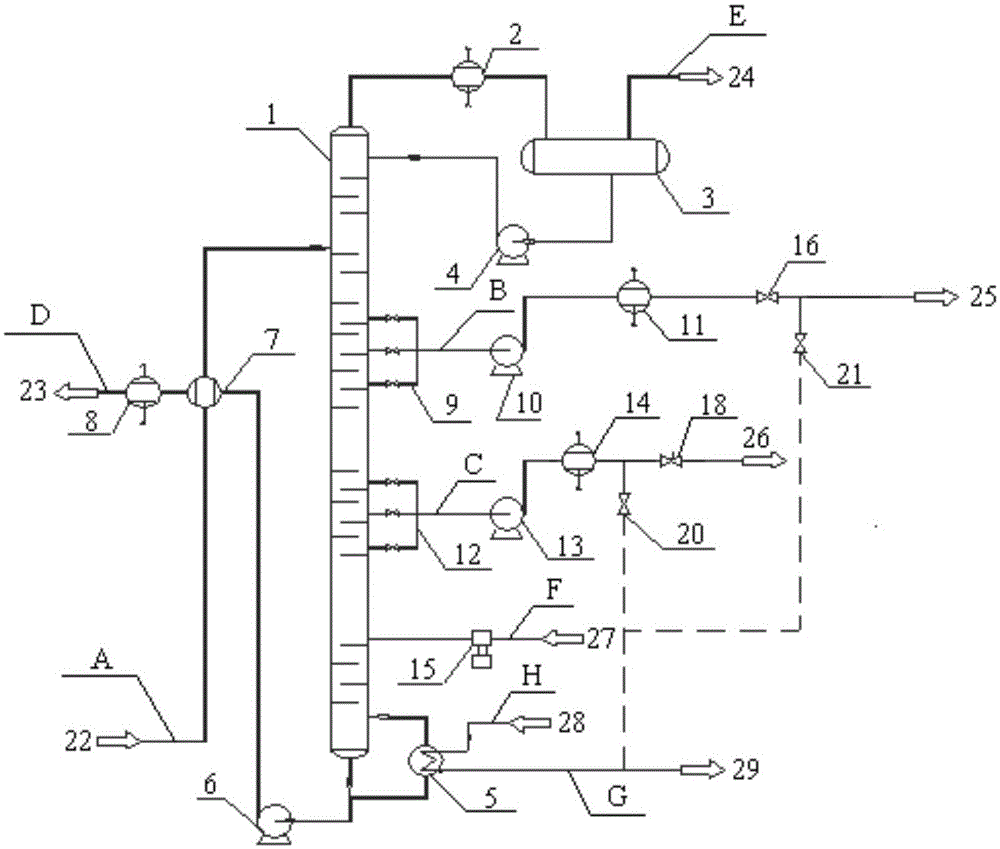
本發(fā)明涉及石油化工行業(yè)酸性污水凈化
技術領域:
,特別涉及一種石油化工酸性污水汽提凈化系統(tǒng)及方法。
背景技術:
:石油化工行業(yè)在原油一次和二次加工過程中(如常減壓、催化裂化、加氫裂化、加氫精制、重整、延遲焦化、硫磺回收等)會產(chǎn)生H2S及NH3濃度較高的酸性污水。通常采用汽提工藝除去石油化工行業(yè)的酸性污水中的H2S和NH3,對酸性污水進行凈化。目前,酸性污水汽提工藝主要包括:雙塔加壓汽提、單塔加壓側(cè)線抽出汽提、單塔低壓全抽出汽提。其中,雙塔加壓汽提以及單塔加壓側(cè)線抽出汽提這兩種工藝本質(zhì)上是相同的,最終都對H2S和NH3分別進行回收?;厥盏腍2S輸送至硫磺回收裝置進行硫磺回收。經(jīng)過汽提凈化的凈化水由汽提塔塔底輸出再輸送回原油加工裝置進行回用,或者輸送至污水處理廠處理后排放。雙塔加壓汽提以及單塔加壓側(cè)線抽出汽提工藝流程復雜、投資及能耗較高,蒸汽單耗分別高達230~280kg/t(酸性水)以及150~200kg/t(酸性水)。在上述的雙塔加壓汽提以及單塔加壓側(cè)線抽出汽提工藝之所以要對H2S和NH3分別進行回收是因為早期的硫磺回收裝置燒嘴設計水平不高,NH3在酸性氣反應爐內(nèi)不能完全分解,造成未反應的NH3與H2S在后續(xù)管路中結鹽腐蝕、堵塞管路。隨著硫磺回收技術水平的大幅提高,已經(jīng)可以將酸性氣中的NH3在反應爐內(nèi)完全分解,不再需要將酸性氣中的NH3分離。而且由于回收的液氨質(zhì)量差且運輸儲存過程中容易發(fā)生爆炸,已經(jīng)沒有必要將H2S和NH3分別進行回收。因此單塔低壓汽提工藝正被國內(nèi)外越來越廣泛地采用。單塔低壓汽提工藝是在0.1MPa左右的壓力下單塔處理酸性水,H2S和NH3同時在塔頂被汽提出來。即酸性氣是H2S和NH3的混合氣體。與雙塔加壓汽提工藝和單塔加壓側(cè)線抽出汽提工藝相比,單塔低壓汽提工藝投資少、能耗低,蒸汽單耗為140~180kg/t(酸 性水)。目前,由于環(huán)保的需要,由經(jīng)過汽提后的凈化水中NH3≤50mg/L、H2S≤20mg/L。為了實現(xiàn)對水資源的循環(huán)利用,石油化工企業(yè)通常將汽提后的凈化水輸送回原油加工裝置進行回用。但是,作為原油加工裝置回用水的凈化水中H2S以及NH3的含量并不需要達到環(huán)保的要求,例如對于加氫裂化裝置來說,當凈化回用水中NH3≤300mg/L時就基本不會對加氫注水效果造成影響。因此,將NH3≤50mg/L、H2S≤20mg/L的凈化水作為原油加工裝置的回用水,會使酸性污水被過度汽提,造成能源的浪費。此外,在催化裂化、延遲焦化等原油加工裝置產(chǎn)生的酸性污水中,除游離氨(NH3)外,還有一部分氨氮是以固定銨形式存在,即以強酸根如SO42-、S2O32-、HSO3-、Cl-等和NH4+結合形成的銨鹽形式存在。所得凈化水所含總氨中有50~80%是以固定銨形式存在的,即當凈化水中的總氨含量為50~400mg/L時,其中的固定銨含量為30~300mmg/L。這部分固定銨采用常規(guī)汽提很難被脫除,如果直接輸送至污水處理廠處理,則會增加后期處理難度。CN1205983公開了一種向汽提塔內(nèi)加氫氧化鈉以去除固定銨的方法。但是該方法得到的凈化水中會含有堿以及鈉離子。如果凈化水中堿濃度過高,當作為電脫鹽設備回用水時,會使原油乳化嚴重;如果凈化水中鈉離子濃度過高,作為加氫裝置的回用水則會引起加氫催化劑中毒。在實現(xiàn)本發(fā)明的過程中,發(fā)明人發(fā)現(xiàn)現(xiàn)有技術中至少存在以下問題:現(xiàn)有的石油化工酸性污水汽提凈化方法能耗較高,且對固定銨含量較高的酸性污水汽提時所得凈化水中的堿濃度及鈉離子濃度過高,不適合繼續(xù)作為回用水使用。技術實現(xiàn)要素:為了解決上述的技術問題,本發(fā)明提供一種能耗低、回用水中堿濃度以及鈉離子濃度較低的石油化工酸性污水汽提凈化系統(tǒng)及方法。