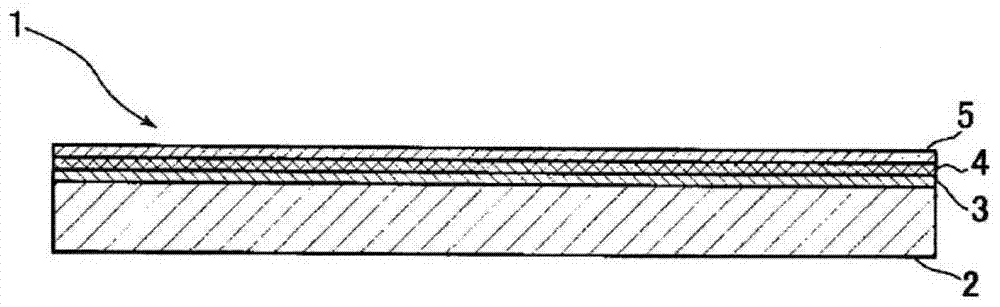
本發(fā)明關(guān)于內(nèi)部形成有固態(tài)電解質(zhì)層(典型為導(dǎo)電高分子層)的固態(tài)電解電容器,及可在這類電容器中使用的電極箔。此外,本發(fā)明關(guān)于集電體及電極,以及使用這些對象的蓄電池、電雙層電容器、混合式電容器等蓄電組件。
背景技術(shù):與固態(tài)電解電容器相關(guān)的先前技術(shù)近年來,伴隨著電子機(jī)器的動作頻率達(dá)到高頻化,電子零件之一的電解電容器中,要求在較以往更高的動作頻率區(qū)域中具有優(yōu)異的阻抗特性的制品。因應(yīng)此要求,開發(fā)出各種將具有高電傳導(dǎo)度的導(dǎo)電性高分子用作為固態(tài)電解質(zhì)的固態(tài)電解電容器。這類固態(tài)電解電容器除了壽命和溫度特性外,尤其高頻特性佳,故廣泛地采用于個人計算機(jī)用的電路等。最單純的例子之一,可通過下列步驟制作出卷繞型的固態(tài)電解電容器:(i)對陽極鋁箔表面進(jìn)行化成處理以形成氧化覆膜后,夾介分隔器紙將該陽極鋁箔與陰極鋁箔予以重迭,將引線材連接于各電極箔后卷繞而制作出電容器組件;(ii)將制作出的電容器組件收容于鋁盒后,浸漬于導(dǎo)電性高分子溶液并加熱使導(dǎo)電性高分子進(jìn)行熱聚合,而在兩電極箔間形成固態(tài)的導(dǎo)電性高分子層。若以陽極鋁箔為陽極,以陰極鋁箔及與該陰極鋁箔電性連接的導(dǎo)電性高分子層為陰極時,由于此等兩極夾介絕緣性的氧化覆膜而連接,故可在兩極間進(jìn)行充放電。上述固態(tài)電解電容器中,在陰極鋁箔上未進(jìn)行化成處理,故不存在人為形成的氧化覆膜。然而,由于實際在制造、使用時所產(chǎn)生的自然氧化,而在陰極鋁箔上亦形成氧化覆膜。此時,整體固態(tài)電解電容器中,形成(i)陽極鋁箔、(ii)陽極鋁箔上的氧化覆膜、(iii)導(dǎo)電性高分子層、(iv)陰極鋁箔上的自然氧化覆膜、(v)陰極鋁箔的層構(gòu)造,而成為等效串聯(lián)連接2個電容器的狀態(tài),因而產(chǎn)生固態(tài)電解電容器整體的靜電電容減少的問題。為了對應(yīng)此問題,已進(jìn)行防止陰極中產(chǎn)生靜電電容成分以增大電容器的靜電電容的研究。以下針對從先前研究所得的數(shù)種陰極箔以及此等先前的陰極箔所具有的問題點進(jìn)行說明。專利文獻(xiàn)1及2中,揭示一種在陰極鋁箔表面形成化成覆膜,并通過蒸鍍在其上方形成TiN等金屬氮化物或TiC等金屬碳化物的覆膜而成的陰極箔。然而,Ti等金屬及其氮化物、碳化物的抗熱氧化性不足,故在這類陰極箔上,由于電容器制造步驟中所包含的熱處理使氧化覆膜成長而產(chǎn)生靜電電容成分,且亦引起ESR(EquivalentSeriesResistance:等效串聯(lián)電阻)上升的問題。專利文獻(xiàn)3中,揭示一種在具有閥作用的金屬的表面形成碳覆膜而成的陰極箔。然而,當(dāng)將碳直接成膜于鋁等的金屬箔時,由于金屬箔與碳覆膜的密著性差,故會引起ESR上升的問題。專利文獻(xiàn)4中,揭示一種在鋁箔表面形成含碳層而成的陰極箔,且在鋁箔表面與該含碳層之間,形成由纖維狀或絲狀碳化鋁(Al4C3、碳化鋁細(xì)絲)所構(gòu)成的中介存在層,以提升層間密著性的陰極箔。然而,這類陰極箔中,上述含碳層是由粒子形態(tài)的碳所構(gòu)成的層,鋁箔表面與含碳層的接觸為點接觸,所以存在有起因于接觸面積小而使界面電阻上升的問題。再者,上述含碳層是將含碳物質(zhì)涂布于鋁箔表面,并通過加熱干燥處理使碳粒子固著的方法來形成,故難以形成較薄的含碳層,而使Al層與固態(tài)電解質(zhì)層之間的電子傳導(dǎo)距離增長,亦會引起ESR上升的問題。此外,這類陰極箔的耐水性不足,尤其在高溫環(huán)境中,作為電子的傳導(dǎo)路徑的碳化鋁細(xì)絲會被切斷,亦會引起導(dǎo)電性降低的問題。專利文獻(xiàn)5中,揭示一種在經(jīng)粗面化的鋁箔上,通過真空蒸鍍法使Ni成膜而成的陰極箔。根據(jù)專利文獻(xiàn)5,形成于Ni層表面的Ni氧化覆膜為半導(dǎo)體且具有導(dǎo)電性,故可實現(xiàn)電容器的低ESR化。然而,并無法忽視因形成氧化覆膜所導(dǎo)致的導(dǎo)電性的降低,且半導(dǎo)體仍不足以作為覆膜構(gòu)成物質(zhì)。至少在覆膜的最上層,仍優(yōu)選使用抗氧化性佳的導(dǎo)電性物質(zhì)。其它,用以在非采用固態(tài)電解而是采用驅(qū)動用電解液而動作的電解電容器中所使用的陰極箔,在專利文獻(xiàn)6中,揭示一種將Ti等金屬蒸鍍在經(jīng)粗面化的鋁箔以形成金屬覆膜,然后通過涂布分散有碳微粒的黏合劑及隨后的加熱處理,使該碳微粒固著而成的陰極箔。然而,專利文獻(xiàn)6所記載的陰極箔中,Ti覆膜表面因驅(qū)動用電解液而產(chǎn)生氧化,在由Ti覆膜所構(gòu)成的層與由碳所構(gòu)成的層的界面上產(chǎn)生較大電阻,而使電容器的ESR上升(專利文獻(xiàn)6所記載的陰極箔中,為了抑制這類Ti氧化所造成的影響,較佳進(jìn)行蝕刻等粗面化處理)。此外,在使用作為固態(tài)電解電容器時,亦由于電容器制造步驟中所包含的熱處理使氧化覆膜成長而使ESR上升。此外,即使通過黏合劑等來接合Ti覆膜與碳,接合部分上產(chǎn)生較大界面電阻,使電容器的ESR上升。固態(tài)電解電容器中,一般而言,若適度地粗化陰極箔表面,則與固態(tài)電解質(zhì)層的接觸面積會增加,因而使ESR降低,但該效果較小。此外,當(dāng)通過蝕刻處理等使鋁基材表面粗面化時,會在所形成的細(xì)微孔內(nèi)部的覆膜與鋁基材之間形成空間,于電容器的制造步驟中所使用的藥品、水分在此空間中引起反應(yīng),由于該反應(yīng)而使表面處于不穩(wěn)定狀態(tài),再者,由于氧擴(kuò)散而使鋁基材與覆膜的界面容易氧化,故會引起界面電阻的上升、及電容器的劣化的問題。此外,伴隨著粗面化的進(jìn)行,亦有電容器的制造成本上升的問題。如上所述,首先在鋁箔上形成金屬膜而成的已知的陰極箔中,存在有覆膜表面的氧化的問題,若氧化反應(yīng)隨時間變化等而進(jìn)行,則陰極具有靜電電容,此外,在鋁箔上直接或夾介金屬覆膜等而形成有碳層的已知的陰極箔中,若層間的密著性不足,則與碳接觸的鋁箔表面或金屬覆膜表面會氧化,因此同樣地陰極具有靜電電容。藉此,如已說明般,固態(tài)電解電容器整體的靜電電容減少。其它,上述先前的各陰極箔系具有ESR的上升或高成本化等問題。與蓄電池、電雙層電容器、混合式電容器等相關(guān)的先前技術(shù)近年來,從便攜式電子機(jī)器的多功能化、汽車及運輸和建設(shè)機(jī)械車輛的燃料成本改善、分散型可再生能源的普及、災(zāi)害緊急時備用電源的擴(kuò)充等觀點來看,對于所裝載的蓄電組件的需求乃逐漸增大。蓄電組件可列舉出電雙層電容器、混合式電容器、蓄電池等,要求該輸出密度(W/kg、W/L)或壽命特性的進(jìn)一步提升。構(gòu)成此等蓄電組件的電極,就處理加工強(qiáng)度或電傳導(dǎo)性等的性能面、及生產(chǎn)性、制造成本等的觀點來看,大多使用由金屬箔所構(gòu)成的集電體。電極是在集電體上形成有由活性物質(zhì)、導(dǎo)電輔助劑、及黏合劑所構(gòu)成的電極層而構(gòu)成,但當(dāng)集電體與該電極層的密著性以及電傳導(dǎo)性、化學(xué)穩(wěn)定性不足時,由于接觸電阻的增加而無法得到滿足的輸出密度,故難以進(jìn)行急速的充放電。再者,伴隨著蓄電組件的充放電循環(huán),集電體與電極層的界面亦隨著時間經(jīng)過,因氧化等化學(xué)變化而造成變質(zhì),或電極層會從集電體剝離等,而有導(dǎo)致內(nèi)部電阻增大或壽命降低的疑慮。與此相關(guān),例如在專利文獻(xiàn)7中,揭示一種于集電體與活性物質(zhì)間形成有碳覆膜層的電池。然而,當(dāng)直接將碳層形成于金屬箔上時,由于金屬箔與碳覆膜層的密著性以及電傳導(dǎo)性、化學(xué)穩(wěn)定性不足,因此逐漸使集電體與電極層的接觸電阻增大,不久即產(chǎn)生輸出密度的降低或內(nèi)部電阻上升的問題,而難以進(jìn)行急速的充放電。其它,根據(jù)本發(fā)明者的調(diào)查,相關(guān)聯(lián)的先前技術(shù)文獻(xiàn)乃存在有專利文獻(xiàn)8至11,但這些所揭示的覆膜構(gòu)成亦具有同樣問題。先前技術(shù)文獻(xiàn)專利文獻(xiàn)專利文獻(xiàn)1:日本特開2007-36282專利文獻(xiàn)2:日本特開2007-19542專利文獻(xiàn)3:日本特開2006-190878專利文獻(xiàn)4:日本特開2006-100478專利文獻(xiàn)5:日本特開2009-49376專利文獻(xiàn)6:日本特開2007-95865專利文獻(xiàn)7:日本特開平11-250900專利文獻(xiàn)8:日本特開2011-142100專利文獻(xiàn)9:日本特開2010-218971專利文獻(xiàn)10:日本特開2009-283275專利文獻(xiàn)11:日本特開2008-270092
