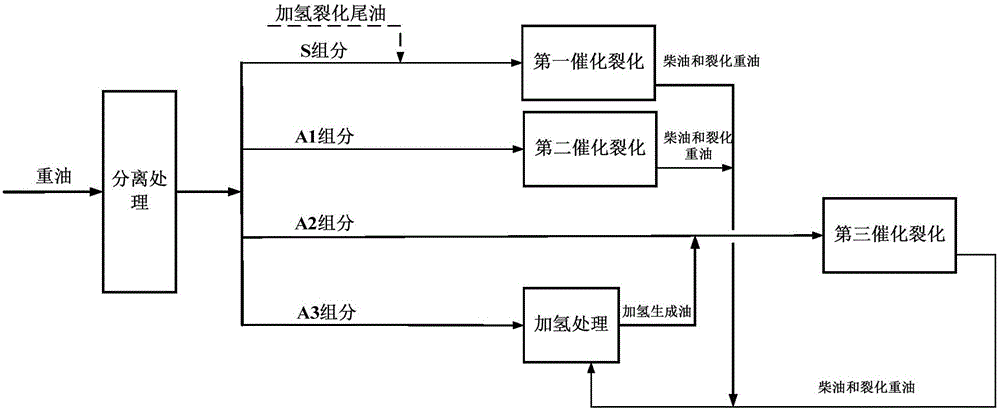
本發(fā)明涉及一種重油分離-加氫處理-催化裂化組合方法。
背景技術(shù):
:催化裂化工藝是最重要的重質(zhì)油輕質(zhì)化的二次加工手段,是液化石油氣、汽油、柴油等輕質(zhì)油品的重要生產(chǎn)過程,是不斷提高重油轉(zhuǎn)化能力的加工過程,也是不斷追求目標產(chǎn)品選擇性的過程。目前來自常減壓裝置進入重油催化裂化裝置加工的原料并沒有從餾分組成及其反應(yīng)性能上進行區(qū)分,都是采用摻煉的形式將各種原料混合在一起進入催化裂化裝置,并在同一個反應(yīng)器內(nèi)和相同工藝條件下進行轉(zhuǎn)化,并沒有根據(jù)結(jié)構(gòu)不同的烴類的反應(yīng)性能差異分別采取優(yōu)化措施。原料中大量的易于轉(zhuǎn)化的烴類與非烴類化合物、稠環(huán)芳烴一同進料反應(yīng),勢必在同一反應(yīng)區(qū)內(nèi)發(fā)生惡性競爭吸附,對裂化性能強的原料的反應(yīng)產(chǎn)生阻滯作用,從而影響整個原料的反應(yīng)轉(zhuǎn)化。反應(yīng)性能較好的易轉(zhuǎn)化烴類的反應(yīng)速率較高,在較溫和的工藝條件下便可以實現(xiàn)高的轉(zhuǎn)化率,而大量的稠環(huán)非烴類化合物、稠環(huán)芳烴及膠質(zhì)反應(yīng)速率低,需要較苛刻的工藝條件和較長的反應(yīng)時間才能達到理想的轉(zhuǎn)化深度。多種裂化性質(zhì)各異的烴類在同一反應(yīng)器內(nèi)和相同工藝條件下進行反應(yīng),不同烴類的反應(yīng)性能差異和反應(yīng)步調(diào)的不一致,會造成反應(yīng)深度不優(yōu)化并相互干擾,嚴重影響了整個原料的催化裂化轉(zhuǎn)化效率。在常規(guī)的催化裂化工藝和催化劑的開發(fā)方向上,仍然繼續(xù)沿著增加重油單程轉(zhuǎn)化能力為開發(fā)目標。這些技術(shù)大都是通過優(yōu)化工藝操作參數(shù)及催化劑以強化重油催化裂化反應(yīng)過程,雖然這些方法只能在一定程度上提高輕質(zhì)油收率,改善催化裂化產(chǎn)物的分布。但對于加工劣質(zhì)原料而言,只通過調(diào)整催 化劑組成和工藝參數(shù)往往顧此失彼,增加重油轉(zhuǎn)化能力的同時通常會伴隨著干氣和焦炭產(chǎn)率的大幅增加,這樣無疑將會導致重油轉(zhuǎn)化選擇性變差,即轉(zhuǎn)化率與干氣和焦炭選擇性之間存在著明顯的矛盾,難以實現(xiàn)烴類的碳氫分配最佳化和石油產(chǎn)品最大化。在重油催化裂化過程中,原料油性質(zhì)、催化劑性能、工藝條件(溫度、劑油質(zhì)量比、空速等)等因素都對產(chǎn)品分布有重要影響,其中原料烴類組成仍然是產(chǎn)品分布的基礎(chǔ)。按照沸點對重油原料進行分離可以在一定程度上提高重油的轉(zhuǎn)化能力,并改善其產(chǎn)物分布。按照沸點將原料油切割為相對易裂化餾分和相對難裂化餾分可以在一定程度上削弱難裂化餾分的不良影響,為易裂化餾分提供一個較好的反應(yīng)環(huán)境,改善產(chǎn)物收率及產(chǎn)品分布。CN102102029A公布了以500-540℃、殘?zhí)恐亓恐禐?~4%為分級點,將重油原料分為優(yōu)質(zhì)原料和劣質(zhì)原料,其結(jié)果與傳統(tǒng)工藝相比,重油分級后,產(chǎn)物分布明顯改善,輕質(zhì)油收率提高,焦炭和干氣收率降低。鈕根林等(鈕根林,陳捷.勝利減壓渣油窄餾分催化裂化性能的研究.煉油設(shè)計,1995,25(2):6-10)利用超臨界流體抽提精密分離裝置將催化裂化原料按照沸點切割為相對優(yōu)質(zhì)和劣質(zhì)的原料,將勝利減渣分為15個組分并考察了前13個餾分的催化裂化性能,實驗表明隨著餾分變重,輕質(zhì)油收率依次降低,焦炭產(chǎn)率逐漸升高。實沸點蒸餾或超臨界流體萃取等方法將重油切割為沸點范圍不同的窄餾分,盡管沸點范圍可以切得很窄,但每個窄餾分仍然是各種烴類的混合物。對于不同的催化原料而言,餾程范圍及化學結(jié)構(gòu)和組成的較大差異決定了它們反應(yīng)性能存在較大差異。各種烴類在催化劑上的吸附能力按其強弱順序大致可排列如下:稠環(huán)芳烴>稠環(huán)環(huán)烷烴>烯烴>單烷基側(cè)鏈的單環(huán)芳烴>環(huán)烷烴>烷烴。按照化學反應(yīng)速率的高低順序排列,則大致情況如下:烯烴>大分子單烷基側(cè)鏈的單環(huán)芳烴>異構(gòu)烷烴及環(huán)烷烴>小分子單烷基側(cè)鏈的單環(huán)芳烴>正構(gòu)烷烴>稠環(huán)芳烴??梢钥闯?,原料中各種烴類、非烴類化合物在催化 劑表面的吸附和裂化能力存在很大區(qū)別,稠環(huán)的非烴類化合物、稠環(huán)芳烴及稠環(huán)環(huán)烷烴吸附能力強而反應(yīng)速率低,而帶有較長側(cè)鏈的單環(huán)芳烴及大分子異構(gòu)烷烴、環(huán)烷烴吸附能力弱而反應(yīng)速率高,這就造成了不同烴類之間的競爭吸附和對反應(yīng)的阻滯作用。