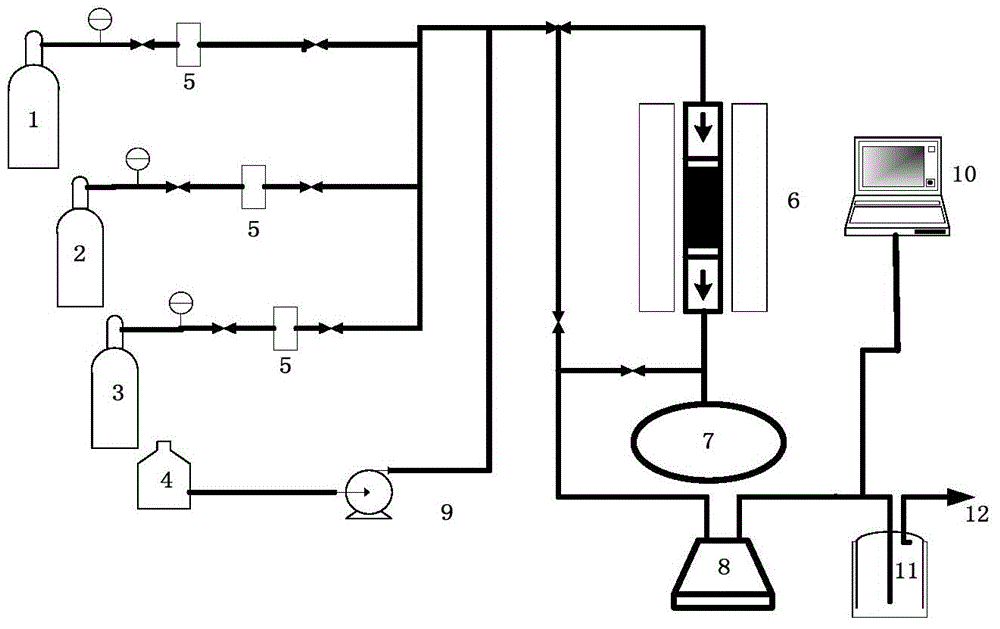
本發(fā)明屬于硫磺回收
技術(shù)領(lǐng)域:
,具體涉及一種用于處理含硫化氫廢氣的催化焚燒催化劑及其制備方法。
背景技術(shù):
:硫化氫是劇毒氣體,不能直接排放到大氣中,空氣中允許硫化氫存在的安全值在10mg/m3以下。硫磺回收裝置的加氫尾氣,經(jīng)胺液吸收凈化后,尾氣中仍然含有少量的硫化氫,含量一般在500ppm以下。因此,硫磺裝置凈化尾氣還必須經(jīng)過焚燒處理,將微量硫化氫轉(zhuǎn)化為二氧化硫后排放。硫磺回收裝置尾氣的焚燒處理分為熱焚燒和催化焚燒兩種工藝,熱焚燒處理溫度較高,一般在600-800℃,消耗大量的燃料和氧,裝置能耗高,溫室氣體CO2的量較大,并經(jīng)常出現(xiàn)溫度過低導(dǎo)致焚燒不完全或溫度過高導(dǎo)致焚燒爐變形等情況。催化焚燒是在較低的溫度(一般200-400℃)及催化劑作用下把硫化氫等硫化物轉(zhuǎn)化為二氧化硫,使用此工藝裝置能耗和操作費用可顯著降低,但裝置建設(shè)成本比熱焚燒工藝略高。多年前燃料價格較低時,催化焚燒工藝的經(jīng)濟(jì)優(yōu)勢不明顯,但隨著國家對節(jié)能降耗、溫室氣體排放的日益重視及燃料氣價格的上漲,催化焚燒的技術(shù)優(yōu)勢已顯現(xiàn)出來。采用催化焚燒與熱焚燒工藝相比,可以節(jié)約近50%的能耗,操作費用也可降低近50%。一個100t/d的硫回收裝置約可節(jié)約1.0467×106kJ/h的熱能,催化劑使用壽命期間累計節(jié)約的燃料費用是所消耗的催化劑費用的10倍以上,當(dāng)裝置規(guī)模更大時,其節(jié)能效果將更加顯著。催化焚燒工藝的技術(shù)關(guān)鍵在于開發(fā)一種活性高、穩(wěn)定性好及耐硫酸鹽化能力強(qiáng)的催化劑,并能在較低溫度下把硫化氫氧化為二氧化硫。CNl049299A公開了一種含硫有機(jī)廢氣焚燒催化劑及其制備方法,該催化劑以硫酸處理改性的天然絲光沸石為載體,V2O5為主要活性組分,少量的鉑、鈀等貴金屬為輔助活性組分。這種催化劑擔(dān)載了貴金屬,成本較高,抗硫中毒能力有限。CNl01306367A公開了一種含硫化氫氣體催化焚燒催化劑及制備方法。催化劑載體為二氧化硅,第一種活性組分為鉍的氧化物,第二種活性組分為鈰、銅或鑭的氧化物。此種催化劑可以用于各種含硫化氫廢氣的催化焚燒處理,適宜條件下硫化氫的氧化率高于99%,二氧化硫生成率高于90%。CNl410149A公開了一種氣體中硫化氫的焚燒催化劑及制備和使用方法,該催化劑的載體為氧化硅,活性組分為鐵和釩的氧化物。技術(shù)實現(xiàn)要素:本發(fā)明的目的是提供一種用于處理含硫化氫廢氣的催化焚燒催化劑,該催化劑具有低溫 活性高、活性穩(wěn)定性好及耐硫酸鹽化能力強(qiáng)的特點;本發(fā)明同時提供了用于處理含硫化氫廢氣的催化焚燒催化劑的制備方法,科學(xué)合理、簡單易行。本發(fā)明所述的用于處理含硫化氫廢氣的催化焚燒催化劑,包括活性組分、助劑和載體,以鐵、釩和鈰的氧化物為活性組分,以氧化鈣為助劑,以二氧化硅和氧化鈦為載體。以質(zhì)量百分比計,催化劑各組分含量如下:所述的鐵的氧化物為氧化鐵,釩的氧化物為五氧化二釩,鈰的氧化物為氧化鈰。