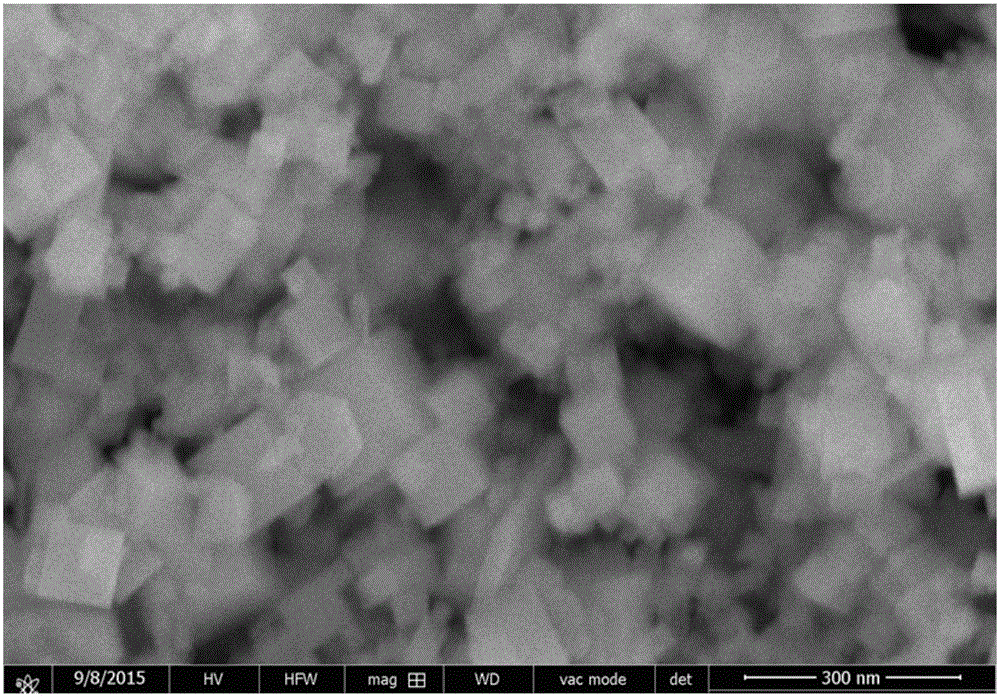
本發(fā)明涉及一種鈰釔復合氧化物擔載鉑的催化劑及其制備方法和應用,該催化劑用于凈化機動車排放炭煙顆粒物,屬于催化氧化
技術領域:
。
背景技術:
:柴油發(fā)動機相比于汽油發(fā)動機具有高的燃油效率、低CO2排放、高耐久性的特點,因而對現(xiàn)代社會具有重要的作用,被廣泛應用在機動車、船只以及大型機械上。然而柴油發(fā)動機的主要排放物碳煙顆粒物(PM)對大氣環(huán)境造成的污染日趨嚴重,嚴重威脅生態(tài)環(huán)境和人體健康。機動車排放的污染物是城市大氣PM2.5的主要來源之一,尤其是在大城市中,由機動車所排放的顆粒物、VOC、多環(huán)芳烴、SO2、NOx以及金屬離子等為PM2.5的主要組成成份。因此,降低PM排放是柴油車尾氣催化凈化的重要任務,開展這方面的研究具有重要的環(huán)境保護意義。提高機動車尾氣排放的顆粒物(PM)凈化用催化劑的活性,降低顆粒物的燃燒溫度,從而使顆粒物捕集器能夠長時間連續(xù)工作,是減少機動車排放顆粒物最直接的方法。多類催化劑已被研究證實對炭煙催化燃燒具有良好的效果,如堿金屬氧化物、過渡金屬氧化物、鈣鈦礦型氧化物、擔載貴金屬的復合氧化物以及鈰基氧化物。貴金屬具有最佳的催化活性,一般將其以納米顆粒的形式分散于載體上來合成催化劑。鈰基氧化物催化劑中的鈰釔復合氧化物具有良好的氧化還原能力,鈰離子能在Ce3+和Ce4+兩種氧化態(tài)間靈活轉化,具有良好的儲放氧作用,在催化反應中起到了氧緩沖器的作用。另外,向CeO2的骨架結構中摻雜過渡金屬元素能提高鈰基催化劑的熱穩(wěn)定性以及氧空缺位的數(shù)量,因而能進一步提高催化劑的反應活性。由于炭煙顆粒催化燃燒消除反應是一個氣-固(顆粒物)-固(催化劑)三相復雜的深度氧化反應過程,催化劑活性的提高不僅與氧化物催化劑本身的氧化還原性能密切相關,同時還與固體催化劑和PM的接觸程度密切相關。同一活性組分的催化劑,與顆粒物的接觸能力越高,活性越好。利用合適的方法調變鈰釔復合氧化物載體的形貌結構具有重要的意義。不同形貌的鈰釔復合氧化物載體能夠暴露不同的活性晶面,形成不同的活性物種,因而具有不同的反應活性。金屬氧化物的特定晶面還能影響表面氧空位的形成能,理論計算結果表明,鈰釔復合氧化物的{111},{110}和{100}晶面具有不同的穩(wěn)定性和氧空位形成能,并且與吸附分子間的相互作用也大不相同。目前已存在的有關擔載貴金屬催化劑的制備方法有浸漬法、共沉淀法、沉積沉淀法、離子交換法、光化學沉積法、化學蒸發(fā)沉積法、金屬有機絡合物固載法及共濺鍍法等。這些方法各有特點,但也存在著貴金屬顆粒不易分散均勻、擔載顆粒尺寸難以保持均一的共性缺點。