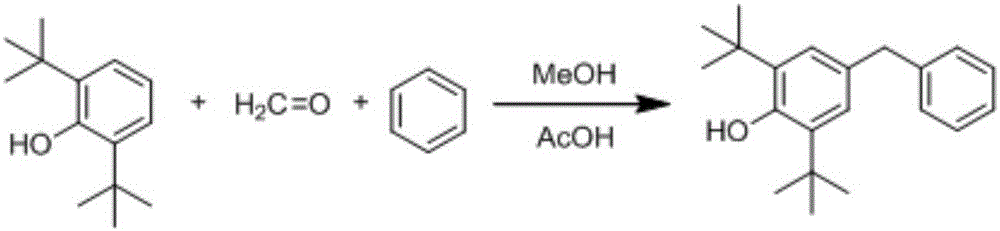
本發(fā)明涉及一種柴油發(fā)動機潤滑油組合物。
背景技術(shù):
:近年來,排放法規(guī)的日益嚴格促使發(fā)動機生產(chǎn)商采用新技術(shù),也促進了內(nèi)燃機油的不斷升級換代,油品在抗氧、分散、清凈和抗磨等各方面性能要求越來越高。現(xiàn)代柴油機功率提高,熱負荷增大,以及采用EGR,使得機油溫度升高,對油品抗氧化能力和高溫清凈性的要求也不斷提高。API柴油發(fā)動機潤滑油規(guī)格中評價其高溫抗氧化能力的發(fā)動機試驗從程序IIIE的64小時,發(fā)展到程序IIIF的80小時,到目前程序IIIG的100小時,而粘度增長的要求從不超過295%降低為275%、150%,對高溫抗氧能力的要求大幅提高。柴油機采用直噴、延遲燃油噴入、高頂環(huán)活塞和尾氣再循環(huán)(EGR)等技術(shù)來滿足高功率、低排放的要求,這些技術(shù)的采用提高了機油中的煙炱含量,容易造成油品黏度增加,堵塞油濾,同時造成缸套活塞環(huán)、閥組等摩擦副的磨損。隨著柴油機油質(zhì)量級別的提高,在保持油品正常黏度的前提下,油中存在的煙炱量越來越高,如在評價煙炱分散性的MackT-8臺架試驗中,從CF-4、CG-4到CH-4、CI-4,油中煙炱量從2.0%、3.8%增加到4.8%。因此,高檔柴油機油的煙炱分散性能要求越來越苛刻。CN100460490C介紹了一種由烷基化二苯胺和酚酯復(fù)配的抗氧劑組分,能較大幅度地提高油品的抗氧化能力。CN96106725公開了一種偶聯(lián)的抗氧型丁二酰亞胺分散劑,是由對苯二酚、鄰苯二酚和對甲酚的一種酚或其混合物將丁二酰亞胺分散劑偶聯(lián)而成,該添加劑具有優(yōu)良的抗氧化性能、熱氧化安定性和分散性。CN200410096315.7公開了一種潤滑油添加劑組合物,該組合物的分散劑采用與CN96106725公開的酚偶聯(lián)的丁二酰亞胺分散劑、硼化丁二酰亞胺分散劑和高分子丁二酰亞胺分散劑復(fù)配,該組合物具有優(yōu)異的煙炱分散性能、良好的抗氧、抗腐蝕性能。CN00107484.9公開了一種含有甲氧酚的抗氧型分散劑,由甲氧酚與多烯多胺縮合后,再與烯基丁二酸酐反應(yīng)而成。該添加劑具有良好的抗氧性、分散性和顏色穩(wěn)定性。CN200410096314.2公開了一種含硼抗氧型分散劑與ZDDP的二元組合物, 該組合物具有良好的抗磨性和分散性。技術(shù)實現(xiàn)要素:本發(fā)明提供了一種柴油發(fā)動機潤滑油組合物及其制備方法、用途。本發(fā)明的柴油發(fā)動機潤滑油組合物,包括以下組分:A>式(I)所示結(jié)構(gòu)的抗氧劑:B>抗氧型聚異丁烯丁二酰亞胺無灰分散劑;C>聚異丁烯單丁二酰亞胺;D>聚異丁烯雙丁二酰亞胺;E>磺酸鹽和硫化烷基酚鹽的混合物;F>二烷基二硫代磷酸鋅;G>主要量的潤滑油基礎(chǔ)油;在本發(fā)明的潤滑油組合物中還可以存在其它添加劑,如降凝劑、黏度指數(shù)改進劑(VM)、抗泡劑等。具體來說,本發(fā)明的柴油發(fā)動機潤滑油組合物包括下列組分:A>為式(I)所示結(jié)構(gòu)的抗氧劑:本發(fā)明的發(fā)明人在研究中發(fā)現(xiàn),潤滑油組合物中的添加劑含有式(I)所示結(jié)構(gòu)的抗氧劑能夠使?jié)櫥徒M合物具有優(yōu)良的抗氧化等性能。