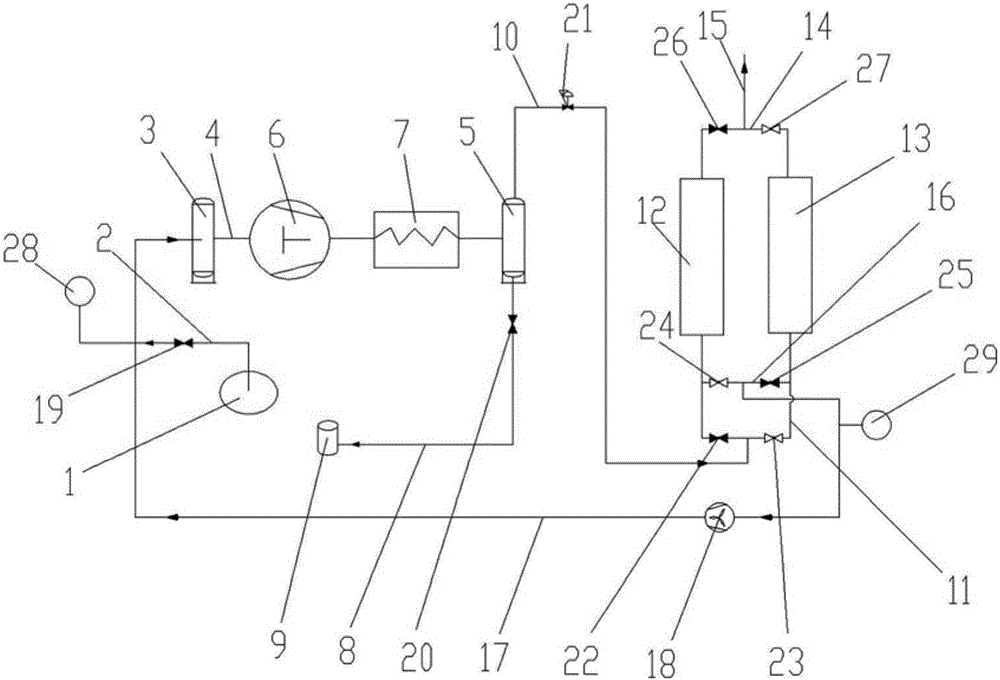
本發(fā)明涉及揮發(fā)性有機(jī)物蒸汽的回收
技術(shù)領(lǐng)域:
,尤其涉及一種油氣中揮發(fā)性有機(jī)物蒸汽的增壓淺冷回收裝置。
背景技術(shù):
:在汽油的供應(yīng)、銷售、貯運(yùn)環(huán)節(jié)中,存在著向大氣中排放高濃度汽油蒸汽的情況,嚴(yán)重地污染了大氣環(huán)境和危害人們的身體健康。以裝車量20萬噸/年的油庫為例,每天轉(zhuǎn)運(yùn)汽油500多噸,操作時間在3小時左右,其產(chǎn)生的汽油蒸汽達(dá)近1000m3,其中所含的汽油將近1噸。為回收這部分汽油蒸汽,常用吸收法、吸附法、冷凝法及膜分離法及其組合工藝方法來回收輕質(zhì)油品蒸發(fā)排放出來的油氣。油氣是汽油與空氣的混合物,組分比較復(fù)雜。儲油罐內(nèi)油氣的濃度根據(jù)汽油的蒸汽壓和氣溫的變化而變化,GB50759-2012《油品裝載系統(tǒng)油氣回收設(shè)施設(shè)計規(guī)范》規(guī)定按30%~45%之間。油氣回收技術(shù)的最關(guān)鍵問題是實(shí)現(xiàn)有機(jī)物組分和空氣分離,油氣回收設(shè)備應(yīng)選用工藝先進(jìn)、成熟可靠、價格合理、適用性強(qiáng)、能耗低、經(jīng)濟(jì)效益好的產(chǎn)品。GB31570-2015石油煉制工業(yè)污染物排放標(biāo)準(zhǔn),油氣收集處理裝置應(yīng)達(dá)到下列指標(biāo):有機(jī)物(非甲烷)排放質(zhì)量濃度≤120mg/m3,處理效率≥95%。吸附-吸收組合工藝油氣回收處理設(shè)備是目前國際國內(nèi)使用較多產(chǎn)品,系統(tǒng)由兩個吸附用活性炭罐、一個吸收高濃度油氣用吸收塔、真空泵及吸收劑循環(huán)送裝置、電氣控制裝置等組成。吸附-吸收組合工藝回收處理工藝流程為:油氣混合物首先通過活性炭罐,其中的有機(jī)物類組份被吸附在活性炭表面,而凈化后的空氣則由活性炭罐頂部的出口排向大氣。兩個活性炭罐按照特定時間在吸附和再生狀態(tài)之間交替切換,再生方式為真空泵真空脫附,從真空泵出來的富油氣進(jìn)入裝有填料的吸收塔。進(jìn)入吸收塔的油氣與自罐區(qū)泵送而來并從吸收塔頂部噴淋而下的常溫貧油逆流接觸,在該過程中油氣被吸收,塔頂含有少量油氣的尾氣返回活性炭罐入口,與新產(chǎn)生的油氣混合后進(jìn)入活性炭罐再次被吸附。吸收了有機(jī)物組份后的富汽油被泵送回汽油儲罐。該產(chǎn)品的技術(shù)缺陷是:1、作為吸收劑的常溫汽油噴淋的過程必將產(chǎn)生一定數(shù)量的蒸發(fā),該部分蒸發(fā)油氣與油庫油氣合流送到活性炭罐進(jìn)口,使吸附負(fù)荷增大,造成活性炭罐龐大,真空泵配置加大。2、設(shè)備一次投資成本大,占地面積大。中國專利CN101306259A“油氣中揮發(fā)性有機(jī)物蒸汽的增壓低溫凝結(jié)回收方法”,采用增壓與深冷的方法進(jìn)行油氣回收。