例如,貴金屬顆粒不易均勻擔載在大孔載體的內表面上,使得塊體催化劑貴金屬顆粒尺寸分布不均,影響催化活性的評價;催化劑使用過程中,高溫的條件下,貴金屬活性組分易于團聚造成催化劑活性下降,催化劑的穩(wěn)定性降低;貴金屬的用量較高,造成目前機動車尾氣凈化裝置的價格昂貴。技術實現(xiàn)要素:為解決上述技術問題,本發(fā)明的目的是提供一種鈰釔復合氧化物擔載鉑的催化劑及其制備方法,該催化劑能夠提高對機動車排放的顆粒物催化氧化活性,尤其是低溫的催化活性以滿足機動車冷啟動的要求。該方法簡單易行,貴金屬的用量少。為了達到上述目的,本發(fā)明提供了一種鈰釔復合氧化物擔載鉑的催化劑,該催化劑以納米立方體結構的鈰釔復合氧化物為載體,以鉑為活性擔載組分,鉑以單原子或納米顆粒的形式擔載在鈰釔復合氧化物的表面。在上述催化劑中,優(yōu)選地,所述鈰釔復合氧化物中鈰的摩爾比為80-99%,更優(yōu)選為85-95%,鈰釔復合氧化物的納米立方體結構的邊長為30-200nm,優(yōu)選為50nm;在上述催化劑中,優(yōu)選地,鉑納米顆粒的尺寸小于10nm。在上述催化劑中,優(yōu)選地,鉑活性組分形貌結構隨著鉑的負載量的變化而變化,以鈰釔復合氧化物的總重量為100%計,鉑的負載量為0.001-1%時,鉑以單原子的形式存在;所述鉑的負載量為1-5%時,鉑以納米顆粒的形式存在。在上述催化劑中,優(yōu)選地,鈰釔復合氧化物的制備可以采用水熱法,更優(yōu)選地,該方法包括以下步驟:a、將鈰前驅體鹽和釔前驅體鹽溶解至水中,得到鹽溶液,所述鈰前驅體鹽和釔前驅體鹽的摩爾比為4:(0.01-1);b、配置質量濃度為1.0-5g/mL的氫氧化鈉溶液;c、將所述氫氧化鈉溶液滴加至攪拌狀態(tài)的所述鹽溶液中,滴加完成后繼續(xù)攪拌,得到混合液,在所述混合液中,所述氫氧化鈉的濃度為5-7mol/L,所述鈰前驅體鹽和釔前驅體鹽的濃度總和為0.3-0.6mol/L;d、將混合液進行晶化,然后降溫至室溫,得到混合物;e、將混合物離心或過濾得到沉淀物,所述沉淀物再經(jīng)過洗滌、干燥得到納米立方體結構的鈰釔復合氧化物。在上述催化劑中,優(yōu)選地,鈰前驅體鹽包括但不限于硝酸亞鈰和氯化亞鈰,釔前驅體鹽包括但不限于硝酸釔。在上述催化劑中,優(yōu)選地,步驟c中,滴加氫氧化鈉完成后繼續(xù)攪拌1h。在上述催化劑中,優(yōu)選地,步驟d中,上述混合液可以轉移至100mL的水熱晶華釜中進行晶化,晶化的溫度為160-200℃,晶化的時間為24h-48h,需要注意的是,此步驟切勿焙燒,且干燥溫度不高于150℃,因為,焙燒或溫度過高將改變載體表面的性質,特別是失去表面羥基,而無法吸附鉑。在上述催化劑中,優(yōu)選地,步驟e中,離心洗滌次數(shù)為3-5次;干燥的溫度為40-80℃,干燥的時間為2h-24h。