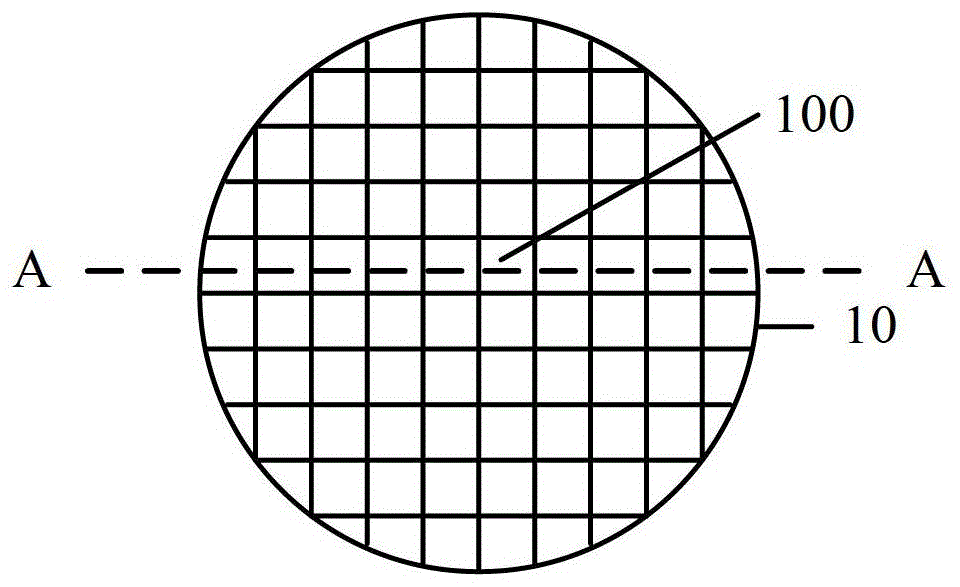
本發(fā)明涉及半導(dǎo)體制造技術(shù)領(lǐng)域,尤其涉及一種晶圓刻蝕后的清洗方法。
背景技術(shù):在半導(dǎo)體制造過程中,晶圓的清洗是非常重要的一個(gè)環(huán)節(jié)。在執(zhí)行晶圓的前段工藝過程(FEOL)和后段工藝過程(BEOL)時(shí),晶圓需要經(jīng)過無數(shù)次的清洗步驟,清洗的次數(shù)取決于晶圓的設(shè)計(jì)和互連的層數(shù)。在過去十幾年中,主要通過批式處理技術(shù)對(duì)晶圓進(jìn)行清洗(即在一個(gè)處理倉中利用浸泡方法或者噴淋法同時(shí)清洗多片晶圓),該方法雖產(chǎn)量較高但效果差、良率低。且隨著半導(dǎo)體器件的特征尺寸(CD,CriticalDimension)不斷減小,晶圓中半導(dǎo)體器件的數(shù)量增加,半導(dǎo)體材料變得越來越脆弱,清洗效果和材料損失的要求變得越來越嚴(yán)格,對(duì)晶圓清洗的要求也越來越高,批式處理技術(shù)逐漸無法滿足晶圓清洗的要求。此外,批式處理技術(shù)無法滿足如快速熱處理(RTP)等工藝的關(guān)鍵擴(kuò)散和CVD技術(shù)。而單個(gè)晶圓清洗方法由于對(duì)每一片晶圓單獨(dú)加工,其具有清洗質(zhì)量高、化學(xué)試劑用量少、循環(huán)周期塊等優(yōu)點(diǎn),大大改進(jìn)了生產(chǎn)力,降低了生產(chǎn)成本。而且,單個(gè)晶圓清洗方法也為整個(gè)制造周期提供了實(shí)現(xiàn)更好的工藝過程控制的機(jī)會(huì),改善了單個(gè)晶圓以及晶圓對(duì)晶圓的均一性,進(jìn)而提高了良率。因此,單個(gè)晶圓清洗方法逐漸替代批式處理技術(shù),成為晶圓清洗工藝的主流方法?,F(xiàn)有工藝中,在干法刻蝕之后,通常利用單個(gè)晶圓清洗方法對(duì)表面介質(zhì)層中形成有刻蝕圖案的晶圓進(jìn)行清洗,以去除刻蝕殘留的聚合物。以在晶圓表面低k或者超低k介質(zhì)層中形成金屬互連線或者插塞為例,在形成金屬互連線或者插塞之前,需先對(duì)晶圓上的低k或者超低k介質(zhì)層進(jìn)行干法刻蝕,形成用于填充金屬互連線或者插塞的通孔;再利用單個(gè)晶圓清洗方法進(jìn)行清洗,去除干法刻蝕形成通孔過程中殘留于低k或者超低k介質(zhì)層上表面以及通孔側(cè)壁上的聚合物;然后對(duì)清洗后的晶圓進(jìn)行檢測,確定清洗后殘留的聚合物是否在設(shè)定范圍之內(nèi);當(dāng)其在設(shè)定范圍內(nèi)時(shí),在低k或者超低k介質(zhì)層中的通孔內(nèi)填充金屬,形成金屬互連線或者插塞,當(dāng)其超出設(shè)定范圍內(nèi)時(shí),需要對(duì)晶圓重新進(jìn)行清洗。然而,在對(duì)清洗后的晶圓進(jìn)行檢測后發(fā)現(xiàn),上述晶圓清洗方法的效果不明顯,返工幾率大,良率低。更多晶圓清洗方法請參考公開號(hào)為CN101529559A的中國專利申請。