具體而言,包括以下的技術方案:本發(fā)明第一方面提供一種石油化工酸性污水汽提凈化系統(tǒng),所述酸性污水中含有H2S和NH3,所述汽提凈化系統(tǒng)包括:汽提塔,所述汽提塔內(nèi)設置40~60塊塔板,用于對所述酸性污水進行汽提凈化;所述汽提塔上還設置有:酸性污水入口,所述酸性污水入口位于自塔頂 向下第2~6塊塔板處;凈化水出口,所述凈化水出口位于所述汽提塔底部;氣體出口,所述氣體出口位于所述汽提塔頂部;酸性污水輸入管線,所述酸性污水輸入管線與所述酸性污水入口連通,用于將初始酸性污水輸送至汽提塔內(nèi);凈化水輸出管線,所述凈化水輸出管線與所述凈化水出口連通,用于將經(jīng)過汽提凈化后的凈化水由所述汽提塔輸出;供熱裝置,所述供熱裝置與所述汽提塔下部連通,用于向所述汽提塔提供熱源;酸性氣體輸出管線,所述酸性氣體輸出管線與所述氣體出口連通,用于將經(jīng)過汽提得到的酸性氣體由汽提塔輸出,所述汽提塔上還設置有:第一回用水出口,所述第一回用水出口位于自塔底向上第9~20塊塔板處;第二回用水出口,所述第二回用水出口位于自塔底向上第3~15塊塔板處;所述汽提凈化系統(tǒng)還包括:第一回用水輸出管線,所述第一回用水輸出管線與所述第一回用水出口連通,用于將自所述第一回用水出口側(cè)線抽出的第一回用水輸出;第二回用水輸出管線,所述第二回用水輸出管線與所述第二回用水出口連通,用于將自所述第二回用水出口側(cè)線抽出的第二回用水輸出。進一步地,所述汽提塔上還設置有:堿液入口,所堿溶液入口位于自塔底向上第4~8塊塔板處;所述汽提凈化系統(tǒng)還包括:堿液輸入管線,所述堿液輸入管線與所述堿液入口連通,用于將堿液輸入汽提塔內(nèi);所述第二回用水出口位于自塔底向上第8~15塊塔板處。優(yōu)選地,所述汽提塔內(nèi)設置40~45塊塔板,所述第一回用水出口位于自塔底向上第9~13塊塔板處;所述第一回用水出口位于自塔底向上第14~20塊塔板處;所述第二回用水出口位于自塔底向上第3~7塊塔板處。優(yōu)選地,所述汽提塔內(nèi)設置55~60塊塔板,所述第一回用水出口位于自塔底向上第14~20塊塔板處;所述第二回用水出口位于自塔底向上第8~15塊塔板處。進一步地,所述凈化水輸出管線分別與所述第一回用水輸出管線以及第二回用水輸出管線連通。進一步地,所述供熱裝置中的凝結水輸出管線分別與所述第一回用水輸出 管線以及第二回用水輸出管線連通。本發(fā)明第二方面提供一種利用本發(fā)明第一方面的汽提凈化系統(tǒng)的汽提凈化方法,所述汽提凈化方法包括以下步驟:將酸性污水由汽提塔的酸性污水入口輸送至汽提塔內(nèi),所述酸性污水經(jīng)過汽提塔內(nèi)的塔板與供熱裝置提供的蒸汽接觸,進行汽提凈化;一部分經(jīng)過凈化的凈化水自上而下流動至第一回用水出口時被側(cè)線抽出,得到第一回用水;一部分經(jīng)過凈化的凈化水自上而下流動至第二回用水出口時被側(cè)線抽出,得到第二回用水;未被側(cè)線抽出的凈化水由汽提塔的凈化水出口輸出;經(jīng)過汽提后所得酸性氣體由汽提塔的氣體出口輸出;所述第一回用水出口位于自塔底向上第9~20塊塔板處;所述第二回用水出口位于自塔底向上第3~15塊塔板處;所述酸性污水入口位于自塔頂向下第2~6塊塔板處;所述凈化水出口位于所述汽提塔底部;所述氣體出口位于所述汽提塔頂部;所述第一回用水、第二回用水以及凈化水中的NH3濃度以及H2S依次降低。進一步地,所述汽提凈化方法還包括:將堿液自汽提塔的堿液入口輸送至汽提塔內(nèi)部,與汽提塔內(nèi)的凈化水混合;所堿溶液入口位于自塔底向上第4~8塊塔板處;所述第二回用水出口位于自塔底向上第8~15塊塔板處。進一步地,將由所述凈化水出口輸出的凈化水分別與第一回用水和第二回用水混合。進一步地,將所述供熱裝置中的凝結水分別與所述第一回用水和第二回用水混合。優(yōu)選地,所述第一回用水中NH3的濃度為300mg/L以下、H2S濃度為25mg/L以下;所述第二回用水中NH3的濃度為150mg/L以下、H2S濃度為20mg/L以下。本發(fā)明實施例提供的技術方案的有益效果:1、本發(fā)明實施例在汽提塔酸性污水入口以及汽提塔底部凈化水出口之間設置第一回用水出口、第二回用水出口,將經(jīng)過一部分塔板汽提凈化的凈化水分別在第一回用水出口和第二回用水出口處被側(cè)線抽出,作為回用水。