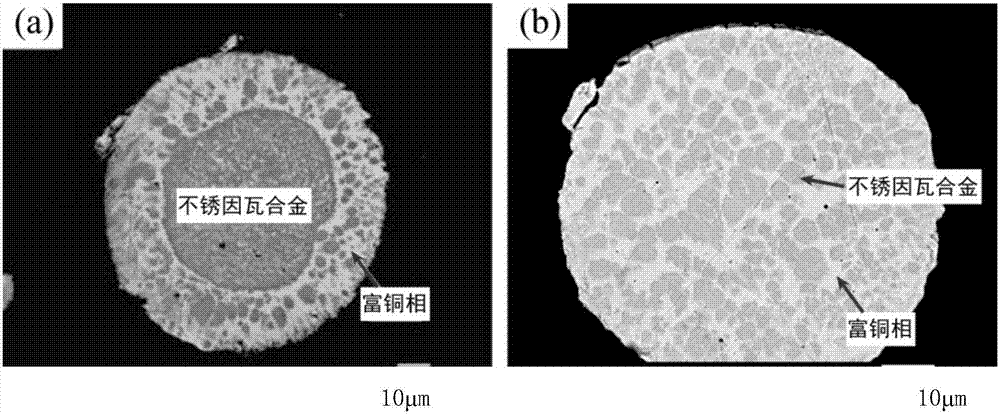
低膨脹高導(dǎo)熱銅-不銹因瓦合金復(fù)合材料及其制備方法技術(shù)領(lǐng)域本發(fā)明涉及一種復(fù)合材料,尤其是涉及一種低膨脹高導(dǎo)熱銅-不銹因瓦合金復(fù)合材料及其制備方法。
背景技術(shù):自1958年第一塊半導(dǎo)體集成電路(IC)問(wèn)世以來(lái),集成電路封裝技術(shù)不斷向高度集成化、小型化和輕量化發(fā)展,這就對(duì)電子封裝材料的性能提出了越來(lái)越高的要求(張臣,沈能玨,電子封裝材料現(xiàn)狀與發(fā)展[J],新材料產(chǎn)業(yè),2003,3:5-11)。隨著芯片集成度和運(yùn)算速度的不斷提高,散熱問(wèn)題已經(jīng)成為各種封裝材料急需解決的重要問(wèn)題。特別對(duì)于大功率器件,熱量如果不能及時(shí)傳導(dǎo)和散發(fā),將導(dǎo)致工作溫度升高,一旦芯片與封裝材料之間的熱膨脹系數(shù)不匹配,相鄰部件及焊點(diǎn)處將產(chǎn)生熱應(yīng)力,導(dǎo)致焊點(diǎn)接觸不牢甚至脫落,使電子元器件失效、嚴(yán)重影響產(chǎn)品的使用壽命和可靠性,因此,開(kāi)發(fā)具備高導(dǎo)熱、低膨脹系數(shù)、易加工和低成本的電子封裝材料已成為當(dāng)務(wù)之急(黃強(qiáng),顧明元,電子封裝材料的研究現(xiàn)狀[J],材料導(dǎo)報(bào),2000,14(9):28-32)。在傳統(tǒng)封裝材料中,Cu及其合金因具有高的熱導(dǎo)率和優(yōu)良的導(dǎo)電性而備受關(guān)注。但是Cu的熱膨脹系數(shù)非常高(17×10-6K-1),與芯片用半導(dǎo)體材料(Si、GaAs)以及基片用陶瓷材料(Al2O3、BeO)的熱膨脹系數(shù)(其范圍在4~7×10-6K-1)不相匹配,容易導(dǎo)致芯片與封裝基板結(jié)合面之間產(chǎn)生大的熱應(yīng)力,甚至產(chǎn)生裂紋而降低電子器件的使用壽命(ShenYL,MetallurgicalandMaterialsTransactionsA,1994,25(4):839-850)。另一方面,不銹因瓦合金(Fe37Co54Cr9)因具有極低的熱膨脹系數(shù)和耐腐蝕性能而被廣泛應(yīng)用于電子封裝領(lǐng)域。不銹因瓦合金是一種特殊的因瓦合金,在其居里溫度以下出現(xiàn)所謂反常熱膨脹現(xiàn)象,使材料的尺寸隨溫度的變化表現(xiàn)為幾乎為零的膨脹率(即因瓦效應(yīng)),從而被廣泛應(yīng)用于電子工業(yè)、精密量具、精密儀表和低溫工程等領(lǐng)域(陳昀,李明光,因瓦合金發(fā)展現(xiàn)狀及應(yīng)用前景[J],機(jī)械研究與應(yīng)用,2009,(4):9-11)。雖然不銹因瓦合金在室溫附近較寬的溫度范圍內(nèi)具有很低的熱膨脹系數(shù)和良好的焊接性能,但由于其導(dǎo)熱能力很差,只能作為小功率整流器的散熱和連接材料。