本發(fā)明還提供上述鈰釔復合氧化物擔載鉑的催化劑的制備方法,該方法包括以下步驟:a、將鈰釔復合氧化物與水混合,并持續(xù)攪拌,得到載體液;b、將鉑前驅體與水配置成鉑前驅體溶液;c、將上述鉑前驅體溶液滴加到所述載體液中,滴加完成后繼續(xù)攪拌,得到混合液;d、將上述混合液在攪拌條件下干燥、焙燒后,得到鈰釔復合氧化物擔載鉑的催化劑。在上述制備方法中,優(yōu)選地,鈰釔復合氧化物與水的質量比為(0.1-2):100;鉑前驅體溶液的濃度為0.01-5g/L;鉑前驅體溶液的滴加速度為0.05-1mL/min。在上述制備方法中,優(yōu)選地,鉑前驅體包括但不限于四氯化鉑和/或二氯亞鉑。在上述制備方法中,優(yōu)選地,步驟d中,干燥的溫度為50-100℃,干燥的時間為2h-24h;所述焙燒的溫度為200-600℃,焙燒的時間為1h-6h。在上述制備方法中,優(yōu)選地,步驟c中,滴加鉑前驅體溶液完成后繼續(xù)攪拌2h-4h。根據(jù)本發(fā)明的具體實施方案,上述鈰釔復合氧化物擔載鉑的催化劑的制備方法可以按照如下具體步驟進行:a、將1g上述納米立方體結構鈰釔復合氧化物載體與50mL水混合,并持續(xù)攪拌,得到載體液;b、配置濃度為5g/L的四氯化鉑溶液;c、將7mL四氯化鉑溶液以1mL/min的速度滴加到上述載體液中,滴加完成后繼續(xù)攪拌2h,得到混合液;d、將上述混合液升溫至80℃,在攪拌條件下將水分蒸干,然后100℃干燥12h后,在500℃下焙燒2h,得到鈰釔復合氧化物擔載鉑的催化劑。本發(fā)明制備的鈰釔復合氧化物擔載鉑的催化劑可以應用在炭煙顆粒物的燃燒中,特別是應用在機動車排放的炭煙顆粒物的燃燒中。本發(fā)明的鈰釔復合氧化物擔載鉑的催化劑具有以下優(yōu)點:1、在制備過程中,主要依靠納米立方體鈰釔復合氧化物的表面羥基(OH-)與四價鉑離子(Pt4+)之間的靜電引力,并在納米立方體鈰釔復合氧化物表面形成Pt(OH)4,使Pt以單原子或納米顆粒形態(tài)均勻分散在鈰釔復合氧化物表面。2、以納米立方體結構的鈰釔復合氧化物作為載體,因此,所得到的催化劑長度均勻,粗細一致;另外,相比于納米立方體結構的氧化鈰,鈰釔復合氧化物展示了更高的抗高溫燒結性能。3、本發(fā)明炭煙顆粒物燃燒用催化劑的制備方法簡單易行,制備過程容易控制,同時將貴金屬以單原子分散或納米顆粒的形式負載于納米立方體鈰釔復合氧化物表面,可以大大減少貴金屬的用量。4、該催化劑可以應用于凈化機動車排放的顆粒物。由于該催化劑的納米立方體結構的鈰釔復合氧化物暴露的(100)晶面與鉑單原子或納米顆粒的強相互作用,能夠為催化反應提供更多的活性位點,因此,該催化劑具有更好的催化活性,尤其是低溫的催化活性以滿足機動車冷啟動的要求。