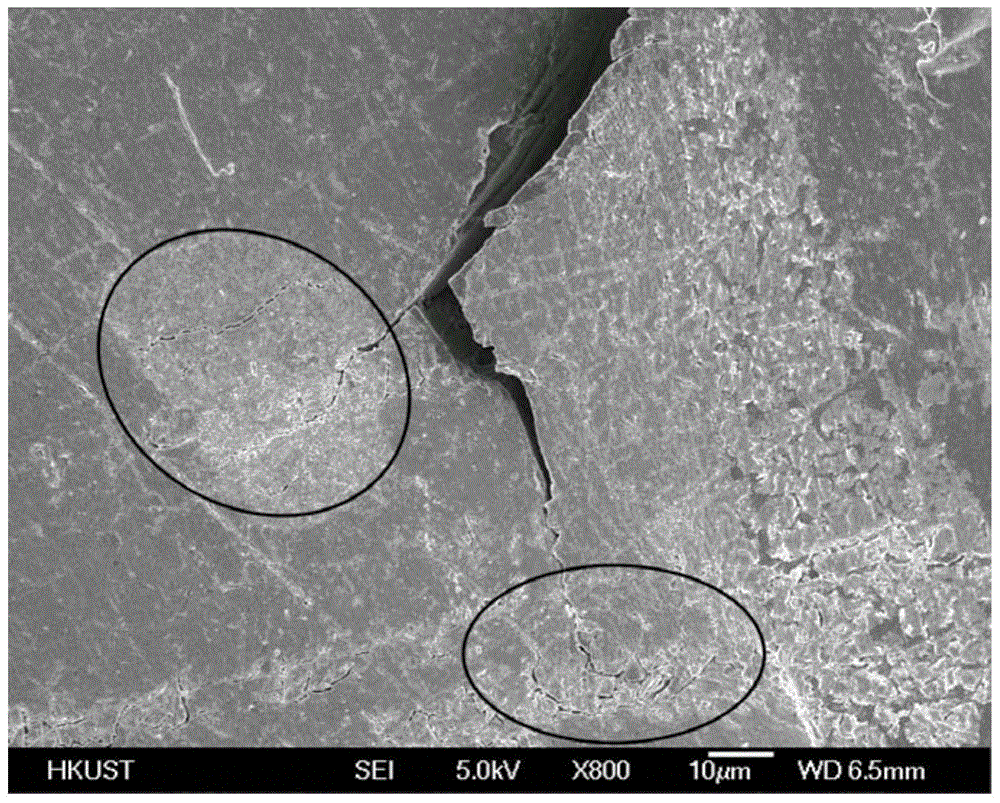
本發(fā)明涉及一種復合材料及其制備方法,特別地,涉及一種環(huán)氧樹脂/碳纖維/埃洛石納米管復合材料及其制備方法。
背景技術:碳纖維增強環(huán)氧樹脂復合材料由于高強、高韌、質(zhì)輕及高熱穩(wěn)定性等優(yōu)異性能廣泛應用于航空、航天和軍事等高端領域。在波音787和空客A380客機上,復合材料的重量占到了50%。飛機上使用復合材料除了減輕重量之外,還可以提高聲阻尼,降低熱傳導速率,從而更容易降低噪音,控制客艙內(nèi)溫度、濕度和通風。在我國大力發(fā)展航空航天事業(yè)的背景下,尤其在飛行器或民用飛機的制造方面,新型高性能碳纖維增強環(huán)氧樹脂復合材料將扮演不可或缺的重要角色。眾所周知,碳纖維增強復合材料的一個失效原因是由于層間剪切強度低,從而導致復合材料出現(xiàn)大量的層間斷裂。因此,如何提高碳纖維環(huán)氧復合材料的層間剪切強度一直是各國碳纖維復合材料研發(fā)人員的研究熱點和重點。目前,國際上主要采用兩種方法提高層壓復合材料的抗分層失效能力。第一種,利用一種先進的織造技術制備三維纖維增強結(jié)構(gòu)的復合材料??茖W家們采用編織,交錯編織以及縫合等方法來構(gòu)建三維纖維結(jié)構(gòu),在提高復合材料層間力學性能方面,縫合方法被證明比編織的方法更加有效。因為縫合工藝所產(chǎn)生的三維碳纖維的增強結(jié)構(gòu)大大限制了在拉伸載荷下裂紋擴展的長度,從而大幅度提高復合材料的層間斷裂韌性。在1994年CRC-AS,TM94012發(fā)布的文章“Improvementofinterlaminarpropertiesinadvancedfibrecompositeswiththrough-thicknessreinforcement”中,Jain等人報道說,在采用了縫合的方法制備碳纖維復合材料后,發(fā)生I型層間分離所需要的能量提高了至少15倍。與此同時,發(fā)生I型斷裂所需要的能量提高了2.9倍到15倍。許多實驗工作和微觀力學模型證明了縫合工藝還可以提高碳纖維增強高分子材料的II型層間斷裂韌性。但是,這種縫合工藝很大程度上影響碳纖維增強方向上的各種力學性能,它會導致材料的硬度和強度均有所降低,嚴重的影響這種高性能材料在飛機制造和其他高端領域方面的應用。除此以外,這種三維縫合的碳纖維結(jié)構(gòu)的復合材料需要依靠先進的編織機器,及高昂的人力成本。因此其造價幾乎是普通層壓的碳纖維增強高分子材料的5-10倍,對于體積比較大或者結(jié)構(gòu)不規(guī)則的產(chǎn)品來說,其成本還會更高。除了上述的方法,一些研究人員為了使得環(huán)氧樹脂(EP)韌性得到提高,在復合材料中加入了一些微米級的軟性有機物(比如:橡膠或其它熱塑性材料)。在Riew,C.K.;Kinloch,A.J.ToughenedplasticsI:Scienceandengineering;AmericanChemicalSociety,Washington,DC(UnitedStates):1993.中,加入軟性有機填充物,在沖擊過程中,其填充物內(nèi)部以及與環(huán)氧樹脂界面產(chǎn)生大量空洞,從而在環(huán)氧樹脂內(nèi)部引發(fā)大規(guī)模的剪切屈服來提高復合材料的沖擊強度。