自第一回 用水出口及第二回用水出口抽出的第一回用水以及第二回用水,由于在汽提凈化過程中與汽提蒸汽接觸時間較短,因此第一回用水以及第二回用水中的NH3濃度以及H2S濃度高于自汽提塔底部凈化水出口輸出的凈化水。第一回用水及第二回用水雖然不能滿足環(huán)保標準,但是能夠滿足加氫裂化、加氫精制、常減壓等原油加工裝置的用水需求,因此,可以將第一回用水及第二回用水輸送至上述原油加工裝置進行回用。本發(fā)明實施例提供的石油化工酸性污水汽提凈化系統(tǒng)及方法根據(jù)凈化水不同的回用質(zhì)量要求,采用不同的汽提深度,避免不必要的汽提蒸汽浪費,有效解決汽提凈化水作為原油加工裝置的回用水時被過度汽提的問題,降低了酸性污水汽提凈化系統(tǒng)運行的能耗,節(jié)約能源。(2)當酸性污水中固定銨含量較高,需要加堿除去固定銨時,在第二回用水出口的下方設置堿液入口,這樣一方面除去了由汽提塔塔底凈化水出口輸出的凈化水中的固定銨,減少環(huán)境污染;另一方面,堿液和固定銨反應生成的鈉鹽以及過量的堿液不會進入到側(cè)線抽出的回用水中,不會影響回用水質(zhì)量,避免由于鈉離子含量以及堿含量過高引起的乳化、催化劑中毒等問題。附圖說明為了更清楚地說明本發(fā)明實施例中的技術方案,下面將對實施例描述中所需要使用的附圖作簡單地介紹,顯而易見地,下面描述中的附圖僅僅是本發(fā)明的一些實施例,對于本領域普通技術人員來講,在不付出創(chuàng)造性勞動的前提下,還可以根據(jù)這些附圖獲得其他的附圖。圖1為本發(fā)明實施例中不需要加入堿液的石油化工酸性污水汽提凈化系統(tǒng)結構示意圖;圖2為本發(fā)明實施例中需要加入堿液的石油化工酸性污水汽提凈化系統(tǒng)結構示意圖;圖3為圖1所示的汽提凈化系統(tǒng)中的汽提塔的結構示意圖;圖4為圖2所示的汽提凈化系統(tǒng)中的汽提塔的結構示意圖。圖中的附圖標記分別表示:1、汽提塔;101、酸性污水入口;102、凈化水出口;103、氣體出口;105、第一回用水出口;106、第二回用水出口;107、堿液入口;104、自塔頂向下第4塊塔板;1031、自塔頂向下第31塊塔板;1033、自塔頂向下第33塊塔板;1035、自塔頂向下第35塊塔板;1037、自塔頂向下第37塊塔板;1039、自塔頂向下第39塊塔板;1041、自塔頂向下第41塊塔板;1043、自塔頂向下第43塊塔板;1045、自塔頂向下第45塊塔板;1047、自塔頂向下第47塊塔板;1049、自塔頂向下第49塊塔板;1051、自塔頂向下第51塊塔板;1056、自塔頂向下第56塊塔板;2、第一冷凝器;3、氣液分離器;4、第一升壓泵;5、供熱裝置;6、第一水泵;7、第一換熱器;8、第一冷卻器;9、第一閥門組;10、第二升壓泵;11、第二冷卻器;12、第二閥門組;13、第三升壓泵;14、第三冷卻器;15、堿液注入泵;16、第一流量調(diào)節(jié)閥;17、第二流量調(diào)節(jié)閥;18、第三流量調(diào)節(jié)閥;19、第四流量調(diào)節(jié)閥;20、第五流量調(diào)節(jié)閥、21、第六流量調(diào)節(jié)閥;22、酸性污水輸入管線;23、凈化水輸出管線;24、酸性氣體輸出管線;25、第一回用水輸出管線;26、第二回用水輸出管線;27、堿液輸入管線;28、熱源蒸汽輸入管線;29、凝結水輸出管線;A、酸性污水;B、第一回用水;C、第二回用水;D、凈化水;E、酸性氣體;F、堿液;G、凝結水;H、汽提蒸汽。具體實施方式為使本發(fā)明的技術方案和優(yōu)點更加清楚,下面將結合附圖對本發(fā)明實施方式作進一步地詳細描述。本發(fā)明第一方面提供一種石油化工酸性污水汽提凈化系統(tǒng),所述酸性污水為原油一次和二次加工過程中產(chǎn)生的含有H2S及NH3的酸性污水,參見圖1和圖3,所述汽提凈化系統(tǒng)包括:汽提塔1,所述汽提塔1內(nèi)設置40~60塊塔板,用于對所述酸性污水進行汽提凈化;所述汽提塔1上還設置有:酸性污水入口101,所述酸性污水入口101位于自塔頂向下第2~6塊塔板處;凈化水出口102,所述凈化水出口102位于所述汽提塔1底部;氣體出口103,所述氣體出口103位于所述汽提塔1頂部;酸性污水輸入管線22,所述酸性污水輸入管線22與所述酸性污水入口101 