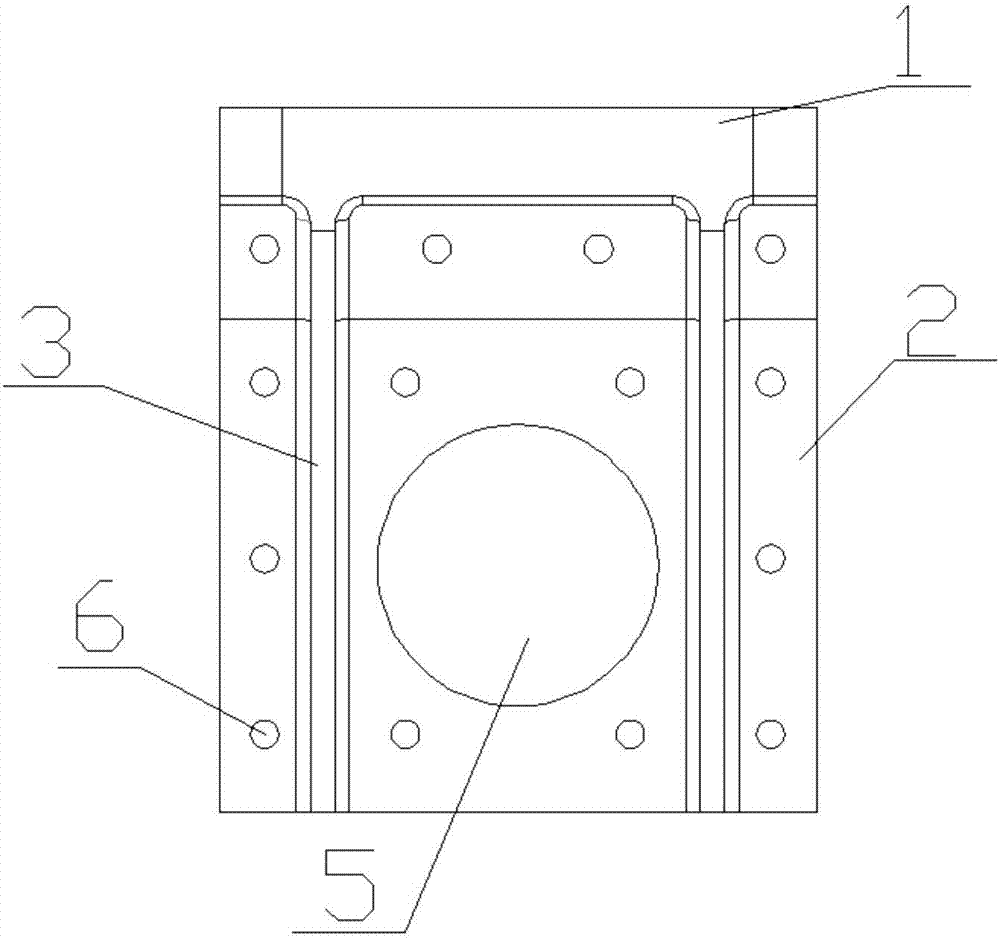
本發(fā)明涉及螺栓盒及其制備方法。
背景技術(shù):
:爆炸螺栓是最早應(yīng)用于航天器的一種火工裝置,其結(jié)構(gòu)主要由螺栓體和螺母組成。爆炸螺栓作為一個連接件,其連接功能的實現(xiàn)與普通螺栓或螺柱的連接方式非常相似,通過擰緊螺母或螺栓體即可將兩個目標連為一體。在螺栓體藥室的外壁上,有一周“v”形槽,在螺栓體的結(jié)構(gòu)上形成一個強度薄弱的環(huán)節(jié)。當(dāng)兩個連接體將要分離時,主裝藥燃燒,藥室內(nèi)的壓力驟然升高,達到一定數(shù)值后,v形槽部位斷裂,在火藥推力的作用下,兩個被連接的物體分離,其承載能力主要通過爆炸螺栓與其對應(yīng)的爆炸螺栓盒完成:次級結(jié)構(gòu)將拉力加載于爆炸螺栓,爆炸螺栓再將拉力載荷通過爆炸螺栓盒傳遞至上級結(jié)構(gòu)中筒殼段的蒙皮上。上述拉力載荷在上述爆炸螺栓盒中的傳遞路徑分為兩條:其中一部分拉力通過爆炸螺栓盒結(jié)構(gòu)整體沿箭體軸向發(fā)生小幅剛體滑移,由螺栓盒底板經(jīng)由背板傳遞至連接螺釘或鉚釘中。此部分拉力使連接螺釘或鉚釘發(fā)生剪切變形,由于結(jié)構(gòu)剛體滑移,因此每個鏈接螺栓所產(chǎn)生的剪切力基本相同。另一部分拉力通過爆炸螺栓盒本身的結(jié)構(gòu)變形,由螺栓盒底板經(jīng)過肋板傳遞至背板上的連接螺釘或鉚釘中。此部分拉力使連接螺釘或鉚釘發(fā)生拉伸變形,而傳統(tǒng)爆炸螺栓盒的肋板設(shè)計使得不同位置的鏈接螺釘或鉚釘?shù)睦ο嗖詈艽螅嚎拷嘲迥┒说穆葆敾蜚T釘拉力遠高于底板附近的螺釘或鉚釘。由于第二條路徑傳遞的拉力占總拉力載荷的大部分,因此傳統(tǒng)爆炸螺栓盒對連接螺釘或鉚釘?shù)睦眯视邢?,往往螺栓盒背板末端螺釘或鉚釘已經(jīng)失效,而底板附近的螺釘或鉚釘尚未塑形變形。如何有效實現(xiàn)爆炸螺栓盒的承受能力,并使其盡可能輕量化,是目前的難題。爆炸螺栓結(jié)構(gòu)簡單,工作可靠,具有較大的能量-質(zhì)量比,同時,具有體積小,操作使用方便的特點。但由于它是通過金屬殼體的斷裂實現(xiàn)連接體的分離,因此,分離時的沖擊非常大,難以實現(xiàn)分離力的準確控制,而且在解鎖分離時還往往有碎片和污染物產(chǎn)生,這對航天器可能產(chǎn)生不利影響。因此,隨著航天技術(shù)的發(fā)展以及對航天器安全性要求的日益提高,爆炸螺栓獨立作為連接與分離裝置在航天器上的應(yīng)用已經(jīng)越來越少。另外,現(xiàn)有爆炸螺栓盒將爆炸產(chǎn)物封閉在盒腔內(nèi),用在需控制污染的場合,具有分離結(jié)構(gòu)簡單、裝配與使用方便等特點。如果爆炸螺栓盒在瞬態(tài)壓力和沖擊作用下發(fā)生破壞,盒內(nèi)或盒體部件飛出,撞擊設(shè)備或儀器,可能影響飛行器的安全。急需一種有效的爆炸螺栓盒解決上述問題。現(xiàn)有爆炸螺栓,多用于多點連接分離面。每個爆炸螺栓形似普通螺栓,內(nèi)部裝有炸藥和點火器。分離時,炸藥被引爆,使剪切鎖剪斷或者沿螺栓削弱槽斷開,實現(xiàn)兩分離體解鎖。爆炸螺栓品種多,主要有開槽式、剪切銷式、鋼球式爆炸螺栓和無污染爆炸螺栓等。這種裝置的優(yōu)點是承載能力大、結(jié)構(gòu)簡單、工作可靠、使用方便。不足之處是往往需要多個螺栓,保證全部螺栓同時斷開困難較大。另外還要保證螺栓斷開時殘骸不傷及周圍的結(jié)構(gòu)和設(shè)備,故必要時應(yīng)相應(yīng)地設(shè)置保護結(jié)構(gòu)。