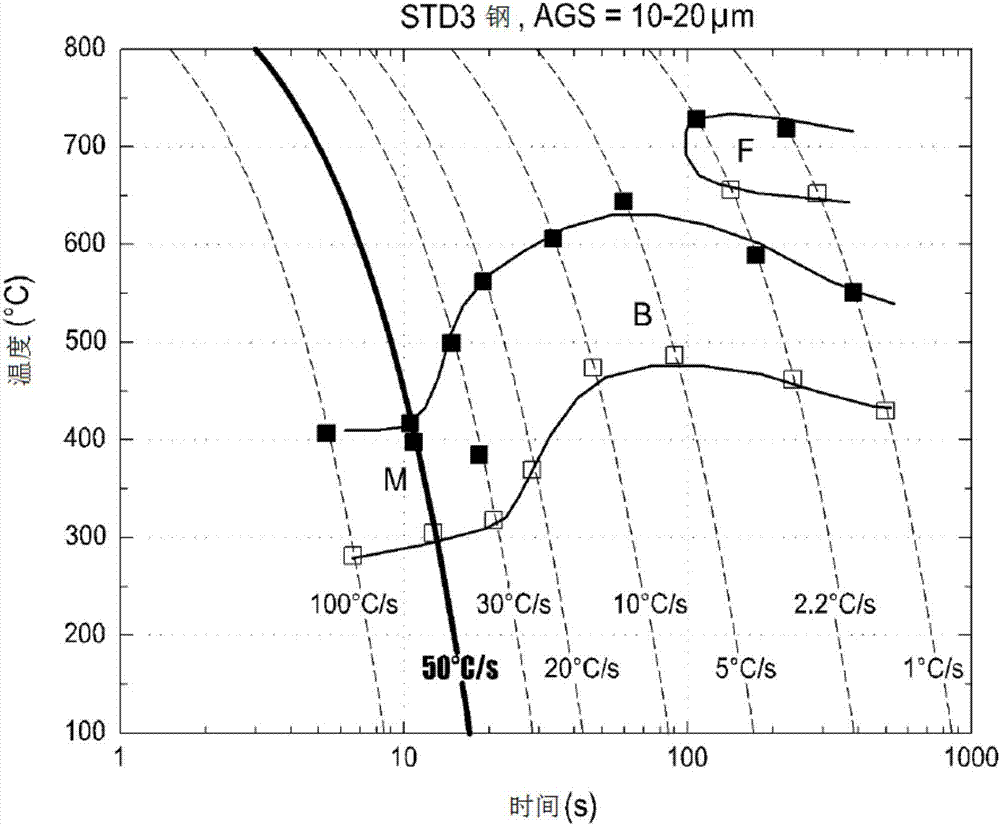
用于連續(xù)管應(yīng)用的高性能材料及其生產(chǎn)方法通過(guò)引用對(duì)任何優(yōu)先權(quán)申請(qǐng)的結(jié)合任何和所有的申請(qǐng),其在隨本申請(qǐng)遞交的申請(qǐng)資料表中表明是被要求外國(guó)或本國(guó)優(yōu)先權(quán)要求,在37CFR1.57規(guī)定下通過(guò)引用結(jié)合于此。相關(guān)申請(qǐng)本申請(qǐng)涉及申請(qǐng)人的共同未決申請(qǐng),該未決申請(qǐng)題為“COILEDTUBEWITHVARYINGMECHANICALPROPERTIESFORSUPERIORPERFORMANCEANDMETHODSTOPRODUCETHESAMEBYACONTINUOUSHEATTREATMENT(具有優(yōu)越性能的可變機(jī)械性能的連續(xù)管及通過(guò)連續(xù)熱處理生產(chǎn)該連續(xù)管的方法)”,于2011年9月9日提出申請(qǐng),序列號(hào)為13/229517,并在2012年7月26日公開(kāi),公開(kāi)號(hào)為US2012/0186686A1,該未決申請(qǐng)通過(guò)引用整個(gè)地結(jié)合于此。
背景技術(shù):近年來(lái),連續(xù)管(coiledtubing)廣泛運(yùn)用于要求高壓和延伸到達(dá)操作(extendedreachoperations)的應(yīng)用中。結(jié)果,需要生產(chǎn)具有提高的拉伸性能的連續(xù)管,以經(jīng)受:i)在懸掛或共用(pooling)長(zhǎng)柱上的軸向負(fù)載,和ii)在操作過(guò)程中施加的升高的壓力。連續(xù)管的標(biāo)準(zhǔn)生產(chǎn)將熱軋條帶用作原材料,其具有在軋制過(guò)程中通過(guò)微結(jié)構(gòu)細(xì)化(microstructuralrefinement)而獲得的機(jī)械性能。該細(xì)化通過(guò)采用不同的微合金添加劑(Ti、N、V)和合適地選擇熱軋?zhí)幚項(xiàng)l件而獲得。其目的在于控制材料再結(jié)晶和晶粒生長(zhǎng),以獲得超精細(xì)的微結(jié)構(gòu)。該材料受限于固溶體合金元素的使用和沉淀硬化,因?yàn)榧?xì)化是同時(shí)允許高強(qiáng)度和韌性的唯一機(jī)制。該原材料對(duì)每個(gè)供應(yīng)者來(lái)說(shuō)是指定的,并在熱軋條帶中可能要求不同的機(jī)械性能,以生產(chǎn)具有不同機(jī)械性能的連續(xù)管。隨著性能的提高,生產(chǎn)成本進(jìn)而原材料成本也增加。已知的是,在“長(zhǎng)條帶”的組裝過(guò)程中使用的條帶到條帶焊接過(guò)程會(huì)使得連接區(qū)域劣化,其中該“長(zhǎng)條帶”將被ERW成型/焊接為連續(xù)管。此后,具有改進(jìn)性能的連續(xù)管在條帶焊接區(qū)域傾向于具有相對(duì)較低的性能。該劣化由這樣的事實(shí)引起,即焊接過(guò)程破壞了在熱軋過(guò)程中引入的細(xì)化,且沒(méi)有簡(jiǎn)單的焊后熱處理能夠再生拉伸和韌性性能。通常,拉伸得以恢復(fù),而韌性及其相關(guān)的疲勞壽命在該區(qū)域中劣化。當(dāng)今的工業(yè)路線可以生產(chǎn)高強(qiáng)度的連續(xù)管,但只在提高的成本下,且條帶焊接接頭相對(duì)于管體具有較差的性能。用于生產(chǎn)連續(xù)管的一種選擇是通過(guò)整體的熱處理。該處理運(yùn)用于已經(jīng)形成為管的處于所謂的“未處理(green)”狀態(tài)的材料上,因?yàn)槠湫阅苓€需要通過(guò)熱處理?xiàng)l件來(lái)定義。在這種情形下,影響最終產(chǎn)品性能的主要變量是鋼化學(xué)成分和熱處理?xiàng)l件。此后,通過(guò)合適地組合鋼成分與焊接材料和熱處理,可以生產(chǎn)在長(zhǎng)度上具有均勻性能的連續(xù)管,而排除了條帶到條帶連接的薄弱環(huán)節(jié),這樣的條帶到條帶連接在高強(qiáng)度的現(xiàn)有連續(xù)管上是關(guān)鍵的。這個(gè)一般概念已經(jīng)在以前描述,但是從未成功地應(yīng)用于高強(qiáng)度連續(xù)管(屈服強(qiáng)度在從80到140ksi的范圍中)的生產(chǎn)。其理由是,在(獲得高生產(chǎn)率所需的)升高的線速度下,熱處理通常導(dǎo)致需要復(fù)雜和延伸的設(shè)施。如果選擇專用的化學(xué)成分和處理?xiàng)l件,可以簡(jiǎn)化該過(guò)程。選擇與合理尺寸的工業(yè)熱處理設(shè)施兼容的化學(xué)成分要求理解影響測(cè)量到的連續(xù)管性能的許多變量,例如:a)軸向機(jī)械性能;b)微結(jié)構(gòu)的均勻性和性能;c)韌性;d)耐疲勞性;e)耐酸性,等等。
技術(shù)實(shí)現(xiàn)要素:下面描述設(shè)計(jì)用于生產(chǎn)熱處理連續(xù)管的化學(xué)成分,其大部分在API5ST標(biāo)準(zhǔn)設(shè)定的連續(xù)管當(dāng)前限定之外。(Max.C:0.16%,Max.Mn:1.2%(CT70-90)Max.Mn:1.65(CT100-110),Max.P:0.02%(CT70-90)Max.P:0.025(CT100-CT110),Max.S:0.005,Si.Max:0.5)。本發(fā)明的實(shí)施方式涉及鋼連續(xù)管(coiledsteeltube)及其生產(chǎn)方法。在一些實(shí)施方式中,該管可以具有大于大約80ksi的屈服強(qiáng)度。該管的成分可以包括0.16-0.35重量%的碳、0.30-2.00重量%的錳、0.10-0.35重量%的硅、多至0.005重量%的硫、多至0.018重量%的磷,余量為鐵和不可避免的雜質(zhì)。該管還包括最終微結(jié)構(gòu),該最終微結(jié)構(gòu)包括回火馬氏體和貝氏體的混合物,其中連續(xù)管的最終微結(jié)構(gòu)包括多于90體積%的回火馬氏體,其中該微結(jié)構(gòu)在管體、ERW線和條帶端對(duì)端連接中是均質(zhì)的。這里公開(kāi)的是由多個(gè)焊接條帶形成的鋼連續(xù)管,其中該管可以包括基礎(chǔ)金屬區(qū)域、焊接連接及其熱影響區(qū),并可以具有大于大約80ksi的屈服強(qiáng)度,包括鐵和0.17-0.35重量%的碳、0.30-2.00重量%的錳、0.10-0.30重量%的硅、0.010-0.040重量%的鋁、多至0.010重量%的硫和多至0.015重量%的磷的成分,和最終微結(jié)構(gòu),該最終微結(jié)構(gòu)包括回火馬氏體和貝氏體的混合物,其中連續(xù)管的最終微結(jié)構(gòu)在基礎(chǔ)金屬區(qū)域、焊接連接和熱影響區(qū)中包括多于90體積%的回火馬氏體,其中該最終微結(jié)構(gòu)在所有基礎(chǔ)金屬區(qū)域、焊接連接和熱影響區(qū)中是均質(zhì)的,和其中該最終微結(jié)構(gòu)在基礎(chǔ)金屬區(qū)域、焊接連接和熱影響區(qū)中包括精細(xì)碳化物的均勻分布。在一些實(shí)施方式中,該成分還包括多至1.0重量%的鉻、多至0.5重量%的鉬、多至0.0030重量%的硼、多至0.030重量%的鈦、多至0.50重量%的銅、多至0.50重量%的鎳、多至0.1重量%的鈮、多至0.15重量%的釩、多至0.0050重量%的氧,和多至0.05重量%的鈣。在一些實(shí)施方式中,該成分包括:0.17到0.30重量%的碳、0.30到1.60重量%的錳、0.10到0.20重量%的硅、多至0.7重量%的鉻、多至0.5重量%的鉬、0.0005到0.0025重量%的硼、0.010到0.025重量%的鈦、0.25到0.35重量%的銅、0.20到0.35重量%的鎳、多至0.04重量%的鈮、多至0.10重量%的釩、多至0.0015重量%的氧、多至0.03重量%的鈣、多至0.003重量%的硫,和多至0.010重量%的磷。在一些實(shí)施方式中,該管可以具有125ksi的最小屈服強(qiáng)度。在一些實(shí)施方式中,該管可以具有140ksi的最小屈服強(qiáng)度。在一些實(shí)施方式中,該管可以具有在125ksi到140ksi之間的最小屈服強(qiáng)度。在一些實(shí)施方式中,該最終微結(jié)構(gòu)在基礎(chǔ)金屬區(qū)域、焊接連接和熱影響區(qū)中可以包括至少95體積%的回火馬氏體。在一些實(shí)施方式中,該管在基礎(chǔ)金屬區(qū)域、焊接連接和熱影響區(qū)中可以具有20μm以下的最終晶粒尺寸。在一些實(shí)施方式中,該管在基礎(chǔ)金屬區(qū)域、焊接連接和熱影響區(qū)中可以具有15μm以下的最終晶粒尺寸。在一些實(shí)施方式中,所述焊接連接可以包括斜焊(biasweld)。