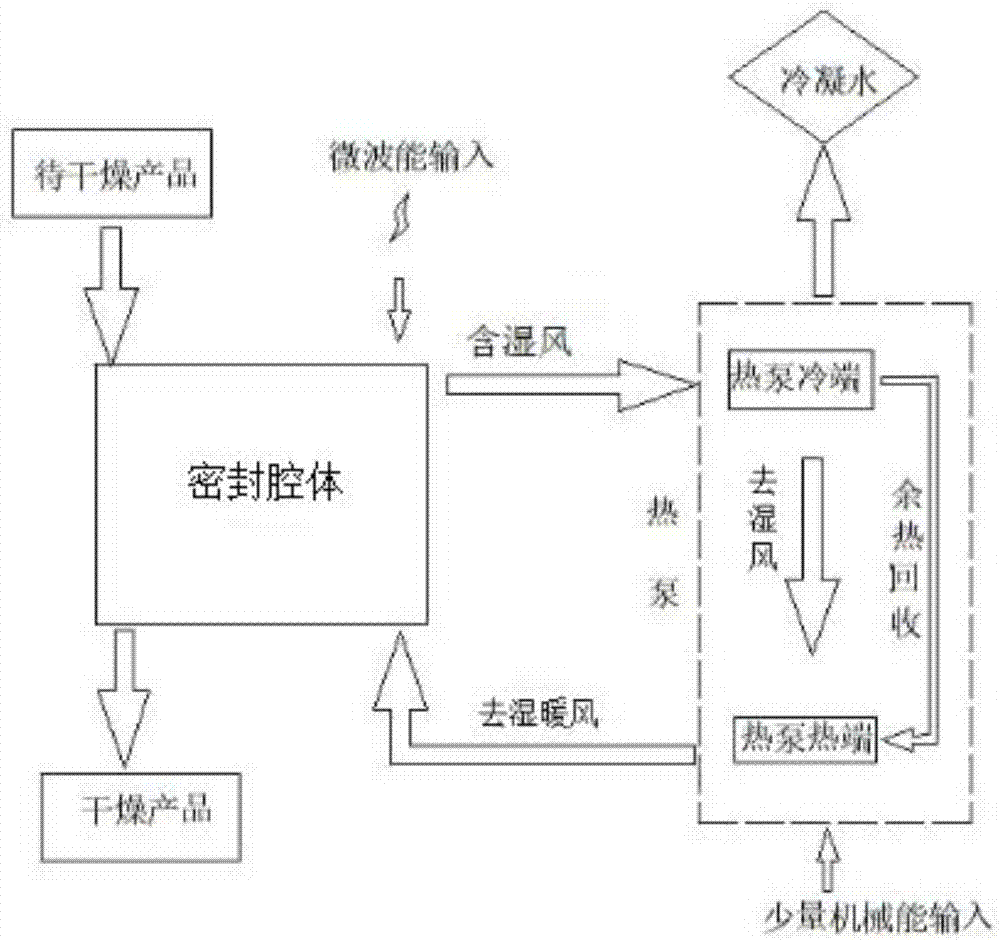
本發(fā)明涉及微波干燥
技術(shù)領(lǐng)域:
,具體涉及一種微波干燥方法及其采用的裝置。
背景技術(shù):
:微波干燥方法充分利用了微波加熱速度快,效率高的優(yōu)點(diǎn),大大縮短了干燥產(chǎn)品所需的時(shí)間,節(jié)能提效效果顯著,微波干燥在社會(huì)生產(chǎn)中得到了充分認(rèn)可。微波干燥是一種內(nèi)部加熱的方法,具體是:濕物料處于振蕩周期極短的微波高頻電場內(nèi),其內(nèi)部的水分子會(huì)發(fā)生極化并沿著微波電場的方向整齊排列,而后迅速隨高頻交變電場方向的交互變化而轉(zhuǎn)動(dòng),并產(chǎn)生劇烈的碰撞和摩擦(每秒鐘可達(dá)上億次),結(jié)果一部分微波能轉(zhuǎn)化為物料中水分子的動(dòng)能,使水的溫度升高直至氣化脫離物料,從而使物料得到干燥。也就是說,微波進(jìn)入物料并被吸收后,其能量在物料電介質(zhì)內(nèi)部直接轉(zhuǎn)換成熱能。現(xiàn)有技術(shù)中采用微波干燥,大概有以下幾種方式:(1)將待干燥產(chǎn)品直接放入微波干燥設(shè)備中進(jìn)行干燥;(2)采用申請?zhí)枮?00920234330.1的實(shí)用新型專利所公開的干燥方法進(jìn)行干燥;(3)用申請?zhí)枮?01410025343.3的發(fā)明專利所公開的干燥方法進(jìn)行干燥。現(xiàn)有技術(shù)中,微波干燥過程中存在以下尚需解決的問題:首先,微波干燥的加熱效率較低。商用微波技術(shù)節(jié)能的關(guān)鍵是因?yàn)槲⒉軐悠愤M(jìn)行從內(nèi)向外的加熱,無需像傳統(tǒng)技術(shù)一樣通過氣體介質(zhì)與待加熱樣品進(jìn)行間接傳熱,加熱干燥同樣產(chǎn)量的樣品,微波加熱技術(shù)可以顯著降低體系的熱負(fù)荷,能量利用率得以顯著提高,實(shí)現(xiàn)節(jié)能?,F(xiàn)有商用微波干燥技術(shù)重視微波對待干燥產(chǎn)品的高效加熱作用,忽視了這些物料被微波加熱時(shí)周邊的低溫氣氛環(huán)境,大量的來自微波的熱能通過對流、輻射、傳導(dǎo)等途徑從物料轉(zhuǎn)移到微波干燥腔體內(nèi)的冷空氣中,導(dǎo)致升溫速度的減慢和微波效率的降低。其次,伴隨現(xiàn)有微波干燥技術(shù)的熱損失過大。隨著干燥過程的進(jìn)行,微波干燥腔體內(nèi)的空氣濕度逐漸增大,溫度也逐漸提高,現(xiàn)有微波干燥工藝采用定時(shí)或濕度高于閥值時(shí)的強(qiáng)行抽氣排濕方法,大量攜帶顯熱和水汽潛熱的濕熱風(fēng)被抽濕排空,損失氣體則外部補(bǔ)充,雖然可以達(dá)到排濕出水的目的,代價(jià)卻是干燥腔內(nèi)熱風(fēng)的大量損失和溫度的大幅降低,損失的熱量的的補(bǔ)償會(huì)直接增大能耗,降低微波干燥工藝的效益。最后,現(xiàn)有商用微波干燥方法未能原有與物料最優(yōu)干燥工藝對接,無法充分發(fā)揮微波干燥快速、高效、的特征,為了滿足物料形狀、形態(tài)、物理化學(xué)性質(zhì)不在微波快速干燥作用下發(fā)生有害變化,只能采取壓制微波加熱貢獻(xiàn),降低微波輸入功率等方案,這些都使微波干燥的效率大打折扣,無法“物盡其用”。綜上所述,急需開發(fā)一種具有干燥效率高、能耗適當(dāng)且干燥產(chǎn)品質(zhì)量好的干燥方法以解決現(xiàn)有技術(shù)的不足。技術(shù)實(shí)現(xiàn)要素:本發(fā)明目的在于提供一種操作方便、干燥效率高、能耗低以及干燥產(chǎn)品質(zhì)量好的微波干燥方法,具體技術(shù)方案如下:一種微波干燥方法,包括以下要素:待干燥產(chǎn)品置于微波干燥設(shè)備中的密閉且隔熱的密封腔體中;微波干燥設(shè)備發(fā)射微波進(jìn)行微波干燥,同時(shí)將密封腔體內(nèi)的氣體進(jìn)行強(qiáng)制對流;監(jiān)控密封腔體內(nèi)的氣體的溫度和待干燥產(chǎn)品的表面溫度,與此同時(shí)不間斷地抽出密封腔體內(nèi)的部分含濕氣體進(jìn)行后處理后返回至密封腔體內(nèi)。