技術(shù)實現(xiàn)要素:本發(fā)明的目的是為了解決現(xiàn)有爆炸螺栓載荷承受力差,強度不高,爆炸威力容易造成污染,難以控制的問題,而提供了一種爆炸螺栓盒及其制備方法。本發(fā)明的一種爆炸螺栓盒,它由頂板、爆炸螺栓盒背板、兩個爆炸螺栓盒斜板構(gòu)成;爆炸螺栓盒背板兩側(cè)安裝有兩個爆炸螺栓盒側(cè)板;爆炸螺栓盒背板和兩個爆炸螺栓盒斜板的頂部設(shè)置有頂板;所述的頂板中心開設(shè)有爆炸螺栓連接孔;所述的爆炸螺栓盒背板中心開設(shè)有減重孔;所述的爆炸螺栓盒背板的豎直部分與彎折部分所形成的角度а為160°,彎折部分與頂板形成的角度β為110°;所述的爆炸螺栓盒背板上開設(shè)有若干個螺釘或鉚釘通孔。本發(fā)明的一種爆炸螺栓盒的制備方法,它是采用爆炸螺栓盒成型模具制備的,具體步驟如下:一、按照制備爆炸螺栓盒所需鋪層角度及預(yù)浸料用量,分別在大分瓣、小分瓣一和小分瓣二的工作面鋪放預(yù)浸料;二、將鋪放好預(yù)浸料的大分瓣、小分瓣一和小分瓣二,分別安放在下板的3個定位槽一內(nèi);三、在步驟一的大分瓣、小分瓣一和小分瓣二工作面鋪放的預(yù)浸料基礎(chǔ)上,按爆炸螺栓盒所需鋪層角度及預(yù)浸料用量,以及厚度要求,繼續(xù)鋪放預(yù)浸料;四、合模a、將左側(cè)板和右側(cè)板下端置于下板的兩側(cè)定位槽二內(nèi),通過設(shè)置在左側(cè)板和右側(cè)板下部的螺釘通孔以及下板兩側(cè)定位槽二內(nèi)的螺絲孔,采用螺栓分別將左側(cè)板和右側(cè)板與下板固定;b、將前側(cè)板和后側(cè)板安放在下板上,使前側(cè)板和后側(cè)板的下表面均貼合下板的上表面;前側(cè)板和后側(cè)板內(nèi)表面均貼合左側(cè)板和右側(cè)板兩側(cè)的端面,并采用螺釘或鉚釘,通過設(shè)置在前側(cè)板和后側(cè)板前后兩端的螺釘或鉚釘通孔固定;c、分別將左側(cè)板和右側(cè)板上端置于上板兩側(cè)的定位槽二內(nèi),通過設(shè)置在左側(cè)板和右側(cè)板上部的螺釘通孔以及上板兩側(cè)定位槽二內(nèi)的螺絲孔,采用螺栓分別將左側(cè)板和右側(cè)板與上板固定;d、通過設(shè)置在上板和下板左右兩端的螺釘或鉚釘通孔,用螺釘或鉚釘將上板和下板(固定;五、將步驟四合模好的成型模具放入固化爐中進行加熱、固化;六、進行脫模;七、對脫模后的試驗件進行機械加工,開設(shè)爆炸螺栓連接孔、減重孔以及螺釘或鉚釘通孔;所述的爆炸螺栓盒成型模具包括下板、大分瓣、小分瓣一、小分瓣二、左側(cè)板、右側(cè)板、前側(cè)板、后側(cè)板和上板;其中,下板上表面開設(shè)有3個定位槽一,上板和下板的兩側(cè)均開設(shè)有定位槽二;大分瓣、小分瓣一、小分瓣二均為長方體結(jié)構(gòu);且大分瓣、小分瓣一及小分瓣二的長度和高度均相同,小分瓣一和小分瓣二的寬度相同;大分瓣的一側(cè)以及小分瓣一與大分瓣相對應(yīng)的一側(cè)均設(shè)置有直角三角形斜臺;所述的直角三角形斜臺的短邊分別位于大分瓣與小分瓣一的后側(cè),且短邊距離大分瓣或小分瓣一的上表面最短距離均為8~10mm;大分瓣、小分瓣一和小分瓣二底部均設(shè)置有形狀與定位槽一相吻合的突起;定位槽二的長度與左側(cè)板、右側(cè)板的長度均相同;左側(cè)板和右側(cè)板內(nèi)側(cè)壁表面上分別設(shè)置有凸臺,凸臺的長度與定位槽二的長度一致,凸臺的寬度與前側(cè)板、后側(cè)板的高度均一致;三個定位槽一中外側(cè)的兩個定位槽一分別距下板邊緣的距離與凸臺寬度相同;每個定位槽一之間距離為定位槽一寬度1.5倍;所述的大分瓣、小分瓣一與小分瓣二上部