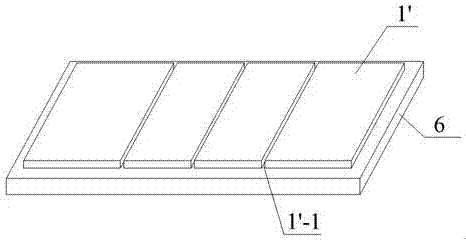
本發(fā)明公開了一種硅基薄膜太陽能電池良品率提升,更趨于技術(shù)創(chuàng)新的細化、細微的改進,屬于太陽能電池制造技術(shù)領(lǐng)域。
背景技術(shù):商業(yè)化生產(chǎn)的薄膜太陽能電池基本分為硅基薄膜、碲化鎘、銅銦鎵硒三類。其中硅基薄膜太陽能電池最廉價相對性價比最合理。從應(yīng)用角度硅基薄膜太陽能電池又分為弱光和強光兩大類。照度萬級LUX以上為強光型硅基薄膜太陽能電池,適合戶外環(huán)境下使用。照度幾千LUX以下為弱光型硅基薄膜太陽能電池,產(chǎn)品適合應(yīng)用在光線較弱的環(huán)境。非晶硅太陽能電池伴隨著液晶顯示技術(shù)的發(fā)展廣泛應(yīng)用于消費類電子產(chǎn)品做電池芯片、傳感器等。強光型硅基薄膜太陽能電池和碲化鎘、銅銦鎵硒薄膜太陽能電池一樣能,用于光伏(PV)電站和光伏建筑一體化(BIPV)。中國發(fā)明專利ZL95104992.5是一種在弱光環(huán)境下使用的非晶硅太陽能電池,該發(fā)明解決了非晶硅薄膜太陽能電池制造中諸多技術(shù)難題和工藝問題,但仍存在一個提高良品率和外觀質(zhì)量等問題。目前,主導(dǎo)薄膜太陽能電池(以下簡稱電池板,電池或電池芯片)市場的硅基薄膜太陽能電池其性價比合理,市場潛力大,但仍面臨著產(chǎn)品的良品率的再提升和外觀質(zhì)量問題,需要突破技術(shù)瓶頸、創(chuàng)新才能達到目的。如硅基薄膜太陽能電池仍存在一個漏電問題,有時出現(xiàn)電壓跳變等現(xiàn)象,使電壓不夠穩(wěn)定。究其原因和加工過程有關(guān),前電極圖形內(nèi)的導(dǎo)電膜會產(chǎn)生毛刺和碎屑,致使相鄰電池節(jié)之間導(dǎo)電膜的絕緣隔離間距減小。另外,膜脫落和電極附著力差與薄膜太陽能電池襯底(或稱基片)附著力性能有關(guān)。如弱光型非晶太陽能電池,漏電流大,在無光照射情況下,正向施加1.7V直流電壓,漏電流遠大于0.3微安。具統(tǒng)計,批量生產(chǎn)時,通常大約有5%的電池芯片的銅漿電極附著力達不到0.6公斤,膜會脫落,嚴重的會導(dǎo)致非晶硅太陽能電池完全失效。產(chǎn)品外觀質(zhì)量,主要集中在表面出現(xiàn)“麻點”。ITO透明導(dǎo)電膜上存在臟污漏電還與ITO導(dǎo)電膜的隔離線暴露在外沾染臟污或空氣中潮濕污物,也都會導(dǎo)致漏電。另外,碳漿背電極與保護背漆層沒有完全重合,導(dǎo)致碳漿背電極邊沿暴露在外也會產(chǎn)生漏電。只有附著力達到0.6公斤及以上,銅漿電極才不易脫落。
技術(shù)實現(xiàn)要素:本發(fā)明通過以上對現(xiàn)有技術(shù)存在的主要問題的分析和研究,并通過工業(yè)試驗,對亟待要解決的產(chǎn)品質(zhì)量難題,提供了技術(shù)解決方案。本發(fā)明的目的是:進一步細化完善硅基薄膜太陽能電池前電極電圖形,克服由膜層脫落而導(dǎo)致電壓不穩(wěn)定;減小漏電流;消除產(chǎn)品外觀表面出現(xiàn)的“麻點”提高產(chǎn)品良品率。本發(fā)明的另一個目的是:解決弱光條件下非晶硅太陽能電池漏電流大的技術(shù)難題,改變硅基薄膜太陽能電池P層內(nèi)部雜質(zhì)缺陷密度,顯著減小漏電流,改善電池性能。本發(fā)明的又一個目的是:改善非晶硅太陽能電池的背電極結(jié)構(gòu),增強電池池背電極包括由背電極引出的銅漿電極附著力,降低生產(chǎn)成本。