以上技術(shù)方案中優(yōu)選的,所述后處理包括以下步驟:步驟a、通過降溫處理將從密封腔體內(nèi)抽出的含濕風(fēng)的溫度降至其露點(diǎn)溫度以下,此時(shí)部分水分結(jié)露成為液態(tài)水而從含濕風(fēng)中脫除,得到去濕風(fēng);步驟b、將去濕風(fēng)進(jìn)行加熱處理,得到去濕暖風(fēng)。以上技術(shù)方案中優(yōu)選的,監(jiān)控腔體內(nèi)氣體溫度以及帶干燥產(chǎn)品表溫度的原則是:微波干燥時(shí)密封腔體內(nèi)的氣體的溫度t1與使用常規(guī)干燥方法的干燥環(huán)境溫度to的關(guān)系為:t1≤to+10℃,此舉可以實(shí)現(xiàn)物料微波干燥工藝與常規(guī)干燥工藝的快速、正確銜接;待干燥產(chǎn)品的表面溫度t2與常規(guī)工藝中等速恒溫階段最高允許的物料的表面溫度tmax的關(guān)系為t2≤tmax+5℃,與微波干燥時(shí)密封腔體內(nèi)的氣體的溫度t1的關(guān)系為t2≤t1+20℃,此舉用于確保微波輸入功率使物料表面溫度自始至終被限定于該框架內(nèi),能夠達(dá)到對物料內(nèi)部水分向外遷徙具有合適的遷徙速度;對含濕風(fēng)進(jìn)行降溫處理時(shí)降溫?fù)Q熱面溫度t3與含濕風(fēng)的露點(diǎn)溫度tl的關(guān)系為tl-10℃≤t3≤tl;去濕暖風(fēng)的溫度t4與含濕風(fēng)的露點(diǎn)溫度tl的關(guān)系為t4≥tl+1℃,此舉則可以控制循環(huán)氣體的溫度、濕度處于有利氣體狀態(tài),維持物料表面水膜合適的蒸發(fā)速度。以上技術(shù)方案中優(yōu)選的,強(qiáng)制對流的方式為采用可控對流的風(fēng)扇進(jìn)行攪拌;氣體進(jìn)行強(qiáng)制對流時(shí)相對于物料的風(fēng)速v的取值為:0.5m/s≤v≤4m/s;所述風(fēng)扇的轉(zhuǎn)速式中:nmax和nmin分別為相對風(fēng)速為4m/s及0.5m/s時(shí)風(fēng)扇的轉(zhuǎn)速,允許最大偏差為20r/min;t1為微波干燥時(shí)密封腔體內(nèi)的氣體的溫度;t2為待干燥產(chǎn)品的表面溫度。以上技術(shù)方案中優(yōu)選的,每小時(shí)從密封腔體內(nèi)抽出并進(jìn)行后處理的氣體的體積為密閉腔體的容積的1/4~2.5倍。以上技術(shù)方案中優(yōu)選的,所述降溫處理為換熱器自然風(fēng)冷、換熱器強(qiáng)制風(fēng)冷、水冷或熱泵冷卻;所述加熱處理為微波加熱、電熱、工業(yè)余熱換熱、地?zé)峒訜帷⑻柲芗訜峄驘岜眉訜?。以上技術(shù)方案中優(yōu)選的,采用熱泵的冷端作為冷源對所述含濕風(fēng)進(jìn)行降溫處理和除濕處理的同時(shí),采用該熱泵的熱端對所述去濕風(fēng)進(jìn)行加熱處理或者是所述熱泵的熱端的熱源還包括熱泵的冷端從大氣、工業(yè)煙氣、天然水體、含地?zé)岬乃w中獲取的熱量;所述微波干燥為連續(xù)式微波干燥或/和間歇式微波干燥,所述微波加熱為連續(xù)式微波加熱或/和間歇式微波加熱。應(yīng)用本發(fā)明的技術(shù)方案,結(jié)合了物料干燥過程的物理化學(xué)規(guī)律,在常規(guī)微波干燥技術(shù)基礎(chǔ)上增加了對于微波干燥設(shè)備中密封腔體內(nèi)氣體介質(zhì)的屬性控制,增加了對于被干燥物料的監(jiān)控,摒除微波干燥過程造成物料干燥過度、變形、燒焦、變性等工藝問題,達(dá)到高效利用微波能進(jìn)行快速微波干燥的目的;同時(shí)通過濕氣循環(huán)再利用、腔體保溫等途徑對微波干燥過程進(jìn)行了節(jié)能強(qiáng)化,具有優(yōu)質(zhì)、高效、節(jié)能的優(yōu)點(diǎn)。