但是,加入了軟性有機物將不可避免的降低復合材料的硬度、強度和玻璃化轉(zhuǎn)變溫度等性能,制造出的材料無法適應航空工業(yè)嚴苛的環(huán)境要求。而且,由于交聯(lián)后的環(huán)氧樹脂本身的塑性變形能力低,這種增韌方法只能少許提高環(huán)氧樹脂的抗沖擊性能,仍然無法突破這種材料的發(fā)展瓶頸。隨著材料科學的快速發(fā)展,納米材料的應用引起了人們的極大興趣和廣泛關注。大量研究表明,使用少量的納米填料可以實現(xiàn)優(yōu)異的增強、增韌效果。因此,還有利用碳納米線來提高該復合材料的層間力學性能。比如,Yokozeki,T.;Iwahori,Y.;Ishibashi,M.;Yanagisawa,T.;Imai,K.;Arai,M.;Takahashi,T.;Enomoto,K.,FracturetoughnessimprovementofCFRPlaminatesbydispersionofcup-stackedcarbonnanotubes.CompositesScienceandTechnology2009,69(14),2268-2273中,TomohiroYokozeki等人在碳纖維增強高分子材料中加入了層疊杯狀(cup-stacked)的碳納米管,可以將I型斷裂韌性提高2倍.他們初步判斷是由于層疊狀納米管的存在引發(fā)裂紋尖端轉(zhuǎn)向?qū)е铝烁蟮臄嗔驯砻娣e的產(chǎn)生,從而提高了這種復合材料層間的斷裂韌性。但是,眾所周知的是,這些納米填料十分昂貴,1克普通的多壁碳納米管的市場價格可達幾百元人民幣,而無論是碳納米管還是碳納米線,對于該復合材料層間力學性能的提高也都十分有限。因此,這種方法在大規(guī)模工業(yè)生產(chǎn)中也是行不通的。因此,目前急需一種韌性和強度同時提高的碳纖維增強環(huán)氧樹脂復合材料及其制備方法。目前,用埃洛石納米管(HNT)和碳纖維(CF)協(xié)同增強增韌環(huán)氧樹脂的研究國內(nèi)尚屬空白。
技術實現(xiàn)要素:本發(fā)明的目的在于提供一種環(huán)氧樹脂/碳纖維/埃洛石納米管(EP/CF/HNT)復合材料的制備方法。該發(fā)明目的通過下列技術方案實現(xiàn),其包括步驟:1)將埃洛石納米管(HNT)分散到分散溶劑中,在室溫下攪拌直至均勻;加入環(huán)氧樹脂,攪拌獲得均勻溶液;2)使所述均勻溶液分層,然后取其上層清液;3)去除過量的分散溶劑,加入固化劑混合均勻獲得混合溶液;4)將上述混合溶液涂刷在碳纖維織物上,進行固化。所述固化包括施加0.1MPa至10MPa的壓強,其目的主要是對復合材料施加壓力,因為在這種條件下有利于復合材料的排氣和產(chǎn)生邊界約束,如此獲得的復合材料才能具有較好的力學性能。進一步地,所述埃洛石納米管的質(zhì)量為埃洛石納米管和環(huán)氧樹脂質(zhì)量總和的1-20%。進一步地,所述埃洛石納米管的質(zhì)量為埃洛石納米管和環(huán)氧樹脂質(zhì)量總和的1-5%。進一步地,所述碳纖維的體積為復合材料體積的10至30%,優(yōu)選29%。進一步地,將所述均勻溶液分層包括步驟:常溫靜置2至12個小時。優(yōu)選靜置2小時。進一步地,將所述均勻溶液分層包括步驟:使用離心機離心處理所述均勻溶液。在步驟2)中,采用靜置或者離心的步驟將均勻溶液分層,其目的相同,都是為了獲取分層之后的上層清液。