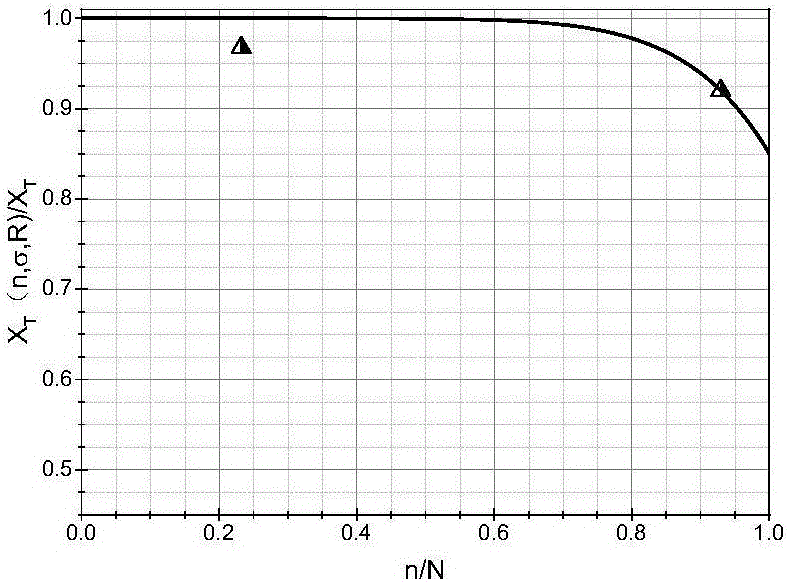
本發(fā)明涉及耐高溫復(fù)合材料結(jié)構(gòu)多失效模式損傷機理驗證方法,屬于結(jié)構(gòu)設(shè)計領(lǐng)域。
背景技術(shù):
:復(fù)合材料結(jié)構(gòu)由于其輕質(zhì)、相對低的費用和制造技術(shù)的發(fā)展,越來越廣泛應(yīng)用于飛行器結(jié)構(gòu)件。飛行器結(jié)構(gòu)件受載環(huán)境復(fù)雜,重量要求苛刻,因此需要進行驗證以保證設(shè)計可靠度。傳統(tǒng)的驗證方法包括實物驗證和仿真驗證兩種,實物驗證周期長,成本高,傳統(tǒng)仿真驗證準確度低,不能真實反映結(jié)構(gòu)設(shè)計水平。技術(shù)實現(xiàn)要素:本發(fā)明的技術(shù)解決問題是:克服現(xiàn)有技術(shù)的不足,提供耐高溫復(fù)合材料結(jié)構(gòu)多失效模式損傷機理驗證方法,實現(xiàn)了復(fù)合材料結(jié)構(gòu)件多層級多修正的虛擬試驗驗證方法,降低了驗證周期和成本,提高了驗證準確度。本發(fā)明的技術(shù)解決方案是:耐高溫復(fù)合材料結(jié)構(gòu)多失效模式損傷機理驗證方法,包括以下步驟:(1)建立耐高溫復(fù)合材料在各失效模式下的破壞機理模型;(2)根據(jù)破壞機理模型建立耐高溫復(fù)合材料元件損傷分析方法,根據(jù)該分析方法對不同載荷工況下元件損傷響應(yīng)進行分析;(3)選取典型耐高溫復(fù)合材料元件進行實物試驗,得到步驟(2)所述各種載荷工況下對應(yīng)的元件損傷響應(yīng)數(shù)據(jù);(4)利用步驟(3)得到的元件損傷響應(yīng)數(shù)據(jù)對步驟(2)的元件損傷分析方法進行修正;(5)根據(jù)修正后的元件損傷分析方法獲得元件損傷響應(yīng)規(guī)律,基于元件損傷響應(yīng)規(guī)律和元件間連接關(guān)系,利用有限元方法對不同載荷工況下構(gòu)件損傷響應(yīng)進行分析;(6)選取典型耐高溫復(fù)合材料構(gòu)件進行實物試驗,得到步驟(5)所述各種載荷工況下對應(yīng)的構(gòu)件損傷響應(yīng)數(shù)據(jù);(7)利用步驟(6)得到的構(gòu)件損傷響應(yīng)數(shù)據(jù)對步驟(5)元件間連接關(guān)系進行修正,得到修正后的元件間連接關(guān)系;(8)根據(jù)步驟(7)得到的修正后元件間連接關(guān)系和步驟(5)得到的元件損傷響應(yīng)規(guī)律,利用有限元分析方法對不同載荷工況下組件、部段以及飛行器損傷響應(yīng)進行分析,完成耐高溫復(fù)合材料結(jié)構(gòu)多層級多修正的虛擬試驗驗證。