本發(fā)明中,式(I)所示結(jié)構(gòu)的化合物的制備方法將在隨后部分予以詳細說明。組分A占本發(fā)明潤滑油組合物總質(zhì)量的0.1%-5%,優(yōu)選0.2%-3%。B>為抗氧型聚異丁烯丁二酰亞胺無灰分散劑,是將聚烯烴基丁二酰亞胺上的氮原子與甲氧基苯酚中的苯環(huán)通過亞烴基相連而形成的偶聯(lián)的丁二酰亞胺分散劑,制備方法是在甲氧基苯酚和多烯多胺的混合物中加入醛反應(yīng)得到縮合胺, 再與聚烯烴基丁二酸酐反應(yīng)而成。所述聚烯烴優(yōu)選C2-C4單烯烴的共聚或均聚物,可以是聚異丁烯、無規(guī)聚丙烯、乙丙共聚物,其數(shù)均分子量為850-5000,優(yōu)選為1000-4000,最好為2000-3000;甲氧基苯酚選自對甲氧基苯酚、鄰甲氧基苯酚、間甲氧基苯酚的一種或多種;醛選自甲醛、乙醛、丙醛、丁醛和苯甲醛中的一種或多種,優(yōu)選甲醛和/或多聚甲醛。組分B可以按專利CN00107484.9的方法制得。組分B占本發(fā)明潤滑油組合物總質(zhì)量的1.5%-10%,優(yōu)選2%-7%。C>聚異丁烯單丁二酰亞胺,該組分可以選用但不限于無錫南方石油添加劑有限公司生產(chǎn)的T151B,錦州石化分公司添加劑廠生產(chǎn)的T151A、T151B,Lubrizol公司生產(chǎn)的LZ894等。組分C占本發(fā)明潤滑油組合物總質(zhì)量的0.9%-6%,優(yōu)選1%-4%。D>聚異丁烯雙丁二酰亞胺。該組分可以選用但不限于無錫南方石油添加劑有限公司生產(chǎn)的T152,錦州石化分公司添加劑廠生產(chǎn)的T154,Lubrizol公司生產(chǎn)的LZ890,Infineum公司生產(chǎn)的C9233、C9236等。組分D占本發(fā)明潤滑油組合物總質(zhì)量的0.8%-5%,優(yōu)選1%-4%。E>磺酸鹽和硫化烷基酚鹽的混合物,優(yōu)選的是磺酸鈣和硫化烷基酚鈣的混合物,最好是堿值為(200-450)mgKOH/g的高堿值磺酸鈣和堿值為(100-200)mgKOH/g的中堿值硫化烷基酚鈣的混合物,二者之間的質(zhì)量比例在0.2-4:1,優(yōu)選0.25-3:1。組分E可以選用但不限于新鄉(xiāng)市瑞豐化工有限責(zé)任公司生產(chǎn)的T106B、T121,蘭州路博潤蘭煉添加劑有限公司生產(chǎn)的LZL115A,Lubrizol公司生產(chǎn)的LZ6477C、LZ6478,Afton公司生產(chǎn)的E611,Hitec7637,ChevronOronite公司生產(chǎn)的OLOA249S,Infineum公司生產(chǎn)的C9330、C9391等。組分E占潤滑油組合物總質(zhì)量的1%-8%,優(yōu)選2%-6%。F>二烷基二硫代磷酸鋅(ZDDP),所述二烷基二硫代磷酸鋅中的烷基是含有2至12個碳原子的烷基,優(yōu)選的是含有2至8個碳原子的烷基,包括但不限于乙基、正丙基、異丙基、正丁基、異丁基、仲丁基、正戊基、異戊基、正己基、異己基、正辛基、2-乙基己基、環(huán)己基和甲基環(huán)戊基中的一種或多種。