技術(shù)實現(xiàn)要素:發(fā)明所欲解決的課題本發(fā)明為了解決先前技術(shù)中的上述問題點而創(chuàng)作。即,本發(fā)明目的為:在將覆膜形成于鋁箔上而成的固態(tài)電解電容器用陰極箔中,通過提高對構(gòu)成覆膜的各層的抗氧化性以及層間的密著性,來防止陰極中靜電電容的產(chǎn)生。此外,本發(fā)明的另一目的為:防止在這類陰極箔中因覆膜中成分構(gòu)成的急遽變化而產(chǎn)生較大界面電阻,并藉此降低電容器的ESR及漏電流(LC:LeakageCurrent)。再者,本發(fā)明的目的為:解決專利文獻(xiàn)7至11所揭示的先前技術(shù)中的問題點,并且為了實現(xiàn)長期間可降低內(nèi)部電阻的增大,維持高輸出密度以進(jìn)行急速的充放電,且壽命特性亦佳的蓄電組件,而提高集電體與電極層的密著性及電傳導(dǎo)性,并且抑制因集電體與電極層的界面上的化學(xué)變化所造成的變質(zhì)。用以解決課題的手段為了解決上述課題,本發(fā)明提供一種電極材料,其特征是,在電極基材上形成有第1導(dǎo)電層、混合存在有構(gòu)成第1導(dǎo)電層的物質(zhì)與碳而成的混合存在層、及實質(zhì)上由碳所構(gòu)成的第2導(dǎo)電層;混合存在層的成分構(gòu)成為:自第1導(dǎo)電層朝向第2導(dǎo)電層,從實質(zhì)上僅含有構(gòu)成第1導(dǎo)電層的物質(zhì)的成分構(gòu)成,變化為實質(zhì)上僅含有碳的成分構(gòu)成。本發(fā)明所提供的電極材料中,由于在第1導(dǎo)電層與第2導(dǎo)電層之間形成有兩導(dǎo)電層的構(gòu)成成分混合存在的混合存在層,故可提升構(gòu)成該第1導(dǎo)電層的物質(zhì)與碳的密著性。根據(jù)該構(gòu)成,可解決因碳與構(gòu)成第1導(dǎo)電層的物質(zhì)的密著不足,使構(gòu)成第1導(dǎo)電層的物質(zhì)氧化而使電極材料具有靜電電容且ESR亦上升的先前技術(shù)的問題。此外,第2導(dǎo)電層實質(zhì)上由碳所構(gòu)成,所以抗氧化性佳。再者,在與第1導(dǎo)電層的交界區(qū)域中,混合存在層實質(zhì)上僅含有構(gòu)成第1導(dǎo)電層的物質(zhì),且在與第2導(dǎo)電層的交界區(qū)域中,混合存在層實質(zhì)上僅含有碳,故亦不會造成在此等交界區(qū)域中因電極材料的成分構(gòu)成急遽變化而產(chǎn)生較大界面電阻的問題。上述記載中,所謂“實質(zhì)上僅含有構(gòu)成第1導(dǎo)電層的物質(zhì)”,并不必然意味著完全不含構(gòu)成該第1導(dǎo)電層的物質(zhì)以外的成分。因應(yīng)層內(nèi)的成分純度的控制、與雜質(zhì)混入相關(guān)的制造技術(shù)上的限制、或是在個別制品中作為上述電極材料所能夠容許的誤差的靜電電容的程度等,混合存在層與各導(dǎo)電層的交界區(qū)域上的實際的成分構(gòu)成可有所變化。此內(nèi)容在“實質(zhì)上由碳所構(gòu)成”、“實質(zhì)上僅含有碳”等記載中亦同。此外,上述記載中,所謂“混合存在層的成分構(gòu)成,自第1導(dǎo)電層朝向第2導(dǎo)電層,從實質(zhì)上僅含有構(gòu)成第1導(dǎo)電層的物質(zhì)的成分構(gòu)成,變化為實質(zhì)上僅含有碳的成分構(gòu)成”,并不必然意味著混合存在層內(nèi)的碳含有率在從第1導(dǎo)電層朝向第2導(dǎo)電層的方向上單調(diào)增加。因應(yīng)由制造技術(shù)上的限制所產(chǎn)生的各成分濃度的變異等,混合存在層內(nèi)的各位置上的實際的成分構(gòu)成可有所變化。然而,較佳系形成混合存在層,以使碳含有率自第1導(dǎo)電層朝向第2導(dǎo)電層連續(xù)地上升。上述第1導(dǎo)電層,可含有:Ta、Ti、Cr、Al、Nb、V、W、Hf、Cu、此等金屬的氮化物、及此等金屬的碳化物中的任一種??墒褂迷跇?gòu)成本發(fā)明的電極材料的第1導(dǎo)電層的物質(zhì)并不限定于此,但當(dāng)使用鋁基材作為電極基材時,就能源效率或與鋁基材的密著性的觀點來看,優(yōu)選使用上述列舉的物質(zhì),最優(yōu)選使用以Ti、Al為首的金屬(只要不損及與基材的密著性或第1導(dǎo)電層的導(dǎo)電性,亦可為合金等含有復(fù)數(shù)種成分)??捎米鳛殡姌O基材的材料并不限于鋁,亦可使用閥作用金屬的Ta、Ti、Nb等其它任意材料,或是將此等任意材料添加于鋁中的鋁合金等。本發(fā)明的電極材料中,使電極基材粗面化者并非必要條件。如后述實施例中使用性能試驗數(shù)據(jù)所說明般,制作本發(fā)明的電極材料時,即使不使電極基材粗面化,使用該電極基材的固態(tài)電解電容器,亦具有與以往相比更優(yōu)異的靜電電容、ESR、及漏電流特性。尤其是電極基材未經(jīng)粗面化所制作的本發(fā)明的電極基材,與經(jīng)粗面化者相比,乃具有優(yōu)異的耐熱性,此將于后述實施例中顯示。此外,本發(fā)明提供一種固態(tài)電解電容器,其含有電容器組件的固態(tài)電解電容器,該電容器組件具有:陽極箔與陰極箔;設(shè)置于該陽極箔與陰極箔之間的分隔器;及形成于該陽極箔與陰極箔之間的固態(tài)的電解質(zhì)層;該固態(tài)電解電容器的特征是使用上述電極材料作為前述陰極箔。本發(fā)明的電極材料特別適合用作為卷繞型或積層型固態(tài)電解電容器中的陰極箔,但除此之外,亦可使用在以采用電解液而動作的電解電容器為首的各種電容器、或是電雙層電容器、鋰離子電容器、鋰離子電池、太陽能電池等。具體而言,若在本發(fā)明的電極材料的上述實質(zhì)上由碳所構(gòu)成的第2導(dǎo)電層上還形成由活性碳所構(gòu)成的層,則可將該電極材料用作為電雙層電容器用的正極或負(fù)極(這類構(gòu)成的電極材料亦可直接使用作為鋰離子電容器的正極),或者是,同樣若在本發(fā)明的電極材料的上述第2導(dǎo)電層上形成由含有Li的活性物質(zhì)所構(gòu)成的層,則可將該電極材料用作為鋰離子電池的正極。即,本發(fā)明的電極材料不僅可在該狀態(tài)下直接用作為電極,亦可如上述般形成追加的層等,因應(yīng)需要進(jìn)行進(jìn)一步的加工而使用作為任意蓄電裝置中的陽極(正極)或陰極(負(fù)極)。上述固態(tài)的電解質(zhì)層可含有:二氧化錳(MnO2)、四氰基苯醌二甲烷(TCNQ)、聚乙撐二氧噻吩(PEDOT)、聚苯胺(PANI)、及聚吡咯中的任一種,但亦可使用此等之外的電解質(zhì)。就其一例而言,由PEDOT所構(gòu)成的固態(tài)電解質(zhì)層的形成,可通過將電容器組件浸漬于3,4-乙撐二氧噻吩及對甲苯磺酸鐵(II)的混合溶液中并進(jìn)行加熱,使電解質(zhì)熱聚合來進(jìn)行。就上述電極材料的典型的一項形態(tài)而言,本發(fā)明提供一種陰極箔,其使用在含有電容器組件的固態(tài)電解電容器的陰極箔,該電容器組件具有:陽極箔與陰極箔;設(shè)置于該陽極箔與陰極箔之間的分隔器;及形成于該陽極箔與陰極箔之間的固態(tài)的導(dǎo)電性高分子層。該陰極箔的特征為:包括未經(jīng)粗面化的鋁箔、形成于鋁箔上且實質(zhì)上由Ti或Al所構(gòu)成的金屬層、形成于金屬層上且混合存在有Ti或Al與碳而成的混合存在層、及形成于混合存在層上且實質(zhì)上由碳所構(gòu)成的碳層;混合存在層的成分構(gòu)成為:自金屬層朝向碳層,從實質(zhì)上僅含有Ti或Al的成分構(gòu)成變化為實質(zhì)上僅含有碳的成分構(gòu)成。上述陰極箔相當(dāng)于如后述實施例中使用性能試驗數(shù)據(jù)所說明的本發(fā)明的典型的一項方式。然而,用以解決上述先前技術(shù)的課題的實施方式顯然并不限定于此。