技術(shù)實(shí)現(xiàn)要素:本發(fā)明解決的問題是提供一種晶圓刻蝕后的清洗方法,提高晶圓清洗的效果,進(jìn)而提高晶圓清洗的良率。為解決上述問題,本發(fā)明提供了一種晶圓刻蝕后的清洗方法,包括:提供晶圓;在晶圓上形成介質(zhì)層,并于所述介質(zhì)層中形成貫穿其厚度的通孔,所述介質(zhì)層為疏水性;進(jìn)行氨氣等離子體處理,使所述介質(zhì)層的上表面以及通孔的側(cè)壁由疏水性轉(zhuǎn)化為親水性;進(jìn)行清洗工藝。可選的,所述氨氣等離子體處理的壓強(qiáng)為5mTorr~200mTorr,電源功率為100W~1000W,時(shí)間為5s~60s,氣體為NH3、He和Ar的混合氣體,所述混合氣體中NH3的流量為10sccm~500sccm,He的流量為10sccm~200sccm,Ar的流量為10sccm~200sccm。與現(xiàn)有技術(shù)相比,本發(fā)明技術(shù)方案具有以下優(yōu)點(diǎn):在晶圓表面介質(zhì)層中形成貫穿介質(zhì)層厚度的通孔之后,進(jìn)行氨氣等離子體處理,在不影響介質(zhì)層孔隙率的前提下,增加位于介質(zhì)層上表面以及通孔側(cè)壁上氫鍵的數(shù)目,使所述介質(zhì)層的上表面以及通孔的側(cè)壁由疏水性轉(zhuǎn)化為親水性,進(jìn)而在晶圓清洗過程中使介質(zhì)層的上表面以及通孔的側(cè)壁更易與清洗溶液接觸,使晶圓刻蝕后殘留的聚合物和污染物隨清洗溶液去除,提高了晶圓清洗的效果以及良率。進(jìn)一步的,在晶圓上形成介質(zhì)層之前,先在晶圓表面形成停止層,在貫穿介質(zhì)層厚度的通孔形成后,進(jìn)行氨氣等離子體處理時(shí),所述停止層能夠有效保護(hù)晶圓,避免氨氣等離子體處理對(duì)晶圓表面以及形成于晶圓中的半導(dǎo)體器件造成損傷。附圖說明圖1為本發(fā)明晶圓刻蝕后的清洗方法一個(gè)實(shí)施方式的流程示意圖;圖2~圖6為本發(fā)明晶圓刻蝕后的清洗方法一個(gè)實(shí)施例的結(jié)構(gòu)示意圖。具體實(shí)施方式為使本發(fā)明的上述目的、特征和優(yōu)點(diǎn)能夠更加明顯易懂,下面結(jié)合附圖對(duì)本發(fā)明的具體實(shí)施方式做詳細(xì)的說明。在下面的描述中闡述了很多具體細(xì)節(jié)以便于充分理解本發(fā)明,但是本發(fā)明還可以采用其它不同于在此描述的其它方式來實(shí)施,因此本發(fā)明不受下面公開的具體實(shí)施例的限制。正如背景技術(shù)部分所述,現(xiàn)有工藝在干法刻蝕之后,通常利用單個(gè)晶圓清洗方法對(duì)表面低k或者超低k介質(zhì)層中形成有刻蝕圖案的晶圓進(jìn)行清洗,以去除刻蝕殘留的聚合物,使清洗后殘留的聚合物在設(shè)定范圍之內(nèi),利于后續(xù)工藝(如:在通孔內(nèi)進(jìn)行的金屬填充工藝)的進(jìn)行。但是,在對(duì)清洗后的晶圓進(jìn)行檢測后發(fā)現(xiàn),現(xiàn)有晶圓清洗方法的效果不明顯,良率低。發(fā)明人經(jīng)過研究發(fā)現(xiàn),單個(gè)晶圓清洗方法對(duì)表面低k或者超低k介質(zhì)層中形成有通孔的晶圓清洗效果不明顯、良率低,是由以下原因造成的:低k或者超低k介質(zhì)層表面為疏水性,通過單個(gè)晶圓清洗方法對(duì)低k或者超低k介質(zhì)層表面進(jìn)行清洗時(shí),清洗溶液難以浸潤其表面,附著于低k或者超低k介質(zhì)層表面的聚合物和污染物難以隨清洗溶液一起脫離低k或者超低k介質(zhì)層表面。基于上述分析可知:可在不損害低k或者超低k介質(zhì)層的前提下,采用使低k或者超低k介質(zhì)層表面由疏水性轉(zhuǎn)化為親水性的方法解決現(xiàn)有效果不明顯、良率低的問題。