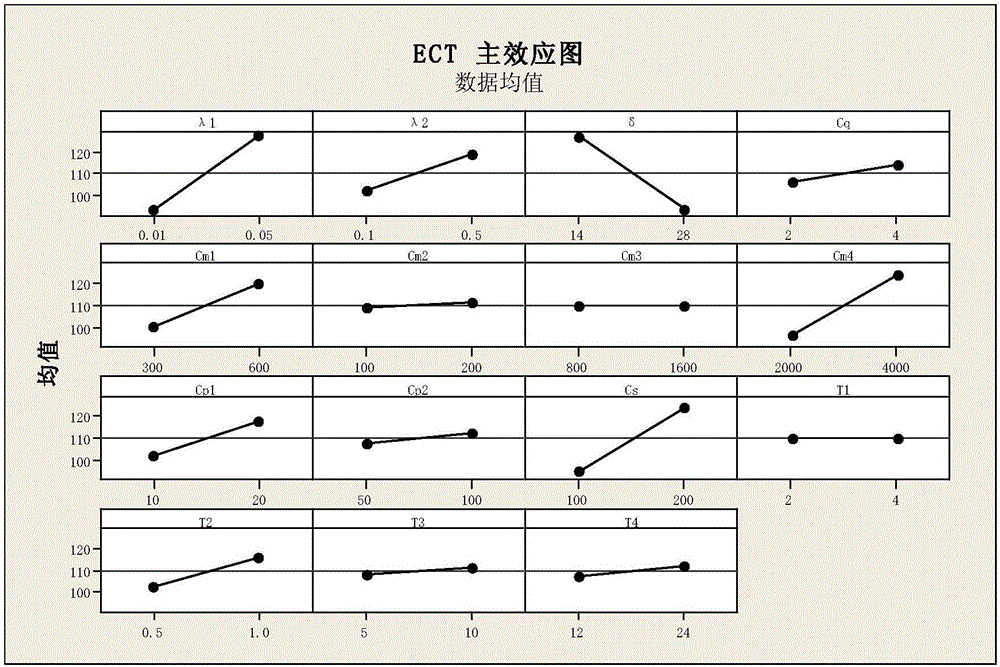
本發(fā)明涉及生產(chǎn)系統(tǒng)過程質(zhì)量與可靠性控制領(lǐng)域,特別涉及一種動態(tài)的過程質(zhì)量控制圖和定齡維修聯(lián)合設(shè)計優(yōu)化控制方法。
背景技術(shù):
:在生產(chǎn)過程中,對設(shè)備系統(tǒng)進行預(yù)防維修和利用控制圖對生產(chǎn)過程進行質(zhì)量監(jiān)控是保證產(chǎn)品質(zhì)量的兩種基本手段和方法。由于定時、定齡等預(yù)防維修策略和質(zhì)量控制圖兩者的集成經(jīng)濟決策相對于單一措施的獨立經(jīng)濟決策在生產(chǎn)運行綜合費用方面更具經(jīng)濟性,關(guān)于預(yù)防維修策略和控制圖的聯(lián)合經(jīng)濟設(shè)計問題近年來廣受關(guān)注,是生產(chǎn)系統(tǒng)質(zhì)量經(jīng)濟效益領(lǐng)域的研究熱點之一。自統(tǒng)計過程質(zhì)量控制和預(yù)防維修聯(lián)合設(shè)計問題提出至今,其研究主要集中在系統(tǒng)運行質(zhì)量成本要素處于靜態(tài)不變條件下的質(zhì)量控制圖和預(yù)防維修參數(shù)聯(lián)合設(shè)計的數(shù)學(xué)建模及其分析領(lǐng)域,并且要求每次維修都修復(fù)如新,這與現(xiàn)實生產(chǎn)實際并不相符。在現(xiàn)實生產(chǎn)中,每次維修不僅往往難以修復(fù)如新,因此系統(tǒng)每個運行階段的故障率并非完全一樣的,而且由于改進策略的實施、成本要素市場價格變化等因素的影響,系統(tǒng)維修成本、產(chǎn)品質(zhì)量抽檢成本、不合格品的生產(chǎn)費用、維修停機生產(chǎn)損失等質(zhì)量成本要素在不同維修間隔運行階段的成本狀況也并不一定是確定不變的,而是呈現(xiàn)出動態(tài)變化的特征。因此,在每次維修完成后,需要根據(jù)系統(tǒng)可靠性變化和運行成本要素結(jié)果變化對聯(lián)合設(shè)計的參數(shù)方案進行持續(xù)的動態(tài)調(diào)整優(yōu)化,否則難以實現(xiàn)通過過程質(zhì)量控制圖和預(yù)防維修聯(lián)合設(shè)計最大可能降低系統(tǒng)生產(chǎn)運行綜合費用的目的。本發(fā)明在充分考慮生產(chǎn)系統(tǒng)運行實際狀態(tài)具有變化性的基礎(chǔ)上,提出一種動態(tài)的過程質(zhì)量控制圖和定齡維修聯(lián)合設(shè)計優(yōu)化控制方法,可以解決生產(chǎn)系統(tǒng)過程質(zhì)量控制圖和定齡維修聯(lián)合設(shè)計方案的持續(xù)優(yōu)化問題。技術(shù)實現(xiàn)要素:針對上述情況,本發(fā)明的目的在于克服現(xiàn)有技術(shù)存在的不足而提供一種可以解決生產(chǎn)系統(tǒng)過程質(zhì)量控制圖和定齡維修聯(lián)合設(shè)計方案的持續(xù)優(yōu)化問題的動態(tài)的過程質(zhì)量控制圖和定齡維修聯(lián)合設(shè)計方案的控制方法。