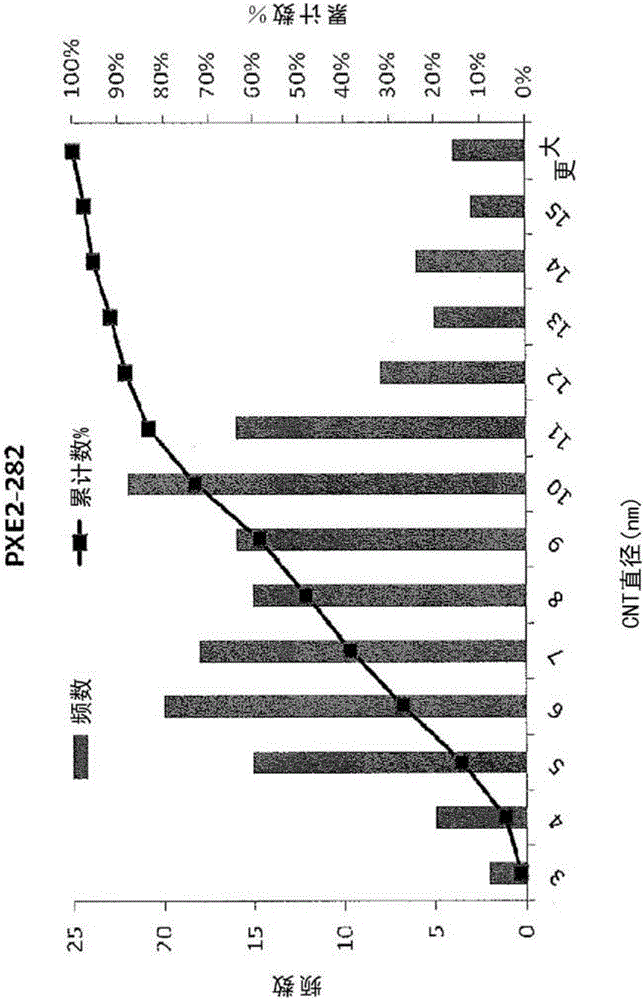
發(fā)明背景本申請(qǐng)要求享有2009年7月17日提交的美國(guó)臨時(shí)專利申請(qǐng)第61/226,438號(hào)的優(yōu)先權(quán)。該美國(guó)臨時(shí)專利申請(qǐng)第61/226438號(hào)的全部通過(guò)引用結(jié)合在此。眾所周知,碳納米管以單壁和多壁的構(gòu)造形式存在。每種構(gòu)造都能提供某些優(yōu)點(diǎn)。單壁納米管由于構(gòu)造異常發(fā)生率低,因此優(yōu)選用于電子應(yīng)用。然而,多壁納米管通常成本更低,如果能夠控制形成的納米管壁的數(shù)量,就可以在電子應(yīng)用中提供符合要求的性能。不幸的是,目前用于生產(chǎn)多壁碳納米管的方法沒(méi)有能力在所得納米管的結(jié)構(gòu)中控制所得的管壁數(shù)量。結(jié)果,目前制得的多壁碳納米管直徑通常為約3-35nm,并包括3-40個(gè)同心石墨烯(graphene)層,即管壁。各層為同軸排列的碳原子圓柱體,其層間距為約0.37nm。管壁和外徑尺寸的這一寬泛分布的范圍限制了多壁納米管用于導(dǎo)電應(yīng)用、導(dǎo)熱應(yīng)用和機(jī)械增強(qiáng)應(yīng)用的價(jià)值。相比之下,多壁納米管如果有相對(duì)較窄分布范圍的管壁和外徑,則可提供接近于單壁納米管的導(dǎo)電特征。此外,多壁納米管能以更低的成本提供這類改進(jìn)。進(jìn)一步,管壁數(shù)量和外徑分布范圍窄的多壁納米管批料(batch)與分布范圍寬的批料相比,能提供增強(qiáng)的導(dǎo)熱性和機(jī)械強(qiáng)度。盡管可能有人會(huì)想到簡(jiǎn)單地從目前制造的分布范圍寬的多壁碳納米管分離分布范圍窄的多壁碳納米管,但實(shí)現(xiàn)這一任務(wù)的技術(shù)并不存在。因此,現(xiàn)在可獲取的多壁納米管完全是以不合要求的寬分布管壁和外徑的批料或批量提供的。如以下所詳細(xì)討論的,本發(fā)明可提供管壁和直徑分布范圍窄的多壁納米管的批料。與熱塑性塑料混合時(shí),所述分布范圍窄的批料可以提供能與單壁納米管匹敵的、比現(xiàn)有可獲取的多壁納米管批料明顯改善的導(dǎo)電特征。本發(fā)明還提供用于制備管壁和外徑分布范圍窄的多壁納米管批料的催化劑和方法。技術(shù)實(shí)現(xiàn)要素:概述在一個(gè)實(shí)施方案中,本發(fā)明提供了一種催化劑前體,所述催化劑前體包括氧化鋁(Al2O3)、氧化鎂(MgO)和鋁酸鎂(MgAl2O4)作為催化劑載體。該催化劑前體還包括鈷、鐵和鉬的金屬氧化物。優(yōu)選的金屬氧化物包括,但不必受限于一種或多種以下的混合的金屬氧化物:CoFe2O4、CoMoO4、CoxMoO4、Fe2(MoO4)3、CoxFeyMoO4;其中x和y表示Co和Fe相對(duì)Mo的原子比,并且x為約1.6-約6.5,y為約0.1-約10.5。含兩種或更多種金屬組分的混合的金屬氧化物為優(yōu)選,因?yàn)閱我唤饘俚难趸飼?huì)產(chǎn)生碳纖維及其它形式的碳。在另一個(gè)實(shí)施方案中,本發(fā)明提供了用于制備催化劑前體和催化劑的方法。所述方法涉及首先制備包括以下兩種或更多種的混合的金屬化合物的溶液:選自乙酸鈷、硝酸鈷的鈷化合物;選自乙酸鐵、硝酸鐵的鐵化合物;選自七鉬酸銨和二鉬酸銨的鉬化合物;以及硝酸鎂。