本發(fā)明中,通過實驗發(fā)現(xiàn),埃洛石納米管某種程度的富集可在最終的環(huán)氧樹脂/碳纖維/埃洛石納米管復合材料產(chǎn)物中形成“海-島結(jié)構(gòu)”,而該“海-島結(jié)構(gòu)”有利于提高該復合材料的層間斷裂韌性。在本發(fā)明中通過步驟1)將埃洛石納米管和環(huán)氧樹脂混合后,雖然攪拌均勻,但是必然還會存在大量的埃洛石納米管的聚集體。這些埃洛石納米管聚集體中有一部分體積過大,容易造成復合材料的應力集中,不利于提高材料的韌性。還有一部分聚集體的體積適中,有助于生成上述的“海-島結(jié)構(gòu)”,提高材料韌性。通過離心或靜置后,體積較大的聚集體沉降,體積適中的聚集體均勻分散在上層清液中。這時取上層清液是去除沉降的聚集體,獲得有利的聚集體,這個步驟對于最終的復合材料優(yōu)異的力學性能是十分重要的。進一步地,所述離心處理的轉(zhuǎn)速優(yōu)選為1000-8000轉(zhuǎn)/分鐘,處理時間為5-15分鐘。進一步地,環(huán)氧樹脂優(yōu)選在60-75℃下加入。室溫下環(huán)氧樹脂是液態(tài),但是粘度較高,隨著溫度的提高,環(huán)氧樹脂的粘度顯著地降低,更有利于環(huán)氧樹脂和埃洛石納米管的混合均勻。進一步地,所述分散溶劑包括,但不限于,丙酮、四氫呋喃、二甲基甲酰胺、乙酸乙酯等。進一步地,所述去除過量的分散溶劑采用真空排出的方法。優(yōu)選采用室溫至75℃的溫度,更有利于分散溶劑的排出。進一步地,所述固化劑包括酸酐類、聚酚類、聚硫醇類和陽離子聚合型及陰離子聚合型固化劑。常用的用于固化環(huán)氧樹脂的固化劑都可適用,本申請優(yōu)選采用亞甲基雙苯二胺(MDA)。進一步地,所述固化工藝優(yōu)選為:在80℃下固化2小時,然后在160℃下固化4小時。本發(fā)明的另一目的在于提供上述制備方法所制備的一種環(huán)氧樹脂/碳纖維/埃洛石納米管復合材料。附圖說明圖1(a)-(c)本發(fā)明實施例3制備的EP/CF/HNT復合材料的掃描電鏡圖。圖2本發(fā)明實施例5制備的EP/CF/HNT復合材料的掃描電鏡圖。圖3(a)-(b)本發(fā)明實施例5制備的EP/CF/HNT復合材料的透射電鏡圖圖4本發(fā)明實施例1-4以及對比例2制備的復合材料的彎曲性能對比圖。圖5本發(fā)明實施例1-4以及對比例2制備的復合材料的沖擊強度對比圖。圖6本發(fā)明實施例2以及對比例1-3制備的材料的沖擊強度對比圖。圖7本發(fā)明實施例1-4以及對比例2制備的復合材料的I型應力-裂紋張開位移曲線(a)和裂紋擴展能量曲線(b)。圖8本發(fā)明的實施例1-4以及對比例2制備的復合材料的I型層間剪切強度的對比圖。圖9(a)-(f)本發(fā)明實施例3所制備的EP/HNT/CF復合材料進行I型層間剪切強度測試后,斷面的掃描電鏡圖。圖10實施例1-4以及對比例2中的復合材料的II型層間斷裂韌性對比圖。圖11本發(fā)明實施例1-4和對比例2制備的復合材料的儲能模量對比圖。圖12本發(fā)明實施例1-4和對比例2制備的復合材料的玻璃化轉(zhuǎn)變溫度對比圖。本發(fā)明的有益效果1.