在一些實(shí)施方式中,在斜焊處的疲勞壽命可以是基礎(chǔ)金屬區(qū)域的至少大約80%。在一些實(shí)施方式中,焊接連接包括其熱影響區(qū)的百分比硬度可以是基礎(chǔ)金屬硬度的110%或更小。這里還公開(kāi)了形成鋼連續(xù)管的方法,其包括:提供條帶,該條帶具有包括鐵和0.17-0.35重量%的碳、0.30-2.00重量%的錳、0.10-0.30重量%的硅、0.010-0.040重量%的鋁、多至0.010重量%的硫,和多至0.015重量%的磷的成分;和將所述條帶焊接在一起,由焊接條帶形成管,其中該管包括基礎(chǔ)金屬區(qū)域、連接焊接和它們的熱影響區(qū);在900-1000℃之間奧氏體化該管;淬火該管以形成馬氏體和貝氏體的最終淬火態(tài)微結(jié)構(gòu)(asquenchedmicrostructure),其中該淬火態(tài)微結(jié)構(gòu)在基礎(chǔ)金屬區(qū)域、焊接連接和熱影響區(qū)中包括至少90%的馬氏體,和在550-720℃之間對(duì)該淬火的管進(jìn)行回火,其中對(duì)淬火的管進(jìn)行回火產(chǎn)生大于大約80ksi的屈服強(qiáng)度,其中在所有基礎(chǔ)金屬區(qū)域、焊接連接和熱影響區(qū)中的微結(jié)構(gòu)是均質(zhì)的,和其中該微結(jié)構(gòu)在基礎(chǔ)金屬區(qū)域、焊接連接和熱影響區(qū)中包括精細(xì)碳化物的均勻分布。在一些實(shí)施方式中,焊接所述條帶可以包括斜焊。在一些實(shí)施方式中,形成該管可以包括形成線連接(linejoint)。在一些實(shí)施方式中,該方法還可以包括在卷軸上卷繞回火的管。在一些實(shí)施方式中,奧氏體化可以在基礎(chǔ)金屬區(qū)域、焊接連接和熱影響區(qū)中形成小于20μm的晶粒尺寸。在一些實(shí)施方式中,該成分還可以包括:多至1.0重量%的鉻、多至0.5重量%的鉬、多至0.0030重量%的硼、多至0.030重量%的鈦、多至0.50重量%的銅、多至0.50重量%的鎳、多至0.1重量%的鈮、多至0.15重量%的釩、多至0.0050重量%的氧,和多至0.05重量%的鈣。在一些實(shí)施方式中,該成分可以包括:0.17到0.30重量%的碳、0.30到1.60重量%的錳、0.10到0.20重量%的硅、多至0.7重量%的鉻、多至0.5重量%的鉬、0.0005到0.0025重量%的硼、0.010到0.025重量%的鈦、0.25到0.35重量%的銅、0.20到0.35重量%的鎳、多至0.04重量%的鈮、多至0.10重量%的釩、多至0.00015重量%的氧、多至0.03重量%的鈣、多至0.003重量%的硫,和多至0.010重量%的磷。在一些實(shí)施方式中,該回火的管可以具有大于或等于125ksi的屈服強(qiáng)度。在一些實(shí)施方式中,該回火的管可以具有140ksi的最小屈服強(qiáng)度。在一些實(shí)施方式中,該回火的管可以具有在125ksi到140ksi之間的最小屈服強(qiáng)度。附圖說(shuō)明圖1A-B示例了對(duì)應(yīng)于STD2(A)和STD3(B)鋼的CCT圖。圖2A-B示例了對(duì)應(yīng)于BTi2(A)和CrMoBTi3(B)鋼的CCT圖。圖3示例了在內(nèi)管表面的冷卻速率,其是壁厚(WT)的函數(shù),用于在噴水下從外部淬火的連續(xù)管。圖4示例了BTi2鋼的拉伸性能,其是最大回火溫度(Tmax)的函數(shù)。峰狀回火循環(huán)用于這些仿真。(右側(cè))720℃處,作為保持時(shí)間的函數(shù)的相同鋼的拉伸性能(等溫回火循環(huán))。圖5A-B示例了在焊縫退火(seamannealing)(PWHT)后,出現(xiàn)在靠近ERW線的中心偏析帶處的未回火的馬氏體。圖5A-B對(duì)應(yīng)于常規(guī)的連續(xù)管等級(jí)90(Grade90)。圖6A-B示例了在等級(jí)110連續(xù)管的疲勞測(cè)試過(guò)程中產(chǎn)生的在中心偏析帶處的局部損壞。圖7A-B示例了等級(jí)100連續(xù)管在具有高的內(nèi)部壓力(9500psi)下的疲勞測(cè)試過(guò)程中產(chǎn)生的在中心偏析帶處的局部損壞。圖8A-B示例了基礎(chǔ)金屬微結(jié)構(gòu),其對(duì)應(yīng)于標(biāo)準(zhǔn)連續(xù)管(A)和通過(guò)本發(fā)明的實(shí)施方式制造的連續(xù)管(B)。在兩種情形下,連續(xù)管都具有對(duì)應(yīng)于等級(jí)110的拉伸性能(從110Ksi到120Ksi的屈服強(qiáng)度)。圖9A-B示例了ERW線微結(jié)構(gòu),其對(duì)應(yīng)于標(biāo)準(zhǔn)連續(xù)管(A)和通過(guò)本發(fā)明的實(shí)施方式制造的連續(xù)管(B)。在兩種情形下,連續(xù)管拉伸性能都對(duì)應(yīng)于等級(jí)110(從110Ksi到120Ksi的屈服強(qiáng)度)。圖10A-B示例了對(duì)應(yīng)于ERW的HAZ的微結(jié)構(gòu),用于標(biāo)準(zhǔn)連續(xù)管(A)和通過(guò)本發(fā)明的實(shí)施方式制造的連續(xù)管(B)。在兩種情形下,連續(xù)管拉伸性能都對(duì)應(yīng)于等級(jí)110(從110Ksi到120Ksi的屈服強(qiáng)度)。圖11A-B示例了對(duì)應(yīng)于斜焊的HAZ的微結(jié)構(gòu),用于標(biāo)準(zhǔn)連續(xù)管(A)和通過(guò)本發(fā)明的實(shí)施方式制造的連續(xù)管(B)。在兩種情形下,連續(xù)管拉伸性能都對(duì)應(yīng)于等級(jí)110(從110Ksi到120Ksi的屈服強(qiáng)度)。圖12示例了使用過(guò)程中在斜焊的融合區(qū)中形成的裂紋(從內(nèi)管面生長(zhǎng))。該裂紋處于大的上貝氏體條的方向上。圖13示例了通過(guò)現(xiàn)有過(guò)程和根據(jù)本發(fā)明的實(shí)施方式的過(guò)程獲得的典型斜焊上的硬度的變化(基礎(chǔ)金屬硬度=100%)。融合區(qū)(FZ,fusionzone)近似地位于在距焊接中心≈+/-5mm之間的區(qū)域中。圖14A-B示例了微結(jié)構(gòu),其對(duì)應(yīng)于在斜焊和ERW線之間的交叉處,用于標(biāo)準(zhǔn)連續(xù)管(A)和通過(guò)本發(fā)明的實(shí)施方式制造的連續(xù)管(B)。在兩種情形下,連續(xù)管拉伸性能都對(duì)應(yīng)于等級(jí)110(從110Ksi到120Ksi的屈服強(qiáng)度)。圖15示例了疲勞測(cè)試機(jī)的示意圖。圖16示例了為BW樣品測(cè)量的疲勞壽命,相對(duì)于對(duì)應(yīng)于BM樣品的那些。結(jié)果是在不同測(cè)試條件和連續(xù)管等級(jí)下的平均值(對(duì)于現(xiàn)有管是80、90和110,對(duì)于根據(jù)本發(fā)明生產(chǎn)的連續(xù)管是80、90、110、125和140)。圖17示例了根據(jù)本發(fā)明的化學(xué)成分和處理?xiàng)l件的實(shí)施方式生產(chǎn)的連續(xù)管疲勞壽命的改進(jìn)。該改進(jìn)取決于與類似條件下相同等級(jí)的現(xiàn)有連續(xù)管測(cè)量得到的疲勞壽命的比較。結(jié)果在不同測(cè)試條件下對(duì)每個(gè)等級(jí)進(jìn)行平均。在非標(biāo)準(zhǔn)的等級(jí)125和140的情形下,疲勞壽命比較是針對(duì)等級(jí)110中的STD3進(jìn)行的。圖18A-B示例了在根據(jù)NACETM0177(90%SMYS,方案A,1barH2S)測(cè)試材料等級(jí)80之后的C環(huán)樣品。A:現(xiàn)有過(guò)程;B:本發(fā)明公開(kāi)的實(shí)施方式。具體實(shí)施方式在鋼廠生產(chǎn)出作為熱軋條帶的連續(xù)管原材料。控制的軋制用于通過(guò)微結(jié)構(gòu)細(xì)化保證高強(qiáng)度和良好的韌性。條帶縱向切割到用于管的生產(chǎn)的寬度,然后通過(guò)連接過(guò)程(例如等離子弧焊或攪拌摩擦焊)端對(duì)端地接合,以形成更長(zhǎng)的條帶。此后,采用ERW過(guò)程形成管。最終的產(chǎn)品性能根據(jù)下述測(cè)量:a)軸向機(jī)械性能,b)微結(jié)構(gòu)和性能的均勻性,c)韌性,d)耐疲勞性,e)耐酸性,等等。采用現(xiàn)有的處理路線,連續(xù)管機(jī)械性能通過(guò)熱軋條帶性能和在焊接操作和管形成過(guò)程中引入的改變的組合而獲得。這樣獲得的性能在連續(xù)管性能如上所列那樣測(cè)量時(shí)受到限制。理由是用于連接條帶的焊接過(guò)程這樣改變了細(xì)化的軋制的微結(jié)構(gòu),即使采用了焊后熱處理,最終的性能仍然受損。