì)廉價(jià)。換句話說(shuō),可以使用廉價(jià)的氮化硅材料粉末和燒結(jié)劑粉末(各個(gè)含有大量fe成分、ca成分和mg成分作為雜質(zhì)),來(lái)獲得進(jìn)一步的成本降低效應(yīng)。此外,在本發(fā)明中,當(dāng)進(jìn)行研磨加工來(lái)獲得表面粗糙度為1μmra或者更低,進(jìn)一步的0.1μmra或者更低的陶瓷燒結(jié)體時(shí),可以降低研磨加工的負(fù)荷,即,當(dāng)進(jìn)行研磨加工來(lái)獲得表面粗糙度為1μmra或者更低的氮化硅燒結(jié)體時(shí),通常進(jìn)行使用金剛石磨石(磨光粉)的研磨加工。在這種情況中,在本發(fā)明的耐磨元件中,存在于晶界相中的ca的化合物是作為無(wú)定形化合物而存在的,其比結(jié)晶化合物軟。ca成分在燒結(jié)步驟后易于浸泡出到陶瓷燒結(jié)體表面上。所以,當(dāng)ca的化合物的無(wú)定形化合物形成于陶瓷燒結(jié)體表面上時(shí),該表面能夠容易地進(jìn)行研磨。為此原因,金剛石磨石的損壞是很小的,并且可以減少氮化硅燒結(jié)體本身的研磨量(研磨余量)。換句話說(shuō),本發(fā)明適用于具有研磨的表面的耐磨元件。本發(fā)明的耐磨元件可以例如是具有幾乎板形狀的一種實(shí)施方案的耐磨元件,并且該耐磨元件的測(cè)試表面進(jìn)行研磨加工來(lái)獲得鏡面。然后,這樣的板形耐磨元件連接到圖3所示的滾動(dòng)磨損測(cè)試設(shè)備1上。將三個(gè)suj2鋼滾珠4(每個(gè)直徑是9.35mm和五級(jí)或者更高級(jí)的表面狀態(tài))置于直徑40mm的軌道上,該軌道布置在板形耐磨元件3的頂表面上。當(dāng)這些鋼滾球4以1200rpm的轉(zhuǎn)速如下的條件下旋轉(zhuǎn)時(shí),即,施加負(fù)荷來(lái)對(duì)該滾珠施加最大接觸應(yīng)力5.9gpa的條件下旋轉(zhuǎn)時(shí),優(yōu)選的是滾動(dòng)壽命是優(yōu)選至少2×107,該滾動(dòng)壽命定義為當(dāng)板形耐磨元件3脫落時(shí),所發(fā)生的旋轉(zhuǎn)數(shù)。本發(fā)明的耐磨元件例如是滾動(dòng)壽命為至少2×107的元件,其等于或者長(zhǎng)于常規(guī)的耐磨元件的滾動(dòng)壽命。本發(fā)明的耐磨元件也可以例如用作球形元件例如滾珠(軸承珠),而非前述的板形元件。在其中本發(fā)明的耐磨元件用作滾珠的情況中,對(duì)于滾珠的尺寸沒(méi)有具體限制,例如,可以合適的使用直徑為3mm或者更大的滾珠。此外,當(dāng)直徑設(shè)定到10mm或者更大,進(jìn)一步20mm或者更大時(shí),與通過(guò)常規(guī)方法所制造的常規(guī)耐磨元件的這些相比,特性例如滾動(dòng)壽命等能夠明顯改進(jìn)。此外,當(dāng)該耐磨元件的直徑設(shè)定到相對(duì)高時(shí),與通過(guò)使用昂貴的氮化硅材料粉末(通過(guò)常規(guī)的酰亞胺熱分解方法合成)所制造的球形耐磨元件相比,制造的主要成本的差異變得更明顯。此外,形成本發(fā)明的耐磨元件來(lái)提供球形體,其每個(gè)的直徑是9.35mm。該球形體進(jìn)行了研磨加工。然后,將這樣的球形體連接到圖3所示的滾動(dòng)磨損測(cè)試設(shè)備上。當(dāng)將三個(gè)球形耐磨元件(滾珠)4(每個(gè)的表面狀態(tài)是5級(jí)或者更大)置于直徑為40mm的軌道上,該軌道布置在suj2鋼板的頂表面上,其測(cè)試表面被鏡面拋光。然后,當(dāng)球形耐磨元件4以1200rpm的轉(zhuǎn)速這樣的條件下旋轉(zhuǎn)時(shí),即,施加負(fù)荷來(lái)對(duì)該球形耐磨元件4施加最大接觸應(yīng)力5.9gpa的條件下旋轉(zhuǎn)時(shí),優(yōu)選的是滾動(dòng)壽命是優(yōu)選至少400小時(shí),該滾動(dòng)壽命定義為當(dāng)球形耐磨元件4的表面脫落時(shí)的持續(xù)時(shí)間。本發(fā)明的耐磨元件具有上述至少400小時(shí)的滾動(dòng)壽命,其等于或者長(zhǎng)于常規(guī)耐磨元件(滾珠)的壽命。接下來(lái),在下文中解釋本發(fā)明的制造耐磨元件的方法。本發(fā)明提供了一種制造由主要由氮化硅組成的陶瓷燒結(jié)體所形成的耐磨元件的方法,該方法包含下面的步驟:制備一種材料粉末混合物,其含有氮化硅材料粉末、燒結(jié)劑粉末、10-3500ppm的按照f(shuō)e元素計(jì)的fe成分、大于1000ppm至2000ppm的按照ca計(jì)的ca成分、和1-2000ppm的按照mg元素計(jì)的mg成分;模制該材料粉末混合物,由此來(lái)形成模制體;在1600-1950℃的燒結(jié)溫度對(duì)該模制體進(jìn)行初級(jí)燒結(jié)操作,由此來(lái)獲得相對(duì)密度為80%或者更高且小于98%的初級(jí)燒結(jié)體;冷卻該初級(jí)燒結(jié)體,其中在燒結(jié)溫度到1400℃的溫度范圍內(nèi),將冷卻速率控制到100℃/小時(shí)或者更大;在1600-1900℃的燒結(jié)溫度對(duì)該初級(jí)燒結(jié)體進(jìn)行次級(jí)燒結(jié)操作,由此來(lái)獲得相對(duì)密度為98%或者更大的次級(jí)燒結(jié)體;和冷卻該次級(jí)燒結(jié)體,其中在燒結(jié)溫度到1400℃的溫度范圍內(nèi),將冷卻速率控制到100℃/小時(shí)或者更大。