本發(fā)明的制備方法所制備的一種EP/CF/HNT復合材料的復合材料具有優(yōu)異的力學性能:加入HNT的復合材料的彎曲模量和彎曲強度都有提高;當HNT含量為2%時,復合材料的沖擊強度最好,約為39KJ/m2,比不含HNT的EP/CF復合材料提高了25%。2.本發(fā)明的制備方法所制備的一種EP/CF/HNT復合材料的復合材料具有優(yōu)異的層間斷裂韌性及層間剪切強度:I型層間斷裂韌性在HNT含量為3%時最高;層間剪切強度在HNT含量為2%時最大,比不含HNT的EP/CF復合材料提高了25%;II型層間斷裂韌性在HNT含量為2%是最大,比起不含HNT的EP/CF復合材料提高了37%。3.本發(fā)明的制備方法所制備的一種EP/CF/HNT復合材料的復合材料的熱學性能也有提高:當HNT含量為2%時,儲能模量提高了10%;當HNT含量為3%時,玻璃化轉(zhuǎn)變溫度提高了9%(從176.2℃至192.6℃)。4.本發(fā)明提供的制備方法,易于操作,控制性強,成本較低。具體實施方式對比例1純環(huán)氧樹脂(EP)的制備將100g環(huán)氧樹脂在75℃下加熱,得到均相溶液。之后加入27gMDA,并輕柔攪拌。將混合了固化劑的混合溶液放置到鋁制模具中進行固化,固化過程為:在80℃下預固化2小時,然后在160℃下預固化4小時。整個固化過程中保持0.3MPa的壓強。對比例2環(huán)氧樹脂/碳纖維(EP/CF)復合材料的制備將100g環(huán)氧樹脂在75℃下加熱,得到均相溶液。之后加入27gMDA,并輕柔攪拌。將混合了固化劑的混合溶液手動刷至碳纖維織物上,該碳纖維織物的體積為整個復合材料體積的29%。接著,將碳纖維織物放置到鋁制模具中進行固化,固化過程為:在80℃下預固化2小時,然后在160℃下預固化4小時。整個固化過程中保持0.3MPa的壓強。對比例3環(huán)氧樹脂/埃洛石納米管(EP/HNT)納米復合材料的制備將埃洛石納米管在丙酮中分散,然后在室溫下機械攪拌30分鐘。將該溶液加入100g環(huán)氧樹脂中,然后在75℃下攪拌2小時獲得均勻的溶液。其中,埃洛石納米管的質(zhì)量占埃洛石納米管和環(huán)氧樹脂總質(zhì)量的2%。將獲得的均勻溶液在常溫下靜置2小時,取上層清液。使用抽真空的方法將剩余的丙酮去除,加入27gMDA,輕柔攪拌。將混合了固化劑的混合溶液放置到鋁制模具中進行固化,固化過程為:在80℃下預固化2小時,然后在160℃下預固化4小時。整個固化過程中保持0.3MPa的壓強。實施例1將埃洛石納米管在丙酮中分散,然后在室溫下機械攪拌30分鐘。在75℃溫度,向上述溶液加入100g環(huán)氧樹脂,然后攪拌2小時獲得均勻的溶液。其中,埃洛石納米管的質(zhì)量占埃洛石納米管和環(huán)氧樹脂總質(zhì)量的1%。將獲得的均勻溶液在常溫下靜置2小時,取上層清液。使用抽真空的方法將剩余的丙酮去除,加入27gMDA,輕柔攪拌。將混合了固化劑的混合溶液手動刷至碳纖維織物上,該碳纖維織物的體積為整個復合材料體積的29%。接著,將碳纖維織物放置到鋁制模具中進行固化,固化過程為:在80℃下預固化2小時,然后在160℃下預固化4小時。整個固化過程中保持0.3MPa的壓強。實施例2將埃洛石納米管在丙酮中分散,然后在室溫下機械攪拌30分鐘。在75℃溫度下,向上述溶液加入100g環(huán)氧樹脂,然后攪拌2小時獲得均勻的溶液。其中,埃洛石納米管的質(zhì)量占埃洛石納米管和環(huán)氧樹脂總質(zhì)量的2%。