為實現(xiàn)本發(fā)明提出的任務(wù)和目的,提供技術(shù)解決支持方案:一種硅基薄膜太陽能電池,包括基片,前電極,PIN光電轉(zhuǎn)化層和背電極,其技術(shù)特征在于所說的前電極是透明導(dǎo)電膜前電極圖形陣列,至少包括ITO、ZnO,、石墨烯透明導(dǎo)電膜中的一種,所說前電極圖形陣列包覆在透明基片上,包括基片的邊沿;所說的PIN光電轉(zhuǎn)化層是硅基非晶硅層,前電極圖形陣列還包括防漏電的隔離線或前電極邊緣的絕緣線,貫通PIN非晶硅層的各種通孔;所說的PIN非晶硅N層的背電極是復(fù)合金屬背電極或碳漿電極中的一種;所說的碳漿電極是有背漆保護層的PIN非晶硅N層背電極,其上引出銅漿電極覆蓋在背漆保護層開口處的背漆保護面和碳漿電極面上,以增強銅漿電極的附著力防止膜層脫落。本發(fā)明的方案還包括硅基薄膜太陽能電池制備方法,其技術(shù)特征是用ITO、ZnO,、石墨烯透明導(dǎo)電膜其中的一種透明導(dǎo)電膜在基片上制備制備前電極圖形陣列,透明導(dǎo)電膜,包括,所說透明包覆在透明基片上,包括基片的邊沿;包括在導(dǎo)電玻璃基片或?qū)щ娋埘喕瑢?dǎo)電膜上形成前電極圖形,其技術(shù)特征在于制備前電極圖形方法包括激光刻劃和絲網(wǎng)印刷;選擇絲網(wǎng)印刷前電極圖形,在相鄰連接的圖形之間均設(shè)有一定寬度的隔離線以防漏電;單元電池周邊有增強附著力的ITO導(dǎo)電膜以防膜層脫落;采用清洗法消除前電極導(dǎo)電圖形表面“麻點”可,包括水清洗,超聲波清洗;PIN的N層背電極層選碳漿電極,用銅漿電極作背電極引出,背漆保護層包覆碳漿電極層。實施本發(fā)明積極效果是通過技術(shù)創(chuàng)新,突破了傳統(tǒng)設(shè)計思路,極大地提高升了非晶硅太陽能電池良品率和外觀質(zhì)量,消除了前電極麻點,漏電流明顯著減少,電壓穩(wěn)定,生產(chǎn)成本降低。常規(guī)弱光型非晶硅太陽能電池工藝的ITO透明導(dǎo)電膜前電極的四周邊沿被除掉,導(dǎo)致在無ITO膜的四周邊沿的非晶硅膜容易脫落,進一步引發(fā)ITO透明導(dǎo)電膜前電極隔離線上的非晶硅脫落,本發(fā)明改變ITO透明導(dǎo)電膜前電極的結(jié)構(gòu),保留非晶硅太陽能電池四周邊沿的ITO膜,不被去除,就能解決非晶硅膜層不脫落的問題。弱光型非晶硅太陽能電池P層非晶硅往往是采用重摻雜制備的,通常硼與硅的摻雜比在1%甚至更高,這樣將導(dǎo)致p層內(nèi)部雜質(zhì)缺陷密度很大,產(chǎn)生大量的載流子復(fù)合中心,顯著增加電池內(nèi)部的漏電流。本發(fā)明采用合適的硅烷和三甲基硼烷的流量配比,在保證電池開路電壓不變的情況下,使硼的摻雜比小于1%,大大減少了p層內(nèi)部雜質(zhì)缺陷密度,顯著減小了漏電流。通常弱光型非晶硅太陽能電池的背電極是采用碳漿導(dǎo)電層,銅漿電極作引出電極,為了對碳漿背電極進行保護,在其上要制作一層背漆保護層,然后再在背漆保護層預(yù)留的開口上制作一層銅漿電極層。通常一般設(shè)計人員的思路是盡量增大銅漿電極與碳漿背電極層的接觸面積,以便盡可能地減小接觸電阻,而銅漿是比較昂貴的材料,其面積不可做得很大,因此設(shè)計的銅漿電極盡量與碳漿背電極接觸面積大,而與背漆保護層的接觸面積盡量小,以節(jié)省成本。但這樣設(shè)計有約5%的電池片的銅漿電極附著力達不到0.6公斤,導(dǎo)致銅漿電極容易脫落。通過試驗我們發(fā)現(xiàn)銅漿電極在背漆保護層上的附著力比銅漿電極在碳漿背電極上的附著力大,另一方面經(jīng)過仔細分析我們認為,非晶硅薄膜是一種半絕緣材料,其電子遷移率低,通常不超過0.5cm2/v.s,因此非晶硅太陽能電池的內(nèi)阻大,其串聯(lián)電阻(包括體電阻,碳漿背電極橫向電阻和透明導(dǎo)電膜前電極的橫向電阻)也大,且遠大于銅漿電極和碳漿背電極的接觸電阻,因此即使減小銅漿電極和碳漿背電極的接觸面積也不會對非晶硅太陽能電池的電性能產(chǎn)生影響,基于此分析,在保持銅漿電極面積不變的情況下,縮小保護背漆層上的開口面積,減小銅漿電極和碳漿背電極的接觸面積,相應(yīng)增大了銅漿電極和保護背漆層的接觸面積,因銅漿電極與背漆保護層結(jié)合力良好,使銅漿電極的附著力顯著增加,可使全部電池片的銅漿電極附著力達到0.6公斤以上,銅漿電極牢固不易脫落。