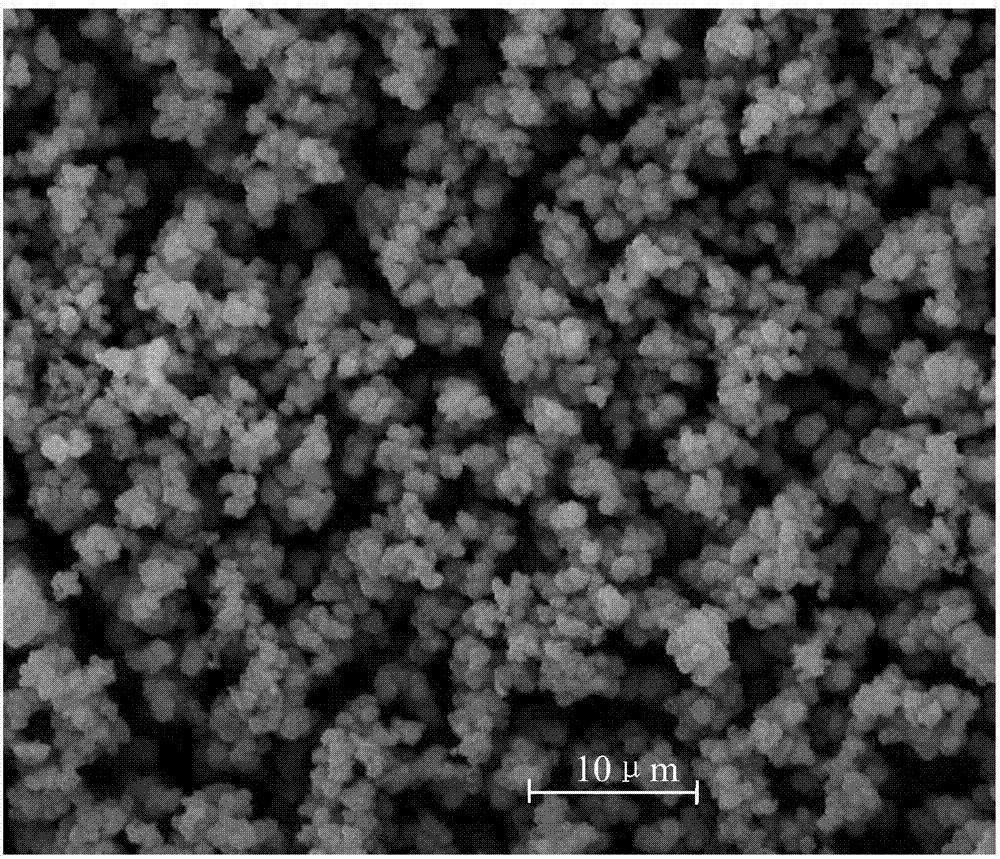
本發(fā)明屬于金屬材料抗高溫氧化領(lǐng)域,具體涉及一種基于鹵素效應(yīng)和預(yù)處理得到陶瓷涂層提高鈦基合金抗高溫氧化性能的方法。技術(shù)背景TiAl基金屬間化合物合金(簡稱TiAl合金),具有密度低(為目前廣泛使用Ni基合金的50%),同時比強度和比剛度高且高溫蠕變性能較好等特點??蓮V泛應(yīng)用于汽車或航空發(fā)動機的高溫部件,如:壓氣機葉片、排氣閥和增壓渦輪等,特別是在航空高溫結(jié)構(gòu)材料方面,TiAl基合金是替代鎳基高溫合金的理想材料,被認為是極具應(yīng)用前景的新型輕質(zhì)高溫結(jié)構(gòu)材料之一。然而,當TiAl合金使用溫度超過750℃時,TiAl合金抗高溫氧化性能迅速惡化,由于在更高溫度下,鈦和鋁與氧的親和能力非常接近,合金表面形成的是TiO2和Al2O3混合層,氧化膜的生長速率很快,容易發(fā)生剝落。這嚴重影響了合金的使用性能。為克服以上不足,國內(nèi)外學(xué)者采用了合金化、離子注入法、表面涂層和陽極氧化等方法改性來提高鈦鋁合金的服役溫度。合金設(shè)計主要包括兩個方面,一是提高TiAl合金中基本元素Al的含量,這固然有利于其抗氧化性能的改善,但Al含量不宜太高,否則一旦析出脆性的TiAl3將影響其力學(xué)性能。二是通過加入第三種或者多種合金元素,如:Nb,Sb,Si,Cr,Y,Mo等雖然也可有效改善TiAl合金的高溫抗氧化性能,但加入量過高通常會導(dǎo)致TiAl合金力學(xué)性能下降。離子注入法雖然注入量可控、重復(fù)性較好,但涉及的設(shè)備較昂貴、生產(chǎn)效率較低,且對TiAl合金成分改變的深度僅局限在表面較淺的范圍(<1μm)。而防護涂層,如金屬涂層MCrAl(Y)、陶瓷涂層(如SiO2、Al2O3和ZrO2等)以及擴散涂層(如Al、Si等)等雖然可作為屏蔽層阻擋氧氣向基體滲透,但各自仍存在一定的問題。金屬涂層與基體間的互擴散較嚴重,界面易析出硬脆相,同時產(chǎn)生柯肯達爾孔洞,嚴重降低了涂層與基體的結(jié)合強度;擴散涂層與基體熱膨脹系數(shù)相差較大。技術(shù)實現(xiàn)要素:本發(fā)明的目的是針對現(xiàn)有鈦鋁合金抗高溫氧化能力不足,提供一種基于鹵素效應(yīng)和預(yù)處理得到陶瓷涂層提高鈦基合金抗高溫氧性能的方法,所獲得的復(fù)合涂層與基體之間具有優(yōu)異的結(jié)合力,顯著提高鈦基合金在1000℃高溫下的抗氧化性能。一種基于鹵素效應(yīng)和預(yù)處理得到陶瓷涂層提高鈦基合金抗高溫氧化性能的方法,包括以下步驟:1)首先去除鈦基合金基體的表面氧化物,然后清洗、干燥;2)將醋酸銨、氯化銨和前軀體氟硅酸鹽與水混合,室溫下攪拌2~48h,得到前軀體溶液;其中醋酸銨、氯化銨和前軀體氟硅酸鹽的摩爾比為(0.1-5):(0.1-3):(0.1~1);3)在三電極槽中加入配好的前軀體溶液,以鈦基合金基體作為工作電極,鉑片或石墨作為對電極,電極間距控制在1-10cm,控制沉積電位為-0.1V~-5.0V進行電沉積,沉積時間為50s~3000s,然后將工作電極水洗后于40~150℃烘干,在鈦基合金表面得到含氟微納米SiO2涂層;4)將表面覆蓋有含氟微納米SiO2涂層的鈦基合金,置于氬氣與氧氣的混合氣體中,于900~1000℃下熱處理10~100min,即制得鈦基合金抗高溫氧化復(fù)合涂層。