例如,從后述性能試驗中,亦可得知本發(fā)明的陰極箔中,即使鋁基材經(jīng)粗面化,使用此固態(tài)電解電容器,與以往相比具有優(yōu)異的靜電電容等特性,且可用作為電極材料的材料亦不限定于鋁。就與鋁的密著性的觀點來看,使用于金屬層的材料優(yōu)選使用Ti或Al中的任一種,但同樣亦可使用Ta、Cr等與鋁具有優(yōu)異密著性的其它材料,或是當(dāng)使用其它電極基材時,可因應(yīng)該基材通過適當(dāng)?shù)牟牧蟻硇纬山饘賹?。例如,?dāng)使用銅箔作為電極基材時,若通過離子蒸鍍法等來形成由與銅箔的密著性佳的Cr所構(gòu)成的金屬層,則可推測為Cr貫穿銅箔表面上的自然氧化覆膜,直接與銅箔結(jié)合而得到高電傳導(dǎo)性,并抑制靜電電容成分的產(chǎn)生,因此可得到與在鋁箔上形成由Ti或Al所構(gòu)成的金屬層時相同的特性。此外,本發(fā)明的陰極箔中,在金屬層與碳層之間形成有構(gòu)成各層的成分所混合存在的混合存在層。依據(jù)這類混合存在層的導(dǎo)入所達(dá)成的金屬與碳間的密著性的提升,顯然在以Ti或Al以外的材料來形成該金屬層時亦同樣可得到,并可推測為由于該密著性的提升,可防止金屬中的氧化覆膜的形成,而抑制陰極箔中的靜電電容的產(chǎn)生。此外,在與金屬層的交界區(qū)域中,混合存在層實質(zhì)上僅含有Ti或Al,且在與碳層的交界區(qū)域中,混合存在層實質(zhì)上僅含有碳,故在該交界區(qū)域中不會引起成分構(gòu)成的急遽變化,而可將界面電阻抑制較低的效果,顯然在以Ti或Al以外的材料來形成該金屬層時亦同樣可得到。為了解決專利文獻(xiàn)7至11所揭示的先前技術(shù)中的問題點,本發(fā)明提供一種電極用集電體,其特征為:在含有金屬的基材上,形成有含有金屬的第1導(dǎo)電層;混合存在有構(gòu)成該含有金屬的第1導(dǎo)電層的物質(zhì)與碳而成的混合存在層;及實質(zhì)上由碳所構(gòu)成的第2導(dǎo)電層而成;前述混合存在層的成分構(gòu)成為:自前述含有金屬的第1導(dǎo)電層朝向前述第2導(dǎo)電層,從實質(zhì)上僅含有構(gòu)成前述含有金屬的第1導(dǎo)電層的物質(zhì)的成分,變化為實質(zhì)上僅含有碳的成分。本發(fā)明所提供的集電體中,由于在含有金屬的基材表面與實質(zhì)上由碳所構(gòu)成的第2導(dǎo)電層之間,形成有含有金屬的第1導(dǎo)電層以及兩導(dǎo)電層的構(gòu)成成分混合存在的混合存在層,故可分別提升基材與第1導(dǎo)電層的密著性、以及第1導(dǎo)電層與第2導(dǎo)電層的密著性,藉此提升各界面的電傳導(dǎo)性及化學(xué)穩(wěn)定性。根據(jù)該構(gòu)成,可解決:因基材與碳的密著性以及界面的電傳導(dǎo)性或化學(xué)穩(wěn)定性不足,使集電體與電極層的接觸電阻增大,并隨著重復(fù)使用而使集電體的內(nèi)部電阻上升并使電極的輸出密度降低的先前技術(shù)的問題。此外,第2導(dǎo)電層實質(zhì)上由碳所構(gòu)成,所以電傳導(dǎo)性以及抗氧化性等的相對于化學(xué)變化的承受性佳。再者,在第1導(dǎo)電層與第2導(dǎo)電層的交界區(qū)域中,在混合存在層內(nèi)的第1導(dǎo)電層側(cè)的區(qū)域,實質(zhì)上僅含有構(gòu)成第1導(dǎo)電層的物質(zhì),且在混合存在層內(nèi)的第2導(dǎo)電層側(cè)的區(qū)域,實質(zhì)上僅含有碳而構(gòu)成,故亦不會造成在此等交界區(qū)域因成分急遽變化而產(chǎn)生較大界面電阻的問題。上述記載中,所謂“實質(zhì)上僅含有構(gòu)成含有金屬的第1導(dǎo)電層的物質(zhì)”,并不必然意味著完全不含構(gòu)成該第1導(dǎo)電層的物質(zhì)以外的成分。因應(yīng)層內(nèi)的成分純度的控制、與雜質(zhì)混入相關(guān)的制造技術(shù)上的限制、或是在個別制品中作為上述集電體所能夠容許的誤差的密著性或接觸電阻的程度等,混合存在層與各導(dǎo)電層的交界區(qū)域上的實際的成分構(gòu)成可有所變化。此內(nèi)容在“實質(zhì)上由碳所構(gòu)成”、“實質(zhì)上僅含有碳”等記載中亦同。此外,上述記載中,所謂“混合存在層的成分,自第1導(dǎo)電層朝向第2導(dǎo)電層,從實質(zhì)上僅含有構(gòu)成含有金屬的第1導(dǎo)電層的物質(zhì)的成分,變化為實質(zhì)上僅含有碳的成分”,并不必然意味著混合存在層內(nèi)的碳含有率在從第1導(dǎo)電層朝向第2導(dǎo)電層的方向上單調(diào)地增加。因應(yīng)由制造技術(shù)上的限制所產(chǎn)生的各成分濃度的變異等,混合存在層內(nèi)的各位置上的實際的成分可有所變化。然而,優(yōu)選形成混合存在層,以使碳含有率自第1導(dǎo)電層朝向第2導(dǎo)電層連續(xù)地上升。上述第1導(dǎo)電層,可含有:Ta、Ti、Cr、Al、Nb、V、W、Hf、Cu、此等金屬的氮化物、及此等金屬的碳化物中的任一種??墒褂迷跇?gòu)成本發(fā)明的集電體的第1導(dǎo)電層的物質(zhì)并不限定于此等,但當(dāng)使用鋁箔作為含有金屬的基材時,就能源效率或與鋁箔的密著性的觀點來看,優(yōu)選使用上述列舉的物質(zhì),更優(yōu)選使用以Ti、Al為首的金屬(只要不損及與基材的密著性或第1導(dǎo)電層的電傳導(dǎo)性,亦可為合金等含有復(fù)數(shù)種成分)。第2導(dǎo)電層所使用的碳并無特別限制,在碳材料中,若構(gòu)成為電傳導(dǎo)性特佳的類石墨碳,則可提高蓄電組件的輸出密度,故更為理想。此外,就制造成本方面來看亦佳。在此,所謂類石墨碳是指在形成金剛石鍵(碳的sp3雜化軌道鍵結(jié))與石墨鍵(碳的sp2雜化軌道鍵結(jié))兩者的鍵所混合存在的非晶質(zhì)結(jié)構(gòu)的碳中,石墨鍵的比率為過半數(shù)者。但是,非晶質(zhì)結(jié)構(gòu)以外,亦包含具有局部由石墨結(jié)構(gòu)所構(gòu)成的結(jié)晶結(jié)構(gòu)(即由sp2雜化軌道鍵結(jié)所構(gòu)成的六角晶系結(jié)晶結(jié)構(gòu))的相。可用作含有金屬的基材的材料并不限定于鋁,亦可使用Ti、Cu、Ni、Hf、不銹鋼等其它任意材料,或由添加此等任意材料于鋁中的鋁合金等所構(gòu)成的金屬箔。各蓄電組件的正極電極及負(fù)極電極中所使用的作為集電體的金屬箔,分別考慮到電解質(zhì)與活性物質(zhì)的動作電位下,可從電化學(xué)穩(wěn)定性或電傳導(dǎo)性、重量、加工性、制造成本等觀點來選擇。當(dāng)蓄電組件為電雙層電容器時,優(yōu)選為正極及負(fù)極均為鋁箔,當(dāng)蓄電組件為混合式電容器或蓄電池時,優(yōu)選為正極為鋁箔,負(fù)極為鋁箔或銅箔。本發(fā)明的集電體中,使含有金屬的基材粗面化者并非必要條件,但如后述實施例中使用性能試驗數(shù)據(jù)所說明般,制作本發(fā)明的集電體時,經(jīng)粗面化的基材可提高集電體與電極層的密著性或集電能力,故對于輸出密度或壽命特性的提升更為有利。除了與含有金屬的第1導(dǎo)電層、混合存在層、及第2導(dǎo)電層相關(guān)的至目前為止所述的效果外,亦可實現(xiàn)集電體與電極層間的因物理定錨效果所致的密著強(qiáng)度的提升,以及因兩者接觸面積的增大所致的接觸電阻的降低效果。尤其在活性物質(zhì)因離子的吸存(插層)與釋出(去插層)而反復(fù)產(chǎn)生體積膨脹及收縮的混合式電容器或蓄電池中,基材的粗面化更為有效。粗面化的手段雖無特別限制,但在如上述般使用鋁箔或銅箔作為基材的材料時,較佳是通過使用酸或堿溶液的化學(xué)或電化學(xué)蝕刻等來進(jìn)行粗面化,該手法可容易地實現(xiàn)有助于因與電極層的定錨效果所致的密著性提升的細(xì)孔結(jié)構(gòu),且亦為生產(chǎn)性佳的手法。在鋰離子電容器等的混合式電容器或鋰離子蓄電池等的蓄電池中,當(dāng)必須進(jìn)行使堿金屬離子或堿土類金屬離子普遍地吸存于組件內(nèi)的正極電極及/或負(fù)極電極的活性物質(zhì)的預(yù)摻雜操作時,因應(yīng)該制造手法的形態(tài)或生產(chǎn)情況,亦可預(yù)先在金屬箔上形成貫通孔。從上述第1導(dǎo)電層至第2導(dǎo)電層為止的包含混合存在層的合計層厚并無特別限制,例如若將此層厚設(shè)為45nm以下,則可防止集電體與電極層的電子傳導(dǎo)距離增長,而進(jìn)一步提高內(nèi)部電阻的降低效果。