以上所說電壓不穩(wěn)定的原因有三個方面,一是由于電池片邊均有ITO膜,在由大板電池板切割成電池片時,相鄰節(jié)的ITO膜易產(chǎn)生毛刺或碎屑使相鄰節(jié)ITO膜的隔離線間距減小,造成漏電的可能性大大增加;二是邊沿的ITO膜的隔離線暴露在外,在電池片運輸過程中,隔離線上沾染的臟污或空氣中潮濕污物導(dǎo)致漏電;三是碳漿背電極與保護背漆層沒有完全重合,導(dǎo)致碳漿背電極邊沿暴露在外,也會因隔離線上沾染的臟污或空氣中潮濕污物導(dǎo)致漏電。通常弱光型非晶硅太陽能電池的工作電流為幾十微安,因此如果漏電流達到了1微安,就會對其電壓產(chǎn)生比較大影響,而相鄰兩節(jié)間的電壓為0.8V,根據(jù)歐姆定律R=U/I,R=0.8/(1x10-6)=0.8x106Ω,也就是說,如果相鄰兩節(jié)間的絕緣電阻小到0.8x106Ω即0.8MΩ,就會對電池電壓產(chǎn)生比較大的影響,通常在實際生產(chǎn)中切割電池片時產(chǎn)生的ITO膜毛刺或碎屑的長度小于0.3mm,假如ITO毛刺長度達到0.28mm其寬度為0.001mm,正好將相鄰兩節(jié)ITO膜相連起來,而實際使用的ITO膜的厚度約為77nm,ITO膜的電阻率為3.85x10-4Ω·cm,根據(jù)電阻公式R=ρL/S可計算出毛刺的電阻為:R=3.85x10-4x0.28x10-1/(0.001x10-1x77x10-7)=1.4x104Ω,此電阻遠小于上述0.8x106Ω,該毛刺引起的漏電流遠大于1微安,將嚴重影響電壓,因此ITO透明導(dǎo)電膜的隔離線寬度定在0.3mm以上,同時考慮到隔離線太寬會減小電池的有效面積,本發(fā)明的隔離線寬度為0.3~0.6mm;另一方面將保護背漆層設(shè)計成比碳漿背電極面積更大,使之完全覆蓋碳漿背電極。通過以上措施消除了電池電壓不穩(wěn)定現(xiàn)象。本發(fā)明以弱光型硅基薄膜太陽能電池為例詳細的技術(shù)內(nèi)容如下:采用14英寸x16英寸的ITO透明導(dǎo)電玻璃,可在其上排布制作許多弱光型非晶硅太陽能電池片。首先制作ITO透明導(dǎo)電膜前電極圖形。在ITO透明導(dǎo)電玻璃上絲網(wǎng)印刷一層耐酸油墨作為掩膜層,通過濕法化學腐蝕法形成所需ITO前電極圖形,相鄰節(jié)透明導(dǎo)電膜前電極之間的隔離線寬在0.4mm~0.6mm范圍。去除耐酸油墨后,進行清洗,為消除麻點,采用獨特的清洗溶液配方和工藝,先進行除油,采用氫氧化鈉和磷酸鈉的混合溶液,重量配比為水:氫氧化鈉:磷酸鈉=(135~155):(1~3):(3~5),將去除耐酸油墨的ITO玻璃放入配好的溶液中,浸泡2~10分鐘,溶液溫度控制在45~50攝氏度;之后進行超聲清洗,超聲清洗液采用獨特配方,重量配比為水:特選清洗粉=(1200~1400):(6~8),將去油后的ITO玻璃放入配好的溶液中,超聲清洗40~80分鐘,溶液溫度控制在45~60攝氏度;ITO玻璃再經(jīng)自動清洗機進行后清洗,清洗完后放入沉積夾具和真空室沉積P,I,N層非晶硅。