二烷基二硫代磷酸鋅可以選用但不限于無錫南方石油添加劑有限公司生產(chǎn)的T202、T203,錦州石化分公司添加劑廠生產(chǎn)的T202、T203、伯仲烷基T204、仲烷基T205,Lubrizol公司的LZ1371、LZ1375、Infineum公司的C9417、C9425、C9426,Afton公司的Hitec7169、Hitec1656等。組分F在潤滑油組合物中的加入量在0.3%-2.5%之間,優(yōu)選0.6%-2.0%。G>主要量的潤滑油基礎(chǔ)油,選自APIⅠ類、Ⅱ類、Ⅲ類、Ⅳ類和Ⅴ類基礎(chǔ)油中的一種多種,優(yōu)選APIⅠ類基礎(chǔ)油和/或APIⅡ類基礎(chǔ)油。在本發(fā)明的潤滑油組合物中還可以存在如下的其它添加劑:降凝劑或稱作潤滑油流動改進劑,可以降低流體流動或可以傾倒的最低溫度,包括但不限于烷基為C8至C18的二烷基富馬酸酯/乙酸乙烯酯共聚物、聚甲基丙烯酸酯、聚α-烯烴、烷基萘等,常見的商品牌號有T803、V385、PPT148等。適合的黏度指數(shù)改進劑包括但不限于聚異丁烯、乙烯與丙烯和高級α-烯烴的共聚物、聚甲基丙烯酸酯、聚烷基甲基丙烯酸酯、甲基丙烯酸酯共聚物、不飽和二羧酸與乙烯基化合物的共聚物、苯乙烯與丙烯酸酯的共聚物、部分氫化的(苯乙烯/異戊二烯、苯乙烯/丁二烯、異戊二烯/丁二烯)的共聚物和部分氫化的(丁二烯和異戊二烯、異戊二烯/二乙烯基苯)的均聚物中的一種或多種,常見的商品牌號有T613、T614、Lubrizol公司的LZ7070、LZ7065、LZ7067、LZ7077,Infineum公司的SV260、SV261等??古輨┛蛇x用聚硅氧烷型,如硅油或聚二甲基硅氧烷。本發(fā)明中,式(I)所示結(jié)構(gòu)的化合物的制備方法優(yōu)選包括:(a)將2,6-二叔丁基苯酚、甲醛和苯進行縮合反應(yīng),生成式(II)所示的中間體M,(b)將步驟(a)得到的中間體M與溴化試劑接觸進行溴代反應(yīng),生成式(III)所示的溴代產(chǎn)物,(c)使步驟(b)得到的溴代產(chǎn)物與式(IV)所示的化合物接觸進行偶聯(lián) 反應(yīng),生成式(I)所示的抗氧劑,本發(fā)明步驟(a)中,縮合反應(yīng)的條件優(yōu)選包括:在惰性氣氛下,在第一溶劑中,在第一催化劑的存在下,將2,6-二叔丁基苯酚、甲醛和苯在-20-0℃下反應(yīng)0.5-1.5h后升至15-30℃,然后加熱至70-80℃反應(yīng)1-3h。本發(fā)明中,惰性氣氛可以為本領(lǐng)域常規(guī)的惰性氣氛,例如可以由氮氣、氬氣等氣體提供。本發(fā)明中,第一溶劑優(yōu)選選自甲醇、乙醇、N,N-二甲基甲酰胺和乙腈中的一種或多種,更優(yōu)選為甲醇和/或乙腈,更進一步優(yōu)選為甲醇。本發(fā)明中,第一催化劑可以為無機酸或有機酸,優(yōu)選醋酸、對甲基苯甲酸和苯磺酸中的一種或多種,更優(yōu)選為醋酸。本發(fā)明中,2,6-二叔丁基苯酚、甲醛和苯的用量基本上為等摩爾量,但甲醛和苯可以適當(dāng)過量。2,6-二叔丁基苯酚、甲醛和苯的摩爾比優(yōu)選為0.9-1.5:0.9-10:0.9-10。