并且,不銹因瓦合金的熱膨脹系數(shù)對(duì)化學(xué)成分非常敏感,成分的偏離將導(dǎo)致其熱膨脹系數(shù)的增大,嚴(yán)重影響使用性能。比如同是退火態(tài),鈷含量也相同,只是一個(gè)含鐵37%、含鉻9%,另一個(gè)含鐵36.5%、含鉻9.5%,前者室溫附近的熱膨脹系數(shù)為-1.2×10-6/℃,后者為0.05×10-6/℃(ShigaM,Invaralloys[J],1996,1(3):340-348)。由于銅或不銹因瓦合金都無(wú)法單獨(dú)滿足電子封裝材料的要求,研究和開(kāi)發(fā)復(fù)合材料引起了研究者的廣泛關(guān)注。美國(guó)德州儀器公司在傳統(tǒng)因瓦合金(Fe64Ni36)板材上雙層覆蓋純銅制成了Cu/因瓦合金(Fe64Ni36)/Cu層狀復(fù)合材料(查爾斯A,哈珀,電子封裝材料與工藝[M],北京:化學(xué)工業(yè)出版社,2006),其中復(fù)合材料的熱膨脹系數(shù)為6.5×10-6K-1。值得注意的是,該復(fù)合材料在平行方向(x-y平面)的熱導(dǎo)率為164W·m-1·K-1,但是在z平面上其熱導(dǎo)率只有24.8W·m-1·K-1,即該類層狀復(fù)合材料在熱物理性能方面存在明顯的各向異性,同時(shí)Cu與因瓦合金層之間存在顯著的界面熱阻,使得熱導(dǎo)率的進(jìn)一步提高受到制約,限制了它的使用范圍。Sunil等人(JhaS.CUVAR-anewcontrolledexpansion,highconductivitymaterialforelectronicthermalmanagement[C],Proceedingsofthe45thElectronicComponentsandTechnologyConference.LasVegas,Nevada.1995:542-547.)將純銅粉與因瓦合金(Fe64Ni36)粉末混合后通過(guò)常溫下擠壓成型制備了銅/因瓦合金復(fù)合材料,并獲得了較好的熱膨脹性能和導(dǎo)熱性能。然而,為了在常溫下獲得高致密度的復(fù)合材料,粉末在擠壓成型時(shí)受到強(qiáng)大的剪切力,從而造成材料的熱物理性能存在各向異性的缺點(diǎn),同時(shí)該材料的使用溫度要求低于400℃,以防因Fe、Ni與Cu在高溫下相互擴(kuò)散對(duì)熱膨脹特性及導(dǎo)熱性能造成不利影響。另外,Stolk等人(StolkJ,ManthiramA.ChemicalsynthesisandpropertiesofnanocrystallineCu–Fe–Nialloys[J].MaterialsScienceandEngineering:B,1999,60(2):112-117)采用水熱還原法合成一定比例的Cu、Fe、Ni納米粉末,再通過(guò)粉末冶金法制備Cu-因瓦合金(Fe64Ni36)納米晶合金,但是粉末經(jīng)900℃燒結(jié)后,因Fe、Ni與Cu的相互擴(kuò)散使得Cu-Fe64Ni36納米合金無(wú)法獲得良好的導(dǎo)熱及熱膨脹性能。