詳情如下:1、節(jié)能方面,具體是:本發(fā)明強(qiáng)調(diào)干燥體系的密閉屬性,具體表現(xiàn)在物流和能量流兩個(gè)方面:a、熱損失控制:對干燥方法與設(shè)備中密封腔體及管道的保溫措施最大程度上降低了干燥體系內(nèi)熱量透過金屬材質(zhì)腔壁、管壁的造成散熱損失,該措施一方面抬升了干燥體系內(nèi)的平均溫度,加速干燥過程,另一方面還可以達(dá)到直接節(jié)電5~10%的工藝效果;b、余熱利用:本發(fā)明摒棄了傳統(tǒng)微波干燥工藝中強(qiáng)制抽取濕熱空氣并直接排空的方案,而是持續(xù)將含濕熱氣抽出,然后將這部分氣體經(jīng)過部分冷凝除濕后全部送回體系進(jìn)行循環(huán)利用,由于這些氣體相對于環(huán)境溫度高得多,相比強(qiáng)排抽濕熱風(fēng)后直接用大氣補(bǔ)充體系內(nèi)氣體,可降低能耗20~35%。2、工藝效果好,本發(fā)明深諳微波干燥及干燥過程物理學(xué)之精髓,相比傳統(tǒng)微波干燥方法更加快捷優(yōu)質(zhì),具體是:本發(fā)明結(jié)合了傳統(tǒng)干燥工藝并結(jié)合微波加熱的特點(diǎn),預(yù)熱升溫階段以循環(huán)熱風(fēng)為主、少用或不用微波為加熱手段加熱密封腔體體的高濕物料,避免微波直接加熱導(dǎo)致開裂、變形;恒速干燥段和減速干燥段,通過控制干燥物料表面溫度t2與氣氛溫度t1(微波干燥時(shí)密封腔體內(nèi)的氣體的溫度),可以使水分從物料內(nèi)部向外表面的遷移速度與物料表面的蒸發(fā)速度相匹配,在此基礎(chǔ)上即可以最大可能性提高水分蒸發(fā)速度,提高單位裝機(jī)功率的產(chǎn)率,又可以確保帶干燥物料的結(jié)構(gòu)在微波環(huán)境中免遭破壞,導(dǎo)致變形、干芯、黑芯的生產(chǎn)事故發(fā)生,徹底解決微波干燥產(chǎn)量大但品質(zhì)不佳,或者保證品質(zhì)條件下產(chǎn)量不達(dá)標(biāo)的行業(yè)性問題,因此,本發(fā)明直接對接物料傳統(tǒng)干燥工藝,使用接近于傳統(tǒng)干燥工藝的環(huán)境(氣氛)工藝條件,獨(dú)特氣氛溫度、物料溫度同時(shí)監(jiān)控,確保微波高效干燥同時(shí)避免物料在微波場中溫度過高造成結(jié)構(gòu)破壞,同時(shí)盡可能保證發(fā)揮出微波快速干燥的特性,確保優(yōu)質(zhì)干燥效果。3、兩方面的優(yōu)勢有效提升干燥產(chǎn)能,具體是:a、物料流方面,針對物料蒸發(fā)的原理進(jìn)行蒸發(fā)過程的設(shè)計(jì),本發(fā)明除了沿用微波加速干燥的理念外,強(qiáng)調(diào)干燥過程中的強(qiáng)制通風(fēng),高溫及強(qiáng)制對流通風(fēng)措施大大提升了針對物料表面水膜的蒸發(fā),實(shí)際效果是微波由于穿透效應(yīng)實(shí)現(xiàn)對物料的快速熱能輸入,完成對物料的通體加熱,加速內(nèi)部結(jié)構(gòu)水的析出以及自由水的向外遷徙,兩方面結(jié)合,大大提升了水分脫除效率,提高了單位裝機(jī)功率的產(chǎn)能。b、能量流方面,一方面,物料升溫及水分從物料內(nèi)部向外表面遷移所需的熱量直接從微波能轉(zhuǎn)化,無須通過傳統(tǒng)窯爐的傳導(dǎo)、對流、輻射這些低效率方式供應(yīng)所需的熱量;另一方面,自物料內(nèi)遷徙至物料表面的游離水的汽化蒸發(fā)所需熱量,一方面可以通過微波能轉(zhuǎn)化快速升溫,另一方面在保證物料表面溫度t2比氣氛溫度t1高的前提下,來自物料內(nèi)部由微波能轉(zhuǎn)化來的熱能并通過傳導(dǎo)作用傳遞給物料表面的水膜,第三方面,循環(huán)氣體在物料表面水膜以適當(dāng)速度流過時(shí),可以加速水膜的蒸發(fā),該蒸發(fā)過程由于強(qiáng)吸熱效應(yīng)會(huì)強(qiáng)烈降低水膜的溫度,直至水膜溫度接近或低于氣氛溫度t1,此時(shí)流動(dòng)氣氛也會(huì)通過強(qiáng)制對流給水膜加熱。