本發(fā)明步驟(a)中,第一催化劑的用量可以為催化量,以2,6-二叔丁基苯酚的摩爾數(shù)為基準,第一催化劑的用量優(yōu)選為5-100摩爾%,更優(yōu)選為10-30摩爾%。本領(lǐng)域技術(shù)人員應(yīng)該理解的是,本發(fā)明步驟(a)中,為了得到較純凈的中間體M,還需要對反應(yīng)后的體系進行后處理,后處理的方式可以包括減壓除去溶劑,然后經(jīng)溶劑稀釋、洗滌、干燥、減壓再除去溶劑,例如,將反應(yīng)后的體系在0.01-0.05MPa、40-60℃下除去溶劑,然后倒入1-10倍體積的乙酸乙酯(或二氯甲烷)中,分別用蒸餾水和飽和食鹽水洗滌,然后在15-30℃下加入無水氯化鈣或者無水硫酸鈉等干燥劑,保持10-60min。過濾除去干燥劑后,在0.01-0.05MPa、40-60℃下除去溶劑,以得到中間體M。本發(fā)明步驟(a)中,2,6-二叔丁基苯酚、甲醛和苯進行縮合反應(yīng)的反應(yīng)方 程式如圖1所示,圖1中,第一溶劑采用的是甲醇,第一催化劑采用的是醋酸,僅為舉例說明的目的,不對本發(fā)明的范圍構(gòu)成限制。本發(fā)明步驟(b)中,溴代反應(yīng)的條件優(yōu)選包括:在惰性氣氛下,在第二溶劑中,在第二催化劑的存在下,在避光條件下,將步驟(a)得到的中間體M與溴化試劑在15-30℃下反應(yīng)1-2h,然后用淬滅劑淬滅。“惰性氣氛”如前所述,在此不再贅述。本發(fā)明中,第二溶劑優(yōu)選選自四氫呋喃、二氯甲烷、氯仿和乙醚中的至少一種,更優(yōu)選為四氫呋喃。本發(fā)明中,第二催化劑優(yōu)選選自硝酸銨、過氧化苯甲酰(BPO)和偶氮二異丁腈(AIBN)中的至少一種。本發(fā)明中,溴化試劑優(yōu)選為N-溴代琥珀酰亞胺(NBS)和/或Br2,更優(yōu)選為NBS。本發(fā)明步驟(b)中,用淬滅劑進行淬滅,淬滅劑可以為本領(lǐng)域常用的淬滅劑,例如可以為飽和食鹽水。本發(fā)明步驟(b)中,中間體M與溴化試劑的用量基本上為等摩爾量,但溴化試劑一般可以適當(dāng)過量,達到反應(yīng)底物的1.1-3倍當(dāng)量。中間體M與溴化試劑摩爾比優(yōu)選為0.9-1.2:0.9-3.0。本發(fā)明步驟(b)中,第二催化劑的用量可以為催化量,以中間體M的摩爾數(shù)為基準,第二催化劑的用量優(yōu)選為10-100摩爾%,更優(yōu)選為40-60摩爾%。本發(fā)明方法步驟(b)中,中間體M與溴化試劑接觸進行溴代反應(yīng)的反應(yīng)方程式如圖2所示,圖2中,溴化試劑采用的是NBS,僅為舉例說明的目的,不對本發(fā)明的范圍構(gòu)成限制。本發(fā)明步驟(b)中,除了生成式(III)所示的溴代產(chǎn)物外,還有微量鄰位的溴代產(chǎn)物生成,沒有間位的溴代產(chǎn)物生成,但鄰位的溴代產(chǎn)物的量很微少,對后續(xù)反應(yīng)沒有實質(zhì)影響,可以忽略不計。本領(lǐng)域技術(shù)人員應(yīng)該理解的是,本發(fā)明步驟(b)中,為了得到較純凈的溴代產(chǎn)物,還需要對淬滅后的體系進行后處理,后處理的方式可以包括水洗、干燥、減壓除去溶劑,例如,將淬滅后的體系用蒸餾水洗滌,然后在15-30℃下加入無水氯化鈣或者無水硫酸鈉等干燥劑,保持10-60min。