使該溶液與過(guò)量的氫氧化鋁粉末反應(yīng),反應(yīng)產(chǎn)物隨后形成糊狀物。形成糊狀物造成反應(yīng)產(chǎn)物團(tuán)聚,從而得到約100-1400微米的粒徑分布。隨后使反應(yīng)產(chǎn)物干燥,減小其尺寸并焙燒,得到催化劑前體。目前優(yōu)選的催化劑前體的粒徑分布為70μm-150μm。前體轉(zhuǎn)化成催化劑要求將催化劑前體放置在適合用作流化床反應(yīng)器的反應(yīng)室內(nèi)。使惰性氣體流過(guò)反應(yīng)室,以對(duì)催化劑前體進(jìn)行流化并預(yù)熱至所要求的反應(yīng)溫度,所述惰性氣體選自氮?dú)?、氬氣或氦氣。在所要求的反?yīng)溫度下達(dá)到穩(wěn)態(tài)條件時(shí),用乙烯和惰性氣體的共混物代替惰性氣體。在與乙烯和惰性氣體共混物接觸的第一個(gè)5分鐘的過(guò)程中,催化劑前體轉(zhuǎn)化成所要求的催化劑。在轉(zhuǎn)化過(guò)程中,鈷和鐵的氧化物被還原成相應(yīng)的金屬。此外,部分氧化鐵被還原成碳化鐵(Fe3C),氧化鉬被還原成碳化鉬(Mo2C)。更進(jìn)一步,本發(fā)明提供生產(chǎn)多壁碳納米管的方法,其中所得多壁納米管批料就組成納米管的管壁數(shù)而言有窄的分布,并且所得納米管外徑也有窄的分布。在本發(fā)明的方法中,催化劑前體如以上所討論的進(jìn)行制備。催化劑前體轉(zhuǎn)化成還原的金屬催化劑后,使乙烯/惰性氣體在所要求的反應(yīng)條件下繼續(xù)流動(dòng)一段時(shí)間,所述時(shí)間應(yīng)足以獲得多壁碳納米管。乙烯/惰性氣體含有約10-約80體積%的乙烯,并且以足夠能使催化劑粒子床流化的速度流動(dòng)。約10-約30分鐘的反應(yīng)期后,切斷流向反應(yīng)室的氣流,并取出載負(fù)(carrying)多壁納米管的粒子。廢(spent)催化劑所載負(fù)的約95-約98%的所得碳產(chǎn)物為碳納米管。約60-約90%的所得多壁碳納米管批料有3-6個(gè)管壁,并且外徑為約3nm-約7nm。因此,本發(fā)明還提供包含碳納米管的新產(chǎn)物,所述碳納米管具有3-6個(gè)管壁,并且外徑為約3nm-約7nm。附圖說(shuō)明圖1提供了氧化鋁載體上各種催化劑組合物的碳收率和碳納米管直徑特征的表格說(shuō)明。圖2A提供了對(duì)應(yīng)于圖1中PXE2-282的催化組合物的碳納米管直徑分布的圖形說(shuō)明。圖2B提供了對(duì)應(yīng)于圖1中PXE2-285的催化組合物的碳納米管直徑分布的圖形說(shuō)明。圖2C提供了對(duì)應(yīng)于圖1中PXE2-288的催化組合物的碳納米管直徑分布的圖形說(shuō)明。圖2D提供了對(duì)應(yīng)于圖1中PXE2-295的催化組合物的碳納米管直徑分布的圖形說(shuō)明。圖3為反應(yīng)溫度和氣體組成對(duì)直徑較小的管的碳收率和選擇性的影響的表格說(shuō)明。圖4A描繪了用TEM確定的對(duì)應(yīng)于SMW-100碳納米管產(chǎn)物的碳納米管直徑分布。圖4B描繪了用TEM確定的對(duì)應(yīng)于MWCNTA碳納米管產(chǎn)物的碳納米管直徑分布。圖4C描繪了用TEM確定的對(duì)應(yīng)于MWCNTB碳納米管產(chǎn)物的碳納米管直徑分布。