三方面的配合和三個(gè)溫度的精準(zhǔn)控制可以可控且高效的方式給精準(zhǔn)控制水分的遷移過程和蒸發(fā)過程,做到品質(zhì)與產(chǎn)量兼修。4、可獲得有效水份及有用揮發(fā)分,具體是:本發(fā)明采用冷凝法降低氣氛含水量,冷凝得到的液態(tài)水及可冷凝有用揮發(fā)分可以直接回收利用。該特點(diǎn)對于水資源缺乏地區(qū)的生產(chǎn)極具經(jīng)濟(jì)價(jià)值。如揮發(fā)物中有其他有用可揮發(fā)副產(chǎn)品,經(jīng)濟(jì)效益更佳,如處理竹產(chǎn)品時(shí)可得到竹醋等高附加值副產(chǎn)品,提高經(jīng)濟(jì)效益。5、應(yīng)用面廣,工藝嫁接性佳,具體是:本發(fā)明提供的方法及裝置是常規(guī)干燥方法與常規(guī)微波干燥法的完美結(jié)合,取兩家之長而摒棄其不足,已有實(shí)踐充分顯示其優(yōu)越,既能滿足常見粉狀、顆粒狀、塊狀等對產(chǎn)品外形無要求的物料干燥,又能對陶瓷坯體、藝術(shù)雕刻等對外形尺寸和內(nèi)部結(jié)構(gòu)有嚴(yán)格要求的物件的干燥,既能滿足高水分含量的物料的快速干燥,也能滿足塑膠粒子等對含水量上限ppm級(jí)的嚴(yán)苛應(yīng)用場合,足見其適應(yīng)性之佳。本發(fā)明還公開一種上述干燥方法采用的裝置,具體包括:包括微波干燥設(shè)備、為所述微波干燥設(shè)備提供循環(huán)熱風(fēng)的循環(huán)風(fēng)調(diào)控系統(tǒng)、溫度傳感器組以及輔助循環(huán)裝置;所述微波干燥設(shè)備包括設(shè)有保溫層的密封腔體,所述密封腔體上設(shè)有含濕風(fēng)出口以及去濕暖風(fēng)進(jìn)口;所述循環(huán)調(diào)控系統(tǒng)包括含濕風(fēng)流通管、對含濕風(fēng)進(jìn)行后處理的處理部件以及去濕暖風(fēng)流通管,所述處理部件的入口端通過含濕風(fēng)流通管與含濕風(fēng)出口連通,所述處理部件的出口端通過去濕暖風(fēng)流通管與去濕暖風(fēng)進(jìn)口連通;所述去濕暖風(fēng)流通管上設(shè)有用于將含濕風(fēng)由密封腔體經(jīng)含濕風(fēng)出口抽出并將去濕暖風(fēng)經(jīng)去濕暖風(fēng)進(jìn)口鼓入密封腔體的循環(huán)風(fēng)機(jī);所述溫度傳感器組包括第一溫度傳感器、第二溫度傳感器、第三溫度傳感器以及第四溫度傳感器,所述第一溫度傳感器用于監(jiān)控所述含濕風(fēng)的溫度,所述第二溫度傳感器用于監(jiān)測所述密封腔體內(nèi)的氣體的溫度,所述第三溫度傳感器用于監(jiān)測待干燥產(chǎn)品的表面溫度,所述第四溫度傳感器用于監(jiān)測去濕暖風(fēng)流通管或去濕暖風(fēng)進(jìn)口的溫度;所述輔助循環(huán)裝置設(shè)置在所述密封腔體的內(nèi)部,用于加強(qiáng)密封腔體內(nèi)的氣體進(jìn)行對流,確保所述密封腔體內(nèi)的氣體的溫度和成分均勻性,并增加水分的蒸發(fā)速率。以上技術(shù)方案中優(yōu)選的,所述處理部件包括冷凝器和加熱器,所述冷凝器用于對所述含濕風(fēng)進(jìn)行降溫處理和除濕處理,所述加熱器用于對所述去濕風(fēng)進(jìn)行加熱處理;所述冷凝器的進(jìn)風(fēng)口通過含濕風(fēng)流通管與含濕風(fēng)出口連通,所述冷凝器的出風(fēng)口與所述加熱器的進(jìn)風(fēng)口連通,所述加熱器的出風(fēng)口通過去濕暖風(fēng)流通管與去濕暖風(fēng)進(jìn)口連通;所述冷凝器的降溫?fù)Q熱面處設(shè)有用于監(jiān)控?fù)Q熱面溫度的第五溫度傳感器;所述冷凝器為以空氣為冷源的自然風(fēng)冷凝器、以空氣為冷源的強(qiáng)制風(fēng)冷冷凝器或以循環(huán)水為冷源的冷凝器;或者是,所述處理部件為熱泵,所述熱泵的冷端入口通過含濕風(fēng)流通管與含濕風(fēng)出口連通,所述熱泵的熱端出口通過去濕暖風(fēng)流通管與去濕暖風(fēng)進(jìn)口連通。