連通,用于將初始酸性污水輸送至汽提塔1內(nèi);凈化水輸出管線23,所述凈化水輸出管線23與所述凈化水出口102連通,用于將經(jīng)過汽提凈化后的凈化水由所述汽提塔1輸出;供熱裝置5,所述供熱裝置5與所述汽提塔1下部連通,用于向所述汽提塔1提供熱源;酸性氣體輸出管線24,所述酸性氣體輸出管線24與所述氣體出口103連通,用于將經(jīng)過汽提得到的酸性氣體由汽提塔1輸出;所述汽提塔1上還設置有:第一回用水出口105,所述第一回用水出口105位于自塔底向上第9~20塊塔板處;第二回用水出口106,所述第二回用水出口106位于自塔底向上第3~15塊塔板處;所述汽提凈化系統(tǒng)還包括:第一回用水輸出管線25,所述第一回用水輸出管線25與所述第一回用水出口105連通,用于將自所述第一回用水出口105側(cè)線抽出的第一回用水輸出;第二回用水輸出管線26,所述第二回用水輸出管線26與所述第二回用水出口106連通,用于將自所述第二回用水出口106側(cè)線抽出的第二回用水輸出。本發(fā)明實施例提供的汽提凈化系統(tǒng)與現(xiàn)有的單塔低壓汽提系統(tǒng)相比,具有明顯的優(yōu)勢,其工作原理為:酸性污水A經(jīng)過酸性污水輸入管線22由酸性污水入口101進入汽提塔進行汽提凈化。酸性污水A與來自供熱裝置5的蒸汽H接觸,溶解在酸性污水A中的NH3以及H2S擴散到汽提蒸汽H中,并隨著汽提蒸汽H由氣體出口103輸出,從而使酸性污水A中的NH3以及H2S含量降低,使酸性污水A得到凈化。當凈化后的水在汽提塔內(nèi)自上而下依次經(jīng)過第一回用水出口105以及第二回用水出口106時,會有部分的凈化水分別從第一回用水出口105以及第二回用水出口106被側(cè)線抽出,作為第一回用水B以及第二回用水C由第一回用水輸送管線25以及第二回用水輸送管線26輸送至相應的原油加工裝置。未被側(cè)線抽出的凈化水D由汽提塔1塔底的凈化水出口102輸出后由凈化水輸送管線23輸送至污水處理廠進行后續(xù)處理。第一回用水B以及第二回用水C由于在汽提凈化過程中與汽提蒸汽H接觸時間較短,因此第一回用水B以及第二回用水C中的NH3濃度以及H2S濃度高于自汽提塔底部凈化水出 口102輸出的凈化水D。第一回用水B及第二回用水C雖然不能滿足環(huán)保標準,但是能夠滿足加氫裂化、加氫精制、常減壓等原油加工裝置的用水需求,因此,可以將第一回用水B及第二回用水C輸送至上述原油加工裝置進行回用。因此,本發(fā)明實施例提供的石油化工酸性污水汽提凈化系統(tǒng)能夠根據(jù)凈化水不同的回用質(zhì)量要求,采用不同的汽提深度,避免不必要的汽提蒸汽浪費,有效解決汽提凈化水作為原油加工裝置的回用水時被過度汽提的問題,降低了酸性污水汽提凈化系統(tǒng)運行的能耗,節(jié)約能源。當酸性污水A中的固定銨含量較高時,則需要加堿來除去固定銨。因此,參見圖2以及圖4,在設置第一回用水出口105以及第二回用水出口106的基礎上,汽提塔1上還設置有:堿液入口107,所堿溶液入口107位于自塔底向上第4~8塊塔板處;所述汽提凈化系統(tǒng)還包括:堿液輸入管線27,所述堿液輸入管線27與所述堿液入口107連通,用于將堿液F輸入汽提塔1內(nèi)。堿液F自堿液入口107進入汽提塔1后,與汽提塔1內(nèi)的含有固定銨的凈化水混合,與其中的NH4+反應,將NH4+轉(zhuǎn)化為NH3,NH3隨汽提蒸汽H由氣體出口103輸出,從而將固定銨除去。為了防止側(cè)線采出的回用水中含有堿,因此,第二回用水出口016應該位于堿液入口107上方,即位于自塔底向上第8~15塊塔板處。采用上述汽提凈化系統(tǒng),一方面除去了由汽提塔塔底凈化水出口輸出的凈化水中的固定銨,減少環(huán)境污染;另一方面,堿液和固定銨反應生成的鈉鹽以及過量的堿液不會進入到側(cè)線抽出的回用水中,不會影響回用水質(zhì)量,避免由于鈉離子含量以及堿含量過高引起的乳化、催化劑中毒等問題。在上述的汽提凈化系統(tǒng)中,堿液入口107在汽提塔1上的位置非常重要,如果堿液入口107位置過高,凈化水中的H2S含量仍然較高,堿液F注入后,會與H2S反應造成塔底硫含量超標;如果堿液入口107位置過低,銨離子解離出的NH3得不到充分的汽提。