吸附能力強而反應(yīng)速率低的稠環(huán)非烴類化合物、稠環(huán)芳烴一旦首先占據(jù)催化劑表面,它們反應(yīng)速率慢,不易脫附,甚至縮合成為焦炭覆蓋在催化劑表面,造成催化劑失活,嚴重影響了其它易于裂化烴類的反應(yīng)速率?;诖?,不把各種重油原料作為一個“整體”來進料,充分考慮寬餾程的重油原料中不同組分裂化性能存在的較大差異,可以將原料油中裂化性能差異較大的組分進行分離后分別進行催化裂化。傳統(tǒng)的催化裂化原料主要是煉廠中常減壓裝置提供的減壓餾分油。減壓蠟油餾分按照烴類結(jié)構(gòu)的不同可以分為不同的烴族組分如非芳烴組分和芳烴組分、飽和烴組分和芳烴組分(不含膠質(zhì)),但芳烴組分中的單環(huán)芳烴、雙環(huán)芳烴和多環(huán)芳烴在催化裂化過程中的反應(yīng)行為仍有較大區(qū)別,目前的研究報道中鮮有將不同環(huán)數(shù)的芳烴從原料中分離富集后進行催化裂化反應(yīng)的研究。目前,市場對石油產(chǎn)品不斷輕質(zhì)化、優(yōu)質(zhì)化和清潔化的要求與原油供應(yīng)日益重質(zhì)化、劣質(zhì)化的矛盾加劇,而我國經(jīng)濟發(fā)展對高價值的輕、中質(zhì)石油產(chǎn)品的需求不斷增加。因此,如何以較經(jīng)濟合理的代價實現(xiàn)重油輕質(zhì)化、所得到產(chǎn)品又能滿足不斷苛刻的汽柴油產(chǎn)品規(guī)格的煉油技術(shù)成了國內(nèi)外煉油技術(shù)開發(fā)商重點開發(fā)的技術(shù)之一。催化裂化柴油的芳烴含量高,十六烷值低,發(fā)動機點火性能差,屬于劣質(zhì)的柴油調(diào)和組分,嚴重影響柴油產(chǎn)品質(zhì)量,是各企業(yè)柴油產(chǎn)品質(zhì)量升級的最大障礙之一。對劣質(zhì)蠟油原料進行加氫預處理,芳烴得到不同程度的飽和,除去硫、氮、金屬等雜質(zhì),再作為催化裂化的原料,可以根據(jù)生產(chǎn)需要,生 產(chǎn)柴油、汽油等優(yōu)質(zhì)產(chǎn)品和中間產(chǎn)品,從而可以改善其催化裂化性能,顯著改善產(chǎn)品的結(jié)構(gòu)。CN1896192A公開了一種蠟油加氫處理和催化裂化雙向方法,蠟油與催化裂化重循環(huán)油和催化裂化柴油一起進入加氫處理裝置反應(yīng)后得到氣體、加氫石腦油、加氫柴油和加氫尾油等產(chǎn)物,其中加氫尾油進入催化裂化裝置反應(yīng),該方法提高了輕油收率,降低了焦炭產(chǎn)率,同時降低了柴油的芳烴含量和硫含量并提高了其十六烷值。與此相似,CN101434865A也公布了一種重質(zhì)餾分油加氫處理與催化裂化聯(lián)合的方法。但這些方法均直接將質(zhì)量較差催化裂化重油和催化裂化柴油與含有大量飽和烴的蠟油原料進行混合,蠟油中的飽和烴在加氫處理過程中由于催化劑上酸性中心的作用而易于裂化成輕烴,造成氣體產(chǎn)率增加,同時生成的加氫重油比重較小,作為催化裂化單元的進料時輕質(zhì)油產(chǎn)率下降。因此,目前的重油加工工藝存在待改進的空間。技術(shù)實現(xiàn)要素:本發(fā)明的目的是提供一種重油分離-加氫處理-催化裂化組合方法,該方法通過將重油進行分離處理所得到的S組分、A1組分、A2組分和A3組分分別進行催化裂化反應(yīng),具有更高的汽油和液化氣產(chǎn)率以及更低的汽油硫氮含量。為了實現(xiàn)上述目的,本發(fā)明提供一種重油分離-加氫處理-催化裂化組合方法,該方法包括:a、將重油進行分離處理,得到S組分、A1組分、A2組分和A3組分;其中,以S組分的總質(zhì)量為基準,所述S組分中飽和烴的質(zhì)量分數(shù)大于90質(zhì)量%;以A1組分的總質(zhì)量為基準,所述A1組分中單環(huán)芳烴的質(zhì)量分數(shù)大于60質(zhì)量%;以A2組分的總質(zhì)量為基準,所述A2組分中單環(huán)芳烴的質(zhì)量分數(shù)小于40質(zhì)量%,雙環(huán)芳烴的質(zhì)量分數(shù)大于30質(zhì)量%,雙環(huán)以上芳烴和膠質(zhì)的總質(zhì)量分數(shù)小于45質(zhì)量%;以A3組分的總質(zhì)量為基 準,所述A3組分中雙環(huán)以上芳烴和膠質(zhì)的總質(zhì)量分數(shù)大于50質(zhì)量%;b、將步驟a中所得的S組分進行第一催化裂化反應(yīng),得到干氣、液化氣、汽油、柴油、焦炭和裂化重油;將步驟a中所得的A1組分進行第二催化裂化反應(yīng),得到干氣、液化氣、汽油、柴油、焦炭和裂化重油;將步驟a中所得的A2組分進行第三催化裂化反應(yīng),得到干氣、液化氣、汽油、柴油、焦炭和裂化重油;將步驟a中所得的A3組分在加氫處理催化劑的作用下進行加氫處理反應(yīng),得到加氫生成油。