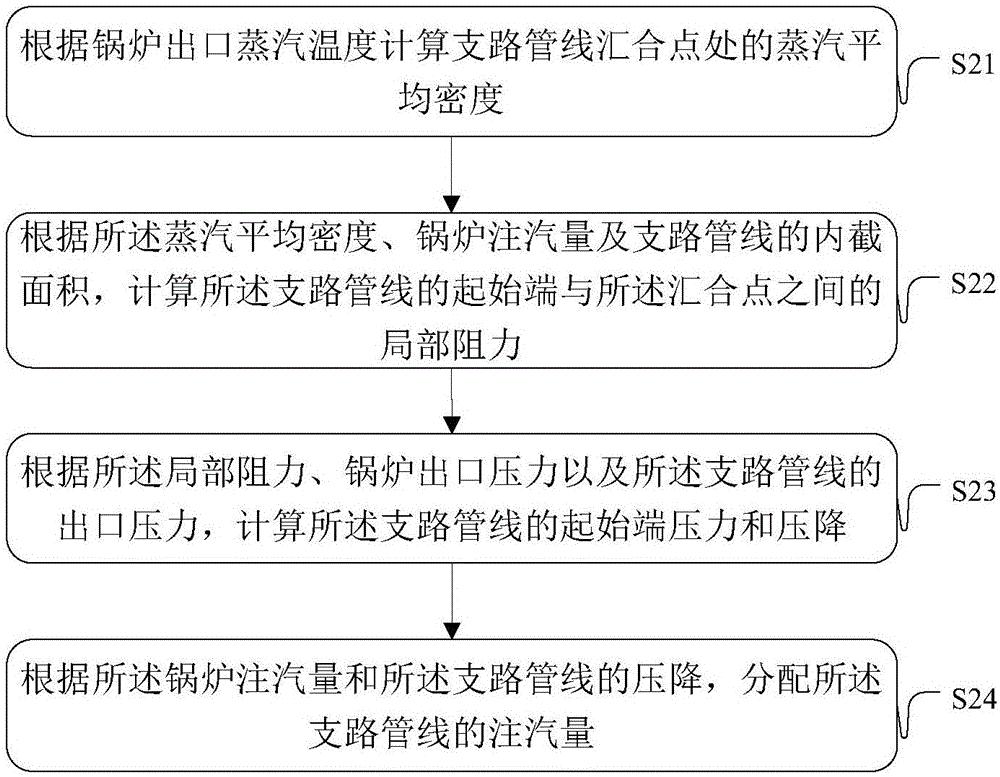
本發(fā)明涉及油藏開采
技術(shù)領(lǐng)域:
,尤其涉及一種確定注汽管熱損失的方法及裝置。
背景技術(shù):
:稠油是指地層條件下粘度大于50mp·s(毫帕·秒),或油層溫度下脫氣原油粘度為1000至10000mp·s的高粘度重質(zhì)原油。由于稠油粘度較大,因此流動性能較差,甚至在某些油層條件下不能流動,給稠油的開采帶來了困難。在石油開采過程中,由于稠油具有高粘度和高凝固點等特性,在儲層和井筒中流動性差,采用常規(guī)開采方式的采收率較低,一般無法保證正常的經(jīng)濟產(chǎn)量。為了保證合理的采收率,往往通過降低原油粘度的方式進行開采。由于稠油的粘度對溫度非常敏感,隨著溫度增加,粘度極大降低,流動也阻力減小,因此目前常用的開采稠油的方式主要有注蒸汽熱采技術(shù),包括蒸汽吞吐、蒸汽驅(qū)、SAGD(蒸汽輔助重力泄油技術(shù))。具體的,所述注蒸汽熱采技術(shù)主要是通過將鍋爐產(chǎn)生的高溫、高壓濕飽和蒸汽,經(jīng)過地面管線傳輸至井口,再由井口通過井筒傳輸后注入稠油油層,以達到降低稠油粘度的目的。目前蒸汽的注汽方式主要有一爐一注、多爐一注和一爐多注等,對應(yīng)的注汽管網(wǎng)結(jié)構(gòu)包括單一注汽管線、星狀管網(wǎng)、樹枝狀管網(wǎng)等。在計算地面管線熱損失的過程中,目前只有一爐一注單一管線的計算方法,即從注汽鍋爐到井口只有一條管線,管線不存在分支及匯入情況。但是大多數(shù)注汽開采是采用星狀或樹枝狀的管網(wǎng)結(jié)構(gòu),目前單一注汽管線熱損失計算方法已不再適用星狀或樹枝狀的管網(wǎng)結(jié)構(gòu)。技術(shù)實現(xiàn)要素:本申請的目的在于提供一種確定注汽管熱損失的方法及裝置,可以用于進一步提高熱損失計算結(jié)果的準(zhǔn)確性。為了實現(xiàn)上述目的,本發(fā)明提供了一種確定注汽管熱損失的方法及裝置,所述方法及裝置具體是這樣實現(xiàn)的:一種確定注汽管熱損失的方法,所述方法包括:根據(jù)鍋爐出口蒸汽溫度、壓力、干度、鍋爐注汽量以及支路管線的出口壓力和內(nèi)截面積,計算所述支路管線的起始端壓力、注汽量;按照預(yù)設(shè)步長對所述支路管線進行分段,以所述支路管線的起始端壓力、注汽量為起始條件,通過對蒸汽壓力、溫度、干度進行迭代計算,依次分段確定單位預(yù)設(shè)步長的支路管線的熱損失。一種確定注汽管熱損失的裝置,所述裝置包括:注汽量分配單元,用于根據(jù)鍋爐出口蒸汽溫度、壓力、干度、鍋爐注汽量以及支路管線的出口壓力和內(nèi)截面積,計算所述支路管線的起始端壓力、注汽量;熱損失計算單元,用于按照預(yù)設(shè)步長對所述支路管線進行分段,以所述支路管線的起始端壓力、注汽量為起始條件,通過對蒸汽壓力、溫度、干度進行迭代計算,依次分段確定單位預(yù)設(shè)步長的支路管線的熱損失。本發(fā)明提供的確定注汽管熱損失的方法及裝置,可以根據(jù)鍋爐出口蒸汽溫度、壓力、干度等已知參數(shù)值,對鍋爐注汽量進行均衡分配,使得每個支路管線獲取合理的注汽量。按照預(yù)設(shè)步長對所述支路管線進行分段,并以所述支路管線的起始端壓力、注汽量為起始條件,通過對蒸汽壓力、溫度、干度進行迭代計算,依次分段確定單位預(yù)設(shè)步長的支路管線的熱損失。分段計算所述支路管線的熱損失,可以使得熱損失計算結(jié)果更加準(zhǔn)確,通過對參數(shù)蒸汽壓力、溫度、干度進行三次迭代計算,進一步提高熱損失計算結(jié)果的準(zhǔn)確性。附圖說明為了更清楚地說明本申請實施例或現(xiàn)有技術(shù)中的技術(shù)方案,下面將對實施例或現(xiàn)有技術(shù)描述中所需要使用的附圖作簡單地介紹,顯而易見地,下面描述中的附圖僅僅是本申請中記載的一些實施例,對于本領(lǐng)域普通技術(shù)人員來講,在不付出創(chuàng)造性勞動性的前提下,還可以根據(jù)這些附圖獲得其他的附圖。