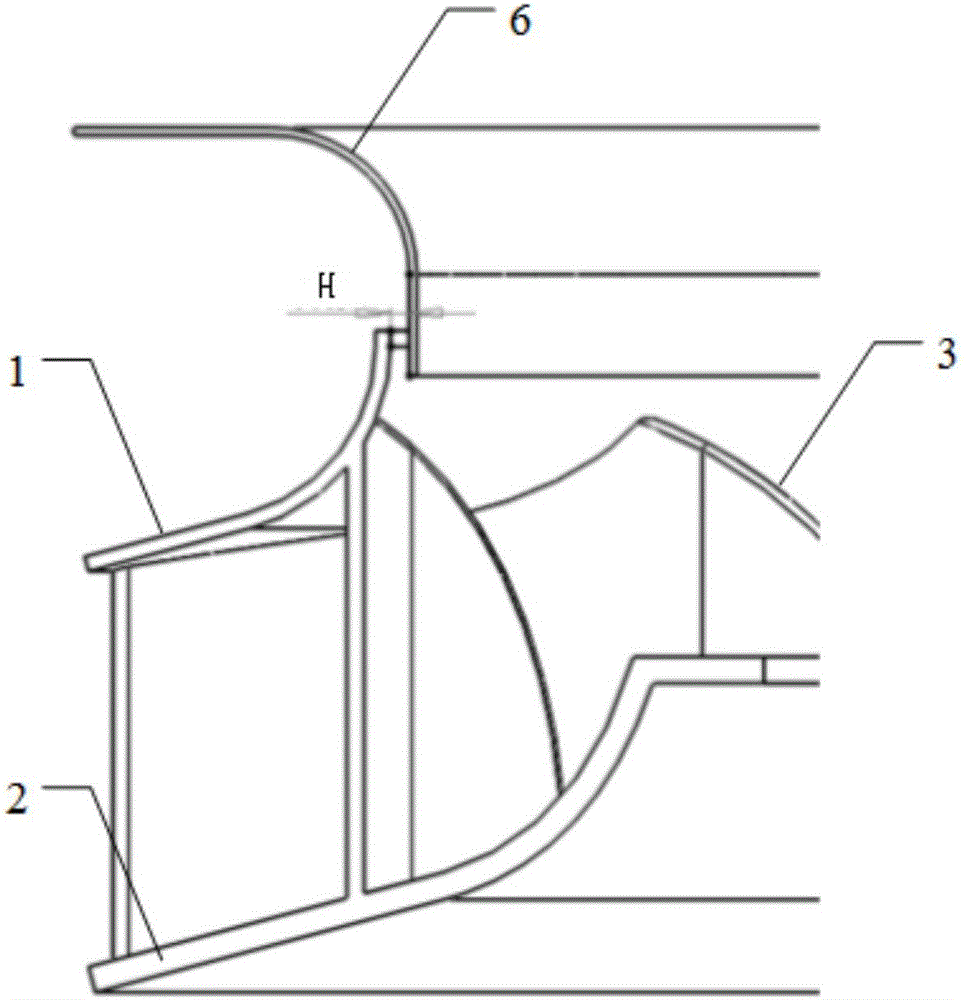
本發(fā)明實(shí)施例涉及風(fēng)機(jī)
技術(shù)領(lǐng)域:
,具體涉及一種后向離心葉輪。
背景技術(shù):
:離心風(fēng)機(jī)用于將軸向到來氣流轉(zhuǎn)變成周向氣流,而離心風(fēng)機(jī)葉輪是離心風(fēng)機(jī)的重要部件。現(xiàn)有技術(shù)中,后向離心風(fēng)機(jī)被廣泛用于對聲學(xué)品質(zhì)要求較高的領(lǐng)域。隨著空氣動力學(xué)的不斷進(jìn)步,各種風(fēng)機(jī)的葉輪研發(fā)都在采用更新穎的設(shè)計(jì)以獲得更高的效率、更低的噪聲、更高的聲學(xué)品質(zhì)。對于后向離心風(fēng)機(jī)而言,效率和噪音往往是相斥的,高效率往往將帶來較高的噪音。圖1為現(xiàn)有技術(shù)中的后向離心葉輪的結(jié)構(gòu),包括輪蓋1、輪盤2及位于輪蓋1和輪盤2之間的葉片3,輪蓋1的入口端為光滑圓弧封閉結(jié)構(gòu),導(dǎo)風(fēng)圈伸入輪蓋1且與輪蓋1之間具有間隙,間隙部分就會有較大的氣流速度,從而在間隙部分就會產(chǎn)生較大噪音并且還可能產(chǎn)生嘯叫聲。技術(shù)實(shí)現(xiàn)要素:本發(fā)明實(shí)施例提供一種后向離心葉輪,在輪蓋入口端開一定順序排列的槽形狀,減小入口端與導(dǎo)風(fēng)圈間隙處的氣流速度及抑制渦流產(chǎn)生,使從間隙泄漏的氣流分段排出,不產(chǎn)生混流,從而起到降低噪聲的目的。本發(fā)明實(shí)施例一種后向離心葉輪的技術(shù)方案包括:輪蓋、輪盤及位于所述輪蓋和所述輪盤之間的葉片,其特征在于,所述輪蓋入口端設(shè)有若干間隔設(shè)置的齒和槽;每一相鄰的所述齒和所述槽構(gòu)成一個(gè)齒槽單元,在所述齒槽單元的外邊緣處,槽寬度與齒寬度之比為0.8~1.2,所述槽寬度與槽深度之比為1~1.5。優(yōu)選的,在上述后向離心葉輪的技術(shù)方案中,在所述齒槽單元中,所述槽的兩側(cè)面的切線的延長線的夾角為0°≤α≤120°。優(yōu)選的,在上述后向離心葉輪的技術(shù)方案中,在所述齒槽單元中,所述槽的兩側(cè)面中的任一個(gè)或兩個(gè)為傾斜面,所述傾斜面相對于所述槽外邊緣所在平面傾斜。優(yōu)選的,在上述后向離心葉輪的技術(shù)方案中,在所述齒槽單元中,所述槽的兩側(cè)面均為傾斜面,且所述槽的兩側(cè)面的切線的延長線的夾角為0°≤α≤45°。