過濾除去干燥劑后,在0.01-0.05MPa、40-60℃下除去溶劑,以得到溴代產(chǎn)物。本發(fā)明步驟(c)中,偶聯(lián)反應(yīng)的條件優(yōu)選包括:在惰性氣氛下,在第三溶劑中,在第三催化劑的存在下,將步驟(b)得到的溴代產(chǎn)物與式(IV)所示的 化合物在80-100℃下反應(yīng)4-8h?!岸栊詺夥铡比缜八?,在此不再贅述。本發(fā)明中,為了使反應(yīng)穩(wěn)定進行,優(yōu)選逐漸升溫至80-100℃,然后在80-100℃下反應(yīng)4-8h。本發(fā)明中,第三溶劑優(yōu)選選自二氯甲烷、氯仿、甲苯和四氫呋喃中的至少一種,更優(yōu)選為二氯甲烷。本發(fā)明中,第三催化劑優(yōu)選包括鈀鹽、配體和堿。鈀鹽優(yōu)選選自醋酸鈀和/或鈀-二亞芐基丙酮絡(luò)合物[Pd2(dba)3];配體優(yōu)選選自三叔丁基磷、聯(lián)萘酚(BINAP)和雙(二苯基膦基)二茂鐵(dppf)中的至少一種;堿優(yōu)選選自叔丁醇鈉、叔丁醇鉀、碳酸銫和碳酸鈉中的至少一種。本發(fā)明步驟(c)中,步驟(b)得到的溴代產(chǎn)物與式(IV)所示的化合物的用量基本上為等摩爾量,但式(IV)所示的化合物可以適當(dāng)過量。步驟(b)得到的溴代產(chǎn)物與式(IV)所示的化合物的摩爾比優(yōu)選為0.9-1.5:0.9-2.5。本發(fā)明步驟(c)中,催化劑的用量可以為催化量,以溴代產(chǎn)物的摩爾數(shù)為基準,鈀鹽的用量優(yōu)選為5-50摩爾%,更優(yōu)選為5-20摩爾%,更進一步優(yōu)選為5-10摩爾%;配體的用量優(yōu)選為5-50摩爾%,更優(yōu)選為10-30摩爾%;堿的用量優(yōu)選為5-50摩爾%,更優(yōu)選為10-30摩爾%。本發(fā)明步驟(c)中,步驟(b)得到的溴代產(chǎn)物與式(IV)所示的化合物接觸進行偶聯(lián)反應(yīng)的反應(yīng)方程式如圖3所示,圖3中,鈀鹽采用的是醋酸鈀,僅為舉例說明的目的,不對本發(fā)明的范圍構(gòu)成限制。本領(lǐng)域技術(shù)人員應(yīng)該理解的是,為了得到較純凈的最終產(chǎn)物,即式(I)所示的抗氧劑,本發(fā)明方法優(yōu)選還包括對反應(yīng)后的體系進行后處理,后處理的方式可以包括過濾、溶劑稀釋、水洗、干燥、減壓除去溶劑,例如,將反應(yīng)后的體系過濾后的濾液倒入1-10倍體積的乙酸乙酯(或二氯甲烷)中,然后用蒸餾水洗滌,然后在15-30℃下加入無水氯化鈣或者無水硫酸鈉等干燥劑,保持10-60min。過濾除去干燥劑后,在0.01-0.05MPa、40-60℃下除去溶劑,以得到式(I)所示的抗氧劑。本發(fā)明制備式(I)所示結(jié)構(gòu)的化合物的方法中,對于第一溶劑、第二溶劑和第三溶劑的量無特殊要求,可以為本領(lǐng)域常規(guī)的溶劑用量,此為本領(lǐng)域技術(shù)人員所公知,在此不再贅述。如上所述,本發(fā)明旨在通過潤滑油組合物中的添加劑含有式(I)所示結(jié)構(gòu)的化合物而使?jié)櫥徒M合物具有優(yōu)良的抗氧化等性能。