將獲得的均勻溶液在常溫下靜置2小時,取上層清液。使用抽真空的方法將剩余的丙酮去除,加入27gMDA,輕柔攪拌。將混合了固化劑的混合溶液手動刷至碳纖維織物上,該碳纖維織物的體積為整個復合材料體積的29%。接著,將碳纖維織物放置到鋁制模具中進行固化,固化過程為:在80℃下預固化2小時,然后在160℃下預固化4小時。整個固化過程中保持0.3MPa的壓強。實施例3將埃洛石納米管在丙酮中分散,然后在室溫下機械攪拌30分鐘。在75℃溫度下,向上述溶液加入100g環(huán)氧樹脂,然后攪拌2小時獲得均勻的溶液。其中,埃洛石納米管的質(zhì)量占埃洛石納米管和環(huán)氧樹脂總質(zhì)量的3%。將獲得的均勻溶液在常溫下靜置2小時,取上層清液。使用抽真空的方法將剩余的丙酮去除,加入27gMDA,輕柔攪拌。將混合了固化劑的混合溶液手動刷至碳纖維織物上,該碳纖維織物的體積為整個復合材料體積的29%。接著,將碳纖維織物放置到鋁制模具中進行固化,固化過程為:在80℃下預固化2小時,然后在160℃下預固化4小時。整個固化過程中保持0.3MPa的壓強。對獲得的復合材料進行掃描電鏡測試,得到如圖1所示的掃描電鏡圖(SEM)。可看見圖中,HNT在環(huán)氧樹脂基質(zhì)中并未完全均勻分散,一些HNT隨機分散在基質(zhì)中,具有較長管間距離,而其他具有較短的管間距離的HNT就形成了HNT富集區(qū)域。實施例4將埃洛石納米管在丙酮中分散,然后在室溫下機械攪拌30分鐘。在75℃溫度下,向上述溶液加入100g環(huán)氧樹脂,然后攪拌2小時獲得均勻的溶液。其中,埃洛石納米管的質(zhì)量占埃洛石納米管和環(huán)氧樹脂總質(zhì)量的5%。將獲得的均勻溶液在常溫下靜置2小時,取上層清液。使用抽真空的方法將剩余的丙酮去除,加入27gMDA,輕柔攪拌。將混合了固化劑的混合溶液手動刷至碳纖維織物上,該碳纖維織物的體積為整個復合材料體積的29%。接著,將碳纖維織物放置到鋁制模具中進行固化,固化過程為:在80℃下預固化2小時,然后在160℃下預固化4小時。整個固化過程中保持0.3MPa的壓強。實施例5將埃洛石納米管在丙酮中分散,然后在室溫下機械攪拌30分鐘。在75℃溫度下,向上述溶液加入100g環(huán)氧樹脂,然后攪拌2小時獲得均勻的溶液。其中,埃洛石納米管的質(zhì)量占埃洛石納米管和環(huán)氧樹脂總質(zhì)量的2.3%。將獲得的均勻溶液在常溫下靜置2小時,取上層清液。使用抽真空的方法將剩余的丙酮去除,加入27gMDA,輕柔攪拌。將混合了固化劑的混合溶液手動刷至碳纖維織物上,該碳纖維織物的體積為整個復合材料體積的29%。接著,將碳纖維織物放置到鋁制模具中進行固化,固化過程為:在80℃下預固化2小時,然后在160℃下預固化4小時。整個固化過程中保持0.3MPa的壓強。對獲得的復合材料進行掃描電鏡測試,得到如圖2所示的掃描電鏡圖。如圖2所示,圖中圈出的區(qū)域為損壞區(qū)域,相當于“海-島結(jié)構(gòu)”中的“島”,當裂紋產(chǎn)生時,該島結(jié)構(gòu)可有效的阻止裂紋的進一步生成,有利于提高復合材料的韌性。對獲得的復合材料進行透射電鏡測試,得到如圖3所示的透射電鏡圖(TEM)。在圖3中可以更清楚地看出,HNT富集區(qū)域并不是HNT的團聚體,其周圍空間實際上填充有環(huán)氧樹脂,不是HNT的簡單團聚體。圖3(a)展示了環(huán)氧樹脂富集區(qū)域,圖3(b)展示了HNT富集區(qū)域。