尤其如上述般對金屬箔施以粗面化時,若制作出如此合計膜厚較小的集電體,則因蝕刻等而形成于金屬箔的細(xì)微且緊致的細(xì)孔結(jié)構(gòu),不會被形成于該上方的覆膜所埋沒,且不會損及上述定錨效果或接觸面積增大的效果,并且無須在細(xì)孔結(jié)構(gòu)的內(nèi)壁上到處地形成第1、第2導(dǎo)電層。當(dāng)將上述集電體用在混合式電容器或蓄電池的負(fù)極電極側(cè)時,構(gòu)成第2導(dǎo)電層的碳本身可成為能夠吸存或釋出堿金屬離子與堿土類金屬離子中的任一種的活性物質(zhì)。然而,為了得到作為蓄電池的充分的能量密度(Wh/kg、Wh/L),含有活性物質(zhì)的電極層要求具有至少1μm的層厚,但就生產(chǎn)性或制造成本方面等來看,將第2導(dǎo)電層形成至可用作為活性物質(zhì)的約1μm的厚度者效果不佳。優(yōu)選形成含有活性物質(zhì)的電極層,以作為與構(gòu)成本案發(fā)明的集電體的上述第2導(dǎo)電層不同的另外的層。本發(fā)明提供一種電極以及使用該電極作為正極及負(fù)極的蓄電池,該蓄電池例如為鋰離子蓄電池或鈉離子蓄電池、鎂離子蓄電池、鈣離子蓄電池等蓄電池,其具有:形成電極層的正極電極,該電極層是由包含有含有堿金屬與堿土類金屬中任一種的過渡金屬氧化物或過渡金屬磷酸化合物的活性物質(zhì)、導(dǎo)電輔助劑、及黏合劑所構(gòu)成;以及形成電極層的負(fù)極電極,該電極層是由可吸存或釋出堿金屬離子與堿土類金屬離子中任一種的碳材料,且含有Sn、Si或氧化硅、S或硫化物、及氧化鈦中任一種的活性物質(zhì)、導(dǎo)電輔助劑、及黏合劑所構(gòu)成,該蓄電池的特征是使用上述集電體。在此,使用在上述蓄電池中的正極活性物質(zhì)中所含有的含有堿金屬與堿土類金屬中任一種的過渡金屬氧化物或過渡金屬磷酸化合物,例如可列舉出LiCoO2、LiMn2O4、LiNiO2、Li(Ni-Mn-Co)O2、Li(Ni-Co-Al)O2、LiFePO4、NaCrO2、NaFeO2、MgHf(MoO4)3、Ca3Co2O6、Ca3CoMnO6等。本發(fā)明提供一種電極以及使用該電極作為正極及負(fù)極的電雙層電容器,該電雙層電容器使用:形成電極層的正極電極,該電極層是由含有活性碳與碳納米管中任一種的活性物質(zhì)、導(dǎo)電輔助劑、及黏合劑所構(gòu)成;以及形成同樣的層構(gòu)造的負(fù)極電極,該電雙層電容器的特征是使用上述集電體。此外,本發(fā)明提供一種電極以及使用該電極作為正極及負(fù)極的混合式電容器,該混合式電容器例如為鋰離子電容器等的混合式電容器,其具有:形成電極層的正極電極,該電極層是由含有活性碳與碳納米管中任一種的活性物質(zhì)、導(dǎo)電輔助劑、及黏合劑所構(gòu)成;以及形成電極層的負(fù)極電極,該電極層是由可吸存或釋出堿金屬離子與堿土類金屬離子中任一種的碳材料,且含有Sn、Si或氧化硅、S或硫化物、及氧化鈦中任一種的活性物質(zhì)、導(dǎo)電輔助劑、及黏合劑所構(gòu)成,該混合式的電容器的特征是使用上述集電體。發(fā)明的效果本發(fā)明的電極材料中,通過將混合存在層形成于電極基材上所形成的第1及第2導(dǎo)電層間來提升層間的密著性,故可防止構(gòu)成第1導(dǎo)電層的物質(zhì)的氧化。此外,在第1或第2導(dǎo)電層與混合存在層的交界區(qū)域中,混合存在層實質(zhì)上僅由構(gòu)成該第1或第2導(dǎo)電層的成分所構(gòu)成,藉此,不會造成在交界區(qū)域中因電極材料的成分構(gòu)成急遽變化而產(chǎn)生界面電阻的上升。通過將這類電極材料用作為陰極箔,即在固態(tài)電解電容器中可達(dá)成靜電電容的增大及ESR與漏電流的降低。此外,如后述性能試驗數(shù)據(jù)所示,本發(fā)明的電極材料的耐熱性極佳,即使在高溫下長時間使用,質(zhì)量亦幾乎不會劣化。此外,即使將由第1導(dǎo)電層、混合存在層、及第2導(dǎo)電層所構(gòu)成的鋁基材上的覆膜薄化至約0.02μm,本發(fā)明的電極材料中作為陰極箔的特性幾乎不會降低,此外,制作陰極箔時亦不需使電極基材粗面化,故可減少所使用的材料并簡化制造步驟而大幅降低制造成本。若將覆膜形成較薄,則卷繞陰極箔時產(chǎn)生龜裂的危險性亦降低。再者,若將覆膜形成較薄,則可縮短電極基材與固態(tài)電解層間的電子傳導(dǎo)距離,而進(jìn)一步降低ESR。本發(fā)明的集電體中,通過將混合存在層形成于基材上所形成的第1及第2導(dǎo)電層間來提升層間的密著性及電傳導(dǎo)性、化學(xué)穩(wěn)定性,故可防止基材表面及構(gòu)成第1導(dǎo)電層的物質(zhì)的氧化等的化學(xué)變化所造成的變質(zhì)。此外,在第1或第2導(dǎo)電層與混合存在層的交界區(qū)域中,混合存在層實質(zhì)上僅由構(gòu)成該第1或第2導(dǎo)電層的成分所構(gòu)成,藉此,不會造成在交界區(qū)域中因電極材料的成分構(gòu)成急遽變化而產(chǎn)生界面電阻的上升。在這類集電體上形成有由活性物質(zhì)、導(dǎo)電輔助劑、及黏合劑所構(gòu)成的電極層的正極電極或負(fù)極電極,其電傳導(dǎo)性良好且從電極層往集電體的集電能力佳,并且化學(xué)穩(wěn)定性亦佳,故可長期地維持集電體與電極層的高密著性。使用此等電極的蓄電池、電雙層電容器、混合式電容器等的蓄電組件中,輸出密度提升且充放電時的電壓降較小,可抑制以大電流進(jìn)行充放電時的組件溫度的上升,故可長時間連續(xù)地進(jìn)行充放電,而大幅地延長充放電周期壽命。附圖說明圖1是表示本發(fā)明的一種實施方式的陰極箔的層構(gòu)造的剖面圖。圖2是表示本發(fā)明的一種實施方式的卷繞型固態(tài)電解電容器的構(gòu)造的分解圖。圖3是用以比較對于使用本發(fā)明的一種實施方式的陰極箔的固態(tài)電解電容器、與使用已知的陰極箔的固態(tài)電解電容器所分別測定的靜電電容的柱狀圖。圖4是用以比較對于使用本發(fā)明的一種實施方式的陰極箔的固態(tài)電解電容器、與使用已知的陰極箔的固態(tài)電解電容器所分別測定的ESR的柱狀圖。圖5是用以比較對于使用本發(fā)明的一種實施方式的陰極箔的固態(tài)電解電容器、與使用已知的陰極箔的固態(tài)電解電容器所分別測定的漏電流的柱狀圖。圖6是用以比較對于使用本發(fā)明的一種實施方式的陰極箔的固態(tài)電解電容器、與使用已知的陰極箔的固態(tài)電解電容器,分別進(jìn)行耐熱性試驗所測定的試驗前后的靜電電容變化率的柱狀圖。圖7是用以比較對于使用本發(fā)明的一種實施方式的陰極箔的固態(tài)電解電容器、與使用已知的陰極箔的固態(tài)電解電容器,分別進(jìn)行耐熱性試驗所測定的試驗前后的ESR變化率的柱狀圖。圖8是表示本發(fā)明的一種實施方式的集電體的層構(gòu)造的剖面圖。圖9是表示本發(fā)明的一種實施方式的正極電極或負(fù)極電極的層構(gòu)造的剖面圖。圖10a是表示本發(fā)明的一種實施方式的鋰離子蓄電池的構(gòu)造的分解圖。圖10b是表示本發(fā)明的一種實施方式的鋰離子蓄電池的外觀構(gòu)造的圖。圖11是比較對于使用本發(fā)明的一種實施方式的集電體的鋰離子蓄電池、與使用作為比較例的集電體的鋰離子蓄電池所分別測定的放電速率特性的結(jié)果。圖12是比較對于使用本發(fā)明的一種實施方式的集電體的鋰離子蓄電池、與使用作為比較例的集電體的鋰離子蓄電池所分別測定的充放電周期壽命特性的結(jié)果。圖13是比較對于使用本發(fā)明的一種實施方式的集電體的鋰離子蓄電池用正極電極、與使用作為比較例的集電體的鋰離子蓄電池用正極電極所分別測定的集電體與電極層的密著強(qiáng)度的SAICAS試驗的結(jié)果。【主要組件符號說明】1、8陰極箔2平滑鋁箔3金屬層4混合存在層5碳層6卷繞型固態(tài)電解電容器7陽極箔9分隔器紙10電容器組件11陽極端子12陰極端子13鋁盒14密封橡膠15金屬箔16金屬層17混合存在層18碳層19集電體(19a正極側(cè)集電體、19b負(fù)極側(cè)集電體)20正極電極層21正極電極22負(fù)極電極層23負(fù)極電極24分隔器25電解質(zhì)26正極端子27負(fù)極端子28鋰離子蓄電池組件29電池盒30鋰離子蓄電池具體實施方式(第1實施方式)以下說明:在未經(jīng)粗面化的鋁箔上形成有由Ti或Al所構(gòu)成的第1導(dǎo)電層、混合存在有Ti或Al與碳而成的混合存在層、及由碳所構(gòu)成的第2導(dǎo)電層的陰極箔,以及使用該陰極箔所制作的固態(tài)電解電容器,作為本發(fā)明的一種實施方式。