本發(fā)明所采用的技術(shù)方案如下,一種動態(tài)的過程質(zhì)量控制圖和定齡維修聯(lián)合設(shè)計方案的控制方法,該方法包括以下階段:第一階段:構(gòu)建以維修間隔期生產(chǎn)運行綜合費用最小為目標的生產(chǎn)系統(tǒng)過程質(zhì)量控制圖和定齡維修聯(lián)合設(shè)計模型并進行靈敏度分析;第二階段:基于聯(lián)合設(shè)計模型,根據(jù)生產(chǎn)過程質(zhì)量與維修成本的參數(shù)信息,利用遺傳算法求解過程質(zhì)量控制圖和定齡維修的設(shè)計方案;第三階段:執(zhí)行設(shè)計方案和管控對策,觸發(fā)停機維修時判斷顯著性影響因素的成本水平是否發(fā)生變化;第四階段:優(yōu)化確定實施方案;根據(jù)第三階段判定結(jié)果的不同,本優(yōu)化過程分為兩種情況:(1)如果顯著性影響因素值未發(fā)生變化,執(zhí)行步M;(2)如果顯著性影響因素值發(fā)生了變化,執(zhí)行步驟N;步驟M:原有聯(lián)合設(shè)計方案不變,優(yōu)化管控對策并確定執(zhí)行;步驟N:更新系統(tǒng)過程質(zhì)量和設(shè)備運行可靠性狀態(tài)信息,利用遺傳算法求解聯(lián)合設(shè)計模型產(chǎn)生新的優(yōu)化設(shè)計方案,并確定執(zhí)行。第一階段包括以下步驟:步驟A:根據(jù)生產(chǎn)系統(tǒng)過程質(zhì)量控制過程和設(shè)備運行過程的特征及其相互關(guān)聯(lián)性,建立生產(chǎn)系統(tǒng)過程質(zhì)量控制圖和維修策略的耦合機制,并由歷史數(shù)據(jù)分析確定生產(chǎn)系統(tǒng)的產(chǎn)品質(zhì)量特性分布函數(shù)和設(shè)備運行的壽命分布函數(shù)的特征信息;步驟B:基于生產(chǎn)系統(tǒng)過程質(zhì)量控制圖和維修策略的耦合機制及兩者的特征信息,在確定所用控制圖和相關(guān)假設(shè)前提下,建立以生產(chǎn)運行綜合費用最小為目標的生產(chǎn)系統(tǒng)過程質(zhì)量控制圖和定齡維修聯(lián)合設(shè)計數(shù)學(xué)模型;步驟C:由步驟B的數(shù)學(xué)模型,對模型的成本相關(guān)參數(shù)與目標值的影響關(guān)系進行靈敏度分析,識別判定顯著性影響因素;步驟D:針對步驟C的顯著性影響因素,根據(jù)實際生產(chǎn)狀況和環(huán)境提出改進的管控對策。所述第二階段包括以下步驟:步驟E:基于matlab語言利用遺傳算法求解聯(lián)合設(shè)計模型;步驟F:根據(jù)求解結(jié)果確定過程質(zhì)量控制圖和定齡維修的設(shè)計方案。所述第三階段包括以下步驟:步驟G:執(zhí)行設(shè)計方案和管控對策,記錄系統(tǒng)運行的過程質(zhì)量和設(shè)備運行信息,尤其是系統(tǒng)產(chǎn)量、合格品、不合格品、質(zhì)量抽檢成本、抽檢時間、抽檢次數(shù)、設(shè)備運行可靠性狀態(tài)信息等;步驟H:觸發(fā)停機維修時,根據(jù)記錄的過程質(zhì)量和設(shè)備運行狀態(tài)信息,判定顯著性影響因素值在這一階段的運行過程中是否發(fā)生變化。