為了減小弱光型非晶硅太陽能電池的漏電流,P層非晶硅采用了特殊的沉積工藝參數(shù)和原料氣體流量配比,流量配比為:三甲基硼烷:甲烷:硅烷:氫氣=(5~7):(30~40):(60~65):(15~17),其中三甲基硼烷的濃度為3%,即三甲基硼烷:(三甲基硼烷+硅烷)=3%,沉積溫度225攝氏度,沉積壓力60Pa,放電功率85W;之后采用激光刻劃非晶硅膜,接著依次絲網(wǎng)印刷碳漿制作碳漿背電極,絲網(wǎng)印刷背漆制作背漆保護層,為了消除電壓不穩(wěn)定現(xiàn)象,將背漆保護層做得比碳漿背電極大,以完全覆蓋碳漿背電極,考慮到絲網(wǎng)印刷有一定的偏移公差,背漆保護層比碳漿背電極四周大0.5~2mm。接著絲網(wǎng)印刷銅漿制作銅漿電極,為了增加銅漿電極的附著力,采用增大銅漿電極與背漆保護層的接觸面積,相應(yīng)減小銅漿電極與碳漿背電極的接觸面積。銅漿電極長x寬范圍為(1.3~1.6)x(2.6~3.5)mm,銅漿電極的邊長比背漆開口的邊長大1mm以上,銅漿電極的寬比背漆開口的寬大0.6mm以上。附圖說明本發(fā)明的工作原理結(jié)合附圖作進一步說明:圖1、是本發(fā)明硅基非晶硅太陽能電池結(jié)構(gòu)的剖面示意圖。其中用ITO透明導(dǎo)電膜作前電極1,PIN硅基非晶硅層2,碳漿電極3,背漆保護層4,銅漿電極5,5-1作為負電極引出,5-2作為正電極引出,基片6是玻璃,2-2選則在一節(jié)不再光電轉(zhuǎn)換的PIN非晶硅層,其中將ITO透明導(dǎo)電膜前電極1引到PIN非晶硅層2的N層為正電極3-2。圖2、是現(xiàn)有技術(shù)ITO透明導(dǎo)電膜的前電極剖面示意圖。其中玻璃基片6,ITO透明導(dǎo)電膜前電極1’,ITO透明導(dǎo)電膜前電極的隔離線1’-1。從圖中可以看到玻璃基片四周沒有ITO透明導(dǎo)電膜,這種設(shè)計后續(xù)會出現(xiàn)玻璃基片周邊沿區(qū)域非晶硅嚴重脫膜,進而引起ITO透明導(dǎo)電膜前電極隔離線上的非晶硅膜脫落,導(dǎo)致太陽能電池失效。附圖3、是本發(fā)明圖1中ITO透明導(dǎo)電膜前電極圖形1示意圖。其中6為玻璃基片,ITO透明導(dǎo)電膜前電極1,ITO透明導(dǎo)電膜前電極1的隔離線1-1,從圖中可以看到玻璃基片6四周邊沿的ITO透明導(dǎo)電膜被保留,可有效防止后續(xù)非晶硅膜的脫落??梢钥吹奖景l(fā)明ITO透明導(dǎo)電膜前電極1的隔離線1-1寬度(0.4~0.6mm)比現(xiàn)有技術(shù)的隔離線(0.3mm以下)1’-1寬,以減小因切割產(chǎn)生圖2導(dǎo)電膜碎屑和毛刺或污物導(dǎo)致漏電的可能性。圖4、是本發(fā)明圖1中背電極的碳漿電極3的剖面示意圖。其中6為玻璃基片,ITO透明導(dǎo)電膜前電極1,ITO透明導(dǎo)電膜前電極1的隔離線1-1,從圖中可以看到玻璃基片6四周邊沿的ITO透明導(dǎo)電膜被保留,可有效防止后續(xù)非晶硅膜的脫落??梢钥吹奖景l(fā)明ITO透明導(dǎo)電膜前電極1的隔離線1-1寬度(0.4~0.6mm)比現(xiàn)有技術(shù)的隔離線(0.3mm以下)1’-1寬,以減小因切割產(chǎn)生圖2導(dǎo)電膜碎屑和毛刺或污物導(dǎo)致漏電的可能性。圖5、是本發(fā)明圖1中背漆保護層4、碳槳電極3剖面示意圖。其中玻璃基片6,背漆保護層4,4-1,4-2皆為背漆開口。通過背漆開口4-1銅漿電極引出負電極,通過背漆開口4-2銅漿電極引出正電極。圖6、是常規(guī)弱光型非晶硅太陽能電池的背漆保護層和碳漿背電極疊合在一起的圖示。其中6是玻璃基片,3’是碳漿背電極,4是背漆保護層,5是銅漿電極。由于絲網(wǎng)印刷存在偏移公差,使得是生產(chǎn)時背漆保護層4不能完全覆蓋住碳漿背電極3’,未被覆蓋住的碳漿背電極3’邊沿處的隔離線易被臟污沾染導(dǎo)致漏電,是使電壓不穩(wěn)定的原因之一。圖7、是圖1中的銅漿電極5的背漆保護層4和碳漿電極3的剖面示意圖。