但如已說明般,用作為基材的鋁箔、及用以形成第1導(dǎo)電層的Ti或Al可通過其它材料來取代,或如使用性能試驗數(shù)據(jù)所說明般,即使不使基材表面粗面化,本發(fā)明的陰極箔亦具有良好特性。(本發(fā)明的陰極箔)圖1是表示上述一種實施方式的陰極箔1的層構(gòu)造的剖面圖。陰極箔1是由:未通過蝕刻處理等進(jìn)行粗面化的平滑鋁箔2、形成于平滑鋁箔2上且由Ti或Al所構(gòu)成的金屬層3、形成于金屬層3上且混合存在有Ti或Al與碳而成的混合存在層4、以及形成于混合存在層4上的碳層5所構(gòu)成。平滑鋁箔2可使用市售的高純度鋁薄片。鋁薄片的厚度并無特別限定,當(dāng)用作為卷繞型的固態(tài)電解電容器用陰極箔時,較佳為20μm以上50μm以下。通過將平滑鋁箔2及作為蒸發(fā)源的Ti或Al的金屬材料配置在真空反應(yīng)室內(nèi)后,通過電子束及等離子體產(chǎn)生電極等使Ti或Al蒸發(fā)及離子化,并將由此產(chǎn)生的金屬陽離子導(dǎo)引至平滑鋁箔2而形成金屬層3。此時,由于對平滑鋁箔2施加負(fù)偏壓電壓,故朝向該平滑鋁箔2的金屬離子被加速而具有高能量(離子蒸鍍法)。因此,Ti或Al離子貫穿平滑鋁箔2表面上所形成的自然氧化覆膜,而與平滑鋁箔2穩(wěn)固地密著。在將由Ti或Al等金屬的氮化物、或碳化物所構(gòu)成的層形成于平滑鋁箔2上的型態(tài)中,只要在氮氣或甲烷氣體等環(huán)境氣體中進(jìn)行上述方法來形成第1導(dǎo)電層即可。此外,用以形成金屬層3的方法,除了離子蒸鍍法外,亦可使用真空蒸鍍法、化學(xué)氣相沉積(CVD)法、濺鍍法等。但就通過使金屬層3與平滑鋁箔2貫穿自然氧化覆膜并穩(wěn)固地密著以將電容器的ESR抑制較低的觀點,以及容易形成平滑的金屬覆膜的觀點來看,優(yōu)選使用離子蒸鍍法?;旌洗嬖趯?與金屬層3相同,可通過離子蒸鍍法等來形成。即,蒸發(fā)源除了Ti或Al的金屬材料外,準(zhǔn)備碳材料,并同時使用該2種蒸發(fā)源來進(jìn)行成膜處理即可。通過導(dǎo)入這類混合存在層4,可提高金屬與碳的密著性,以防止氧化覆膜的形成?;旌洗嬖趯?的優(yōu)選構(gòu)成為:在與金屬層3的交界區(qū)域中實質(zhì)上僅含有Ti或Al,且在與碳層5的交界區(qū)域中實質(zhì)上僅含有碳,尤其自金屬層3朝向碳層5使碳含有率連續(xù)地上升。這類混合存在層4的一例,可通過下列方式形成:(i)混合存在層4的成膜開始時將電子束僅照射在金屬材料以僅形成Ti或Al的覆膜;(ii)隨著時間的經(jīng)過逐漸降低電子束對該金屬材料的照射量,同時提高電子束對碳材料的照射量,藉此使金屬與碳混合存在,且以愈往上層碳含有率愈高的方式形成混合存在覆膜;(iii)成膜結(jié)束時,通過將電子束對該金屬材料的照射量設(shè)為零,而可僅形成碳的覆膜。其它,當(dāng)通過濺鍍法來形成混合存在層4時,可隨著時間的經(jīng)過而降低施加于金屬靶材的電壓(降低金屬靶材的濺鍍速度),提高施加于C靶材的電壓(提高C靶材的濺鍍速度)等,通過任意方法來形成較佳型態(tài)的混合存在層4。后述性能試驗數(shù)據(jù)中,實施例7至12的數(shù)據(jù)系使用上述離子蒸鍍法,并使用以尤其自金屬層3朝向碳層5使碳含有率連續(xù)地上升的方式形成混合存在層4而成的陰極箔1而得者。然而,混合存在層4中,即使存在有一部分例如隨著朝向碳層5使碳含有率減少的區(qū)域(起因于成膜技術(shù)的限制等,此情形有可能產(chǎn)生),亦可推測同樣地可得到與先前技術(shù)的陰極箔相比更佳的特性。這是由于即使在這類區(qū)域中,亦混合存在有Ti或Al與碳而提升成分間的密著性,所以可防止Ti或Al的氧化,并抑制陰極中的內(nèi)部電容量的產(chǎn)生之故。此外,當(dāng)混合存在層4的一部分區(qū)域中碳含有率不連續(xù)地變化時,雖可視為因在該處中的界面電阻的上升使ESR特性些許降低,但由于混合存在有Ti或Al與碳而提升成分間的密著性,故可推測陰極箔能夠得到同樣的特性(關(guān)于此點,后述性能試驗數(shù)據(jù)中,請參照實施例1至6的數(shù)據(jù))。碳層5與金屬層3及混合存在層4相同,可通過離子蒸鍍法等來形成。典型而言,上述混合存在層4的形成過程中,在將電子束對金屬材料的照射量降低至零后,在將電子束僅照射在碳材料的狀態(tài)下持續(xù)進(jìn)行一定時間的覆膜形成處理,藉此可形成碳層5。本發(fā)明的碳層5并非如專利文獻(xiàn)6所記載的陰極箔般,在使碳微粒分散于黏合劑后涂布此黏合劑并加熱而形成,而是優(yōu)選使用離子蒸鍍法等來形成。這是由于在使用黏合劑來形成的碳微粒層中,下層的Ti或Al與碳的接觸為點接觸,而造成界面電阻的上升,且密著性亦惡化的故。碳層5較佳系形成為平滑且緊密的碳覆膜。金屬層3、混合存在層4、及碳層5的厚度,分別可為0.005μm以上0.01μm以下,此外,如后述性能試驗數(shù)據(jù)所示,若此等3層的厚度合計為0.02μm以上,則可得到作為陰極箔的良好特性。但亦可將各層形成更厚。此外,形成金屬層3、混合存在層4、及碳層5各層的步驟,優(yōu)選為以同一成膜方式來進(jìn)行。這是由于可通過制造步驟的簡化來大幅地降低制造成本的故。但各層亦可通過不同方式來成膜。(本發(fā)明的固態(tài)電解電容器)圖2是表示使用上述陰極箔1所制作的卷繞型固態(tài)電解電容器6的分解圖。卷繞型固態(tài)電解電容器6可通過下列方法制作出:(i)經(jīng)由分隔器紙9,將通過化成處理使氧化覆膜形成于陽極鋁箔上的陽極箔7、與具有圖1所示的層構(gòu)造的陰極箔8重迭,并將陽極端子11連接于陽極箔7,將陰極端子12連接于陰極箔8后,卷繞此而制作出電容器組件10。(ii)將電容器組件10收容于鋁盒13后,浸漬于含有正丁醇作為稀釋劑的3,4-乙撐二氧噻吩、與作為氧化劑的對甲苯磺酸鐵(II)的混合溶液中進(jìn)行加熱,并通過熱聚合來形成聚乙撐二氧噻吩的固態(tài)電解質(zhì)層。亦可通過聚吡咯系或聚苯胺系導(dǎo)電性高分子,或是TCNQ絡(luò)合物等,來形成固態(tài)電解質(zhì)層。(本發(fā)明的固態(tài)電解電容器的性能試驗)首先準(zhǔn)備:如上述般未進(jìn)行鋁箔的粗面化所制作的陰極箔、或用于比較而進(jìn)行鋁箔的粗面化所制作的陰極箔,以及使用Ti作為金屬層所制作的陰極箔、或使用Al作為金屬層所制作的陰極箔,來作為本發(fā)明的陰極箔,然后準(zhǔn)備:將由金屬層、混合存在層、及碳層所構(gòu)成的覆膜的厚度設(shè)為0.5μm與0.02μm者。系采用此等本發(fā)明的陰極箔的各種形式來制作出圖2所示的構(gòu)成的卷繞型固態(tài)電解電容器,并測定靜電電容、ESR、及漏電流。此外,亦對使用基材及覆膜的構(gòu)成分別不同的已知技術(shù)的陰極箔所制作的除了陰極箔的外其它與本發(fā)明的電容器為同一構(gòu)成的卷繞型固態(tài)電解電容器進(jìn)行同樣的測定,并比較雙方的試驗結(jié)果。在進(jìn)行比較用的測定后的固態(tài)電解電容器的已知例1至16、以及本發(fā)明的固態(tài)電解電容器的實施例1至12中所使用的陰極箔的構(gòu)成,分別如下所述。(已知例1)對平滑鋁箔施以蝕刻處理而成的陰極箔。(已知例2)于平滑鋁箔形成Ti覆膜0.5μm而成的陰極箔。(已知例3)于平滑鋁箔形成Ti覆膜0.02μm而成的陰極箔。(已知例4)于平滑鋁箔形成TiN覆膜0.5μm而成的陰極箔。(已知例5)于平滑鋁箔形成TiN覆膜0.02μm而成的陰極箔。(已知例6)于平滑鋁箔形成TiC覆膜0.5μm而成的陰極箔。(已知例7)于平滑鋁箔形成TiC覆膜0.02μm而成的陰極箔。(已知例8)于平滑鋁箔形成碳覆膜0.5μm而成的陰極箔。(已知例9)于平滑鋁箔形成碳覆膜0.02μm而成的陰極箔。(已知例10)于平滑鋁箔形成碳化鋁后,使碳微粒固著而成的陰極箔(膜厚因陰極箔表面內(nèi)的位置不同而不同,為0.5μm至1μm)。(已知例11)對平滑鋁箔施以蝕刻處理,形成Ti覆膜0.25μm且還形成碳覆膜0.25μm而成的陰極箔。(已知例12)對平滑鋁箔施以蝕刻處理,形成Ti覆膜0.01μm且還形成碳覆膜0.01μm而成的陰極箔。(已知例13)于平滑鋁箔形成Ti覆膜0.25μm且還形成碳覆膜0.25μm而成的陰極箔。(已知例14)于平滑鋁箔形成Ti覆膜0.01μm且還形成碳覆膜0.01μm而成的陰極箔。