優(yōu)選地,其中,以S組分的總質(zhì)量為基準,所述S組分中飽和烴的質(zhì)量分數(shù)大于95質(zhì)量%;以A1組分的總質(zhì)量為基準,所述A1組分中單環(huán)芳烴的質(zhì)量分數(shù)大于70質(zhì)量%;以A2組分的總質(zhì)量為基準,所述A2組分中單環(huán)芳烴的質(zhì)量分數(shù)小于30質(zhì)量%,雙環(huán)芳烴的質(zhì)量分數(shù)大于35質(zhì)量%,雙環(huán)以上芳烴和膠質(zhì)的總質(zhì)量分數(shù)小于40質(zhì)量%;以A3組分的總質(zhì)量為基準,所述A3組分中雙環(huán)以上芳烴和膠質(zhì)的總質(zhì)量分數(shù)大于60質(zhì)量%。優(yōu)選地,該方法還包括步驟c:將步驟b中所得加氫生成油進行第四催化裂化反應(yīng),得到干氣、液化氣、汽油、柴油、焦炭和裂化重油。優(yōu)選地,該方法還包括:將所述第一催化裂化反應(yīng)得到的柴油和/或裂化重油的至少一部分、所述第二催化裂化反應(yīng)得到的柴油和/或裂化重油的至少一部分、所述第三催化裂化反應(yīng)得到的柴油和/或裂化重油的至少一部分以及所述第四催化裂化反應(yīng)得到的柴油和/或裂化重油的至少一部分與所述A3組分一起進行所述加氫處理反應(yīng)。優(yōu)選地,該方法還包括步驟d:將步驟b中所得加氫生成油與A2組分一起進行所述第三催化裂化反應(yīng)。優(yōu)選地,該方法還包括:將所述第一催化裂化反應(yīng)得到的柴油和/或裂化重油的至少一部分、所述第二催化裂化反應(yīng)得到的柴油和/或裂化重油的至少一部分以及所述第三催化裂化反應(yīng)得到的柴油和/或裂化重油的至少一部 分與所述A3組分一起進行所述加氫處理反應(yīng)。優(yōu)選地,該方法還包括:將加氫裂化尾油與所述S組分一起進行所述第一催化裂化反應(yīng)。優(yōu)選地,其中,所述重油為初餾點在350℃以上的直餾減壓餾分油和/或二次加工過程所得初餾點大于350℃的餾分。優(yōu)選地,其中,所述二次加工過程為選自加氫處理過程、加氫裂化過程、催化裂化過程和溶劑脫瀝青過程中的至少一種。優(yōu)選地,其中,步驟a中所述分離處理為選自溶劑萃取處理、固相萃取處理和膜分離處理方法中的至少一種。優(yōu)選地,其中,所述溶劑萃取處理為選自溶劑精制萃取、超臨界流體萃取和離子液體萃取中的至少一種。優(yōu)選地,其中,所述固相萃取處理包括以下步驟:先將所述重油采用稀釋劑稀釋后送入固定相中,得到第一固定相;然后用C5-C6的烷烴沖洗所述第一固定相,得到所述S組分和第二固定相;然后用芳烴和C5-C6的烷烴體積比為1:(15-25)的溶劑沖洗第二固定相,得到所述A1組分和第三固定相;然后用芳烴和C5-C6的烷烴體積比為1:(3-5)的溶劑沖洗第三固定相,得到所述A2組分和第四固定相;然后用芳烴和一元醇體積比為1:(0.8-1.5)的溶劑沖洗第四固定相,得到所述A3組分;其中,所述固定相含有負載銀的氧化鋁,以所述負載銀的氧化鋁的總質(zhì)量為基準,負載的銀的質(zhì)量分數(shù)為0.5-12質(zhì)量%。優(yōu)選地,其中,所述固定相還含有按照流體流向位于所述負載銀的氧化鋁上游的硅膠以及位于所述負載銀的氧化鋁下游的氧化鋁;以質(zhì)量計,所述硅膠、所述負載銀的氧化鋁以及所述位于所述負載銀的氧化鋁下游的氧化鋁的質(zhì)量比為1:(2.5-5.0):(0-1.2);其中,所述氧化鋁的比表面積為50-300米2/克,孔體積為0.1-0.55毫升/克,所述硅膠的比表面為250-850米2/克, 孔體積為0.25-0.99毫升/克。優(yōu)選地,其中,所述稀釋劑為C5-C6的烷烴,以體積計,所述稀釋劑與重油的體積之比為(1-10):1;所述芳烴為苯和/或甲苯,所述一元醇為甲醇和/或乙醇;以質(zhì)量計,所述固定相與所述重油的質(zhì)量比為(8-30):1。優(yōu)選地,其中,步驟b中所述第一催化裂化反應(yīng)的條件為:溫度為420-520℃,質(zhì)量空速為2-20小時-1,劑油比為(1-10):1。優(yōu)選地,其中,步驟b中所述第二催化裂化反應(yīng)的條件為:溫度為420-520℃,質(zhì)量空速為2-20小時-1,劑油比為(1-10):1。優(yōu)選地,其中,步驟b中所述第三催化裂化反應(yīng)的條件為:溫度為480-540℃,質(zhì)量空速為2-20小時-1,劑油比為(2-30):1。優(yōu)選地,其中,步驟b中所述加氫處理反應(yīng)的條件為:氫分壓為3-12兆帕,反應(yīng)溫度為280-360℃,加氫處理催化劑為不含有酸中心的芳烴加氫飽和催化劑;步驟b中所述加氫生成油的初餾點為155-175℃。優(yōu)選地,其中,步驟c中所述第四催化裂化反應(yīng)的條件為:溫度為450-540℃,質(zhì)量空速為2-20小時-1,劑油比為(2-30):1。