圖4D描繪了用TEM確定的對(duì)應(yīng)于MWCNTC碳納米管產(chǎn)物的碳納米管直徑分布。圖5是聚碳酸酯中的SMW-100碳納米管和3種商業(yè)碳納米管產(chǎn)品的體積電阻率的圖形說(shuō)明。圖6A是含有尼龍66樹脂的復(fù)合材料的前后表面電阻的圖形說(shuō)明,所述復(fù)合材料載負(fù)了2.5重量%的SMW-100碳納米管或載負(fù)了2.5重量%的商業(yè)途徑可獲得的多壁碳納米管。圖6B是含有尼龍66樹脂的復(fù)合材料的前后表面電阻的圖形說(shuō)明,所述復(fù)合材料載負(fù)了3.5重量%的SMW-100碳納米管或載負(fù)了3.5重量%的商業(yè)途徑可獲得的多壁碳納米管。圖7描繪了包括不同形式的碳納米管的薄膜的表面電阻率。優(yōu)選實(shí)施方案的詳細(xì)說(shuō)明本發(fā)明以下詳細(xì)公開內(nèi)容將說(shuō)明催化劑前體、制備催化劑前體的方法以及將其轉(zhuǎn)化成所要求的催化劑的方法。另外,本發(fā)明提供了在所述催化劑上產(chǎn)生所要求的多壁碳納米管批料的方法,其中所述碳納米管產(chǎn)物具有窄分布范圍的管壁和外徑。如在本說(shuō)明書中所用,“碳含量”是指基于碳的最終產(chǎn)品(碳納米管+催化劑)的百分比。所以,如果250g的最終產(chǎn)品是碳并且最終產(chǎn)品總共是500g,那么碳含量就是50%或50.0(如圖1中所用)。如在本說(shuō)明書中所用,“碳收率”是指相對(duì)于反應(yīng)中所用的催化劑的量所產(chǎn)生的碳產(chǎn)物的量。其定義如以下公式:(最終產(chǎn)品中碳的量(g)/催化劑的量(g))x100。例如,使用了250g的催化劑、產(chǎn)生了250g碳產(chǎn)物的反應(yīng)的碳收率為100%((50g/250g)x100=100%)。如在本說(shuō)明書中所使用,(包括圖2A-2D;2A-4D),“頻數(shù)(frequency)”是指在具有規(guī)定直徑(x軸)的樣品中碳納米管的數(shù)量。例如在圖2A中,大約有20個(gè)直徑是約6nm的碳納米管。1.催化劑前體和催化劑本發(fā)明的催化劑前體具有負(fù)載在氧化鋁和鋁酸鎂粒子上的混合的金屬氧化物的表面相?;旌系慕饘傺趸锸呛袃煞N或更多金屬組分的氧化物。另外,氧化鋁/鋁酸鎂載體載負(fù)氧化鎂的表面處理。氧化鋁/鋁酸鎂粒子載負(fù)的氧化鎂不一定是包圍層。MgO與Al2O3的原子比為約0.02-0.04。換言之,對(duì)于0.02:1的比例,對(duì)于每個(gè)原子的MgO有50個(gè)原子的Al2O3,而在0.04:1的比例時(shí),對(duì)于每個(gè)原子的MgO有25個(gè)原子的Al2O3。如以下所指出,這些計(jì)算中所使用的部分MgO可以轉(zhuǎn)變成MgAl2O4?;旌系慕饘傺趸锏膬?yōu)選的表面相包括但不限于以下一種或多種:CoFe2O4、CoMoO4、CoxMoO4、CoxFeyMoO4、Fe2(MoO4)3。典型地,金屬氧化物在催化劑前體上提供以下重量百分濃度的金屬:約0.5-約2.0的Co;約0.3-約2.0%的Mo;和約0-約3.0%的Fe。因此,對(duì)于CoxFeyMoO4,x可以是約1.6-6.5,且y可以是0.1-10.5。更優(yōu)選地,x可以是約3.3且y為2.6-6.3。