(已知例15)于平滑鋁箔形成Al覆膜0.25μm且還形成碳覆膜0.25μm而成的陰極箔。(已知例16)于平滑鋁箔形成Al覆膜0.01μm且還形成碳覆膜0.01μm而成的陰極箔。(實施例1)對平滑鋁箔施以蝕刻處理,形成Ti覆膜0.2μm、Ti及碳的混合存在層a0.1μm、及碳覆膜0.2μm而成的陰極箔。(實施例2)對平滑鋁箔施以蝕刻處理,形成Ti覆膜0.008μm、Ti及碳的混合存在層a0.004μm、及碳覆膜0.008μm而成的陰極箔。(實施例3)于平滑鋁箔形成Ti覆膜0.2μm、Ti及碳的混合存在層a0.1μm、及碳覆膜0.2μm而成的陰極箔。(實施例4)于平滑鋁箔形成Ti覆膜0.008μm、Ti及碳的混合存在層a0.004μm、及碳覆膜0.008μm而成的陰極箔。(實施例5)于平滑鋁箔形成Al覆膜0.2μm、Al及碳的混合存在層a0.1μm、及碳覆膜0.2μm而成的陰極箔。(實施例6)于平滑鋁箔形成Al覆膜0.008μm、Al及碳的混合存在層a0.004μm、及碳覆膜0.008μm而成的陰極箔。(實施例7)對平滑鋁箔施以蝕刻處理,形成Ti覆膜0.2μm、Ti及碳的混合存在層b0.1μm、及碳覆膜0.2μm而成的陰極箔。(實施例8)對平滑鋁箔施以蝕刻處理,形成Ti覆膜0.008μm、Ti及碳的混合存在層b0.004μm、及碳覆膜0.008μm而成的陰極箔。(實施例9)于平滑鋁箔形成Ti覆膜0.2μm、Ti及碳的混合存在層b0.1μm、及碳覆膜0.2μm而成的陰極箔。(實施例10)于平滑鋁箔形成Ti覆膜0.008μm、Ti及碳的混合存在層b0.004μm、及碳覆膜0.008μm而成的陰極箔。(實施例11)于平滑鋁箔形成Al覆膜0.2μm、Al及碳的混合存在層b0.1μm、及碳覆膜0.2μm而成的陰極箔。(實施例12)于平滑鋁箔形成Al覆膜0.008μm、Al及碳的混合存在層b0.004μm、及碳覆膜0.008μm而成的陰極箔。于基材上的覆膜形成,除了已知例10的陰極箔外,均通過上述離子蒸鍍法來進(jìn)行。尤其是已知例4至7中的氮化鈦及碳化鈦的覆膜形成,分別是在氮氣及甲烷氣的環(huán)境氣體中,以鈦為蒸發(fā)源進(jìn)行的,已知例8、9中的碳覆膜的形成,是以碳為蒸發(fā)源進(jìn)行的。實施例1至12的覆膜形成亦如已說明般,是通過離子蒸鍍法來進(jìn)行的。在此,實施例1至6中的混合存在層a形成為Ti或Al與碳的比率為一致,另一方面,實施例7至12中的混合存在層b,形成為愈往上層碳的存在比率愈高。已知例10中,使用制造販賣的樣本。性能試驗的結(jié)果如下列第1表所示。[表1]表1中,cap.表示電容器的靜電電容(單位:μF),ESR表示等效串聯(lián)電阻(單位:mΩ),LC表示漏電流(單位:μA)。在120Hz的頻率中測定靜電電容。等效串聯(lián)電阻在100kHz的頻率中測定。漏電流是對固態(tài)電解電容器施加定額4V的直流電壓,并測定經(jīng)過3分鐘后的值。此外,表1所示的靜電電容、ESR、漏電流的各項測定結(jié)果,于圖3至圖5中顯示為柱狀圖。如表1及圖3的柱狀圖所示,實施例1至12中的靜電電容的測定值較已知例1至16中的測定值更大。與將未形成金屬等覆膜的蝕刻箔用作為陰極箔的已知例1中的測定值(175.4μF)相比,可得知實施例1至12中的靜電電容增加約60%。此外,已知例11、12與實施例1、2及實施例7、8的電容器,僅在陰極箔上是否于Ti層與碳層之間形成有混合存在層者為不同(實施例1、2及實施例7、8的電容器,僅在陰極箔的混合存在層中各成分的含有率是否具有梯度者為不同),但可得知實施例1、2中的測定值(279.1μF、及277.3μF)及實施例7、8中的測定值(282.1μF、及280.1μF),較已知例11及12中的測定值(264.1μF、及258.1μF)更大。同樣可得知新設(shè)置有混合存在層的實施例3至6、及實施例9至12中的測定值較已知例13至16中的測定值更大。尤其可得知,在通過上述方法使混合存在層的成分含有率具有梯度的實施例7至12中的測定值,較混合存在層的成分含有率不具有梯度的實施例1至6中的測定值更大。此外,如表1及圖4的柱狀圖所示,實施例1至12中的ESR的測定值較已知例1至16中的測定值更小。與將未形成金屬等覆膜的蝕刻箔用作為陰極箔的已知例1中的測定值(12.32mΩ)相比,可得知實施例1至12中的ESR降低約60至65%。此外,已知例11、12與實施例1、2及實施例7、8的電容器,如已說明般,僅在陰極箔中是否于Ti層與碳層之間形成有混合存在層者為不同,但可得知實施例1、2中的測定值(4.76mΩ、4.82mΩ)及實施例7、8中的測定值(4.61mΩ、4.73mΩ),較已知例11及12中的測定值(6.43mΩ、7.10mΩ)更小。同樣地可得知新設(shè)置有混合存在層的實施例3至6、及實施例9至12中的測定值較已知例13至16中的測定值更小。尤其可得知,在通過上述方法使混合存在層的成分含有率具有梯度的實施例7至12中的測定值,較混合存在層的成分含有率不具有梯度的實施例1至6中的測定值更小。再者,已知例11及12、13及14、15及16的各個陰極箔的覆膜構(gòu)成為相同,僅厚度為不同的0.5μm及0.02μm的電容器的例子,但如表1及圖4的柱狀圖所示,可得知不論何者均因覆膜的薄化而使ESR上升(上升幅度為0.3mΩ至0.7mΩ)。相對于此,比較本發(fā)明中僅覆膜厚度不同的實施例1及2、3及4、5及6中的ESR測定值時,實施例1中的測定值(4.76mΩ)與實施例2中的測定值(4.82mΩ)雖幾乎不變(這類測定結(jié)果推測為在實施例1及2中與鋁箔經(jīng)粗面化具有關(guān)系),實施例4中的測定值(4.39mΩ)較實施例3中的測定值(4.56mΩ)更小,此外,實施例6中的測定值(4.37mΩ)較實施例5中的測定值(4.51mΩ)更小。該傾向在混合存在層的成分含有率具有梯度的實施例7至12中亦可觀測到。因此,至少在未使鋁箔粗面化而使用的具體實例中,就即使將覆膜形成較薄亦可維持良好的ESR特性的方面來看,可理解到本發(fā)明的陰極箔較已知者更佳。此外,如表1及圖5的柱狀圖所示,實施例1至12中的漏電流的測定值較已知例1至16中的漏電流的測定值更小。此外,可得知形成有混合存在層b的實施例7至12中的測定值,較形成有混合存在層a的實施例1至6中的測定值更小。當(dāng)比較已知例11至16中的測定值與實施例1至6中的測定值時,可得知通過設(shè)置混合存在層而能夠?qū)⒙╇娏鹘档图s20%。此外,當(dāng)比較設(shè)置有混合存在層a的實施例1至6中的測定值與設(shè)置有混合存在層b的實施例7至12中的測定值時,可得知降低約數(shù)%。本發(fā)明的固態(tài)電解電容器的耐熱性試驗接著對上述已知例的電容器與實施例的電容器進(jìn)行耐熱性試驗。耐熱性試驗是在125℃的溫度下,分別對已知例1至16與實施例1至12的各電容器施加定額電壓4V達(dá)1000小時來進(jìn)行,并比較試驗前后的靜電電容及ESR的測定值。下表2顯示在各電容器中,試驗后所測定的靜電電容與ESR以及試驗前后的此等測定值的變化率。[表2]表2中,ΔC/C為靜電電容測定值于試驗前后的變化率,以百分率來表示[(試驗后的測定值)-(試驗前的測定值)]/(試驗前的測定值)。同樣地,ΔESR/ESR為以百分率來表示ESR測定值于試驗前后的變化率。各變化率計算時,試驗前的測定值使用表1所示的值。此外,表2所示的靜電電容及ESR的各變化率,于圖6至圖7中顯示為柱狀圖。首先探討耐熱性試驗后的靜電電容,如第2表所示,實施例1至12中的靜電電容的測定值較已知例1至16中的測定值更大。尤其是實施例7至12的靜電電容的測定值較實施例1至6中的靜電電容的測定值更大。可得知本發(fā)明的電容器,即使在耐熱性試驗后亦具有較已知的電容器更大的靜電電容。再者,探討靜電電容測定值于試驗前后的變化率,從表2及圖6中可得知,該變化率在已知例1至16與實施例1至12之間有著極大的不同。亦即,已知例11及12的電容器中,通過耐熱性試驗,使靜電電容測定值分別減少3.8%及4.5%,但在此等中設(shè)置有混合存在層而成的實施例1及2的電容器中,因耐熱性試驗所導(dǎo)致的靜電電容測定值的減少率為1.6%及2.0%,此外,實施例7及8的減少率僅為0.9%及1.3%。同樣地,可得知新設(shè)置有混合存在層的實施例3至6及實施例9至12中的減少率較已知例13至16中的靜電電容測定值的減少率更小,尤其是實施例9至12中的減少率較實施例3至6中的減少率更小,可得知本發(fā)明的陰極箔在靜電電容特性上,其耐熱性較已知者更佳。實施例7及8中的靜電電容的減少率為0.9%及1.3%,相對于此,使用平滑鋁箔來制作陰極箔的實施例9及10中的靜電電容的減少率為0.7%及0.3%。