前端向下彎折;其中,上部的水平端面與彎折端面所形成的角度а為160°,彎折端面與前部的豎直面形成的角度β為110°;左側(cè)板和右側(cè)板的上部和下部均開設(shè)有多個螺釘通孔,且定位槽二與螺釘通孔相對應(yīng)的位置開設(shè)有螺絲孔,左側(cè)板和右側(cè)板通過螺釘分別固定與定位槽二上;前側(cè)板和后側(cè)板的內(nèi)表面分別貼合于左側(cè)板和右側(cè)板兩側(cè)的端面,且前側(cè)板和后側(cè)板的下表面分別與下板的上表面貼合;前側(cè)板和后側(cè)板的前端和后端均開設(shè)有螺釘或鉚釘通孔;前側(cè)板和后側(cè)板通過螺釘或鉚釘通孔固定連接;上板和下板的左右兩端均開設(shè)有螺釘或鉚釘通孔,并通過螺釘或鉚釘通孔固定連接。本發(fā)明包含以下有益效果:本發(fā)明設(shè)計的爆炸螺栓盒在150000n拉力有限元載荷測試中,本發(fā)明的爆炸螺栓盒具有很好的承載力,在此拉力下,不螺栓孔能夠承載較大應(yīng)力。本發(fā)明采用碳纖維材料制備爆炸螺栓盒,和鋁合金件相比,重量下降了14.5%。本發(fā)明通過設(shè)計爆炸螺栓盒的模具,有效解決了制備爆炸螺栓盒過程中,容易出現(xiàn)制備的爆炸螺栓盒手里不均,制備復(fù)雜的問題。本發(fā)明通過設(shè)置背板的角度及預(yù)浸料用量,以及背板、頂板和斜板的厚度,以及背板和頂板的角度設(shè)置,使得采用碳纖維制備出來的爆炸螺栓盒具有非常高的承載能力。附圖說明圖1為爆炸螺栓盒結(jié)構(gòu)示意圖;圖2為圖1的正視圖;圖3為圖1的俯視圖;圖4為圖1的后視圖;圖5為圖1的仰視圖;圖6為圖1的側(cè)視圖;圖7為爆炸螺栓盒模具結(jié)構(gòu)示意圖;圖8為小分瓣一結(jié)構(gòu)示意圖;圖9和圖10均為在大小分瓣的工作面鋪放預(yù)浸料的結(jié)構(gòu)爆炸螺栓盒模具示意圖;圖11、圖12和圖13均為分瓣定位示意圖;圖14和圖15為鋪放剩余蒙皮部分(黑色部分)示意圖;圖16為安裝左、右側(cè)板后示意圖;圖17為安裝前、后側(cè)板后示意圖;圖18為安裝上板后示意圖;圖19為經(jīng)機械加工后的試驗件(爆炸螺栓盒)照片;圖20為剛性邊界試驗裝置圖,其中,1為試驗件,2為液壓缸(最大20噸),3為拉力傳感器,4為位移傳感器,5為應(yīng)變片測試系統(tǒng);圖21為應(yīng)變測量點圖;圖22為鋁合金試驗件應(yīng)變測試曲線圖;其中,a至h分別對應(yīng)1~8#測量點;圖23為鋁合金試驗件與碳纖維試驗件位移測試曲線圖;其中,a為碳纖維試驗件位移測試曲線,b為為鋁合金試驗件位移測試曲線;圖24為第一次拉伸試驗后試驗件照片(厚板出現(xiàn)開裂);圖25為改進鋪層設(shè)計后的第二次拉伸試驗照片;圖26為剛性邊界條件實驗裝置結(jié)構(gòu)示意圖;其中,1為對接螺栓,2為加裝工裝,3為墊片,4為試驗件,5為固定螺栓,6為固定座椅,f為力,箭頭方向為用力方向;圖27為等剛度邊界條件試驗裝置;其中,1為加裝工裝,2為加載螺栓,3為試驗件,4為固定座椅,f為力,箭頭方向為用力方向;圖28為整體有限元模型圖;圖29為x向最大位移分布圖;圖30為y向最大位移分布圖;圖31為z向最大位移分布圖;圖32為組合最大位移分布圖;圖33為最大應(yīng)力校核值分布圖;圖34為最大應(yīng)力校核值分布圖;圖35為x向應(yīng)力分布圖;圖36為y向應(yīng)力分布圖;圖37為yz向應(yīng)力分布圖;圖38為xz向應(yīng)力分布圖。