圖A放大圓圈內(nèi)表示銅漿電極5分別在背漆保護層4和碳漿電極3引出的正電極3-2,玻璃基片6,碳漿背電極3,背漆保護層4,銅漿電極5,碳漿電極3比背漆保護層4面積小,因此即使絲網(wǎng)印刷有偏移公差,背漆保護層4也能在四周邊沿完全覆蓋包住碳漿背電極3,可減小產(chǎn)生電壓不穩(wěn)定的幾率,銅漿電極5覆蓋在背漆開口4-1、4-2上(見圖5),銅漿電極5與背漆保護層4相接觸區(qū)域的面積比常規(guī)非晶硅太陽能電池的銅漿電極與背漆保護層相接觸區(qū)域面積大,使得所有單元電池的銅漿電極附著力都到0.6公斤以上,銅漿電極非常牢固不易脫落,顯示背漆保護層保住碳漿背電極邊沿位置。圖8、是本發(fā)明實施例6圓形透明導(dǎo)電膜前電極的剖面示意圖。其中玻璃基片6D,ZnO透明導(dǎo)電膜前電極1D,相鄰節(jié)ZnO透明導(dǎo)電膜前電極間的隔離線1D-1,ZnO透明導(dǎo)電膜前電極邊沿的絕緣線1D-2,用于切割ZnO透明導(dǎo)電膜前電極1D和背電極時防止搭接在一起導(dǎo)致短路。圖9、是本發(fā)明實施例6激光刻除PIN膜的剖面示意圖。其中PIN非晶硅基薄膜2D,PIN非晶硅基薄的激光打孔形成的刻劃線2D-1,作為相鄰單節(jié)電池間正負電極串聯(lián)通道,玻璃基片6D,ZnO透明導(dǎo)電膜前電極1D,相鄰節(jié)ZnO透明導(dǎo)電膜前電極間的隔離線1D-1。圖10、是本發(fā)明實施例6前電極和金屬背電極剖面示意圖。ZnO透明導(dǎo)電膜前電極1D、相鄰節(jié)ZnO透明導(dǎo)電膜前電極間的隔離線1D-1,激光刻劃復(fù)合背電極3D是銀膜和鎳銅合金的復(fù)合膜,激光貫穿刻劃非晶硅基薄膜和復(fù)合背電極形成的激光刻劃線3D-1,單節(jié)電池間的隔離線2D,非晶硅基薄膜,玻璃基片6D。圖11、是本發(fā)明實施例6的透明視窗的剖面示意圖。圓形非晶硅太陽能單元電池制作完背漆保護層并去除中央圓形區(qū)域的非晶硅基薄膜和背電極形成透明視窗后的剖面示意圖,其中背漆保護層4D,背漆開口4D-1,焊接正負極引線之用,是PIN非晶硅基薄膜2D,玻璃基片6D,ZnO透明導(dǎo)電膜前電極1D,相鄰節(jié)ZnO透明導(dǎo)電膜前電極間的隔離線1D-1,透明視窗2D-2。圖12、是本發(fā)明實施例7第一次沖孔形成的導(dǎo)流孔的示意圖。柔性非晶硅和非晶硅鍺疊層太陽能電池第一次沖孔后的示意圖。其中聚酰亞胺柔性基片6R,第一次沖孔形成的導(dǎo)流孔,用于將背電極引到聚酰亞胺柔性基片背面。圖13、是本發(fā)明實施例7的第一次沖孔示意圖。柔性非晶硅和非晶硅鍺疊層太陽能電池第一次沖孔后在聚酰亞胺柔性基片正面鍍連續(xù)濺鍍金屬鋁膜,銀膜和ITO透明導(dǎo)電膜和在聚酰亞胺柔性基片背面濺鍍金屬鋁膜后的剖面圖,其中金屬鋁膜3R-1,金屬銀膜3R-2,ITO透明導(dǎo)電膜3R-3,導(dǎo)流孔被上述各層膜填充后導(dǎo)流孔3R-4,聚酰亞胺柔性基片6R,第一次沖孔形成的導(dǎo)流孔6R-1是,聚酰亞胺柔性基片背面的金屬鋁膜7R。圖14、是本發(fā)明實施例7的第二次沖孔剖面圖示意圖。是柔性非晶硅和非晶硅鍺疊層太陽能電池第二次沖孔后形成匯流孔3R-5,用于匯集電流藉此將相鄰單節(jié)電池正負極相串聯(lián)。圖15、是本發(fā)明實施例7的柔性非晶硅和非晶硅鍺疊的面示意圖。柔性非晶硅和非晶硅鍺疊層沉積成硅基薄膜后的N型非晶硅膜2R-N1,本征非晶硅鍺膜2R-I1,P型非晶硅膜2R-P1,N型氧化硅(SiOx)2R-N2,是本征非晶硅鍺膜2R-I2,P型非晶硅膜2R-P2,經(jīng)硅基薄膜填充后的導(dǎo)流孔2R-1,經(jīng)硅基薄膜填充后的匯流孔2R-2。圖16、是本發(fā)明實施例7的激光刻劃后的剖面示意圖。