HNT富集區(qū)域,相當于“海-島結(jié)構(gòu)”中的島,可視為具有高含量HNT的剛性復合粒子,其在環(huán)氧樹脂增韌中發(fā)揮著重要的作用。實施例6將埃洛石納米管在丙酮中分散,然后在室溫下機械攪拌30分鐘。在75℃溫度下,向上述溶液加入100g環(huán)氧樹脂,然后攪拌2小時獲得均勻的溶液。其中,埃洛石納米管的質(zhì)量占埃洛石納米管和環(huán)氧樹脂總質(zhì)量的20%。將獲得的均勻溶液在常溫下靜置12小時,取上層清液。使用抽真空的方法將剩余的丙酮去除,加入27gMDA,輕柔攪拌。將混合了固化劑的混合溶液手動刷至碳纖維織物上,該碳纖維織物的體積為整個復合材料體積的10%。接著,將碳纖維織物放置到鋁制模具中進行固化,固化過程為:在80℃下預固化2小時,然后在160℃下預固化4小時。整個固化過程中保持0.1MPa的壓強。實施例7將埃洛石納米管在丙酮中分散,然后在室溫下機械攪拌30分鐘。在75℃溫度下,向上述溶液加入100g環(huán)氧樹脂,攪拌2小時獲得均勻的溶液。其中,埃洛石納米管的質(zhì)量占埃洛石納米管和環(huán)氧樹脂總質(zhì)量的10%。將獲得的均勻溶液在常溫下靜置6小時,取上層清液。使用抽真空的方法將剩余的丙酮去除,加入27gMDA,輕柔攪拌。將混合了固化劑的混合溶液手動刷至碳纖維織物上,該碳纖維織物的體積為整個復合材料體積的30%。接著,將碳纖維織物放置到鋁制模具中進行固化,固化過程為:在80℃下預固化2小時,然后在160℃下預固化4小時。整個固化過程中保持10MPa的壓強。實施例8將埃洛石納米管在丙酮中分散,然后在室溫下機械攪拌30分鐘。在60℃溫度下,向上述溶液加入100g環(huán)氧樹脂,攪拌2小時獲得均勻的溶液。其中,埃洛石納米管的質(zhì)量占埃洛石納米管和環(huán)氧樹脂總質(zhì)量的15%。將獲得的均勻溶液進行離心處理,離心轉(zhuǎn)速為8000轉(zhuǎn)/分鐘,處理5分鐘后,取上層清液。使用抽真空的方法將剩余的丙酮去除,加入27gMDA,輕柔攪拌。將混合了固化劑的混合溶液手動刷至碳纖維織物上,該碳纖維織物的體積為整個復合材料體積的20%。接著,將碳纖維織物放置到鋁制模具中進行固化,固化過程為:在80℃下預固化2小時,然后在160℃下預固化4小時。整個固化過程中保持0.3MPa的壓強。實施例9將埃洛石納米管在丙酮中分散,然后在室溫下機械攪拌30分鐘。在75℃溫度下,向上述溶液加入100g環(huán)氧樹脂,攪拌2小時獲得均勻的溶液。其中,埃洛石納米管的質(zhì)量占埃洛石納米管和環(huán)氧樹脂總質(zhì)量的8%。將獲得的均勻溶液進行離心處理,離心轉(zhuǎn)速為1000轉(zhuǎn)/分鐘,處理15分鐘后,取上層清液。使用抽真空的方法將剩余的丙酮去除,加入27gMDA,輕柔攪拌。將混合了固化劑的混合溶液手動刷至碳纖維織物上,該碳纖維織物的體積為整個復合材料體積的29%。接著,將碳纖維織物放置到鋁制模具中進行固化,固化過程為:在80℃下預固化2小時,然后在160℃下預固化4小時。整個固化過程中保持0.3MPa的壓強。實施例10參考測試標準ASTMD790,對實施例1-4獲得的復合材料,以及對比例2的納米復合材料進行彎曲測試。圖4列舉了各個實施例分別的彎曲模量和彎曲強度。