與現(xiàn)有技術(shù)相比,本發(fā)明的優(yōu)越性在于:1、基于分離技術(shù)實現(xiàn)了重油中S組分、A1組分、A2組分和A3組分的分離,針對動力學行為差異較大的S組分、A1組分和A2組可以分別在最匹配的催化裂化條件下進行單獨反應(yīng),既消除了不同烴類之間的相互影響,又可以使每種烴族在最優(yōu)化的條件下反應(yīng),提高了重油中氫的利用率,從而節(jié)約石油資源。2、本發(fā)明的方案可以在A3組分的催化裂化單元前串聯(lián)一個加氫處理單元,以實現(xiàn)兩種目的:首先,加氫技術(shù)為選擇性加氫,A3組分發(fā)生加氫脫硫、加氫脫氮反應(yīng),并選擇性飽和多環(huán)芳烴和膠質(zhì),適度飽和雙環(huán)芳烴,單環(huán)芳烴飽和少,并且催化劑上幾乎沒有酸中心,生成的部分飽和或全飽和的 大分子烴類可以得到最大程度的保留,為催化裂化單元生產(chǎn)低硫汽油提供優(yōu)質(zhì)原料,同時可通過控制加氫處理單元的反應(yīng)深度來控制催化汽油硫氮含量;其次,從不同的催化裂化單元流出的催化裂化柴油和催化裂化重油均返回到加氫處理單元,其中的雙環(huán)以上芳烴的適度加氫飽和反應(yīng)后作為催化裂化單元的進料,為催化裂化單元生產(chǎn)高辛烷值汽油提供優(yōu)質(zhì)進料。3、通過本發(fā)明提供的方法,可以將催化裂化柴油和催化裂化重油返回加氫處理單元進行加氫后再進行裂化,首先催化裂化單程轉(zhuǎn)化不追求高轉(zhuǎn)化率,而追求整個過程的總轉(zhuǎn)化率,在催化裂化單元不生產(chǎn)芳烴含量高、十六烷值低的催化柴油,降低了干氣和焦炭的產(chǎn)率,提高了液化氣和高辛烷值汽油的收率;其次催化裂化反應(yīng)流出物的分餾系統(tǒng)僅分餾出汽油餾分等輕質(zhì)產(chǎn)品,分餾塔所需的理論塔板數(shù)大大降低;最后對富含多環(huán)芳烴和膠質(zhì)的原料起到稀釋作用,二者以一定比例混合后使混合原料油的輸送更加容易。4、增加了催化裂化過程原料選擇范圍,提高了原料中的氫利用率,改善了產(chǎn)物分布,提高汽油產(chǎn)率和丙烯產(chǎn)率,使產(chǎn)品結(jié)構(gòu)調(diào)整更加靈活。5、強化分離過程、加氫處理與催化裂化技術(shù)更加合理的集成,為煉油生產(chǎn)過程高效化和煉油產(chǎn)品的合理化提供了一條新的途徑。6、本發(fā)明將重油進行分離處理,降低了S組分、A1組分和A2組分中的硫氮含量,并進一步降低S組分、A1組分和A2組分經(jīng)催化裂化所得產(chǎn)品的硫氮含量,另外,高硫氮含量的A3組分,可以進行加氫處理反應(yīng)進行脫除硫氮,從而降低了催化裂化產(chǎn)品中的硫氮含量。本發(fā)明的其他特征和優(yōu)點將在隨后的具體實施方式部分予以詳細說明。附圖說明附圖是用來提供對本發(fā)明的進一步理解,并且構(gòu)成說明書的一部分,與下面的具體實施方式一起用于解釋本發(fā)明,但并不構(gòu)成對本發(fā)明的限制。在 附圖中:圖1是本發(fā)明方法第一種具體實施方式的流程示意圖;圖2是本發(fā)明方法第二種具體實施方式的流程示意圖。具體實施方式以下結(jié)合附圖對本發(fā)明的具體實施方式進行詳細說明。應(yīng)當理解的是,此處所描述的具體實施方式僅用于說明和解釋本發(fā)明,并不用于限制本發(fā)明。本發(fā)明提供一種重油分離-加氫處理-催化裂化組合方法,該方法包括:a、將重油進行分離處理,得到S組分、A1組分、A2組分和A3組分;其中,以S組分的總質(zhì)量為基準,所述S組分中飽和烴的質(zhì)量分數(shù)大于90質(zhì)量%,優(yōu)選大于95質(zhì)量%;以A1組分的總質(zhì)量為基準,所述A1組分中單環(huán)芳烴的質(zhì)量分數(shù)大于60質(zhì)量%,優(yōu)選大于70質(zhì)量%;以A2組分的總質(zhì)量為基準,所述A2組分中單環(huán)芳烴的質(zhì)量分數(shù)小于40質(zhì)量%,優(yōu)選小于30質(zhì)量%,雙環(huán)芳烴的質(zhì)量分數(shù)大于30質(zhì)量%,優(yōu)選大于35質(zhì)量%,雙環(huán)以上芳烴和膠質(zhì)的總質(zhì)量分數(shù)小于45質(zhì)量%,優(yōu)選小于40質(zhì)量%;以A3組分的總質(zhì)量為基準,所述A3組分中雙環(huán)以上芳烴和膠質(zhì)的總質(zhì)量分數(shù)大于50質(zhì)量%,優(yōu)選大于60質(zhì)量%;b、將步驟a中所得的S組分進行第一催化裂化反應(yīng),得到干氣、液化氣、汽油、柴油、焦炭和裂化重油;將步驟a中所得的A1組分進行第二催化裂化反應(yīng),得到干氣、液化氣、汽油、柴油、焦炭和裂化重油;將步驟a中所得的A2組分進行第三催化裂化反應(yīng),得到干氣、液化氣、汽油、柴油、焦炭和裂化重油;將步驟a中所得的A3組分在加氫處理催化劑的作用下進行加氫處理反應(yīng),得到加氫生成油。