圖1是本發(fā)明提供的確定注汽管熱損失方法的一種實施例的流程圖;圖2是本發(fā)明提供的計算所述支路管線注汽量方法的一種實施例的流程圖;圖3是本發(fā)明提供的計算支路管線匯合點處蒸汽平均密度方法的一種實施例的流程圖;圖4是本發(fā)明提供的計算單位支路管線熱損失量方法的一種實施例的方法流程圖;圖5是本發(fā)明提供的計算單位支路管線的壓力降方法的一種實施例的方法流程圖;圖6是本發(fā)明提供的井口壓力迭代計算方法的一種實施例的方法流程圖;圖7是本發(fā)明提供的確定注汽管熱損失裝置的一種實施例的模塊結(jié)構(gòu)示意圖;圖8是本發(fā)明提供的注汽量分配單元的一種實施例的模塊結(jié)構(gòu)示意圖;圖9是本發(fā)明提供的密度計算單元的一種實施例的模塊結(jié)構(gòu)示意圖;圖10是本發(fā)明提供的熱損失計算單元的一種實施例的模塊結(jié)構(gòu)示意圖;圖11是本發(fā)明提供的參數(shù)預(yù)置單元的一種實施例的模塊結(jié)構(gòu)示意圖;圖12是本發(fā)明提供的確定注汽管熱損失裝置的另一種實施例的模塊結(jié)構(gòu)示意圖。具體實施方式為了使本
技術(shù)領(lǐng)域:
的人員更好地理解本申請中的技術(shù)方案,下面將結(jié)合本申請實施例中的附圖,對本申請實施例中的技術(shù)方案進行清楚、完整地描述,顯然,所描述的實施例僅僅是本申請一部分實施例,而不是全部的實施例?;诒旧暾堉械膶嵤├?,本領(lǐng)域普通技術(shù)人員在沒有做出創(chuàng)造性勞動前提下所獲得的所有其他實施例,都應(yīng)當(dāng)屬于本申請保護的范圍。圖1是本發(fā)明提供的確定注汽管熱損失方法的一種實施例的方法流程圖,如圖1所示,所述方法可以包括:S1:根據(jù)鍋爐出口蒸汽溫度、壓力、干度、鍋爐注汽量以及支路管線的出口壓力和內(nèi)截面積,計算所述支路管線的起始端壓力、注汽量。在注蒸汽熱采稠油的過程中,蒸汽的壓力、溫度、干度等熱力參數(shù)會由于地面管線輸送過程中產(chǎn)生的熱損失和壓力損失而發(fā)生變化。其中熱損失的大小直接影響了注入井筒底部的蒸汽的熱力狀態(tài),從而決定注蒸汽熱采效果的好壞。所述干度是指每千克濕蒸汽中含有干蒸汽的質(zhì)量百分?jǐn)?shù)的大小,對于注蒸汽熱采而言,干度越大,越有利于提高注蒸汽熱采的效果。在注蒸汽熱采時,需要計算地面管線內(nèi)蒸汽的熱力參數(shù):壓力、溫度、干度、熱損失,基于計算出的熱力參數(shù),對地面管線進行改進,以最大限度地減小蒸汽運移過程中的熱量損失,提高蒸汽干度,從而提高注蒸汽開采稠油的效果。本實施例中的稠油開采注汽結(jié)構(gòu)可以為呈星狀管網(wǎng)分布的一爐多注結(jié)構(gòu),在該結(jié)構(gòu)中,鍋爐出口的蒸汽注入各個支路管線中。所述支路管線與鉆井相連接,在鉆井井口可以測量得到支路管線的出口壓力。本發(fā)明提供一種計算所述支路管線注汽量方法的一種實施例,圖2是本發(fā)明提供的計算所述支路管線注汽量方法的一種實施例的方法流程圖,如圖2所示,所述根據(jù)鍋爐出口蒸汽溫度、鍋爐出口蒸汽壓力、鍋爐注汽量以及支路管線的內(nèi)截面積,計算所述支路管線的注汽量可以包括:S21:根據(jù)鍋爐出口蒸汽溫度計算支路管線匯合點處的蒸汽平均密度。本實施例中的鍋爐出口蒸汽溫度、鍋爐出口蒸汽壓力、鍋爐注汽量以及支路管線的內(nèi)截面積等參數(shù)值均可以直接測得。所述支路管線匯合點為所述鍋爐的出口處,本實施例中的蒸汽平均密度為所述鍋爐出口處的蒸汽的平均密度。本發(fā)明提供一種計算支路管線匯合點處蒸汽平均密度方法的一種實施例,圖3是本發(fā)明提供的計算支路管線匯合點處蒸汽平均密度方法的一種實施例的方法流程圖,如圖3所示,所述根據(jù)鍋爐出口蒸汽溫度計算支路管線匯合點處的蒸汽平均密度包括:S31:根據(jù)鍋爐出口蒸汽溫度計算支路管線匯合點處的蒸汽液相密度、蒸汽汽相密度、蒸汽液相粘度以及蒸汽汽相粘度。