與使用常規(guī)的初級(jí)和次級(jí)燒結(jié)步驟的方法相比,本發(fā)明的方法采用其中燒結(jié)體的相對(duì)密度控制到相對(duì)低的80-小于98%的初級(jí)燒結(jié)步驟,和采用了其中將燒結(jié)體的相對(duì)密度進(jìn)一步提高到98%或者更大的次級(jí)燒結(jié)步驟(致密化的燒結(jié)步驟)。當(dāng)進(jìn)行上述初級(jí)和次級(jí)燒結(jié)步驟時(shí),甚至在其中材料粉末混合物中的fe成分,ca成分和mg成分的量相對(duì)大的情況中,也能夠容易地制造耐磨元件,其具有優(yōu)異的硬度和斷裂韌性,并且將硬度和斷裂韌性的離差抑制到±10%的范圍中。此外,在初級(jí)和次級(jí)燒結(jié)步驟之后,將該燒結(jié)體以100℃/h或者更大的冷卻速率快速冷卻,直到該燒結(jié)體的溫度低到1400℃,以使得可以防止ca的化合物變成結(jié)晶化合物。作為用于制造上述耐磨元件的氮化硅原料粉末,例如優(yōu)選使用這樣的氮化硅原料粉末,其含有10-3500ppm的按照f(shuō)e元素計(jì)的fe成分、大于1000ppm至2000ppm的按照ca計(jì)的ca成分、和1-2000ppm的按照mg元素計(jì)的mg成分。作為含有處于上述范圍內(nèi)的fe成分、ca成分和mg成分的氮化硅材料粉末,例如合適的可以使用廉價(jià)的通過(guò)金屬氮化方法所制造的氮化硅原料粉末。此外,作為該氮化硅材料粉末,考慮到燒結(jié)特性例如彎曲強(qiáng)度和斷裂韌性等,優(yōu)選可以使用這樣的氮化硅材料粉末,其含有至少80質(zhì)量%,優(yōu)選90-97質(zhì)量%的α-氮化硅,該α-氮化硅含有1.5質(zhì)量%或者更低的,優(yōu)選0.9%-1.2質(zhì)量%的氧,并且平均粒徑是1.2μm或者更低,優(yōu)選大約0.6-大約1.0μm。就此而言,已知的是氮化硅原料粉末具有α-相類型和β-相類型。由β-相類型氮化硅粉末制成的氮化硅燒結(jié)體傾向于具有不足的強(qiáng)度。相反,在燒結(jié)操作之后,α-相類型氮化硅材料粉末變成β-相類型氮化硅晶粒,因此這里能夠提供高強(qiáng)度的燒結(jié)體,其中該具有高長(zhǎng)徑比的氮化硅晶粒是高度纏繞的。在α-相類型和β-相類型氮化硅材料粉末總量中,當(dāng)在本發(fā)明的方法中將α-相類型氮化硅材料粉末的混合比控制到至少80質(zhì)量%時(shí),能夠改進(jìn)該耐磨元件的彎曲強(qiáng)度、斷裂韌性和滾動(dòng)壽命。另一方面,考慮到燒結(jié)特性,將α-相類型氮化硅材料粉末的混合比限制到97質(zhì)量%或者更低。優(yōu)選α-相類型氮化硅材料粉末的量是90-95質(zhì)量%。此外,作為氮化硅材料粉末,具體的,使用平均粒徑為0.8μm或者更低的細(xì)原料粉末能夠提供孔隙率為2%或者更低的致密燒結(jié)體,甚至使用較少量的燒結(jié)劑時(shí)也是如此,因此是優(yōu)選的。這種燒結(jié)體的孔隙率可以根據(jù)阿基米德原理來(lái)容易的測(cè)量和確定。優(yōu)選的是將稀土元素加入到該氮化硅原料粉末中作為燒結(jié)助劑(燒結(jié)劑)。作為稀土元素,優(yōu)選的是將選自y、ho、er、yb、la、sc、pr、ce、nd、dy、sm和gd等的至少一種元素加入到該氮化硅原料粉末中。這些稀土元素與氮化硅原料粉末反應(yīng)來(lái)產(chǎn)生液相,因此充當(dāng)了燒結(jié)促進(jìn)劑(燒結(jié)劑)。優(yōu)選的是將稀土元素的添加量控制到相對(duì)于包含氮化硅材料粉末和其他燒結(jié)助劑的整個(gè)材料粉末混合物(下文簡(jiǎn)稱為“材料粉末混合物”)為1-5質(zhì)量%。當(dāng)稀土元素的添加量小于1質(zhì)量%時(shí),所形成的耐磨元件具有不足的密度和強(qiáng)度。具體的,當(dāng)該稀土元素具有高原子重量的鑭系元素時(shí),耐磨元件見具有相對(duì)低的強(qiáng)度。另一方面,當(dāng)燒結(jié)助劑的添加量超過(guò)5質(zhì)量%時(shí),產(chǎn)生了過(guò)量的晶界相。這能夠提高耐磨元件的孔數(shù)或者降低強(qiáng)度。此外,還優(yōu)選的是將鋁成分加入到氮化硅原料粉末中。這種鋁成分優(yōu)選作為氧化鋁(a12o3)或者氮化鋁(aln)來(lái)加入。此外,優(yōu)選的是將這些鋁成分的總添加量設(shè)定到相對(duì)于整個(gè)材料粉末混合物為1-5質(zhì)量%(以al元素計(jì))的范圍內(nèi)。加入氧化鋁(al2o3)來(lái)提高稀土元素作為燒結(jié)促進(jìn)劑的功能,這允許在低的燒結(jié)溫度時(shí)提高密度,控制晶體結(jié)構(gòu)中的晶粒的生長(zhǎng),和提高機(jī)械強(qiáng)度,例如耐磨元件的彎曲強(qiáng)度和斷裂韌性等。優(yōu)選的是在其中氧化鋁與aln一起協(xié)同使用的情況中,將氧化鋁的添加量控制到相對(duì)于整個(gè)材料粉末混合物為4質(zhì)量%或者更低的范圍內(nèi)。當(dāng)氧化鋁的添加量大于4質(zhì)量%時(shí),燒結(jié)體中的氧含量升高。該升高的氧含量引起了晶界相中存在的成分不均勻的分布和耐磨元件滾動(dòng)壽命的降低,因此不是優(yōu)選的。相反,當(dāng)氧化鋁(al2o3)的添加量小于2質(zhì)量%時(shí),由于添加al2o3所形成的效應(yīng)是不足的,因此優(yōu)選的是將氧化鋁的添加量控制到2質(zhì)量%或者更大。由于上述觀點(diǎn),氧化鋁(al2o3)的添加量更優(yōu)選設(shè)定到2質(zhì)量%至3.5質(zhì)量%或者更低的范圍。