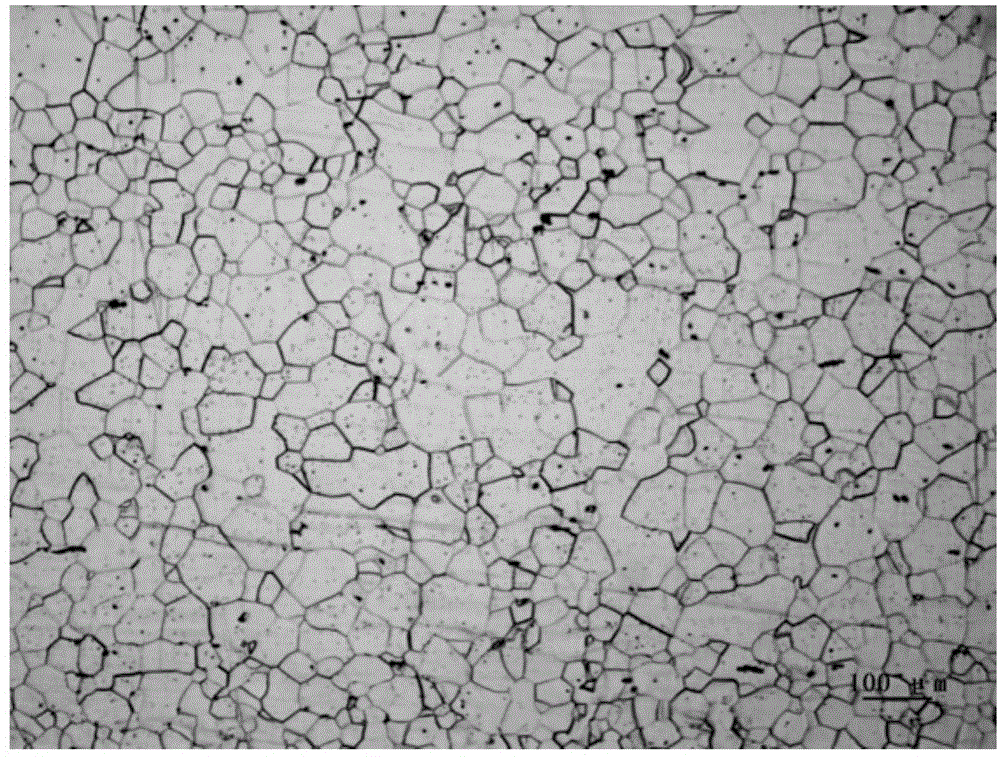
本發(fā)明屬于中鉻鐵素體不銹鋼冷軋板制備領(lǐng)域,具體涉及一種汽車排氣系統(tǒng)用中鉻鐵素體不銹鋼的冷軋生產(chǎn)方法。
背景技術(shù):
:近幾年隨著我國汽車工業(yè)的快速發(fā)展,汽車排放等級化、為實現(xiàn)節(jié)能而提出的汽車減重等要求進一步提高。不銹鋼材料特別是高性能的中鉻鐵素體不銹鋼材料得到了廣泛應(yīng)用,用量也在逐年增加,其主要用于排氣系統(tǒng)。汽車排氣系統(tǒng)用中鉻鐵素體不銹鋼通常為冷軋板,20世紀50年代發(fā)展起來的往復式冷軋是目前不銹鋼冷軋板帶的主要生產(chǎn)方式,其原料一般為退火酸洗態(tài)熱軋板坯。熱軋板坯經(jīng)過一定程度的冷軋變形獲得了厚度很薄、尺寸精確、表面光潔和性能均一的冷硬態(tài)板帶鋼,再經(jīng)過后續(xù)的熱處理和精整就能使板帶鋼具有良好的力學性能和加工性能。汽車排氣系統(tǒng)用中鉻鐵素體不銹鋼要求具有較好的成形性。排氣系統(tǒng)零部件在沖壓生產(chǎn)過程中因成形性不良容易產(chǎn)生各種起皺和開裂等缺陷,造成制件報廢,不僅提高了制造成本,而且造成了材料浪費。與成形性有關(guān)的材料性能參數(shù)主要有:塑形應(yīng)變比r、極限深沖比LDR、應(yīng)變硬化系數(shù)n、強度、延伸率。r值高,越不易減薄,可滿足零部件的沖壓加工要求;LDR越高,成形性越好;n值越大,拉延能力越強,沖壓性能越好;強度和延伸率越高,材料性能越好,越不易發(fā)生加工開裂等問題。通常認為,r值的主要影響因素是冷軋總壓下率,較高的冷軋總壓下率能使再結(jié)晶退火后的有利織構(gòu)增強,有利于提高冷軋薄板的沖壓成形性能?,F(xiàn)有往復軋制工藝生產(chǎn)的中鉻鐵素體不銹鋼,r值一般在1.1~1.4之間,在加工成形過程中因成形性比較薄弱而發(fā)生的問題普遍比較多。此外,汽車排氣管置于車輛底盤下,因此排氣系統(tǒng)用鐵素體不銹鋼的表面粗糙度要求比外觀用鐵素體不銹鋼的要求較低。外觀用中鉻鐵素體不銹鋼產(chǎn)品的粗糙度要 求一般在0.3μm以下,汽車排氣系統(tǒng)用中鉻鐵素體不銹鋼的粗糙度值一般高于這個范圍。技術(shù)實現(xiàn)要素:本發(fā)明的目的在于提供一種汽車排氣系統(tǒng)用中鉻鐵素體不銹鋼的冷軋生產(chǎn)方法,該方法生產(chǎn)效率高,且可大大提高鋼的塑形應(yīng)變比r值,提升合金的沖壓性能,粗糙度滿足用戶要求,同時保證汽車排氣系統(tǒng)業(yè)對強度、延伸率等力學性能要求,具體是:r值為1.5~1.8,屈服強度≥240MPa,抗拉強度≥415MPa,延伸率≥36%,粗糙度≤0.7μm,為排氣系統(tǒng)用中鉻鐵素體不銹鋼的工業(yè)化生產(chǎn)提供一種新的工藝技術(shù)。