所述的鐵的氧化物和釩的氧化物的質(zhì)量比為4:1-1:4,優(yōu)選為1:1。所述的氧化鈣的含量優(yōu)選為1%。催化劑的活性組份為鐵、釩和鈰的氧化物,鐵的氧化物為氧化鐵,氧化鐵含量占催化劑質(zhì)量含量1-10%,優(yōu)選為4-7%,氧化鐵以硝酸鐵、檸檬酸鐵銨、氯化鐵等可溶性鐵鹽的形式加入;釩的氧化物為五氧化二釩,五氧化二釩含量占催化劑質(zhì)量含量1-10%,優(yōu)選為4-7%,五氧化二釩以偏釩酸銨、草酸釩等形式加入;鈰的氧化物為氧化鈰,氧化鈰含量占催化劑質(zhì)量含量0.1-2%,優(yōu)選為0.5-1.5%,氧化鈰以硝酸鈰、氯化鈰等形式加入。本發(fā)明所述的用于處理含硫化氫廢氣的催化焚燒催化劑的制備方法,步驟如下:(1)催化劑的載體采用擠出成型法制備將二氧化硅粉、偏鈦酸、助劑、擴(kuò)孔劑、粘結(jié)劑和水一起混捏后,經(jīng)擠條、干燥、焙燒而制成載體;(2)催化劑采用浸漬法制備載體經(jīng)活性組分浸漬液浸漬后,進(jìn)一步經(jīng)干燥、焙燒制成用于處理含硫化氫廢氣的催化焚燒催化劑。步驟(1)中所述的二氧化硅粉為氣相法二氧化硅,SiO2≥99%,比表面≥200m2/g,優(yōu)選比表面≥300m2/g。步驟(1)中所述的偏鈦酸指標(biāo):偏鈦酸中SO42-≤4%,TiO2≥75%。步驟(1)中所述的擴(kuò)孔劑為聚乙烯醇、聚丙烯酰胺、田菁粉、檸檬酸或淀粉中的一種或幾種,優(yōu)選田菁粉。步驟(1)中所述的粘結(jié)劑為醋酸、檸檬酸、草酸或硝酸中的一種,優(yōu)選硝酸。步驟(1)中所述的焙燒溫度為400-700℃,優(yōu)選為500℃;焙燒時間為2-6小時。步驟(2)中所述的焙燒溫度為300-700℃,優(yōu)選為500℃;焙燒時間為2-6小時。催化劑外觀為φ3條形。催化劑采用等體積浸漬法制備。本發(fā)明所述的用于處理含硫化氫廢氣的催化焚燒催化劑的制備方法,具體步驟如下:(1)載體的制備選取氣相法二氧化硅粉(比表面≥300m2/g),偏鈦酸、氧化鈣、水、粘結(jié)劑、擴(kuò)孔劑加入捏合機(jī)。上述混合物經(jīng)捏合后,使用直徑為ф3mm條型孔板擠條成型,于110-150℃烘干2-4小時,于400-700℃焙燒2-6小時,可制成載體。載體比表面應(yīng)大于200m2/g,用N2吸附法測定所制備載體的比表面積。(2)半成品催化劑的制備取一定量的去離子水,在不斷攪拌下加入所需量的可溶性鐵鹽及鈰鹽,使之形成穩(wěn)定的溶液,攪拌至完全溶解,定容即得活性組分浸漬液。取一定量的上述共浸液,浸漬載體10分鐘-3小時,最好是0.5-1小時,于110-150℃烘干2-6小時。(3)催化劑的制備取一定量的去離子水,加熱到60℃以上,在不斷攪拌條件下將草酸溶解到水中。然后將偏釩酸銨緩慢加入到草酸溶液中,偏釩酸銨與草酸的摩爾比為1:4,攪拌生成穩(wěn)定溶液,定容生成浸漬液,將半成品催化劑進(jìn)行浸漬,浸漬時間10分鐘-3小時,最好是0.5-1小時,在110-150℃烘干2-6小時,300-700℃焙燒2-6小時,即得本發(fā)明的催化劑。本發(fā)明催化劑可用于處理石油煉制、天然氣凈化及煤化工等行業(yè)產(chǎn)生的含硫化氫廢氣,降低裝置的能耗。