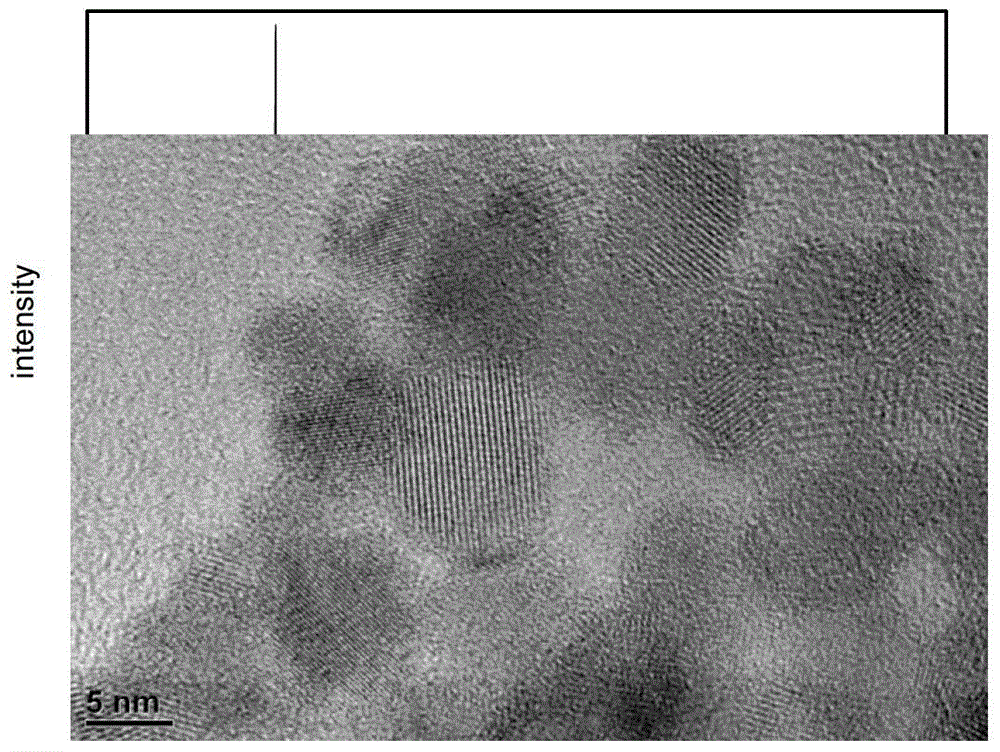
本發(fā)明涉及石油化工領(lǐng)域,具體地說,涉及一種FCC再生煙氣脫硝用復(fù)合氧化物催化劑及其制備方法。
背景技術(shù):催化裂化(FCC)裝置是原油深度加工過程中的重要單元,在煉油工業(yè)中占有舉足輕重的地位。在催化裂化反應(yīng)過程中,原料油發(fā)生裂化的同時,其中30%~50%的含氮化合物進入油焦,并隨之沉積在催化劑表面。催化劑因表面附著油焦而活性降低,必須進行再生處理。在再生器燒焦過程中,大部分含氮化合物轉(zhuǎn)化為N2,但也有10%~30%轉(zhuǎn)化為NOx,隨再生煙氣排出。其中主要成分為NO,體積百分?jǐn)?shù)約為90%,剩余10%左右為NO2。根據(jù)原料和操作條件的不同,再生煙氣中NOx濃度也存在差異,但普遍高于《大氣污染物綜合排放標(biāo)準(zhǔn)》(GB16297-1996)中要求的420mg/m3(1997年以前建設(shè)的裝置)和240mg/m3(1997年及以后建設(shè)的裝置),且均未配備煙氣脫硝設(shè)施。另一方面,由于原油加工業(yè)的迅速發(fā)展和原油劣質(zhì)化的不利影響,煉油企業(yè)的NOx排放量越來越大。通常,再生煙氣是煉油廠NOx排放的主要來源,約占其總排放量的50%。截止目前,中國石油共有41套FCC裝置,總生產(chǎn)能力達5080萬噸/年,再生煙氣排放總量超過500萬Nm3/h,NOx年排放量約為1.2萬噸。如果采用煙氣脫硝技術(shù)對其進行處理,以NOx去除率為80%計算,僅此一項,就可實現(xiàn)集團公司NOx排放量降低10%??梢?,F(xiàn)CC再生煙氣中NOx排放問題已成為中國石油各煉油企業(yè)的共性問題,嚴(yán)重地制約了中國石油節(jié)能減排和清潔生產(chǎn)工作的向前推進??梢灶A(yù)見,隨著環(huán)保標(biāo)準(zhǔn)的日益嚴(yán)格,中國石油各煉油企業(yè)對FCC再生煙氣脫硝技術(shù)的生產(chǎn)需求必將迅速擴大。目前,國內(nèi)外也已工業(yè)應(yīng)用的FCC再生煙氣脫硝技術(shù)包括:低NOx燒焦技術(shù)、氧化吸收法、添加助劑法、選擇性非催化還原(SNCR)法和選擇性催化還原(SCR)法。五種FCC再生煙氣脫硝技術(shù)特點不同,分別適用于不同的處理條件和處理要求,需要因地制宜地進行選擇。但是,就中國石油現(xiàn)有的41套FCC裝置而言,若要從整體上解決再生煙氣脫硝問題,選擇性催化還原(SCR)因處理效果穩(wěn)定、適應(yīng)范圍廣、工藝成熟,無疑是最有競爭力的技術(shù)。目前,國內(nèi)已申請了很多關(guān)于SCR催化劑的專利。公開號為CN101480611介紹了一種水溶液體系中原位釩摻雜鈦基脫硝催化劑,但是由于是水溶液體系,所以釩的摻雜形式主要是在鈦氧化物的表面;公開號為CN102198397介紹了一種利用沉淀法,通過添加硅溶膠合成具有高比表面積的納米二氧化鈦載體,從而使活性組分之間產(chǎn)生強的相互作用,提高催化劑的活性。