優(yōu)選的,在上述后向離心葉輪的技術(shù)方案中,若干個(gè)所述齒槽單元等分成若干個(gè)齒槽組合,每一所述齒槽組合中的所述齒槽單元相異。優(yōu)選的,在上述后向離心葉輪的技術(shù)方案中,每一所述齒槽組合由兩個(gè)齒槽單元組成,在所述齒槽單元的外邊緣處,其中一個(gè)所述齒槽單元的槽寬度與齒寬度之比為1.0,另一個(gè)所述齒槽單元的槽寬度與齒寬度之比為1.1。優(yōu)選的,在上述后向離心葉輪的技術(shù)方案中,在所述齒槽單元的外邊緣處,所述齒厚度與所述槽寬度之比為0.5~0.8。優(yōu)選的,在上述后向離心葉輪的技術(shù)方案中,所述輪蓋入口端壁厚為3mm~8mm。采用上述技術(shù)方案的有益效果是:本發(fā)明的后向離心葉輪在輪蓋入口端開一定順序排列的槽形狀,減小入口端與導(dǎo)風(fēng)圈間隙處的氣流速度及抑制渦流產(chǎn)生,使從間隙泄漏的氣流分段排出,不產(chǎn)生混流,從而起到降低噪聲的目的。附圖說明為了更清楚地說明本發(fā)明實(shí)施例或現(xiàn)有技術(shù)中的技術(shù)方案,下面將對實(shí)施例或現(xiàn)有技術(shù)描述中所需要使用的附圖作簡單地介紹,顯而易見地,下面描述中的附圖僅僅是本發(fā)明的實(shí)施例,對于本領(lǐng)域普通技術(shù)人員來講,在不付出創(chuàng)造性勞動的前提下,還可以根據(jù)提供的附圖獲得其他的附圖。圖1為現(xiàn)有技術(shù)中的一種后向離心葉輪的結(jié)構(gòu)圖;圖2為現(xiàn)有技術(shù)中的后向離心葉輪與導(dǎo)風(fēng)圈的配合狀態(tài)示意圖;圖3為本實(shí)施例中的一種后向離心葉輪的結(jié)構(gòu)圖;圖4為本實(shí)施例中的一種后向離心葉輪的齒槽的一個(gè)實(shí)施例的結(jié)構(gòu)圖;圖5為本實(shí)施例中的一種后向離心葉輪的齒槽的另一個(gè)實(shí)施例的結(jié)構(gòu)圖;圖6為本實(shí)施例中的一種后向離心葉輪的齒槽的另一個(gè)實(shí)施例的結(jié)構(gòu)圖;圖7為本實(shí)施例中的一種后向離心葉輪的齒槽的另一個(gè)實(shí)施例的結(jié)構(gòu)圖;圖8為本實(shí)施例中的一種后向離心葉輪的齒槽的另一個(gè)實(shí)施例的結(jié)構(gòu)圖;圖9為本實(shí)施例中的一種后向離心葉輪的鋸齒的厚度示意圖。具體實(shí)施方式本發(fā)明實(shí)施例提供一種后向離心葉輪,在輪蓋入口端開一定順序排列的槽形狀,減小入口端與導(dǎo)風(fēng)圈間隙處的氣流速度及抑制渦流產(chǎn)生,使從間隙泄漏的氣流分段排出,不產(chǎn)生混流,從而起到降低噪聲的目的。