另一方面,將氮化鋁(aln)理想的以相對(duì)于整個(gè)材料粉末混合物為3質(zhì)量%或者更低來(lái)加入,來(lái)防止或者降低燒結(jié)操作過(guò)程中氮化硅成分的蒸發(fā),和提高稀土元素作為燒結(jié)促進(jìn)劑的功能。但是,大于3質(zhì)量%的添加量的aln降低了耐磨元件的機(jī)械強(qiáng)度和滾動(dòng)壽命,因此不是優(yōu)選的。相反,當(dāng)?shù)X(aln)的添加量小于1質(zhì)量%時(shí),通過(guò)加入aln引起的上述作用是不足的。因此,aln的添加量?jī)?yōu)選控制到1質(zhì)量%或者更大。就此而言,將2-4質(zhì)量%的al2o3和1-3質(zhì)量%的aln二者加入到氮化硅材料粉末能夠更有效的改進(jìn)耐磨元件的機(jī)械特性。但是,過(guò)量的al2o3和aln的總量降低了耐磨(磨損)元件的滾動(dòng)壽命。因此,將鋁成分在原料粉末混合物中的總量?jī)?yōu)選設(shè)定到6質(zhì)量%或者更低(氧化物當(dāng)量)。另一方面,優(yōu)選的是將選自ti、hf、zr、w、mo、ta、nb和cr的氧化物、碳化物、氮化物、硅化物和硼化物中的至少一種化合物加入到氮化硅原料粉末中。這些化合物提高了稀土氧化物等作為燒結(jié)促進(jìn)劑的功能,促進(jìn)了結(jié)晶結(jié)構(gòu)的離差,和改進(jìn)了包含燒結(jié)的氮化硅的耐磨元件的機(jī)械強(qiáng)度和滾動(dòng)壽命。在這些化合物中,ti、mo和hf的化合物是特別優(yōu)選的。當(dāng)例如ti等的這些化合物相對(duì)于整個(gè)材料粉末混合物的添加量按照其元素計(jì)小于0.1質(zhì)量%時(shí),通過(guò)加入所述化合物帶來(lái)的功能是不足的。另一方面,當(dāng)添加量超過(guò)5質(zhì)量%時(shí),該耐磨元件的機(jī)械強(qiáng)度和滾動(dòng)壽命降低。因此,將該化合物的添加量限制到0.1-5質(zhì)量%的范圍。更理想的,將該化合物的量具體限制到0.5-2質(zhì)量%的范圍。此外,碳化硅(sic)也可以加入到該氮化硅原料粉末中。碳化硅(sic)是作為單個(gè)粒子分散在晶體結(jié)構(gòu)中,并且明顯改進(jìn)了耐磨元件的滾動(dòng)壽命。當(dāng)碳化硅相對(duì)于整個(gè)材料粉末混合物的添加量小于2質(zhì)量%時(shí),通過(guò)加入碳化硅所帶來(lái)的作用是不足的。另一方面,當(dāng)添加量超過(guò)7質(zhì)量%時(shí),該燒結(jié)體導(dǎo)致了不足的致密化和耐磨元件彎曲強(qiáng)度的降低。因此,將碳化硅的量?jī)?yōu)選限制到2-7質(zhì)量%的范圍。順便說(shuō)一下,碳化硅可以分成α-類型和β-類型,其二者都表現(xiàn)出相同的操作作用,因此可以加入任一類型的碳化硅。本發(fā)明的耐磨元件是通過(guò)例如下面的方法來(lái)制造的。即,上述原料粉末混合物是如下來(lái)制備的:將預(yù)定量的所需添加劑例如燒結(jié)助劑(其包含稀土元素,如果需要,包含鋁成分例如氧化鋁(al2o3)和/或氮化鋁(aln),和任選存在的化合物例如ti等)加入到如上所述的氮化硅細(xì)粉末中。此外,將有機(jī)粘合劑成分加入到這種原料粉末混合物中,由此來(lái)制備粒狀粉末。同時(shí),在原料粉末混合物中沒(méi)有預(yù)先包含預(yù)定量的fe成分、ca成分和mg成分的情況中,通過(guò)補(bǔ)足各個(gè)成分不足的量來(lái)制備該原料粉末混合物。因此,將因此獲得的粒狀粉末模制成具有預(yù)定形狀的壓實(shí)體(模制體)。作為模制粒狀粉末的方法,合適的是使用通用的模制壓模方法和cip(冷等靜壓)方法等。在通過(guò)模制壓模方法和cip(冷等靜壓)方法形成壓實(shí)體(模制體)的情況中,該粒狀粉末優(yōu)選在120mpa或者更大的壓力下模制來(lái)形成晶界相,其中特別是在燒結(jié)操作之后,很難形成孔和空穴。當(dāng)模制壓力小于120mpa時(shí),容易形成由稀土元素化合物形成的粘著部分(cohesiveportion)(隔離部分),其主要形成了晶界相。另外,所形成的模制體具有不足的密度,并且該耐磨元件易于產(chǎn)生許多裂紋。另一方面,當(dāng)模制壓力設(shè)定超過(guò)200mpa時(shí),模制模具的耐久性降低,因此生產(chǎn)率不好。因此,模制壓力優(yōu)選設(shè)定為120-200mpa。隨后,將模制體(模制壓實(shí)體)在非氧化性氣氛中在600℃-800℃的溫度加熱或者在空氣中在400℃-500℃的溫度加熱1-2小時(shí),來(lái)充分除去有機(jī)粘合劑成分,并且使該模制體脫脂。然后,將該脫脂的模制體在惰性氣體例如氮?dú)獾姆茄趸詺夥罩羞M(jìn)行初級(jí)燒結(jié)步驟,由此將所形成的初級(jí)燒結(jié)體的相對(duì)密度控制到80%或者更高且小于98%。其后,將所形成的初級(jí)燒結(jié)體進(jìn)一步在非氧化性氣氛中進(jìn)行次級(jí)燒結(jié)步驟,以使得所形成的次級(jí)燒結(jié)體的相對(duì)密度控制到98%或者更大,由此來(lái)形成氮化硅燒結(jié)體(耐磨元件)。就此而言,燒結(jié)體的相對(duì)密度定義為基于阿基米德原理所測(cè)量的實(shí)際密度相對(duì)于氮化硅燒結(jié)體理論密度的比率(%)。作為獲得理論密度的方法,該理論密度可以簡(jiǎn)單地通過(guò)下面的簡(jiǎn)化方法來(lái)獲得。