本發(fā)明的技術(shù)方案產(chǎn)生的積極效果如下:(1)本方案可以實現(xiàn)針對實施過程顯著性因素的數(shù)據(jù)變化重新優(yōu)化確定實施方案,與傳統(tǒng)技術(shù)相比,具有能夠?qū)崿F(xiàn)設(shè)計方案根據(jù)系統(tǒng)運行實際變化情況持續(xù)改進和優(yōu)化的優(yōu)點;(2)本方案實施無需要求每次維修都修復(fù)如新這一假設(shè)前提,并且考慮了成本要素市場價格是個動態(tài)變化過程等問題,與傳統(tǒng)技術(shù)相比,具有更符合生產(chǎn)實際情況的優(yōu)點;(3)本方案模型的運行時間都是基于系統(tǒng)實際運行狀態(tài)數(shù)據(jù)實時更新測定,不再需根據(jù)控制圖的ARL進行估計,與傳統(tǒng)技術(shù)相比,具有數(shù)據(jù)更精確的優(yōu)點。本發(fā)明給出了一種動態(tài)的生產(chǎn)系統(tǒng)過程質(zhì)量控制圖和定齡維修聯(lián)合設(shè)計優(yōu)化控制方法,充分考慮了生產(chǎn)系統(tǒng)實際運行狀態(tài)具有階段變化性的現(xiàn)實特征,可以解決生產(chǎn)系統(tǒng)過程質(zhì)量控制圖和定齡維修聯(lián)合設(shè)計方案的持續(xù)優(yōu)化問題。附圖說明圖1為本發(fā)明為實現(xiàn)動態(tài)的對生產(chǎn)系統(tǒng)過程質(zhì)量控制圖和定齡維修聯(lián)合設(shè)計優(yōu)化控制的流程圖。圖2為本發(fā)明測試用生產(chǎn)系統(tǒng)的聯(lián)合模型靈敏度分析結(jié)果主效應(yīng)圖。圖3為本發(fā)明測試用生產(chǎn)系統(tǒng)的聯(lián)合模型靈敏度分析結(jié)果方差分析表。圖4本發(fā)明測試用生產(chǎn)系統(tǒng)聯(lián)合模型基本參數(shù)在不同維修間隔期的動態(tài)信息數(shù)據(jù)表。圖5為本發(fā)明測試用生產(chǎn)系統(tǒng)的過程質(zhì)量控制圖和定齡維修在不同運行周期的聯(lián)合設(shè)計方案結(jié)果。具體實施方式以下以一個測試生產(chǎn)系統(tǒng)為例,對本發(fā)明的實施方式作進一步詳細說明。動態(tài)的過程質(zhì)量控制圖和定齡維修聯(lián)合設(shè)計方案的控制方法,如圖1、2、3、4、5所示,該方法的具體如下步驟:步驟1:分析系統(tǒng)建立維修策略和控制圖監(jiān)測的耦合機制;假設(shè)系統(tǒng)存在三種可能狀態(tài):受控、失控、故障。