發(fā)明人經(jīng)過進(jìn)一步研究發(fā)現(xiàn):在通過氦氣和/或氫氣等離子對(duì)低k介質(zhì)層表面的掩膜層進(jìn)行灰化處理時(shí),由于氦氣和/或氫氣不包含氧原子,其不會(huì)對(duì)低k或者超低k介質(zhì)層造成損害,但是,灰化處理后的低k或者超低k介質(zhì)層表面仍為疏水性;若通過氦氣和/或氫氣等離子對(duì)低k或者超低k介質(zhì)層進(jìn)一步進(jìn)行過刻蝕,低k或者超低k介質(zhì)層表面仍不能從疏水性轉(zhuǎn)變?yōu)橛H水性,而且過刻蝕還可能導(dǎo)致低k或者超低k介質(zhì)層的孔隙率提高,降低了低k或者超低k介質(zhì)層的k值,影響其性能。而通過氨氣等離子對(duì)低k或者超低k介質(zhì)層表面進(jìn)行處理時(shí),氨氣等離子不會(huì)影響低k或者超低k介質(zhì)層的k值,且氨氣等離子體中的氫鍵會(huì)附著于低k或者超低k介質(zhì)層表面,使低k或者超低k介質(zhì)層表面由疏水性轉(zhuǎn)化為親水性,使低k或者超低k介質(zhì)層表面易于與清洗溶液接觸,進(jìn)而使殘留于低k或者超低k介質(zhì)層表面的聚合物和污染物隨清洗溶液一起去除,提高晶圓清洗的效果。針對(duì)上述分析,本發(fā)明提供了一種晶圓刻蝕后的清洗方法,在晶圓表面介質(zhì)層中形成通孔后,對(duì)介質(zhì)層上表面以及通孔的側(cè)壁進(jìn)行氨氣等離子體處理,使介質(zhì)層的上表面以及通孔的側(cè)壁由疏水性轉(zhuǎn)化為親水性,最后再進(jìn)行清洗工藝,去除殘留于介質(zhì)層上表面以及通孔側(cè)壁上的聚合物和污染物。本發(fā)明晶圓刻蝕后的清洗方法的清洗效果好、良率高。下面結(jié)合附圖進(jìn)行詳細(xì)說明。參考圖1,為本發(fā)明晶圓刻蝕后的清洗方法一個(gè)實(shí)施方式的流程示意圖,包括:步驟S1,提供晶圓,并在晶圓上由下至上依次形成停止層和介質(zhì)層;步驟S2,在所述介質(zhì)層上形成掩膜層,所述掩膜層中形成有與通孔形狀對(duì)應(yīng)的掩膜圖形;步驟S3,沿掩膜圖形刻蝕所述介質(zhì)層,形成貫穿所述介質(zhì)層厚度的通孔,在形成通孔的同時(shí)去除介質(zhì)層上部分厚度的掩膜層;步驟S4,去除介質(zhì)層上剩余的掩膜層;步驟S5,進(jìn)行氨氣等離子體處理,使所述介質(zhì)層的上表面以及通孔的側(cè)壁由疏水性轉(zhuǎn)化為親水性;步驟S6,進(jìn)行清洗工藝。圖2~圖6為本發(fā)明晶圓刻蝕后的清洗方法一個(gè)實(shí)施例的結(jié)構(gòu)示意圖,結(jié)合圖2~圖6,通過具體實(shí)施例對(duì)本發(fā)明晶圓刻蝕后的清洗方法做進(jìn)一步說明。首先,參考圖2,提供晶圓10。圖2為晶圓10的俯視圖,所述晶圓10分成若干器件區(qū)域?,F(xiàn)有工藝中,通常在一片晶圓的各器件區(qū)域中制作相同的半導(dǎo)體器件,且各半導(dǎo)體器件同時(shí)制作,制作的工藝、流程以及條件完全相同,以簡化半導(dǎo)體器件的制作工藝,降低半導(dǎo)體器件的制作成本。因此,可以以對(duì)晶圓10中一個(gè)器件區(qū)域上的介質(zhì)層進(jìn)行刻蝕形成通孔,并進(jìn)行刻蝕后清洗工藝為例,對(duì)本發(fā)明的晶圓刻蝕后的清洗方法進(jìn)行說明。本實(shí)施例中,以對(duì)晶圓10中器件區(qū)域100上的介質(zhì)層中形成通孔,并進(jìn)行刻蝕后清洗工藝為例,對(duì)本發(fā)明的晶圓刻蝕后的清洗方法進(jìn)行說明,晶圓10中其他器件區(qū)域上半導(dǎo)體器件的制作工藝與器件區(qū)域100上半導(dǎo)體器件的制作工藝相同,在此不再贅述。