柔性非晶硅和非晶硅鍺疊層太陽能電池沉積完ITO透明導(dǎo)電膜并經(jīng)激光刻劃后,其中ITO透明導(dǎo)電膜1R,作為前電極,經(jīng)ITO透明導(dǎo)電膜填充的匯流孔1R-1,是激光貫穿刻劃復(fù)合背電極,硅基薄膜和ITO透明導(dǎo)電膜形成的隔離線3R-6,聚酰亞胺柔性基片背面的金屬鋁膜用激光刻劃隔離線7R-1。圖17、是本發(fā)明實施例7的層壓封裝完后的剖面示意圖。柔性非晶硅和非晶硅鍺疊層太陽能電池層壓封裝完后,其中PET(聚對苯二甲酸乙二醇酯)4R,正負極引出涂錫帶5R,ETFE(乙烯-四氟乙烯共聚物)8R是,EVA(乙烯-醋酸乙烯共聚物)9R是。具體實施方式例1、本發(fā)明實施例圖3,圖5、圖7具體制作方法如下:制備前電極圖形在356x406平方毫米的ITO透明導(dǎo)電玻璃上按照弱光型非晶硅太陽能電池需要設(shè)計前電極圖形(單元電池由四個單節(jié)電池串聯(lián)組成,整個ITO透明導(dǎo)電玻璃上以單元電池長寬尺寸為周期陣列排布)采用絲網(wǎng)印刷方法印刷一層耐酸油墨,并固化作為腐蝕掩膜層,接著將固化耐酸油墨的ITO透明導(dǎo)電玻璃,放入三氯化鐵,鹽酸和水的混合溶液中進行腐蝕,將裸露的ITO透明導(dǎo)電膜腐蝕掉,形成ITO透明導(dǎo)電膜前電極1,相鄰節(jié)ITO透明導(dǎo)電膜前電極間的隔離線1-1的寬度為0.5mm;水清洗將腐蝕完的透明導(dǎo)電玻璃放入氫氧化鈉溶液中去除耐酸油墨,并用自來水進行沖洗干凈,接著將ITO透明導(dǎo)電玻璃放入氫氧化鈉和磷酸鈉的混合溶液中進行除油,混合溶液的重量配比為水:氫氧化鈉:磷酸鈉=144:2.6:3.5,將除去耐酸油墨的ITO玻璃放入配好的溶液中,浸泡10分鐘,溶液溫度控制在45~50攝氏度;超聲清洗將除油后的ITO透明導(dǎo)電玻璃放入獨特配方的清洗液中進行超聲清洗,清洗液重量配比為水:清洗物質(zhì)=1450:6.5,將去油后的ITO玻璃放入配好的溶液中,超聲清洗80分鐘,溶液溫度控制在45~60攝氏度,之后用自動清洗機和純水進行后清洗,并經(jīng)風刀吹干待用;PIN非晶硅膜沉積將清洗好的ITO透明導(dǎo)電玻璃,裝入沉積夾具中并放入真空室中采用等離子體化學氣相沉積法進行PIN非晶硅膜沉積,其中P層非晶硅采用特殊沉積工藝參數(shù)和原料氣體流量配比,流量配比為:三甲基硼烷:甲烷:硅烷:氫氣=7:30:60:15,沉積溫度200~250攝氏度,沉積壓力50~70Pa,放電功率80~90W,沉積時間85~95秒;激光刻劃隔離線綠激光刻劃非晶硅膜,形成連接相鄰兩節(jié)單節(jié)電池的激光打孔刻劃線,每束激光功率為0.4~0.6瓦,激光刻劃線寬0.1~0.2mm,在刻劃的同時進行強力吸塵,防止因刻劃形成的非晶硅碎屑散落到激光打孔刻劃的隔離線內(nèi)影響電池性能;背電極形成依次絲網(wǎng)印刷碳漿并烘干固化成碳漿背電極3,固化溫度控制在145~155攝氏度,固化時間為55~65分鐘;絲網(wǎng)印刷背漆并烘干固化形成背漆保護層4,固化溫度控制在135~145攝氏度,固化時間為40分鐘,以消除漏電和電壓不穩(wěn)定隱患,背漆保護層4比碳漿背電極3四周大1mm目的使背漆保護層4能可靠地覆蓋碳漿背電極3;背電極引出在背漆開口4-1處絲網(wǎng)印刷銅漿,并烘干固化形成銅漿電極5,分兩步進行固化,首先在75~85攝氏度下恒溫75~85分鐘,然后再升高溫度至145~155攝氏度,恒溫35~45分鐘。其中背漆開口4-1長寬為1.8x0.7mm,銅漿電極5長寬為2.9x1.4mm,可使所有單元電池的銅漿電極5附著力達到0.6公斤。最后進行切割,按檢驗標準測試,合格后包裝入庫。實施例2制作步驟與實施例1相同。