在任何情況下,催化劑前體上都應(yīng)存在足量的金屬氧化物,使所得催化劑包括以下重量百分比的金屬組分:約0.5-約2.0的Co;約0.3-約2.0%的Mo;和約0-約3.0%的Fe。在所得催化劑中,鐵可以作為還原的金屬或碳化物(Fe3C)存在,而鉬可以作為碳化物(Mo2C)存在。優(yōu)選地,基于催化劑前體組合物的重量,每種金屬組分的重量百分?jǐn)?shù)為:Co約0.75-約1.5%;Mo約0.5-約1.0%;和Fe約0.5-約2.0%。相應(yīng)地,活性金屬組分以以下原子比存在,其中Mo為定值:Co與Mo之比為約1.6-約6.5,更優(yōu)選約2.44-約4.88,最優(yōu)選約3.3;Fe與Mo之比為約0-約10.5,更優(yōu)選約1.75-約6.98,最優(yōu)選約2.62-約6.28。催化劑載體上Mg離子的存在可減少氧化鋁載體表面上強(qiáng)酸位點(diǎn)的數(shù)量。通過(guò)減少催化劑載體表面上強(qiáng)酸位點(diǎn)的量,使用改進(jìn)的催化劑可主要產(chǎn)生碳納米管,并且產(chǎn)生明顯減少的無(wú)定形碳或其它碳產(chǎn)物。如以下所討論,使用改進(jìn)催化劑的催化反應(yīng)可產(chǎn)生至少90%、優(yōu)選高于98%的碳納米管,以作為所得碳產(chǎn)物。本發(fā)明的催化劑前體粒徑優(yōu)選約20μm-約500μm。優(yōu)選地,所述粒徑約20μm-250μm。更優(yōu)選地,催化劑前體粒徑約20μm-約150μm。在以下討論的目前優(yōu)選的方法中,粒徑范圍約70μm-約150μm。通過(guò)將金屬氧化物還原為相應(yīng)的金屬和金屬碳化物,即Fe°、Fe3C、Co°和Mo2C,可以將如上所述的催化劑前體轉(zhuǎn)化為催化劑粒子。催化劑粒子具有與催化劑前體相同存在的金屬原子比。所得納米尺寸的金屬鈷和金屬鐵的沉積物可以決定催化劑粒子上產(chǎn)生的多壁納米管的內(nèi)徑。另外,存在Mo2C可分散或隔開金屬鈷,從而避免了鈷的燒結(jié),并提供所要求的鈷的粒徑。通常,載體上所得金屬沉積物的直徑是約1.5nm-約3.0nm。優(yōu)選地,所得還原鐵和還原鈷金屬的沉積物直徑是約1.5nm-約2.2nm。另外,如以上所指出,最終的催化劑粒子比只利用氧化鋁作為載體的催化劑粒子有更少的表面酸性位點(diǎn)??傊?,本發(fā)明的最終催化劑粒子的粒徑為約20μm-約500μm。優(yōu)選地,粒徑為約20μm-250μm。更優(yōu)選地,催化劑前體粒徑為約20μm-約150μm。在以下討論的目前優(yōu)選的制造多壁納米管的方法中,目前優(yōu)選的粒徑為約70μm-約150μm。所述催化劑粒子包含:a.約91.0-97.6重量%、優(yōu)選約94.8-約97.3重量%的γ氧化鋁(γ-Al2O3);b.約0.5-約3.3重量%、優(yōu)選0.5-1.0重量%的Mg(以MgO和MgAl2O4的形式);c.約0.5-約2.0重量%、優(yōu)選約0.75-約1.5重量%的還原的Co;d.約0.3-約2.0重量%、優(yōu)選0.5-1.0重量%的Mo2C形式的Mo;以及,e.約0-約3.0重量%、優(yōu)選0.5-2.0重量%的還原鐵和碳化鐵(Fe°、Fe3C)形式的Fe。典型地,少于2.0重量%的催化劑粒子可以是金屬碳化物。