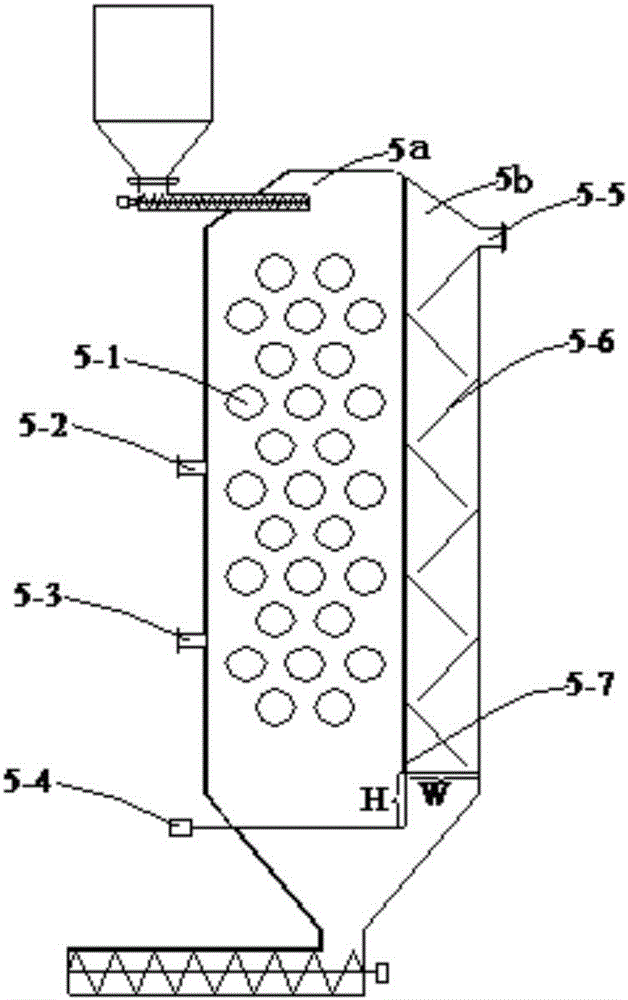
本發(fā)明涉及化工領(lǐng)域,尤其涉及一種具有內(nèi)置除塵裝置的生物質(zhì)熱解系統(tǒng)和方法。
背景技術(shù):
:生物質(zhì)作為地球第四大能源,儲量僅次于煤炭、石油、天然氣。同時,生物質(zhì)也是儲量最大的可再生能源,是最理想的化石能源替代能源。目前,生物質(zhì)能源的主要利用方式為直接焚燒、厭氧發(fā)酵、氣化、熱解等。其中直接焚燒熱效率低,不僅造成能源浪費,還造成一定的環(huán)境問題;厭氧發(fā)酵對原料要求較高,且占地較大、反應(yīng)時間長,無法大規(guī)模處理生物質(zhì)資源;氣化技術(shù)則受限于反應(yīng)器的不通用性、生物油問題及氣體熱值低等;生物質(zhì)熱解技術(shù)是將生物質(zhì)能源直接轉(zhuǎn)化為液體燃料最有效的途徑。生物質(zhì)熱解是指在無氧或限氧的條件下,將生物質(zhì)升溫至550℃左右,生物質(zhì)轉(zhuǎn)化為生物油、生物炭和熱解氣的過程。然而,市面上所有的熱解技術(shù)均存在生物油含塵量高的問題。目前的除塵技術(shù)主要為旋風(fēng)除塵技術(shù)、金屬濾網(wǎng)除塵技術(shù)、顆粒床除塵技術(shù)。旋風(fēng)除塵技術(shù)的除塵效率較低;金屬濾網(wǎng)除塵技術(shù)的承受溫度較低、易發(fā)生高溫腐蝕和氧化;顆粒床除塵技術(shù)效率較高。但是,目前的除塵技術(shù)主要采用外置式,高溫油氣除塵過程中均需加熱保溫,避免生物油的二次裂解或冷凝,造成生物油的損失。技術(shù)實現(xiàn)要素:鑒于現(xiàn)有技術(shù)的不足,本發(fā)明旨在提供一種具有內(nèi)置除塵裝置的生物質(zhì)熱解系統(tǒng)和方法。該系統(tǒng)及方法可有效提取生物質(zhì)中的生物油及熱解氣,并降低熱解產(chǎn)物的含塵量,具有較高的能源利用效率。本發(fā)明公開了一種具有內(nèi)置除塵裝置的生物質(zhì)熱解系統(tǒng),所述系統(tǒng)包括:反應(yīng)器、旋風(fēng)分離器、換熱器;所述反應(yīng)器具有生物質(zhì)入口、熱解油氣出口、生物炭出口;所述旋風(fēng)分離器具有熱解油氣入口,該熱解油氣入口用于接收由所述反應(yīng)器的熱解油氣出口排出的熱解油氣;所述換熱器具有生物炭入口,該生物炭入口用于接收由所述反應(yīng)器的生物炭出口排出的生物炭;其中,所述反應(yīng)器中具有沿所述反應(yīng)器高度方向布置的隔板,所述隔板將所述反應(yīng)器分隔為熱解區(qū)和除塵區(qū);所述熱解區(qū)和所述除塵區(qū)底部相通;所述反應(yīng)器具有相對布置的側(cè)壁a和側(cè)壁a',其中,所述除塵區(qū)包括相對布置的所述側(cè)壁a和所述隔板;并且,在所述側(cè)壁a和所述隔板上布置有多個斜板;所述斜板具有端部b和端部b',其中端部b固定在所述隔板或所述側(cè)壁a上,端部b'懸空;兩個相鄰的斜板的端部b分別固定在所述隔板和所述側(cè)壁a上,使得所述兩個相鄰的斜板交叉設(shè)置。進(jìn)一步的,所述反應(yīng)器中的斜板與水平方向的夾角為45°~75°。