具體實施方式具體實施方式一:本實施方式的一種爆炸螺栓盒,它由頂板1、爆炸螺栓盒背板2、兩個爆炸螺栓盒斜板3構(gòu)成;爆炸螺栓盒背板2兩側(cè)安裝有兩個爆炸螺栓盒側(cè)板3;爆炸螺栓盒背板2和兩個爆炸螺栓盒斜板3的頂部設(shè)置有頂板1;所述的頂板1中心開設(shè)有爆炸螺栓連接孔4;所述的爆炸螺栓盒背板2中心開設(shè)有減重孔5;所述的爆炸螺栓盒背板2的豎直部分與彎折部分所形成的角度а為160°,彎折部分與頂板1形成的角度β為110°;所述的爆炸螺栓盒背板2上開設(shè)有若干個螺釘或鉚釘通孔6。具體實施方式二:本實施方式與具體實施方式一不同的是:所述的爆炸螺栓盒背板2的厚度為13mm;爆炸螺栓盒斜板3厚度為9mm;頂板1厚度為30mm。其它與具體實施方式一相同。具體實施方式三:本實施方式與具體實施方式一不同的是:爆炸螺栓盒是采用碳纖維或鋁合金制成的。其它與具體實施方式一相同。具體實施方式四:本實施方式的一種爆炸螺栓盒的制備方法,它是采用爆炸螺栓盒成型模具制備的,具體步驟如下:一、按照制備爆炸螺栓盒所需鋪層角度及預(yù)浸料用量,分別在大分瓣7、小分瓣一8和小分瓣二12的工作面鋪放預(yù)浸料;二、將鋪放好預(yù)浸料的大分瓣7、小分瓣一8和小分瓣二12,分別安放在下板2的3個定位槽一9內(nèi);三、在步驟一的大分瓣7、小分瓣一8和小分瓣二12工作面鋪放的預(yù)浸料基礎(chǔ)上,按爆炸螺栓盒所需鋪層角度及預(yù)浸料用量,以及厚度要求,繼續(xù)鋪放預(yù)浸料;四、合模a、將左側(cè)板3和右側(cè)板4下端置于下板2的兩側(cè)定位槽二10內(nèi),通過設(shè)置在左側(cè)板3和右側(cè)板4下部的螺釘通孔13以及下板2兩側(cè)定位槽二10內(nèi)的螺絲孔14,采用螺栓分別將左側(cè)板3和右側(cè)板4與下板2固定;b、將前側(cè)板5和后側(cè)板6安放在下板2上,使前側(cè)板5和后側(cè)板6的下表面均貼合下板2的上表面;前側(cè)板5和后側(cè)板6內(nèi)表面均貼合左側(cè)板3和右側(cè)板4兩側(cè)的端面,并采用螺釘或鉚釘,通過設(shè)置在前側(cè)板5和后側(cè)板6前后兩端的螺釘或鉚釘通孔15固定;c、分別將左側(cè)板3和右側(cè)板4上端置于上板1兩側(cè)的定位槽二10內(nèi),通過設(shè)置在左側(cè)板3和右側(cè)板4上部的螺釘通孔13以及上板1兩側(cè)定位槽二10內(nèi)的螺絲孔14,采用螺栓分別將左側(cè)板3和右側(cè)板4與上板1固定;d、通過設(shè)置在上板1和下板2左右兩端的螺釘或鉚釘通孔16,用螺釘或鉚釘將上板1和下板2固定;五、將步驟四合模好的成型模具放入固化爐中進行加熱、固化;六、進行脫模;七、對脫模后的試驗件進行機械加工,開設(shè)爆炸螺栓連接孔、減重孔以及螺釘或鉚釘通孔;所述的爆炸螺栓盒成型模具包括下板2、大分瓣7、小分瓣一8、小分瓣二12、左側(cè)板3、右側(cè)板4、前側(cè)板5、后側(cè)板6和上板1;其中,下板2上表面開設(shè)有3個定位槽一9,上板1和下板2的兩側(cè)均開設(shè)有定位槽二10;大分瓣7、小分瓣一8、小分瓣二12均為長方體結(jié)構(gòu);且大分瓣7、小分瓣一8及小分瓣二12的長度和高度均相同,小分瓣一8和小分瓣二12的寬度相同;大分瓣7的一側(cè)以及小分瓣一8與大分瓣7相對應(yīng)的一側(cè)均設(shè)置有直角三角形斜臺17;所述的直角三角形斜臺17的短邊分別位于大分瓣7與小分瓣一8的后側(cè),且短邊距離大分瓣7或小分瓣一8的上表面最短距離均為8~10mm;大分瓣7、小分瓣一8和小分瓣二12底部均設(shè)置有形狀與定位槽一相吻合的突起13;定位槽二10的長度與左側(cè)板3、右側(cè)板4的長度均相同;左側(cè)板3和右側(cè)