進一步,所述的鈦基合金為含鋁的鈦基合金。更進一步,所述的鈦基合金選自Ti3-Al、Ti-Al、Ti-Al3、Ti-6Al-4V、TiAlNb、Ti-47Al-2Cr-2Nb中的一種。進一步,步驟1)中,可用砂紙將鈦基合金基體打磨去除表面氧化物;清洗試劑可采用丙酮、乙醇等,優(yōu)選采用超聲進行多次清洗。進一步,步驟2)中,氟硅酸鹽優(yōu)選六氟硅酸鈉、六氟硅酸鉀或六氟硅酸銨中的一種或兩種及以上混合。更優(yōu)選所述的氟硅酸鹽含有六氟硅酸銨,最優(yōu)選為六氟硅酸銨。進一步,步驟2)中,醋酸銨、氯化銨和前軀體氟硅酸鹽的摩爾比優(yōu)選為1:0.075-0.1:0.1-0.2,最優(yōu)選為1:0.1:0.2。進一步,步驟3)中,對電極優(yōu)選為石墨電極。進一步,步驟3)中,沉積電位優(yōu)選為-1.0V~-3.0V,更優(yōu)選為-2.0V~-2.5V,最優(yōu)選-2.0V。進一步,步驟3)中,沉積時間優(yōu)選為500s-1500s,更優(yōu)選為1000-1500s,最優(yōu)選為1000s。進一步,步驟4)中,氬氣與氧氣的混合氣體中,氧氣體積含量為5%-20%,優(yōu)選10%。進一步,步驟4)中,熱處理溫度優(yōu)選為900~1000℃,更優(yōu)選為950-1000℃,最優(yōu)選為1000℃。進一步,步驟4)中,熱處理時間優(yōu)選為10~60min,更優(yōu)選為30-60min,最優(yōu)選為30min。進一步,所述的制備方法由步驟1)~步驟4)組成。本發(fā)明的有益效果是:(1)與常規(guī)通過sol-gel法制備的SiO2涂層不同的是,本發(fā)明通過電沉積技術(shù)在鈦基合金表面制備得到微納米級SiO2涂層,該微納米SiO2涂層與基體存在化學(xué)鍵合作用,因而具有優(yōu)異的結(jié)合力;同時,又因為以氟硅酸鹽為硅源,在電沉積SiO2的過程中帶入一定量的F元素到基體表面。經(jīng)過高溫預(yù)氧化,SiO2可與基體中的Ti和Al元素發(fā)生固相化學(xué)反應(yīng),在金屬表面形成連續(xù)而致密的玻璃態(tài)保護層;同時,基體表面由于F元素的存在,使得在預(yù)氧化過程中,發(fā)生鹵素效應(yīng),優(yōu)先促進形成連續(xù)致密的Al2O3膜,與是直接氧化不同的是預(yù)氧化處理,降低了氧分壓,從而使得Al2O3膜更為純凈致密,使抗高溫氧化能力進一步提高。預(yù)氧化處理可內(nèi)部原位形成連續(xù)致密的Al2O3膜,外部形成連續(xù)而致密的玻璃態(tài)SiO2保護層,該復(fù)合保護層協(xié)同作用,可阻有效止空氣中的氧向基體擴散,同時阻止金屬內(nèi)部的陽離子向外擴散,進而提高鈦基合金的抗高溫氧化性能。(2)本發(fā)明制備工藝簡單、操作方便、效率高、易于實現(xiàn)。附圖說明圖1為1000℃循環(huán)氧化100h的動力學(xué)曲線(曲線1為裸TiAl合金,曲線2為TiAl合金按照實施例4在六氟硅酸銨中-2.0V沉積電位下電沉積1000s所得試樣)。圖2為實施例4制備的含F(xiàn)元素的SiO2涂層的掃描電子顯微鏡照片。圖3為實施例4所得試樣經(jīng)1000℃循環(huán)氧化100h后的掃描電子顯微鏡照片。