已知在每個維修間隔期內(nèi),系統(tǒng)由受控轉(zhuǎn)為失控和由失控轉(zhuǎn)為故障停機的時間點t分別服從參數(shù)為λ1和λ2的指數(shù)分布,密度函數(shù)分別為f1(u)和f2(v);系統(tǒng)輸出的過程質(zhì)量特性為X,受控時X~N(μ,σ2),失控時X~N(μ+δ,σ2);采用控制圖監(jiān)控系統(tǒng)過程質(zhì)量特性X,維修事件由控制圖報警、系統(tǒng)故障或定齡維修時間到達三種情況觸發(fā)?;谝陨霞僭O(shè),經(jīng)分析可知,在一個維修間隔周期內(nèi),系統(tǒng)的維修方式和控制圖監(jiān)測存在以下5種可能形成停機維修事件的耦合機制:事件S1:從上一次維修完成后開始,系統(tǒng)在整個定期維修周期內(nèi)一直受控且控制圖未誤發(fā)報警信號,最后運行到達定期維修時間點觸發(fā)停機維修,形成定齡維修事件;事件S2:從上一次維修完成后開始,系統(tǒng)一直受控,但控制圖在第i次抽檢時誤發(fā)報警信號觸發(fā)停機維修行為,形成補償維修事件;事件S3:從上一次維修完成后開始,系統(tǒng)運行至u時刻(u發(fā)生在第r個抽樣間隔期)由受控轉(zhuǎn)為失控狀態(tài),控制圖在第j次抽檢時發(fā)出了正確報警信號觸發(fā)停機維修,形成狀態(tài)維修事件;事件S4:從上一次維修完成后開始,系統(tǒng)運行至u時刻(u發(fā)生在第r個抽樣間隔期)由受控轉(zhuǎn)為失控狀態(tài),由于控制圖一直漏發(fā)報警信號,系統(tǒng)一直失控運行至定期維修時間點觸發(fā)停機維修,形成狀態(tài)維修事件;事件S5:從上一次維修完成后開始,系統(tǒng)運行至u時刻(u發(fā)生在第r個抽樣間隔期)由受控轉(zhuǎn)為失控狀態(tài),但由于控制圖一直漏發(fā)警報,系統(tǒng)運行至v時刻(v發(fā)生在第m個抽樣間隔期)進一步轉(zhuǎn)為故障停機狀態(tài),形成故障維修事件。步驟2:建立以上各維修事件的周期期望運行時間長度函數(shù)ET(Si);若記控制圖的參數(shù)為(n,h,w),犯第一類錯誤和第二類錯誤的概率分別為a和β;定期維修的間隔周期為Td=(k+1)h;定齡維修時間為T1,補償維修時間為T2,狀態(tài)維修時間為T3,故障維修時間為T4,則分析可知,各維修事件的周期期望運行時間長度為:步驟3:建立以上各維修事件的周期期望運行成本函數(shù)EC(Si);假設(shè)系統(tǒng)的過程質(zhì)量檢測時間不計,系統(tǒng)故障、控制圖報警或到達定齡維修點立即進行相應(yīng)維修,系統(tǒng)修好后馬上投入運行,則系統(tǒng)成本主要由以下幾部分組成:系統(tǒng)維修成本、產(chǎn)品抽檢成本、不合格品的生產(chǎn)費用、維修停機生產(chǎn)損失。記平均每次定齡維修成本為Cm1,平均每次補償維修成本為Cm2,平均每次狀態(tài)維修成本為Cm3,平均每次故障維修成本為Cm4;平均每個樣品的抽檢成本為Cq;系統(tǒng)正常時單位時間不合格品生產(chǎn)費用為Cp1,系統(tǒng)異常時單位時間不合格品生產(chǎn)費用為Cp2;維修停機單位時間生產(chǎn)損失為Cs。