所述步驟(2)中根據(jù)破壞機理模型建立耐高溫復(fù)合材料元件損傷分析方法的步驟如下:(2.1)建立耐高溫復(fù)合材料在各失效模式下的破壞準則:(a)纖維拉伸損傷,疲勞準則為:其中σxx≥0;(b)纖維壓縮損傷,疲勞準則為:其中σxx<0;(c)基纖剪切,疲勞準則為:其中σxx<0;(d)基體開裂,疲勞準則為:其中σyy≥0;(e)基體擠壓,疲勞準則為:其中σyy<0;(f)層間拉伸損傷,疲勞準則為:其中σzz≥0;(g)層間壓縮損傷,疲勞準則為:其中σzz<0;式中,σij為各單元的應(yīng)力分量,i、j分別取x、y、z其中一項,x、y、z與材料各主方向相互對應(yīng);XT(n,σ,k)、YT(n,σ,k)和ZT(n,σ,k)分別為拉-拉疲勞載荷下,加載到一定周期時,復(fù)合材料單層板的縱向強度、橫向強度和法向強度;XC(n,σ,k)、YC(n,σ,k)和ZC(n,σ,k)分別為壓-壓疲勞載荷下,加載到一定周期時,復(fù)合材料單層板的縱向強度、橫向強度和法向強度;Sxy(n,σ,k)、Sxz(n,σ,k)和Syz(n,σ,k)分別為剪切疲勞載荷下,復(fù)合材料單層板的剪切強度,其中n為疲勞載荷循環(huán)次數(shù),σ為應(yīng)力,k為應(yīng)力比;對于結(jié)構(gòu)中的任意單元體,如果其應(yīng)力分量滿足上述方程中的某一個,那么在該單元體處,就有相應(yīng)模式的損傷發(fā)生;(2.2)利用步驟(3.1)建立的破壞準則,建立如下耐高溫復(fù)合材料元件強度和剛度降階模型:式中:σU為復(fù)合材料單層板初始強度;E(0)為復(fù)合材料單層板初始剛度;S(n,σ,k)為復(fù)合材料單層板疲勞剩余強度;E(n,σ,k)為復(fù)合材料單層板疲勞剩余剛度;Nf為復(fù)合材料單層板在應(yīng)力σ及應(yīng)力比k下的疲勞壽命;(2.3)基于強度和剛度降階模型,對不同載荷工況下元件損傷響應(yīng)進行分析。所述步驟(4)的實現(xiàn)方法為:(3.1)對強度和剛度降階模型進行靈敏度分析,得到待擬合參數(shù),進而得到以下待修正的強度和剛度降階模型:其中c1、c2、c3、c4為待擬合參數(shù);(3.2)計算每種工況下,實物試驗得到的元件損傷響應(yīng)數(shù)據(jù)與元件損傷分析方法得到的分析結(jié)果的擬合度;(3.3)所有工況下的擬合度取平均值,根據(jù)該平均值計算待擬合參數(shù)的具體數(shù)值,完成元件級損傷分析模型修正。所述步驟(7)的實現(xiàn)方法為:(4.1)計算每種工況下,實物試驗得到的構(gòu)件損傷響應(yīng)數(shù)據(jù)與有限元分析結(jié)果的差值;(4.2)根據(jù)構(gòu)件損傷響應(yīng)數(shù)據(jù)與有限元分析結(jié)果的差值,通過靈敏度分析確定元件間連接參數(shù)的調(diào)整量,同時保證元件間連接參數(shù)在取值范圍內(nèi),從而完成元件間連接關(guān)系的修正。與現(xiàn)有技術(shù)相比,本發(fā)明具有如下有益效果:本發(fā)明建立元件級、構(gòu)件級、組件及以上的損傷分析方法,并在每一層級選取典型產(chǎn)品進行實物數(shù)據(jù),利用實物數(shù)據(jù)對損傷分析方法進行修正,實現(xiàn)了復(fù)合材料結(jié)構(gòu)件多層級多修正的虛擬試驗驗證方法,降低了驗證周期和成本,提高了驗證準確度。