在本發(fā)明的一個實施例中,所述蒸汽液相密度、蒸汽汽相密度、蒸汽液相粘度以及蒸汽汽相粘度的計算公式可以分別為:ρl=(0.9967-4.615×10-5Tb-3.063×10-6Tb2)×103(1)Zg=1.012-4.461×10-4Tb+2.98×10-6Tb2-1.663×10-8Tb3(3)μg=(0.36Tb+88.37)×10-4(5)其中,ρl為蒸汽液相密度,單位為kg/m3,ρg為蒸汽液相密度,單位為kg/m3,Zg為氣體壓縮因子,Tb為鍋爐出口溫度,μl為蒸汽液相粘度,單位為mp·s,μg為蒸汽汽相粘度,單位為mp·s。S32:根據(jù)所述支路管線匯合點處的蒸汽液相密度、蒸汽汽相密度以及所述鍋爐出口干度計算所述支路管線匯合點處的體積含氣率。在本發(fā)明的一個實施例中,所述匯合點處的體積含氣率的計算公式可以為:其中,Hg為所述匯合點處的體積含氣率,xb為鍋爐出口干度,ρl為蒸汽液相密度,單位為kg/m3,ρg為蒸汽液相密度,單位為kg/m3。S33:根據(jù)所述體積含氣率計算所述支路管線匯合點處的蒸汽平均密度。在本發(fā)明的一個實施例中,所述支路管線匯合點處的蒸汽平均密度的計算公式可以為:ρm=Hgρg+(1-Hg)ρl(7)其中,ρm為所述支路管線匯合點處的蒸汽平均密度,Hg為所述匯合點處的體積含氣率,ρl為蒸汽液相密度,單位為kg/m3,ρg為蒸汽液相密度,單位為kg/m3。S22:根據(jù)所述蒸汽平均密度、鍋爐注汽量及支路管線的內(nèi)截面積,計算所述支路管線的起始端與所述匯合點之間的局部阻力。在本發(fā)明的一個實施例中,可以通過所述支路管線平均流速計算所述支路管線的起始端與所述匯合點之間的局部阻力,其中,所述支路管線平均流速的計算公式可以為:其中,vm為所述支路管線的平均流速,單位為m/s,G為鍋爐注汽量,A為所述支路管線的內(nèi)截面積,A=πri2,其中ri為所述支路管線的內(nèi)截面半徑。在本發(fā)明的一個實施例中,所述支路管線的起始端與所述匯合點之間的局部阻力的計算公式可以為:其中,△pb為所述支路管線的起始端與所述匯合點之間的局部阻力,△pw為液體單向流的局部壓強損失,單位為Pa,B為中間參數(shù),X為馬蒂內(nèi)利參數(shù),△pw、B、X的計算公式可以分別為:其中,ζ為局部阻力系數(shù),vm為所述支路管線的平均流速,g為重力加速度,xb為鍋爐出口干度,ρl為蒸汽液相密度,單位為kg/m3,ρg為蒸汽液相密度,單位為kg/m3,μl為蒸汽液相粘度,單位為mp·s,μg為蒸汽汽相粘度,單位為mp·s。S23:根據(jù)所述局部阻力、鍋爐出口壓力以及所述支路管線的出口壓力,計算所述支路管線的起始端壓力和壓降。本實施例中,可以根據(jù)所述支路管線的起始端與所述匯合點之間的局部阻力、鍋爐出口壓力以及所述支路管線的出口壓力,計算所述支路管線的起始端壓力和壓降,具體的,在本發(fā)明的一個實施例中,所述支路管線的起始端壓力的計算公式為:pstart=pb-Δpb(13)其中,pstart為所述支路管線的起始端壓力,pb為鍋爐出口壓力,△pb為所述支路管線的起始端與所述匯合點之間的局部阻力。根據(jù)所述支路管線的起始端壓力,可以計算所述支路管線的壓降,所述壓降的計算公式可以為:Δp=pstart-p(14)其中,Δp為所述支路管線的壓降,p為所述支路管線的出口壓力。S24:根據(jù)所述鍋爐注汽量和所述支路管線的壓降,分配所述支路管線的注汽量。本實施例中,可以根據(jù)所述支路管線的壓降,可以計算得到所述支路管線的注汽量,所述注汽量的計算公式可以為:其中,Gj為所述支路管線的注汽量,其中j為所述支路管線在所有支路管線中的編號,Δpj為所述支路管線的壓降,G為鍋爐注汽量,N為所有支路管線的個數(shù)。本實施例中,可以根據(jù)鍋爐出口蒸汽溫度、壓力、干度、鍋爐注汽量等已知參數(shù)數(shù)據(jù)對鍋爐注汽量進行合理分配,使得各個支路管線獲取與其出口壓力、管線尺寸相匹配的注汽量,可以降低傳輸過程中的熱損失。S2:按照預(yù)設(shè)步長對所述支路管線進行分段,以所述支路管線的起始端壓力、注汽量為起始條件,通過對蒸汽壓力、溫度、干度進行迭代計算,依次分段確定單位預(yù)設(shè)步長的支路管線的熱損失。