減少的疲勞壽命和差的耐酸性能與微結(jié)構(gòu)中的不均勻性和焊接上脆弱的組分相關(guān)。已經(jīng)提議,新的路線至少應(yīng)包括整體熱處理。該路線已經(jīng)被概括地描述,但是從未具體化。本發(fā)明描述了化學(xué)成分和原材料特性,其與合適的焊接過(guò)程以及熱處理?xiàng)l件結(jié)合,將產(chǎn)生經(jīng)淬火和回火的產(chǎn)品,該產(chǎn)品在管體和條帶連接焊接中都具有高的性能。該材料設(shè)計(jì)用于連續(xù)管,這樣的選擇不僅是因?yàn)橄鄬?duì)成本,而且優(yōu)選地是為了最大化應(yīng)用于連續(xù)管操作的特殊條件下的疲勞壽命(在同時(shí)發(fā)生軸向負(fù)載和內(nèi)部壓力下彎曲的低周疲勞)。本發(fā)明涉及高強(qiáng)度連續(xù)管(最小屈服強(qiáng)度從80ksi到140ksi),其與通過(guò)API5ST限定的標(biāo)準(zhǔn)產(chǎn)品相比具有增加的低周疲勞壽命。此外,抗硫化物應(yīng)力開(kāi)裂(SSC,SulfideStressCracking)性也在本發(fā)明中提高。性能的這種出色組合通過(guò)鋼化學(xué)成分和處理?xiàng)l件的合適選擇而獲得。工業(yè)過(guò)程不同于整體熱處理(FBHT,F(xiàn)ullBodyHeatTreatment)應(yīng)用中的標(biāo)準(zhǔn)路線,該過(guò)程在美國(guó)申請(qǐng)US2012/0186686A1中公開(kāi)。該FBHT是在連續(xù)管通過(guò)ERW(ElectricalResistanceWelding,電阻焊接)形成之后進(jìn)行的,并包括至少一個(gè)周期的奧氏體化、淬火和回火。上述公開(kāi)更特別地涉及鋼化學(xué)成分和處理參數(shù),以生產(chǎn)具有上述性能的淬火和回火的連續(xù)管。盡管通過(guò)對(duì)具有給定成分的基礎(chǔ)材料進(jìn)行熱處理產(chǎn)生某些機(jī)械性能是一般知識(shí)的一部分,但是用于連續(xù)管的特殊應(yīng)用采用具有特殊化學(xué)成分的原材料,以最小化特殊變量的有害作用,例如在本發(fā)明的特殊性能上的偏析模式(segregationpattern)。對(duì)于連續(xù)管最重要的一個(gè)性能是提高的耐低周疲勞性。這是因?yàn)樵跇?biāo)準(zhǔn)的現(xiàn)場(chǎng)操作過(guò)程中,連續(xù)管頻繁地卷起和展開(kāi),引入周期的塑性變形,這最終將產(chǎn)生破壞。在低周疲勞過(guò)程中,在較軟的材料區(qū)域中,變形偏向于位于微觀尺度處。當(dāng)脆化組分(brittleconstituents)出現(xiàn)在這些應(yīng)變集中區(qū)域處或其附近時(shí),裂紋可以容易地成核并擴(kuò)展。因此,疲勞壽命的減少與不均勻的微結(jié)構(gòu)(具有較軟的區(qū)域,其中局部變形)和脆化組分(其成核和/或擴(kuò)展裂紋)相關(guān)。所有這些微結(jié)構(gòu)特征出現(xiàn)在焊接的熱影響區(qū)(HAZ,HeatAffectedZone)。具有一些類型的管體微結(jié)構(gòu),其也具有上述特征。這是因?yàn)樗鼈儼ㄓ驳暮蛙浀慕M分的混合物,例如鐵素體、珠光體和貝氏體。在這種情形下,應(yīng)變局限于較軟的鐵素體中,靠近貝氏體的邊界,其中裂紋成核并擴(kuò)展。高強(qiáng)度的連續(xù)管現(xiàn)在具有這類微結(jié)構(gòu)。為了避免在低周疲勞過(guò)程中應(yīng)變局部化,微結(jié)構(gòu)必須不僅在整個(gè)管體和連接上都均勻,而且是在微觀尺度下如此。對(duì)于低碳鋼,包括回火的馬氏體的微結(jié)構(gòu)是理想的,其基本上是鐵素體基質(zhì),具有均勻和精細(xì)的碳化物分布。其后,本發(fā)明描述的化學(xué)成分選擇和處理?xiàng)l件的目的在于通過(guò)FBHT實(shí)現(xiàn)均勻的微結(jié)構(gòu)(在管體、斜焊和ERW線中),其包括至少90%的回火馬氏體,優(yōu)選地多于95%的回火馬氏體。此外,回火馬氏體更適合于產(chǎn)生比標(biāo)準(zhǔn)連續(xù)管微結(jié)構(gòu)(包括鐵素體、珠光體和貝氏體)高的超高強(qiáng)度等級(jí),為此,需要十分昂貴的合金添加劑,以達(dá)到高于大約125Ksi的屈服強(qiáng)度。當(dāng)與含有貝氏體的結(jié)構(gòu)比較時(shí),回火馬氏體的其他重要好處在于其改進(jìn)的抗SSC性。鋼化學(xué)成分已經(jīng)定義為最適合于采用FBHT生產(chǎn)熱處理連續(xù)管,并可以描述為碳(重量%C),錳(重量%Mn),硅(重量%Si),鉻(重量%Cr),鉬(重量%Mo)和微合金元素,例如硼(重量%B),鈦(重量%Ti),鋁(重量%Al),鈮(重量%Nb)和釩(重量%V)的含量。另外,上限可能在于不可避免的雜質(zhì)上,例如硫(重量%S),磷(重量%P)和氧(重量%O)。為了生產(chǎn)包括回火馬氏體的最終結(jié)構(gòu),本發(fā)明的鋼化學(xué)成分主要不同于連續(xù)管的現(xiàn)有技術(shù),因?yàn)槠渚哂休^高的碳含量(例如參見(jiàn)API5ST,其中連續(xù)管允許的最大碳含量是0.16%),這允許通過(guò)包括至少一個(gè)周期的奧氏體化、淬火和回火的FBHT來(lái)獲得想要的微結(jié)構(gòu)。這里使用的術(shù)語(yǔ)“幾乎”、“大約”和“基本上”表示接近所述量的量,但仍然執(zhí)行想要的功能或?qū)崿F(xiàn)想要的結(jié)果。例如,術(shù)語(yǔ)“幾乎”、“大約”和“基本上”可以指在所述量的小于10%內(nèi)、小于5%內(nèi)、小于1%內(nèi)、小于0.1%內(nèi)和小于0.01%內(nèi)。碳是這樣的元素,通過(guò)在熱處理過(guò)程中提高可淬硬性和促進(jìn)碳化物沉淀,其不昂貴的添加增加了鋼的強(qiáng)度。如果碳減少到0.17%以下,可淬硬性不能夠保證,在熱處理過(guò)程中可能形成大的貝氏體片段。貝氏體的外形使其難以達(dá)到具有想要的疲勞壽命和抗SSC性的80ksi以上的屈服強(qiáng)度。當(dāng)前的連續(xù)管路線不適于熱處理,因?yàn)锳PI5ST所允許的最大碳含量是0.16%。現(xiàn)有的連續(xù)管的微結(jié)構(gòu)呈現(xiàn)大的貝氏體片段,其在更高強(qiáng)度等級(jí)削弱了韌性、疲勞壽命和抗SSC性,也即連續(xù)管具有在110Ksi以上的最小屈服強(qiáng)度。另一方面,具有大于0.35%的碳的鋼將具有差的可焊性,在焊接和焊接后熱處理操作中容易出現(xiàn)脆化組分和裂紋。此外,較高的碳含量可能導(dǎo)致淬火后大量保留的奧氏體,其隨著回火而轉(zhuǎn)變?yōu)榇嗷M分。這些脆化組分削弱了疲勞壽命和抗SSC性。因此,鋼成分的C含量在從大約0.17%到大約0.35%的范圍內(nèi)變化,優(yōu)選地是從大約0.17%到大約0.30%。錳的添加提高了可淬硬性和強(qiáng)度。Mn也有助于在制鋼過(guò)程中去氧和硫控制。如果Mn含量小于大約0.30%,其可能難以獲得想要的強(qiáng)度水平。然而,當(dāng)Mn含量增加時(shí),可以形成大的偏析模式。在熱處理過(guò)程中,Mn偏析區(qū)域?qū)A向于形成脆化組分,這將削弱韌性并減少疲勞壽命。此外,這些偏析區(qū)域增加了材料對(duì)硫化物應(yīng)力開(kāi)裂(SSC)的敏感性。相應(yīng)地,在采用改進(jìn)的抗SSC性的應(yīng)用中,鋼成分的Mn含量在從0.30%到2.0%的范圍內(nèi)變化,優(yōu)選地從0.30%到1.60%,更優(yōu)選地從0.30%到0.80%。硅是這樣的元素,其的添加在制鋼過(guò)程中具有脫氧作用,還增加了鋼的強(qiáng)度。在一些實(shí)施方式中,如果Si超出大約0.30%,韌性可能下降。此外,可能形成大的偏析模式。因此,鋼成分的Si含量在大約0.10%到0.30%之間的范圍內(nèi)變化,優(yōu)選地在大約0.10%到大約0.20%的范圍內(nèi)。鉻的添加增加了鋼的可淬硬性和回火穩(wěn)定性。Cr可以用于部分地替換鋼成分中的Mn,以實(shí)現(xiàn)高的強(qiáng)度而不產(chǎn)生大的偏析模式,該偏析模式將削弱疲勞壽命和抗SSC性。然而,Cr是昂貴的添加劑,且因?yàn)槠鋵?duì)熱成形負(fù)載的作用,使得連續(xù)管更難以生產(chǎn)。因此,在一些實(shí)施方式中,Cr限制到大約1.0%,優(yōu)選地到大約0.7%。鉬是這樣的元素,其的添加對(duì)于增加鋼的強(qiáng)度是有效的,還有助于在回火過(guò)程中延遲軟化。對(duì)回火穩(wěn)定性允許在減少M(fèi)n含量下生產(chǎn)高強(qiáng)度的鋼,增加了疲勞壽命和抗SSC性。