具體實施方式下面以具體實施例對本發(fā)明的技術(shù)方案做進一步說明,但本發(fā)明的保護范圍不限于此:實施例1首先用砂紙將鈦鋁合金試樣(鈦鋁原子比為1:1)打磨去除表面氧化物,然后依次在丙酮和乙醇中超聲清洗10min,最后用熱風吹干待用。依次往燒杯中加入1mol醋酸氨、0.1mol氯化銨、0.2mol六氟硅酸銨、100mL水,室溫下攪拌40h待用。以打磨清洗好的鈦鋁合金試樣(鈦鋁原子比為1:1)作為陰極,石墨電極作為對電極,Ag/AgCl電極作為參比電極,電極間距控制在1cm,控制沉積電位為-1V,沉積時間為1500s,沉積完成后將工作電極用去離子水沖洗后于40℃烘干,得到含F(xiàn)的微納米SiO2涂層。隨后,將該覆蓋有含F(xiàn)的微納米SiO2涂層的鈦鋁合金置于混合氣體(90%的氬氣與10%的氧氣)中,于900℃下熱處理60min,得到Al2O3-SiO2復(fù)合涂層,采用1000℃循環(huán)氧化100h后單位面積的增重來評估其抗高溫氧化性能,具體結(jié)果如表1。表1裸TiAl合金和覆蓋有抗高溫氧化涂層的TiAl合金試樣實驗結(jié)果樣品增重mg/cm2裸TiAl合金86.38覆蓋有抗高溫氧化復(fù)合涂層的TiAl合金1.84實施例2首先用砂紙將鈦鋁合金試樣(鈦鋁原子比為3:1)打磨去除表面氧化物,然后依次在丙酮和乙醇中超聲清洗10min,最后用熱風吹干待用。依次往燒杯中加入2mol醋酸氨、0.15mol氯化銨、0.2mol六氟硅酸鉀、100mL水,室溫下攪拌40h待用。以打磨清洗好的鈦鋁合金試樣(鈦鋁原子比為3:1)作為陰極,石墨電極作為對電極,Ag/AgCl電極作為參比電極,電極間距控制在10cm,控制沉積電壓為-3.0V,沉積時間為500s,沉積完成后將工作電極用去離子水沖洗后于150℃烘干,得到含F(xiàn)的微納米SiO2涂層。隨后,將該覆蓋有含F(xiàn)的微納米SiO2涂層的鈦鋁合金置于混合氣體(90%的氬氣與10%的氧氣)中,于1000℃下熱處理10min,得到Al2O3-SiO2復(fù)合涂層,抗高溫氧化性能評估同實施例1,實驗結(jié)果列于表2。表2裸TiAl合金和覆蓋有抗高溫氧化涂層的Ti3Al合金試樣實驗結(jié)果樣品增重mg/cm2裸TiAl合金86.38覆蓋有抗高溫氧化涂層的Ti3Al合金6.36實施例3首先用砂紙將鈦鋁合金試樣(鈦鋁原子比為3:1)打磨去除表面氧化物,然后依次在丙酮和乙醇中超聲清洗10min,最后用熱風吹干待用。依次往燒杯中加入2mol醋酸氨、0.15mol氯化銨、0.1mol六氟硅酸銨、0.1mol六氟硅酸鉀、100mL水,室溫下攪拌20h待用。打磨清洗好的鈦鋁合金試樣(鈦鋁原子比為3:1)作為陰極,石墨電極作為對電極,Ag/AgCl電極作為參比電極,電極間距控制在5cm,控制沉積電位為-3.0V,沉積時間為500s,沉積完成后將工作電極用去離子水沖洗后于150℃烘干,得到含F(xiàn)的微納米SiO2涂層。隨后,將該覆蓋有含F(xiàn)的微納米SiO2涂層的鈦鋁合金置于混合氣體(90%的氬氣與10%的氧氣)中,于900℃下熱處理30min,得到Al2O3-SiO2復(fù)合涂層,抗高溫氧化性能評估同實施例1,實驗結(jié)果列于表3。