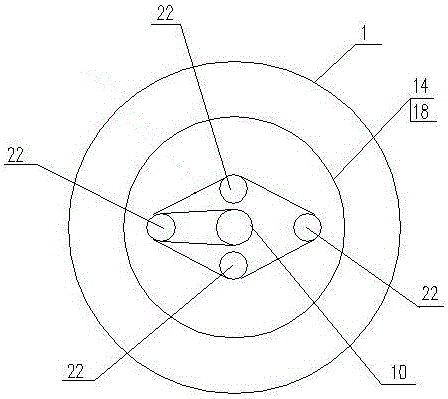
本實用新型涉及一種攪拌裝置,主要用于制藥、食品以及檸檬酸生產,屬于化工設備技術領域,具體說是一種大型發(fā)酵罐攪拌裝置。
背景技術:大型發(fā)酵罐設備是制藥、食品以及檸檬酸等生產企業(yè)發(fā)酵生產工藝所配備的專用裝備,大型發(fā)酵罐是一種立式安裝的圓筒形容器,直徑可達到6米以上,高度至8米左右。發(fā)酵罐的罐體頂端設計有進料口、罐體側壁設計有冷卻管,罐體內部設置有攪拌器,罐體底部設置有過濾空氣進氣口。在發(fā)酵過程中,通過大型泵機將已經過濾的新鮮空氣源源不斷地輸入發(fā)酵罐中,攪拌器持續(xù)不斷地攪拌發(fā)酵液,使發(fā)酵液中的各類物質充分混合,罐體各處的發(fā)酵液溫度與濃度統一;將發(fā)酵罐的罐底部泵機輸入的新鮮空氣分散成小氣泡,增加氣、液接觸面積;強化發(fā)酵液的湍流程度,降低氣泡周圍的液膜厚度和湍流中的流體的阻力,從而提高氧的轉移速率;減少菌絲結團,降低細胞壁周圍的液膜阻力,有利于菌體對氧的吸收,同時,可盡快排除細胞代謝產生的“廢氣”和“廢物”,有利于細胞的代謝活動。因此,攪拌裝置對發(fā)酵生產起著舉足輕重的作用。目前,大型發(fā)酵罐的攪拌裝置是通過安裝在罐體頂部的電機帶動一根自罐底至頂部的攪拌軸,在攪拌軸的不同高度上布置有若干組葉片,屬于單軸攪拌方式。由于大型發(fā)酵罐罐體直徑大,葉片回轉直徑越大,則攪拌范圍越大,對于發(fā)酵工藝有利,但是,由于攪拌阻力與葉片線速度平方成正比,隨著葉片回轉半徑增大,攪拌阻力必然急劇加大,能耗也急劇加大,而且攪拌均勻性也受影響。因此,葉片回轉半徑只能局限在一定范圍內選取,實際上,也就使罐體直徑只能局限在一定范圍內選取,所以,目前看到的傳統罐體形狀大致呈現“瘦高”型。因此,在一定罐體容積的條件下,盡管相對減小罐體直徑,增大罐體高度可以降低攪拌阻力,但是,由于罐體底部壓強與罐體高度呈正比例關系,罐體高度增加則罐體底部壓強增大,最終使要求的罐體底部過濾空氣輸入泵機功率成正比例增加。對于傳統的大型發(fā)酵罐裝備,罐體底部過濾空氣輸入電機功率占發(fā)酵過程電力消耗的60%以上,是發(fā)酵過程電力消耗的最大因素,而攪拌動力約占總電力消耗30%左右。通常,一個直徑6米、高8米的大型發(fā)酵罐設備,過濾空氣泵機與頂部攪拌器電機功率之和達數百千瓦。隨著生化技術的持續(xù)發(fā)展以及對生化產品需求量不斷增加,對發(fā)酵罐的大型化、節(jié)能與高效提出了越來越高的要求,目前,國際上最大標準式發(fā)酵罐容積已達380立方米。但是,迄今為止,對大型攪拌罐節(jié)能降耗研究之側重點,均基于以單軸攪拌為前提條件所開展的對于高效率電機、高效節(jié)能攪拌葉片的研究與開發(fā),但是,都未取得理想的效果。因此,這是長期以來困擾本領域的技術難題,發(fā)酵罐的大型化與節(jié)能這對矛盾至今也未得到很好地解決。如何設計一種大型發(fā)酵罐攪拌裝置,既能使發(fā)酵液能夠得到充分攪拌,提高發(fā)酵質量,又能降低攪拌能耗、降低罐體底部過濾空氣輸入電力消耗,這是目前本領域亟待解決的技術問題。