圖3為圖2中晶圓10中器件區(qū)域100沿AA方向的剖視圖。參考圖3,在器件區(qū)域100上由下至上依次形成停止層102和介質(zhì)層104。本實(shí)施例中,所述器件區(qū)域100中還可形成有半導(dǎo)體器件(圖未示)。所述停止層102的材料為氮化硅,所述介質(zhì)層104為疏水性,所述介質(zhì)層104的材料可為低k材料或者超低k材料。繼續(xù)參考圖3,在所述介質(zhì)層104上形成掩膜層,所述掩膜層中形成有與通孔形狀對(duì)應(yīng)的掩膜圖形112。本實(shí)施例中,所述掩膜層為多層結(jié)構(gòu),位于介質(zhì)層104上的掩膜層由下至上依次包括:圖形膜層106a、介質(zhì)層抗反射層(DielectricAnti-ReflectionCoat簡稱DARC)108和光刻膠層(photoresist,簡稱為PR)110。所述掩膜圖形112位于掩膜層中的光刻膠層110中,形成掩膜圖形112的方法為曝光、顯影工藝。之所以選擇多層結(jié)構(gòu)的掩膜層,是因?yàn)椋盒纬捎谄骷^(qū)域100中的半導(dǎo)體器件特征尺寸較小,光刻膠層110的厚度較薄,以包含掩膜圖形112的光刻膠層110為掩模對(duì)介質(zhì)層104進(jìn)行刻蝕時(shí),光刻膠層110易在通孔形成之前被完全去除,而采用圖形膜層106a、介質(zhì)層抗反射層108和光刻膠層110共同作為掩膜層,可以通過包含掩膜圖形112的光刻膠層110定義出圖形,在之后的刻蝕中圖形被轉(zhuǎn)移到介質(zhì)層反射層108和圖形膜層106a,在光刻膠層110被消耗完之后,由介質(zhì)層抗反射層108做掩模,在介質(zhì)層抗反射層108被消耗完之后,由圖形膜層106a做掩模。以保證在圖形膜層106a被完全去除之前,形成通孔。具體的,所述圖形膜層106a的材料為無定形碳,形成所述圖形膜層106a的方法為化學(xué)氣相沉積;所述介質(zhì)層抗反射層108的材料為氮化硅或者氮氧化硅,形成所述介質(zhì)層抗反射層108的方法為化學(xué)氣相沉積。在其他實(shí)施例中,所述掩膜層還可為單層結(jié)構(gòu),所述掩膜層的材料為光刻膠。參考圖4,沿圖3中掩膜圖形112刻蝕所述介質(zhì)層104,形成貫穿所述介質(zhì)層104厚度的通孔114,在形成通孔114的同時(shí)去除介質(zhì)層104上部分厚度的掩膜層。本實(shí)施例中,沿圖3中掩膜圖形112刻蝕所述介質(zhì)層104,形成貫穿所述介質(zhì)層104厚度的通孔114的方法為干法刻蝕,如各向異性干法刻蝕。本實(shí)施例中,由于光刻膠層110和介質(zhì)層抗反射層108的厚度遠(yuǎn)小于圖形膜層106a的厚度,在形成通孔114時(shí)去除部分厚度的掩膜層為光刻膠層110、介質(zhì)層抗反射層108和部分厚度的圖形膜層106a,剩余的掩膜層為部分厚度的圖形膜層106b。在其他實(shí)施例中,剩余的掩膜層還可為由部分厚度的光刻膠層、介質(zhì)層抗反射層和圖形膜層構(gòu)成的多層結(jié)構(gòu),或者部分厚度的介質(zhì)層抗反射層和圖形膜層構(gòu)成的多層結(jié)構(gòu),其與形成通孔114之前掩膜層中光刻膠層110、介質(zhì)層抗反射層108和圖形膜層106a各層的厚度以及形成通孔114的刻蝕工藝有關(guān)。在形成通孔114時(shí),所述停止層102能夠有效保護(hù)位于其下方的器件區(qū)域100表面或者器件區(qū)域100中的半導(dǎo)體器件。