因此,對于潤滑油組合 物的制備方法無特殊要求,可以采用本領(lǐng)域常規(guī)使用的方法,例如,為了制造所述柴油發(fā)動機潤滑油組合物,將本發(fā)明前述的式(I)所示結(jié)構(gòu)的抗氧劑作為潤滑油添加劑之一,與潤滑油基礎(chǔ)油以及分散劑、金屬清凈劑、ZDDP按照預(yù)定比例或添加量混合均勻即可。更具體而言,為了制造本發(fā)明的柴油發(fā)動機潤滑油組合物,可以將上述各潤滑油添加劑分別加入到潤滑油基礎(chǔ)油中,加熱混合均勻即可。此時的混合溫度一般為40℃-90℃,混合時間一般為1小時-6小時。本發(fā)明采用了式(I)所示結(jié)構(gòu)的抗氧劑,同時采用了抗氧型無灰分散劑和其它無灰分散劑的優(yōu)化組合,并復(fù)配適合的清凈劑、ZDDP和其它功能添加劑,發(fā)揮了添加劑之間的協(xié)同效應(yīng),使?jié)櫥徒M合物具有優(yōu)異的抗氧、煙炱分散、高溫清凈性能,能夠滿足CH-4、CI-4級別的高性能柴油發(fā)動機潤滑油的要求。附圖說明圖1是制備抗氧劑的步驟(a)的反應(yīng)方程式。圖2是制備抗氧劑的步驟(b)的反應(yīng)方程式。圖3是制備抗氧劑的步驟(c)的反應(yīng)方程式。圖4是制備例制備的抗氧劑的氫譜譜圖。圖5是制備例制備的抗氧劑的碳譜譜圖。圖6是制備例制備的抗氧劑的質(zhì)譜譜圖。具體實施方式實施例和對比例中使用添加劑的來源見表1。表1在以下實施例和對比例中,應(yīng)用了下述方法:產(chǎn)物的理化分析方法:通過電感耦合等離子體離子發(fā)射光譜法測定元素含量;結(jié)構(gòu)表征方法:核磁共振法(1H氫譜,13C碳譜),高分辨質(zhì)譜。制備例在帶有電磁攪拌子(攪拌速度為200rpm)的500ml燒瓶中充入氮氣保護,加入150ml的甲醇和0.01mol的醋酸,在冰水浴中充分冷卻后,然后分別加入0.1mol的2,6-二叔丁基苯酚,0.2mol的甲醛和0.3mol的苯。反應(yīng)1小時后移去冰水浴,升至25℃后加熱至75℃持續(xù)回流2小時后停止反應(yīng),將反應(yīng)后的體系在0.03MPa、50℃下蒸出溶劑,然后加入250ml乙酸乙酯,并轉(zhuǎn)入分液漏斗中,分別用100ml蒸餾水(兩次)和50ml飽和食鹽水洗滌,并加入10g無水氯化鈣在25℃下干燥20min,過濾后的濾液在40℃、0.03MPa下蒸除溶劑,得到中間體產(chǎn)物M1。在帶有電磁攪拌子(攪拌速度為200rpm)的500ml燒瓶中充入氮氣保護,加入150ml的干燥四氫呋喃,然后溶入中間體產(chǎn)物M1,并加入0.05mol的硝酸銨,在避光條件下慢慢加入0.1mol溴代試劑NBS。在25℃下攪拌反應(yīng)1.5h,然后用飽和食鹽水淬滅,然后用100ml蒸餾水(兩次)洗滌,并加入10g無水硫酸鈉在25℃下干燥20min。過濾后的濾液在40℃、0.03MPa下蒸除溶劑,得到溴代產(chǎn)物。在帶有電磁攪拌子(攪拌速度為200rpm)的500ml燒瓶中充入氮氣保護,加入150ml的二氯甲烷作為溶劑,分別加入上述溴代產(chǎn)物和0.12mol的苯三唑化合物,隨后加入0.02mol的三叔丁基磷,0.02mol的叔丁醇鈉和0.005mol的Pd(OAc)2。逐漸升溫至90℃,持續(xù)攪拌6h。