板4內(nèi)側(cè)壁表面上分別設(shè)置有凸臺11,凸臺11的長度與定位槽二10的長度一致,凸臺11的寬度與前側(cè)板5、后側(cè)板6的高度均一致;三個定位槽一9中外側(cè)的兩個定位槽一9分別距下板2邊緣的距離與凸臺11寬度相同;每個定位槽一9之間距離為定位槽一9寬度1.5倍;所述的大分瓣7、小分瓣一8與小分瓣二12上部前端向下彎折;其中,上部的水平端面與彎折端面所形成的角度а為160°,彎折端面與前部的豎直面形成的角度β為110°;左側(cè)板3和右側(cè)板4的上部和下部均開設(shè)有多個螺釘通孔13,且定位槽二10與螺釘通孔13相對應(yīng)的位置開設(shè)有螺絲孔14,左側(cè)板3和右側(cè)板4通過螺釘分別固定與定位槽二10上;前側(cè)板5和后側(cè)板6的內(nèi)表面分別貼合于左側(cè)板3和右側(cè)板4兩側(cè)的端面,且前側(cè)板5和后側(cè)板6的下表面分別與下板2的上表面貼合;前側(cè)板5和后側(cè)板6的前端和后端均開設(shè)有螺釘或鉚釘通孔15;前側(cè)板5和后側(cè)板6通過螺釘或鉚釘通孔15固定連接;上板1和下板2的左右兩端均開設(shè)有螺釘或鉚釘通孔16,并通過螺釘或鉚釘通孔16固定連接。具體實施方式五:本實施方式與具體實施方式四不同的是:所述的鋪層角度及預(yù)浸料用量具體指:爆炸螺栓盒背板的角度及預(yù)浸料用量條件如下:90°:45°:-45°=50%:25%:25%;爆炸螺栓盒斜板的角度及預(yù)浸料用量條件如下:90°:45°:-45°=50%:25%:25%;爆炸螺栓盒頂板的角度及預(yù)浸料用量條件如下:0°:90°:45°:-45°=25%:25%:25%:25%。其它與具體實施方式四相同。具體實施方式六:本實施方式與具體實施方式四不同的是:所述的鋪層角度及預(yù)浸料用量具體指:爆炸螺栓盒背板的角度及預(yù)浸料用量條件如下:90°:45°:-45°=50%:25%:25%;爆炸螺栓盒斜板的角度及預(yù)浸料用量條件如下:90°:45°:-45°=80%:10%:10%;爆炸螺栓盒頂板的角度及預(yù)浸料用量條件如下:0°:90°:45°:-45°=25%:25%:25%:25%。其它與具體實施方式四相同。具體實施方式七:本實施方式與具體實施方式四不同的是:所述的厚度指復(fù)合材料爆炸螺栓盒的背板、斜板和頂板的厚度,分別為13mm、9mm和30mm。其它與具體實施方式四相同。具體實施方式八:本實施方式與具體實施方式四不同的是:所述的預(yù)浸料為碳纖維預(yù)浸料或鋁合金預(yù)浸料。其它與具體實施方式四相同。具體實施方式九:本實施方式與具體實施方式四不同的是:在開始鋪放預(yù)浸料前,在大分瓣7、小分瓣一8和小分瓣二12的工作面,以及直角三角形斜臺17表面涂覆脫模劑。其它與具體實施方式四相同。本
發(fā)明內(nèi)容不僅限于上述各實施方式的內(nèi)容,其中一個或幾個具體實施方式的組合同樣也可以實現(xiàn)發(fā)明的目的。通過以下實施例驗證本發(fā)明的有益效果:實施例11、爆炸螺栓盒結(jié)構(gòu)本實施例的復(fù)合材料爆炸螺栓盒(見圖1至圖6)高200mm,寬170mm,由頂板1、爆炸螺栓盒背板2、兩個爆炸螺栓盒斜板3構(gòu)成;爆炸螺栓盒背板2兩側(cè)安裝有兩個爆和炸螺栓盒側(cè)板3;爆炸螺栓盒背板2和兩個爆炸螺栓盒斜板3的頂部設(shè)置有頂板1;所述的頂板1中心開設(shè)有爆炸螺栓連接孔4;所述的爆炸螺栓盒背板2中心開設(shè)有減重孔5;所述的爆炸螺栓盒背板2的豎直部分與彎折部分所形成的角度а為160°,彎折部分與頂板1形成的角度β為110°;所述的爆炸螺栓盒背板2上開設(shè)有若干個螺釘或鉚釘通孔6。