為達到上述目的,本發(fā)明主要采用如下技術(shù)方案:一種汽車排氣系統(tǒng)用中鉻鐵素體不銹鋼的冷軋生產(chǎn)方法,包括如下步驟:1)冶煉、鑄造將煉鋼原料熔煉,澆注,采用模鑄或連鑄鑄造成鑄錠或鑄坯;2)鑄錠鍛造將鑄錠進行鍛造,加熱到1100~1200℃后保溫一段時間鍛造,保溫時間按1~3min/mm×鑄錠厚度控制,終鍛溫度>900℃;鑄坯則不需要鍛造;3)鍛坯或鑄坯熱軋鍛坯或鑄坯進行熱軋,加熱溫度為1100~1200℃,保溫時間按1~3min/mm×坯厚控制,保溫后軋制,終軋溫度≥900℃,熱軋板最終厚度為3.5~5.0mm;4)熱軋板退火、酸洗退火溫度為930~1000℃,退火時間按1~3min/mm×板厚控制,用硝酸和氫氟酸混酸酸洗;5)冷軋通過五連軋機組進行五個道次的連續(xù)軋制,控制各軋制道次的壓下率,第1道次壓下率為19~21%,第2道次壓下率為34~36%,第3、4、5道次壓下率之比為6~7:4~5:3,總壓下率≥70%;冷軋后板厚度為0.8~1.5mm。6)退火、酸洗退火溫度為930~1000℃,退火時間按1~3min/mm×板厚控制,用硝酸和氫氟酸混酸酸洗。進一步,本發(fā)明步驟5)冷軋中第1道次到第5道次軋輥表面粗糙度依次為1.0~0.9μm、0.9~0.8μm、0.8~0.6μm、0.5~0.3μm、0.2~0.3μm。又,步驟5)冷軋中從第1道次到第5道次的軋制速度依次為90~120m/min、130~160m/min、170~200m/min、220~250m/min、270~300m/min。再,本發(fā)明所述中鉻鐵素體不銹鋼的r值為1.5~1.8,屈服強度≥240MPa,抗拉強度≥415MPa,延伸率≥36%,粗糙度≤0.7μm。本發(fā)明步驟5)采用五機架冷連軋的冷軋方式,與以往往復式軋制方式不同,本發(fā)明的五機架串聯(lián)是在軋制時帶鋼順序通過五個機架,一次性完成壓下變形。本發(fā)明步驟5)冷軋過程中通過控制各軋制道次的壓下率和總壓下率不低于70%,使成品板帶的縱向斷面(平行軋制方向)獲得最大剪切應(yīng)變幅值,以獲得大的剪切應(yīng)變能和大量的亞晶界,在冷軋后的退火過程中通過再結(jié)晶獲得具有γ織構(gòu)的退火組織。實踐經(jīng)驗表明,γ織構(gòu)越強,成形性越好。因此,本發(fā)明通過控制冷軋工藝,增加剪切應(yīng)變來提高成形性。本發(fā)明為了獲得帶鋼的表面粗糙度≤0.7μm,冷軋工藝中軋輥表面粗糙度選用0.2~1.0μm,第1道次-第5道次軋輥表面粗糙度依次減小,依次為1.0~0.9μm、0.9~0.8μm、0.8~0.6μm、0.5~0.3μm和0.2~0.3μm。