亦即,就耐熱性的觀點來看,優(yōu)選不對鋁箔施以蝕刻處理。此外,圖6中,從實施例3至6及9至10的柱狀圖中可得知,在此等實施例中,與將覆膜厚度設(shè)為0.5μm時相比,設(shè)為0.02μm時較能將靜電電容測定值的減少率抑制為較低。亦即,未對鋁箔施以蝕刻處理來制作本發(fā)明的陰極箔時,就耐熱性的觀點來看,優(yōu)選將覆膜形成較薄。然后,探討耐熱性試驗后的ESR,如表2所示,實施例1至12中的ESR的測定值較已知例1至16中的測定值更小。尤其是實施例7至12的ESR的測定值較實施例1至6中的ESR的測定值更小。可得知本發(fā)明的電容器,即使在耐熱性試驗后亦具有較已知的電容器更小的ESR。再者,探討ESR測定值于試驗前后的變化率,從表2及圖7得知,該變化率在已知例1至16與實施例1至12的間有著極大的不同。亦即,已知例11及12的電容器中,因耐熱性試驗所導(dǎo)致的ESR測定值的增加率分別為18.8%及25.4%,但在此等中設(shè)置有混合存在層a而成的實施例1及2的電容器中,因耐熱性試驗所導(dǎo)致的ESR測定值的增加率為2.5%及2.3%,此外,在設(shè)置有混合存在層b而成的實施例7及8的電容器中,因耐熱性試驗所導(dǎo)致的ESR測定值的增加率僅為2.2%及2.1%。同樣地,可得知新設(shè)置有混合存在層的實施例3至6及實施例9至12中的增加率較已知例13至16中的ESR測定值的增加率更小,尤其是實施例7至12中的ESR測定值的增加率較實施例1至6中的ESR測定值的增加率更小,可得知本發(fā)明的陰極箔在ESR特性上,其耐熱性較已知者更佳。實施例7及8中的ESR的增加率為2.2%及2.1%,相對于此,使用平滑鋁箔來制作陰極箔的實施例9及10中的ESR的增加率為0.5%及0.2%。亦即,就耐熱性的觀點來看,優(yōu)選不對鋁箔施以蝕刻處理。(第2實施方式)以下說明:在經(jīng)粗面化的鋁箔上形成有由Ti或Al所構(gòu)成的第1導(dǎo)電層、混合存在有Ti或Al與類石墨碳(以下有時記載為GLC的情形)而成的混合存在層、及由GLC所構(gòu)成的第2導(dǎo)電層的集電體,以及使用該集電體所制作的鋰離子蓄電池,作為本發(fā)明的另一項實施形態(tài)。但如已說明般,用作為集電體的基材的鋁箔、及用以形成第1導(dǎo)電層的Ti或Al可通過其它材料來取代,或如后述使用性能試驗數(shù)據(jù)所說明般,即使不使基材表面粗面化,本發(fā)明的集電體亦具有良好特性。此外,如已說明般,本發(fā)明的集電體的用途亦不限于鋰離子蓄電池,亦可將該集電體使用在其它蓄電池、電雙層電容器、混合式電容器等的任意的蓄電組件的電極用途。(本發(fā)明的集電體)圖8是表示上述一項實施形態(tài)的集電體19的層構(gòu)造的剖面圖。集電體19包括:通過在酸性溶液中進(jìn)行電化學(xué)蝕刻處理而施以粗面化后的屬于鋁箔的金屬箔15;形成于該金屬箔15上且由Ti或Al的金屬覆膜所構(gòu)成的金屬層16;形成于金屬層16上且混合存在有該Ti或Al與GLC而成的混合存在層17;以及形成于該混合存在層17上且由GLC所構(gòu)成的碳層18。鋁箔可使用市售的高純度鋁箔。鋁箔的厚度并無特別限定,就加工性或電傳導(dǎo)性、重量、體積、成本等來看,較佳為5μm以上50μm以下。通過將金屬箔15及作為蒸發(fā)源的Ti或Al的金屬材料配置在真空反應(yīng)室內(nèi)后,通過電子束及等離子體產(chǎn)生電極等使Ti或Al蒸發(fā)及離子化,并將由此產(chǎn)生的金屬陽離子導(dǎo)引至該金屬箔15而形成金屬層16。就成膜方法的一例而言,可列舉離子蒸鍍法等的物理氣相沉積法(PVD)。在將由Ti或Al等金屬的氮化物、或碳化物所構(gòu)成的層形成于金屬箔15上的態(tài)樣中,只要在氮氣或甲烷氣體等環(huán)境氣體中進(jìn)行上述方法來形成第1導(dǎo)電層即可。此外,用以形成金屬層16的方法、即離子蒸鍍法以外的物理氣相沉積法,可列舉真空蒸鍍法或濺鍍法等。亦可使用熱CVD或光CVD、等離子體CVD、有機(jī)金屬氣相沉積法等化學(xué)氣相沉積(CVD)法?;旌洗嬖趯?7與金屬層16相同,可通過離子蒸鍍法等來形成。亦即,蒸發(fā)源除了Ti或Al的金屬材料外,更準(zhǔn)備石墨材料,并同時使用該2種蒸發(fā)源來進(jìn)行成膜處理即可。通過導(dǎo)入這類混合存在層17,即可提高金屬與GLC的密著性及化學(xué)穩(wěn)定性,防止因金屬的化學(xué)反應(yīng)所造成的變質(zhì)?;旌洗嬖趯?7較佳構(gòu)成為:在與金屬層16的交界區(qū)域中實質(zhì)上僅含有Ti或Al,且在與碳層18的交界區(qū)域中實質(zhì)上僅含有碳(GLC),尤其自金屬層16朝向碳層18使GLC含有率連續(xù)地上升。就這類混合存在層17的一例而言,可通過下列方式形成:(i)混合存在層17的成膜開始時將電子束僅照射在金屬材料以僅形成Ti或Al的覆膜;(ii)隨著時間的經(jīng)過逐漸降低電子束對該金屬材料的照射量,同時提高電子束對石墨材料的照射量,藉此使金屬與GLC混合存在,且以愈往上層GLC含有率愈高的方式形成混合存在覆膜;(iii)成膜結(jié)束時,將電子束對該金屬材料的照射量設(shè)為零,而可僅形成GLC的覆膜。除此之外,當(dāng)通過濺鍍法來形成混合存在層17時,可隨著時間的經(jīng)過而降低施加于金屬靶材的電壓(降低金屬靶材的濺鍍速度),以提高施加于石墨靶材的電壓(提高石墨靶材的濺鍍速度)等,通過任意方法來形成較佳態(tài)樣的混合存在層17。后述性能試驗數(shù)據(jù)中,實施例1至4的數(shù)據(jù)是使用上述離子蒸鍍法,并使用以尤其自金屬層16朝向碳層18使GLC含有率連續(xù)地上升的方式形成混合存在層17而成的集電體19而得者。然而,在混合存在層17中,即使存在有一部分例如GLC含有率隨著朝向碳層18而減少的區(qū)域(起因于成膜技術(shù)的限制等,此情形有可能產(chǎn)生),亦可推測同樣可得到與已知技術(shù)的集電體相比更佳的特性。這是由于即使在這類區(qū)域中,Ti或Al與GLC亦混合存在而提升成分間的密著性,所以可防止Ti或Al的氧化等的化學(xué)反應(yīng)所造成的變質(zhì),而長期間將集電體與電極層的接觸電阻抑制為較低。碳層18與金屬層16及混合存在層17相同,可通過離子蒸鍍法等來形成。典型而言,在上述混合存在層17的形成過程中,在將電子束對金屬材料的照射量降低至零后,在將電子束僅照射在碳材料的狀態(tài)下持續(xù)進(jìn)行一定時間的覆膜形成處理,藉此可形成碳層18。本發(fā)明的碳層18并非在使碳微粒分散于樹脂黏合劑等的黏結(jié)劑后涂布此黏結(jié)劑而形成,而是與上述的金屬層16及混合存在層17相同,較佳例如使用離子蒸鍍法等的蒸鍍法來形成。這是由于在與黏結(jié)劑捏揉而形成的碳微粒層中,碳的占有率會降低達(dá)實質(zhì)混合的黏結(jié)劑的份量,此外,下層的Ti或Al與碳粒子的接觸為點接觸,再者,上述涂布法中,難以提高界面的電傳導(dǎo)性,造成界面電阻的上升,密著性亦惡化,并且難以均勻地被覆較薄之故。碳層18較佳形成為平滑且緊密的GLC覆膜。金屬層16、混合存在層17、及碳層18的厚度,分別可為0.1nm以上15nm以下左右,若至少此等3層的厚度合計為0.3nm以上,則可得到作為集電體的良好特性。但在不損及電傳導(dǎo)性或經(jīng)濟(jì)性的范圍內(nèi),亦可將各層形成較厚,但在使金屬箔粗面化時,考慮到對細(xì)孔構(gòu)造內(nèi)壁的均勻被覆性,較佳將該3層的厚度合計設(shè)為45nm以下。此外,形成金屬層16、混合存在層17、及碳層18各層的步驟,較佳是以同一成膜方式來進(jìn)行。這是由于可通過制造步驟的簡化來提高生產(chǎn)性且大幅降低制造成本的故。但在不損及經(jīng)濟(jì)性的范圍內(nèi),此等各層亦可通過不同方式來成膜。(本發(fā)明的蓄電池)圖9是表示使用上述集電體19(將正極所使用的集電體設(shè)為正極側(cè)集電體19a,將負(fù)極所使用的集電體設(shè)為負(fù)極側(cè)集電體19b)所制作的正極電極21、負(fù)極電極23的剖面圖,圖10a、圖10b是表示使用該電極21、23所制作的一例的鋰離子蓄電池30的分解圖及外觀圖。