本實施例的爆炸螺栓盒可以由鋁合金或者碳纖維制備得到。2、爆炸螺栓盒試驗件(以下簡稱試驗件)成型模具設(shè)計根據(jù)爆炸螺栓盒形狀,爆炸螺栓盒試驗件成型模具采用分瓣形式。成型模具整體包括下板2、大分瓣7、小分瓣一8、小分瓣二12、左側(cè)板3、右側(cè)板4、前側(cè)板5、后側(cè)板6和上板1;其中,下板2上表面開設(shè)有3個定位槽一9,上板1和下板2的兩側(cè)均開設(shè)有定位槽二10;成型模具的形式示意圖如圖7和圖8所示。成型模具下板2上表面開設(shè)有3個定位槽一9,用來定位大分瓣7、小分瓣一8和小分瓣二12;上板1和下板2左右兩側(cè)各開一個定位槽二10,用來定位左側(cè)板3、右側(cè)板4與上板1、下板2的位置關(guān)系;在大分瓣7側(cè)邊及小分瓣一8和小分瓣二12單側(cè)邊對斜板3留有1/2的厚度,來保證斜板3的厚度;通過以上定位關(guān)系,可以保證試驗件斜板3的位置、厚度和試驗件左右方向的尺寸。左側(cè)板3、右側(cè)板4與上板1、下板2定位后,正好定位前側(cè)板5和后側(cè)板6,這樣可以保證試驗件前后方向的尺寸;同時,左側(cè)板3和右側(cè)板4的凸臺11厚度與前側(cè)板5和后側(cè)板6的高度是一致的,用來定位試驗件上下方向的尺寸。3、爆炸螺栓盒試驗件鋪層設(shè)計根據(jù)對爆炸螺栓盒各部位的受力情況及有限元分析結(jié)果,優(yōu)化設(shè)計了爆炸螺栓盒背板、頂板和兩條斜板各部分的碳纖維鋪層角度及用量(見表1)。表1爆炸螺栓盒碳纖維鋪層角度及用量表區(qū)域鋪層(°)背板13mm90°:45°:-45°=50%:25%:25%斜板9mm90°:45°:-45°=50%:25%:25%頂板30mm0°:90°:45°:-45°=25%:25%:25%:25%4、試驗件制備一、按照按表1中爆炸螺栓盒所需鋪層角度及預(yù)浸料用量,分別在大分瓣7、小分瓣一8和小分瓣二12的工作面先鋪放一層預(yù)浸料;由于大分瓣7、小分瓣一8和小分瓣二12側(cè)面都有直角三角形斜臺17的結(jié)構(gòu),在三者組合到一起后,在大分瓣7與小分瓣一8、小分瓣二12之間存在空隙,此步驟主要是將預(yù)浸料填充此空隙,制備爆炸螺栓盒的斜板3,而在鋪放預(yù)浸料的時候在大分瓣7、小分瓣一8和小分瓣二12的工作面會鋪設(shè)一層薄薄的預(yù)浸料,但是此預(yù)浸料并不能達到表1中背板和頂板的厚度要求,還需要在步驟三中繼續(xù)鋪設(shè)預(yù)浸料以達到表1中背板和頂板的厚度要求;(如圖9所示)二、將鋪放好預(yù)浸料的大分瓣7、小分瓣一8和小分瓣二12,分別安放在下板2的3個定位槽一9內(nèi);(如圖10所示)三、在上一步講各分瓣安裝到定位槽一9中后,大分瓣7、小分瓣一8和小分瓣二12相互之間就固定,從而填充在三者空隙內(nèi)的預(yù)浸料也就固定,初步完成爆炸螺栓盒的斜板3的制備,接下來在大分瓣7、小分瓣一8和小分瓣二12已經(jīng)鋪設(shè)一層薄薄預(yù)浸料的工作面上,繼續(xù)按照按表1中爆炸螺栓盒所需鋪層角度及預(yù)浸料用量,以及厚度來整體鋪放剩余預(yù)浸料(蒙皮部分),使得鋪設(shè)后的背板和頂板的預(yù)浸料厚度達到表1中要求,而斜板的厚度,由于事先直角三角形斜臺17的厚度已經(jīng)設(shè)定好,因此在填充預(yù)浸料后,制備的斜板厚度也滿足表1的要求;(如圖11所示)四、合模a、將左側(cè)板3和右側(cè)板4按位置關(guān)系,將安裝左側(cè)板3和右側(cè)板4下端置于在下板2的兩側(cè)定位槽二10內(nèi),通過設(shè)置在左