表3裸TiAl合金和覆蓋有抗高溫氧化涂層的Ti3Al合金試樣實驗結(jié)果樣品增重mg/cm2裸TiAl合金86.38覆蓋有抗高溫氧化涂層的Ti3Al合金5.75實施例4首先用砂紙將鈦鋁合金試樣(鈦鋁原子比為1:1)打磨去除表面氧化物,然后依次在丙酮和乙醇中超聲清洗10min,最后用熱風吹干待用。依次往燒杯中加入1mol醋酸氨、0.1mol氯化銨、0.2mol六氟硅酸銨、100mL水,室溫下攪拌40h待用。打磨清洗好的鈦鋁合金試樣(鈦鋁原子比為1:1)作為陰極,石墨電極作為對電極,Ag/AgCl電極作為參比電極,電極間距控制在5cm,控制沉積電位為-2.0V,沉積時間為1000s,沉積完成后將工作電極用去離子水沖洗后于100℃烘干,得到含F(xiàn)的微納米SiO2涂層。隨后,將該覆蓋有含F(xiàn)的微納米SiO2涂層的鈦鋁合金置于混合氣體(90%的氬氣與10%的氧氣)中,于1000℃下熱處理30min,得到Al2O3-SiO2復(fù)合涂層,抗高溫氧化性能評估同實施例1,實驗結(jié)果列于表4。表4裸TiAl合金和覆蓋有抗高溫氧化涂層的TiAl合金試樣實驗結(jié)果樣品增重mg/cm2裸TiAl合金86.38覆蓋有抗高溫氧化涂層的TiAl合金0.74實施例5具體步驟同實施例4,所不同的是改變了使用的鈦鋁合金基體,抗高溫氧化性能評估同實施例1,實驗結(jié)果列于表5。表5不同鈦鋁合金基體實驗結(jié)果樣品增重mg/cm2Ti3-Al4.41Ti-Al31.04Ti-6Al-4V6.58Ti-47Al-2Cr-2Nb0.95實施例6具體步驟同實施例4,所不同的是改變了SiO2電沉積時間,分別為500s、800s、1000s、1500s。抗高溫氧化性能評估同實施例1,實驗結(jié)果列于表6。表6不同電沉積時間實驗結(jié)果樣品增重mg/cm2500s10.86800s4.551000s0.741500s1.57實施例7具體步驟同實施例4,所不同的是改變了SiO2電沉積沉積電位,分別為-1.0V、-1.5V、-2.0V、-2.5V、-3.0V??垢邷匮趸阅茉u估同實施例1,實驗結(jié)果列于表7。表7不同電沉積電流密度實驗結(jié)果實施例8具體步驟同實施例4,所不同的是改變了預(yù)氧化溫度,分別為900℃、950℃、1000℃。抗高溫氧化性能評估同實施例1,實驗結(jié)果列于表8。表8不同預(yù)氧化溫度實驗結(jié)果樣品增重mg/cm2900℃3.12950℃2.021000℃0.74實施例9具體步驟同實施例4,所不同的是改變了預(yù)氧時間,分別為0min、10min、30min、60min??垢邷匮趸阅茉u估同實施例1,實驗結(jié)果列于表9。表9不同預(yù)氧化時間實驗結(jié)果樣品增重mg/cm20min5.4210min4.3230min0.7460min0.76實施例10具體步驟同實施例4,所不同的是對電極改變?yōu)殂K片??垢邷匮趸阅茉u估同實施例1,實驗結(jié)果列于表10。表10不同對電極的實驗結(jié)果樣品增重mg/cm2鉑片2.73石墨0.74實施例11具體步驟同實施例4,所不同的是改變了不同氟硅酸鹽作為硅源,分別為六氟硅酸鈉、六氟硅酸鉀、六氟硅酸氨、六氟硅酸氨+六氟硅酸鈉(摩爾比1∶1)??垢邷匮趸阅茉u估同實施例1,實驗結(jié)果列于表11。表11不同氟硅酸鹽作為硅源實驗結(jié)果樣品增重mg/cm2六氟硅酸鈉4.62六氟硅酸鉀3.19六氟硅酸銨0.74六氟硅酸銨+六氟硅酸鈉(摩爾比1∶1)2.09當前第1頁1 2 3