然而目前為止,尚未有銅和不銹因瓦合金復(fù)合材料的研究報(bào)道,這是因?yàn)镃u原子和Fe、Co、Cr原子是相互排斥的,Cu和Fe、Co、Cr相互之間的固溶度很低,采用傳統(tǒng)的合金熔煉方法來(lái)制備Cu-Fe-Co-Cr合金,將發(fā)生嚴(yán)重的成分偏析或相分離,從而導(dǎo)致材料性能的不均勻,無(wú)法實(shí)際應(yīng)用。因此,研究和開(kāi)發(fā)銅-不銹因瓦合金的有效復(fù)合方法,制備具有低膨脹、高導(dǎo)熱性能的銅-不銹因瓦合金復(fù)合材料將具有重大的理論意義和應(yīng)用價(jià)值。
技術(shù)實(shí)現(xiàn)要素:本發(fā)明針對(duì)目前電子封裝材料急需的低膨脹、高導(dǎo)熱性等性能需求,提供一種低膨脹高導(dǎo)熱銅-不銹因瓦合金復(fù)合材料及其制備方法。所述低膨脹高導(dǎo)熱銅-不銹因瓦合金復(fù)合材料按質(zhì)量百分比的組成為:Cu20%~75%,F(xiàn)e9%~30%,Co12%~45%,Cr2%~8%,添加劑0~5%,所述添加劑選自W,Nb,Ta,Mo,C,B,V等中的至少一種。所述低膨脹高導(dǎo)熱銅-不銹因瓦合金復(fù)合材料的制備方法,包括以下步驟:(1)通過(guò)相圖計(jì)算方法,設(shè)計(jì)復(fù)合材料的成分,使其成分中存在富Cu相和富Fe-Co-Cr相的液相兩相分離區(qū);(2)按步驟(1)的計(jì)算結(jié)果稱取各種原材料,放入氣霧化制粉設(shè)備,抽真空,在氬氣保護(hù)下感應(yīng)熔煉,待合金完全熔化成液體后進(jìn)行氣霧化,得到核/殼型自包裹復(fù)合粉體,使富Cu相為殼層,富Fe-Co-Cr相形成不銹因瓦合金并成為復(fù)合粉體的核;(3)將步驟(2)中制得的核/殼型自包裹復(fù)合粉體放入燒結(jié)爐中,在氬氣保護(hù)下進(jìn)行熱壓燒結(jié),冷卻后得到銅-不銹因瓦合金復(fù)合材料燒結(jié)體;(4)將步驟(3)中的得到的銅-不銹因瓦合金復(fù)合材料燒結(jié)體進(jìn)行退火處理,即得低膨脹高導(dǎo)熱銅-不銹因瓦合金復(fù)合材料。在步驟(2)中,所述核/殼型自包裹復(fù)合粉體的粒徑可為20~320μm,可以是單核,也可以是多核,并且兩種粉的比例是可以通過(guò)調(diào)節(jié)成分和氣體霧化的工藝參數(shù)進(jìn)行調(diào)控的。在燒結(jié)的過(guò)程中,可以采用不同燒結(jié)工藝,如等靜壓或者軸向施加壓力;另外可以根據(jù)實(shí)際需求,選擇不同尺寸和形狀的燒結(jié)模具,從而制得不同尺寸和形狀的復(fù)合材料。在步驟(3)中,所述熱壓燒結(jié)的溫度可為600~1000℃,熱壓燒結(jié)的壓力可為30MPa以上。在步驟(3)中,所述退火處理的溫度可為250~500℃,退火處理的時(shí)間可為4~72h。本發(fā)明制備的低膨脹高導(dǎo)熱銅-不銹因瓦合金復(fù)合材料可以在退火處理后直接應(yīng)用,也可以再經(jīng)過(guò)軋制等工藝處理后再投入使用。另外,本發(fā)明還可以將銅-不銹因瓦合金自包裹復(fù)合粉與純Cu粉進(jìn)行混合燒結(jié),來(lái)調(diào)節(jié)復(fù)合材料的熱膨脹系數(shù)和熱導(dǎo)率。