側(cè)板3和右側(cè)板4下部的螺釘通孔13以及下板2兩側(cè)定位槽二10內(nèi)的螺絲孔14,采用螺栓分別將左側(cè)板3和右側(cè)板4與下板2固定;(如圖12所示)b、將前側(cè)板5和后側(cè)板6按位置關(guān)系,安放在下板2上,使前側(cè)板5和后側(cè)板6的下表面均貼合下板2的上表面;前側(cè)板5和后側(cè)板6內(nèi)表面均緊貼合左側(cè)板3和右側(cè)板4兩側(cè)的端面,并通過設(shè)置在前側(cè)板5和后側(cè)板6前后兩端的螺釘或鉚釘通孔15固定;(如圖13所示)c、按位置關(guān)系安裝上板1,分別將左側(cè)板3和右側(cè)板4上端置于上板1兩側(cè)的定位槽二10內(nèi),通過設(shè)置在左側(cè)板3和右側(cè)板4上部的螺釘通孔13以及上板1兩側(cè)定位槽二10內(nèi)的螺絲孔14,采用螺栓分別將左側(cè)板3和右側(cè)板4與上板1固定;(如圖14所示)d、通過設(shè)置在上板1和下板2左右兩端的螺釘或鉚釘通孔16,用螺釘或鉚釘將上板1和下板2固定;五、將步驟四合模好的成型模具放入固化爐中進行加熱、固化;六、進行脫模;七、對脫模后的試驗件進行機械加工,開設(shè)爆炸螺栓連接孔、減重孔以及螺釘或鉚釘通孔;(如圖15所示)。首先,對上述制備的爆炸螺栓盒進行有限元模型分析(仿真模擬),通過模擬分析,初步判斷所制備的爆炸螺栓盒性能,及所應(yīng)改進之處。隨后通過拉伸承載試驗進一步驗證,爆炸螺栓盒的性能。5、試驗件有限元模型分析根據(jù)爆炸螺栓盒數(shù)模,對復(fù)合材料爆炸螺栓盒進行剛度和強度的分析。復(fù)合材料爆炸螺栓盒上連接大螺栓加載荷,在14個螺釘或鉚釘通孔6上設(shè)置14個小螺栓約束。5.1、有限元模型建立采用ansys有限元軟件建立模型,單元選用shell99單元模擬復(fù)合材料層合板結(jié)構(gòu)。shell99是個線性層結(jié)構(gòu)殼單元,可以用于分析應(yīng)用多層結(jié)構(gòu)殼模型。復(fù)合材料爆炸螺栓盒,增加鋼板、大螺栓和小螺栓模擬實際受載情況,如圖24,坐標系設(shè)定如下:原點:爆炸螺栓盒背板底邊中心;x軸:平行于爆炸螺栓盒厚板;y軸:平行于爆炸螺栓盒背板;z軸:垂直于爆炸螺栓盒背板。采用shell99層單元模擬實際鋪層(初步設(shè)計為90°:45°:-45°=25%:37.5%:37.5%)情況。受150000n拉力測試。5.2、材料及質(zhì)量特性復(fù)合材料爆炸螺栓盒為碳纖維樹脂復(fù)合材料層合板結(jié)構(gòu),參考復(fù)合材料單向板性能參數(shù),性能參數(shù)見表5。表5t800/tde85性能參數(shù)縱向模量140gpa橫向模量9gpa剪切模量4.8gpa泊松比0.3縱向拉伸強度2100mpa縱向壓縮強度950mpa橫向拉伸強度25mpa橫向壓縮強度190mpa剪切強度50mpa密度1600kg/m35.3、失效準則采用最大的應(yīng)力失效準則,判定單層是否失效。單層的最大應(yīng)力失效準則由下式表示:σ1=xt(壓縮時|σ1|=xc)σ2=y(tǒng)t(壓縮時|σ2|=y(tǒng)c)|τ12|=s此式表明,當(dāng)單層在平面應(yīng)力的任何應(yīng)力狀態(tài)下,單層正軸向的任何一個應(yīng)力分量到達極限應(yīng)力時,單層就失效。5.4、計算結(jié)果5.4.1、位移計算結(jié)果組合最大位移計算結(jié)果為0.8mm。x向最大位移分布計算結(jié)果見圖25,y向最大位移分布計算結(jié)果見圖26,z向最大位移分布計算結(jié)果見圖27,組合最大位移分布計算結(jié)果見圖28??