技術實現要素:本實用新型為現有技術存在的上述問題,提供一種大型發(fā)酵罐攪拌裝置,既能使發(fā)酵液能夠得到充分攪拌,提高發(fā)酵質量,又能降低攪拌能耗、降低罐體底部過濾空氣輸入電力消耗。本實用新型的目的是通過以下技術方案實現的:一種大型發(fā)酵罐攪拌裝置,包括:罐體、罐體內的攪拌裝置及控制系統,其特征在于,所述攪拌裝置中包括中心軸和葉片軸,所述中心軸豎向設置在罐體內的中間,所述中心軸上設置回轉盤,所述中心軸由中心軸動驅動電機驅動并帶動所述回轉盤轉動,所述回轉盤上至少設置兩根所述葉片軸,所述葉片軸上設置攪拌葉片,所述葉片軸由葉片軸驅動電機驅動,使所述葉片軸在隨所述回轉盤公轉的同時也在自轉。對上述技術方案的改進:所述罐體的頂部設置一傳動支架,在傳動支架上設置一電機支架,所述中心軸動驅動電機和葉片軸驅動電機安裝在電機支架上;在傳動支架上正對罐體中心的位置設置一個內部有雙排滾動軸承的中心軸上軸承座,有一轉動軸套安裝在中心軸上軸承座的雙排滾動軸承之間,且轉動軸套的上端伸出中心軸上軸承座的上端,轉動軸套的下端伸入罐體內部一段距離,所述中心軸安裝在轉動軸套的中心,所述中心軸的上端與中心軸動驅動電機的轉軸用聯軸器連接,所述中心軸的下端安裝在中心軸滑動軸承中,所述中心軸滑動軸承設置在所述罐體內底部。對上述技術方案的進一步改進:所述回轉盤包括上回轉盤和下回轉盤,所述中心軸上部設置與其垂直的所述上回轉盤,所述上回轉盤位于所述轉動軸套下方,所述中心軸的下部設置與其垂直的所述下回轉盤,所述葉片軸設置在所述上回轉盤與下回轉盤之間,各所述葉片軸與所述中心軸等距且均勻布置,各所述葉片軸用葉片軸軸承座安裝在所述上回轉盤上,各所述葉片軸與下回轉盤之間用滑動軸承連接。對上述技術方案的進一步改進:所述葉片軸的上端均設置有葉片軸齒形帶輪,所述轉動軸套的上端安裝一轉動軸套上齒形帶輪,轉動軸套的下端安裝一轉動軸套下齒形帶輪,葉片軸驅動電機的轉軸上設置一葉片軸驅動電機齒形帶輪,葉片軸驅動電機齒形帶輪與轉動軸套上齒形帶輪之間用齒形帶連接,轉動軸套下齒形帶輪與葉片軸上的各個齒形帶輪之間用齒形帶連接。對上述技術方案的進一步改進:在上回轉盤與罐體的頂部之間設置一回轉盤封閉蓋,所述回轉盤封閉蓋固定在中心軸上,將上回轉盤、葉片軸軸承座、葉片軸齒形帶輪及轉動軸套下齒形帶輪封閉在其中。對上述技術方案的進一步改進:所述葉片軸上的攪拌葉片分別為上位葉片組、中位葉片組和下位葉片組,所述上位葉片組和下位葉片組中的葉片均采用高效軸流式攪拌葉片,所述上位葉片組與下位葉片組布置方向相反,所述中位葉片組設置在所述上位葉片組與下位葉片組之間,所述中位葉片組葉片為凹葉徑流式攪拌葉片。對上述技術方案的進一步改進:所述中心軸動驅動電機和葉片軸驅動電機均為三相異步電機,所述控制系統中包括控制中心軸動驅動電機和葉片軸驅動電機轉速、轉向的可編程控制器和變頻器。本實用新型與現有技術相比有如下優(yōu)點和積極效果:本實用新型罐體內攪拌裝置中包括一根中心軸和若干葉片軸,中心軸上設置回轉盤,中心軸由中心軸動驅動電機驅動并帶動回轉盤轉動,回轉盤上至少設置兩個所述葉片軸,葉片軸上設置攪拌葉片并由葉片軸驅動電機驅動,使所述葉片軸在隨回轉盤公轉的同時也在自轉。通過公轉與自轉相結合完成攪拌功能,也就是以多點局部攪拌達到整體攪拌的目的。攪拌葉片從罐體徑向和罐體高度方向上都能均勻分布,既能使發(fā)酵液能夠得到充分攪拌,提高發(fā)酵質量,又能降低攪拌能耗。本實用新型罐體的設計直徑范圍較為寬泛,在一定罐體的容積條件下,可相對加大罐體的直徑,降低罐體的高度,成比例降低罐體內部發(fā)酵液對于罐體部的壓強,大幅度降低罐體底部過濾空氣輸入泵機電力消耗。本實用新型在使用時,通過控制葉片軸自轉與公轉,通過由可編程控制器、變頻器等組成的控制系統實現對兩個電機的聯動、速度控制、葉片軸轉動方向等控制,可以靈活實現葉片軸自轉與公轉之間的多種運動與速度的組合形式,例如高速自轉與低速公轉,順時針公轉與逆時針自轉,順時針公轉與順時針自轉等組合形式。