附圖說明圖1a為實施例1制備得到的Cube-Ce0.9Y0.1O2的掃描電鏡圖;圖1b為實施例1制備得到的Pt/Cube-Ce0.9Y0.1O2的掃描電鏡圖;圖2a為實施例1制備得到的Pt/Cube-Ce0.9Y0.1O2的透射電鏡圖(50nm);圖2b為實施例1制備得到的Pt/Cube-Ce0.9Y0.1O2的透射電鏡圖(20nm);圖2c為實施例1制備得到的Pt/Cube-Ce0.9Y0.1O2的透射電鏡圖(5nm);圖2d為實施例2制備得到的Pt/Cube-Ce0.9Y0.1O2的透射電鏡圖(5nm);圖3為實施例1制備得到的Cube-Ce0.9Y0.1O2和Pt/Cube-Ce0.9Y0.1O2和實例2制備得到的Pt1/Cube-Ce0.9Y0.1O2的X射線衍射圖譜,圖中,(1)為Cube-Ce0.9Y0.1O2,(2)為Pt/Cube-Ce0.9Y0.1O2,(3)為Pt1/Cube-Ce0.9Y0.1O2;圖4為實施例1制備得到的Cube-Ce0.9Y0.1O2和Pt/Cube-Ce0.9Y0.1O2的活性評價結果圖。具體實施方式為了對本發(fā)明的技術特征、目的和有益效果有更加清楚的理解,現(xiàn)對本發(fā)明的技術方案進行以下詳細說明,但不能理解為對本發(fā)明的可實施范圍的限定。實施例1本實施例提供了一種鈰釔復合氧化物擔載鉑納米顆粒的催化劑的制備方法,該方法包括以下步驟:1、制備納米立方體結構的鈰釔復合氧化物,包括以下步驟:a、將1.49g的硝酸亞鈰和0.16g硝酸釔溶解至5mL水中,得到鈰釔鹽溶液;b、將14.4g的氫氧化鈉用55mL水溶解,得到氫氧化鈉溶液;c、將步驟b得到的氫氧化鈉溶液滴加至攪拌狀態(tài)的步驟a得到的鈰釔鹽溶液中,滴加完成后,繼續(xù)攪拌1h;d、將步驟c得到的混合液轉移至100mL水熱晶華釜中恒溫180℃晶化24h,然后自然降溫至室溫;e、將步驟d得到的混合物離心分離得到沉淀物,再經(jīng)過3次洗滌,80℃干燥12h后得到所述納米立方體結構的鈰釔復合氧化物載體,可以記為Cube-Ce0.9Y0.1O2。2、制備鈰釔復合氧化物擔載鉑的催化劑,包括以下步驟:a、將1.0g上述制備的納米立方體結構的鈰釔復合氧化物載體與50mL水混合,并持續(xù)攪拌,得到載體液;b、配置濃度為5g/L的四氯化鉑溶液;c、將7mL的四氯化鉑溶液以1mL/min的速度滴加到所述載體液中,滴加完成后繼續(xù)攪拌2h,得到混合液,在此過程中,依靠納米立方體鈰釔復合氧化物的表面羥基(OH-)與四價鉑離子(Pt4+)之間的靜電引力,使得Pt離子均勻分散吸附在鈰釔復合氧化物表面;d、在攪拌條件下,將上述混合液100℃干燥12h后,在500℃下焙燒2h,得到鈰釔復合氧化物擔載鉑的催化劑,可以記為Pt/Cube-Ce0.9Y0.1O2。其中,以Cube-Ce0.9Y0.1O2的質量為100%計,Pt的擔載量為4%。將實施例1制備得到的Cube-Ce0.9Y0.1O2和Pt/Cube-Ce0.9Y0.1O2分別進行掃描電鏡分析,通過圖1a-圖1b可以看出,上述制備得到的Cube-Ce0.9Y0.1O2和Pt/Cube-Ce0.9Y0.1O2均為納米立方體狀結構,且擔載鉑納米顆粒沒有破壞納米立方體的結構。