如圖4所示,相對于不含埃洛石納米管的EP/CF復合材料,添加了HNT的EP/HNT/CF復合材料(HNT的含量為1%、2%、3%和5%)的彎曲模量和彎曲強度都有增長,說明HNT的加入提高了復合材料的彎曲性能。實施例11參考ASTMD256標準,對實施例1-4獲得的復合材料,以及對比例2的納米復合材料進行沖擊強度測試。圖5列舉了各個實施例復合材料的沖擊強度。由圖5可以看出,埃洛石納米管的添加提高了復合材料的沖擊強度。當添加的HNT質(zhì)量分數(shù)為2%時,復合材料的沖擊強度最大,約為39KJ/m2,與不含HNT的純EP/CF復合材料相比,沖擊強度增長了約25%。通常情況下,纖維增強的復合材料的沖擊斷裂強度由與沖擊載荷方向相垂直的纖維決定,沖擊能量主要通過纖維拔出/架橋和纖維斷裂來消散。而本實施例中所提到的沖擊強度的提高主要原因是:基體材料斷裂過程中形成的大量被HNT穩(wěn)定的微裂紋,這些微裂紋的形成消耗了大量沖擊能量從而提高了復合材料的沖擊強度。此外,納米管的橋聯(lián)、拔出和斷裂也為沖擊強度的提高做出了一部分貢獻。實施例12參考ASTMD256標準,對實施例2獲得的納米復合材料,以及對比例1-3的材料進行沖擊強度測試。圖6中列舉了各個實施例復合材料的沖擊強度。比較純環(huán)氧樹脂、EP/CF復合材料、EP/HNT納米復合材料以及HNT質(zhì)量分數(shù)為2%的EP/HNT/CF復合材料的沖擊強度,如圖6所示,EP/HNT/CF復合材料的沖擊強度高于純EP、EP/HNT、EP/CF的沖擊強度。此外,可以看出EP/HNT/CF復合材料的沖擊強度比EP/HNT加上EP/CF的沖擊強度還要更高,這說明EP/HNT/CF復合材料的增韌效果并不是HNT和CF增韌效果的簡單疊加,說明HNT和CF的組合存在協(xié)同效應。這種協(xié)同效應的產(chǎn)生正是由于增強碳纖維作為一個剛性的填充物,限制了CF之間的環(huán)氧樹脂的塑性形變,在高速的沖擊應力下,CF之間的環(huán)氧樹脂的脆性更大,更容易產(chǎn)生微裂紋,由于HNT的存在,這些微裂紋會被HNT橋聯(lián)穩(wěn)定而不會形成使得材料整體斷裂的主裂紋。因此,HNT和CF的聯(lián)合使得環(huán)氧樹脂的沖擊強度進一步增加。實施例13I型層間斷裂韌性參考測試標準ASTMD5528,利用雙懸臂梁法(DCB)測定纖維增強復合材料的I型層間斷裂韌性GIc。圖7(a)示出了HNT含量不同的EP/HNT/CF復合材料在DCB測試中獲得典型的載荷-裂紋張開位移(COD)曲線。對于所有的樣品,應力隨著COD的增長呈線性增長,直至裂紋產(chǎn)生的最大載荷點,然后隨著裂紋進一步發(fā)展逐漸降低。I型層間斷裂韌性的引發(fā)值由在載荷達到最大值處的載荷和COD值決定。在加入了HNT之后,復合材料的最大載荷均有所提高,在HNT含量為3%時,復合材料的最大載荷最大。在圖7(b)中圖示了含有不同HNT含量的復合材料的裂紋擴展能量曲線(R曲線)。GIc表示材料產(chǎn)生裂紋所需要的能量,GIc越大,表明產(chǎn)生裂紋所需要的能量就越大,即越不容易產(chǎn)生裂紋。由圖7(b)中可看出,無論I型層間斷裂韌性(GIc)的引發(fā)值和GIc的擴展值,總體都隨著HNT濃度的增加而增大。EP/HNT/CF復合材料的GIc初始值為0.35-0.43KJ/m2,而含有質(zhì)量百分數(shù)為3%和5%的HNTs的復合材料的GIc引發(fā)值是不含HNTs的EP/CF復合材料的GIc引發(fā)值的兩倍。