本實施例中,可以按照預(yù)設(shè)步長對所述支路管線進行分段,以所述支路管線的起始端壓力、注汽量為起始條件,通過對蒸汽壓力、溫度、干度進行迭代計算,依次分段確定單位預(yù)設(shè)步長的支路管線的熱損失。所述支路管線的起始端壓力、注汽量可以在S1中計算得到。在本申請的一個實施例中,提供一種計算單位支路管線熱損失量的方法,圖4是本發(fā)明提供的計算單位支路管線熱損失量方法的一種實施例的方法流程圖,如圖4所示,所述按照預(yù)設(shè)步長對所述支路管線進行分段,以所述支路管線的起始端壓力、干度、注汽量為起始條件,通過對蒸汽壓力、溫度、干度進行迭代計算,依次分段確定單位預(yù)設(shè)步長的所述支路管線的熱損失可以包括:S41:從所述支路管線的起始端獲取預(yù)設(shè)步長的單位支路管線,設(shè)置所述單位支路管線的預(yù)設(shè)干度降、預(yù)設(shè)外壁溫度、預(yù)設(shè)壓力降,根據(jù)所述支路管線的起始端壓力、干度、注汽量,計算所述單位支路管線的壓力降。本實施例中,可以設(shè)置所述支路管線的預(yù)設(shè)步長為Δz,按照步長Δz對所述支路管線進行分段,得到若干個單位支路管線,本實施例從最靠近鍋爐的單位支路管線開始,逐個向井口方向順延的單位支路管線進行處理。本發(fā)明提供一種計算所述單位支路管線的壓力降的方法,圖5是本發(fā)明提供的計算單位支路管線的壓力降方法的一種實施例的方法流程圖,如圖5所示,所述計算所述單位支路管線的壓力降可以包括:S51:根據(jù)所述支路管線的起始端壓力、干度、注汽量計算所述單位支路管線的蒸汽平均密度、摩擦系數(shù)。本實施例中,采用迭代的計算方法獲取所述單位支路管線的壓力降,預(yù)先設(shè)置所述單位支路管線的預(yù)設(shè)干度降為Δxi、預(yù)設(shè)外壁溫度Tw、預(yù)設(shè)壓力降△pi,其中i為所述單位支路管線在所述支路管線中的編號。在本發(fā)明的一個實施例中,所述單位支路管線的終端壓力、溫度、干度的計算公式可以分別為:pi=pi-1-△pi(16)Ti=195.94pi0.225-17.8(17)xi=xi-1-△xi(18)其中,pi,Ti,xi分別為所述單位支路管線的終端壓力、溫度、干度,pi-1,xi-1分別為所述單位支路管線的起始端壓力、干度,當(dāng)i=1時,pi-1,xi-1分別為所述支路管線的起始端壓力、干度。計算所述單位支路管線的平均壓力、溫度、干度,所述公式可以為:pavi=(pi-1+pi)/2(19)Tavi=(Ti-1+Ti)/2(20)xavi=(xi-1+xi)/2(21)其中,pavi,Tavi,xavi分別為所述單位支路管線的平均壓力、溫度、干度。本實施例中,可以利用公式(1)-(7),將所述參數(shù)Tavi分別替換公式(1)-(5)中的Tb,將xavi分別替換公式(6)中的xb,計算得到所述單位支路管線的蒸汽平均密度ρ′m,并根據(jù)下述公式計算得到所述單位支路管線的平均粘度μ′m:μ′m=Hg′μ′g+(1-H′g)μ′l(22)其中,H′g為所述單位支路管線的平均體積含氣率,μ′l為所述單位支路管線的平均蒸汽液相粘度,單位為mp·s,μ′g為所述單位支路管線的平均蒸汽汽相粘度,單位為mp·s。本實施例中,將公式(8)參數(shù)ρ′m替換成ρm,可以計算得到所述單位支路管線的平均流速v′m,根據(jù)所述單位支路管線的內(nèi)截面半徑ri、蒸汽平均流速v′m、蒸汽平均密度ρ′m、蒸汽平均粘度μ′m可以計算得到所述單位支路管線的雷諾數(shù)Re,計算公式為:本實施例中,根據(jù)所述單位支路管線的雷諾數(shù)Re,可以計算所述單位支路管線的摩擦系數(shù),表1是管線雷諾數(shù)與摩擦系數(shù)計算公式關(guān)系對應(yīng)表,表1中的Ra為已知參數(shù)管壁粗糙度,d為所述單位支路管線的內(nèi)截面直徑。