將實施例1制備得到的Pt/Cube-Ce0.9Y0.1O2進行透射電鏡(TEM)分析,Pt/Cube-Ce0.9Y0.1O2的低倍、高倍透射電鏡圖分別如圖2a(50nm),圖2b(20nm)和圖2d(5nm)所示;通過圖2a-圖2c可以進一步證明上述制備得到的Pt/Cube-Ce0.9Y0.1O2存在納米立方體狀結構,其長度約為100nm,寬度為15nm,圖中立方體鈰鋯復合氧化物表面的黑色小顆粒物為負載型Pt納米顆粒,由此可見Pt納米顆粒高度分散在鈰釔復合氧化物納米立方體表面,Pt納米顆粒的平均粒徑尺寸大約為4nm。實施例2本實施例提供了一種鈰釔復合氧化物擔載單原子分散的鉑的催化劑的制備方法,該方法包括以下步驟:1、制備納米立方體結構的鈰釔復合氧化物,具體采用水熱合成法,包括以下步驟:a、將1.49g的硝酸亞鈰和0.16g硝酸釔溶解至5mL水中,得到鈰釔鹽溶液;b、將14.4g的氫氧化鈉用55mL水溶解,得到氫氧化鈉溶液;c、將步驟b得到的氫氧化鈉溶液滴加至攪拌狀態(tài)的步驟a得到的鈰釔鹽溶液中,滴加完成后,繼續(xù)攪拌1h;d、將步驟c得到的混合液轉移至100mL水熱晶華釜中恒溫180℃晶化24h,然后自然降溫至室溫;e、將步驟d得到的混合物離心分離得到沉淀物,再經(jīng)過3次洗滌,80℃干燥12h后得到所述納米立方體結構的鈰釔復合氧化物載體,可以記為Cube-Ce0.9Y0.1O2。2、制備鈰釔復合氧化物擔載鉑的催化劑,包括以下步驟:a、將1.0g上述制備的納米立方體結構的鈰釔復合氧化物載體與50mL水混合,并持續(xù)攪拌,得到載體液;b、配置濃度為5g/L的四氯化鉑溶液;c、將2mL的四氯化鉑溶液以1mL/min的速度滴加到所述載體液中,滴加完成后繼續(xù)攪拌2h,得到混合液,在此過程中,依靠納米立方體鈰釔復合氧化物的表面羥基(OH-)與四價鉑離子(Pt4+)之間的靜電引力,使得Pt離子均勻分散吸附在鈰釔復合氧化物表面;d、將上述混合液在攪拌條件下80℃將水分蒸干,然后100℃干燥12h后,在500℃下焙燒2h,得到鈰釔復合氧化物擔載鉑的催化劑,可以記為Pt1/Cube-Ce0.9Y0.1O2。其中,以Cube-Ce0.9Y0.1O2的質量為100%計,Pt的擔載量為1.0wt%。將實施例2制備得到的Pt1/Cube-Ce0.9Y0.1O2進行透射電鏡(TEM)分析,Pt1/Cube-Ce0.9Y0.1O2的低倍、高倍透射電鏡圖分別如圖2d(5nm)所示;通過上述樣品的透射電鏡圖(圖2d)可以進一步證明上述制備得到的Pt1/Cube-Ce0.9Y0.1O2存在納米立方體狀結構,圖2d中沒有觀察到Pt納米顆粒的存在,由此證明,活性組分Pt以單原子形態(tài)分散在鈰釔復合氧化物納米立方體表面。