根據(jù)本發(fā)明,所述S組分中主要含有包括鏈烷烴和環(huán)烷烴的飽和烴,其余可以為芳烴;所述A1組分、A2組分和A3組分中所含的芳烴是本領(lǐng)域技 術(shù)人員所熟知的,本發(fā)明不再贅述,A3組分所含的膠質(zhì)是指將渣油的正庚烷可溶質(zhì)通過氧化鋁液相色譜分離出飽和烴和芳烴后得到的組分,具體可參見《催化裂化化學與工藝》,許友好著,2013,科學出版社,例如,可以采用RIPP10-90測試方法進行分離測定,由于重油組成與渣油都可以采用飽和烴、芳烴、膠質(zhì)和瀝青質(zhì)進行界定,因此重油中的膠質(zhì)也可以如此定義。本發(fā)明優(yōu)選的是,在符合每個組分定義的條件下,分離處理應(yīng)盡可能的使鏈烷烴和環(huán)烷烴富集在S組分中,單環(huán)芳烴集中在A1組分中,雙環(huán)芳烴集中在A2組分中,雙環(huán)以上芳烴和膠質(zhì)集中在A3組分中,減少四者之間的交叉。根據(jù)本發(fā)明,由于A3組分的不飽和度較高,而經(jīng)過加氫處理后的A3組分是一種良好的催化裂化原料,因此該方法還可以包括步驟c:將步驟b中所得加氫生成油進行第四催化裂化反應(yīng),得到干氣、液化氣、汽油、柴油、焦炭和裂化重油;以及可以進一步包括步驟d:將步驟b中所得加氫生成油與A2組分一起進行所述第三催化裂化反應(yīng)。本發(fā)明中加氫處理是為了通過加氫使單環(huán)以上芳烴和膠質(zhì)發(fā)生不同程度的飽和,而單環(huán)芳烴盡可能少的被飽和,同時盡可能多地保留加氫后的芳烴,因此采用的加氫處理優(yōu)選為選擇性加氫處理,得到的產(chǎn)品主要是加氫生成油,且其收率優(yōu)選不低于70-99重量%。所述加氫生成油是指沸點為150℃-600℃左右的餾分油,以HT-A3標記,優(yōu)選加氫生成油的初餾點為150℃-250℃,更優(yōu)選為155℃-175℃。本發(fā)明可以通過控制加氫處理時加氫生成油的收率來控制加氫改質(zhì)的程度,從而確保加氫改質(zhì)時既不會導致氣體產(chǎn)率太高,導致?lián)p失太多的輕質(zhì)油,也能夠確保后續(xù)的催化裂化容易進行。根據(jù)本發(fā)明,為了進一步利用催化裂化反應(yīng)所得的柴油和裂化重油,實現(xiàn)柴油和裂化重油的全轉(zhuǎn)化,因此該方法在步驟c之后還可以包括:將所述第一催化裂化反應(yīng)得到的柴油和/或裂化重油的至少一部分、所述第二催化裂化反應(yīng)得到的柴油和/或裂化重油的至少一部分、所述第三催化裂化反應(yīng)得到 的柴油和/或裂化重油的至少一部分以及所述第四催化裂化反應(yīng)得到的柴油和/或裂化重油的至少一部分與所述A3組分一起進行所述加氫處理反應(yīng)。該方法在步驟d后還可以包括:將所述第一催化裂化反應(yīng)得到的柴油和/或裂化重油的至少一部分、所述第二催化裂化反應(yīng)得到的柴油和/或裂化重油的至少一部分以及所述第三催化裂化反應(yīng)得到的柴油和/或裂化重油的至少一部分與所述A3組分一起進行所述加氫處理反應(yīng)。催化裂化所得的柴油主要是指催化裂化全餾分產(chǎn)品中221℃-343℃左右的餾分,所得的裂化重油主要指催化裂化全餾分產(chǎn)品中350℃以上餾分。其中,催化裂化所得的柴油中雙環(huán)以上芳烴含量可以占40質(zhì)量%以上,進一步可達50質(zhì)量%以上,這部分餾分返回加氫處理單元進行適度飽和,然后進入催化裂化單元繼續(xù)進行裂化反應(yīng),為生成高辛烷值汽油提供優(yōu)質(zhì)進料;本發(fā)明柴油在加氫處理單元混合進料中的質(zhì)量分數(shù)范圍可以為大于0至50重%,更優(yōu)選為大于0至30重%。所述的裂化重油中雙環(huán)及以上芳烴含量可以達40質(zhì)量%以上,進一步可達50質(zhì)量%以上,這部分餾分返回加氫處理單元進行適度飽和,增加氫含量,然后進入催化裂化單元繼續(xù)進行裂化反應(yīng),為生成高辛烷值汽油提供優(yōu)質(zhì)進料。本發(fā)明的裂化重油在加氫處理單元混合進料中的質(zhì)量分數(shù)范圍優(yōu)選為大于0至50重%,更優(yōu)選大于0至30重%。根據(jù)本發(fā)明,可以將加氫裂化尾油與所述S組分一起進行所述第一催化裂化反應(yīng)。所述加氫裂化尾油是指加氫裂化反應(yīng)所產(chǎn)生的未裂化的飽和烴。根據(jù)本發(fā)明,所述重油是本領(lǐng)域技術(shù)人員所熟知的,可以為初餾點在350℃以上的直餾減壓餾分油和/或二次加工過程所得初餾點大于350℃的餾分,所述的初餾點是指油品餾程的最小值。其中,所述二次加工過程可以為選自加氫處理過程、加氫裂化過程、催化裂化過程和溶劑脫瀝青過程中的至少一種。根據(jù)本發(fā)明,步驟a中所述分離處理是指將重油分離為S組分、A1組 分、A2組分和A3組分的過程,可以為選自溶劑萃取處理、固相萃取處理和膜分離處理方法中的至少一種,不同的分離處理方法可以單獨使用,也可以串聯(lián)使用。所述溶劑萃取處理優(yōu)選為選自溶劑精制萃取、超臨界流體萃取和離子液體萃取中的至少一種,可以采用單溶劑萃取,也可以采用多溶劑萃取方式,優(yōu)選采用多溶劑萃取方式。