系統(tǒng)主要由氣體壓縮機(jī)、低溫制冷機(jī)、低溫油氣捕集器、控制系統(tǒng)等組成。其工藝流程為先利用氣體壓縮機(jī)對從儲油罐內(nèi)溢出的揮發(fā)性有機(jī)物蒸汽進(jìn)行抽吸增壓至0.85MPa,然后由制冷機(jī)對飽和的蒸汽進(jìn)一步冷卻到-95℃,蒸汽進(jìn)入低溫蒸汽捕集器中被凝結(jié)成液體排至儲油罐回收;未液化的余氣從低溫蒸汽捕集器被排放到大氣。其存在的以下缺點(diǎn):1、該裝置采用開式流程,動態(tài)調(diào)節(jié)性差,當(dāng)裝置初始運(yùn)行以及油氣濃度變化時,制冷系統(tǒng)很難一下就達(dá)到理想的冷凝效果,將使尾氣中有機(jī)物濃度超標(biāo)。2、由于油氣的水分的存在,低溫運(yùn)行系統(tǒng)會出現(xiàn)冰堵。3、深冷工況使設(shè)備選材上造成成本增加。技術(shù)實(shí)現(xiàn)要素:本發(fā)明的目的是為了解決現(xiàn)有技術(shù)中存在的缺點(diǎn),而提出的一種油氣中揮發(fā)性有機(jī)物蒸汽的增壓淺冷回收裝置。為了實(shí)現(xiàn)上述目的,本發(fā)明采用了如下技術(shù)方案:一種油氣中揮發(fā)性有機(jī)物蒸汽的增壓淺冷回收裝置,其特征在于:包括儲油罐,儲油罐通過第一管道連接緩沖罐,緩沖罐通過第二管道連接分離罐,在第二管道上由緩沖罐到分離罐的方向依次連接壓縮機(jī)和制冷機(jī),分離罐的下側(cè)通過第三管道連接收集罐,分離罐的上側(cè)通過第四管道連接第五管道,第五管道的兩端分別連接第一吸附罐和第二吸附罐,第一吸附罐和第二吸附罐之間還連接第六管道,第六管道連接放空管,在第五管道上連接兩端均與其連通的第七管道,第七管道的兩端設(shè)置在第四管道接頭的兩側(cè),第七管道還通過第八管道連接緩沖罐,在第八管道上連接真空泵;在所述第一管道上連接第一閥門,在第三管道上連接第二閥門,在第四管道連接第三閥門,在第四管道接頭與第一吸附罐之間的第五管道上連接第四閥門,在第四管道接頭與第二吸附罐之間的第五管道上連接第五閥門,在第八管道接頭兩側(cè)的第七管道上分別連接第六閥門和第七閥門,在放空管與第一吸附罐之間的第六管道上連接第八閥門,在放空管與第二吸附罐之間的第六管道上連接第九閥門。優(yōu)選地,在所述第一管道上還連接第一壓力傳感器。優(yōu)選地,在所述第八管道連接第二壓力傳感器。優(yōu)選地。所述制冷機(jī)冷卻后的有機(jī)物蒸汽的溫度為0℃-6℃。本發(fā)明的優(yōu)點(diǎn)在于:本方法首先使用壓縮機(jī)對來自油氣回收總管的油氣抽吸增壓,進(jìn)制冷機(jī)冷卻至4℃左右,75%以上的油氣組分冷凝液化,液化后的有機(jī)物蒸汽液體經(jīng)儲氣罐/分離罐底部排出進(jìn)入儲油罐回收,尾氣進(jìn)活性炭吸附罐,尾氣中的汽油組分被吸附,油氣中的空氣則穿透吸附層并攜帶符合環(huán)保標(biāo)準(zhǔn)的余量有機(jī)物被排放至大氣中。活性炭吸附的油氣經(jīng)真空泵解析后再次進(jìn)壓縮機(jī)增壓冷凝后回收。本發(fā)明的回收方法安全可靠,工藝流程合理,制冷系統(tǒng)及吸附罐實(shí)現(xiàn)小型化,整體技術(shù)經(jīng)濟(jì)指標(biāo)優(yōu)良。