下面將結(jié)合本發(fā)明實(shí)施例中的附圖,對本發(fā)明實(shí)施例中的技術(shù)方案進(jìn)行清楚、完整地描述,顯然,所描述的實(shí)施例僅僅是本發(fā)明一部分實(shí)施例,而不是全部的實(shí)施例。基于本發(fā)明中的實(shí)施例,本領(lǐng)域普通技術(shù)人員在沒有做出創(chuàng)造性勞動前提下所獲得的所有其他實(shí)施例,都屬于本發(fā)明保護(hù)的范圍。如圖2至圖5所示,本發(fā)明實(shí)施例中的后向離心葉輪包括輪蓋1、輪盤2及位于輪蓋1和輪盤2之間的葉片3;輪蓋1的入口端設(shè)有若干間隔設(shè)置的齒5和槽4,每兩個(gè)齒5之間設(shè)有一個(gè)槽4,每一相鄰的齒5和槽4構(gòu)成一個(gè)齒槽單元;在任意一個(gè)齒槽單元中,在齒槽單元的邊緣處即在齒槽單元靠近輪蓋入口端的一側(cè),槽寬度L1與齒寬度L2之比為0.8~1.2,槽寬度L1與槽深度L3之比為1~1.5。本實(shí)施例中的后向離心葉輪與導(dǎo)風(fēng)圈6配套使用的過程中,如圖2所示,導(dǎo)風(fēng)圈6伸入輪蓋1并與輪蓋1之間具有空隙H,當(dāng)外界氣流經(jīng)導(dǎo)風(fēng)圈6進(jìn)入后向離心葉輪時(shí),氣流從導(dǎo)風(fēng)圈6進(jìn)入后會從空隙H泄漏一小部分氣流,在輪蓋1的入口端開設(shè)槽4,可以使泄漏氣流不經(jīng)過風(fēng)阻較大的空隙H排出而從槽4排出,從而減小了氣流噪音。關(guān)于槽寬度、齒寬度的比例關(guān)系以及槽寬度與槽深度的比例關(guān)系,本發(fā)明人進(jìn)行過多次試驗(yàn),表一和表二是相關(guān)的試驗(yàn)數(shù)據(jù)。表一槽寬度與齒寬度之比(保證同一槽深度)表二槽寬度與槽深度之比(保證同一齒寬度)當(dāng)槽寬度比較小時(shí),泄漏氣流風(fēng)速較大,會有較大的噪音;當(dāng)槽寬度比較大時(shí),氣流泄漏量太大,也會造成較大的噪音。根據(jù)上表所示試驗(yàn)數(shù)據(jù),可知:當(dāng)槽深度保持不變時(shí),槽寬度與齒寬度之比<0.8時(shí),噪音值>77.1,槽寬度與齒寬度之比>1.2時(shí),噪音值>76.7,但是在槽寬度與齒寬度之比為0.8~1.2時(shí),噪音值為74.7-75.1,效果最好。當(dāng)槽深度較小時(shí),氣流要先經(jīng)過間隙再從槽泄漏氣流,這時(shí)的間隙風(fēng)阻較大,氣流會有較大噪音;當(dāng)槽深度較大時(shí),氣流不需要經(jīng)過間隙就泄漏排出,這時(shí)泄漏量較大,氣流噪音大。