進(jìn)一步的,所述斜板在水平方向的投影為所述除塵區(qū)寬度的4/5~9/10;所述斜板的端部b'與相對側(cè)的所述隔板或所述側(cè)壁a的垂直距離為所述除塵區(qū)寬度的1/10~1/5。進(jìn)一步的,所述兩個相鄰的斜板之間的夾角為30°~90°。進(jìn)一步的,所述除塵區(qū)橫截面積為所述熱解區(qū)橫截面積的1/32~1/4。上述的系統(tǒng)中,所述隔板的下部設(shè)置有料位計;所述料位計與所述隔板下端的垂直距離為100~500㎜;所述熱解區(qū)中自上而下設(shè)置有輻射管;所述輻射管與燃?xì)馊肟诤蜔煔獬隹谶B接。上述的系統(tǒng)中,進(jìn)一步包括熱解油氣單元、生物炭單元、煙氣單元;所述熱解油氣單元包括依次連接的反應(yīng)器、旋風(fēng)分離器、二級干燥器、凈化裝置、氣柜和油罐、燃?xì)膺M(jìn)口;所述生物炭單元包括依次連接的反應(yīng)器、換熱器、生物炭儲倉;所述煙氣單元包括依次連接的反應(yīng)器、換熱器、一級干燥器。本發(fā)明還公開了一種利用上述系統(tǒng)處理生物質(zhì)的方法,所述方法包括以下步驟:將生物質(zhì)經(jīng)由所述生物質(zhì)入口運送至所述反應(yīng)器中,進(jìn)行熱解反應(yīng)得到高溫生物炭和熱解油氣,所述熱解油氣進(jìn)入所述除塵區(qū)進(jìn)行除塵,得到初步除塵的熱解油氣;所述初步除塵的熱解油氣經(jīng)過所述熱解油氣單元處理后,得到生物油和熱解氣;所述高溫生物炭經(jīng)過所述生物炭單元處理后,得到低溫生物炭。上述處理生物質(zhì)的方法中,所述生物質(zhì)粒徑≤3mm、含水率≤10wt%。上述處理生物質(zhì)的方法中,所述高溫生物炭的溫度為450~650℃,所述低溫生物炭的溫度為200~350℃。本發(fā)明的系統(tǒng)和方法可有效提取生物質(zhì)中的生物油和熱解氣,采用內(nèi)置除塵裝置,可利用系統(tǒng)內(nèi)部顯熱,無需外加熱源,能源利用效率高。該系統(tǒng)可有效降低熱解油氣的含塵量,避免生物油的冷凝及二次裂解,大大簡化了熱解油氣的后續(xù)處理工序。產(chǎn)生的熱解油氣可用于生物質(zhì)原料的干燥,同時,生物質(zhì)原料可以對熱解油氣進(jìn)行過濾,該系統(tǒng)可用于處理多種生物質(zhì)原料。附圖說明圖1是本發(fā)明實施例中具有內(nèi)置除塵裝置的生物質(zhì)熱解系統(tǒng)的流程示意圖。圖2是本發(fā)明實施例中熱解反應(yīng)器的裝置示意圖。附圖中的附圖標(biāo)記如下:1、一級回轉(zhuǎn)窯干燥器;2、二級回轉(zhuǎn)窯干燥器;3、料倉;4、進(jìn)料螺旋;5、熱解反應(yīng)器;5a、熱解區(qū);5b、除塵區(qū);5-1、輻射管;5-2、燃?xì)膺M(jìn)口;5-3、煙氣出口;5-4、料位計;5-5、熱解油氣出口;5-6、斜板;5-7、隔板;6、旋風(fēng)旋風(fēng)分離器;7、灰室;8、凈化裝置;9、氣柜;10、油罐;11、出料螺旋;12、換熱器;13、生物炭儲倉。