然后將反應(yīng)后的體系過濾后的濾液加入250ml乙酸乙酯,并轉(zhuǎn)入分液漏斗中,用100ml蒸餾水(兩次)洗滌,并加入10g無水硫酸鈉在25℃下干燥20min。過濾后的濾液在40℃、0.03MPa下蒸除溶劑,得到最終產(chǎn)物S1。S1的理化分析數(shù)據(jù)如下:氮含量,11.2%。將S1進行結(jié)構(gòu)表征,分別得到氫譜、碳譜和高分辨率質(zhì)譜譜圖,分別見圖4、圖5和圖6。從上述制備例的理化分析數(shù)據(jù)、圖4、圖5和圖6可以看出,S1具有式(I)所示的結(jié)構(gòu):實施例1-5與對比例1-3。實施例1-5為本發(fā)明的柴油發(fā)動機潤滑油的組成。將各組分按比例加入到調(diào)和容器中,常壓下加熱45℃-80℃,攪拌1小時-2小時,制備得到黏度級別為15W-40的CI-4級別柴油發(fā)動機潤滑油組合物。實施例1-2與對比例1-2分別具有除抗氧劑外全部相同的配方組成。實施例3與對比例3分別具有除分散劑外全部相同的配方組成。實施例1-5與對比例1-3的各自組成比例(質(zhì)量分數(shù))見表2。用壓力差示掃描量熱試驗(PDSC)和ASTMD4742薄層氧化試驗測定油品的氧化誘導(dǎo)期,評價油品的抗氧化性能,誘導(dǎo)期越長,油品抗氧性能越好。PDSC的設(shè)定溫度為215℃。實施例1-5和對比例1-3的氧化誘導(dǎo)期結(jié)果見表3。從表3可以看出,實施例中油品的TFOUT和PDSC氧化誘導(dǎo)期均明顯優(yōu)于其對比例。試驗數(shù)據(jù)表明,本發(fā)明的實施例采用S1抗氧劑比使用烷基二苯胺或酚酯型抗氧劑有更優(yōu)異的抗氧性能,分散劑中復(fù)合抗氧型聚異丁烯丁二酰亞胺可以改善抗氧性。表2表3油樣TFOUT/minPDSC/min實施例117239.5實施例217039.0實施例317541.3實施例417842.0實施例517339.7對比例115229.9對比例214828.9對比例315932.0實施例6-9與對比例6-1、6-2、6-3、6-4及對比例7-9。實施例6-9為本發(fā)明的柴油發(fā)動機潤滑油的組成。將各組分按比例加入到調(diào)和容器中,常壓下加熱45℃-80℃,攪拌1小時-2小時,制備得到黏度級別為15W-40的CI-4級別柴油發(fā)動機潤滑油組合物(實施例6和實施例7)和CH-4級別柴油發(fā)動機潤滑油組合物(實施例8和實施例9)。實施例6-9與對比例6-1、6-2、6-3、6-4及對比例7-9分別具有除分散劑外全部相同的配方組成,其各自組成比例見表4。用碳黑分散試驗來評價油品對煙炱的分散性能,具體做法如下:用碳黑作煙炱模擬物,分散到全配方油中,用逆流黏度管測含碳黑油的黏度,計算黏度增長率,增長率越小,表明油樣的分散性能越好。詳見US6294506B1和CN200410096315.7。實施例6-9與對比例6-1、6-2、6-3、6-4及對比例7-9的碳黑分散試驗結(jié)果見表5。表4表5油樣碳黑分散試驗黏度增長率/%實施例650實施例748實施例860實施例961對比例6-184對比例6-266對比例6-372對比例6-475對比例776對比例885對比例980從表5可以看出,實施例中油品的碳黑分散試驗黏度增長率比相對應(yīng)的對比例降低了16%-34%。