本發(fā)明與現(xiàn)有技術(shù)相比,具有如下有益效果:采用本發(fā)明制備的催化劑具有低溫活性高、活性穩(wěn)定性好及耐硫酸鹽化能力強(qiáng)等優(yōu)點。使用本催化劑在一定條件下硫化氫轉(zhuǎn)化率≥99%、二氧化硫生成率≥96%,該催化劑可滿足采用催化焚燒工藝處理含硫化氫廢氣裝置的技術(shù)要求,可降低裝置的能耗,具有顯著的經(jīng)濟(jì)效益和社會效益。附圖說明圖1是本發(fā)明催化劑制備工藝流程圖;圖2是硫磺微反評價裝置工藝流程圖;圖中:1、氮氣;2、硫化氫;3、氧氣;4、水;5、質(zhì)量流量計;6、反應(yīng)器;7、積硫器; 8、冷阱;9、水泵;10、自控系統(tǒng);11、堿液罐;12、尾氣排空。具體實施方式以下結(jié)合實施例對本發(fā)明做進(jìn)一步描述。實施例1將200克氣相法二氧化硅(比表面積為380m2/g,SiO2≥99%)、75克偏鈦酸(SO42-為3.8%,TiO2為78%)、3克氧化鈣、4克田菁粉、30克硝酸,300克去離子水混合均勻,在擠條機(jī)上擠出成型,在120℃干燥4小時,在500℃焙燒4小時,由此制得的載體比表面積為295m2/g。將74.3克Fe(NO3)3﹒9H2O、7.8克Ce(NO3)3.6H2O加入到180克去離子水中,混合均勻,用得到的溶液浸漬上步制得的載體,浸漬時間為2個小時,在120℃干燥4小時制得半成品催化劑。取200ml去離子水加熱到70℃,將59克草酸(C2H2O4)溶入去離子水中形成草酸溶液,再將19.2克NH4VO3加入草酸溶液中充分反應(yīng)生成浸漬液,用浸漬液浸漬半成品催化劑,浸漬時間為2個小時,在120℃干燥4小時,在500℃下焙燒4小時制得成品催化劑。由此制得的催化劑中氧化鐵含量占催化劑質(zhì)量含量5%,五氧化二釩含量占催化劑質(zhì)量含量5%,氧化鈰含量占催化劑質(zhì)量含量1%,氧化鈦含量占催化劑質(zhì)量含量20%。實施例2將202克氣相法二氧化硅(比表面積為380m2/g,SiO2≥99%)、75克偏鈦酸(SO42-為3.8%,TiO2為78%)、3克氧化鈣、4克田菁粉、30克硝酸,300克去離子水混合均勻,在擠條機(jī)上擠出成型,在120℃干燥4小時,在500℃焙燒4小時,由此制得的載體比表面積為295m2/g。將74.3克Fe(NO3)3﹒9H2O、3.9克Ce(NO3)3.6H2O加入到180克去離子水中,混合均勻,用得到的溶液浸漬上步制得的載體,浸漬時間為2個小時,在120℃干燥4小時制得半成品催化劑。取200ml去離子水加熱到70℃,將59克草酸(C2H2O4)溶入去離子水中形成草酸溶液,再將19.2克NH4VO3加入草酸溶液中充分反應(yīng)生成浸漬液,用浸漬液浸漬半成品催化劑,浸漬時間為2個小時,在120℃干燥4小時,在500℃下焙燒4小時制得成品催化劑。由此制得的催化劑中氧化鐵含量占催化劑質(zhì)量含量5%,五氧化二釩含量占催化劑質(zhì)量含量5%,氧化鈰含量占催化劑質(zhì)量含量0.5%,氧化鈦含量占催化劑質(zhì)量含量20%。