本發(fā)明采用壓縮后淺冷液化,只有少量有機(jī)蒸汽進(jìn)入吸附罐,可減少昂貴的吸附劑用量,減小設(shè)備尺寸利于小型化的整體橇裝。同時閉式循環(huán)可使處理效率及尾氣排放有機(jī)物含量國際最新排放標(biāo)準(zhǔn),本發(fā)明采用變頻驅(qū)動的壓縮機(jī),可靈活調(diào)節(jié)運(yùn)行負(fù)荷,實(shí)現(xiàn)與油庫作業(yè)同步,適合油庫油氣負(fù)荷不穩(wěn)定的工況特點(diǎn)。附圖說明圖1是本發(fā)明所提供的一種油氣中揮發(fā)性有機(jī)物蒸汽的增壓淺冷回收裝置的結(jié)構(gòu)示意圖;圖2是范德瓦爾斯方程的p-v圖。具體實(shí)施方式為了使本發(fā)明的目的、技術(shù)方案及優(yōu)點(diǎn)更加清楚明白,以下結(jié)合附圖及實(shí)施例,對本發(fā)明進(jìn)行進(jìn)一步詳細(xì)說明。應(yīng)當(dāng)理解,此處所描述的具體實(shí)施例僅僅用以解釋本發(fā)明,并不用于限定本發(fā)明。如圖1所示,本發(fā)明提供的一種油氣中揮發(fā)性有機(jī)物蒸汽的增壓淺冷回收裝置,包括儲油罐1,儲油罐1通過第一管道2連接緩沖罐3,緩沖罐3通過第二管道4連接分離罐5,在第二管道4上由緩沖罐3到分離罐5的方向依次連接壓縮機(jī)6和制冷機(jī)7,制冷機(jī)7冷卻后的有機(jī)物蒸汽的溫度為0℃-6℃,本方案優(yōu)選為2℃、4℃或5℃。分離罐5的下側(cè)通過第三管道8連接收集罐9,分離罐5的上側(cè)通過第四管道10連接第五管道11,第五管道11的兩端分別連接第一吸附罐12和第二吸附罐13,第一吸附罐12和第二吸附罐13之間還連接第六管道14,第六管道14連接放空管15,在第五管道11上連接兩端均與其連通的第七管道16,第七管道16的兩端設(shè)置在第四管道10接頭的兩側(cè),第七管道16還通過第八管道17連接緩沖罐3,在第八管道17上連接真空泵18和第二壓力傳感器29,第二壓力傳感器29連接在真空泵18的進(jìn)氣口。在所述第一管道2上連接第一閥門19和第一壓力傳感器28,在第三管道8上連接第二閥門20,在第四管道10連接第三閥門21,在第四管道10接頭與第一吸附罐12之間的第五管道11上連接第四閥門22,在第四管道10接頭與第二吸附罐13之間的第五管道11上連接第五閥門23,在第八管道17接頭兩側(cè)的第七管道16上分別連接第六閥門24和第七閥門25,在放空管15與第一吸附罐12之間的第六管道14上連接第八閥門26,在放空管15與第二吸附罐13之間的第六管道14上連接第九閥門27。如圖2所示,由范德瓦爾斯方程可知,在臨界條件下真實(shí)氣體的液化有兩條途徑:增加壓力或者降低溫度,以及二者同時進(jìn)行。當(dāng)溫度低于臨界溫度Tc時,隨著壓力的升高,曲線出現(xiàn)轉(zhuǎn)折,Q為開始液化點(diǎn),P-Q為氣液共存段,P為完全液化點(diǎn)。