以上技術(shù)方案中優(yōu)選的,所述輔助循環(huán)裝置包括強(qiáng)制對流風(fēng)扇組;所述第一溫度傳感器、第二溫度傳感器、第四溫度傳感器以及第五溫度傳感器均為接觸式測溫器,所述第三溫度傳感器為紅外線溫度傳感器;所述含濕風(fēng)流通管、去濕暖風(fēng)流通管、冷凝器和加熱器的外壁上均設(shè)有保溫層。應(yīng)用本發(fā)明的裝置,裝置簡單易實(shí)現(xiàn),設(shè)備初期投入低。除了上面所描述的目的、特征和優(yōu)點(diǎn)之外,本發(fā)明還有其它的目的、特征和優(yōu)點(diǎn)。下面將參照圖,對本發(fā)明作進(jìn)一步詳細(xì)的說明。附圖說明構(gòu)成本申請的一部分的附圖用來提供對本發(fā)明的進(jìn)一步理解,本發(fā)明的示意性實(shí)施例及其說明用于解釋本發(fā)明,并不構(gòu)成對本發(fā)明的不當(dāng)限定。在附圖中:圖1是本發(fā)明優(yōu)選實(shí)施例1的裝置示意圖;圖2是采用圖1的裝置的干燥流程示意圖;圖3是本發(fā)明優(yōu)選實(shí)施例2的裝置中的循環(huán)調(diào)控系統(tǒng)的結(jié)構(gòu)示意圖;圖4是采用圖3的裝置的干燥流程示意圖;其中,1、微波干燥設(shè)備,1.1、密封腔體,1.11、含濕風(fēng)出口,1.12、去濕暖風(fēng)進(jìn)口,2、循環(huán)調(diào)控系統(tǒng),2.1、含濕風(fēng)流通管,2.2、處理部件,2.21、冷凝器,2.22、加熱器,2.3、去濕暖風(fēng)流通管,3、溫度傳感器組,3.1、第一溫度傳感器,3.2、第二溫度傳感器,3.3、第三溫度傳感器,3.4、第四溫度傳感器,3.5、第五溫度傳感器,4、輔助循環(huán)裝置,5、待干燥產(chǎn)品,6、干燥產(chǎn)品,7、傳送裝置。具體實(shí)施方式以下結(jié)合附圖對本發(fā)明的實(shí)施例進(jìn)行詳細(xì)說明,但是本發(fā)明可以根據(jù)權(quán)利要求限定和覆蓋的多種不同方式實(shí)施。實(shí)施例1:一種微波干燥方法(以干燥最大尺寸30mm的積木為例,含水21.5%至含水率2%),其采用的裝置詳見圖1,具體包括微波干燥設(shè)備1、為所述微波干燥設(shè)備1提供循環(huán)熱風(fēng)的循環(huán)風(fēng)調(diào)控系統(tǒng)2、溫度傳感器組3以及輔助循環(huán)裝置4,詳情如下:所述微波干燥設(shè)備1包括設(shè)有保溫層的密封腔體1.1,所述密封腔體1.1上設(shè)有含濕風(fēng)出口1.11以及去濕暖風(fēng)進(jìn)口1.12。所述循環(huán)調(diào)控系統(tǒng)2包括含濕風(fēng)流通管2.1、對含濕風(fēng)進(jìn)行后處理的處理部件2.2以及去濕暖風(fēng)流通管2.3,所述處理部件的入口端通過含濕風(fēng)流通管與含濕風(fēng)出口連通,所述處理部件的出口端通過去濕暖風(fēng)流通管與去濕暖風(fēng)進(jìn)口連通,此處上述處理部件采用熱泵,具體連接關(guān)系是:所述熱泵的冷端入口通過含濕風(fēng)流通管2.1與含濕風(fēng)出口1.11連通,所述熱泵的熱端出口通過去濕暖風(fēng)流通管2.3與去濕暖風(fēng)進(jìn)口1.12連通。所述去濕暖風(fēng)流通管上設(shè)有用于將含濕風(fēng)由密封腔體經(jīng)含濕風(fēng)出口抽出并將去濕暖風(fēng)經(jīng)去濕暖風(fēng)進(jìn)口鼓入密封腔體的循環(huán)風(fēng)機(jī)(未圖示)。