實施例3將170克氣相法二氧化硅(比表面積為380m2/g,SiO2≥99%)、113克偏鈦酸(SO42-為3.8%,TiO2為78%)、3克氧化鈣、4克田菁粉、30克硝酸,300克去離子水混合均勻,在擠條機(jī)上擠出成型,在120℃干燥4小時,在500℃焙燒4小時,由此制得的載體比表面積為 276m2/g。將74.3克Fe(NO3)3﹒9H2O、3.7.8克Ce(NO3)3.6H2O加入到180克去離子水中,混合均勻,用得到的溶液浸漬上步制得的載體,浸漬時間為2個小時,在120℃干燥4小時制得半成品催化劑。取200ml去離子水加熱到70℃,將59克草酸(C2H2O4)溶入去離子水中形成草酸溶液,再將19.2克NH4VO3加入草酸溶液中充分反應(yīng)生成浸漬液,用浸漬液浸漬半成品催化劑,浸漬時間為2個小時,在120℃干燥4小時,在500℃下焙燒4小時制得成品催化劑。由此制得的催化劑中氧化鐵含量占催化劑質(zhì)量含量5%,五氧化二釩含量占催化劑質(zhì)量含量5%,氧化鈰含量占催化劑質(zhì)量含量1%,氧化鈦含量占催化劑質(zhì)量含量30%。實施例4將230克氣相法二氧化硅(比表面積為380m2/g,SiO2≥99%)、38克偏鈦酸(SO42-為3.8%,TiO2為78%)、3克氧化鈣、4克田菁粉、30克硝酸,300克去離子水混合均勻,在擠條機(jī)上擠出成型,在120℃干燥4小時,在500℃焙燒4小時,由此制得的載體比表面積為308m2/g。將74.3克Fe(NO3)3﹒9H2O、7.8克Ce(NO3)3.6H2O加入到180克去離子水中,混合均勻,用得到的溶液浸漬上步制得的載體,浸漬時間為2個小時,在120℃干燥4小時制得半成品催化劑。取200ml去離子水加熱到70℃,將59克草酸溶入去離子水中形成草酸溶液,再將19.2克NH4VO3加入草酸溶液中充分反應(yīng)生成浸漬液,用浸漬液浸漬半成品催化劑,浸漬時間為2個小時,在120℃干燥4小時,在500℃下焙燒4小時制得成品催化劑。由此制得的催化劑中氧化鐵含量占催化劑質(zhì)量含量5%,五氧化二釩含量占催化劑質(zhì)量含量5%,氧化鈰含量占催化劑質(zhì)量含量1%,氧化鈦含量占催化劑質(zhì)量含量10%。實施例5將193克氣相法二氧化硅(比表面積為380m2/g,SiO2≥99%)、75克偏鈦酸(SO42-為3.8%,TiO2為78%)、3克氧化鈣、4克田菁粉、30克硝酸,300克去離子水混合均勻,在擠條機(jī)上擠出成型,在120℃干燥4小時,在500℃焙燒4小時,由此制得的載體比表面積為295m2/g。將149克Fe(NO3)3﹒9H2O、7.8克Ce(NO3)3.6H2O加入到180克去離子水中,混合均勻,用得到的溶液浸漬上步制得的載體,浸漬時間為2個小時,在120℃干燥4小時制得半成品催化劑。取200ml去離子水加熱到70℃,將30克草酸溶入去離子水中形成草酸溶液,再將9.6克NH4VO3加入草酸溶液中充分反應(yīng)生成浸漬液,用浸漬液浸漬半成品催化劑,浸漬時間為2個小時,在120℃干燥4小時,在500℃下焙燒4小時制得成品催化劑。由此制得的催化劑中氧化鐵含量占催化劑質(zhì)量含量10%,五氧化二釩含量占催化劑質(zhì)量含量2.5%, 氧化鈰含量占催化劑質(zhì)量含量1%,氧化鈦含量占催化劑質(zhì)量含量20%。