Mo添加劑還可以減小磷到晶粒邊界的偏析,改進(jìn)了抗晶粒間破裂性。然而,該鐵合金是昂貴的,使其需要減小鋼成分內(nèi)的最大Mo含量。因此,在某些實(shí)施方式中,最大的Mo是大約0.5%。硼是這樣的元素,其的添加對(duì)于改進(jìn)鋼的可淬硬性非常有效。例如,通過(guò)抑制鐵素體在淬火過(guò)程中形成,B可以提高可淬硬性。在一些實(shí)施方式中,B用于實(shí)現(xiàn)鋼中良好的可淬硬性(也即作為包括至少90%馬氏體的淬火結(jié)構(gòu)),通過(guò)Mn含量的減少提高疲勞壽命和抗SSC性。如果B含量小于大約0.0005重量%,在這些實(shí)施方式中可能難以獲得鋼想要的可淬硬性。然而,如果B含量過(guò)高,粗的碳化硼可能形成在晶粒邊界處,負(fù)面地影響韌性。相應(yīng)地,在一個(gè)實(shí)施方式中,在該成分中,B的含量低于大約0.0030%,在另一個(gè)實(shí)施方式中,B的含量從大約0.0005%到0.0025%。鈦是這樣的元素,通過(guò)將氮雜質(zhì)固定為氮化鈦(TiN)并抑制氮化硼的形成,其的添加對(duì)于提高鋼中B的作用是有效的。如果Ti含量太低,在一些實(shí)施方式中可能難以獲得硼對(duì)于鋼的可淬硬性的想要的作用。另一方面,如果Ti含量高于0.03重量%,粗的氮化鈦和碳化物(TiN和TiC)可能形成,負(fù)面地影響延展性和韌性。相應(yīng)地,在某些實(shí)施方式中,Ti的含量可以限制到大約0.030%。在其他實(shí)施方式中,Ti的含量可以在從大約0.010%到大約0.025%的范圍內(nèi)??紤]到低機(jī)械性能的連續(xù)管的生產(chǎn)受益于低回火穩(wěn)定性,B和Ti添加劑改進(jìn)了可淬硬性而不增加回火穩(wěn)定性。其后,其允許80ksi等級(jí)的生產(chǎn)而在回火過(guò)程中沒(méi)有顯著大的均熱時(shí)間,從而提高了生產(chǎn)率。由于連續(xù)管生產(chǎn)在熱處理線中的一個(gè)限制是線的長(zhǎng)度,以在回火過(guò)程中對(duì)材料進(jìn)行充分的均熱,B和Ti的使用特別地涉及低屈服強(qiáng)度連續(xù)管的生產(chǎn)。銅在鋼成分的某些實(shí)施方式中不是必需的元素。然而,在一些連續(xù)管應(yīng)用中,Cu可能需要用于改進(jìn)耐大氣腐蝕性。這樣,在某些實(shí)施方式中,鋼成分的Cu含量可以限制于或小于大約0.50%。在其他實(shí)施方式中,Cu含量在從大約0.25%到大約0.35%的范圍內(nèi)。鎳是這樣的元素,其的添加增加了鋼的強(qiáng)度和韌性。如果Cu添加到鋼成分中,Ni可以用于避免已知為熱脆性(hotshortness)的熱軋缺陷。然而,Ni非常昂貴,在某些實(shí)施方式中,鋼成分的Ni含量限制于或小于或等于大約0.50%。在其他實(shí)施方式中,Ni的含量可以在從大約0.20%到大約0.35%的范圍內(nèi)。鈮是這樣的元素,其到鋼成分的添加可以在對(duì)奧氏體區(qū)域再加熱的過(guò)程中細(xì)化鋼的奧氏體晶粒尺寸。Nb還可以在回火過(guò)程中沉淀,通過(guò)顆粒彌散硬化而增加鋼的強(qiáng)度。在一個(gè)實(shí)施方式中,鋼成分的Nb含量可以在大約0%到大約0.10%之間的范圍內(nèi)變化,有效地在大約0%到大約0.04%的范圍內(nèi)。釩是這樣的元素,通過(guò)在回火過(guò)程中碳化物的沉淀,其的添加可以用于提高鋼的強(qiáng)度。然而如果鋼成分的V含量大于大約0.15%,可能形成大體積的碳化釩晶粒,伴隨著鋼韌性的減小。由此,在某些實(shí)施方式中,鋼的V含量限制于大約0.15%,優(yōu)選地大約0.10%。鋁是這樣的元素,其到鋼成分的添加在制鋼過(guò)程中具有脫氧作用,并進(jìn)一步細(xì)化鋼的晶粒尺寸。在一個(gè)實(shí)施方式中,如果鋼成分的Al含量小于大約0.010%,鋼可能易受氧化影響,展現(xiàn)出高水平的夾雜物。在其他實(shí)施方式中,如果鋼成分的Al含量大于大約0.040%,可能形成粗的沉淀物,這將削弱鋼的韌性。因此,鋼成分的Al含量可以在大約0.010%到大約0.040%的范圍內(nèi)變化。硫是這樣的元素,其引起鋼的韌性和可加工性下降。相應(yīng)地,在一些實(shí)施方式中,鋼成分的S含量限制于最大大約0.010%,優(yōu)選地大約0.003%。磷是這樣的元素,其引起鋼韌性的下降。相應(yīng)地,鋼成分的P含量限制于最大大約0.015%,優(yōu)選地大約0.010%。氧可以是在鋼成分內(nèi)的雜質(zhì),其主要以氧化物的形式出現(xiàn)。在鋼成分的實(shí)施方式中,當(dāng)O含量增加時(shí),鋼的沖擊性能被削弱。相應(yīng)地,在鋼成分的某些實(shí)施方式中,想要相對(duì)低的O含量,小于或等于大約0.0050重量%,優(yōu)選地小于或等于大約0.0015重量%。鈣是這樣的元素,其到鋼成分的添加通過(guò)改變硫化夾雜物的形狀而改進(jìn)韌性。在一個(gè)實(shí)施方式中,鋼成分可以包括Ca/S>1.5的Ca對(duì)S的最小含量比。在鋼成分的其他實(shí)施方式中,過(guò)多的Ca是不必要的,鋼成分可以包括最大大約0.05%的Ca含量,優(yōu)選地大約0.03%。不可避免的雜質(zhì),包括但是不限于N、Pb、Sn、As、Sb、Bi等,其含量?jī)?yōu)選地保持為盡可能地低。然而,假如這些雜質(zhì)保持在選擇的水平之下,根據(jù)本發(fā)明的鋼成分的實(shí)施方式形成的鋼的性能(例如強(qiáng)度、韌性)可以基本上不削弱。在一個(gè)實(shí)施方式中,鋼成分的N含量可以小于大約0.010%,優(yōu)選地小于或等于0.008%。在另一個(gè)實(shí)施方式中,鋼成分的Pb含量可以小于或等于大約0.005%。在其他實(shí)施方式中,鋼成分的Sn含量可以小于或等于大約0.02%。在其他實(shí)施方式中,鋼成分的As含量可以小于或等于大約0.012%。在另一個(gè)實(shí)施方式中,鋼成分的Sb含量可以小于或等于大約0.008%。在其他實(shí)施方式中,鋼成分的Bi含量可以小于而等于大約0.003%。本發(fā)明的特定鋼化學(xué)成分的選擇將根據(jù)最終產(chǎn)品規(guī)格和工業(yè)設(shè)施約束(例如在感應(yīng)熱處理線中,難以在回火過(guò)程中獲得大的均熱時(shí)間)??赡軙r(shí),Mn的添加將減少,因?yàn)槠渫ㄟ^(guò)形成大的偏析模式而削弱疲勞壽命和抗SSC性。Cr和較小含量的Mo將用于取代Mn,整體熱處理將保持為盡可能的簡(jiǎn)單。這兩種元素都增加了碳化物穩(wěn)定性和耐軟化性,其將導(dǎo)致回火過(guò)程中大的均熱時(shí)間。其后,這些元素優(yōu)選地用于更高的強(qiáng)度等級(jí)(例如等級(jí)110和更高),其中想要回火穩(wěn)定性,并在較低的等級(jí)(等級(jí)80)中避免,其中需要長(zhǎng)的和不切實(shí)際的工業(yè)熱處理線。在較低等級(jí)(等級(jí)80)的情形下,優(yōu)選地是B和Ti微合金添加劑與合適的C含量組合。這些元素允許獲得良好的可淬硬性而不使用高的Mn添加劑。而且,B和Ti不增加回火穩(wěn)定性。其后,簡(jiǎn)單和短的回火處理可以用于實(shí)現(xiàn)想要的強(qiáng)度水平。對(duì)應(yīng)于本發(fā)明的工業(yè)處理方法在下面的段落中描述,其集中于整體熱處理(FBHT)條件。用于連續(xù)管的原材料在鋼廠生產(chǎn)為具有可以從大約0.08英寸到大約0.30英寸變化的壁厚的熱軋條帶??刂频能堉瓶梢杂射摴?yīng)者用于細(xì)化軋態(tài)微結(jié)構(gòu)(asrolledmicrostructure)。然而,軋態(tài)條帶的重要的微結(jié)構(gòu)細(xì)化是不需要的,因?yàn)樵诒景l(fā)明中,微結(jié)構(gòu)和機(jī)械性能主要通過(guò)最終的FBHT限定。在熱軋?zhí)幚碇械脑撿`活性有助于減少原材料成本,允許采用鋼化學(xué)成分,所述鋼化學(xué)成分在可以使用復(fù)雜的熱軋過(guò)程時(shí)不能使用(通常,控制的軋制可以僅用于低碳微合金鋼中)。鋼條帶縱向切割為用于管生產(chǎn)的寬度。其后,條帶通過(guò)焊接過(guò)程端對(duì)端地連接(例如等離子弧焊或攪拌摩擦焊),以形成更長(zhǎng)的條帶,允許獲得管的長(zhǎng)度。這些焊接的條帶例如通過(guò)ERW過(guò)程形成為管。典型的連續(xù)管外徑在1英寸和5英寸之間。管長(zhǎng)度為大約15000英尺,但是長(zhǎng)度可以在大約10000英尺到大約40000英尺之間。在形成管后,采用整體熱處理(FBHT)。熱處理的目的在于生產(chǎn)均勻的最終微結(jié)構(gòu),其包括至少90%的回火馬氏體,其余為貝氏體。