表1管線雷諾數(shù)與摩擦系數(shù)計算公式關(guān)系對應(yīng)表S52:計算所述單位支路管線在起始端壓力、干度下的起始平均流速,在終端壓力、干度下的終端平均流速。本實施中,利用公式(1)-(3)、(6)、(7)、(17)計算所述單位支路管線在起始端壓力pi-1、干度xi-1下的起始平均流速vi-1,在終端壓力pi、干度xi下的終端平均流速vi,具體計算過程在此不再贅述。S53:根據(jù)所述單位支路管線的蒸汽平均密度、摩擦系數(shù)、起始平均流速、終端平均流速,計算所述單位支路管線的壓力降。本實施例中,根據(jù)所述單位支路管線的蒸汽平均密度ρ′m、摩擦系數(shù)fm、起始平均流速vi-1、終端平均流速vi,計算所述單位支路管線的壓力降△pi',計算公式可以為:其中,K為常數(shù),fm為摩擦系數(shù),ρ′m為蒸汽平均密度,Δz為預(yù)設(shè)步長,vi-1為起始平均流速,vi為終端平均流速,ri為所述單位支路管線的內(nèi)截面半徑,g為重力加速度,θ為所述單位支路管線的傾角,Gj為所述支路管線的注汽量,A為所述單位支路管線的內(nèi)截面面積。S42:當(dāng)所述壓力降與所述預(yù)設(shè)壓力降之間的誤差小于第一閾值時,根據(jù)所述預(yù)設(shè)外壁溫度、空氣溫度以及所述單位支路的內(nèi)、外截面半徑,計算所述單位支路管線的外壁溫度。計算所述單位支路管線的壓力降△pi'與預(yù)設(shè)壓力降△pi之間的誤差,若所述誤差大于等于第一閾值,重新設(shè)置所述預(yù)設(shè)壓力降△pi的值,例如,可以設(shè)置△pi=△pi',返回至步驟S51,進行迭代計算。若所述閾值小于第一閾值,則進行溫度迭代計算。具體地,可以根據(jù)所述預(yù)設(shè)外壁溫度Tw、空氣溫度Ta、所述單位支路的內(nèi)截面半徑ri、外截面半徑ro計算所述單位支路管線的單位長度上的熱阻值,所述熱阻值的計算公式可以為:其中,R1為對流層的對流換熱熱阻,R2為污垢層的對流換熱熱阻,R3為管壁熱阻,R4為絕熱層熱阻,R5為低速氣膜層熱阻,hf為液膜層對流換熱系數(shù),單位為kcal/(m2·h·℃),hp為污垢層對流換熱系數(shù),單位為kcal/(m2·h·℃),ri、ro為所述單位支路的內(nèi)、外截面半徑,rins為絕熱層的外半徑,λp為管線的導(dǎo)熱系數(shù),單位為kcal/(h·m·℃),λins為絕熱層的導(dǎo)熱系數(shù),單位為kcal/(h·m·℃),hfc為絕熱層外表面上強迫對流熱系數(shù),單位為kcal/(m2·h·℃)。本實施例中,hfc=hfc'+hfc",即hfc由對流換熱系數(shù)hfc'和輻射換熱系數(shù)hfc"組成,計算公式分別為:其中,C為常數(shù),λa為空氣的導(dǎo)熱系數(shù),單位為kcal/(h·m·℃),Re為雷諾數(shù),Re=νaDs/υa,νa為風(fēng)速,單位為m/s,υa為空氣的運動粘度,單位為m2/s,Ds為絕熱層外徑,單位為m,n的值可以根據(jù)雷諾值的大小進行選取,表2為雷諾數(shù)與常數(shù)C、n之間的對應(yīng)關(guān)系表:表2雷諾數(shù)與常數(shù)C、n之間的對應(yīng)關(guān)系表Re5-8080-5×1035×103-5×104>5×104C0.810.6250.1970.023n0.400.460.60.8其中,ε為管壁外黑度,Ta為空氣溫度,單位為℃,Tw為絕熱層外壁溫度,單位為℃。本實施例中,忽略所述對流層和污垢層的對流換熱熱阻R1和R2,則可以計算得到所述單位支路管線上的單位長度、單位時間的熱損失q,單位為kcal/(h·m),計算公式為:另外,假設(shè)所述管線的絕熱層外表面溫度為Tw',那么,所述單位支路管線上的單位長度、單位時間的熱損失q的計算公式還可以為:已知Ts、Ta、R3、R4、R5,根據(jù)公式(28)、(29),可以計算得到Tw'。S43:當(dāng)所述外壁溫度與所述預(yù)設(shè)外壁溫度之間的誤差小于第二閾值時,根據(jù)所述支路管線的起始端壓力、所述預(yù)設(shè)壓力降計算所述單位支路管線的干度降。