而且,通過各葉片軸調整傳動機構,各葉片軸之間的自轉方向可以相同,也可以不同;各葉片軸之間的自轉速度可以相同,也可以不同,以滿足生產工藝與節(jié)能降耗的要求。附圖說明圖1是本實用新型大型發(fā)酵罐攪拌裝置的結構示意圖;圖2是本實用新型大型發(fā)酵罐攪拌裝置的中心軸與葉片軸在罐體內的平面布置示意圖。圖中標號為:1-罐體、2-傳動支架、2.1-電機支架、3-回轉盤封閉蓋、4-葉片軸驅動電機、5-葉片軸驅動電機齒形帶輪、6-轉動軸套上齒形帶輪、7-中心軸驅動電機、8-中心軸上軸承座、9-中心軸、10-轉動軸套、11-轉動軸套下齒形帶輪、12-葉片軸齒形帶輪、13-葉片軸軸承座、14-上回轉盤、15-上位葉片組、16-中位葉片組、17-下位葉片組、18-下回轉盤、19-布氣盤支架、20-閥門、21-布氣盤、22-葉片軸。具體實施方式以下結合附圖對本實用新型作進一步詳細描述:參見圖1、圖2,本實用新型一種大型發(fā)酵罐攪拌裝置的實施例,包括:罐體1及罐體1內的攪拌裝置,攪拌裝置中包括中心軸9和葉片軸22,所述中心軸9豎向設置在罐體1內的中間(本實施例的中心軸9設置在罐體1的中心線上),在中心軸9上設置回轉盤,中心軸9由中心軸動驅動電機7驅動并帶動回轉盤轉動,在回轉盤上至少設置兩根葉片軸22(本實施例為4根葉片軸22),在葉片軸22上設置攪拌葉片,葉片軸22由葉片軸驅動電機4驅動,使葉片軸22在隨所述回轉盤公轉的同時也在自轉。具體而言:在罐體1的頂部設置一傳動支架2,在傳動支架2上設置一電機支架2.1,所述中心軸動驅動電機7和葉片軸驅動電機4安裝在電機支架2.1上;在傳動支架2上正對罐體1中心的位置設置一個內部有雙排滾動軸承的中心軸上軸承座8,有一轉動軸套10安裝在中心軸上軸承座8的雙排滾動軸承之間,且轉動軸套10的上端伸出中心軸上軸承座8的上端,轉動軸套10的下端伸入罐體1內部一段距離,所述中心軸9安裝在轉動軸套10的中心,所述中心軸9的上端與中心軸動驅動電機7的轉軸用聯軸器連接,中心軸9的下端安裝在中心軸滑動軸承中,中心軸滑動軸承設置在罐體1內底部。上述回轉盤包括上回轉盤14和下回轉盤18,在中心軸9上部設置與其垂直的上回轉盤14,上回轉盤14位于所述轉動軸套10下方,所述中心軸9的下部設置與其垂直的所述下回轉盤18,所述葉片軸22設置在所述上回轉盤14與下回轉盤18之間,各所述葉片軸22與所述中心軸9等距且均勻布置,各所述葉片軸22用葉片軸軸承座13安裝在所述上回轉盤14上,各所述葉片軸22與下回轉盤18之間用滑動軸承連接。上述葉片軸22的上端均設置有葉片軸齒形帶輪12,所述轉動軸套10的上端安裝一轉動軸套上齒形帶輪6,轉動軸套10的下端安裝一轉動軸套下齒形帶輪11,葉片軸驅動電機4的轉軸上設置一葉片軸驅動電機齒形帶輪5,葉片軸驅動電機齒形帶輪5與轉動軸套上齒形帶輪6之間用齒形帶連接,轉動軸套下齒形帶輪11與葉片軸22上的各個齒形帶輪12之間用齒形帶連接。在葉片軸22上的攪拌葉片分別為上位葉片組15、中位葉片組16和下位葉片組17,上述上位葉片組15和下位葉片組17中的葉片均采用高效軸流式攪拌葉片,上述上位葉片組15與下位葉片組17布置方向相反,轉動時可以形成發(fā)酵液上下對流。中位葉片組16設置在上位葉片組15與下位葉片組17之間,中位葉片組16葉片為凹葉徑流式攪拌葉片。在葉片軸22轉動時,上位葉片組15讓液體向下流動,下位葉片組17讓液體向上流動,形成對著沖擊,中位葉片組16轉動時將液體向四周擴沖。在上回轉盤14與罐體1的頂部之間設置一回轉盤封閉蓋3,所述回轉盤封閉蓋3固定在中心軸9上,將上回轉盤14、葉片軸軸承座13、葉片軸齒形帶輪12及轉動軸套下齒形帶輪11封閉在其中。