附圖說明圖1為本發(fā)明方法流程圖;圖2為[0]16織物單向板強度退化曲線;圖3為[0]16織物單向板剛度退化曲線;圖4為開孔壁板剪切疲勞試驗損傷分析有限元模型。具體實施方式本發(fā)明采用多層級的積木式的分析和修正方法,可以最大程度降低復(fù)合材料結(jié)構(gòu)驗證周期和成本,提高驗證準確度。如圖1所示,本發(fā)明具體步驟如下:(1)建立耐高溫復(fù)合材料在各失效模式下的破壞機理模型。(2)根據(jù)破壞機理模型建立耐高溫復(fù)合材料元件損傷分析方法,根據(jù)該分析方法對不同載荷工況下元件損傷響應(yīng)進行分析。根據(jù)破壞機理模型建立耐高溫復(fù)合材料元件損傷分析方法的步驟如下:(2.1)建立耐高溫復(fù)合材料在各失效模式下的破壞準則:(a)纖維拉伸損傷,疲勞準則為:其中σxx≥0;(b)纖維壓縮損傷,疲勞準則為:其中σxx<0;(c)基纖剪切,疲勞準則為:其中σxx<0;(d)基體開裂,疲勞準則為:其中σyy≥0;(e)基體擠壓,疲勞準則為:其中σyy<0;(f)層間拉伸損傷,疲勞準則為:其中σzz≥0;(g)層間壓縮損傷,疲勞準則為:其中σzz<0;式中,σij為各單元的應(yīng)力分量,i、j分別取x、y、z其中一項,x、y、z與材料各主方向相互對應(yīng);XT(n,σ,k)、YT(n,σ,k)和ZT(n,σ,k)分別為拉-拉疲勞載荷下,加載到一定周期時,復(fù)合材料單層板的縱向強度、橫向強度和法向強度;XC(n,σ,k)、YC(n,σ,k)和ZC(n,σ,k)分別為壓-壓疲勞載荷下,加載到一定周期時,復(fù)合材料單層板的縱向強度、橫向強度和法向強度;Sxy(n,σ,k)、Sxz(n,σ,k)和Syz(n,σ,k)分別為剪切疲勞載荷下,復(fù)合材料單層板的剪切強度,其中n為疲勞載荷循環(huán)次數(shù),σ為應(yīng)力,k為應(yīng)力比。對于結(jié)構(gòu)中的任意單元體,如果其應(yīng)力分量滿足上述方程中的某一個,那么在該單元體處,就有相應(yīng)模式的損傷發(fā)生。(2.2)利用破壞準則,建立如下耐高溫復(fù)合材料元件強度和剛度降階模型:式中:σU——復(fù)合材料單層板初始強度;E(0)——復(fù)合材料單層板初始剛度;S(n,σ,k)——復(fù)合材料單層板疲勞剩余強度;E(n,σ,k)——復(fù)合材料單層板疲勞剩余剛度;Nf——復(fù)合材料單層板在應(yīng)力σ及應(yīng)力比k下的疲勞壽命。(2.3)基于強度和剛度降階模型,對不同載荷工況下元件損傷響應(yīng)(疲勞壽命)進行分析。(3)選取典型耐高溫復(fù)合材料元件進行實物試驗,得到不同載荷工況下對應(yīng)的元件損傷響應(yīng)數(shù)據(jù)。(4)利用步驟(3)得到的元件損傷響應(yīng)數(shù)據(jù)對步驟(2)的元件損傷分析方法進行修正。具體方法如下:(4.1)對強度和剛度降階模型進行靈敏度分析,得到待擬合參數(shù),進而得到以下待修正的強度和剛度降階模型:其中c1、c2、c3、c4為待擬合參數(shù);(4.2)計算每種工況下,實物試驗得到的元件損傷響應(yīng)數(shù)據(jù)與元件損傷分析方法得到的分析結(jié)果的擬合度;(4.3)所有工況下的擬合度取平均值,根據(jù)該平均值應(yīng)用數(shù)值統(tǒng)計分析算法(如L-M算法),計算待擬合參數(shù)的具體數(shù)值,完成元件級損傷分析模型修正。