所述固相萃取處理中所述的固相可以包括分離柱、真空系統(tǒng)等設(shè)備,優(yōu)選包括以下步驟:先將所述重油采用稀釋劑稀釋后送入固定相中,得到第一固定相;然后用C5-C6的烷烴沖洗所述第一固定相,得到所述S組分和第二固定相;然后用芳烴和C5-C6的烷烴體積比為1:(15-25)的溶劑沖洗第二固定相,得到所述A1組分和第三固定相;然后用芳烴和C5-C6的烷烴體積比為1:(3-5)的溶劑沖洗第三固定相,得到所述A2組分和第四固定相;然后用芳烴和一元醇體積比為1:(0.8-1.5)的溶劑沖洗第四固定相,得到所述A3組分;其中,所述固定相含有負載銀的氧化鋁,以所述負載銀的氧化鋁的總質(zhì)量為基準,負載的銀的質(zhì)量分數(shù)為0.5-12質(zhì)量%。所述固定相還可以含有按照流體流向位于所述負載銀的氧化鋁上游的硅膠以及位于所述負載銀的氧化鋁下游的氧化鋁;以質(zhì)量計,所述硅膠、所述負載銀的氧化鋁以及所述位于所述負載銀的氧化鋁下游的氧化鋁的質(zhì)量比可以為1:(2.5-5.0):(0-1.2);其中,所述氧化鋁的比表面積可以為50-300米2/克,孔體積可以為0.1-0.55毫升/克,所述硅膠的比表面可以為250-850米2/克,孔體積可以為0.25-0.99毫升/克。所述稀釋劑可以為C5-C6的烷烴,以體積計,所述稀釋劑與重油的體積之比可以為(1-10):1;所述芳烴可以為苯和/或甲苯,所述一元醇可以為甲醇和/或乙醇;以質(zhì)量計,所述固定相與所述重油的質(zhì)量比可以為(8-30):1。根據(jù)本發(fā)明,所述催化裂化反應(yīng)是本領(lǐng)域技術(shù)人員所熟知的,本發(fā)明不再贅述。根據(jù)反應(yīng)原料的不同,催化裂化反應(yīng)的條件可以不同,例如,步驟b中所述第一催化裂化反應(yīng)的條件可以為:溫度為420-520℃,優(yōu)選為 480-520℃,質(zhì)量空速為2-20小時-1,優(yōu)選為15-20小時-1,劑油比為(1-10):1,優(yōu)選為(2-6):1。步驟b中所述第二催化裂化反應(yīng)的條件可以為:溫度為420-520℃,優(yōu)選為480-520℃,質(zhì)量空速為2-20小時-1,優(yōu)選為15-20小時-1,劑油比為(1-10):1,優(yōu)選為(2-6):1。步驟b中所述第三催化裂化反應(yīng)的條件可以為:溫度為480-540℃,優(yōu)選為480-520℃,質(zhì)量空速為2-20小時-1,優(yōu)選為15-20小時-1,劑油比為(2-30):1,優(yōu)選為(2-6):1。步驟c中所述第四催化裂化反應(yīng)的條件可以為:溫度為450-540℃,優(yōu)選為480-520℃,質(zhì)量空速為2-20小時-1,優(yōu)選為15-20小時-1,劑油比為(2-30):1,優(yōu)選為(2-6):1。根據(jù)本發(fā)明,所述加氫處理反應(yīng)是本領(lǐng)域技術(shù)人員所熟知的,本發(fā)明不再贅述。步驟b中所述加氫處理反應(yīng)的條件可以為:氫分壓為3-12兆帕,反應(yīng)溫度為280-360℃,加氫處理催化劑為不含有酸中心的芳烴加氫飽和催化劑;步驟b中所述加氫生成油的初餾點為155-175℃。本發(fā)明的第一種具體實施方式如圖1所示:將重油進行分離處理后得到了S組分、A1組分、A2組分和A3組分,將所得的S組分、A1組分和A2組分分別進行第一催化裂化反應(yīng)、第二催化裂化反應(yīng)和第三催化裂化反應(yīng),得到干氣、液化氣、汽油、柴油、焦炭和裂化重油;將所得A3組分進行加氫處理反應(yīng),得到的加氫生成油進行第四催化裂化反應(yīng),得到干氣、液化氣、汽油、柴油、焦炭和裂化重油;將所得的柴油和裂化重油進行加氫處理反應(yīng),得到加氫生成油。同時,可以將加氫裂化尾油與S組分混合后一起進行第一催化裂化反應(yīng)。本發(fā)明的第二種具體實施方式如圖2所示:將重油進行分離處理后得到了S組分、A1組分、A2組分和A3組分,將所得的S組分和A1組分分別進行第一催化裂化反應(yīng)和第二催化裂化反應(yīng),得到干氣、液化氣、汽油、柴油、焦炭和裂化重油;將所得A3組分進行加 氫處理反應(yīng),得到的加氫生成油和A2組分一起進行第三催化裂化反應(yīng),得到干氣、液化氣、汽油、柴油、焦炭和裂化重油;將所得的柴油和裂化重油進行加氫處理反應(yīng),得到加氫生成油。同時,可以將加氫裂化尾油與S組分混合后一起進行第一催化裂化反應(yīng)。下面將通過實施例來進一步說明本發(fā)明,但是本發(fā)明并不因此而受到任何限制。本發(fā)明實施例所采用的試劑和儀器,如無特殊說明,均為本領(lǐng)域常規(guī)的儀器和試劑。本發(fā)明實施例和對比例中采取的催化裂化反應(yīng)在美國KTI公司生產(chǎn)的ACEModelAP裝置上進行,實驗中催化劑裝量均為9g,反應(yīng)溫度為500℃,質(zhì)量空速為16小時-1,劑/油質(zhì)量比(C/O)為4。