該微結(jié)構(gòu),其具有均勻的碳化物分布和在20μm以下、優(yōu)選地15μm以下的晶粒尺寸,保證了強(qiáng)度、延展性、韌性和低周疲勞壽命的良好組合。而且,如前所述,通過(guò)合適地選擇鋼化學(xué)成分,與現(xiàn)有結(jié)構(gòu)相比,其中包括鐵素體、珠光體和大體積百分率的上貝氏體,該類微結(jié)構(gòu)適合于改進(jìn)抗硫化物應(yīng)力開(kāi)裂(SSC)性。FBHT包括跟隨有回火處理(T)的至少一個(gè)奧氏體化和淬火循環(huán)(Q)。奧氏體化在900℃和1000℃之間的溫度下進(jìn)行。在該階段中,在平衡溫度Ae3以上的總的持續(xù)時(shí)間應(yīng)當(dāng)選擇為保證鐵碳化物完全分解而沒(méi)有多余的奧氏體晶粒生長(zhǎng)。目標(biāo)晶粒尺寸在20μm以下,優(yōu)選地在15μm以下。必須進(jìn)行淬火,控制最小冷卻速率,以獲得最終的淬火態(tài)微結(jié)構(gòu),其在整個(gè)管中包括至少90%的馬氏體。回火在550℃和720℃之間的溫度下進(jìn)行。在720℃之上的熱處理可以導(dǎo)致部分馬氏體轉(zhuǎn)變?yōu)楦咛紛W氏體。該組分必須避免,因?yàn)槠鋬A向于轉(zhuǎn)變?yōu)榇嗷M分,這可能削弱韌性和疲勞壽命。另一方面,如果回火在550℃以下進(jìn)行,位錯(cuò)的淬火態(tài)結(jié)構(gòu)的恢復(fù)過(guò)程沒(méi)有完成。其后,韌性可能再次大大地減小?;鼗鹧h(huán)必須選擇在上述溫度范圍內(nèi),以獲得想要的機(jī)械性能。最小的屈服強(qiáng)度可以從80ksi變化為140ksi。在溫度下的合適的持續(xù)時(shí)間必須選擇為保證在基礎(chǔ)管和焊接區(qū)域中(ERW線和條帶到條帶連接)均勻的碳化物分布。在一些情形下,為了提高強(qiáng)度和韌性的組合,可能需要進(jìn)行多于一次的奧氏體化、淬火和回火循環(huán)。在FBHT之后,管可以經(jīng)受定尺寸過(guò)程,以保證指定的尺寸容差、應(yīng)力釋放,并卷繞成卷。例子:例子A:改進(jìn)可淬硬性的化學(xué)成分選擇如前所述,本發(fā)明的微結(jié)構(gòu)包括至少90%的回火馬氏體,其中精細(xì)碳化物均勻分布,其余為貝氏體。該微結(jié)構(gòu)允許生產(chǎn)連續(xù)管,該連續(xù)管具有高強(qiáng)度、延伸的低周疲勞壽命和改進(jìn)的抗SSC性的想要的組合?;鼗瘃R氏體通過(guò)至少一個(gè)淬火和回火熱處理獲得,該熱處理在管通過(guò)ERW形成之后進(jìn)行。如果需要額外的細(xì)化以改進(jìn)抗SSC性,熱處理可以重復(fù)兩次或更多次。這是因?yàn)殡S后的奧氏體化和淬火循環(huán)減小的不僅僅是先前的奧氏體晶粒尺寸,還有馬氏體塊和馬氏體束的尺寸。為獲得具有良好可淬硬性的目標(biāo)微結(jié)構(gòu),至少90%的馬氏體必須在淬火過(guò)程的末尾形成。充分的化學(xué)成分選擇對(duì)于獲得這樣的馬氏體的體積百分率是至關(guān)重要的。合適的鋼成分的選擇基于試驗(yàn)結(jié)果,所述試驗(yàn)在熱機(jī)械模擬器3500中進(jìn)行。隨后進(jìn)行工業(yè)測(cè)試,以確認(rèn)實(shí)驗(yàn)室發(fā)現(xiàn)。在實(shí)驗(yàn)室中分析的一些鋼化學(xué)成分列在表A1中。對(duì)于所有這些化學(xué)成分,都在中進(jìn)行了膨脹測(cè)試(dilatometrictests),以構(gòu)建連續(xù)冷卻轉(zhuǎn)換(CCT,ContinuousCoolingTransformation)圖。這些CCT圖,結(jié)合對(duì)從模擬器獲得的樣品的金相分析,用于確定最小冷卻速率,以獲得多于90%的馬氏體。該臨界冷卻速率,其主要依賴于鋼化學(xué)成分,將稱為CR90。鋼CMnSiCrMoNiCu其他STD10.130.800.350.52-0.150.28TiSTD20.140.800.330.550.100.170.27Nb-TiSTD30.140.800.340.570.320.220.28Nb-TiCMn10.172.000.20-----CMn20.251.600.20-----BTi10.171.600.20----B-TiBTi20.251.300.20----B-TiCrMo10.171.000.251.000.50---CrMo20.250.600.201.000.50---CrMoBTi10.170.600.201.000.50--B-TiCrMoBTi20.240.400.151.000.25--B-TiCrMoBTi30.240.400.151.000.50--B-TiCrMoBTi40.260.600.150.500.25B-Ti表A1:實(shí)驗(yàn)研究的鋼的化學(xué)成分。元素含量表示為重量百分比(wt%)。獲得的CCT圖的例子呈現(xiàn)在圖1-2中。在所有情形下,奧氏體化在900-950℃下進(jìn)行,以獲得10-20μm的精細(xì)奧氏體晶粒尺寸(AGS)。STD1、STD2和STD3鋼具有在API5ST規(guī)格內(nèi)的化學(xué)成分,但是在本發(fā)明的范圍之外,因?yàn)樗鼈兙哂械偷奶继砑樱ū鞟1)。在STD1和STD2的情形下,臨界冷卻CR90大于100℃/秒,對(duì)于STD3為大約50℃/秒。圖1A-B表示對(duì)應(yīng)于STD2(A)和STD3(B)鋼的CCT圖。粗體表示產(chǎn)生最終微結(jié)構(gòu)的臨界冷卻條件,該微結(jié)構(gòu)包括大約90%的馬氏體,其余為貝氏體。圖2A-B表示對(duì)應(yīng)于BTi2和CrMoBTi3鋼的CCT圖。粗體表示產(chǎn)生最終微結(jié)構(gòu)的臨界冷卻條件,該微結(jié)構(gòu)包括大約90%的馬氏體,其余為貝氏體。第一個(gè)是與B-Ti微合金的C-Mn鋼(參見(jiàn)表A1)。CrMoBTi2是具有Cr和Mo添加的中碳鋼,也與B-Ti微合金。測(cè)量的臨界冷卻速率(對(duì)應(yīng)于CCT圖中粗體所示的冷卻曲線)對(duì)于BTi2和CrMoBTi3分別是25℃/s和15℃/s。在圖3中示出的是在工業(yè)淬火噴頭設(shè)備中處理的管的平均冷卻速率(噴射水,從外表面冷卻管)。值示出為管壁厚(WT,WallThickness)的函數(shù)。圖中陰影區(qū)域?qū)?yīng)于連續(xù)管應(yīng)用中典型的壁厚范圍。清楚的是,當(dāng)選擇適用于獲得大于90%回火馬氏體的鋼化學(xué)成分時(shí),合金的臨界冷卻速率應(yīng)等于或小于30℃/s。另外,在上述設(shè)備中對(duì)更厚的管(WT=0.3英寸)淬火的過(guò)程中,將形成多于10%的貝氏體。STD1,STD2和STD3具有在30℃/s以上的臨界冷卻速率,其后這些鋼不適合于本發(fā)明。另一方面,可淬硬性在BTi2和CrMoBTi3鋼中是足夠的??纱阌残缘母倪M(jìn)原因在于增加的碳含量和B-Ti添加。表A2中示出了對(duì)表A1的鋼測(cè)量得到的臨界冷卻速率。STD1,STD2和STD3是當(dāng)前用于連續(xù)管等級(jí)80、90和110的化學(xué)成分,并滿足API5ST。然而,甚至更多的合金STD3具有臨界冷卻速率,以保證在具有相關(guān)范圍內(nèi)的WT的管中多于90%的回火馬氏體。清楚的是,標(biāo)準(zhǔn)材料不足以產(chǎn)生本發(fā)明的目標(biāo)微結(jié)構(gòu),且可淬硬性必須提高。在低合金鋼中,影響可淬硬性的最重要的元素是碳。其后,C提高到API5ST規(guī)定的最大值(0.16重量%)之上,使得臨界冷卻速率不高于30℃/s。在本發(fā)明中,碳添加在從0.17%到0.35%的范圍中(選擇最大水平以保證良好的可焊性和韌性)。如同剛剛提到的,該化學(xué)成分的其余部分必須調(diào)節(jié)到具有等于或小于30℃/s的CR90值。表A2:獲得高于多于90%的馬氏體的臨界冷卻速率(CR90),對(duì)所分析的鋼測(cè)量。值由膨脹測(cè)試和金相分析而確定。下面用于選擇足夠的鋼化學(xué)成分的原則從對(duì)表A2中的實(shí)驗(yàn)結(jié)果的分析中獲得。C-Mn鋼:可淬硬性主要取決于碳和錳的添加劑。當(dāng)C處于下限時(shí),大約2%的Mn可以用于獲得想要的可淬硬性(CMn1鋼)。然而,Mn是產(chǎn)生強(qiáng)的偏析模式的元素,而偏析模式將減少疲勞壽命。其后,Mn添加劑在較高碳的配方中下降。例如,當(dāng)碳含量為大約0.25%時(shí),1.6%的Mn足以獲得可淬硬性(CMn2鋼)。B-Ti鋼:這些合金是與硼和鈦微合金的普通碳鋼。由于增加了與硼作用相關(guān)的可淬硬性,Mn可以進(jìn)一步減少。對(duì)于在下限中的碳,大約1.6%的Mn可以用于獲得可淬硬性。當(dāng)碳含量為大約0.25%時(shí),1.3%的Mn足以獲得可淬硬性(BTi2鋼)。