本實施例中,計算所述絕熱層外壁溫度為Tw'與預(yù)設(shè)外壁溫度Tw之間的誤差,若所述誤差大于等于第二閾值,重新設(shè)置所述外壁溫度Tw的值,例如,可以設(shè)置Tw=Tw',返回至步驟S42,進行迭代計算。當(dāng)所述外壁溫度Tw'與所述預(yù)設(shè)外壁溫度Tw之間的誤差小于第二閾值時,根據(jù)所述支路管線的起始端壓力、所述預(yù)設(shè)壓力降計算所述單位支路管線的干度降。具體地,可以計算所述單位支路管線的飽和水、飽和蒸汽的熱焓,在將所述飽和水、飽和蒸汽的熱焓對蒸汽壓力進行求導(dǎo),具體公式可以為:hg=(12500+1.88Tavi-3.7×10-6Tavi3.2)/4.186(31)其中,hl、hg為飽和水、飽和蒸汽的熱焓,單位為kcal/kg,Tavi為所述單位支路管線的平均溫度。根據(jù)所述飽和水、飽和蒸汽的熱焓計算所述單位支路管線的干度降,所述干度的計算公式可以為:C1=G(hg-hl)(35)需要說明的是,公式(35)-(37)中的G為所述支路管線的注汽量。S44:當(dāng)所述干度降與所述預(yù)設(shè)干度降之間的誤差小于第三閾值時,計算所述單位支路管線的熱損失量。本實施例中,計算(xi-xi-1)與預(yù)設(shè)干度降Δxi之間的誤差,若所述誤差大于等于第三閾值,重新設(shè)置所述外壁溫度Δxi的值,例如,可以設(shè)置Δxi=xi-xi-1,返回至步驟S2,進行迭代計算。當(dāng)所述干度降與所述預(yù)設(shè)干度降之間的誤差小于第三閾值時,計算所述單位支路管線的熱損失量,所述熱損失量Δqi的計算公式為:Δqi=qi-qi-1=q×△z×4.186/3600(38)其中,qi-1為所述單位支路管線上的起始端熱損失,當(dāng)i=1時,qi-1=0,q為所述單位支路管線上的單位長度、單位時間的熱損失,△z為所述支路管線的步長,也是所述單位支路管線的長度。在本發(fā)明的一個實施例中,還可以進一步對所述熱損失的計算過程進行迭代,本發(fā)明還提供一種井口壓力迭代計算的方法,圖6是本發(fā)明提供的井口壓力迭代計算方法的一種實施例的方法流程圖,如圖6所示,所述方法可以包括:S61:計算所述支路管線的終端壓力。按照預(yù)設(shè)步長將所述支路管線進行分成若干段單位支路管線,逐個計算各個單位支路的熱損失以及單位支路管線的終端壓力、干度、溫度,計算公式為(16)-(18)。所述支路管線的終端壓力為所述支路管線中最接近井口的單位支路管線的終端壓力。S62:計算所述終端壓力與實測井口壓力之間的誤差。S63:當(dāng)所述誤差小于第四閾值時,累加分段確定的單位預(yù)設(shè)步長的支路管線的熱損失,生成所述支路管線的熱損失。計算所述終端壓力與實測井口壓力之間的誤差,當(dāng)所述誤差大于等于第四閾值時,可以設(shè)置返回至步驟S2,并設(shè)置當(dāng)所述終端壓力大于實測井口壓力時,增加公式(24)中的K值,當(dāng)所述終端壓力小于實測井口壓力時,減小公式(24)中的K值。當(dāng)所述誤差小于第四閾值時,累加分段確定的單位預(yù)設(shè)步長的支路管線的熱損失,生成所述支路管線的熱損失,所述熱損失的計算公式為:其中,N為對所述支路管線按照步長劃分的單位支路管線的段數(shù)。整個一爐多注的星狀管網(wǎng)的熱損失總量的計算公式為:其中,M為所述一爐多注的星狀管網(wǎng)中的支路管線的個數(shù)。本發(fā)明提供的確定注汽管熱損失的方法,可以根據(jù)鍋爐出口蒸汽溫度、壓力、干度等已知參數(shù)值,對鍋爐注汽量進行均衡分配,使得每個支路管線獲取合理的注汽量。按照預(yù)設(shè)步長對所述支路管線進行分段,并以所述支路管線的起始端壓力、注汽量為起始條件,通過對蒸汽壓力、溫度、干度進行迭代計算,依次分段確定單位預(yù)設(shè)步長的支路管線的熱損失。分段計算所述支路管線的熱損失,可以使得熱損失計算結(jié)果更加準(zhǔn)確,通過對參數(shù)蒸汽壓力、溫度、干度進行三次迭代計算,進一步提高熱損失計算結(jié)果的準(zhǔn)確性。