技術(shù)實現(xiàn)要素:本發(fā)明的目的在于提供一種FCC再生煙氣脫硝用催化劑,其是一種乙醇體系中的原位骨架摻雜釩的納米二氧化鈦,使催化劑的活性組分直接分散在二氧化鈦的骨架中,分散性好。該方法制備簡單,且合成的全為結(jié)晶度較高的銳鈦礦晶型,在很寬的溫度區(qū)間具有很好的活性,具有很好的抗SO2性能。本發(fā)明所制備是基于乙醇體系,采用溶膠凝膠法合成的原位骨架摻雜釩的納米二氧化鈦催化劑。釩的摻雜量為0.8%~1.4%,活性組分釩進入二氧化鈦的骨架。本發(fā)明所述的釩鈦骨架摻雜氧化物催化劑及其制備方法,包括如下步驟:(1)將0.5~2gP123溶解到10~30g乙醇中稱為a液;(2)將0.0338~0.0591g釩源溶解到1~2g濃縮的HCl和0.2~0.6g44%的H2SO4中稱為b液;(3)將b液加入a液中,至于水浴中,在40~50℃下強力攪拌溶解3~4小時,獲得均一透明溶膠;(4)然后加入3~4g鈦源,繼續(xù)強力攪拌20~25小時;(5)用培養(yǎng)皿轉(zhuǎn)移至恒溫恒濕干燥箱中,溶劑蒸發(fā)并誘導(dǎo)P123的自組裝,蒸發(fā)誘導(dǎo)后形成凝膠,然后干燥,最終在N2氣氛以及空氣氣氛下焙燒獲得催化劑;溶劑蒸發(fā)并誘導(dǎo)P123自組裝過程:保持恒溫恒濕,溫度40~50℃,相對濕度50~60%,蒸發(fā)誘導(dǎo)時間持續(xù)40~50小時所采用的前軀體釩源是偏釩酸銨、鈦源是異丙醇鈦。所述的凝膠的干燥溫度為100~120℃,持續(xù)40~50h。所述的焙燒條件為在氮氣氛中300~400℃氣氛下處理3~4h,隨后在空氣中400~500℃焙燒6~7h,升溫速率為每分鐘1~2℃。本復(fù)合氧化物催化劑用作FCC再生煙氣脫硝用催化劑,在其作用下進行高效選擇催化還原形成氮氣進行消除。通過本發(fā)明,可制得納米粒子形貌,抗熱及抗二氧化硫穩(wěn)定性較好的原位骨架摻雜的釩鈦氧化物催化劑。該方法合成的釩鈦氧化物催化劑比普通的釩鈦催化劑具有較強的穩(wěn)定性,較高的比表面積,并且在FCC再生煙氣脫硝中具有較高的反應(yīng)活性及抗SO2的性能。該合成方法簡單,制備周期短,具有較好的應(yīng)用前景。附圖說明圖1為實施例1制備的催化劑V2O5/TiO2的TEM照片圖2為實施例1制備的催化劑V2O5/TiO2的HR-TEM照片圖3為實施例1制備的催化劑V2O5/TiO2的XRD譜圖圖4為實施例1~4制備的催化劑V2O5/TiO2的活性測試圖具體實施方式以下通過具體實施例介紹本發(fā)明的實現(xiàn)和所具有的有益效果,但不應(yīng)據(jù)此對本發(fā)明的實施范圍構(gòu)成任何限定。催化劑的活性測試方法:催化劑壓片后研磨過篩,取40~60目的部分。實驗在連續(xù)流動的固定床反應(yīng)器上進行,具體是將0.4g過篩后的催化劑裝入到石英玻璃管中,管內(nèi)溫度由管式電阻爐和控溫儀進行程序升溫控制?;旌蠚怏w模擬真實煙氣,由其所對應(yīng)的鋼瓶提供。