所述溫度傳感器組3包括第一溫度傳感器3.1、第二溫度傳感器3.2、第三溫度傳感器3.3以及第四溫度傳感器3.4,所述第一溫度傳感器3.1設(shè)置在所述含濕風(fēng)流通管2.1的內(nèi)部,用于監(jiān)測所述含濕風(fēng)流通管2.1的溫度;所述第二溫度傳感器3.2設(shè)置在所述密封腔體1.1的內(nèi)部,用于監(jiān)測所述密封腔體1.1內(nèi)部的溫度;所述第三溫度傳感器3.3設(shè)置在所述密封腔體1.1的內(nèi)壁上,用于監(jiān)測待干燥產(chǎn)品5的表面溫度;所述第四溫度傳感器3.4設(shè)置在所述濕暖風(fēng)流通管2.2的內(nèi)部,用于監(jiān)測去濕暖風(fēng)流通管2.2的溫度。所述輔助循環(huán)裝置4設(shè)置在所述密封腔體的內(nèi)部,其包括多個(gè)強(qiáng)制對流風(fēng)扇,用于加強(qiáng)密封腔體內(nèi)的氣體進(jìn)行對流,確保所述密封腔體內(nèi)的氣體的溫度和成分均勻性,并增加水分的蒸發(fā)速率。第一溫度傳感器、第二溫度傳感器以及第四溫度傳感器均為接觸式測溫器,所述第三溫度傳感器為紅外線溫度傳感器(非接觸式)。所述含濕風(fēng)流通管和去濕暖風(fēng)流通管的外壁上均設(shè)有保溫層。本實(shí)施例的裝置還可以與傳送裝置7聯(lián)合使用。傳送裝置7可采用以下結(jié)構(gòu):包括傳送待干燥產(chǎn)品5和干燥產(chǎn)品6的傳送皮帶、帶動(dòng)所述傳送皮帶進(jìn)行運(yùn)動(dòng)的動(dòng)力源以及支撐所述傳送皮帶的支撐架。本實(shí)施例的微波干燥方法詳見圖2,具體包括以下步驟:將待干燥產(chǎn)品置于微波干燥設(shè)備中的密閉且隔熱的密封腔體中;微波干燥設(shè)備發(fā)射微波進(jìn)行微波干燥,同時(shí)將密封腔體內(nèi)的氣體進(jìn)行強(qiáng)制對流,微波干燥為連續(xù)式微波干燥或/和間歇式微波干燥;監(jiān)控密封腔體內(nèi)的氣體的溫度和待干燥產(chǎn)品的表面溫度,與此同時(shí)不間斷地對密封腔體內(nèi)的部分含濕氣體進(jìn)行后處理后循環(huán)至密封腔體內(nèi)。上述后處理包括以下步驟:步驟a、通過降溫處理將從密封腔體內(nèi)抽出的含濕風(fēng)的溫度降至其露點(diǎn)溫度以下,此時(shí)部分水分結(jié)露成為液態(tài)水而從含濕風(fēng)中脫除,得到去濕風(fēng);步驟b、將去濕風(fēng)進(jìn)行加熱處理,得到去濕暖風(fēng)。監(jiān)控腔體內(nèi)氣體溫度以及帶干燥產(chǎn)品表溫度的原則是:微波干燥時(shí)密封腔體內(nèi)的氣體的溫度t1與使用常規(guī)干燥方法的干燥環(huán)境溫度to的關(guān)系為:t1≤to+10℃,此舉可以實(shí)現(xiàn)物料微波干燥工藝與常規(guī)干燥工藝的快速、正確銜接;待干燥產(chǎn)品的表面溫度t2與常規(guī)工藝中等速恒溫階段最高允許的物料的表面溫度tmax的關(guān)系為t2≤tmax+5℃,與微波干燥時(shí)密封腔體內(nèi)的氣體的溫度t1的關(guān)系為t2≤t1+20℃,此舉用于確保微波輸入功率使物料表面溫度自始至終被限定于該框架內(nèi),能夠達(dá)到對物料內(nèi)部水分向外遷徙具有合適的遷徙速度;對含濕風(fēng)進(jìn)行降溫處理時(shí)降溫?fù)Q熱面溫度t3與含濕風(fēng)的露點(diǎn)溫度tl的關(guān)系為tl-10℃≤t3≤tl;去濕暖風(fēng)的溫度t4與含濕風(fēng)的露點(diǎn)溫度tl的關(guān)系為t4≥tl+1℃,此舉則可以控制循環(huán)氣體的溫度、濕度處于有利氣體狀態(tài),維持物料表面水膜合適的蒸發(fā)速度。強(qiáng)制對流的方式為采用可控對流的風(fēng)扇進(jìn)行攪拌;氣體進(jìn)行強(qiáng)制對流時(shí)相對于物料的風(fēng)速v的取值為:0.5m/s≤v≤4m/s;所述風(fēng)扇的轉(zhuǎn)速式中:nmax和nmin分別為相對風(fēng)速為4m/s及0.5m/s時(shí)風(fēng)扇的轉(zhuǎn)速,允許最大偏差為20r/min;t1為微波干燥時(shí)密封腔體內(nèi)的氣體的溫度;t2為待干燥產(chǎn)品的表面溫度。