因此,本發(fā)明實施例中的堿液入口107位于自塔底向上第4~8塊塔板處,優(yōu)選位于自塔底向上第6塊塔板處。以塔板數(shù)為56塊為例,堿液入口107可以位于自塔底向上第6塊塔板處,即自塔頂向下第51塊塔板1051處。在上述的汽提凈化系統(tǒng)中,對于沒有設置堿液入口107的汽提塔1來說,其內(nèi)部塔板的數(shù)量優(yōu)選為40~45塊,則第一回用水出口105優(yōu)選位于自塔底向上第9~13塊塔板處,第二回用水出口106優(yōu)選位于自塔底向上第3~7塊塔板處。 對于設置了堿液入口107的汽提塔1來說,其內(nèi)部塔板的數(shù)量優(yōu)選為55~60塊,則第一回用水出口105優(yōu)選位于自塔底向上第14~20塊塔板處,第二回用水出口106優(yōu)選位于自塔底向上第8~15塊塔板處。在上述的汽提凈化系統(tǒng)中,第一回用水出口105以及第二回用水出口106的位置可以根據(jù)原油加工裝置對于回用水中NH3以及H2S濃度的要求設定。為了便于操作,可以如圖1以及圖2所示,設置多個第一回用水出口105以及第二回用水出口106,通過第一閥門組9以及第二閥門組12來控制第一回用水出口105以及第二回用水出口106的具體位置。在上述的汽提凈化系統(tǒng)中,酸性氣體輸出管線24上設置有第一冷凝器2、氣液分離器3以及第一升壓泵4。由氣體出口103輸出的酸性氣體E經(jīng)過第一冷凝器2冷凝后得到氣液混合物,然后進入氣液分離器3進行氣液分離。其中,氣相部分為含NH3的H2S的混合氣體,該混合氣體輸送至硫磺回收裝置進行硫磺回收;液相部分由第一升壓泵4升壓后輸送回汽提塔1。在上述的汽提凈化系統(tǒng)中,第一回用水輸出管線25上還設置有第二升壓泵10、第二冷卻器11。自第一回用水出口105側(cè)線抽出的第一回用水B經(jīng)第二升壓泵11升壓到界區(qū)所需壓力并經(jīng)第二冷卻器11冷卻后輸送至相應的原油加工裝置。第二回用水輸出管線26上還設置有第三升壓泵13、第三冷卻器14。自第二回用水出口106側(cè)線抽出的第二回用水C經(jīng)第三升壓泵13升壓到界區(qū)所需壓力并經(jīng)第三冷卻器14冷卻后輸送至相應的原油加工裝置。如果作為電脫鹽等操作溫度較高的設備的回用水,可以不經(jīng)過冷卻直接使用。在上述的汽提凈化系統(tǒng)中,凈化水輸出管線23上還設置有第一水泵6、第一換熱器7以及第一冷卻器8,凈化水D由第一水泵6抽出后,經(jīng)過第一換熱器7與酸性污水A換熱后,再經(jīng)過第一冷卻器8進一步降溫后輸送至污水處理廠。在上述的汽提凈化系統(tǒng)中,由于凈化水D中NH3以及H2S含量較少,可以將凈化水輸出管線23分別與所述第一回用水輸出管線25以及第二回用水輸出管線26連通,將凈化水D分別與第一回用水B與第二回用水C混合,以調(diào)節(jié)第一回用水B以及第二回用水C中NH3以及H2S的含量。對于設置堿液入口107的汽提凈化系統(tǒng)來說,由于凈化水D中含有大量鈉離子和堿,因此,可以將加熱裝置5的凝結水輸出管線29與第一回用水輸出管線25以及第二回用水輸出 管線26連通,利用汽提蒸汽H冷凝后的凝結水G來調(diào)節(jié)第一回用水B以及第二回用水C中NH3以及H2S的含量。還可以分別在第一回用水輸出管線25、第二回用水輸出管線26、第一回用水輸出管線25與凈化水輸出管線23連通的管線、第二回用水輸出管線26與凈化水輸出管線23連通的管線、第一回用水輸出管線25與凝結水輸出管線29連通的管線、第二回用水輸出管線26與凝結水輸出管線29連通的管線上設置第一流量調(diào)節(jié)閥門16、第二流量調(diào)節(jié)閥17、第三流量調(diào)節(jié)閥18、第四流量調(diào)節(jié)閥19、第五流量調(diào)節(jié)閥20以及第六流量調(diào)節(jié)閥21,通過流量調(diào)節(jié)閥門調(diào)節(jié)流量,實現(xiàn)第一回用水B、第二回用水C與凈化水D或者凝結水G混合的比例。在上述的汽提凈化系統(tǒng)中,可以根據(jù)石油煉制企業(yè)實際需要,在汽提塔1上只設置第一回用水出口105或者只設置第二回用水出口106,同時取消第一回用水輸出管線25或者第二回用水輸出管線26以及其他相關部件。