實施例6將193克氣相法二氧化硅(比表面積為380m2/g,SiO2≥99%)、75克偏鈦酸(SO42-為3.8%,TiO2為78%)、3克氧化鈣、4克田菁粉、30克硝酸,300克去離子水混合均勻,在擠條機(jī)上擠出成型,在120℃干燥4小時,在500℃焙燒4小時,由此制得的載體比表面積為295m2/g。將37.2克Fe(NO3)3﹒9H2O、7.8克Ce(NO3)3.6H2O加入到180克去離子水中,混合均勻,用得到的溶液浸漬上步制得的載體,浸漬時間為2個小時,在120℃干燥4小時制得半成品催化劑。取200ml去離子水加熱到70℃,將118克草酸溶入去離子水中形成草酸溶液,再將38.4克NH4VO3加入草酸溶液中充分反應(yīng)生成浸漬液,用浸漬液浸漬半成品催化劑,浸漬時間為2個小時,在120℃干燥4小時,在500℃下焙燒4小時制得成品催化劑。由此制得的催化劑中氧化鐵含量占催化劑質(zhì)量含量2.5%,五氧化二釩含量占催化劑質(zhì)量含量10%,氧化鈰含量占催化劑質(zhì)量含量1%,氧化鈦含量占催化劑質(zhì)量含量20%。實施例7將197克氣相法二氧化硅(比表面積為380m2/g,SiO2≥99%)、75克偏鈦酸(SO42-為3.8%,TiO2為78%)、3克氧化鈣、4克田菁粉、30克硝酸,300克去離子水混合均勻,在擠條機(jī)上擠出成型,在120℃干燥4小時,在500℃焙燒4小時,由此制得的載體比表面積為295m2/g。將74.3克Fe(NO3)3﹒9H2O、15.6克Ce(NO3)3.6H2O加入到180克去離子水中,混合均勻,用得到的溶液浸漬上步制得的載體,浸漬時間為2個小時,在120℃干燥4小時制得半成品催化劑。取200ml去離子水加熱到70℃,將59克草酸(C2H2O4)溶入去離子水中形成草酸溶液,再將19.2克NH4VO3加入草酸溶液中充分反應(yīng)生成浸漬液,用浸漬液浸漬半成品催化劑,浸漬時間為2個小時,在120℃干燥4小時,在500℃下焙燒4小時制得成品催化劑。由此制得的催化劑中氧化鐵含量占催化劑質(zhì)量含量5%,五氧化二釩含量占催化劑質(zhì)量含量5%,氧化鈰含量占催化劑質(zhì)量含量2%,氧化鈦含量占催化劑質(zhì)量含量20%。實施例8將200克氣相法二氧化硅(比表面積為350m2/g,SiO2≥99%)、75克偏鈦酸(SO42-為3.8%,TiO2為78%)、3克氧化鈣、4克田菁粉、30克硝酸,300克去離子水混合均勻,在擠條機(jī)上擠出成型,在120℃干燥4小時,在500℃焙燒4小時,由此制得的載體比表面積為267m2/g。將74.3克Fe(NO3)3﹒9H2O、7.8克Ce(NO3)3.6H2O加入到180克去離子水中,混合均 勻,用得到的溶液浸漬上步制得的載體,浸漬時間為2個小時,在120℃干燥4小時制得半成品催化劑。取200ml去離子水加熱到70℃,將59克草酸(C2H2O4)溶入去離子水中形成草酸溶液,再將19.2克NH4VO3加入草酸溶液中充分反應(yīng)生成浸漬液,用浸漬液浸漬半成品催化劑,浸漬時間為2個小時,在120℃干燥4小時,在500℃下焙燒4小時制得成品催化劑。由此制得的催化劑中氧化鐵含量占催化劑質(zhì)量含量5%,五氧化二釩含量占催化劑質(zhì)量含量5%,氧化鈰含量占催化劑質(zhì)量含量1%,氧化鈦含量占催化劑質(zhì)量含量20%。