(5)根據(jù)修正后的元件損傷分析方法獲得元件損傷響應(yīng)規(guī)律,基于元件損傷響應(yīng)規(guī)律和元件間理想連接關(guān)系,利用有限元方法對不同載荷工況下構(gòu)件損傷響應(yīng)進行分析。(6)選取典型耐高溫復(fù)合材料構(gòu)件進行實物試驗,得到步驟(5)所述各種載荷工況下對應(yīng)的構(gòu)件損傷響應(yīng)數(shù)據(jù)。(7)利用步驟(6)得到的構(gòu)件損傷響應(yīng)數(shù)據(jù)對步驟(5)元件間理想連接關(guān)系進行修正,得到修正后的元件間連接關(guān)系。具體方法如下:(7.1)計算每種工況下,實物試驗得到的構(gòu)件損傷響應(yīng)數(shù)據(jù)與有限元分析結(jié)果的差值;(7.2)根據(jù)構(gòu)件損傷響應(yīng)數(shù)據(jù)與有限元分析結(jié)果的差值,通過靈敏度分析確定元件間連接參數(shù)的調(diào)整量,具體公式如下:其中,為損傷分析結(jié)果F(r)對元件間連接參數(shù)r的靈敏度,ΔF(r)為試驗結(jié)果與分析結(jié)果的差值,Δr表示元件間連接參數(shù)的調(diào)整量。通過求上式在各工況下的最小二乘解,確定元件間連接參數(shù)的調(diào)整量,同時保證元件間連接參數(shù)在取值范圍內(nèi),從而完成元件間連接關(guān)系的修正。(8)根據(jù)步驟(7)得到的修正后元件間連接關(guān)系和步驟(5)得到的元件損傷響應(yīng)規(guī)律,利用有限元分析方法對不同載荷工況下組件、部段以及飛行器損傷響應(yīng)進行分析,完成耐高溫復(fù)合材料結(jié)構(gòu)多層級多修正的虛擬試驗驗證。實施例:以[0]16織物單向板在拉-拉疲勞載荷下的壽命試驗為例,簡要說明本發(fā)明的實施過程。選擇85%的載荷作為[0]16織物單向板強度和剛度退化試驗的疲勞載荷固定值。采用本發(fā)明給出的元件損傷分析方法對元件損傷響應(yīng)進行分析,得到[0]16織物單向板強度退化曲線如圖2所示,不同循環(huán)次數(shù)下剩余剛度的變化趨勢如圖3所示。其中圖2中縱坐標為[0]16織物單向板在指定循環(huán)次數(shù)下的剩余拉伸強度與靜載拉伸強度的比值XT(n,σ,R)/XT,橫坐標為加載次數(shù)與疲勞壽命的比值(n/N)。圖3中縱坐標為[0]16織物單向板在指定循環(huán)次數(shù)下的剩余拉伸剛度與靜載拉伸剛度的比值E11(n,σ,R)/E11,橫坐標為加載次數(shù)與疲勞壽命的比值(n/N)。選取試驗件進行實物試驗,表1給出了不同循環(huán)加載次數(shù)下試驗件的剩余強度和剩余剛度的基本數(shù)據(jù)。