梢?,z向最大位移位于加載大螺栓孔處,y向最大位移和組合最大位移位于厚板上緣處。5.4.2、應(yīng)力準則校核結(jié)果最大應(yīng)力準則校核值為1.8,發(fā)生在螺栓孔附近。最大應(yīng)力準則校核值分布云圖見圖29。最大應(yīng)力準則校核超過1,則可以判定為單層失效。根據(jù)最大應(yīng)力準則校核值分布云圖,可以確定單層失效位置發(fā)生在加載大螺栓孔附近。5.4.3、單層應(yīng)力計算結(jié)果根據(jù)最大應(yīng)力準則校核值分布云圖,確定了單層失效位置發(fā)生在螺栓孔附近,但還需確定是哪個方向單層應(yīng)力失效。根據(jù)單層各個方向應(yīng)力分量計算結(jié)果(見圖30、圖31、圖32、圖33、圖34),可見,加載大螺栓孔附近應(yīng)力較高,螺栓孔周圍90度拉伸應(yīng)力、面內(nèi)剪切應(yīng)力、層間剪切應(yīng)力較高,可能發(fā)生膠層開裂。5.4.4、有限元分析結(jié)論通過對復(fù)合材料爆炸螺栓盒施加150000n拉力時的有限元分析,可知,爆炸螺栓盒具有很好的承載力。6、碳纖維試驗件加載試驗為了研究碳纖維復(fù)合材料在受到較大集中載荷時的剛度特性、破壞模式、承載效率及本發(fā)明爆炸螺栓盒的可行性進行如下測試。6.1、按照表3的配套表準備碳纖維試驗件進行加載的材料。表3試驗工裝生產(chǎn)配套表6.2、試驗加載要求拉伸試驗包括剛性邊界條件和等剛度邊界條件兩類試驗。圖22為剛性邊界條件裝置示意圖,圖23為等剛度邊界條件試驗裝置示意圖。加載要求:試驗中按照下表4進行加載測試。表4加載表測量要求:試驗件粘貼應(yīng)變片,用以測量加載過程中的應(yīng)變;采用位移計測量加載過程中特定點的位移;試驗件在加載過程中采用聲發(fā)射檢測方法對試驗件的損傷過程進行檢測。7、試驗件拉伸性能測試分別對鋁合金試驗件和碳纖維試驗件進行加載試驗,測試試驗件的極限載荷、指定點應(yīng)變和位移、以及破壞模式等。7.1、鋁合金件加載試驗鋁合金試驗件只做剛性邊界拉伸承載試驗,自搭建的試驗裝置如圖16所示。該試驗裝置由液壓缸、拉力傳感器、位移傳感器和應(yīng)變測量系統(tǒng)等部分組成。應(yīng)變測量點如圖17所示,共計20個測量點。鋁合金試驗件的應(yīng)變(1~8#測量點)和位移測試曲線如圖18和圖19所示。由于液壓缸最大做動力為20噸,為了安全起見,本次試驗的最大載荷為18噸。7.2、碳纖維試驗件試驗根據(jù)拉伸試驗要求設(shè)計的試驗件拉伸夾具及拉伸試驗裝置。并對試驗件進行了第一次拉伸試驗(該拉伸試驗的背板、斜板和頂板厚度均小于表2的厚度),試驗件破壞狀態(tài)如圖20所示。第一次試驗后,斜板3和背板2完好如初,破壞位置發(fā)生在頂板1,破壞現(xiàn)象為層間開裂。根據(jù)此種現(xiàn)象,在頂板1相應(yīng)位置增加螺栓,將爆炸螺栓盒的背板、斜板和頂板厚度變成表2的厚度要求,并進行了第二次拉伸試驗。第二次試驗時,破壞載荷提高。破壞現(xiàn)象為在頂板1與斜板3連接處及頂板1發(fā)生開裂(見圖21)。說明第一次試驗后的改進方案起到了明顯效果。因此,在上次試驗改進方案基礎(chǔ)上,繼續(xù)增加在頂板1層間開裂位置增加螺栓。并且,提高斜板3的90°鋪層的比例,從50%提高到80%。爆炸螺栓盒背板2、頂板1和兩條斜板3各部分的碳纖維鋪層角度及用量調(diào)整見表2。表2第二次試驗后爆炸螺栓盒碳纖維鋪層角度及用量表。由此可知,本實施例的爆炸螺栓盒通過調(diào)整鋪設(shè)角度及纖維用量后,能夠達到很好的抗拉伸效果。當(dāng)前第1頁12