Cr-Mo鋼:這些鋼具有Cr和Mo添加劑,它們對(duì)于增加回火穩(wěn)定性是有用的,這使得它們適合于超高強(qiáng)度等級(jí)。此外,Cr和Mo是改進(jìn)可淬硬性的元素;所以Mn添加劑可以進(jìn)一步減少。然而,Cr和Mo是昂貴的添加劑,其減小了鋼的熱加工性,它們的最大含量分別限制到1%和0.5%。在一個(gè)例子中,其中碳處于下限,大約1%的Mn可以用于實(shí)現(xiàn)CR90(CrMo1)。如果鋼也是與B-Ti的微合金,可以實(shí)現(xiàn)Mn進(jìn)一步減少到0.6%(CrMoBTi1)。例子B:用于不同連續(xù)管等級(jí)的化學(xué)成分選擇為分析表A1呈現(xiàn)的鋼的回火行為,以進(jìn)行了工業(yè)熱處理的仿真。這些仿真包括在900-950℃的奧氏體化,以30℃/秒的淬火和回火。在STD1、STD2和STD3鋼的特殊情形下,采用了更高的冷卻速率,以在淬火過(guò)程中獲得至少90%的馬氏體。對(duì)于STD1和STD2,采用大約150℃/s的淬火速率,而對(duì)于STD3,冷卻是在50℃/s。當(dāng)提供外部水冷卻時(shí),這些更高的冷卻速率可以在小樣品中在處獲得。在淬火之后,樣品采用兩類循環(huán)回火:-峰狀循環(huán):以50℃/s加熱到最大溫度(Tmax),其在從550℃到720℃的范圍中。以大約1.5℃/s冷卻到室溫。這些循環(huán)旨在仿真在感應(yīng)爐中實(shí)際的回火條件,其特征在于高的加熱速率,在最大溫度處沒(méi)有均熱時(shí)間,以及空氣冷卻。-等溫循環(huán):以50℃/s加熱到710℃/s,在該溫度下均熱從1分鐘到1小時(shí)的時(shí)間,并以大約1.5℃/s冷卻。該循環(huán)用于仿真工業(yè)線中的回火,其中具有多個(gè)均熱電感器或隧道爐。在所有的情形下,回火溫度在從550℃/s到720℃/s的范圍中。高于720℃/s的溫度需要避免,因?yàn)闆](méi)有想要的再奧氏體化發(fā)生。另一方面,如果回火在550℃/s以下進(jìn)行,位錯(cuò)(dislocated)結(jié)構(gòu)的恢復(fù)不完全,材料出現(xiàn)脆化組分,這將削弱疲勞壽命。峰狀回火循環(huán)優(yōu)選用于減少線的長(zhǎng)度并提高生產(chǎn)率。其后,獲得具有特定鋼化學(xué)成分的給定等級(jí)的可行性主要通過(guò)回火曲線確定,該回火曲線采用該類循環(huán)獲得。如果在720℃/s下進(jìn)行峰狀回火之后,強(qiáng)度仍然對(duì)于該等級(jí)過(guò)高,可以在最大溫度下進(jìn)行均熱。然而,隨著均熱時(shí)間增加,可能需要更大、更昂貴和更低生產(chǎn)率的工業(yè)線。在圖4中(左邊圖)呈現(xiàn)了對(duì)BTi2鋼測(cè)量的回火曲線。拉伸性能示出為最大回火溫度的函數(shù)。峰狀熱循環(huán)用于仿真中。從圖中可以看到,等級(jí)90到125可以通過(guò)從大約710℃到575℃地改變最大峰值溫度而分別獲得。不將回火溫度減小到550℃以下的話,該化學(xué)成分不可能達(dá)到140Ksi的屈服強(qiáng)度。關(guān)于較低的等級(jí),710℃下3分鐘的均熱可以用于獲得等級(jí)80(圖4右側(cè)圖)。基從仿真獲得的結(jié)果,構(gòu)建出表B1。對(duì)于每種分析的鋼,該表示出生產(chǎn)不同等級(jí)的可行性,其最小屈服強(qiáng)度的范圍從80Ksi到140Ksi。例如,在BTi2的情形下,采用峰狀回火循環(huán)達(dá)到等級(jí)90到125是可行的。但是720℃下2分鐘的均熱可以用于等級(jí)80的情形下,這是在相應(yīng)的單元標(biāo)記“均熱”的原因。表B1:采用分析的鋼化學(xué)成分工業(yè)生產(chǎn)等級(jí)80到140的可行性。當(dāng)“均熱”出現(xiàn)在單元中時(shí),這意味著720℃下多于1分鐘的均熱可以用于達(dá)到該等級(jí)。從獲得的結(jié)果可以清楚,為了獲得較高的等級(jí),可以采用增加的碳和Cr-Mo添加劑。特別地,由于低的碳含量,等級(jí)140不能用標(biāo)準(zhǔn)化學(xué)成分實(shí)現(xiàn),如在API5ST中所述那樣。另一方面,為達(dá)到等級(jí)80,具有低碳的貧化學(xué)成分(leanchemistry),沒(méi)有Cr或Mo添加劑是最佳的選擇。在這種情形下,B-Ti微合金添加劑可以用于保證好的可淬硬性(例如,像BTi1的化學(xué)成分是好的替代選擇)。重點(diǎn)要指出的是,為了用標(biāo)準(zhǔn)鋼(STD1、STD2、STD3)產(chǎn)生馬氏體結(jié)構(gòu),在實(shí)驗(yàn)室中需要采用比在工廠中可實(shí)現(xiàn)的更高的淬火速率。其后,如果我們將冷卻速率限制到該工業(yè)上可獲得的冷卻速率,這些連續(xù)管等級(jí)都不能用現(xiàn)有的鋼采用FBHT處理路線獲得。例子C:減少固化過(guò)程中偏析負(fù)面作用的化學(xué)成分選擇在鋼固化過(guò)程中,合金元素傾向于在液體中保持稀釋,因?yàn)槠湎啾扔诠腆w(δ鐵素體或奧氏體)具有更高的溶解度。隨著固化,富集溶質(zhì)的區(qū)域形成兩類非均勻的化學(xué)成分模式:微觀偏析和宏觀偏析。微觀偏析由在枝晶間空間中富集溶質(zhì)的液體凝固而造成。但是其不構(gòu)成主要問(wèn)題,因?yàn)槲⒂^偏析的作用可以在隨后的熱加工過(guò)程中去除。另一方面,宏觀偏析是化學(xué)成分在較大規(guī)模的鑄造部分中的非均勻性。這不能夠通過(guò)在高溫下和/或熱加工中均熱而完全消除。在本發(fā)明所關(guān)注的情況中,其是連續(xù)的厚板鑄造,這會(huì)產(chǎn)生中線偏析帶。顯著的中心偏析帶必須避免,因?yàn)椋?作為未回火馬氏體的脆化組分可能出現(xiàn)在該區(qū)域中,這是作為焊接操作的結(jié)果(斜焊和ERW,例如參見(jiàn)圖5A-B)。這些不想要的組分在隨后的整體熱處理中去除。然而,通過(guò)在焊接和熱處理操作之間彎曲,管可能塑性變形,在工業(yè)生產(chǎn)過(guò)程中產(chǎn)生破壞。-在FBHT之后,中心偏析帶的殘余部分是富集替代溶質(zhì)(如Mn、Si、Mo)的區(qū)域,其具有比材料其余部分更高的粗碳化物密度。該區(qū)域在低周疲勞過(guò)程中易于使裂紋成核,如在圖6-7中觀察到的那樣。此外,顯著的偏析帶與差的抗SSC性相關(guān)。盡管不可能去除宏觀偏析,其對(duì)于韌性、疲勞壽命和抗SSC性的負(fù)面作用可以通過(guò)合適選擇鋼化學(xué)成分而減小?;趯?duì)對(duì)應(yīng)于大范圍的鋼化學(xué)成分的樣品的EDX測(cè)量,在中心偏析帶中富集因子對(duì)不同合金元素進(jìn)行了估計(jì)。結(jié)果在表C1中示出。富集因子(EF,enrichmentfactor)是在中心帶處每種元素含量和基體中對(duì)應(yīng)于平均值的含量之間的比率。這些因子主要依賴于液體和固體之間的熱力學(xué)分配系數(shù),和在固化過(guò)程中的擴(kuò)散率。元素EFMn1.6Si3.2Cr1.2Mo2.1Ni1.3Cu3.4表C1:在中心偏析帶處的富集因子(EF),對(duì)應(yīng)于不同的替代合金元素。表C1清楚地表示存在一些元素,其具有強(qiáng)的趨勢(shì)會(huì)在固化過(guò)程中偏析,如Si和Cu。另一方面,Cr和Ni具有低的富集因子。Ni是昂貴的添加劑,但是當(dāng)需要在不產(chǎn)生強(qiáng)的偏析模式下需要獲得可淬硬性和/或回火穩(wěn)定性時(shí),可以采用Cr。富集因子給出了關(guān)于含量增加的信息,該含量可以為在中心偏析帶處的每個(gè)元素所期待。然而,關(guān)于在焊接或熱處理過(guò)程中形成脆化組分的材料趨勢(shì),不是所有這些元素都具有相同的作用??梢杂^察到,可淬硬性提高得越高,在處理過(guò)程中形成脆化組分的趨勢(shì)越強(qiáng)。重要的是,具有高擴(kuò)散系數(shù)的元素,例如碳和硼,會(huì)在固化過(guò)程中偏析,但是在熱軋過(guò)程中均質(zhì)化。其后,它們不會(huì)有助于在偏析帶處形成脆化組分。從對(duì)CCT圖(例子A)的分析可得出,錳產(chǎn)生最多的可淬硬性增長(zhǎng)。這要除去碳和硼,它們?cè)跓彳堉蟛怀尸F(xiàn)大的偏析模式。另一方面,Si和Cu,其具有偏析的強(qiáng)烈趨勢(shì),對(duì)可淬硬性不起主要作用。由于其高的富集因子和對(duì)可淬硬性的大的作用,當(dāng)試圖減少宏觀偏析的負(fù)面作用時(shí),如同減少低周疲勞壽命那樣,Mn添加劑必須盡可能地減少。高M(jìn)n含量普通地添加到鋼成分中,因?yàn)槠鋵?duì)可淬硬性的作用。在本發(fā)明中,可淬硬性主要通過(guò)較高的碳添加劑實(shí)現(xiàn),所以Mn的含量通??梢詼p小。采用硼和/或鉻添加劑可實(shí)現(xiàn)錳的進(jìn)一步減少。