實施例9將200克氣相法二氧化硅(比表面積為380m2/g,SiO2≥99%)、75克偏鈦酸(SO42-為3.8%,TiO2為78%)、3克氧化鈣、4克田菁粉、30克硝酸,300克去離子水混合均勻,在擠條機(jī)上擠出成型,在120℃干燥4小時,在500℃焙燒4小時,由此制得的載體比表面積為295m2/g。將89.8克檸檬酸鐵銨、7.8克Ce(NO3)3.6H2O加入到180克去離子水中,混合均勻,用得到的溶液浸漬上步制得的載體,浸漬時間為2個小時,在120℃干燥4小時制得半成品催化劑。取200ml去離子水加熱到70℃,將59克草酸(C2H2O4)溶入去離子水中形成草酸溶液,再將19.2克NH4VO3加入草酸溶液中充分反應(yīng)生成浸漬液,用浸漬液浸漬半成品催化劑,浸漬時間為2個小時,在120℃干燥4小時,在500℃下焙燒4小時制得成品催化劑。由此制得的催化劑中氧化鐵含量占催化劑質(zhì)量含量5%,五氧化二釩含量占催化劑質(zhì)量含量5%,氧化鈰含量占催化劑質(zhì)量含量1%,氧化鈦含量占催化劑質(zhì)量含量20%。對比例1將203克氣相法二氧化硅(比表面積為380m2/g,SiO2≥99%)、75克偏鈦酸(SO42-為3.8%,TiO2為78%)、3克氧化鈣、4克田菁粉、30克硝酸,300克去離子水混合均勻,在擠條機(jī)上擠出成型,在120℃干燥4小時,在500℃焙燒4小時,由此制得的載體比表面積為295m2/g。將74.3克Fe(NO3)3﹒9H2O加入到180克去離子水中,混合均勻,用得到的溶液浸漬上步制得的載體,浸漬時間為2個小時,在120℃干燥4小時制得半成品催化劑。取200ml去離子水加熱到70℃,將59克草酸(C2H2O4)溶入去離子水中形成草酸溶液,再將19.2克NH4VO3加入草酸溶液中充分反應(yīng)生成浸漬液,用浸漬液浸漬半成品催化劑,浸漬時間為2個小時,在120℃干燥4小時,在500℃下焙燒4小時制得成品催化劑。由此制得的催化劑中氧化鐵含量占催化劑質(zhì)量含量5%,五氧化二釩含量占催化劑質(zhì)量含量5%,氧化鈦含量占催化劑質(zhì)量含量20%。對比例2將259克氣相法二氧化硅(比表面積為380m2/g,SiO2≥99%)、3克氧化鈣、4克田菁粉、30克硝酸,300克去離子水混合均勻,在擠條機(jī)上擠出成型,在120℃干燥4小時,在500℃焙燒4小時,由此制得的載體比表面積為316m2/g。將74.3克Fe(NO3)3﹒9H2O、7.8克Ce(NO3)3.6H2O加入到180克去離子水中,混合均勻,用得到的溶液浸漬上步制得的載體,浸漬時間為2個小時,在120℃干燥4小時制得半成品催化劑。取200ml去離子水加熱到70℃,將59克草酸(C2H2O4)溶入去離子水中形成草酸溶液,再將19.2克NH4VO3加入草酸溶液中充分反應(yīng)生成浸漬液,用浸漬液浸漬半成品催化劑,浸漬時間為2個小時,在120℃干燥4小時,在500℃下焙燒4小時制得成品催化劑。由此制得的催化劑中氧化鐵含量占催化劑質(zhì)量含量5%,五氧化二釩含量占催化劑質(zhì)量含量5%,氧化鈰含量占催化劑質(zhì)量含量1%。實施例10在硫磺微反評價裝置上對實施例1至實施例9、對比例1至對比例2制備的催化劑進(jìn)行活性評價,結(jié)果見表1。