眾所周知,Cu原子與Fe,Co,Cr原子是相互排斥的,在低溫條件下,Cu在Fe,Co,Cr中的固溶度很低,而在高溫條件下存在著富Cu相與富Fe-Co-Cr相的液相兩相分離區(qū),采用普通的復(fù)合材料制備方法容易發(fā)生偏析,無(wú)法將Cu和富Fe-Co-Cr相良好的結(jié)合在一起。本發(fā)明恰恰利用Cu原子與Fe,Co,Cr原子相互排斥這一點(diǎn),首先通過(guò)相圖計(jì)算技術(shù),設(shè)計(jì)復(fù)合材料的成分,使其成分中存在富Cu相與富Fe-Co-Cr相的液相兩相分離區(qū),進(jìn)而采用氣霧化制粉技術(shù),一次性地制備出核/殼型自包裹復(fù)合粉體,并且使富Cu相形成殼,富Fe-Co-Cr相形成不銹因瓦合金并成為復(fù)合粉體的核(如圖1、圖2所示),其中復(fù)合粉體可以是單核也可以是多核,單核粉體和多核粉體的比例可以通過(guò)控制成分和氣霧化工藝條件進(jìn)行調(diào)節(jié)。進(jìn)而通過(guò)熱壓燒結(jié)工藝,將復(fù)合粉體燒結(jié)成型,制備出均勻致密的燒結(jié)體材料,最后將燒結(jié)體進(jìn)行退火處理,即可制得銅-不銹因瓦合金復(fù)合材料。本發(fā)明的工藝流程圖如圖3所示。本發(fā)明的技術(shù)方案有以下優(yōu)點(diǎn):1)采用氣霧化制粉技術(shù)制備銅-不銹因瓦合金自包裹復(fù)合粉體,可以將相互排斥的Cu和不銹因瓦合金有效復(fù)合,使復(fù)合材料同時(shí)擁有Cu的優(yōu)良導(dǎo)熱性能和不銹因瓦合金的低膨脹性能。2)將復(fù)合粉體通過(guò)粉末冶金方法熱壓燒結(jié)成型,可以使復(fù)合材料中的富銅相和不銹因瓦合金相均勻分布,不會(huì)發(fā)生偏析,使復(fù)合材料的組織均勻穩(wěn)定,各向同性。3)在燒結(jié)階段,可以根據(jù)實(shí)際需要,選擇不同尺寸和形狀的燒結(jié)模具,本發(fā)明的復(fù)合粉體可以良好得填充到燒結(jié)模具各個(gè)部分,進(jìn)而制得不同尺寸、不同形狀的復(fù)合材料,尤其適合于制備大尺寸或者復(fù)雜形狀的復(fù)合材料產(chǎn)品。4)本發(fā)明復(fù)合粉體的富Cu相外殼容易燒結(jié),可以在低溫條件下燒結(jié)成型,且燒結(jié)體致密度高。燒結(jié)溫度的降低,不僅降低了生產(chǎn)成本,而且還可以防止高溫條件下Cu原子與Fe、Co、Cr發(fā)生互擴(kuò)散而導(dǎo)致不銹因瓦合金成分的偏離,從而影響低膨脹性能。5)本發(fā)明復(fù)合材料的最終結(jié)構(gòu)為富Cu相基體上均勻分布著不銹因瓦合金相的質(zhì)點(diǎn),富Cu相可以提高復(fù)合材料整體的加工性能,拓展了復(fù)合材料的應(yīng)用范圍。與現(xiàn)有技術(shù)相比,本發(fā)明具有以下優(yōu)勢(shì):1.本發(fā)明的復(fù)合材料性能優(yōu)良。