例子可以在表C2中看到,該表表示用于從CCT圖中獲得的不同的鋼成分的臨界冷卻速率(CR90)(數(shù)據(jù)從前面例子A中取得)。為了在大約0.25%的碳含量下實(shí)現(xiàn)鋼中的可淬硬性,當(dāng)添加硼時(shí),Mn可以從1.6%減少到1.3%,且如果附加地使用Cr-Mo,可進(jìn)一步減少到0.4%。表2:獲得大于90%的馬氏體的臨界冷卻速率(CR90),為所分析的鋼測(cè)量。值由膨脹測(cè)試和金相分析而確定。例子D:微結(jié)構(gòu)的均質(zhì)化如前所述,連續(xù)管的疲勞壽命強(qiáng)烈地依賴于作為微結(jié)構(gòu)異質(zhì)性的微觀特征。軟、硬微組分的組合傾向于產(chǎn)生塑性應(yīng)變局部化,其是裂紋成核和擴(kuò)展的驅(qū)動(dòng)力。在本部分比較了通過(guò)標(biāo)準(zhǔn)生產(chǎn)方法獲得的連續(xù)管微結(jié)構(gòu),該方法應(yīng)用于在API5ST內(nèi)的化學(xué)成分,和在本發(fā)明公開(kāi)的范圍內(nèi)對(duì)應(yīng)于化學(xué)成分和處理?xiàng)l件的那些?;鶞?zhǔn)材料所使用的是標(biāo)準(zhǔn)連續(xù)管等級(jí)110(從110Ksi到120Ksi的屈服強(qiáng)度),其具有表A1中名為STD2的化學(xué)成分,這是在API5ST規(guī)格內(nèi)的。該標(biāo)準(zhǔn)材料與通過(guò)化學(xué)BTi2和采用FBHT生產(chǎn)得到的相同等級(jí)的連續(xù)管相比較。在該比較中,不同的管位置將被考慮:-基礎(chǔ)金屬(BM):除去ERW線和斜焊的連續(xù)管微結(jié)構(gòu),當(dāng)“除去”意味著不包括在該區(qū)域中時(shí),在任何焊接操作和它們可能的焊接后熱處理(PWHT,Post-WeldHeatTreatment)過(guò)程中產(chǎn)生熱影響區(qū)(HAZ)。-斜焊(BW):對(duì)應(yīng)于條帶到條帶連接的微結(jié)構(gòu)區(qū)域,其可以通過(guò)等離子弧焊(PAW,PlasmaArcWelding)、攪拌摩擦焊(FSW,F(xiàn)rictionStirWelding)或任何其他焊接技術(shù)進(jìn)行。在該區(qū)域中還包括在焊接和PWHT過(guò)程中相應(yīng)的熱影響區(qū)。-ERW線:在管形成及其局部化的PWHT過(guò)程中,由縱向ERW焊接導(dǎo)致的微結(jié)構(gòu),該局部化的PWHT過(guò)程通常是焊縫退火。如同前面的情形,該區(qū)域也包括相應(yīng)的熱影響區(qū)。在圖8A-B中呈現(xiàn)了對(duì)應(yīng)于標(biāo)準(zhǔn)連續(xù)管(A)和本發(fā)明(B)的基礎(chǔ)金屬微結(jié)構(gòu)。在第一情形下,觀察到具有精細(xì)碳化物分布的鐵素體基質(zhì)。該基質(zhì)和精細(xì)結(jié)構(gòu)由控制的熱軋過(guò)程導(dǎo)致。本發(fā)明的微結(jié)構(gòu)(圖8B)主要包括回火馬氏體。貝氏體的體積百分率在本例中小于5%?;鼗瘃R氏體結(jié)構(gòu)也是在鐵素體基質(zhì)中碳化鐵的精細(xì)分布?,F(xiàn)有結(jié)構(gòu)和新結(jié)構(gòu)之間的主要區(qū)別涉及鐵素體晶粒和子晶粒的形態(tài),和位錯(cuò)密度。然而,關(guān)于細(xì)化和均勻性,兩個(gè)結(jié)構(gòu)非常類似。在圖9A-B中示出了對(duì)應(yīng)于ERW線的掃描電子顯微圖。清楚的是,現(xiàn)有結(jié)構(gòu)的兩個(gè)微組分出現(xiàn):存在軟鐵素體晶粒和硬塊,其包括精細(xì)珠光體、馬氏體和一些殘留的奧氏體的混合物。在該類結(jié)構(gòu)中,塑性應(yīng)變?cè)阼F素體中局部化,裂紋可以成核并在鄰近的脆化組分(未回火馬氏體和高碳?xì)埩魥W氏體)中擴(kuò)展。另一方面,用本發(fā)明范圍內(nèi)的化學(xué)成分和處理?xiàng)l件獲得的ERW線微結(jié)構(gòu)是均質(zhì)的,并非常類似于相應(yīng)的基礎(chǔ)金屬結(jié)構(gòu)。對(duì)應(yīng)于ERW的HAZ的微結(jié)構(gòu)出現(xiàn)在圖10A-B中。在標(biāo)準(zhǔn)材料中,清楚的是中心偏析帶的殘余部分的出現(xiàn),其在焊縫退火之后部分地轉(zhuǎn)變?yōu)槲椿鼗瘃R氏體。再次,這些是脆化組分,其沿著ERW線局部化,并可以在使用過(guò)程中成核和擴(kuò)展裂紋。破壞風(fēng)險(xiǎn)高于前面的例子,因?yàn)閯倓偺岬降慕M分具有更大的尺寸。另一方面,在淬火和回火過(guò)的連續(xù)管中,靠近ERW線的結(jié)構(gòu)是均勻的,而看不到中心偏析帶的殘余部分。在圖11A-B中呈現(xiàn)了一些掃描電子顯微圖,其對(duì)應(yīng)于現(xiàn)有連續(xù)管和本發(fā)明兩者的斜焊HAZ?,F(xiàn)有材料中,微結(jié)構(gòu)非常不同于在基礎(chǔ)金屬(BM)中的。其主要包括上貝氏體,且晶粒尺寸是大的(50微米,比較于BM的小于15微米)。該類粗結(jié)構(gòu)對(duì)于低周疲勞是不足夠的,因?yàn)榱鸭y可以容易地沿著貝氏體條板擴(kuò)展。圖12中示出了疲勞裂紋的例子,該疲勞裂紋在斜焊中橫跨粗貝氏體。這是靠近主要破壞的次級(jí)裂紋,該主要破壞發(fā)生在標(biāo)準(zhǔn)連續(xù)管等級(jí)110的使用過(guò)程中。另一方面,本發(fā)明中的斜焊微結(jié)構(gòu)再次非常類似于對(duì)應(yīng)于基礎(chǔ)金屬的微結(jié)構(gòu)。沒(méi)有上貝氏體晶粒被觀察到。重要的是,一些貝氏體可能在整體熱處理之后出現(xiàn),但是由于足夠的化學(xué)成分和處理?xiàng)l件的選擇,該組分的相應(yīng)的體積百分率低于10%。這是本發(fā)明所述化學(xué)成分良好可淬硬性的主要理由。此外,由于奧氏體化溫度的上限,最終的晶粒尺寸是小的(小于20微米),然后會(huì)擴(kuò)展裂紋的大的貝氏體條板得以完全避免。圖13-14呈現(xiàn)了通過(guò)本發(fā)明公開(kāi)的鋼化學(xué)成分和處理?xiàng)l件的組合獲得的微結(jié)構(gòu)的均勻性的其他例子。在圖13中示出了現(xiàn)有生產(chǎn)的連續(xù)管中橫跨斜焊的硬度的典型變化,比較于采用新化學(xué)成分和處理方法所獲得的。清楚的是,當(dāng)使用本發(fā)明時(shí),硬度變化大大地減小。結(jié)果,材料在局部區(qū)域(本例中斜焊的HAZ)累積應(yīng)力的趨勢(shì)也得以減小,疲勞壽命得以提高。圖14A-B表示一些微結(jié)構(gòu),其對(duì)應(yīng)于在斜焊和ERW線之間的交叉處。清楚的是,隨著現(xiàn)有路線獲得大的微結(jié)構(gòu)異質(zhì)性。這些異質(zhì)性采用本發(fā)明公開(kāi)的化學(xué)成分和處理?xiàng)l件而被成功消除。例子E:連續(xù)管疲勞測(cè)試為了比較根據(jù)本發(fā)明生產(chǎn)的連續(xù)管相對(duì)于標(biāo)準(zhǔn)產(chǎn)品的性能,一系列測(cè)試在實(shí)驗(yàn)室中進(jìn)行。連續(xù)管樣品在如圖15中示意性示出的疲勞機(jī)中測(cè)試。該機(jī)器能夠仿真卷起和展開(kāi)操作過(guò)程中的彎曲變形,同時(shí)施加以內(nèi)部壓力。因此,測(cè)試對(duì)于低周疲勞條件下的材料進(jìn)行評(píng)級(jí)是有用的,其接近在實(shí)際現(xiàn)場(chǎng)操作過(guò)程中的那些經(jīng)歷。在測(cè)試過(guò)程中,疲勞樣品(管件,5或6英尺長(zhǎng))夾在一端上,而交替力通過(guò)液壓作動(dòng)器施加在相反端上。通過(guò)在固定半徑的彎曲心軸上彎曲樣品,將變形周期施加在測(cè)試樣品上,然后對(duì)抗筆直的支撐而將其拉直。鋼帽焊接在樣品的端部處并連接到液壓泵上,從而使得循環(huán)得以進(jìn)行,樣品填充以處于恒定內(nèi)部壓力下的水,直至發(fā)生破壞。當(dāng)發(fā)生內(nèi)部壓力丟失時(shí),測(cè)試結(jié)束,因?yàn)榱鸭y發(fā)展通過(guò)壁厚。測(cè)試在具有不同化學(xué)成分和等級(jí)的連續(xù)管上進(jìn)行,如表E1所示。管幾何在所有情形下都一樣(OD2”,重量0.19”)。STD1,STD2和STD3是在API5ST中所述限度內(nèi)的鋼,接著進(jìn)行標(biāo)準(zhǔn)路線的處理。BTi1、BTi2和CrMoBTi4是根據(jù)本發(fā)明選擇和處理的化學(xué)成分。