鋰離子蓄電池30可通過下列方法制作出:(i)夾介分隔器,重迭:在集電體19a上形成有將作為活性物質(zhì)的磷酸鐵鋰(LiFePO4)、作為導(dǎo)電輔助劑的乙炔黑、作為黏合劑的丁苯橡膠、作為增黏劑的羧甲基纖維素銨鹽、及與水捏揉而成的電極層20的正極電極21,以及在集電體19b上形成有將作為活性物質(zhì)的石墨、作為導(dǎo)電輔助劑的乙炔黑、作為黏合劑的丁苯橡膠、作為增黏劑的羧甲基纖維素銨鹽、及與水捏揉而成的電極層22的負(fù)極電極23,然后將正極耳片端子26連接于正極側(cè)集電體19a,將負(fù)極耳片端子27連接于負(fù)極側(cè)集電體19b后,重迭此復(fù)數(shù)片而制作出鋰離子蓄電池組件28。(ii)將鋰離子蓄電池組件28收容于盒29后,注入將作為電解質(zhì)25的六氟化磷酸鋰(LiPF6)溶解于有機(jī)溶劑的碳酸乙烯酯及碳酸二乙酯的混合溶液而成的電解液后,將盒密封。電池的制作中所使用的活性物質(zhì)、導(dǎo)電輔助劑、黏合劑、電解質(zhì)的材質(zhì)或組合、以及組件構(gòu)造(鈕扣型、卷繞型、積層型等)并不限定于此等。(本發(fā)明的集電體的性能試驗)本發(fā)明的集電體的性能試驗,分別對下列集電體進(jìn)行,即,以如上述般通過在酸性溶液中進(jìn)行電化學(xué)蝕刻處理而施以粗面化后的鋁箔為基材所制作的集電體,以及以未經(jīng)粗面化的鋁箔為基材所制作的集電體。各個集電體中,金屬層系使用Ti或Al,將由金屬層、混合存在層、及碳層所構(gòu)成的覆膜的厚度設(shè)為合計25nm。以提高評估精確性者為目的,性能評估用的鋰離子蓄電池組件,以將上述電極層形成于該集電體上而成的電極作為正極電極,對極則使用鋰板來制作出性能試驗用的鈕扣型電池,使用該鈕扣型電池,來測定并評估該正極電極的放電速率特性、及充放電周期壽命特性。通過下列方式評估正極電極的放電速率特性,首先各進(jìn)行一次下列充放電:(i)以既定的充電速率電流值對上述鈕扣型電池進(jìn)行定電流充電至4.2V為止,然后進(jìn)行定電壓充電至電流值成為0.01C為止來實施充電,(ii)然后以既定的放電速率電流值進(jìn)行定電流放電至3.0V為止來實施放電,以放電速率電流值0.2C時的放電電容量為基準(zhǔn),從各放電速率電流值中所測定的鈕扣型電池的放電電容量的比率中,計算出電容量維持率(各放電速率電流值時的放電電容量[mAh/g]÷放電速率電流值0.2C時的放電電容量[mAh/g]×100)而進(jìn)行評估。將環(huán)境溫度設(shè)定在25℃,一邊將上述放電速率電流值從0.2C改變至10C,一邊評估放電速率特性,并比較各放電速率電流值時的電容量維持率。當(dāng)放電速率電流值未達(dá)1C時,上述既定的充電速率電流值設(shè)為與該放電速率電流值相同的值,當(dāng)放電速率電流值為1C以上時,固定在1C。在此,所謂放電速率電流值1C,表示花費1小時使電池的全電容量放電的電流值,所謂放電速率電流值10C,意味著于6分鐘內(nèi)使全電池電容量放電的急速放電。正極電極的充放電周期壽命特性,是將環(huán)境溫度設(shè)定在25℃,且將充電速率電流值及放電速率電流值均固定在1C后,反復(fù)進(jìn)行上述充放電20周期,并且于每次完成1周期時,以初期(第1周期)的放電電容量為基準(zhǔn)來計算出電容量維持率而而進(jìn)行評估。為了驗證金屬箔的粗面化對于集電體與電極層的密著強(qiáng)度所帶來的效果,使用SAICAS(SurfaceAndInterfacialCuttingAnalysisSystem)裝置作為斜向切削裝置來進(jìn)行試驗。將寬度1mm的具有金剛石刀尖的刀刃,從電極表面以一定速度(水平:6μm/s、垂直:0.6μm/s)斜向地切入,到達(dá)集電體與電極層的接合界面后,以一定速度(水平:6μm/s)水平地移動,將此時施加于刀刃的水平應(yīng)力作為剝離強(qiáng)度來進(jìn)行比較。在進(jìn)行比較用的測定后的蓄電池的比較例1至7、以及本發(fā)明的蓄電池的實施例1至4中所使用的集電體的構(gòu)成,分別如下所述。(比較例1)由平滑鋁箔所構(gòu)成的集電體。(比較例2)對平滑鋁箔施以蝕刻處理而成的集電體。(比較例3)于平滑鋁箔形成類石墨碳覆膜20nm而成的集電體。(比較例4)于平滑鋁箔形成Ti覆膜12.5nm、類石墨碳覆膜12.5nm而成的集電體。(比較例5)對平滑鋁箔施以蝕刻處理,并形成Ti覆膜12.5nm、類石墨碳覆膜12.5nm而成的集電體。(比較例6)于平滑鋁箔形成Al覆膜12.5nm、類石墨碳覆膜12.5nm而成的集電體。(比較例7)對平滑鋁箔施以蝕刻處理,并形成Al覆膜12.5nm、類石墨碳覆膜12.5nm而成的集電體。(實施例1)于平滑鋁箔形成Ti覆膜10nm、Ti及類石墨碳覆膜的混合存在層5nm、及類石墨碳覆膜10nm而成的集電體。(實施例2)對平滑鋁箔施以蝕刻處理,并形成Ti覆膜10nm、Ti及類石墨碳覆膜的混合存在層5nm、及類石墨碳覆膜10nm而成的集電體。(實施例3)于平滑鋁箔形成Al覆膜10nm、Al及類石墨碳覆膜的混合存在層5nm、及類石墨碳覆膜10nm而成的集電體。(實施例4)對平滑鋁箔施以蝕刻處理,并形成Al覆膜10nm、Al及類石墨碳覆膜的混合存在層5nm、及類石墨碳覆膜10nm而成的集電體。于金屬箔上的覆膜形成,均通過上述離子蒸鍍法來進(jìn)行。關(guān)于各比較例、及實施例的放電速率特性的試驗結(jié)果,如表3至表13所示。此外,關(guān)于各比較例、及實施例的每個放電速率電流值中所決定的電容量維持率,于圖11中顯示為柱狀圖。[表3][表4][表5][表6][表7][表8][表9][表10][表11][表12][表13]觀察圖11,與使用比較例1至7的集電體時的放電速率特性相比,使用本發(fā)明的集電體的實施例1至4的放電速率特性提升較為明顯。此外,表14至表15顯示于各個比較例1至7、實施例1至4中結(jié)束充放電的1周期時所決定的電容量維持率,并于圖12中顯示為柱狀圖。[表14][表15]實施例1實施例2實施例3實施例41(周期數(shù))1001001001002100.1100.2100.1100.33100.1100.4100.3100.44100.4100.5100.1100.35100.2100.5100.3100.46100.3100.4100.4100.57100.1100.7100.2100.68100.4100.8100.3100.69100.2100.4100.3100.410100.3100.5100.4100.311100.2100.8100.3100.512100.3100.9100.4100.813100.4101.3100.2100.914100.5101.2100.3101.015100.3101.1100.4101.016100.2101.2100.1100.917100.3101.2100.2101.018100.5100.9100.3100.919100.6100.9100.2101.020100.1101.1100.3100.9圖12中,與使用隨著周期數(shù)的增加而產(chǎn)生電容量維持率的降低的比較例1至7的集電體時的充放電周期壽命特性相比,使用本發(fā)明的集電體的實施例1至4中,在第20周期為止均未引起電容量的降低,可得知充放電循環(huán)壽命的提升較為明顯。圖13是顯示關(guān)于比較例1及2、實施例1及2,用以評估金屬箔的粗面化對集電體與電極層的密著強(qiáng)度所帶來的效果的SAICAS試驗的結(jié)果。不論有無形成覆膜,金屬箔的粗面化對于電極層間的密著強(qiáng)度的效果皆明顯。如上所述,使用本發(fā)明的集電體所制作出的電極中,顯示在高放電速率下的使用以及多數(shù)次的重復(fù)使用所造成的質(zhì)量的劣化極小。這類效果可考慮為:由于本發(fā)明的集電體具有已說明般的覆膜構(gòu)成,所以可得到界面上的高電傳導(dǎo)性及化學(xué)穩(wěn)定性而產(chǎn)生這類效果。起因于本發(fā)明的覆膜構(gòu)成的電傳導(dǎo)性及化學(xué)穩(wěn)定性的提升,顯然受到集電體的具體用途所影響,有鑒于此,當(dāng)將本發(fā)明的集電體使用在鋰離子蓄電池的負(fù)極電極側(cè)時,或是使用在電雙層電容器或混合式電容器等的正極電極側(cè)、負(fù)極電極側(cè)時,亦可推測為同樣地抑制品質(zhì)劣化。(產(chǎn)業(yè)利用性)本發(fā)明的電極材料可應(yīng)用作為卷繞型或積層型固態(tài)電解電容器的陰極箔。此外,本發(fā)明的電極材料亦可使用在以采用電解液而動作的以電解電容器為首的各種電容器、或是電雙層電容器、鋰離子電容器、鋰離子電池、太陽能電池等。本發(fā)明的集電體可應(yīng)用作為蓄電池、電雙層電容器、混合式電容器的電極。此外,本發(fā)明的集電體亦可使用在采用電解質(zhì)而驅(qū)動的太陽能電池等。