相應(yīng)的混合氣體組成為:CNO=CNH3=1000ppm,CO2=3%,平衡氣為N2,體積空速為16000h-1。進出口NO的濃度值由ThermoFisher42iHLNO分析儀在線檢測。NO轉(zhuǎn)化率的具體計算公式如下:測得的活性結(jié)果如附圖4所示。實施例11%V2O5/TiO2催化劑的制備將1gP123溶解到20g乙醇中稱為a液,將0.0422g偏釩酸銨溶解到1.4g的HCl和0.46g的44%的H2SO4稱為b液,將b液加入a液中,至于水浴中,強力攪拌,獲得均一透明溶膠。隨后加入15g異丙醇鈦,繼續(xù)強力攪拌一定時間,在相對濕度為50-60%下40℃空氣中靜置2天,形成的薄膜在100℃干燥2天,在氮氣氛中350℃氣氛下處理3h,隨后在空氣中450攝氏度焙燒6h。圖1為實施例1制備的催化劑V2O5/TiO2的TEM照片,由圖中顯示,制備的催化劑顆粒粒徑均在5~10nm,粒徑均勻,具有納米粉體形貌,顆粒間存在較大間隙;圖2為實施例1制備的催化劑V2O5/TiO2的HR-TEM照片,由圖中可以看到原子條紋相,條紋密集均勻;圖3為實施例1制備的催化劑V2O5/TiO2的XRD譜圖,結(jié)果顯示,合成的催化劑顯示為純銳鈦礦晶型,且結(jié)晶度較高,沒有發(fā)現(xiàn)氧化釩的衍射峰,可能是由于釩的負載量較少,且分散均勻。圖4為實施例1~4制備的催化劑V2O5/TiO2的活性測試圖,結(jié)果顯示當(dāng)V2O5負載量為1%時,催化劑的催化活性表現(xiàn)出最佳效果。最高脫硝率能達到95.4%,在300~450℃都能保持80%以上的轉(zhuǎn)化率。實施例20.8%V2O5/TiO2催化劑的制備將1gP123溶解到20g乙醇中稱為a液,將0.0338g偏釩酸銨溶解到1.4g的HCl和0.46g的44%的H2SO4稱為b液,將b液加入a液中,至于水浴中,強力攪拌,獲得均一透明溶膠。隨后加入15g異丙醇鈦,繼續(xù)強力攪拌一定時間,在相對濕度為50-60%下40℃空氣中靜置2天,形成的薄膜在100℃干燥2天,在氮氣氛中350℃氣氛下處理3h,隨后在空氣中450攝氏度焙燒6h。實施例31.2%V2O5/TiO2催化劑的制備將1gP123溶解到20g乙醇中稱為a液,將0.0506g偏釩酸銨溶解到1.4g的HCl和0.46g的44%的H2SO4稱為b液,將b液加入a液中,至于水浴中,強力攪拌,獲得均一透明溶膠。隨后加入15g異丙醇鈦,繼續(xù)強力攪拌一定時間,在相對濕度為50-60%下40℃空氣中靜置2天,形成的薄膜在100℃干燥2天,在氮氣氛中350℃氣氛下處理3h,隨后在空氣中450攝氏度焙燒6h。實施例41.4%V2O5/TiO2催化劑的制備將1gP123溶解到20g乙醇中稱為a液,將0.0591g偏釩酸銨溶解到1.4g的HCl和0.46g的44%的H2SO4稱為b液,將b液加入a液中,至于水浴中,強力攪拌,獲得均一透明溶膠。隨后加入15g異丙醇鈦,繼續(xù)強力攪拌一定時間,在相對濕度為50-60%下40℃空氣中靜置2天,形成的薄膜在100℃干燥2天,在氮氣氣氛中350℃氣氛下處理3h,隨后在空氣中450攝氏度焙燒6h。