本發(fā)明首先采用氣霧化制粉技術(shù),制備出銅-不銹因瓦合金自包裹復(fù)合粉體,將相互排斥的Cu和不銹因瓦合金進(jìn)行有效復(fù)合,使復(fù)合材料同時(shí)擁有Cu的優(yōu)良導(dǎo)熱性能和不銹因瓦合金的低膨脹性能和抗腐蝕性能,滿足了人們對(duì)電子封裝材料的性能不斷提高的要求。為了評(píng)價(jià)本發(fā)明復(fù)合材料的性能,本發(fā)明的研究者還通過(guò)真空電弧熔煉法制備了Cu(Fe64Ni36)合金,以及將純Cu粉與不銹因瓦合金粉直接進(jìn)行燒結(jié),并測(cè)試了各個(gè)樣品的熱膨脹系數(shù)和熱導(dǎo)率,其結(jié)果如表1所示。從表1中不難看出,與Cu-Fe64Ni36合金和純Cu粉/不銹因瓦合金粉直接燒結(jié)得到的合金相比,本發(fā)明的銅-不銹因瓦合金復(fù)合材料具備較好的綜合物理性能。2.本發(fā)明的復(fù)合材料性能穩(wěn)定,在各個(gè)方向上都具有優(yōu)良的性能,各向同性。本發(fā)明將復(fù)合粉體通過(guò)粉末冶金方法熱壓燒結(jié)成型,可以使復(fù)合材料中的富銅相和不銹因瓦合金相均勻分布,不會(huì)發(fā)生偏析,使復(fù)合材料的組織均勻穩(wěn)定,在各個(gè)方向上都具有優(yōu)良的性能,即各向同性。與層狀復(fù)合材料相比,本發(fā)明具有明顯優(yōu)勢(shì)。3.本發(fā)明產(chǎn)品不受尺寸或形狀限制,可以是塊體、板材、片狀或者其他復(fù)雜形狀。本發(fā)明在燒結(jié)階段,可以根據(jù)實(shí)際需要,選擇不同尺寸和形狀的燒結(jié)模具,另一方面,本發(fā)明的復(fù)合粉體可以良好得填充到燒結(jié)模具各個(gè)部分,進(jìn)而制得不同尺寸、不同形狀的復(fù)合材料,尤其適合于制備大尺寸或者復(fù)雜形狀的復(fù)合材料產(chǎn)品。4.本發(fā)明加工方法簡(jiǎn)單,不需要鍛造、高壓軋制等復(fù)雜工序,產(chǎn)品一次成型,生產(chǎn)成本低;氣霧化制粉和粉末冶金是已發(fā)展成熟的工業(yè)技術(shù),可以大規(guī)模批量化生產(chǎn),生產(chǎn)效率高。5.本發(fā)明還可以選擇性的添加W、Mo等元素,改善復(fù)合材料的強(qiáng)度等性能,以適應(yīng)特殊場(chǎng)合的使用需求。本發(fā)明的復(fù)合材料將銅合金的優(yōu)良導(dǎo)熱性能以及不銹因瓦合金的低膨脹性能有機(jī)融合在一起,彌補(bǔ)了單一材料的缺陷,并且復(fù)合材料的組織均勻穩(wěn)定,在各個(gè)方向上都具有優(yōu)良的性能,即各向同性。本發(fā)明生產(chǎn)成本低,加工方法簡(jiǎn)單,不需要鍛造、高壓軋制等復(fù)雜工序,產(chǎn)品一次成型,不受尺寸和形狀限制,可以制備大尺寸器件以及形狀復(fù)雜的器件;同時(shí)氣霧化制粉和粉末冶金是已發(fā)展成熟的工業(yè)技術(shù),可以大規(guī)模批量化生產(chǎn)。另外,選擇性添加的W、Mo等元素可以改善復(fù)合材料的強(qiáng)度等性能,以適應(yīng)不同的使用性能要求。