同時還可以適當?shù)臏p少塔板的數(shù)目。例如,當僅用做加氫裂化或催化裂化等裝置注水時,取消第二回用水出口106以及第二回用水輸出管線26,同時取消第二回用水出口106對應的塔板;當僅用做常減壓或加氫精制等裝置注水時,取消第一回用水出口105以及第一回用水輸出管線25,同時取消第一回用水出口105對應的塔板。根據(jù)上述對汽提凈化系統(tǒng)工作原理的解釋,本發(fā)明第二方面提供一種利用本發(fā)明第一方面的汽提凈化系統(tǒng)對酸性污水進行汽提凈化的方法。所述汽提凈化方法包括以下步驟:將酸性污水A由汽提塔1的酸性污水入口101輸送至汽提塔1內(nèi),所述酸性污水A經(jīng)過汽提塔1內(nèi)的塔板與供熱裝置5提供的蒸汽接觸,進行汽提凈化;一部分經(jīng)過凈化的凈化水自上而下流動至第一回用水出口105時被側(cè)線抽出,得到第一回用水B;一部分經(jīng)過凈化的凈化水自上而下流動至第二回用水出口106時被側(cè)線抽出,得到第二回用水C;未被側(cè)線抽出的凈化水D由汽提塔1的凈化水出口102輸出;經(jīng)過汽提后所得酸性氣體E由汽提塔1的氣體出口103輸出;所述第一回用水出口105位于自塔底向上第9~20塊塔板處;所述第二回用水出口106位于自塔底向上第3~15塊塔板處;所述酸性污水入口101位于自塔 頂向下第2~6塊塔板處;所述凈化水出口102位于所述汽提塔1底部;所述氣體出口103位于所述汽提塔1頂部;所述第一回用水B、第二回用水C以及凈化水D中的NH3濃度以及H2S依次降低。本發(fā)明實施例提供的石油化工酸性污水汽提凈化方法能夠根據(jù)凈化水不同的回用質(zhì)量要求,采用不同的汽提深度,避免不必要的汽提蒸汽浪費,有效解決汽提凈化水作為原油加工裝置的回用水時被過度汽提的問題,降低了酸性污水汽提凈化系統(tǒng)運行的能耗,節(jié)約能源。在上述的汽提凈化方法中,如果酸性污水A中固定銨含量較高,則在上述步驟的基礎上,還包括以下步驟:將堿液F自汽提塔1的堿液入口107輸送至汽提塔1內(nèi)部,與汽提塔1內(nèi)的凈化水混合。堿液入口107位于第二回用水出口106下方。一方面除去了由汽提塔塔底凈化水出口輸出的凈化水中的固定銨,減少環(huán)境污染;另一方面,堿液和固定銨反應生成的鈉鹽以及過量的堿液不會進入到側(cè)線抽出的回用水中,不會影響回用水質(zhì)量,避免由于鈉離子含量以及堿含量過高引起的乳化、催化劑中毒等問題。在上述的汽提凈化方法中,可以通過將凈化水D與第一回用水B和第二回用水C混合或者凝結水G與第一回用水B和第二回用水C混合的方法來調(diào)節(jié)第一回用水B和第二回用水C中NH3以及H2S的含量。在上述的汽提凈化方法中,酸性污水A在進入酸性污水入口101之前,還可以先利用本領域常規(guī)技術手段進行前處理,即酸性污水A首先進入酸性水脫氣罐脫除溶在其中的輕烴組份,然后在液位控制下自壓進入酸性水原料罐,經(jīng)罐內(nèi)除油設施除油及沉降脫油后,由酸性污水加壓泵升壓,然后經(jīng)過第一換熱器7與來自凈化水輸出管線23的凈化水D換熱后進入汽提塔1。在上述的汽提凈化系統(tǒng)中,各物料的溫度、壓力本領域技術人員可以根據(jù)實際情況自行設置,本發(fā)明實施例不做特殊限定。第一回用水B、第二回用水C以及凈化水D中的NH3以及H2S的含量也由本領域技術人員根據(jù)實際情況調(diào)整,本發(fā)明實施例同樣不做特殊限定。值得一提的是,凈化水D滿足污水處理場所要求的指標越苛刻,凈化水作為回用水被過度汽提的程度也越大,采用本發(fā)明實施例提供的凈化系統(tǒng)及方法所獲得的節(jié)能效果也越明顯。實施例1本實施例提供一種不需要加堿除去固定銨的酸性污水汽提凈化裝置及方法。如圖1和圖3所示,本實施例中的汽提塔1中內(nèi)設置43塊塔板,酸性污水入口101位于自塔頂向下第4塊塔板104處;分別在自塔頂向下第31塊塔板1031、第33塊塔板1033及第35塊塔板1035處設置第一回用水出口105(即自塔底向上第9、11、13塊塔板),利用第一閥門組9控制第一回用水B輸出的具體位置。