實驗參數(shù)穩(wěn)定后,進入反應(yīng)程序,催化劑在自身重力和N2作用下進入反應(yīng)器,原料油在柱塞泵推動下沿加料細管進入反應(yīng)器催化劑流化床層中,與流化態(tài)的催化劑顆粒接觸反應(yīng),同時采用N2汽提600-900s。反應(yīng)產(chǎn)物被N2帶入-10℃的液收瓶中進行氣液分離,氣體產(chǎn)物收集完成由Agilent6890GC(TCD檢測器)在線分析組成;液體產(chǎn)物收集后離線稱重,分別進行模擬蒸餾和汽油單體烴分析(采用RIPP81-90測試方法進行測試),汽油和柴油的餾分切割點分別為221℃和343℃;生焦催化劑卸出后在multiEA2000碳硫分析儀上進行焦炭和硫含量分析(采用RIPP106-90測試方法進行測試),所有產(chǎn)物質(zhì)量加和計算物料平衡。實施例和對比例中采用中國石化催化劑有限公司生產(chǎn)的牌號為MLC-500的催化裂化催化劑作為實驗用催化劑,其微反活性可以通過現(xiàn)有技術(shù)中的RIPP92-90測量方法測量,基本物性列于表3。實施例的加氫處理過程在煙臺科立化工設(shè)備有限公司生產(chǎn)的500mL精密高壓反應(yīng)釜內(nèi)進行,該反應(yīng)釜加熱功率為1.5K重,有效容積為0.5L,最高轉(zhuǎn)速1500rpm。將一定量A3加入反應(yīng)釜內(nèi),所采用的催化劑為石油化工 科學研究院生產(chǎn)的粒度在40~60目的硫化態(tài)催化劑,牌號為RIB-429。用氫氣將釜內(nèi)空氣置換后,開啟攪拌轉(zhuǎn)速為338rpm,同時開始程序升溫至反應(yīng)溫度為340℃,到達設(shè)定溫度后,氫分壓調(diào)節(jié)至5MPa,攪拌轉(zhuǎn)速為985rpm,反應(yīng)時間為12h反應(yīng)結(jié)束后,開啟循環(huán)冷凝水降溫冷卻至室溫,用N2置換釜內(nèi)氣體數(shù)次后放空,對釜內(nèi)液體產(chǎn)物的液體產(chǎn)物進行餾分切割,得到加氫生成油HT-A3。S組分、A1組分、A2組分和A3組分、HT-A3組分以及HCW的烴族組成采用RIPP10-90測試方法進行測試。本發(fā)明的RIPP測試方法為選自《石油化工分析方法(RIPP試驗方法)》,楊翠定等編,科學出版社,1990。實施例1本實施例用于說明本發(fā)明提供的重油分離-加氫處理-催化裂化組合方法中重油分離單元的實施方法。在分離柱內(nèi)底層裝填30g中性氧化鋁(比表面積為152米2/克,孔體積為0.213毫升/克),中間裝填110g負載銀離子的氧化鋁(銀的質(zhì)量分數(shù)為7.05質(zhì)量%,采用硝酸銀浸漬方法制備),上層裝填30g硅膠(比表面積為479米2/克,孔體積為0.349毫升/克);將分離柱下端與抽真空系統(tǒng)相連。固定相的總體積為150mL。取減壓餾分油(VGO,塔河原油取自中國石化西北分公司塔河油田,在石油化工科學研究院經(jīng)實沸點蒸餾得到塔河減壓蠟油)樣品10.20g(11.19mL),溶于30mL正己烷中,先用100mL的正己烷潤濕上述分離柱內(nèi)裝填的固定相,再將上述油樣的正己烷溶液加入到分離柱中。分別用170mL正己烷沖洗出S組分,255mL甲苯:正己烷體積比為1:19的溶劑沖洗出A1組分,255mL甲苯:正己烷體積比為1:4的溶劑沖洗出A2組分,255mL甲苯:乙醇體積比為1:1的溶劑沖洗出A3組分。采用旋轉(zhuǎn)蒸發(fā)器蒸干S組分、A1組分、A2組分和A3組分 中的溶劑,得到S組分4.94克,A1組分1.56克,A2組分1.52克,A3組分1.83g,損失0.35克。實施例、對比例中所使用的原料油和分離后的亞組分的基本物性數(shù)據(jù)列于表1,亞組分S、亞組分A1、A2和A3的烴族組成數(shù)據(jù)列于表2。實施例2如圖1所示,將實施例1所得的S組分、A1組分和A2組分在反應(yīng)溫度為500℃、劑油質(zhì)量比為4,空速為16小時-1的條件下分別進行第一催化裂化、第二催化裂化和第三催化裂化;將所得的A3組分在精密高壓反應(yīng)釜內(nèi)進行加氫處理,得到的初餾點為160℃加氫生成油(HT-A3,烴族組成如表2所示),在反應(yīng)溫度為500℃、劑油質(zhì)量比為4,空速為16小時-1的條件下進行第四催化裂化;將第一催化裂化、第二催化裂化、第三催化裂化和第四催化裂化所得的催化裂化柴油和催化裂化重油全部返回加氫處理使用;原料的轉(zhuǎn)化率、總液收、輕質(zhì)油收率,還有六種主要產(chǎn)物干氣、液化氣、汽油、柴油、裂化重油和焦炭的產(chǎn)率,汽油中的硫含量和氮含量,如表4所示。從表4中數(shù)據(jù)可以看出,與對比例1中VGO直接催化裂化的實驗結(jié)果相比,將S組分、A1組分、A2組分和HT-A3組分分別催化裂化所得的液化氣、汽油分別匯總后,液化氣、汽油產(chǎn)率匯總結(jié)果1分別高于蠟油直接進行催化裂化的液化氣、汽油產(chǎn)率,同時汽油中的硫含量和氮含量明顯低于蠟油直接催化裂化的汽油硫含量和氮含量,說明采用本發(fā)明的方法將重油先進行分離處理以及加氫處理后再進行催化裂化,所得到的高價值產(chǎn)品產(chǎn)率及性質(zhì)優(yōu)于直接將重油進行催化裂化的產(chǎn)品。