微反裝置的反應(yīng)器由內(nèi)徑為20mm的不銹鋼管制成,反應(yīng)器放置在恒溫箱內(nèi)。催化劑裝填量為10ml,上部裝填相同粒度的石英砂進(jìn)行混合預(yù)熱。采用日本島津GC—2014氣相色譜儀在線分析反應(yīng)器入口及出口氣體中H2S、SO2和O2的含量,采用GDX—301擔(dān)體分析硫化物,采用5A分子篩分析O2含量,柱溫120℃,采用熱導(dǎo)檢測器,以氫氣作載氣,柱后流速25ml/min。以2H2S+3O2→2SO2+2H2O作為指標(biāo)反應(yīng),考察催化劑的活性,入口氣體體積組成:H2S1%、O24%、H2O30%,其余為N2,氣體體積空速為5000h-1,反應(yīng)溫度為290℃。根據(jù)下式計算硫化氫的轉(zhuǎn)化率和二氧化硫的生成率:(1)H2S轉(zhuǎn)化率ηAct=M0-M1M0×100%]]>其中:M0—原料氣中干基硫化氫體積百分?jǐn)?shù)。M1—尾氣中干基硫化氫體積百分?jǐn)?shù)。(2)SO2生成率ηYld=C1M0-M1×100%]]>其中:M0—原料氣中干基硫化氫體積百分?jǐn)?shù)。M1—尾氣中干基硫化氫體積百分?jǐn)?shù)。C1—尾氣中干基二氧化硫體積百分?jǐn)?shù)。表1催化劑活性數(shù)據(jù)催化劑轉(zhuǎn)化率ηAct%生成率ηYld%實施例199.999.0實施例299.998.3實施例399.299.3實施例499.998.3實施例599.998.1實施例699.099.3實施例799.799.1實施例899.898.8實施例999.998.9對比例199.795.3對比例299.694.8實施例11:以實施例1制備的催化劑和通過國外同類催化劑A進(jìn)行了不同溫度下催化活性比較,結(jié)果見表2。表2催化劑活性比較*評價條件為入口氣體組成H2S1%、O24%、H2O30%,其余N2,氣體體積空速5000h-1。從表2中數(shù)據(jù)可以看出,實施例1制備的催化劑的催化性能優(yōu)于國外同類催化劑A,尤其低溫催化活性明顯高于進(jìn)口催化劑。實施例12對實施例1制備的催化劑和國外同類催化劑A進(jìn)行了苛刻老化試驗,苛刻老化試驗可模擬催化劑發(fā)生水熱老化及硫酸鹽化的情形,相當(dāng)于工業(yè)裝置連續(xù)運(yùn)行了3年的時間。苛刻老化條件:(1)催化劑550℃焙燒2小時;(2)空速1000h-1,溫度260℃,氣體組成(v/v)SO2:空氣:水蒸汽=1:2.5:6.5對催化劑進(jìn)行處理,時間2小時。將苛刻老化后的催化劑進(jìn)行了活性評價,評價條件如下:入口氣體組成H2S1%、O24%、 H2O30%,其余N2,反應(yīng)溫度290℃,氣體體積空速5000h-1,評價數(shù)據(jù)見表3。表3苛刻老化試驗后催化劑活性比較由表3中數(shù)據(jù)可以看出,催化劑經(jīng)苛刻老化處理后,實施例1制備的催化劑的H2S轉(zhuǎn)化率和SO2生成率略有下降,而國外同類催化劑A均發(fā)生了不同程度的明顯下降,這說明本發(fā)明催化劑具有活性穩(wěn)定性好及耐硫酸鹽化能力強(qiáng)的特點。當(dāng)前第1頁1 2 3