分別在自塔頂向下第37塊塔板1037、第39塊塔板1039及第41塊塔板1041處設置第二回用水出口106(即自塔底向上第3、5、7塊塔板),利用第二閥門組12控制第二回用水C輸出的具體位置。汽提塔1的塔頂溫度為110~120℃、塔底溫度為125~136℃、塔頂壓力為0.12~0.16MPa(g)、塔底壓力為0.17~0.20MPa(g)。酸性污水A首先進入酸性水脫氣罐,再進入兩級酸性水原料罐進一步除油。然后酸性污水A經(jīng)過換熱器7與來自汽提塔1塔底凈化水出口的凈化水D換熱到80~85℃,由酸性污水入口101進入汽提塔1進行汽提凈化。汽提后酸性氣體E經(jīng)第一冷凝器2冷凝冷卻至85~90℃后進入氣液分離器3,分出的酸性水由第一升壓泵4升壓送回汽提塔1上部作為回流;氣相部分輸送至硫磺回收裝置。供熱裝置5(塔底重沸器)為汽提塔1提供熱源,汽提蒸汽H為0.6~1.0MPa(g)蒸汽,由熱源蒸汽輸入管線28輸入。第一回用水B由第一回用水出口105被側(cè)線抽出,第一回用水B的溫度為118~131℃、壓力為0.15~0.18MPa(g);第二回用水C由第二回用水出口106被側(cè)線抽出,第二回用水C的溫度為120~133℃、壓力為0.16~0.19MPa(g)。未被側(cè)線抽出的凈化水D由第一水泵6抽出,再經(jīng)第一換熱器7與酸性污水A換熱至60~65℃,最后經(jīng)第一冷卻器8冷卻至40℃后送至污水處理場。其中,第一回用水B中NH3含量≤300mg/L、H2S含量≤25mg/L,滿足加氫裂化或催化裂化等裝置的回用水指標要求,因此,第一回用水B由第二升壓泵10升壓到界區(qū)所需要的壓力并經(jīng)第二冷卻器11冷卻到40℃后輸送至加氫裂化或催化裂化等裝置;第二回用水C中NH3含量≤150mg/L、H2S含量≤20mg/L,滿足常減壓電脫鹽或加氫精制等裝置回用水要求,因此,第二回用水C由第三升壓泵13升壓到界區(qū)所需要的壓力并經(jīng)第三冷卻器14冷卻到40℃后輸送至加氫精制裝置;由于常減壓電脫鹽的操作溫度一般在100~140℃之間,因此第二 回用水C可以不經(jīng)過冷卻直接與原油混合。凈化水D中NH3含量≤50mg/L、H2S含量≤25mg/L??梢岳脙艋瓺對第一回用水B、第二回用水C中的NH3含量以及H2S含量進行調(diào)節(jié)。例如,第一回用水B的抽出量為40t/h,其中H2S含量16mg/L、NH3含量120mg/L;凈化水D流量為60t/h,其中H2S含量8mg/L、NH3含量40mg/L,現(xiàn)需要將第一回用水B作為常減壓裝置電脫鹽注水,要求NH3含量為80mg/L,因此,需要將第一回用水B和凈化水D按照質(zhì)量比1:1混合,可以通過調(diào)節(jié)第一流量調(diào)節(jié)閥16以及第二流量調(diào)節(jié)閥17將第一回用水B和凈化水D的流量均調(diào)節(jié)為20t/h將二者混合。實施例2本實施例提供一種需要加堿除去固定銨的酸性污水汽提凈化裝置及方法。如圖2和圖4所示,本實施例中的汽提塔1中內(nèi)設置56塊塔板,酸性污水入口101位于自塔頂向下第4塊塔板104處;分別在自塔頂向下第39塊塔板1039、第41塊塔板1041及第43塊塔板1043處設置第一回用水出口105(即自塔底向上第14、16、18塊塔板),利用第一閥門組9控制第一回用水B輸出的具體位置。分別在自塔頂向下第45塊塔板1045、第47塊塔板1047及第49塊塔板1049處設置第二回用水出口106(即自塔底向上第8、10、12塊塔板),利用第二閥門組12控制第二回用水C輸出的具體位置;在自塔頂向下第51塊塔板處(即自塔底向上第6塊塔板)設置堿液入口107。堿液F(質(zhì)量濃度10%的氫氧化鈉溶液)通過堿液輸入管線27由堿液注入泵15輸送至堿液入口107進而進入汽提塔1,鈉離子取代銨離子與強酸根離子結合,形成穩(wěn)定的鹽,銨離子得以解離以氨的形式從水中分離。由于注入堿液F后,所得凈化水D中鈉離子和堿含量較高,因此,利用凝結水G來調(diào)節(jié)第一回用水B以及第二回用水C中NH3以及H2S的含量。除以上所述外,其余工藝流程、操作條件等與實施例1相同。本實施例中所用酸性污水A及第一回用水B、第二回用水C、凈化水D以及酸性氣體E的性質(zhì)如表1所示。