當(dāng)槽寬度保持不變時(shí),槽寬度與槽深度之比<1時(shí),噪音值>75.1;槽寬度與槽深度之比>1.5時(shí),噪音值>75.1;槽寬度與槽深度之比為1~1.5時(shí),噪音值為74.7-75.1,效果最好。如圖6和圖7所示,在齒槽單元中,槽的兩側(cè)面的切線的延長線的夾角為0°≤α≤120°,進(jìn)一步的,在該齒槽單元中,槽的兩側(cè)面中的任一個(gè)或兩個(gè)為傾斜面,傾斜面相對于槽外邊緣所在平面傾斜。優(yōu)選的,如下表所示,在齒槽單元中,槽的兩側(cè)面均為傾斜面,且槽的兩側(cè)面的切線的延長線的夾角為0°≤α≤45°時(shí),噪音值相對降低。下表是相關(guān)的試驗(yàn)數(shù)據(jù)。表三不同夾角所對應(yīng)噪音值(保證同一槽寬度)在上述后向離心葉輪中,如圖8所示,若干個(gè)齒槽單元等分成若干個(gè)齒槽組合,每一齒槽組合包括至少兩個(gè)槽寬度與齒寬度之比不一的齒槽單元,具體可為一種為槽寬度與齒寬度之比為1.0,另一種為槽寬度與齒寬度之比為1.1。本發(fā)明人進(jìn)行過多次試驗(yàn),下表是相關(guān)的試驗(yàn)數(shù)據(jù)。類型槽寬度與槽深度之比噪音值相同比值1.075.2組合比值1.0和1.174.9表四相異齒槽單元所對應(yīng)的噪音值在上述后向離心葉輪中,齒厚度與槽寬度L1之比為0.5~0.8,本發(fā)明人進(jìn)行過多次試驗(yàn),下表是相關(guān)的試驗(yàn)數(shù)據(jù)。表五齒厚度與槽寬度之比對噪音值的影響在上述后向離心葉輪中,不具體限定槽4和齒5的形狀,如齒5的形狀可以為圖4所示的矩形,也可以為圖5所示的類矩形(即底面為弧形),可以為圖6所示的梯形,也可以為圖7所示的類梯形(即底面為弧形)。如圖9所示,輪蓋入口端壁厚L4為3mm~8mm,本發(fā)明人通過對輪蓋入口端壁厚的厚度進(jìn)行多次試驗(yàn),下表是相關(guān)的試驗(yàn)數(shù)據(jù)。以上實(shí)施例僅用以說明本發(fā)明的技術(shù)方案,而非對其限制;盡管參照前述實(shí)施例對本發(fā)明進(jìn)行了詳細(xì)的說明,本領(lǐng)域的普通技術(shù)人員應(yīng)當(dāng)理解:其依然可以對前述各實(shí)施例所記載的技術(shù)方案進(jìn)行修改,或者對其中部分技術(shù)特征進(jìn)行等同替換;而這些修改或者替換,并不使相應(yīng)技術(shù)方案的本質(zhì)脫離本發(fā)明各實(shí)施例技術(shù)方案的精神和范圍。當(dāng)前第1頁1 2 3