重要的是,CrMoBTi4鋼用于生產(chǎn)兩個(gè)非標(biāo)準(zhǔn)的等級(jí),具有125Ksi和140Ksi的最小屈服強(qiáng)度(API5ST中描述的最高等級(jí)具有110Ksi的SMYS)。測(cè)試在具有和不具有斜焊的管件上進(jìn)行(在所有情形下,縱向ERW線包括在樣品中)。測(cè)試的嚴(yán)格性主要依賴于兩個(gè)參數(shù):彎曲半徑和內(nèi)部壓力。在本研究中,彎曲半徑是48英寸,其對(duì)應(yīng)于大約2%的塑性應(yīng)變??紤]在1600psi和13500psi之間的內(nèi)部壓力,這產(chǎn)生在從大約10%到60%的等級(jí)最小屈服強(qiáng)度范圍中的箍應(yīng)力(hoopstress)。表E1:在本研究中分析的化學(xué)成分和連續(xù)管等級(jí)。在圖16中呈現(xiàn)了一些關(guān)于比較的結(jié)果,該比較在具有和不具有斜焊(BW)的樣品中測(cè)量到的疲勞壽命之間進(jìn)行。圖中所示的值對(duì)應(yīng)于在測(cè)試現(xiàn)有的和非現(xiàn)有的連續(xù)管等級(jí)時(shí)獲得的平均值。在現(xiàn)有材料的情形下,當(dāng)測(cè)試的樣品含有斜焊時(shí),疲勞壽命有明顯的減小。另一方面,當(dāng)測(cè)試在BW樣品上進(jìn)行時(shí),根據(jù)本發(fā)明生產(chǎn)的連續(xù)管不出現(xiàn)疲勞壽命的重要變化。這是管均勻性結(jié)構(gòu)的結(jié)果,在基礎(chǔ)金屬、ERW線和斜焊之間的機(jī)械性能幾乎沒(méi)有區(qū)別。圖17示出了通過(guò)本發(fā)明公開(kāi)的化學(xué)成分和處理?xiàng)l件獲得的連續(xù)管疲勞壽命的提高。對(duì)于等級(jí)80、90和110,比較針對(duì)通過(guò)現(xiàn)有方法生產(chǎn)的等效等級(jí)。在等級(jí)125和140的情形下,這是非標(biāo)準(zhǔn)的,疲勞壽命比較針對(duì)等級(jí)110中的STD3鋼進(jìn)行,其在類似的條件下(管幾何、彎曲半徑和內(nèi)部壓力)測(cè)試。圖中示出的結(jié)果對(duì)應(yīng)于每個(gè)等級(jí)的平均值,誤差條表示在使用不同的內(nèi)部壓力時(shí)獲得的差量。在圖17中,清楚的是,當(dāng)采用根據(jù)本發(fā)明的化學(xué)成分和處理?xiàng)l件時(shí),觀察到疲勞壽命的顯著改進(jìn)。例如,在等級(jí)110中,疲勞壽命提高了大約100%。這是這樣的事實(shí)的結(jié)果,即在現(xiàn)有的連續(xù)管中,疲勞性能受限于斜焊(其通常是關(guān)于低周疲勞的弱點(diǎn),引起其微結(jié)構(gòu)的異質(zhì)性和脆化組分)。在根據(jù)本發(fā)明生產(chǎn)的連續(xù)管中,在斜焊處沒(méi)有重要的疲勞壽命減少,這大大地提高了管的總性能。關(guān)于非標(biāo)準(zhǔn)等級(jí),疲勞壽命中大的改進(jìn)是由于這樣的事實(shí),即比較是針對(duì)在類似處理?xiàng)l件下測(cè)試的現(xiàn)有110等級(jí)。然而,對(duì)于相同的內(nèi)部壓力,施加的箍應(yīng)力更加接近較低等級(jí)的最小屈服強(qiáng)度,而等級(jí)110的測(cè)試嚴(yán)格性比較于等級(jí)125和140提升了。這些結(jié)果表明,通過(guò)更高的等級(jí)(在現(xiàn)有方法中未實(shí)現(xiàn)),疲勞壽命對(duì)于相同的使用條件有了大大提高。例子F:抗硫化物應(yīng)力開(kāi)裂性在含有H2S的環(huán)境中關(guān)于氫脆化的材料性能涉及腐蝕環(huán)境、存在可能局部地增加氫的含量的阱(traps)(例如沉淀和位錯(cuò)),以及存在脆化區(qū)域的組合作用,其中裂紋可以容易地?cái)U(kuò)展。在現(xiàn)有連續(xù)管材料中的關(guān)鍵的脆化區(qū)域的可能來(lái)源是原材料中的替代元素(例如Mn)的偏析模式。不同含量的區(qū)域傾向于以不同方式響應(yīng)在斜焊、PWHT、ERW和焊縫退火過(guò)程中施加的熱循環(huán),并可能導(dǎo)致脆化組分的局部形成。特別地,當(dāng)材料在ERW處理之后焊縫退火,管體快速地從焊接區(qū)域提取熱。如果偏析足夠高,由于冷卻條件,伸長(zhǎng)的高硬區(qū)域可能形成,其中可能出現(xiàn)馬氏體。這些區(qū)域?qū)⒈3衷诠苤?,成為裂紋容易擴(kuò)展的路徑。新的處理用作制造的最后階段的事實(shí)允許過(guò)度硬化區(qū)域最小化。其他相關(guān)差異是:a)在管冷成型過(guò)程中引入的位錯(cuò)沒(méi)有出現(xiàn)在新產(chǎn)品中,b)在新產(chǎn)品中的碳化物比典型的珠光體/貝氏體長(zhǎng)脆化碳化物更小并是隔離的。結(jié)果,根據(jù)本發(fā)明的化學(xué)成分和處理?xiàng)l件生產(chǎn)的連續(xù)管對(duì)含H2S的環(huán)境中的開(kāi)裂具有改進(jìn)的性能。表F1:在本研究中分析的鋼化學(xué)成分和連續(xù)管等級(jí)。為了對(duì)抗SSC開(kāi)裂性進(jìn)行第一分析,連續(xù)管等級(jí)80樣品通過(guò)這樣生產(chǎn):i)標(biāo)準(zhǔn)的處理和ii)新的化學(xué)成分-處理采用NACETM0177的方法C(C環(huán))進(jìn)行評(píng)估。鋼化學(xué)成分在表F1中示出。兩種材料(在每種情形下由3個(gè)樣品)都在C環(huán)樣品的中心處對(duì)ERW焊縫縫進(jìn)行測(cè)試,采用了如下條件:負(fù)載:80Ksi的90%,方案A,1barH2S,測(cè)試時(shí)間:720小時(shí)在標(biāo)準(zhǔn)連續(xù)管的情形下,所有3個(gè)樣品都失敗了。另一方面,對(duì)應(yīng)于新的化學(xué)成分-處理的樣品通過(guò)了測(cè)試(圖5A-B,具有C環(huán)的圖片)。盡管進(jìn)行更多的測(cè)試,以分析不同等級(jí)的耐脆化性,和斜焊的作用,本第一結(jié)果表明,比較于標(biāo)準(zhǔn)條件有了清楚的提高,這歸功于新處理方法情形下,基礎(chǔ)金屬和ERW線更均勻的微結(jié)構(gòu)。如圖18A-B所示,通過(guò)現(xiàn)有過(guò)程形成的C環(huán)具有大的下到中間的裂紋,而通過(guò)本發(fā)明的過(guò)程的實(shí)施方式形成的C環(huán)沒(méi)有裂紋。在一些實(shí)施方式中,B-Ti和Cr-Mo添加劑可以減小最大Mn。在一些實(shí)施方式中,等級(jí)可以高于110,這不同于采用現(xiàn)有方法所獲得的。結(jié)合特定方面、實(shí)施方式或例子描述的特征、材料、特性或組應(yīng)理解為可應(yīng)用于這里描述的其他方面、實(shí)施方式或例子,除非與其不兼容。本發(fā)明公開(kāi)的所有特征(包括后面的權(quán)利要求、摘要和附圖),和/或這樣公開(kāi)的任何方法或過(guò)程的所有步驟,可以以任何組合結(jié)合,除非至少一些特征和/或步驟互相排斥。保護(hù)范圍不限于任何前面實(shí)施方式的細(xì)節(jié)。保護(hù)范圍延伸到本發(fā)明公開(kāi)的特征的任何新穎的一個(gè)或任何新穎的組合(包括任何后面的權(quán)利要求、摘要和附圖),或者這樣公開(kāi)的任何方法或過(guò)程的步驟的任何新穎的一個(gè)或任何新穎的組合。盡管已經(jīng)描述了某些實(shí)施方式,這些實(shí)施方式已經(jīng)只通過(guò)例子呈現(xiàn),而不旨在限定保護(hù)范圍。事實(shí)上,這里所述的新穎方法和裝置可以以許多形式具體化。而且,可以對(duì)這里所述的方法、成分和裝置的形式作出不同的省略、替換和改變。本領(lǐng)域技術(shù)人員將理解的是,在一些實(shí)施方式中,在示例的和/或公開(kāi)的過(guò)程中發(fā)生的實(shí)際步驟可以不同于在圖中所示的。根據(jù)實(shí)施方式,上面所述的某些步驟可以去除,其他的可以增加。而且,上面公開(kāi)的具體實(shí)施方式的特征和屬性可以以不同方式組合,以形成其他實(shí)施方式。所有這些都落入本發(fā)明的范圍內(nèi)。盡管本發(fā)明包括某些實(shí)施方式、例子和應(yīng)用,本領(lǐng)域技術(shù)人員將理解的是,本發(fā)明將具體公開(kāi)的實(shí)施方式延伸到其他替代的實(shí)施方式和/或使用和明顯的變形及其等同物,包括這樣的實(shí)施方式,其不具有這里陳述的所有特征和優(yōu)點(diǎn)。相應(yīng)地,本發(fā)明的范圍不旨在通過(guò)這里的優(yōu)選實(shí)施方式的具體公開(kāi)而限定,而可以通過(guò)這里呈現(xiàn)或者將來(lái)呈現(xiàn)的權(quán)利要求限定。