由此可得S1事件的周期期望運行成本為:同理可得,EC(S2)=Σi=1k(Cm2+Cq×in+Cp1×ih+Cs×T2)×(1-a)i-1×a×∫ih∞f1(u)du---(7)]]>EC(S3)=Σj=1kΣr=1j∫(r-1)hrh∫jh-u∞[Cm3+Cq×jn+Cp1×u+Cp2×(jh-u)+Cs×T3]×[(1-a)r-1βj-r(1-β)×f1(u)×f2(v)]dvdu---(8)]]>EC(S4)=Σr=1k+1∫(r-1)hrh∫(k+1)h-u∞{Cm3+Cq×(k+1)n+Cp1×u+Cp2×[(k+1)h-u]+Cs×T3)}×(1-a)r-1βk+1-r×f1(u)×f2(v)dvdu---(9)]]>EC(S5)=Σm=1k+1Σr=1m{(1-a)r-1βm-r∫(r-1)hrhf1(u)×∫(m-1)hmh[Cm4+Cq×(m-1)h+Cp1×u+Cp2×(v-h)+Cs×T4]f2(v-u)dvdu}---(10)]]>步驟4:建立生產(chǎn)系統(tǒng)的過程質(zhì)量控制和定齡維修聯(lián)合設(shè)計目標函數(shù);以兩次維修間隔期內(nèi)期望單位時間生產(chǎn)運行綜合費用最小為目標,可得目標函數(shù)為minECT=E(C)E(T)=Σi=15EC(Si)Σi=15ET(Si)---(11)]]>式中:EC(Si)-事件Si狀態(tài)下的周期期望運行成本;ET(Si)-事件Si狀態(tài)下的周期期望運行時間;i=1,2,3,4,5。步驟5:進行模型參數(shù)的靈敏度分析,并根據(jù)結(jié)果提出過程管控對策;靈敏度分析利用mintab16方差分析模塊的主效應(yīng)圖分析功能進行計算,如圖2所示。步驟6:利用遺傳算法求解聯(lián)合設(shè)計模型,確定實施方案;遺傳算法采用matlab語言編程實現(xiàn),種群規(guī)模popsize=50,交叉概率pc=0.6,變異概率pm=0.1,最大遺傳代數(shù)maxgen=100。步驟7:執(zhí)行過程質(zhì)量控制和定齡維修的設(shè)計方案以及過程管控對策;方案執(zhí)行過程中,收集相關(guān)參數(shù)的基礎(chǔ)信息數(shù)據(jù)。步驟8:判定是否停機維修;根據(jù)停機維修的觸發(fā)條件,判定是否停機維修;如果不停機維修,繼續(xù)運行,執(zhí)行步驟9,如果停機維修,執(zhí)行步驟10。步驟9:原有聯(lián)合設(shè)計方案不變,優(yōu)化管控對策并確定執(zhí)行;步驟10:停機維修后優(yōu)化確定下一個運行周期的設(shè)計方案和管控對策;停機維修時,基于新收集的參數(shù)基礎(chǔ)信息數(shù)據(jù),分析判定顯著性因素結(jié)果是否變化:如果無變化,提出新的過程管控對策并結(jié)合原有設(shè)計方案執(zhí)行下一個運行周期;如果有變化,則根據(jù)變化結(jié)果優(yōu)化確定下一個運行周期的設(shè)計方案,并結(jié)合原有管控對策執(zhí)行下一個運行周期。整個實施控制的流程圖如圖1所示。(1)測試系統(tǒng)定義。