其中,污水處理場凈化水為凈化水D,加氫裂化回用水為第一回用水B,常減壓裝置回用水為第二回用水C,硫磺回收酸性氣為酸性氣體E。表1實施例2中酸性污水和凈化后各產(chǎn)品性質(zhì)對比例本對比例采用現(xiàn)有的單塔低壓汽提工藝對酸性污水進行汽提凈化。其中,汽提塔內(nèi)設置36塊塔板,在自塔頂向下第31塊塔板處設置堿液入口,10%的氫氧化鈉溶液自堿液入口進入汽提塔。全部凈化水由塔底凈化水出口輸出,然后在塔底液位控制下部分送至常減壓裝置、部分送至加氫裂化裝置回用,剩余部分送到污水處理場。其余同實施例2。本對比例中,酸性污水和經(jīng)處理后的產(chǎn)品性質(zhì)見表2。表2對比例中酸性污水和凈化后各產(chǎn)品性質(zhì)從上述表1和表2的數(shù)據(jù)可以看出,實施例2和對比例的酸性污水的用量和性質(zhì)完全相同。但是最終產(chǎn)品中,對比例至加氫裝置回用水和至常減壓裝置回用水中Na+濃度均為115mg/L,而實施例中至加氫裝置回用水和至常減壓裝置回用水中Na+濃度均為0。而實施例和對比例中輸送至污水處理廠的凈化水的性質(zhì)沒有明顯的差別。由此可見。采用本發(fā)明實施例提供的方法,一方面除去了由汽提塔塔底凈化水出口輸出的凈化水中的固定銨,減少環(huán)境污染;另一方面,堿液和固定銨反應生成的鈉鹽以及過量的堿液不會進入到側(cè)線抽出的回用水中,不會影響回用水質(zhì)量,避免由于鈉離子含量以及堿含量過高引起的乳化、 催化劑中毒等問題。表3中對比了實施例2和對比例采用的汽提凈化系統(tǒng)及方法的能耗、所需設備情況及投資等數(shù)據(jù)。表3實施例2和對比例的能耗所需設備情況及投資對比序號項目比較例實施例一能量消耗對比1汽提塔頂冷凝器負荷/kW412018962汽提塔底凈化水冷卻負荷/kW201114513第一回用水冷卻器負荷/kW010354汽提塔底重沸器負荷/kW960378415用電負荷/kW134.8135.26消耗1.0MPa蒸汽量/kg.h-116853137617消耗循環(huán)水量/t.h-1527.21377.238處理每噸酸性水能耗/MJ.t-1460.72367.97二所需設備情況對比1酸性水汽提塔塔板數(shù)36562酸性水汽提塔直徑/m1.81.63第一回用水升壓泵無有4第一回用水冷卻器無有5第二回用水升壓泵無有6汽提塔底重沸器尺寸較大尺寸較小7汽提塔頂冷凝器尺寸較大尺寸較小8汽提塔頂回流罐尺寸較大尺寸較小9汽提塔頂回流泵尺寸較大尺寸較小10酸性水-凈化水換熱器尺寸較大尺寸較小11凈化水冷卻器尺寸較大尺寸較小三投資對比1相對投資98.76100.00從表3可以看出,實施例2中汽提塔塔板數(shù)多余對比例,但塔直徑較小;與對比例相比,實施例新增的設備有第一回用水升壓泵、第一回用水冷卻器、第二回用水升壓泵,但汽提塔底重沸器(供熱裝置5)、汽提塔頂冷凝器(第一冷凝器2)、汽提塔頂回流罐(氣液分離器3)、汽提塔頂回流泵(第一升壓泵4)、酸性水-凈化水換熱器(第一換熱器7)等設備尺寸較小??傮w來講,雖然實施例設備投資略高,但與對比例相比差別不大;對于公用工程消耗來說,實施例和對比例蒸汽單耗分別為13.761kg/t(酸性水)和16.853kg/t(酸性水),循環(huán)水單耗分別為3.77t/t(酸性水)和5.27t/t(酸性水),實施例的蒸汽單耗和循環(huán)水單耗明顯低于對比例;在總能耗上,實施例與對比例相比降低了28.45%,節(jié)能效果明顯。綜上,本發(fā)明實施例提供的石油化工酸性污水汽提凈化系統(tǒng)及方法根據(jù)凈化水不同的回用質(zhì)量要求,采用不同的汽提深度,避免不必要的汽提蒸汽浪費,有效解決汽提凈化水作為原油加工裝置的回用水時被過度汽提的問題,降低了酸性污水汽提凈化系統(tǒng)運行的能耗,節(jié)約能源,并且能夠避免凈化水作為回用水時堿含量和鈉離子含量過高,影響回用水質(zhì)量。以上所述僅是為了便于本領域的技術人員理解本發(fā)明的技術方案,并不用以限制本發(fā)明。凡在本發(fā)明的精神和原則之內(nèi),所作的任何修改、等同替換、改進等,均應包含在本發(fā)明的保護范圍之內(nèi)。當前第1頁1 2 3