將實施例1制備得到的Cube-Ce0.9Y0.1O2和Pt/Cube-Ce0.9Y0.1O2、實施例2制備得到的Pt1/Cube-Ce0.9Y0.1O2分別進行X射線衍射分析,上述催化劑的X射線衍射譜圖如圖3所示,在圖3中,(1)為Cube-Ce0.9Y0.1O2、(2)為Pt/Cube-Ce0.9Y0.1O2和(3)為Pt1/Cube-Ce0.9Y0.1O2,從圖3中可以看出,圖中(1)、(2)和(3)的衍射峰均為Cube-Ce0.9Y0.1O2的特征衍射峰,沒有出現(xiàn)Pt納米顆粒的衍射峰,該結果表明本發(fā)明制備得到的Pt納米顆粒粒徑尺寸較小,尺寸分布較窄,已經(jīng)超出了XRD儀器的檢測范圍。實施例3本實施例提供了實施例1制備得到的Cube-Ce0.9Y0.1O2和Pt/Cube-Ce0.9Y0.1O2在機動車排放的顆粒物燃燒中的應用,即考察上述催化劑的催化劑活性。催化劑活性的評價方法:使用固定床微型反應器-氣相色譜檢測系統(tǒng)對上述兩種催化劑進行活性評價。應用過程中的具體參數(shù):上述催化劑樣品的用量均為100mg,催化劑與吸附炭的質量比為10:1。具體步驟:將稱量好的上述催化劑和吸附炭置于小燒杯中,用藥匙攪拌均勻,使催化劑與顆粒物松散接觸,將上述催化劑和吸附炭裝入6mm的石英反應管中,其中,控制氣體流量為50mL/min,氣體中NO的體積含量為2000ppm,O2的體積含量為5%,余量為He;升溫速率控制為2℃/min左右。評價方式:催化劑的氧化能力強弱采用吸附炭的燃燒溫度來表示,其中,吸附炭的起燃溫度(T10)、燃燒速率最大時對應的溫度(T50)和燃盡溫度(T90)分別表示顆粒物燃燒完成10%、50%和90%時對應的溫度點,T10、T50、T90的計算方法是對程序升溫氧化反應中,碳黑燃燒產(chǎn)生的CO2與CO的曲線進行積分,CO2與CO積分面積之和的10%、50%、90%的數(shù)值所對應的溫度點即為T10、T50和T90。上述催化劑的活性評價結果如圖4所示,其中,圖4的縱坐標為CO2濃度,橫坐標為溫度,圖4中的(1)和(2)分別為Cube-Ce0.9Y0.1O2和Pt/Cube-Ce0.9Y0.1O2催化機動車排放的炭煙顆粒物,上述催化劑的活性評價數(shù)據(jù)見表1所示,表1中,SCO2m(%)表示二氧化碳的選擇性。表1催化劑T10/℃T50/℃T90/℃SCO2m(%)機動車排放的炭煙顆粒物48258564655.0Cube-Ce0.9Y0.1O240147551090.9Pt/Cube-Ce0.9Y0.1O229837241299.5從表1及圖4可以看出,Cube-Ce0.9Y0.1O2的炭煙燃燒催化活性溫度T10、T50和T90分別為401、475和510。擔載Pt納米顆粒之后,Pt/Cube-Ce0.9Y0.1O2展示了更高的催化活性,T10、T50和T90分別下降為298、372和412℃,這表明Pt納米顆粒能夠大幅度提高催化炭煙燃燒活性。當前第1頁1 2 3