本發(fā)明的復(fù)合材料在電子封裝、精密儀器儀表、模具等領(lǐng)域均有廣闊的應(yīng)用前景。附圖說(shuō)明圖1為本發(fā)明中自包裹型復(fù)合粉體內(nèi)部組織示意圖。圖2為本發(fā)明中自包裹型復(fù)合粉體內(nèi)部組織SEM圖。圖(a)為單核;(b)為多核。圖3為本發(fā)明的工藝流程圖。圖4為本發(fā)明復(fù)合粉體燒結(jié)體的組織圖。具體實(shí)施方式實(shí)施例1:以高純度金屬Cu、Fe、Co、Cr為原料,按Cu700g,F(xiàn)e110g,Co160g,Cr30g進(jìn)行配置,實(shí)際配置過(guò)程中的誤差保證在0.001g以內(nèi)。先將稱量好的合金原料超聲清洗后,置于霧化設(shè)備的真空感應(yīng)爐中。將霧化設(shè)備腔體抽至1×10-3Pa的真空度,充氬氣至略大于1個(gè)大氣壓,待合金完全熔化成液體后啟動(dòng)氣壓裝置,使熔融液體流入霧化室,同時(shí)迅速打開(kāi)高壓氬氣閥(氣壓為3~10MPa)噴射高壓氣體使金屬液體霧化。當(dāng)熔融液體全部流入霧化室中,即可關(guān)閉氬氣氣流閥。待霧化設(shè)備冷卻后,可于霧化設(shè)備最下端的集料罐中得到粉末狀樣品。本發(fā)明的燒結(jié)過(guò)程在氬氣保護(hù)氛圍下進(jìn)行,燒結(jié)溫度為850℃,壓力為30MPa。待燒結(jié)體冷卻后,在500℃下進(jìn)行退火處理8h后空冷,即可得到銅-不銹因瓦合金復(fù)合材料。EPMA分析結(jié)果表明,復(fù)合材料中富Fe-Co-Cr相的成分近似為Fe37Co54Cr9,即形成了不銹因瓦合金。經(jīng)測(cè)試,該復(fù)合材料的熱膨脹系數(shù)為10.66×10-6K-1,熱導(dǎo)率為107.4W·m-1·K-1,如表1所示。實(shí)施例2:以高純度金屬Cu、Fe、Co、Cr為原料,按Cu400g,F(xiàn)e220g,Co320g,Cr60g進(jìn)行配置,實(shí)際配置過(guò)程中的誤差保證在0.001g以內(nèi)。先將稱量好的合金原料超聲清洗后,置于霧化設(shè)備的真空感應(yīng)爐中。將霧化設(shè)備腔體抽至1×10-3Pa的真空度,充氬氣至略大于1個(gè)大氣壓,待合金完全熔化成液體后啟動(dòng)氣壓裝置,使熔融液體流入霧化室,同時(shí)迅速打開(kāi)高壓氬氣閥(氣壓為3~10MPa)噴射高壓氣體使金屬液體霧化。當(dāng)熔融液體全部流入霧化室中,即可關(guān)閉氬氣氣流閥。待霧化設(shè)備冷卻后,可于霧化設(shè)備最下端的集料罐中得到粉末狀樣品。本發(fā)明的燒結(jié)過(guò)程在氬氣保護(hù)氛圍下進(jìn)行,燒結(jié)溫度為900℃,壓力為30MPa。待燒結(jié)體冷卻后,在300℃下進(jìn)行退火處理12h后空冷,即可得到銅-不銹因瓦合金復(fù)合材料。EPMA分析結(jié)果表明,復(fù)合材料中富Fe-Co-Cr相的成分近似為Fe37Co54Cr9,即形成了不銹因瓦合金。