表1指定循環(huán)次數(shù)下[0]16織物單向板剩余剛度和剩余強度由于Z0-22和Z0-23在額定疲勞次數(shù)的疲勞試驗時發(fā)生斷裂,因此在剩余剛度和剩余強度退化公式時剔除兩個失效的試驗,剩余剛度和強度同初始值的比值如表2所示。表2[0]16織物單向板剩余剛度和剩余強度與初始剛度強度比值編號次數(shù)比n/NXT(n,σ,R)/XTE11(n,σ,R)/E11Z0-170.023241.055370.95697Z0-180.023241.087711.19421Z0-190.232360.967741.00583Z0-200.232361.086741.01528Z0-210.774551.086810.90822Z0-240.929450.925580.90235根據(jù)圖2和實物試驗得到的元件損傷響應(yīng)數(shù)據(jù),計算實物試驗得到的元件損傷響應(yīng)數(shù)據(jù)與元件損傷分析方法得到的分析結(jié)果的擬合度,采用L-M算法,得到待擬合參數(shù)c4=8.592,所得到的剩余強度退化公式為:根據(jù)圖3和實物試驗得到的元件損傷響應(yīng)數(shù)據(jù),計算實物試驗得到的元件損傷響應(yīng)數(shù)據(jù)與元件損傷分析方法得到的分析結(jié)果的擬合度,從而得到回歸系數(shù)。因為考慮到剛度出現(xiàn)退化的試件只有3個,不能自由度不能完全滿足,故對參數(shù)進行調(diào)整。c1參數(shù)采用參考值c1=1.230進行計算。采用L-M算法,最終得到待擬合參數(shù)c1=1.230,c2=4.261,c3=0.220,即[0]16織物單向板剩余剛度E11(n,σ,R)的退化公式:將元件剩余強度和剩余剛度退化公式作為輸入條件,預(yù)置連接理想?yún)?shù)(加強筋與壁板連接剛度理想值為1.0E10),采用有限元分析方法,對構(gòu)件(以開孔壁板為例)進行有限元分析,建立的有限元模型如圖4所示。開孔壁板在剪切疲勞載荷下的實物試驗結(jié)果和有限元分析結(jié)果如表3所示,其中破壞載荷為實物試驗結(jié)果,以破壞載荷試驗結(jié)果與分析結(jié)果的比對為例進行連接參數(shù)修正。表3開孔剪切壁板破壞試驗數(shù)據(jù)采用本發(fā)明方法對連接參數(shù)進行修正,加強筋與壁板連接剛度修正值為0.97E10。以修正的元件強度剛度降階模型和連接參數(shù)修正值為輸入條件,應(yīng)用有限元方法進行復(fù)合材料機翼結(jié)構(gòu)損傷分析,對機翼結(jié)構(gòu)在相應(yīng)疲勞載荷工況下的剩余強度進行預(yù)估,得到考慮多失效模式影響下機翼結(jié)構(gòu)的最大承載數(shù)值。本發(fā)明方法,實現(xiàn)了復(fù)合材料結(jié)構(gòu)件多層級多修正的虛擬試驗驗證方法,降低了驗證周期和成本,提高了驗證準確度。同時還可以進一步開發(fā)實時顯示對比系統(tǒng),從而能夠清楚地看出分析結(jié)果與試驗結(jié)果的實時顯示比對以及分析修正。本發(fā)明說明書中未作詳細描述的內(nèi)容屬于本領(lǐng)域?qū)I(yè)技術(shù)人員的公知技術(shù)。當前第1頁1 2 3