例如,根據(jù)理化詞典(physical-chemistrydictionary)等,氮化硅所述的理論密度是3.185g/cm3,釔氧化物(y2o3)是5.03g/cm3,氧化鋁(al2o3)是4.0g/cm3,和氧化鎂(mgo)是3.58g/cm3。氮化硅燒結(jié)體的理論密度還可以通過(guò)將y含量轉(zhuǎn)化成釔氧化物,將al成分轉(zhuǎn)化成氧化鋁,將mg成分轉(zhuǎn)化成氧化鎂,如下來(lái)計(jì)算。氮化硅燒結(jié)體的理論密度=(氮化硅的質(zhì)量×理論密度+釔氧化物的質(zhì)量×理論密度+…)例如,當(dāng)假定各成分的含量是92質(zhì)量%的氮化硅,5質(zhì)量%的釔氧化物和3質(zhì)量%的氧化鋁時(shí),具有上述組成的氮化硅燒結(jié)體的理論密度是通過(guò)下面的計(jì)算式來(lái)計(jì)算的。(氮化硅的質(zhì)量:0.92×3.185+釔氧化物的質(zhì)量:0.05×5.03+氧化鋁的質(zhì)量:0.03×4.0)=3.3017g/cm3如上所述,根據(jù)本發(fā)明,將模制體在初級(jí)燒結(jié)步驟中燒結(jié),來(lái)獲得80-98%或者更低的相對(duì)密度,其低于通過(guò)常規(guī)制造方法所制造的燒結(jié)體的密度。其后,將該燒結(jié)體進(jìn)一步在次級(jí)燒結(jié)步驟中燒結(jié),來(lái)主要提高燒結(jié)體的相對(duì)密度。結(jié)果,可以將氮化硅燒結(jié)體(耐磨元件)的硬度和斷裂韌性的離差抑制到±10%的范圍內(nèi)。此外,在初級(jí)和次級(jí)燒結(jié)步驟之后,進(jìn)行冷卻步驟。在冷卻步驟中,將該燒結(jié)體以100℃/h或者更大的冷卻速率快速冷卻,直到燒結(jié)體的溫度降低到1400℃。當(dāng)該快速冷卻步驟是以100℃/h或者更大的冷卻速率進(jìn)行時(shí),晶界相會(huì)變成無(wú)定形相。當(dāng)晶界相變成無(wú)定形相時(shí),它可以防止ca的化合物變成結(jié)晶化合物。對(duì)上述冷卻速率的上限沒(méi)有特別的限制,但是,500℃/h或者更低的冷卻速率是優(yōu)選的。燒結(jié)溫度是1600℃/h或者更大,以使得如果冷卻步驟是以超過(guò)500℃的冷卻速率進(jìn)行的,則用于冷卻設(shè)備的負(fù)荷變大。將要控制的溫度范圍設(shè)定到燒結(jié)溫度到1400℃的原因如下。即,當(dāng)稀土元素化合物和al成分用作燒結(jié)劑時(shí),這些成分一度形成了液相。其后,直到1400℃的溫度,該液相凝固,由此來(lái)完全變成晶界相。就此而言,在1400℃或者更低的溫度范圍不需要對(duì)冷卻速率進(jìn)行特別的控制。此外,當(dāng)控制這樣的冷卻速率時(shí),不僅能夠形成均勻的晶界相,而且還降低了密度的離差。此外,這里可以獲得優(yōu)異的特性,例如維氏硬度是1400或者更大,和斷裂韌性是5.5mpa·m1/2或者更大,優(yōu)選該維氏硬度是1430或者更大,和該斷裂韌性是6.0mpa·m1/2或者更大。另外,硬度或者斷裂韌性的離差可以抑制到±10%的范圍內(nèi)。即,當(dāng)在初級(jí)燒結(jié)步驟中相對(duì)密度設(shè)定到小于80%或者大于98%時(shí),難以將氮化硅燒結(jié)體(耐磨元件)的維氏硬度和斷裂韌性的離差設(shè)定到±10%的范圍,即使在次級(jí)燒結(jié)步驟中將相對(duì)密度設(shè)定為98%或者更大也是如此。在本發(fā)明中,從在前述的次級(jí)燒結(jié)步驟完成時(shí)將氮化硅燒結(jié)體的密度設(shè)定到高密度和將氮化硅燒結(jié)體的硬度和斷裂韌性的離差抑制到±10%范圍的觀點(diǎn)來(lái)說(shuō),優(yōu)選的是燒結(jié)體的密度應(yīng)當(dāng)在初級(jí)燒結(jié)步驟的階段設(shè)定到85%-小于98%的范圍內(nèi)。為了實(shí)現(xiàn)初級(jí)燒結(jié)步驟完成后燒結(jié)體的相對(duì)密度為80-小于98%,應(yīng)當(dāng)在例如1600℃-1950℃的溫度進(jìn)行常壓燒結(jié)操作或者壓力燒結(jié)操作2–8小時(shí),更優(yōu)選在1700℃-1850℃進(jìn)行2–6小時(shí)。當(dāng)初級(jí)燒結(jié)步驟的上述燒結(jié)溫度低于上述溫度范圍的下限或者當(dāng)初級(jí)燒結(jié)步驟的燒結(jié)時(shí)間小于上述時(shí)間范圍的下限,則難以在初級(jí)燒結(jié)步驟完成的階段將初級(jí)燒結(jié)體的密度設(shè)定到80%或者更大。此外,在其中初級(jí)燒結(jié)步驟的燒結(jié)溫度超過(guò)上述溫度范圍上限或者其中初級(jí)燒結(jié)步驟的燒結(jié)時(shí)間超過(guò)上述時(shí)間范圍上限的情況中,燒結(jié)在初級(jí)燒結(jié)步驟過(guò)度進(jìn)行,以至于這里會(huì)恐怕所形成的初級(jí)燒結(jié)體的密度超過(guò)98%。此外,該次級(jí)燒結(jié)步驟優(yōu)選是通過(guò)例如進(jìn)行高溫等靜壓(hip)處理來(lái)進(jìn)行的,在其中將初級(jí)燒結(jié)體在其中對(duì)初級(jí)燒結(jié)體施加70mpa或者更大優(yōu)選100mpa或者更大的壓力的狀態(tài)在1600-1900℃的溫度進(jìn)一步燒結(jié)0.5-2小時(shí)。