在不同的柴油機油配方和不同的分散劑加劑量情況下,本發(fā)明采用的抗氧型無灰分散劑和單丁二酰亞胺及雙丁二酰亞胺的三元優(yōu)化組合比各個單獨的分散劑以及任意的兩種分散劑的組合具有更優(yōu)異的分散性能,發(fā)揮了協(xié)同效應(yīng),而對比例6-1使用普通的高分子無灰分散劑代替三元組合中的抗氧型無灰分散劑,達不到協(xié)同效果,反而使碳黑分散效果比使用單一分散劑的效果還差。在碳黑分散試驗中,在95%置信度水平下,5%的黏度增長率變化被認為是顯著變化(US6294506B1),本發(fā)明的丁二酰亞胺分散劑組合顯著降低了油品的黏度增長率,使油品具有優(yōu)異的煙炱分散性能。實施例10-12與對比例10-12。實施例10-13為本發(fā)明的柴油發(fā)動機潤滑油的組成。將各組分制備得到黏度級別為15W-40的CH-4級別柴油發(fā)動機潤滑油組合物(實施例10和實施例11)和CI-4級別柴油發(fā)動機潤滑油組合物(實施例12)。實施例10-12與對比例10-12分別具有除分散劑外全部相同的配方組成,其各自組成比例見表6,其碳黑分散試驗結(jié)果見表7。表6表7油樣碳黑分散試驗黏度增長率/%實施例1065實施例1163實施例1250對比例1081對比例1179對比例1269從表6和表7可以看出,在同樣采用抗氧型無灰分散劑和單丁二酰亞胺及雙丁二酰亞胺三元組合的情況下,本發(fā)明的實施例10-12的碳黑分散試驗粘度增長率都低于相應(yīng)的對比例,對比例10的抗氧型無灰分散劑含量不在本發(fā)明的范圍內(nèi),對比例11的單丁二酰亞胺和雙丁二酰亞胺的含量都不在本發(fā)明的范圍內(nèi),對比例12中的雙丁二酰亞胺的含量不在本發(fā)明的范圍內(nèi)。試驗數(shù)據(jù)表明,采用本發(fā)明的實施例具有優(yōu)異的煙炱分散性能。實施例13-16與對比例13-17。實施例13-16為本發(fā)明的柴油發(fā)動機潤滑油的組成。將各組分制備得到黏度級別為15W-40的CH-4級別柴油發(fā)動機潤滑油組合物。實施例13與對比例13、14具有除抗氧劑外全部相同的配方組成。實施例13與對比例15具有除分散劑外全部相同的配方組成。實施例13-16與對比例16、17具有除清凈劑外全部相同的配方組成。實施例13-16與對比例13-17各自組成比例見表8。表8對實施例13-16與對比例13-17調(diào)制的油品進行了成焦板試驗,成焦板試驗采用的設(shè)備是日本Meitech公司生產(chǎn)的25B-19型成焦板儀,該試驗?zāi)M發(fā)動機曲軸箱和缸套活塞環(huán)潤滑油循環(huán)的工作條件,使測試油品不斷受熱氧化成焦的過程。試驗時間為6h,油溫為150℃,板溫為330℃。表9由表9的試驗結(jié)果可知,實施例13比相對應(yīng)的對比例13、14有更好的清凈性能,表明使用S1抗氧劑比使用烷基二苯胺或酚酯型抗氧劑有更好的清凈性能,而實施例13與對比例15的比較表明分散劑中復(fù)配聚異丁烯雙丁二酰亞胺可以改善清凈性。實施例13-16與對比例16、17的比較表明高堿磺酸鈣和中堿硫化烷基酚鈣的混合物與單獨的磺酸鈣或硫化烷基酚鈣相比具有更好的清凈性能。本發(fā)明的潤滑油組合物具有優(yōu)異的高溫清凈性能。當(dāng)前第1頁1 2 3