用于多壁碳納米管催化生產(chǎn)的還原金屬的原子比與催化劑前體相比不會(huì)有很大變化,因?yàn)闆](méi)有大量產(chǎn)生金屬碳化物。2.制備催化劑前體粒子和催化劑粒子的方法本發(fā)明提供制備適用于催化形成多壁碳納米管的催化劑前體和催化劑的方法。尤其是,本發(fā)明的催化劑能夠生產(chǎn)管壁和直徑分布范圍窄的多壁碳納米管的批料。在一個(gè)優(yōu)選的實(shí)施方案中,所述方法涉及首先制備包含以下兩種或更多種的混合的金屬化合物的溶液:選自乙酸鈷、硝酸鈷的鈷化合物;選自乙酸鐵、硝酸鐵的鐵化合物;選自七鉬酸銨和二鉬酸銨的鉬化合物;以及硝酸鎂。優(yōu)選的溶液包括水中的乙酸鈷、硝酸鐵、七鉬酸銨和硝酸鎂。與所選的鈷化合物無(wú)關(guān),溶液含有的鈷離子濃度為約20g/L-約50g/L;鉬離子濃度為約10.5g/L-約70.3g/L;鐵離子濃度為約35g/L-約105g/L;并且,Mg離子濃度為約6.7g/L-約27.0g/L。優(yōu)選的溶液含有的鈷離子為約26.7g/L-約40.0g/L;鉬離子為約17.6g/L-約35.2g/L;鐵離子為約52.7g/L-約70.1g/L;并且,鎂離子為約6.7g/L-約13.5g/L。最優(yōu)選的是以下離子濃度的溶液:鈷離子為約33.4g/L;鉬離子為約17.6g/L;鐵離子為約63.1g/L;并且鎂離子為約6.7g/L。合理選擇金屬離子濃度可加強(qiáng)所要求的混合的金屬氧化物的形成。因此,要求在溶液中提供合理化學(xué)計(jì)量比的金屬,以實(shí)現(xiàn)該結(jié)果。以上引述的金屬離子然后與氫氧化鋁反應(yīng),得到金屬氫氧化物和其它離子化合物的混合物,包括但不限于化學(xué)計(jì)量比可以不同于以下所示的氫氧化物:Mg(OH)2,、Fe(OH)3、Co(OH)2、CoMoO4·nH2O、Fe2(MoO4)3·nH2O。典型地上述反應(yīng)在室溫下進(jìn)行約2-4小時(shí)。反應(yīng)產(chǎn)物有類似糊狀物的稠度(consistency),這可促進(jìn)粒子團(tuán)聚。優(yōu)選地,所述糊狀物的含水量為約20-40重量%水。更優(yōu)選糊狀物含有約25-約30重量%的水。如果粒子團(tuán)聚有要求,可操控(manipulate)類似糊狀物的產(chǎn)物,以得到粒徑為約100μm-約1400μm的團(tuán)聚粒子。通常粒子可以在反應(yīng)期間團(tuán)聚。優(yōu)選地,團(tuán)聚粒子為約100μm-約500μm。在優(yōu)選的方法中,團(tuán)聚粒子在捏合或混合糊狀物的機(jī)器中混合約20-約50分鐘。捏合后,使產(chǎn)物陳化另外約2-3小時(shí)??偟臅r(shí)間長(zhǎng)度可取決于批料大小。對(duì)于約200-約2000克的批料,優(yōu)選的捏合時(shí)間為約30分鐘。更大的批料可以要求更長(zhǎng)的混合時(shí)間。團(tuán)聚后,對(duì)粒子進(jìn)行干燥和篩分,分離低于1400μm的粒子。優(yōu)選地,篩分步驟提供約100μm-約500μm的粒子。將團(tuán)聚粒子干燥至約10-20重量%水的含水量。優(yōu)選地,干燥粒子含低于15重量%的水。干燥步驟優(yōu)選在約30℃-50℃的溫度下進(jìn)行。干燥和篩分后,在約400℃-600℃的溫度下在流動(dòng)氣體下煅燒粒子約3小時(shí)-約8小時(shí)的時(shí)間。