僅改變水清洗環(huán)節(jié)中的工藝參數(shù):將腐蝕完的透明導(dǎo)電玻璃放入氫氧化鈉溶液中去除耐酸油墨,并用自來水進行沖洗干凈,接著將去除耐酸油墨的ITO透明導(dǎo)電玻璃放入氫氧化鈉和磷酸鈉的混合溶液中進行除油,混合溶液的重量配比為水:氫氧化鈉:磷酸鈉=150:2.0:5.0,將去除耐酸油墨的ITO玻璃放入配好的溶液中,浸泡10分鐘,溶液溫度控制在45~50攝氏度;實施例3制作環(huán)節(jié)與實施例1相同。僅改變超聲清洗環(huán)節(jié)的工藝參數(shù):將除油后的ITO透明導(dǎo)電玻璃放入獨特配方的清洗液中進行超聲清洗,清洗液重量配比為水:清洗物質(zhì)=1200:8.0,將去油后的ITO玻璃放入配好的溶液中,超聲清洗80分鐘,溶液溫度控制在45~60攝氏度,之后用自動清洗機和純水進行后清洗,并經(jīng)風刀吹干待用;實施例4制作步驟與實施例1相同。僅改變PIN非晶硅膜沉積驟中的工藝參數(shù):將后清洗好的ITO透明導(dǎo)電玻璃,裝入沉積夾具中并放入真空室中進行P,I,N非晶硅膜沉積,其中P層非晶硅采用特殊的沉積工藝參數(shù)和原料氣體流量配比,流量配比為:三甲基硼烷:甲烷:硅烷:氫氣=5:40:65:17,沉積溫度200~250攝氏度,沉積壓力50~70Pa,放電功率80~90W,沉積時間85~95秒;實施例5制作步驟與實施例1相同,僅改變背電極形成中的工藝參數(shù):依次絲網(wǎng)印刷碳漿并烘干固化成碳漿背電極3,固化溫度控制在145~155攝氏度,固化時間為55~65分鐘,絲網(wǎng)印刷背漆并烘干固化形成背漆保護層4,固化溫度控制在135~145攝氏度,固化時間為50分鐘,為消除漏電隱患,背漆保護層4比碳漿背電極3四周大0.6mm,使背漆保護層4能可靠地覆蓋碳漿背電極3,如圖5所示;背電極引出如圖7所示。在背漆開口4-1處絲網(wǎng)印刷銅漿,并烘干固化形成銅漿電極5,分兩步進行固化,首先在75~85攝氏度下恒溫75~85分鐘,然后再升高溫度至145~155攝氏度,恒溫35~45分鐘。其中背漆開口4-1長寬為2.0x0.9mm,銅漿電極長5寬為3.0x1.8mm,可使所有單元電池的銅漿電極5附著力達到0.6公斤以上。最后進行切割,按檢驗標準測試,合格后包裝入庫。實施例6見附圖8~11:此實施例例為圓形非晶硅太陽能電池,主要用于太陽能手表,制作如下:制備前電極圖形在356x406平方毫米的ZnO透明導(dǎo)電玻璃上按照非晶硅太陽能電池需要的圖形(單元電池為圓形,由四個單節(jié)電池串聯(lián)組成,每個單節(jié)電池為圓弧形狀,中間為圓形的透明視窗,整個ZnO透明導(dǎo)電玻璃上以單元電池尺寸為周期陣列排布單元電池)采用耐酸油墨作為掩膜,濕法化學腐蝕ZnO透明導(dǎo)電膜,形成ZnO透明導(dǎo)電膜前電極1D,四周的ZnO透明導(dǎo)電膜是保留的,相鄰節(jié)ZnO透明導(dǎo)電膜前電極間的隔離線1D-1的寬度為0.6mm;其中絕緣線1D-2,寬度0.3mm,是防止在切割時ZnO透明導(dǎo)電膜前電極和背電極搭接在一起導(dǎo)致短路。除耐酸油墨接著去除耐酸油墨,除油及超聲清洗后,再用自動清洗機和純水進行清洗,并經(jīng)風刀吹干待用;PIN非晶硅基薄膜沉積將清洗好的ZnO透明導(dǎo)電玻璃,裝入沉積夾具中并放入真空室中采用等離子體化學氣相沉積法進行PIN非晶硅基薄膜沉積,其中N為N型氧化硅(SiOx),以增加對短波段光的反射,提高疊層電池的短路電流。N型氧化硅(SiOx)的沉積氣體流量比為:CO2:SiH4=0.5,射頻電源放電功率90W,沉積溫度220攝氏度;激光刻劃采用綠激光刻劃非晶硅基薄膜,形成連接相鄰兩節(jié)單節(jié)電池的激光打孔刻劃線2D-1,每束激光功率為0.5瓦,激光刻劃線寬0.2mm,在刻劃的同時進行強力吸塵,防止因刻劃形成的非晶硅基薄膜碎屑散落到激光打孔刻劃線影響電池性能;制備復(fù)合背電極采用平面磁控濺射法依次濺鍍ZnO膜,銀膜和鎳銅合金膜,厚度分別為100nm,80nm和120nm,形成復(fù)合背電極3D,以增加對光的反射,提高電池轉(zhuǎn)換效率。