第1、2道次軋輥粗糙度大,可保證大的壓下率,后面三道次帶鋼壓下率減小,同時要求帶鋼表面光潔度高、板形好,因此,后面三道次軋輥粗糙度依次減小。本發(fā)明鋼板厚度介于0.8~1.5mm之間:本發(fā)明鋼是應(yīng)用到汽車排氣系統(tǒng)領(lǐng)域,若材料厚度<0.8mm,滿足不了汽車使用要求;材料厚度>1.5mm,材料太厚,導致成本增加和增加車身重量,對于汽車廠來說是不可接受的。本發(fā)明步驟5)從第1道次到第5道次的軋制速度次為90~120m/min,130~160m/min,170~200m/min,220~250m/min,270~300m/min:軋制板材厚度越薄,對應(yīng)的軋制速度越大,本發(fā)明需保證每道次軋制速度與對應(yīng)板帶厚度的乘積接近。本發(fā)明利用數(shù)值模擬和實驗相結(jié)合的手段,通過各道次壓下率的分配調(diào)整及總壓下率,最終獲得r值為1.5~1.8的中鉻鐵素體不銹鋼,成形性相對較高,粗糙度滿足汽車排氣管要求,并保證了n值、強度和延伸率等性能要求。本發(fā)明的有益效果:1)本發(fā)明采用五連軋冷軋工藝,控制各道次的冷軋壓下率分配,獲得鋼板內(nèi)部幅值高的且在鋼板厚度方向上均勻的剪切應(yīng)變,高的剪切應(yīng)變可獲得大的剪切應(yīng)變能和大量的亞晶界,有利于退火后形成成形的組織和晶粒取向,即織構(gòu)越強。由于鋼中沿厚度方向應(yīng)變的高低最終決定冷軋產(chǎn)品的成形性。因此,本發(fā)明在不改變成分體系的前提下,通過冷軋工藝控制獲得高的成形性,同時降低了生產(chǎn)成本。2)與傳統(tǒng)往復式軋制生產(chǎn)工藝相比,五連軋生產(chǎn)的產(chǎn)能是其2~3倍,工藝成本僅是其50~70%,每噸鋼可節(jié)省成本至少幾百元。本發(fā)明在滿足用戶對汽車排氣系統(tǒng)用鋼加工和使用要求的同時,降低了生產(chǎn)成本,提高了鋼廠的生產(chǎn)效率和成材率。附圖說明圖1為本發(fā)明實施例1的退火板帶晶粒組織。圖2為對比例1的退火板帶晶粒組織。圖3為本發(fā)明實施例1鋼板在冷軋后縱向斷面剪切應(yīng)變。圖4為對比例1鋼板在冷軋后縱向斷面剪切應(yīng)變。具體實施方式下面結(jié)合實施例對本發(fā)明做進一步說明。本發(fā)明以4.0~5.0mm板坯連續(xù)冷軋1.0~1.2mm厚板帶為例。表1為本發(fā)明實施例1-5和對比例1的化學成分,具體制造方法如下:首先將煉鋼原料采用電爐熔煉,連鑄成200mm鑄坯;鑄坯于1100~1130℃保溫,保溫時間按1min/mm×坯厚計算,保溫后開始軋制,終軋溫度控制在900℃以上。熱軋后退火酸洗,退火溫度960~970℃,退火時間按1min/mm×板厚, 用硝酸和氫氟酸混酸酸洗;冷軋后退火酸洗,退火溫度960~970℃,退火時間按1min/mm×板厚,用硝酸和氫氟酸混酸酸洗。