在上述罐體1內底部設置布氣盤21,在布氣盤21上設置布氣盤支架19,在布氣盤支架19中心設置上述的中心軸滑動軸承。在發(fā)酵罐的罐體1頂端設計有進料口、罐體1側壁設計有冷卻管,罐體1底部設置有過濾空氣進氣口,在過濾空氣進氣口上安裝閥門20,在罐體1底部安裝過濾空氣輸入泵機,通過過濾空氣進氣口向罐體1輸送過濾空氣,由閥門20控制過濾空氣的開關。上述中心軸動驅動電機7和葉片軸驅動電機4均為三相異步電機,所述控制系統中包括控制中心軸動驅動電機7和葉片軸驅動電機4轉速、轉向的可編程控制器和變頻器。工作時,由于中心軸9上軸承座8的內部有雙排滾動軸承,因此,中心軸9和轉動軸套10都是可以轉動的,只是中心軸9由中心軸動驅動電機7驅動,轉動軸套10由葉片軸驅動電機4通過葉片軸驅動電機齒形帶輪5和轉動軸套上齒形帶輪6及齒形帶驅動。中心軸9帶動上回轉盤14和下回轉盤18繞罐體1中心線轉動,此時,各葉片軸22也在繞罐體1中心線公轉,同時,各葉片軸22自身也在轉動,其上的上位葉片組15、中位葉片組16和下位葉片組17繞葉片軸22轉動。這樣,通過上回轉盤14和下回轉盤18公轉與葉片軸22自轉相結合的方式,既有多點局部攪拌,又有整體攪拌,使大型發(fā)酵罐里的發(fā)酵液能夠得到充分攪拌。這種多點局部攪拌方式減小了各攪拌軸的阻力,使攪拌更充分,也降低了攪拌能耗。本實用新型是以多軸攪拌為基礎,即在罐體1內部空間內平行布置多根葉片軸22,多根葉片軸22以公轉加自轉的運動方式,以多點的、位置連續(xù)變動的局部攪拌,最終實現發(fā)酵液整體均勻攪拌。由于采用多根葉片軸22攪拌,攪拌葉片尺寸可取傳統攪拌葉片直徑尺寸的二分之一至三分之一,根據攪拌葉片直徑尺寸與攪拌阻力的關系,在相同的轉速條件下,盡管攪拌葉片數量增加了,但總攪拌能耗可降低20%—30%。由于采用在罐體1內部空間內平行布置多根葉片軸22,以公轉加自轉的運動方式完成攪拌功能,因此,與單軸攪拌方式比較,罐體1設計直徑范圍相對寬泛。在一定罐體1的容積條件下,可相對加大罐體1的直徑,降低罐體1的高度,則成比例降低罐體1內部發(fā)酵液對于罐體1底部的壓強,罐體1外形可呈“矮胖”型,成比例降低了罐體1底部過濾空氣輸入泵機電力消耗。以目前較普遍采用的直徑6米、高8米的大型發(fā)酵罐設備為例,罐體1容積約為226立方米。如果將罐體1直徑適當放大,設計為7.5米,則罐體1高度設計為5米,即可保持罐體1的容積仍然為226立方米,但是,罐體1底部壓強則降低至原來的62.5%,降低了37.5%,也就是罐體1底部過濾空氣輸入泵機電力消耗降低了37.5%。因此,通過優(yōu)化罐體1的直徑與高度尺寸,可得極佳節(jié)能效果,基本解決了發(fā)酵罐的大型化與節(jié)能這對矛盾。本實用新型大型發(fā)酵罐攪拌裝置的使用時,其控制系統通過可編程控制器、變頻器控制所述中心軸動驅動電機7和葉片軸驅動電機4的聯動、轉速以及中心軸9與葉片軸22的轉動方向,實現葉片軸22的自轉與公轉,由各葉片軸22上的葉片對罐體1內的物料進行攪拌,以多點局部攪拌,實現罐體1內的整體攪拌。葉片軸22的自轉方向與公轉方向可以相同,也可以相反;而且,通過調整各葉片軸22的傳動機構,各葉片軸22之間的自轉方向可以相同,也可以相反;各葉片軸22之間的自轉轉速可以相同,也可以不同;以滿足生產工藝與節(jié)能降耗的要求。一般葉片軸22公轉速度低于10轉/分鐘,葉片軸22自轉速度為100-200轉/分鐘。當然,上述說明并非是對本實用新型的限制,本實用新型也并不限于上述舉例,本技術領域的普通技術人員,在本實用新型的實質范圍內,所作出的變化、改型、添加或替換,也應屬于本實用新型的保護范圍。