具體實施方式以下結(jié)合附圖和實施例,對本發(fā)明的具體實施方式進(jìn)行更加詳細(xì)的說明,以便能夠更好地理解本發(fā)明的方案以及其各個方面的優(yōu)點。然而,以下描述的具體實施方式和實施例僅是說明的目的,而不是對本發(fā)明的限制。根據(jù)圖1所示的流程示意圖,可以將本發(fā)明中具有內(nèi)置除塵裝置的生物質(zhì)熱解系統(tǒng)分為三個單元:熱解油氣單元、生物炭單元、煙氣單元。以下分別結(jié)合該三個單元的流程圖對本發(fā)明的系統(tǒng)和方法進(jìn)行詳細(xì)的介紹。①熱解油氣單元包括依次連接的反應(yīng)器、旋風(fēng)分離器、二級干燥器、凈化裝置、氣柜和油罐、燃?xì)膺M(jìn)口。本發(fā)明實施例中,上述裝置分別為熱解反應(yīng)器5、旋風(fēng)分離器6、二級回轉(zhuǎn)窯干燥器2、凈化裝置8、氣柜9和油罐10、燃?xì)膺M(jìn)口5-2。i本文首先對熱解反應(yīng)器5進(jìn)行了介紹:由圖2,熱解反應(yīng)器5為方形立式結(jié)構(gòu),并且頂部和底部的主視剖面圖均為梯形。熱解反應(yīng)器5中設(shè)置有隔板5-7,其沿反應(yīng)器的高度方向布置,將反應(yīng)器縱向分隔為兩個區(qū)域:熱解區(qū)5a和除塵區(qū)5b。并且,熱解區(qū)5a和除塵區(qū)5b的底部是連通的。本發(fā)明實施例的反應(yīng)器中具有側(cè)壁a和側(cè)壁a'。并且,側(cè)壁a和側(cè)壁a'相對布置,側(cè)壁a和隔板5-7相對布置,隔板5-7和側(cè)壁a'也相對布置。即在本發(fā)明的方形立式反應(yīng)器中,側(cè)壁a、隔板5-7、側(cè)壁a'相互平行。并且,除塵區(qū)5b包括側(cè)壁a和隔板5-7,熱解區(qū)5a包括隔板5-7和側(cè)壁a'。在除塵區(qū)5b的側(cè)壁a和隔板5-7上,自下而上均勻布置有多個斜板5-6。其在側(cè)壁a和隔板5-7上的數(shù)量分別為m和n。此處,m和n所代表的數(shù)值可以相同也可以不同。每個斜板5-6都有兩個端部,分別命名為端部b和端部b'。其中,端部b固定在側(cè)壁a或隔板5-7上,端部b'懸空在除塵區(qū)5b中。并且,當(dāng)斜板5-6的端部b固定在側(cè)壁a上時,其相鄰的斜板5-6的端部b均固定在隔板5-7上,使得每兩個相鄰的斜板5-6呈現(xiàn)交叉設(shè)置的方式。本發(fā)明實施例中,除塵區(qū)5b的寬度為W,除塵區(qū)5b橫截面積為熱解區(qū)5a橫截面積的1/32~1/4。本實施例中,斜板5-6與水平方向的夾角均為45°~75°。并且,斜板5-6在水平方向的投影均為4/5W~9/10W。斜板5-6的端部b'與相對側(cè)的隔板5-7或側(cè)壁a的垂直距離為1/10W~1/5W。每兩個相鄰的斜板5-6之間的夾角的范圍均為30°~90°。在側(cè)壁a上布置的最上端的斜板5-6之上,設(shè)置有熱解油氣出口5-5。熱解區(qū)5a中設(shè)置有多個輻射管5-1,其在熱解區(qū)5a中自上而下分層分布。輻射管5-1的兩端分別與燃?xì)膺M(jìn)口5-2和煙氣出口5-3連接,并且燃?xì)膺M(jìn)口5-2的水平位置在煙氣出口5-3的水平位置之上。