實施例3如圖2所示,將S組分和A1組分在反應(yīng)溫度為500℃、劑油質(zhì)量比為4, 空速為16小時-1的條件下分別進行第一催化裂化和第二催化裂化;將所得的A3組分在精密高壓反應(yīng)釜內(nèi)進行加氫處理,得到的初餾點為160℃加氫生成油(HT-A3,烴族組成如表2所示),在反應(yīng)溫度為500℃、劑油質(zhì)量比為4,空速為16小時-1的條件下與A2組分一起進行第三催化裂化;原料的轉(zhuǎn)化率、總液收、輕質(zhì)油收率,還有六種主要產(chǎn)物干氣、液化氣、汽油、柴油、裂化重油和焦炭的產(chǎn)率,汽油中的硫含量和氮含量,如表5所示。從表5中數(shù)據(jù)可以看出,與對比例1中VGO直接催化裂化的實驗結(jié)果相比,將S組分、A1組分以及A2與HT-A3的混合組分分別催化裂化所得的液化氣、汽油分別匯總后,液化氣、汽油產(chǎn)率匯總結(jié)果2分別高于蠟油直接進行催化裂化的液化氣、汽油產(chǎn)率,同時汽油中的硫含量和氮含量明顯低于蠟油直接催化裂化的汽油硫含量和氮含量,說明采用本發(fā)明的方法將重油先進行分離處理以及加氫處理后再進行催化裂化,所得到的高價值產(chǎn)品產(chǎn)率及性質(zhì)優(yōu)于直接將重油進行催化裂化的產(chǎn)品。實施例4將實施例1所得的S組分和加氫裂化尾油(HCW,來自石油化工科學研究院加氫裂化中型裝置,基本性質(zhì)如表1所示,烴族組成如表2所示)以1:1的質(zhì)量比混合的混合物在反應(yīng)溫度為500℃、劑油質(zhì)量比為4,空速為16小時-1的條件下進行催化裂化反應(yīng),其轉(zhuǎn)化率、總液收、輕質(zhì)油收率,還有六種主要產(chǎn)物干氣、液化氣、汽油、柴油、裂化重油和焦炭的產(chǎn)率,汽油中的硫含量和氮含量,如表6所示。從表6中可以看出,將S組分和加氫裂化尾油混合后進行催化裂化,所得液化氣和汽油產(chǎn)品產(chǎn)率高以及汽油中硫氮含量低。對比例1將VGO直接作為催化裂化原料,進入催化裂化單元,在反應(yīng)溫度為500℃、劑油質(zhì)量比為4,空速為16小時-1的條件下進行催化裂化反應(yīng),其轉(zhuǎn)化率、總液收、輕質(zhì)油收率,還有六種主要產(chǎn)物干氣、液化氣、汽油、柴油、裂化重油和焦炭的產(chǎn)率,汽油中的硫含量和氮含量如表4,5所示。表1重油原料及各烴族組分的基本性質(zhì)。項目SA1A2A3VGOHCW密度(100℃)/(g·cm-3)0.80860.86530.92650.97660.88250.7911黏度(100℃)/(mm2·s-1)4.8296.71710.46233.8039.84633.571殘?zhí)?,?lt;0.05<0.050.214.280.48<0.05重(C),%85.9087.2287.1484.0886.0785.59重(H),%13.9212.3010.369.1911.9914.34n(H)/n(C)1.941.691.431.311.672.03重(S)/(μg.g-1)6745004600464001700010重(N)/(μg.g-1)1.77.0266800018001.0沸程范圍/℃350~478357~525365~520392~558350~559350~496表2為S、A1、A2、A3、HT-A3和HCW的烴族組成,表中數(shù)據(jù)單位為質(zhì)量百分數(shù)為重%。烴類型SA1A2A3HT-A3HCW總飽和烴97.400022.799.4總芳烴2.6100.0100.060.077.30.6總單環(huán)芳烴2.674.324.79.429.20.6總雙環(huán)芳烴013.237.111.123.40雙環(huán)以上芳烴012.538.239.524.70膠質(zhì)00.00.040.00.00總計100100100100100100表3為MLC-500的基本物性項目MLC-500物理性質(zhì)比表面積/(m2·g-1)122孔體積/(cm3·g-1)0.184顆粒度,目70~270化學組成(w),%Na2O0.25Al2O356.4SiO236.9RE2O33.7微反活性(12小時老化)69表4為實施例2與對比例1的實驗數(shù)據(jù)。表5為實施例3與對比例1的實驗數(shù)據(jù)。表6為實施例4的實驗數(shù)據(jù)。項目實施例4原料S+HCW反應(yīng)溫度/℃500空速/h-116催化劑MLC-500劑油比(C/O)4轉(zhuǎn)化率(重),%91.99輕質(zhì)油收率(重),%70.95總液收(重),%96.40產(chǎn)品收率(重),%干氣0.82液化氣25.45汽油64.49柴油6.46裂化重油1.55焦炭1.23合計100汽油性質(zhì)硫含量(重),μg/g0.5氮含量(重),μg/g0.02當前第1頁1 2 3