當(dāng)次級(jí)燒結(jié)步驟的上述燒結(jié)溫度低于上述溫度范圍的下限或者當(dāng)壓力低于上述范圍時(shí),或者當(dāng)次級(jí)燒結(jié)步驟的燒結(jié)時(shí)間小于上述時(shí)間范圍的下限時(shí),恐怕在次級(jí)燒結(jié)步驟完成階段所形成的氮化硅燒結(jié)體(次級(jí)燒結(jié)體)的相對(duì)密度將不是98%或者更大的高密度。另外,這里還恐怕難以將氮化硅次級(jí)燒結(jié)體的硬度,斷裂韌性和密度的離差抑制到±10%的范圍內(nèi)。另一方面,當(dāng)燒結(jié)溫度超過(guò)上述溫度范圍的上限時(shí),恐怕氮化硅成分易于蒸發(fā)和分解。此外,在其中燒結(jié)時(shí)間超過(guò)上述時(shí)間范圍的上限時(shí),恐怕相對(duì)密度無(wú)法進(jìn)一步提高和致密化效應(yīng)是飽和的,因此增加了制造時(shí)間(加工時(shí)間),因此不是優(yōu)選的。此外,當(dāng)初級(jí)和次級(jí)燒結(jié)操作的時(shí)間設(shè)定到1600℃或者更高的高溫時(shí),燒結(jié)劑變成了液體成分,并且例如氮化硅粉末中所包含的ca成分浸泡出到液相中,因此會(huì)形成其中ca的化合物存在于燒結(jié)體的燒結(jié)的表面上的狀態(tài)。如上所述,根據(jù)本發(fā)明的制造耐磨元件的方法,當(dāng)使用含有10-3500ppm的fe成分、大于1000ppm至2000ppm或者更低的ca成分和1-2000ppm的mg成分的材料粉末混合物時(shí),進(jìn)一步的該燒結(jié)操作是分別在兩個(gè)階段中進(jìn)行的,可以制造其中將該氮化硅燒結(jié)體的硬度和斷裂韌性的離差抑制到±10%的范圍內(nèi)的氮化硅燒結(jié)體(耐磨元件)。此外,根據(jù)本發(fā)明的制造耐磨元件的方法,例如這里可以制造其中氮化硅晶粒長(zhǎng)徑是40μm或者更低,和平均長(zhǎng)徑比是2或者更大,優(yōu)選4或者更大的這樣的氮化硅燒結(jié)體(耐磨元件)。此外,如果需要,將因此獲得的陶瓷燒結(jié)體進(jìn)行研磨加工。在其中將陶瓷燒結(jié)體用作耐磨元件的情況中,優(yōu)選的是進(jìn)行鏡面研磨加工,來(lái)獲得表面粗糙度ra為1μm或者更低,進(jìn)一步的0.1μm或者更低。該研磨加工是使用金剛石磨石來(lái)進(jìn)行的。此時(shí),當(dāng)ca的化合物存在于陶瓷燒結(jié)體的燒結(jié)的表面時(shí),該燒結(jié)的表面的硬度可以稍降低一些。所以,研磨時(shí)間可以縮短,并且還會(huì)降低金剛石磨石的損傷,因此能夠降低研磨加工的負(fù)荷。此外,當(dāng)ca的化合物被配置到存在于燒結(jié)的表面上時(shí),研磨余量(待研磨的燒結(jié)體的量)會(huì)降低。所以,在其中進(jìn)行鏡面研磨加工來(lái)獲得表面粗糙度ra為1μm或者更低,進(jìn)一步的0.1μm或者更低的情況中,研磨余量比常規(guī)的燒結(jié)體小,因此能夠獲得鏡面拋光表面,而不排出廢料。此外,根據(jù)本發(fā)明的制造耐磨元件的方法,在其中耐磨元件具有板形的情況中,可以制造滾動(dòng)壽命為2×107或者更大的板形耐磨元件,該滾動(dòng)壽命是通過(guò)預(yù)定的操作來(lái)定義的。此外,在其中耐磨元件為球形的情況中,可以制造球形耐磨元件,其滾動(dòng)壽命是400小時(shí)或者更大,該滾動(dòng)壽命是通過(guò)預(yù)定的操作來(lái)定義的。實(shí)施方案接下來(lái),將參考下述的實(shí)施例和對(duì)比例來(lái)詳細(xì)具體的解釋本發(fā)明的實(shí)施方案。(實(shí)施例1-7和對(duì)比例1-4)這里制備了多種si3n4(氮化硅)材料粉末,其是通過(guò)金屬氮化方法來(lái)制造的,并且每個(gè)材料粉末包含下表1所示的不同量的fe成分(以fe元素計(jì)為10–3500ppm)、ca成分(以ca元素計(jì)為50–2000ppm)和mg成分(以ca元素計(jì)為10–2000ppm)。將這些氮化硅材料粉末與作為燒結(jié)促進(jìn)劑(燒結(jié)劑)的y2o3(釔氧化物)粉末、al2o3(氧化鋁)粉末、aln(氮化鋁)粉末和hfo2(二氧化鉿)粉末進(jìn)行混合,由此來(lái)制備各自含有表1所示量的fe成分、ca成分和mg成分的材料粉末混合物。就此而言,在其中氮化硅材料粉末中的fe,ca和mg的量不足的情況中,通過(guò)進(jìn)一步加入氧化物到氮化硅材料粉末中來(lái)控制所述量從而獲得表1所示的含量值。就此而言,使用各自具有平均粒徑為0.3-1.5μm的氮化硅材料粉末和燒結(jié)促進(jìn)劑粉末。此外,在該材料粉末混合物中,y2o3的含量是3質(zhì)量%,aln的含量是2質(zhì)量%,hfo2是1質(zhì)量%,并且補(bǔ)足量是氮化硅材料粉末。例如,非氮化硅材料粉末的材料粉末,即,y2o3粉末、al2o3粉末、aln粉末和hfo2粉末中的每種作為燒結(jié)促進(jìn)劑,其包含10ppm或者更低量的fe成分、ca成分和mg成分。將每種材料粉末混合物在乙醇中使用氮化硅球作為研磨介質(zhì)進(jìn)行濕磨(共混和研磨)48小時(shí),然后干燥來(lái)制備均勻的材料粉末混合物。此外,將有機(jī)粘合劑加入到每種均勻的材料粉末混合物中,由此來(lái)制備共混的粒狀粉末。[表1]接下來(lái),將每個(gè)共混的粒狀粉末以150mpa的模壓力進(jìn)行壓模,由此來(lái)制備多個(gè)模制體。隨后,將這些模制體在溫度450℃的空氣流動(dòng)氣氛中脫脂4小時(shí)。其后,將每個(gè)脫脂的模制體在表2所示的燒結(jié)條件下、在壓力0.7mpa的氮?dú)夥障逻M(jìn)行初級(jí)燒結(jié)步驟(操作),由此來(lái)形成各初級(jí)燒結(jié)體。