每小時(shí)從密封腔體內(nèi)抽出并進(jìn)行后處理的氣體的體積為密閉腔體的容積的1/4~2.5倍。采用熱泵的冷端作為冷源對所述含濕風(fēng)進(jìn)行降溫處理和除濕處理的同時(shí),采用該熱泵的熱端對所述去濕風(fēng)進(jìn)行加熱處理(此處,所述熱泵的熱端的熱量還可以包括熱泵的冷端從大氣、工業(yè)煙氣、天然水體、含地?zé)岬乃w中獲取的熱量)。采用本實(shí)施例的干燥方法和裝置所得干燥產(chǎn)品的性能詳見表1。實(shí)施例2:本實(shí)施例的具體方案詳見圖3和圖4,其與實(shí)施例1不同之處在于以下兩個(gè)方面:裝置結(jié)構(gòu)不同,具體是:(1)所述處理部件包括冷凝器2.21和加熱器2.22,所述冷凝器2.21用于對所述含濕風(fēng)進(jìn)行降溫處理和除濕處理,所述加熱器2.22用于對所述去濕風(fēng)進(jìn)行加熱處理(加熱器可以是換熱器、熱泵等可以加熱的部件,采用熱泵時(shí),具體是:熱泵的冷端從大氣、工業(yè)煙氣、天然水體、含地?zé)岬乃w中獲取熱量并傳遞給熱端,所述熱泵的熱端用作加熱器);所述冷凝器的進(jìn)風(fēng)口通過含濕風(fēng)流通管與含濕風(fēng)出口連通,所述冷凝器的出風(fēng)口與所述加熱器的進(jìn)風(fēng)口連通,所述加熱器的出風(fēng)口通過去濕暖風(fēng)流通管與去濕暖風(fēng)進(jìn)口連通;(2)所述冷凝器的降溫?fù)Q熱面處設(shè)有用于監(jiān)控?fù)Q熱面溫度的第五溫度傳感器,所述第五溫度傳感器為接觸式測溫器;(3)所述冷凝器為以循環(huán)水為冷源的冷凝器(還可以根據(jù)實(shí)際情況,采用以空氣為冷源的自然風(fēng)或強(qiáng)制風(fēng)冷冷凝器)。1、工藝略有不同,詳情是:去濕風(fēng)經(jīng)含濕風(fēng)流通管進(jìn)入冷凝器進(jìn)行降溫和去濕,得到去濕風(fēng);去濕風(fēng)進(jìn)入加熱器加熱后經(jīng)去濕暖風(fēng)流通管返回密封腔體內(nèi)(在循環(huán)風(fēng)機(jī)的協(xié)同作用下)。采用本實(shí)施例的干燥方法和裝置所得干燥產(chǎn)品的性能詳見表1。表1實(shí)施例1-2與對比實(shí)施例1-3所得干燥產(chǎn)品的性能比較表(抽樣檢測容量500件)案例/參數(shù)單位微波裝機(jī)功率產(chǎn)能kg/(kw.h)干燥能耗(kwh/kg)良品率%實(shí)施例17.110.56596.5實(shí)施例26.950.78597.4對比實(shí)施例15.162.16~2.4278.4對比實(shí)施例25.561.86~2.0883.3對比實(shí)施例35.741.78~1.9785.2從表1可知:表1中實(shí)施例1和2是本發(fā)明的實(shí)施效果,對比實(shí)施例1是現(xiàn)階段市面流行的微波干燥工藝的實(shí)施效果;對比實(shí)施例2和對比實(shí)施例3都使用抽出部分熱風(fēng)作為循環(huán)風(fēng)使用的方案,區(qū)別是對比實(shí)施例2抽出部分的循環(huán)風(fēng)直接加熱后返回用于干燥,同時(shí)排出部分混合風(fēng)進(jìn)行排濕;對比實(shí)施例3則對循環(huán)風(fēng)進(jìn)行甄別,風(fēng)溫高于某個(gè)閥值后才返回使用,返回使用的那部分熱風(fēng)進(jìn)行除濕處理,否則直接排放掉。微波能屬于二次能源,即將原始能源轉(zhuǎn)化的電能經(jīng)微波元器件轉(zhuǎn)化為微波能用于加熱物品,電能轉(zhuǎn)化為微波的效率約為70%,其余能量轉(zhuǎn)化為微波元件的熱能而耗散。對比實(shí)施例1采用微波加熱聯(lián)合電熱的方式,采用直接甄別含濕熱風(fēng)的相對濕度,濕度超標(biāo)則直接抽取含濕熱風(fēng)的方式排濕而不做任何循環(huán)使用,熱能損失嚴(yán)重。