熱解反應(yīng)器5包括料倉3和進(jìn)料螺旋4。其中,進(jìn)料螺旋4位于料倉3的下端,并且與熱解區(qū)5a頂部的生物質(zhì)入口連接。同時,料倉3依次與二級回轉(zhuǎn)窯干燥器2、一級回轉(zhuǎn)窯干燥器1連接。熱解區(qū)5a底部的梯形部分設(shè)置有料位計5-4,其下部設(shè)置有出料螺旋11,出料螺旋11與熱解反應(yīng)器5底部的生物炭出口連接。并且,料位計5-4與隔板5-7下端的垂直距離H為100~500㎜。ⅱ熱解反應(yīng)器5中進(jìn)行的熱解反應(yīng)過程如下:生物質(zhì)原料的粒徑≤3mm、含水率≤50wt%(wt%為質(zhì)量百分比),將其依次運送至一級回轉(zhuǎn)窯干燥器1、二級回轉(zhuǎn)窯干燥器2中。干燥后的生物質(zhì)含水率≤10wt%。然后將干燥后的生物質(zhì)運送至料倉3中,在進(jìn)料螺旋4的作用下通過生物質(zhì)入口輸送至熱解區(qū)5a中,其中輻射管的溫度為650~800℃,熱解反應(yīng)得到高溫生物炭和熱解油氣。熱解油氣的溫度為450~600℃,其經(jīng)熱解區(qū)5a和除塵區(qū)5b底部相通的位置經(jīng)由熱解區(qū)5a運行至除塵區(qū)5b中。熱解油氣不斷的與除塵區(qū)5b中的斜板5-6發(fā)生碰撞,其中的粉塵就會降落至熱解反應(yīng)器5底部,從而可對熱解油氣進(jìn)行初步的除塵。熱解反應(yīng)器5中內(nèi)置的除塵區(qū)5b對熱解油氣的除塵效率≥85wt%。初步除塵的熱解油氣經(jīng)由熱解油氣出口5-5排出,并運送至旋風(fēng)分離器6中,進(jìn)行進(jìn)一步的分離除塵。沉積在底部的粉塵排出至灰室7中。上層除塵后的熱解油氣,經(jīng)由旋風(fēng)分離器6上部的氣液出口排出至二級回轉(zhuǎn)窯干燥器2中,對其中的生物質(zhì)原料進(jìn)行二級干燥,同時生物質(zhì)原料還可對熱解油氣進(jìn)行過濾處理。然后,熱解油氣經(jīng)由二級回轉(zhuǎn)窯干燥器2上的油氣出口,被運送至凈化裝置8中,經(jīng)過凈化得到生物油和熱解氣。生物油存儲于油罐10中,熱解氣存儲于氣柜9中。熱解氣經(jīng)由燃?xì)膺M(jìn)口5-2被運送至輻射管5-1中,為熱解反應(yīng)器5提供熱量。由于熱解油氣溫度較高并且具有腐蝕性,因此,斜板5-6的材料選擇的是耐高溫且耐腐蝕的不銹鋼。同時,隔板5-7是由耐熱且易傳熱的不銹鋼材料制作而成的,使得熱解區(qū)5a的熱量可以傳遞到除塵區(qū)5b中,避免熱解油氣在除塵區(qū)5b中冷凝。②生物炭單元包括依次連接的反應(yīng)器、換熱器、生物炭儲倉。本發(fā)明實施例中,上述各裝置分別為熱解反應(yīng)器5、換熱器12、生物炭儲倉13。上述①中熱解反應(yīng)得到的高溫生物炭溫度為450~650℃,隨著熱解反應(yīng)的進(jìn)行逐漸堆至熱解反應(yīng)器5底部。當(dāng)堆積的高溫生物炭高度達(dá)到料位計5-4上部時,啟動出料螺旋11;直到高溫生物炭高度降低至料位計5-4下部時,關(guān)閉出料螺旋11,停止出料。