測試用設(shè)備系統(tǒng)定義如下:系統(tǒng)發(fā)生異常前的受控時間服從參數(shù)λ1的指數(shù)分布,故障停機前的失控時間服從參數(shù)λ2的指數(shù)分布;受控狀態(tài)下輸出質(zhì)量特性X~N(77,82),失控時引起X的均值漂移值為δ,過程質(zhì)量采用控制圖(n,h,w)進行監(jiān)控,定齡維修周期長度為Td=(k+1)h,系統(tǒng)停機維修行為由控制圖報警、故障或到達定齡維修時間點三個事件觸發(fā),n,h,w,k均為決策變量;成本因素包括平均每個樣品的抽檢成本Cq,定齡維修的單次平均成本Cm1、補償維修的單次平均成本Cm2、狀態(tài)維修的單次平均成本Cm3、故障維修的單次平均成本Cm4,系統(tǒng)受控時單位時間不合格品生產(chǎn)費用Cp1、系統(tǒng)失控時單位時間不合格品生產(chǎn)費用Cp2、維修停機的單位時間生產(chǎn)損失Cs;時間因素包括系統(tǒng)運行時間T、定齡維修時間T1、補償維修時間T2、狀態(tài)維修時間T3、故障維修時間T4。(2)測試系統(tǒng)聯(lián)合模型參數(shù)的的靈敏度分析。基于測試系統(tǒng)定義,為聯(lián)合模型參數(shù)靈敏度分析結(jié)果如圖2和圖3所示,即該系統(tǒng)聯(lián)合設(shè)計的顯著性因素為λ1,δ、Cm4和Cs,針對以上顯著性因素提出過程管控對策;(3)測試系統(tǒng)初始過程設(shè)計方案求解?;趫D4中的初始數(shù)據(jù)信息,利用遺傳算法求解聯(lián)合設(shè)計模型,得到過程質(zhì)量控制和定齡維修的初始設(shè)計方案見圖5中的初始過程設(shè)計方案結(jié)果數(shù)據(jù)。遺傳算法采用matlab語言編程實現(xiàn),種群規(guī)模popsize=50,交叉概率pc=0.6,變異概率pm=0.1,最大遺傳代數(shù)maxgen=100。(4)執(zhí)行初始設(shè)計方案和過程管控對策觸發(fā)停機維修。根據(jù)初始設(shè)計方案和過程管控對策,執(zhí)行生產(chǎn)系統(tǒng)的過程質(zhì)量控制和定齡維修活動,收集過程質(zhì)量和設(shè)備運行可靠性和維護的相關(guān)基礎(chǔ)信息。(5)停機維修后下一運行周期設(shè)計方案的優(yōu)化。在增加上一個運行過程所收集的相關(guān)基礎(chǔ)信息數(shù)據(jù)后,分析得到的模型參數(shù)新數(shù)據(jù)見圖4中的更新數(shù)據(jù),發(fā)現(xiàn)顯著性因素的結(jié)果具有顯著變化;基于更新數(shù)據(jù)計算得到的下一個運行周期的過程質(zhì)量控制和定齡維修優(yōu)化設(shè)計方案見圖5中的優(yōu)化方案結(jié)果數(shù)據(jù)。遺傳算法的參數(shù)設(shè)置與(3)相同。本發(fā)明在系統(tǒng)的全壽命周期內(nèi),將每個維修間隔期作為一個決策階段,并在每個階段都根據(jù)更新數(shù)據(jù)借助遺傳算法對系統(tǒng)過程質(zhì)量控制圖和定齡維修進行聯(lián)合設(shè)計或管控對策的優(yōu)化,通過這種持續(xù)優(yōu)化獲得更符合生產(chǎn)實際的執(zhí)行方案,從而實現(xiàn)降低生產(chǎn)運行綜合成本的目的。當(dāng)前第1頁1 2 3