激光貫穿刻劃隔離線3D-1采用綠激光貫穿刻劃非晶硅基薄膜2D和復(fù)合背電極3D,形成節(jié)與節(jié)之間的隔離線3D-1,每束激光功率為1.0瓦并調(diào)整好激光頻率,激光刻劃線寬0.5mm,在刻劃的同時進行強力吸塵,防止因刻劃形成的非晶硅基薄膜碎屑散落到隔離線影響電池性能;形成透明視窗采用激光刻劃方法將設(shè)計需要透明的區(qū)域上的非晶硅基薄膜及復(fù)合背電極去除,形成透明視窗,每束激光功率7W,紅外激光波長為1064nm。絲網(wǎng)印刷背漆并烘干固化形成背漆保護層4D,固化溫度控制在135~145攝氏度,固化時間為40分鐘,背漆開口4D-1為焊接正負極引線之用;最后進行切割,按檢驗標準測試,合格后包裝入庫。實施例7此例為柔性非晶硅和非晶硅鍺疊層太陽能電池,見附圖12至17圖:柔性基片第一次沖孔在356x406平方毫米的聚酰亞胺柔性基片6R上按照非晶硅太陽能電池需要的圖形(此例中,沿寬度566mm方向等分分成40節(jié),整個單元電池有40個單節(jié)電池內(nèi)部組成。每個單元電池為矩形形狀。)沿寬度方向的兩側(cè)邊沿距邊沿10mm出進行第一次沖孔,作為導(dǎo)流孔6R-1,孔徑2.5mm,相鄰孔間距9mm,并用純水沖洗干凈吹干;制備復(fù)合背電極3R采用平面磁控濺射法在已沖孔的聚酰亞胺柔性基片上正面連續(xù)濺鍍金屬鋁膜,銀膜和ITO透明導(dǎo)電膜,作為復(fù)合背電極3R,,以增加對入射光的反射;并在背面濺鍍金屬鋁膜7R;第二次沖孔將已濺鍍金屬膜的聚酰亞胺柔性基片沿長度方向進行第二次沖孔,作為匯流孔3R-5,孔徑1.5mm,相鄰孔間距5mm,并用純水沖洗干凈和吹干;氣相沉積光電轉(zhuǎn)換層將已第二次沖孔的聚酰亞胺柔性基片裝入沉積夾具中并放入真空室中采用等離子體化學氣相沉積法進行連續(xù)兩個子電池N1,I1,P1和N2,I2,P2硅基薄膜沉積,構(gòu)成非晶硅非晶硅鍺疊層電池光電轉(zhuǎn)換層主體2R,其中I1為本征非晶硅鍺膜,N1為N型非晶硅膜,P1為P型非晶硅膜,I2為本征非晶硅膜,P2為P型非晶硅膜,N2為N型氧化硅(SiOx),以增加對短波段光的反射,提高疊層電池的短路電流。N型氧化硅(SiOx)的沉積氣體流量比為:CO2:SiH4=0.4,射頻電源放電功率90W,沉積溫度200攝氏度;平面磁控濺射采用平面磁控濺射法在沉積完硅基薄膜的聚酰亞胺柔性基片上濺鍍ITO透明導(dǎo)電膜作為前電極1R,在基片背面濺鍍一層金屬鋁膜以形成正負極的內(nèi)部互連;采用綠激光將ITO透明導(dǎo)電膜,所有硅基薄膜層和復(fù)合背電極層貫穿刻劃形成隔離線3R-6,同時將背面的金屬鋁膜按相應(yīng)圖形進行錯位刻劃形成隔離線7R-1,最終形成相鄰單節(jié)電池內(nèi)部串聯(lián)的單元電池。每束激光功率為0.6瓦,激光刻劃隔離線寬0.5mm,在刻劃的同時進行強力吸塵,防止因刻劃形成的非晶硅基薄膜碎屑散落到激光打刻劃線影響電池性能;將已做好的單元電池用涂錫帶把正負電極引出5R,并在其正面鋪上EVA(乙烯-醋酸乙烯共聚物)9R和ETFE(乙烯-四氟乙烯共聚物)8R,在背面鋪設(shè)EVA(乙烯-醋酸乙烯共聚物)9R和PET(聚對苯二甲酸乙二醇酯)4R,然后放入層壓機進行層壓封裝,層壓溫度140攝氏度,層壓時間50分鐘。層壓后進行修邊,檢測,至此全部制作過程完成。以上結(jié)合附圖對本發(fā)明創(chuàng)造的實施例作了詳細說明,但本發(fā)明創(chuàng)造的并不限于上述實施例,在本領(lǐng)域普通技術(shù)人員所具備的的知識范圍內(nèi)還可以,在不脫離本發(fā)明創(chuàng)造宗旨的前提下作出各種變化。