高溫生物炭經(jīng)由出料螺旋11出料后,被運送至換熱器12中,并且與其中的低溫?zé)煔膺M(jìn)行換熱,導(dǎo)致高溫生物炭溫度降低,得到200~350℃的低溫生物炭,然后儲存在生物炭儲倉13中。③煙氣單元包括依次連接的反應(yīng)器、換熱器、一級干燥器。本發(fā)明實施例中,上述裝置分別為熱解反應(yīng)器5、換熱器12、一級回轉(zhuǎn)窯干燥器1。由輻射管5-1的煙氣出口5-3排出的低溫?zé)煔鉁囟葹?0~150℃,低溫?zé)煔獗贿\送至換熱器12中,與其中的高溫生物炭進(jìn)行換熱,得到升溫后煙氣,其溫度為110~180℃。升溫后煙氣輸送至回一級轉(zhuǎn)窯干燥器1中對其中的生物質(zhì)原料進(jìn)行一級干燥處理。實施例選用粒徑≤3㎜、含水率為33wt%的木屑作為生物質(zhì)原料,將木屑依次運送到一級回轉(zhuǎn)窯干燥器1、二級回轉(zhuǎn)窯干燥2中進(jìn)行干燥,干燥后的木屑含水率為8wt%。將干燥后的木屑輸送至料倉3中,由進(jìn)料螺旋4輸送至熱解區(qū)5a中。木屑依靠自身重力下落,并與輻射管5-1接觸發(fā)生熱解反應(yīng),其中輻射管5-1的溫度為700℃。熱解反應(yīng)得到高溫生物炭和熱解油氣。高溫生物炭堆積至熱解反應(yīng)器5底部,通過料位計5-4控制出料,由出料螺旋11排出至換熱器12中。熱解油氣溫度為500℃,由熱解區(qū)5a運行至除塵區(qū)5b中進(jìn)行初步除塵,然后依次經(jīng)旋風(fēng)分離器6、二級回轉(zhuǎn)窯干燥器2、凈化裝置8處理后得到生物油和熱解氣。生物油儲存在油罐10中,熱解氣儲存在氣柜9中。熱解氣可經(jīng)由燃?xì)膺M(jìn)口5-2運送至輻射管5-1中,用于提供熱量。輻射管5-1排出的溫度為120℃的低溫?zé)煔?,輸送至換熱器12中,與其中的高溫生物炭換熱,得到升溫后煙氣,溫度為180℃,生物炭換熱降溫后儲存在生物炭儲倉13中。升溫后煙氣運送至一級回轉(zhuǎn)窯干燥器1中對木屑進(jìn)行一級干燥。熱解油氣用于在二級回轉(zhuǎn)窯干燥器2中,對經(jīng)過一級干燥的木屑進(jìn)行二級干燥。該實施例取得的有益效果見如下各表。表1產(chǎn)物分布生物油/%生物炭/%熱解氣/%熱解水/%43.425.617.513.5(備注:%為質(zhì)量百分?jǐn)?shù))表2除塵前后熱解油氣含塵量對比除塵前熱解油氣含塵量除塵后熱解油氣含塵量138g/Nm316g/Nm3由表1和表2可知,本發(fā)明實施例可有效提取生物質(zhì)中的能源物質(zhì),并且具有較優(yōu)的除塵效果。需要說明的是,以上參照附圖所描述的各個實施例僅用以說明本發(fā)明而非限制本發(fā)明的范圍,本領(lǐng)域的普通技術(shù)人員應(yīng)當(dāng)理解,在不脫離本發(fā)明的精神和范圍的前提下對本發(fā)明進(jìn)行的修改或者等同替換,均應(yīng)涵蓋在本發(fā)明的范圍之內(nèi)。此外,除上下文另有所指外,以單數(shù)形式出現(xiàn)的詞包括復(fù)數(shù)形式,反之亦然。另外,除非特別說明,那么任何實施例的全部或一部分可結(jié)合任何其它實施例的全部或一部分來使用。當(dāng)前第1頁1 2 3