冷軋裝備采用五連軋機組,帶乳化液軋制,軋制速度從第一道次到第五道次,依次為90~120m/min、130~160m/min、170~200m/min、220~250m/min、270~300m/min。軋輥表面粗糙度控制在0.2~1.0μm,從第一道次到第五道次粗糙度依次減小,分別為1.0~0.9μm、0.9~0.8μm、0.8~0.6μm、0.5~0.3μm、和0.2~0.3μm,實施例1-5的冷軋生產(chǎn)工藝如表2所示。對比例1鋼的冷軋方式采用傳統(tǒng)二十輥往復式軋制,其他制造方法同實施例,對比例1的二十輥往復式冷軋工藝如表3所示。實施例1的冷軋退火板縱向晶粒組織如圖1所示,對應(yīng)的晶粒度為7級。對比例1的晶粒組織如圖2所示,晶粒度為6.5級。由圖1、圖2可知,本發(fā)明五連軋生產(chǎn)的鋼比對比例1二十輥生產(chǎn)的鋼晶粒更細小、更均勻,這是由于本發(fā)明鋼在冷軋過程中內(nèi)部形成的形變儲能和剪切應(yīng)變更大。因此,本發(fā)明再結(jié)晶形核率高,退火后晶粒更細,在厚度方向上晶粒大小也很均勻。實施例1和對比例1鋼板在冷軋后縱向斷面剪切應(yīng)變分別如圖3、圖4所示。由圖3、4可知,實施例1對應(yīng)的板坯縱向斷面上能夠形成貫穿板厚、幅值較大、分布規(guī)律的剪切應(yīng)變環(huán),且剪切應(yīng)變幅值高于對比例1,高的剪切應(yīng)變可以在獲得大的剪切應(yīng)變能和大量的亞晶界,在冷軋后的退火過程中獲得有利的再結(jié)晶組織和晶粒取向,從而提高成形性能。實施例1-5與對比例1對應(yīng)冷軋退火板的力學性能、成形性和粗糙度指標如表4所示。表4中,Rp0.2為屈服極限、Rm為強度極限、n為應(yīng)變硬化指數(shù)、r為塑性應(yīng)變比、A為延伸率、LDR為極限深沖比。由表4可知,按本發(fā)明工藝冷軋后的退火板帶r值高出0.4~0.6,延伸率高出2~3%,LDR高出0.1,強度和n值與對比例1相當,且粗糙度介于0.4~0.7μm之間,滿足汽車排氣系統(tǒng)用鋼的使用要求。因此,本發(fā)明生產(chǎn)的鋼材性能指標良好,工藝成本低,生產(chǎn)效率高。表1實施例和對比例的化學成分單位:wt,%表2表3表4Rp0.2/MPaRm/MPaA50/%n(5%-15%)r(15%)粗糙度/μmLDR實施例1265445390.251.80.42.3實施例2263430380.251.70.52.3實施例3282461390.241.60.42.3實施例4269446380.241.70.62.3實施例5265444390.251.70.72.3對比例1268434360.241.20.252.2當前第1頁1 2 3