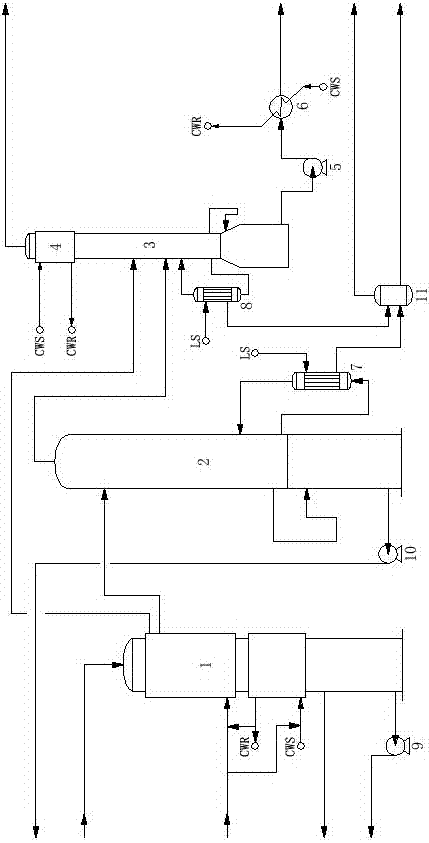
本發(fā)明屬于化工設(shè)備技術(shù)領(lǐng)域,特別涉及一種用于熱法聯(lián)堿生產(chǎn)的母液脫氨工藝及設(shè)備。
背景技術(shù):母液脫氨和煅燒是熱法聯(lián)堿生產(chǎn)的兩大重要工段。目前典型的熱法聯(lián)堿脫氨工藝流程為:利用出脫氨塔的高溫脫氨尾氣與進(jìn)入脫氨塔的濾過母液進(jìn)行換熱,預(yù)熱后的母液進(jìn)入母液脫氨塔上部,液體自上而下流動(dòng)和再沸器產(chǎn)生的蒸汽逆流接觸,以脫除母液中的游離氨和CO2,預(yù)熱母液后的脫氨氣經(jīng)塔頂冷凝器冷凝后送至吸氨塔制備氨鹽水,冷凝液作為回流液全部進(jìn)入脫氨塔。而煅燒工段的約115℃的高溫爐氣經(jīng)除塵,進(jìn)入爐氣冷凝塔,爐氣得到冷卻,冷凝液送至氨回收工段,冷卻后爐氣經(jīng)洗滌后送壓縮利用。在現(xiàn)有工廠生產(chǎn)中及典型的工藝流程設(shè)計(jì)中,高溫爐氣冷卻通常采用冷卻水進(jìn)行間接冷卻,生產(chǎn)每噸純堿約30萬千卡的熱量需移出,此過程要消耗大量的冷卻水。以聯(lián)堿行業(yè)準(zhǔn)入規(guī)模年產(chǎn)60萬噸聯(lián)堿裝置計(jì),爐氣冷凝每小時(shí)消耗的冷卻水量約2250噸。
技術(shù)實(shí)現(xiàn)要素:本發(fā)明的目的在于:針對上述存在的問題,提供一種結(jié)合母液脫氨和煅燒兩大工段的熱量供求特點(diǎn),優(yōu)化能量利用,顯著降低脫氨液的蒸發(fā)當(dāng)量和爐氣冷卻水用量的用于熱法聯(lián)堿生產(chǎn)的母液脫氨工藝及設(shè)備。本發(fā)明的技術(shù)方案是這樣實(shí)現(xiàn)的:一種用于熱法聯(lián)堿生產(chǎn)的母液脫氨工藝,其特征在于:包括以下工藝流程:首先,將來自煅燒工序的110~115℃的高溫煅燒爐氣與來自制堿過程的濾過母液在爐氣冷凝器中進(jìn)行換熱,預(yù)熱后的濾過母液溫度達(dá)到85~90℃,同時(shí)爐氣得到冷卻;然后,將預(yù)熱后的濾過母液送至母液脫氨塔,生成的脫氨尾氣直接進(jìn)入尾氣精餾塔進(jìn)行精餾;最后,經(jīng)尾氣精餾塔頂部的尾氣冷凝器冷卻后的精餾尾氣送至吸氨塔吸收,而尾氣精餾塔底部氨含量低于5ppm的凈氨液經(jīng)冷卻后供其他用戶使用。本發(fā)明所述的用于熱法聯(lián)堿生產(chǎn)的母液脫氨工藝,其經(jīng)過母液脫氨塔脫出的脫氨尾氣直接進(jìn)入尾氣精餾塔進(jìn)料板,尾氣精餾塔外設(shè)的精餾塔再沸器采用低壓蒸汽提供熱源,尾氣精餾塔頂部的尾氣冷凝器的冷凝液回流進(jìn)入尾氣精餾塔,脫氨尾氣的精餾在真空壓力下操作,真空度范圍在10~40Kpa。本發(fā)明所述的用于熱法聯(lián)堿生產(chǎn)的母液脫氨工藝,其所述母液脫氨塔底部的脫氨液經(jīng)冷凝液閃發(fā)器回收低壓蒸汽后,通過脫氨母液泵送至蒸發(fā)結(jié)晶工序,冷凝液閃發(fā)器頂部生成的閃發(fā)汽送至相應(yīng)管網(wǎng),冷凝液閃發(fā)器底部生成的蒸汽冷凝液送至相應(yīng)管網(wǎng)。本發(fā)明所述的用于熱法聯(lián)堿生產(chǎn)的母液脫氨工藝,其所述尾氣精餾塔底部的凈氨液經(jīng)冷凝液閃發(fā)器回收低壓蒸汽后,通過凈...