此外,將每個(gè)初級(jí)燒結(jié)體然后在表2所示的燒結(jié)條件下進(jìn)行次級(jí)燒結(jié)步驟,由此來(lái)制造各次級(jí)燒結(jié)體和來(lái)提供由氮化硅燒結(jié)體組成的各耐磨性元件。就此而言,上述的次級(jí)燒結(jié)步驟是作為其中在氮?dú)夥罩袑?duì)該初級(jí)燒結(jié)體施加了100mpa的壓力的高溫等靜壓(hip)方法來(lái)進(jìn)行的。測(cè)量了在初級(jí)燒結(jié)步驟之后燒結(jié)體的密度(相對(duì)密度)和次級(jí)燒結(jié)步驟之后燒結(jié)體的密度(相對(duì)密度)。各測(cè)量結(jié)果表示在下面的表2中。就此而言,每個(gè)燒結(jié)體的密度(相對(duì)密度)(%)是作為通過(guò)阿基米德原理所測(cè)量的實(shí)際的密度相對(duì)于氮化硅燒結(jié)體的理論密度比率(%)來(lái)測(cè)量的。[表2]就此而言,燒結(jié)體的密度(其是通過(guò)阿基米德原理測(cè)量的)是3.10g/cm3-3.26g/cm3。具體的,燒結(jié)體實(shí)際測(cè)量值如下。在實(shí)施例1中,初級(jí)燒結(jié)體的密度是3.24g/cm3,而次級(jí)燒結(jié)體的密度是3.26g/cm3。在實(shí)施例1中,初級(jí)燒結(jié)體的密度是3.24g/cm3,而次級(jí)燒結(jié)體的密度是3.26g/cm3。在實(shí)施例2中,初級(jí)燒結(jié)體的密度是3.24g/cm3,而次級(jí)燒結(jié)體的密度是3.26g/cm3。在實(shí)施例3中,初級(jí)燒結(jié)體的密度是3.24g/cm3,而次級(jí)燒結(jié)體的密度是3.26g/cm3。在實(shí)施例4中,初級(jí)燒結(jié)體的密度是3.16g/cm3,而次級(jí)燒結(jié)體的密度是3.18g/cm3。在實(shí)施例5中,初級(jí)燒結(jié)體的密度是3.23g/cm3,而次級(jí)燒結(jié)體的密度是3.25g/cm3。在實(shí)施例6中,初級(jí)燒結(jié)體的密度是3.25g/cm3,而次級(jí)燒結(jié)體的密度是3.28g/cm3。在實(shí)施例7中,初級(jí)燒結(jié)體的密度是3.14g/cm3,而次級(jí)燒結(jié)體的密度是3.16g/cm3。在對(duì)比例1中,初級(jí)燒結(jié)體的密度是3.12g/cm3,而次級(jí)燒結(jié)體的密度是3.15g/cm3。在對(duì)比例2中,初級(jí)燒結(jié)體的密度是3.12g/cm3,而次級(jí)燒結(jié)體的密度是3.13g/cm3。在對(duì)比例3中,初級(jí)燒結(jié)體的密度是3.10g/cm3,而次級(jí)燒結(jié)體的密度是3.14g/cm3。在對(duì)比例4中,初級(jí)燒結(jié)體的密度是3.10g/cm3,而次級(jí)燒結(jié)體的密度是3.15g/cm3。此外,在實(shí)施例1-7和對(duì)比例1–2的氮化硅燒結(jié)體中,氮化硅晶粒的β-相比是95-98%。另一方面,在對(duì)比例3–4的氮化硅燒結(jié)體中,氮化硅晶粒的β-相比是90-92%。接下來(lái),對(duì)于因此根據(jù)每個(gè)實(shí)施例和對(duì)比例所制造的耐磨元件,測(cè)量了維氏硬度、斷裂韌性值,及其平均值、其離差、和滾動(dòng)壽命。就此而言,維氏硬度是根據(jù)日本工業(yè)標(biāo)準(zhǔn)(jis-r-1610)規(guī)定的方法測(cè)量的。根據(jù)每個(gè)實(shí)施例和對(duì)比例的耐磨元件3的維氏硬度的平均值是通過(guò)對(duì)在圖2所示的a-e五個(gè)測(cè)量點(diǎn)上測(cè)量的五個(gè)測(cè)量值進(jìn)行平均來(lái)獲得的。此外,維氏硬度的離差是通過(guò)下面的方式來(lái)獲得的。即,在所測(cè)量的5個(gè)值中,將在數(shù)字上與平均值偏離最大的最遠(yuǎn)值(遠(yuǎn)離平均值最大的最遠(yuǎn)值)定義為“最大偏離值”。然后,將所測(cè)量的平均值和最大偏離值代入下面的計(jì)算式中,由此來(lái)計(jì)算維氏硬度的離差。離差[%]=[(平均值–最大偏離值)/平均值]×100另外,斷裂韌性是根據(jù)日本工業(yè)標(biāo)準(zhǔn)(jis-r-1607)規(guī)定的if方法來(lái)測(cè)量的。此外,通過(guò)與維氏硬度的這些相同的方法來(lái)獲得平均值和斷裂韌性的離差。各耐磨(磨損)元件中每個(gè)的滾動(dòng)壽命是通過(guò)使用圖3所示的推力類型滾動(dòng)磨損(磨損)測(cè)試設(shè)備1來(lái)測(cè)量的。該推力類型滾動(dòng)磨損測(cè)試設(shè)備1配置為包含:布置在測(cè)試設(shè)備1的主體2上的板形耐磨(磨損)元件3;布置在耐磨元件3上表面上的三個(gè)鋼滾珠4;布置在鋼滾珠4上的導(dǎo)板5;連接到導(dǎo)板5上的驅(qū)動(dòng)軸6;和用于限定各鋼滾珠4之間的間隔的支持架(固定器)7。主體2填充有潤(rùn)滑油8,用于潤(rùn)滑滾動(dòng)部分。在這種測(cè)量操作中,作為用于推力類型滾動(dòng)磨損(磨損)測(cè)試設(shè)備1的板形耐磨(磨損)元件3,使用了這樣的測(cè)試樣品,其是通過(guò)將實(shí)施例和對(duì)比例的每個(gè)耐磨元件加工成尺寸為70mm×70mm×3mm(厚度)的樣品而形成的。此時(shí),將板形元件(耐磨元件)3的表面粗糙度(ra)設(shè)定為0.01μm。