經(jīng)測(cè)試,該復(fù)合材料的熱膨脹系數(shù)為6.78×10-6K-1,熱導(dǎo)率為56.4W·m-1·K-1,如表1所示。實(shí)施例3:以高純度金屬Cu、Fe、Co、Cr為原料,按Cu250g,F(xiàn)e280g,Co400g,Cr70g進(jìn)行配置,實(shí)際配置過(guò)程中的誤差保證在0.001g以內(nèi)。先將稱量好的合金原料超聲清洗后,置于霧化設(shè)備的真空感應(yīng)爐中。將霧化設(shè)備腔體抽至1×10-3Pa的真空度,充氬氣至略大于1個(gè)大氣壓,待合金完全熔化成液體后啟動(dòng)氣壓裝置,使熔融液體流入霧化室,同時(shí)迅速打開(kāi)高壓氬氣閥(氣壓為3~10MPa)噴射高壓氣體使金屬液體霧化。當(dāng)熔融液體全部流入霧化室中,即可關(guān)閉氬氣氣流閥。待霧化設(shè)備冷卻后,可于霧化設(shè)備最下端的集料罐中得到粉末狀樣品。本發(fā)明的燒結(jié)過(guò)程在氬氣保護(hù)氛圍下進(jìn)行,燒結(jié)溫度為600℃,壓力為40MPa。待燒結(jié)體冷卻后,在400℃下進(jìn)行退火處理10h后空冷,即可得到銅-不銹因瓦合金復(fù)合材料。EPMA分析結(jié)果表明,復(fù)合材料中富Fe-Co-Cr相的成分近似為Fe37Co54Cr9,即形成了不銹因瓦合金。經(jīng)測(cè)試,該復(fù)合材料的熱膨脹系數(shù)為5.75×10-6K-1,熱導(dǎo)率為42.2W·m-1·K-1,本發(fā)明復(fù)合材料的熱膨脹系數(shù)和熱導(dǎo)率測(cè)試結(jié)果如表1所示。表1本發(fā)明中自包裹型復(fù)合粉體內(nèi)部組織示意圖參見(jiàn)圖1,本發(fā)明中自包裹型復(fù)合粉體內(nèi)部組織SEM圖參見(jiàn)圖2,本發(fā)明的工藝流程圖參見(jiàn)圖3,本發(fā)明復(fù)合粉體燒結(jié)體的組織圖參見(jiàn)圖4。本發(fā)明首先利用相圖計(jì)算技術(shù)設(shè)計(jì)合金成分,使其存在富Cu相與富Fe-Co-Cr相液相兩相分離區(qū);再采用氣霧化制粉方法,一次性制備出核/殼型自包裹復(fù)合粉體,并且使富Cu相形成殼層,富Fe-Co-Cr相形成不銹因瓦合金并成為復(fù)合粉體的核;進(jìn)而采用粉末冶金工藝,將復(fù)合粉體進(jìn)行熱壓燒結(jié),制備出均勻致密的燒結(jié)體材料;最后將燒結(jié)體進(jìn)行退火處理,即得低膨脹高導(dǎo)熱銅-不銹因瓦合金復(fù)合材料。該復(fù)合材料的成分按質(zhì)量百分比為:Cu20%~75%,F(xiàn)e9%~30%,Co12%~45%,Cr2%~8%,以及可選擇性的少量添加W,Nb,Ta,Mo,C,B,V等0~5%。本發(fā)明的復(fù)合材料組織均勻,性能穩(wěn)定,各向同性;本發(fā)明生產(chǎn)成本低,加工方法簡(jiǎn)單,可以大規(guī)模批量化生產(chǎn),產(chǎn)品不受尺寸和形狀限制,在電子封裝、精密儀器儀表、模具等領(lǐng)域均有廣闊的應(yīng)用前景。