本發(fā)明另一方面還提供一種確定注汽管熱損失的裝置,圖7是本發(fā)明提供的確定注汽管熱損失裝置的一種實施例的模塊結(jié)構(gòu)示意圖,結(jié)合附圖7,該裝置70包括:注汽量分配單元71,用于根據(jù)鍋爐出口蒸汽溫度、壓力、干度、鍋爐注汽量以及支路管線的出口壓力和內(nèi)截面積,計算所述支路管線的起始端壓力、注汽量;熱損失計算單元72,用于按照預(yù)設(shè)步長對所述支路管線進行分段,以所述支路管線的起始端壓力、注汽量為起始條件,通過對蒸汽壓力、溫度、干度進行迭代計算,依次分段確定單位預(yù)設(shè)步長的支路管線的熱損失??蛇x的,在本發(fā)明的一個實施例中,圖8是本發(fā)明提供的注汽量分配單元的一種實施例的模塊結(jié)構(gòu)示意圖,如圖8所示,所述注汽量分配單元71可以包括:密度計算單元81,用于根據(jù)鍋爐出口蒸汽溫度計算支路管線匯合點處的蒸汽平均密度;局部阻力計算單元82,用于根據(jù)所述蒸汽平均密度、鍋爐注汽量及支路管線的內(nèi)截面積,計算所述支路管線的起始端與所述匯合點之間的局部阻力;壓降計算單元83,用于根據(jù)所述局部阻力、鍋爐出口壓力以及所述支路管線的出口壓力,計算所述支路管線的起始端壓力和壓降;注汽量計算單元84,用于根據(jù)所述鍋爐注汽量和所述支路管線的壓降,分配所述支路管線的注汽量??蛇x的,在本發(fā)明的一個實施例中,圖9是本發(fā)明提供的密度計算單元的一種實施例的模塊結(jié)構(gòu)示意圖,如圖9所示,所述密度計算單元81可以包括:基本參數(shù)計算單元91,用于根據(jù)鍋爐出口蒸汽溫度計算支路管線匯合點處的蒸汽液相密度、蒸汽汽相密度、蒸汽液相粘度以及蒸汽汽相粘度;體積含氣量計算單元92,用于根據(jù)所述支路管線匯合點處的蒸汽液相密度、蒸汽汽相密度以及所述鍋爐出口干度計算所述支路管線匯合點處的體積含氣率;平均密度計算單元93,用于根據(jù)所述體積含氣率計算所述支路管線匯合點處的蒸汽平均密度??蛇x的,在本發(fā)明的一個實施例中,圖10是本發(fā)明提供的熱損失計算單元的一種實施例的模塊結(jié)構(gòu)示意圖,如圖10所示,所述熱損失計算單元72可以包括:參數(shù)預(yù)置單元101,用于從所述支路管線的起始端獲取預(yù)設(shè)步長的單位支路管線,設(shè)置所述單位支路管線的預(yù)設(shè)干度降、預(yù)設(shè)外壁溫度、預(yù)設(shè)壓力降,根據(jù)所述支路管線的起始端壓力、干度、注汽量,計算所述單位支路管線的壓力降;外壁溫度計算單元102,用于當(dāng)所述壓力降與所述預(yù)設(shè)壓力降之間的誤差小于第一閾值時,根據(jù)所述預(yù)設(shè)外壁溫度、空氣溫度以及所述單位支路的內(nèi)、外截面半徑,計算所述單位支路管線的外壁溫度;干度降計算單元103,用于當(dāng)所述外壁溫度與所述預(yù)設(shè)外壁溫度之間的誤差小于第二閾值時,根據(jù)所述支路管線的起始端壓力、所述預(yù)設(shè)壓力降計算所述單位支路管線的干度降;單位熱損失計算單元104,用于當(dāng)所述干度降與所述預(yù)設(shè)干度降之間的誤差小于第三閾值時,計算所述單位支路管線的熱損失量??蛇x的,在本發(fā)明的一個實施例中,圖11是本發(fā)明提供的參數(shù)預(yù)置單元的一種實施例的模塊結(jié)構(gòu)示意圖,如圖11所示,所述參數(shù)預(yù)置單元101可以包括:摩擦系數(shù)計算單元111,用于根據(jù)所述支路管線的起始端壓力、干度、注汽量計算所述單位支路管線的蒸汽平均密度、摩擦系數(shù);流速計算單元112,用于計算所述單位支路管線在起始端壓力、干度下的起始平均流速,在終端壓力、干度下的終端平均流速;壓力降計算單元113,用于根據(jù)所述單位支路管線的蒸汽平均密度、摩擦系數(shù)、起始平均流速、終端平均流速,計算所述單位支路管線的壓力降。