對比實(shí)施例2采用部分循環(huán)風(fēng)直接加熱但并不除濕的方式,降低了循環(huán)風(fēng)的相對濕度,同時(shí)提高了溫度,整體措施比對比實(shí)施例1更有利與提高干燥效率,與此同時(shí),該方案采用不間斷循環(huán)使用部分含濕風(fēng)加熱返回循環(huán)利用的方式,同時(shí)不間斷排放部分含濕風(fēng),有利于微波干燥氣氛參數(shù)的整體平穩(wěn),因此干燥品質(zhì)比對比實(shí)施例1高。對比實(shí)施例3和對比實(shí)施例2類似,因此兩者的能耗指標(biāo)均比對比實(shí)施例1低,干燥質(zhì)量也比后者高。對比實(shí)施例3相對對比實(shí)施例2,主要多了對出風(fēng)風(fēng)溫的甄別,溫度太低的出風(fēng)經(jīng)濟(jì)價(jià)值低,可以直接抽出排放,熱損失相對較??;溫度高于閥值的出風(fēng),除濕之后再返回使用,這樣做可以充分利用返回這部分溫度較高的熱風(fēng),而除濕又有利于降低整體風(fēng)的濕度,提高干燥腔內(nèi)干燥的效率,因此該方案相對對比實(shí)施例2的改進(jìn)效果顯著,其各項(xiàng)指標(biāo)也有所提升。采用本發(fā)明方案的實(shí)施例2和實(shí)施例1在對比實(shí)施例2、3利用循環(huán)風(fēng)這一優(yōu)點(diǎn)的基礎(chǔ)上,進(jìn)一步消化吸收了干燥過程的物理學(xué)本質(zhì),先是對循環(huán)氣體100%循環(huán)利用,循環(huán)風(fēng)返回干燥腔前先是經(jīng)過冷凝方式的除濕處理,除濕程度由于水的液相—?dú)庀嗥胶鈼l件而精確可控,即做到對循環(huán)風(fēng)濕度的精確控制,又容易實(shí)現(xiàn)冷凝過程溫降盡可能小,即熱損失盡可能小,因此這兩個(gè)方案的能耗指標(biāo)相對三個(gè)對比實(shí)施例方案改進(jìn)巨大。另外,本發(fā)明兩個(gè)方案還對待干燥積木物料的表面溫度進(jìn)行精密檢測,防止微波加熱過度造成被干燥樣品損傷,因此以合格品個(gè)數(shù)為基礎(chǔ)的良品率遠(yuǎn)在對比方案以上。實(shí)施例1和實(shí)施例2的主要區(qū)別是后者分別直接采用冷凝器和加熱器配合對循環(huán)氣體進(jìn)行循環(huán)風(fēng)濕度和溫度調(diào)控,前者直接采用熱泵的冷端和熱端充當(dāng)冷凝器和加熱器,這樣做的效果是循環(huán)風(fēng)冷凝時(shí)損失的熱能,包括大部分水蒸氣冷凝釋放的潛熱,均由于熱泵的作用直接轉(zhuǎn)移至熱泵的熱端用于加熱經(jīng)過除濕的低溫干燥風(fēng),再加上來自熱泵自身機(jī)械能轉(zhuǎn)化而來的熱能,不考慮熱泵的能源效率和器壁散熱的熱損失,可以做到循環(huán)風(fēng)除濕—加熱環(huán)節(jié)熱能利用率100%,考慮熱泵熱貢獻(xiàn)的實(shí)際效果,能源利用率甚至可以超過100%,如可以利用熱泵從環(huán)境抓取熱量用于給循環(huán)氣體加熱,因此實(shí)施例1的能耗指標(biāo)較實(shí)施例2更好;經(jīng)過試驗(yàn)證明:實(shí)施例1和實(shí)施例2的良品率相差很小,計(jì)件數(shù)量500件時(shí)僅相差4個(gè),可以認(rèn)為處于相同水平)。對比實(shí)施例1:將待干燥產(chǎn)品直接放入微波干燥設(shè)備中進(jìn)行干燥。對比實(shí)施例2:采用申請?zhí)枮?00920234330.1的實(shí)用新型專利所公開的干燥方法進(jìn)行干燥。對比實(shí)施例3:采用申請?zhí)枮?01410025343.3的發(fā)明專利所公開的干燥方法進(jìn)行干燥。以上所述僅為本發(fā)明的優(yōu)選實(shí)施例而已,并不用于限制本發(fā)明,對于本領(lǐng)域的技術(shù)人員來說,本發(fā)明可以有各種更改和變化。凡在本發(fā)明的精神和原則之內(nèi),所作的任何修改、等同替換、改進(jìn)等,均應(yīng)包含在本發(fā)明的保護(hù)范圍之內(nèi)。當(dāng)前第1頁12