此外,作為用于推力類型滾動(dòng)磨損(磨損)測(cè)試設(shè)備1的滾珠4,使用了每個(gè)由suj2構(gòu)成并且直徑是9.35mm的球形珠。在這種推力類型滾動(dòng)磨損測(cè)試設(shè)備中,對(duì)suj2滾珠4施加一定的負(fù)荷,來(lái)施加5.9gpa的最大接觸應(yīng)力。在這個(gè)條件下,這些滾珠4以1200rpm的速度旋轉(zhuǎn)。然后,當(dāng)由耐磨元件構(gòu)成的板形元件3的表面脫落時(shí),測(cè)量隨時(shí)間所發(fā)生的旋轉(zhuǎn)數(shù)。就此而言,通過(guò)將作為最大旋轉(zhuǎn)數(shù)的上限設(shè)定到3×107來(lái)測(cè)量旋轉(zhuǎn)數(shù)。表3表示了測(cè)量結(jié)果。[表3]從上表3所示的結(jié)果中很顯然,在各實(shí)施例1–7的耐磨元件中,其中進(jìn)行初級(jí)燒結(jié)步驟來(lái)獲得80-小于98%的相對(duì)密度,和進(jìn)行次級(jí)燒結(jié)步驟來(lái)獲得98%或者更大的相對(duì)密度,證實(shí)了將維氏硬度和斷裂韌性二者的離差控制到±10%的范圍內(nèi)。此外,還證實(shí)了實(shí)施例1–7的每個(gè)板形耐磨元件的全部的滾動(dòng)壽命超過(guò)了3×107圈,并且該耐磨元件還具有優(yōu)異的滾動(dòng)壽命。接下來(lái),對(duì)于因此根據(jù)每個(gè)實(shí)施例和對(duì)比例所制造的耐磨元件來(lái)說(shuō),測(cè)量了氮化硅晶粒的長(zhǎng)徑的最大值,同時(shí)計(jì)算了氮化硅晶粒的平均長(zhǎng)徑比。氮化硅晶粒的長(zhǎng)徑的最大值是通過(guò)下面的方式來(lái)測(cè)量的。即,切割所述的耐磨元件。隨后,通過(guò)×5000或者更大的放大倍率的掃描類型的電子顯微鏡(sem),對(duì)任選自切割表面的單位面積(100μm×100μm)進(jìn)行照相。觀察照片上該單位面積內(nèi)所選擇的具有最大長(zhǎng)徑的氮化硅晶粒,并且測(cè)量所選擇的氮化硅晶粒的長(zhǎng)徑,使得所測(cè)量的長(zhǎng)徑定義為長(zhǎng)徑的最大值。此外,平均長(zhǎng)徑比是通過(guò)下面的方式來(lái)計(jì)算的。即,對(duì)于存在于所觀察的照片中上述單位面積內(nèi)的全部的氮化硅晶粒,測(cè)量長(zhǎng)徑和短徑,由此從每個(gè)氮化硅晶粒的長(zhǎng)徑和短徑來(lái)獲得長(zhǎng)徑比。結(jié)果,平均長(zhǎng)徑比是通過(guò)將各長(zhǎng)徑比平均來(lái)計(jì)算的。表4表示了測(cè)量結(jié)果。[表4]從上表4所示的結(jié)果中很顯然,在各實(shí)施例1–7的耐磨元件中,其中進(jìn)行初級(jí)燒結(jié)步驟來(lái)獲得80-小于98%的相對(duì)密度,和進(jìn)行次級(jí)燒結(jié)步驟來(lái)獲得98%或者更大的相對(duì)密度,證實(shí)了長(zhǎng)徑的氮化硅晶粒的最大值是40μm或者更低,和在該耐磨元件的結(jié)構(gòu)中沒(méi)有產(chǎn)生長(zhǎng)徑超過(guò)40μm的任何粗的氮化硅晶粒。此外,在各實(shí)施例1–7的每個(gè)耐磨元件中,氮化硅晶粒的平均長(zhǎng)徑比是2或者更大,并且證實(shí)了該耐磨元件形成了其中柱形氮化硅晶粒彼此復(fù)雜纏繞的微觀結(jié)構(gòu)。接下來(lái),制備了與各實(shí)施例1–7和對(duì)比例1的耐磨元件相同的氮化硅燒結(jié)體。對(duì)于各氮化硅燒結(jié)體的燒結(jié)的表面和研磨的表面,進(jìn)行了xrd分析,來(lái)證實(shí)是否檢測(cè)到ca的化合物或者mg的化合物的結(jié)晶峰。另外,當(dāng)每個(gè)氮化硅元件進(jìn)行了研磨加工來(lái)獲得1μm或者0.1μm的表面粗糙度ra時(shí),測(cè)量了研磨加工的負(fù)荷。就此而言,通過(guò)假定對(duì)比例1的研磨時(shí)間是100作為比率基準(zhǔn),將該研磨加工的負(fù)荷表示為研磨時(shí)間的比率。表5表示了測(cè)量結(jié)果。[表5]從上表5所示的結(jié)果中很顯然,作為對(duì)各實(shí)施例的陶瓷燒結(jié)體進(jìn)行xrd分析的結(jié)果,在各陶瓷燒結(jié)體的燒結(jié)的表面和研磨的表面二者的全部都沒(méi)有檢測(cè)出ca的化合物或者mg的化合物的結(jié)晶峰。結(jié)果,證實(shí)了結(jié)晶ca的化合物或者mg的化合物沒(méi)有存在于各耐磨元件中。另外,還證實(shí)了目標(biāo)的研磨的表面能夠以比對(duì)比例1更短的研磨加工時(shí)間來(lái)獲得。相反在對(duì)比例1中,檢測(cè)到y(tǒng)-hf-o類型結(jié)晶化合物的衍射峰。(實(shí)施例8-11和對(duì)比例5)接下來(lái),在其中制造了作為一種耐磨元件的滾珠(軸承珠)的情況中,將評(píng)價(jià)因此所制造的滾珠的特性。制備了用于各實(shí)施例8-11和對(duì)比例5的多種材料粉末混合物,從而具有下表6所示的組成。[表6]接下來(lái),將該材料粉末混合物模制,由此來(lái)形成具有表6所示的上述組成的軸承珠模制體。然后,將該軸承珠模制體在表8所示的條件下進(jìn)行初級(jí)燒結(jié)操作和次級(jí)燒結(jié)操作,由此來(lái)制造具有表7所示直徑的各軸承珠。[表7]樣品no.