可選的,在本發(fā)明的一個實施例中,圖12是本發(fā)明提供的確定注汽管熱損失裝置的另一種實施例的模塊結(jié)構(gòu)示意圖,結(jié)合附圖12,該裝置120還包括:終端壓力計算單元121,用于計算所述支路管線的終端壓力;誤差計算單元122,用于計算所述終端壓力與實測井口壓力之間的誤差;熱損失總量計算單元123,用于當(dāng)所述誤差小于第四閾值時,累加分段確定的單位預(yù)設(shè)步長的支路管線的熱損失,生成所述支路管線的熱損失。本發(fā)明提供的確定注汽管熱損失的裝置,可以根據(jù)鍋爐出口蒸汽溫度、壓力、干度等已知參數(shù)值,對鍋爐注汽量進行均衡分配,使得每個支路管線獲取合理的注汽量。按照預(yù)設(shè)步長對所述支路管線進行分段,并以所述支路管線的起始端壓力、注汽量為起始條件,通過對蒸汽壓力、溫度、干度進行迭代計算,依次分段確定單位預(yù)設(shè)步長的支路管線的熱損失。分段計算所述支路管線的熱損失,可以使得熱損失計算結(jié)果更加準(zhǔn)確,通過對參數(shù)蒸汽壓力、溫度、干度進行三次迭代計算,進一步提高熱損失計算結(jié)果的準(zhǔn)確性。本說明書中的各個實施例均采用遞進的方式描述,每個實施例重點說明的都是與其他實施例的不同之處,各個實施例之間相同相似的部分互相參見即可。尤其,對于系統(tǒng)實施例而言,由于其基本相似于方法實施例,所以描述的比較簡單,相關(guān)之處參見方法實施例的部分說明即可。雖然通過實施例描繪了本申請,本領(lǐng)域普通技術(shù)人員知道,本申請有許多變形和變化而不脫離本申請的精神,希望所附的權(quán)利要求包括這些變形和變化而不脫離本申請的精神。雖然本申請?zhí)峁┝巳鐚嵤├蛄鞒虉D所述的方法操作步驟,但基于常規(guī)或者無創(chuàng)造性的勞動可以包括更多或者更少的操作步驟。實施例中列舉的步驟順序僅僅為眾多步驟執(zhí)行順序中的一種方式,不代表唯一的執(zhí)行順序。在實際中的裝置或客戶端產(chǎn)品執(zhí)行時,可以按照實施例或者附圖所示的方法順序執(zhí)行或者并行執(zhí)行(例如并行處理器或者多線程處理的環(huán)境)。上述實施例闡明的裝置或模塊,具體可以由計算機芯片或?qū)嶓w實現(xiàn),或者由具有某種功能的產(chǎn)品來實現(xiàn)。為了描述的方便,描述以上裝置時以功能分為各種模塊分別描述。在實施本申請時可以把各模塊的功能在同一個或多個軟件和/或硬件中實現(xiàn)。當(dāng)然,也可以將實現(xiàn)某功能的模塊由多個子模塊或子單元組合實現(xiàn)。本申請中所述的方法、裝置或模塊可以以計算機可讀程序代碼方式實現(xiàn)控制器按任何適當(dāng)?shù)姆绞綄崿F(xiàn),例如,控制器可以采取例如微處理器或處理器以及存儲可由該(微)處理器執(zhí)行的計算機可讀程序代碼(例如軟件或固件)的計算機可讀介質(zhì)、邏輯門、開關(guān)、專用集成電路(ApplicationSpecificIntegratedCircuit,ASIC)、可編程邏輯控制器和嵌入微控制器的形式,控制器的例子包括但不限于以下微控制器:ARC625D、AtmelAT91SAM、MicrochipPIC18F26K20以及SiliconeLabsC8051F320,存儲器控制器還可以被實現(xiàn)為存儲器的控制邏輯的一部分。本領(lǐng)域技術(shù)人員也知道,除了以純計算機可讀程序代碼方式實現(xiàn)控制器以外,完全可以通過將方法步驟進行邏輯編程來使得控制器以邏輯門、開關(guān)、專用集成電路、可編程邏輯控制器和嵌入微控制器等的形式來實現(xiàn)相同功能。因此這種控制器可以被認(rèn)為是一種硬件部件,而對其內(nèi)部包括的用于實現(xiàn)各種功能的裝置也可以視為硬件部件內(nèi)的結(jié)構(gòu)?;蛘呱踔粒梢詫⒂糜趯崿F(xiàn)各種功能的裝置視為既可以是實現(xiàn)方法的軟件模塊又可以是硬件部件內(nèi)的結(jié)構(gòu)。當(dāng)前第1頁1 2 3