實施例14I型層間剪切強度參考測試標準ASTMD2344,使用短梁剪切法(SBS)表征復合材料的層間剪切強度,在圖8示出了由SBS測試獲得的含有不同HNT含量的EP/HNT/CF復合材料的層間剪切強度(ILSS)??捎^察到,隨著HNT含量的增加,復合材料的ILSS穩(wěn)定增長,其ILSS值為52-63Mpa。含有質(zhì)量分數(shù)為3%的HNTs復合材料的ILSS值為60Mpa,比起不含HNT的EP/CF復合材料大約提高了25%。對實施例3制備的樣條進行SBS測試后的斷裂面進行掃描電鏡分析,獲得圖9,圖9顯示了復合材料樣品在SBS測試后的損壞區(qū)域。在圖9(a)中,裂紋穿過碳纖維進一步發(fā)展,并且由于裂紋偏轉(zhuǎn)而具有分叉,出現(xiàn)了典型的層間剪切失效,隨著應力進一步的增大,CF和環(huán)氧樹脂基質(zhì)之間出現(xiàn)層離。圖9(b)圖示了經(jīng)過富含HNT顆粒的裂紋,其標記為A。在該裂紋生長的過程中,其穿過HNT的富集區(qū)域并轉(zhuǎn)向。圖9(c)為圖9(b)中A區(qū)域的放大圖,發(fā)現(xiàn)HNT富集區(qū)域產(chǎn)生了大量微裂紋,這些微裂紋通過HNT橋聯(lián)被穩(wěn)定。微裂紋的形成和穩(wěn)定將富含HNT的顆粒變成了塑性破損區(qū)域,其能夠吸收大量的能量,并且阻止或減緩裂紋進一步擴展,使得體系韌性更好,更強。在圖9(d)中圖示了環(huán)氧樹脂中生成的數(shù)個微裂紋,但是HNT橋聯(lián)阻止了微裂紋的生長(如圖9(e)所示),或該微裂紋的生長被富含HNT的顆粒阻止了(如圖9(f)所示),所有上述的機理都是導致ILSS增強的原因。實施例15II型層間斷裂韌性采用終端缺口斷裂法(ENF)表征復合材料的II型臨界層間斷裂韌性GIIc,圖10圖示了纖維復合材料II型層間斷裂韌性與埃洛石納米管含量的關系。EP/CF/HNT復合材料的GIIc值為1.6-1.8kJ/m2。當只添加質(zhì)量分數(shù)為1%的HNT,GIIc就增長了24%,當HNT的含量增加到2%時,增長量上升至37%。眾所周知,纖維增強的聚合物復合材料的斷裂韌性主要取決于能量損耗,比如纖維-基質(zhì)脫離,纖維拔出和纖維僑聯(lián),以及基質(zhì)和纖維斷裂的能量損耗。由此可知HNT的加入使環(huán)氧樹脂基材韌性增大,從而GIIc值提高。實施例16熱性能圖11對比了本發(fā)明實施例1-4和對比例制備的復合材料的儲能模量。在室溫以及更高溫度下,含有埃洛石納米管的復合材料的儲能模量比純EP/CF復合材料的儲能模量高。特別是在HNT的質(zhì)量百分數(shù)為2%時,在室溫下儲能模量提高了約10%。圖12顯示了在DMA測試中,HNT的加入對玻璃化轉(zhuǎn)變溫度的影響。測試數(shù)據(jù)表明,復合材料的玻璃化轉(zhuǎn)變溫度(Tg)隨著HNT含量的逐步增加而逐漸提高。這主要是由于聚合物分子的活動性受到HNT的限制。在HNT加入量為3%時,Tg提高了9%(從176.2℃至192.6℃),這時再添加HNT,Tg開始減小,這是由于HNT含量增多引起團聚增多引起的。因此,適量HNT的加入不僅改善了復合材料的力學性能,同時也提高了其熱性能。