軸承珠直徑(mm)實(shí)施例83實(shí)施例910實(shí)施例1015實(shí)施例1120對(duì)比例53[表8]接下來(lái),對(duì)于圖1所示的因此獲得的各自軸承珠的橫截面上設(shè)的五個(gè)測(cè)量點(diǎn)a–e來(lái)說(shuō),測(cè)量了其維氏硬度、斷裂韌性、密度和離差。要注意的是,該測(cè)量方法與實(shí)施例1所用的方法相同。此外,還測(cè)量了該軸承珠的滾動(dòng)壽命。使用圖3所示的前述推力類型滾動(dòng)磨損(研磨)測(cè)試設(shè)備1,測(cè)量作為耐磨元件的滾珠的滾動(dòng)壽命。就此而言,在前述的用于測(cè)量板形耐磨元件的滾動(dòng)壽命而提出的方法中,圖3所示的板形元件3由耐磨元件構(gòu)成,而滾珠4由suj2構(gòu)成。但是,與前述情況相比,在本發(fā)明的測(cè)量方法中,將由suj2構(gòu)成的板形元件用作板元件3,同時(shí)使用了滾珠4(表面粗糙度ra為0.01μm),其是通過(guò)加工實(shí)施例8-11和對(duì)比例5的耐磨元件來(lái)形成。在這種使用推力類型的滾動(dòng)磨損測(cè)試設(shè)備1的測(cè)量操作中,對(duì)滾珠4(每個(gè)由耐磨元件構(gòu)成)施加負(fù)荷,來(lái)接收最大5.9gpa的接觸應(yīng)力。在這種條件下,驅(qū)動(dòng)軸6和這些滾珠4是以1200rpm的轉(zhuǎn)速來(lái)旋轉(zhuǎn)的。然后,測(cè)量當(dāng)由耐磨元件構(gòu)成的滾珠4的表面脫落時(shí)的時(shí)間作為滾動(dòng)壽命。就此而言,通過(guò)設(shè)定上限400小時(shí)作為最大旋轉(zhuǎn)時(shí)間(小時(shí))來(lái)測(cè)量旋轉(zhuǎn)時(shí)間。表9表示了測(cè)量結(jié)果。[表9]從上表9所示的結(jié)果中很顯然,在每個(gè)由各實(shí)施例8–11的耐磨元件構(gòu)成的滾珠中,證實(shí)了維氏硬度、斷裂韌性值和密度全部的離差都是小的。此外,氮化硅晶粒的最大長(zhǎng)徑全部是0.01μm或者更小,和長(zhǎng)徑比是2或者更大。另外,因此獲得的各軸承珠的每個(gè)的密度是3.18g/cm3或者更大。另一方面,在軸承珠是對(duì)比例5的耐磨元件的情況中,斷裂韌性的離差是大的。此外,對(duì)由各實(shí)施例8-11和對(duì)比例5的氮化硅燒結(jié)體構(gòu)成的軸承珠的燒結(jié)的表面和研磨的表面進(jìn)行xrd分析,由此來(lái)確定能否檢測(cè)出ca的化合物的結(jié)晶峰。此外,測(cè)量了研磨加工的負(fù)荷。通過(guò)假定對(duì)比例5中的研磨時(shí)間是100來(lái)作為比率基準(zhǔn),將研磨加工的負(fù)荷表示為研磨時(shí)間的比率。表10表示了測(cè)量結(jié)果。[表10]從表10所示的結(jié)果中很顯然,與其中檢測(cè)出ca的化合物晶體的對(duì)比例5的軸承珠相比,在每個(gè)由其中沒(méi)有檢測(cè)出ca的化合物的各實(shí)施例8–11的耐磨元件構(gòu)成的軸承珠的情況中,很顯然能夠明顯縮短研磨時(shí)間,因此它還證實(shí)了能夠明顯降低加工成本。即,本發(fā)明實(shí)施例的軸承珠能夠通過(guò)400小時(shí)的研磨測(cè)試,進(jìn)一步的能夠降低研磨加工的負(fù)荷。此外,同樣很顯然通過(guò)更短的研磨時(shí)間能夠獲得相同的表面粗糙度。所以,該耐磨元件的制造成本能夠明顯降低和改進(jìn)。工業(yè)應(yīng)用性如上所述,根據(jù)本發(fā)明的由主要由氮化硅燒結(jié)體組成的陶瓷燒結(jié)體所形成的耐磨元件,該陶瓷燒結(jié)體含有10-3500ppm的按照f(shuō)e元素計(jì)的fe成分、大于1000ppm至2000ppm或者更低的按照ca元素計(jì)的ca成分、和1-2000ppm的按照mg元素計(jì)的mg成分,以使得這里能夠提供其中將耐磨元件的密度、硬度和斷裂韌性中每個(gè)的離差抑制到±10%的范圍內(nèi)的耐磨元件,并且該耐磨元件具有優(yōu)異的可靠性和低成本性能。此外,根據(jù)本發(fā)明,可以獲得燒結(jié)的表面(燒結(jié)完成表面),其易于研磨。此外,根據(jù)該制造耐磨元件的方法,如下來(lái)制造該耐磨元件:制備一種材料粉末混合物,其含有氮化硅材料粉末、燒結(jié)劑粉末、10-3500ppm的按照f(shuō)e元素計(jì)的fe成分、大于1000ppm至2000ppm的按照ca元素計(jì)的ca成分、和1-2000ppm的按照mg元素計(jì)的mg成分;模制該材料粉末混合物,由此來(lái)形成模制體;對(duì)該模制體進(jìn)行初級(jí)燒結(jié)操作,由此來(lái)獲得相對(duì)密度為80%或者更高且小于98%的初級(jí)燒結(jié)體;和對(duì)該初級(jí)燒結(jié)體進(jìn)行次級(jí)燒結(jié)操作,由此來(lái)獲得相對(duì)密度為98%或者更大的次級(jí)燒結(jié)體,使得這里能夠容易的制造這樣一種耐磨元件,其含有10-3500ppm的fe成分、大于1000ppm至2000ppm的ca成分、和1-2000ppm的mg成分,并且具有被抑制到±10%范圍內(nèi)的密度、硬度和斷裂韌性。參考標(biāo)記列表1…推力類型滾動(dòng)磨損(磨損)測(cè)試設(shè)備,2…設(shè)備體,3…板形耐磨元件(或者suj2金屬板),4…滾珠(或者球形耐磨元件),5…導(dǎo)板,6…驅(qū)動(dòng)旋轉(zhuǎn)軸,7…固定器,8…潤(rùn)滑油。當(dāng)前第1頁(yè)12