參考圖5,去除介質(zhì)層104上剩余的掩膜層。本實(shí)施例中,由于剩余的掩膜層為部分厚度的圖形膜層106b,相應(yīng)的,去除介質(zhì)層104上剩余的掩膜層的方法為灰化工藝,所述灰化工藝的氣體可為氫氣或/和氦氣,其具體工藝為本領(lǐng)域技術(shù)人員所熟知,在此不再贅述。需要說明的是,在去除介質(zhì)層104上剩余的掩膜層時(shí),需嚴(yán)格控制灰化工藝的時(shí)間,在剩余的掩膜層被完全去除后立即停止灰化工藝,避免灰化工藝對(duì)介質(zhì)層104進(jìn)行過刻蝕,進(jìn)而避免灰化工藝對(duì)介質(zhì)層104的k值造成影響。繼續(xù)參考圖5,進(jìn)行氨氣等離子體處理,使所述介質(zhì)層104的上表面以及通孔114的側(cè)壁由疏水性轉(zhuǎn)化為親水性。本實(shí)施例中,所述氨氣等離子體處理的壓強(qiáng)可為5mTorr~200mTorr,電源功率可為100W~1000W,時(shí)間可為5s~60s,氣體可為NH3、He和Ar的混合氣體,所述混合氣體中NH3的流量為10sccm~500sccm,He的流量為10sccm~200sccm,Ar的流量為10sccm~200sccm。由于NH3、He和Ar的混合氣體中不包含氧原子,其不會(huì)對(duì)介質(zhì)層104的k值造成影響;且氨氣等離子體中的氫鍵會(huì)附著于介質(zhì)層104的上表面以及通孔114的側(cè)壁,使介質(zhì)層104的上表面以及通孔114的側(cè)壁由疏水性轉(zhuǎn)化為親水性。在進(jìn)行氨氣等離子處理時(shí),所述通孔114底部的停止層102還能夠有效保護(hù)位于其下方的器件區(qū)域100表面或者器件區(qū)域100中的半導(dǎo)體器件。參考圖6,去除通孔114底部的停止層102。本實(shí)施例中,去除通孔114底部的停止層102的方法為干法刻蝕。具體的,所述干法刻蝕的壓強(qiáng)可為5mTorr~200mTorr,電源功率可為100W~1000W,時(shí)間為5s~60s,氣體可為CH4、CHF3、CH3F、He和Ar的混合氣體,所述混合氣體中CH4的流量為10sccm~500sccm,CHF3的流量為10sccm~200sccm,CH3F的流量為10sccm~100sccm,He的流量為10sccm~200sccm,Ar的流量為10sccm~200sccm。繼續(xù)參考圖6,進(jìn)行清洗工藝。本實(shí)施例中,所述清洗工藝可為單個(gè)晶圓清洗工藝;所述清洗工藝的清洗溶液為水基清洗溶液。由于介質(zhì)層104的上表面以及通孔114的側(cè)壁為親水性,其易于與清洗溶液接觸,進(jìn)而使殘留于介質(zhì)層104上表面以及通孔114的側(cè)壁的聚合物和污染物隨清洗溶液一起去除,提高晶圓清洗的效果,晶圓清洗的良率高。本發(fā)明雖然已以較佳實(shí)施例公開如上,但其并不是用來限定本發(fā)明,任何本領(lǐng)域技術(shù)人員在不脫離本發(fā)明的精神和范圍內(nèi),都可以利用上述揭示的方法和技術(shù)內(nèi)容對(duì)本發(fā)明技術(shù)方案做出可能的變動(dòng)和修改,因此,凡是未脫離本發(fā)明技術(shù)方案的內(nèi)容,依據(jù)本發(fā)明的技術(shù)實(shí)質(zhì)對(duì)以上實(shí)施例所作的任何簡單修改、等同變化及修飾,均屬于本發(fā)明技術(shù)方案的保護(hù)范圍。