本發(fā)明中油氣的一次液化采用增壓+淺冷,余氣吸附分離后循環(huán)到壓縮機(jī)入口,閉式循環(huán)使目標(biāo)有機(jī)物均液化為汽油得到回收。按本發(fā)明設(shè)計的處理量為300m3/h回收裝置,每小時的汽油回收量可達(dá)305kg,計算參照的油氣組分如下表:組分AIRC3C4C5C6+Mol-Frac0.60.040.120.180.06結(jié)合各混合氣體的物性參數(shù),由計算可知,總流量13.5kmol/h的上述油氣壓縮到4bar冷卻到4℃的溫度時,理論總液化量每小時可達(dá)4.171kmol即291.4kg,未液化的氣體組分含量如下:組分AIRC3C4C5C6+Kmol/h8.0710.3760.5720.2850.024Mol-Frac0.8650.04030.0610.03060.0026液化率達(dá)76.8%,未液化的23.2%進(jìn)吸附系統(tǒng)分離后循環(huán)進(jìn)入增壓淺冷系統(tǒng)二次液化。由此可知,吸附系統(tǒng)尺寸及吸附劑用量只是全吸附時四分之一。同時,由進(jìn)一步程序計算可知,隨吸附系統(tǒng)回流組分的加入,有機(jī)物蒸汽濃度增加,有利于液化率的提升。當(dāng)沒有來自付油平臺油氣時,系統(tǒng)只需對吸附罐解析的純凈有機(jī)蒸汽處理時,此時可達(dá)到100%液化。其工作原理為:在付油平臺向槽罐車的儲油罐1內(nèi)加油時,罐內(nèi)的液面不斷升高,液面上飽和蒸汽壓亦不斷升高。當(dāng)油氣收集管線的第一壓力傳感器28檢測到壓力已達(dá)到設(shè)定的壓力時,第一閥門19自動打開,油氣進(jìn)到緩沖罐3,進(jìn)壓縮機(jī)6增壓到4bar,再進(jìn)入制冷機(jī)7冷卻到4℃左右后進(jìn)入分離罐5,第三閥門21采用自力式壓力控制閥,在第三閥門21的作用下分離罐5壓力穩(wěn)定在4bar,分離罐5為現(xiàn)有技術(shù),當(dāng)分離罐5液化組分達(dá)到液位控制器設(shè)定值時,第二閥門20打開,液態(tài)排放到收集罐9內(nèi)。未液化的氣體通過第三閥門21減壓到常壓,然后通過第四閥門22進(jìn)入第一吸附罐12,有機(jī)物組分被硅膠層和活性炭層吸附,含微量有機(jī)氣體的空氣經(jīng)第八閥門26和放空管15放空。當(dāng)?shù)谝晃焦?2即將達(dá)到穿透時,電控裝置啟動切換程序,第五閥門23和第九閥門27打開,第四閥門22和第八閥門26關(guān)閉,第二吸附罐13開始吸附,同時,第六閥門24打開,第七閥門25關(guān)閉,真空泵18隨即啟動,解吸蒸汽匯集到油氣收集管線,當(dāng)?shù)诙毫鞲衅?9達(dá)到絕對壓力達(dá)到10kPa時,解析過程結(jié)束,第二吸附罐13經(jīng)均壓后等待下次工作切換,由此形成系統(tǒng)的閉式循環(huán)過程。最終使95%以上的有機(jī)物得到液化回收,確保排放尾氣的有機(jī)物含量低于120mg/m3。當(dāng)沒有來自付油平臺油氣時,壓縮機(jī)6根據(jù)解析氣體的氣量大小調(diào)節(jié)電機(jī)工作頻率,維持第一壓力傳感器28壓力穩(wěn)定。當(dāng)前第1頁1 2 3