更優(yōu)選煅燒步驟在約400℃-500℃的溫度下進(jìn)行約3.5小時(shí)-約4.5小時(shí)。最優(yōu)選地煅燒步驟在約440℃-460℃的溫度下進(jìn)行約3.5小時(shí)-約4.5小時(shí)。優(yōu)選地,煅燒氣體選自空氣、氮?dú)狻⒑饧捌浠旌衔?。典型地,?yōu)選的煅燒氣體是煅燒條件下惰性的氣體。干燥和煅燒步驟將團(tuán)聚粒子減小至約20μm-約500μm的粒徑?;蛘撸W釉陟褵斑M(jìn)行篩分,且如有必要進(jìn)行研磨,以使煅燒可以產(chǎn)生20μm-250μm的粒子。優(yōu)選地,煅燒產(chǎn)生約20μm-200μm的粒子。更優(yōu)選的是約20μm-150μm的粒子。在以下討論的優(yōu)選方法中,優(yōu)選的粒徑范圍是約70μm-約150μm。所得粒子基本上不含水,即水分不多于3重量%。粒子煅燒將金屬氫氧化物轉(zhuǎn)化成相應(yīng)的氧化物。例如,氫氧化鐵與鉬酸鹽煅燒得到鉬酸鐵(Fe2(MoO4)3)。類似地,氫氧化鈷與鉬酸鹽煅燒得到鉬酸鈷(CoMoO4)。進(jìn)一步,煅燒過(guò)程中Fe(OH)3和Co(OH)2結(jié)合產(chǎn)生CoFe2O4。最后,Mg(OH)2煅燒期間得到MgO,氫氧化鋁(Al(OH)3)轉(zhuǎn)化成γ氧化鋁,即γ-Al2O3。煅燒過(guò)程中,Mg(OH)2氧化還可防止在γ-Al2O3表面上形成強(qiáng)酸位點(diǎn)。所得表面構(gòu)造認(rèn)為是類似于Mg-Al-O的混合氧化物。在任何情況下,載負(fù)MgO的γ-Al2O3表面酸度明顯低于不存在Mg(OH)2時(shí)煅燒的γ-Al2O3的表面酸度。進(jìn)一步,在煅燒過(guò)程中,除了形成相應(yīng)的鎂和鋁的氧化物,與氫氧化鋁相鄰的一部分Mg+2離子產(chǎn)生平行反應(yīng)。在該反應(yīng)中,鎂離子在氧化鋁中的溶解性使得鎂能取代粒子表面附近的一部分氧化鋁四面體結(jié)構(gòu),從而產(chǎn)生鋁酸鎂(MgAl2O4),一種具有類似尖晶石結(jié)構(gòu)的化合物。形成鋁酸鎂優(yōu)于形成CoAl2O4和FeAlO3。因此,該有利的反應(yīng)可保護(hù)催化金屬在所得載體粒子表面上還原并轉(zhuǎn)化成的催化位點(diǎn)。尤其是,還原的鈷在所得載體表面上獲得納米粒子尺寸域的形式,鐵變?yōu)檫€原的鐵和碳化鐵,而鉬變?yōu)樘蓟f。碳化鐵和還原的鐵在催化劑載體表面上分散所述鈷,從而控制所得納米管的內(nèi)徑。所得催化劑載體具有一種構(gòu)造,在該構(gòu)造中鋁酸鎂結(jié)合到主要在粒子外層的γ-Al2O3晶體結(jié)構(gòu)中。另外,γ氧化鋁的表面載負(fù)MgO。不受限于理論,表面上的MgO可能是與粒子氧化鋁的混合氧化物,即Mg-Al-O混合氧化物。該構(gòu)造由鎂離子與氧化鋁在煅燒過(guò)程中的反應(yīng)產(chǎn)生。最后,優(yōu)選的催化劑載體優(yōu)選不含CoAl2O4和FeAlO3。如果存在FeAlO3,那么優(yōu)選催化劑載體包括低于0.5重量%的FeAlO3。如果存在CoAl2O4,那么優(yōu)選催化劑載體包括低于0.5重量%的CoAl2O4。催化劑載體粒子表面上存在鎂可減少催化劑前體載體粒子的表面酸度,和所得的催化劑載體粒子。通過(guò)減少載體粒子表面上酸性位點(diǎn)的數(shù)量,本發(fā)明的方法可改善碳納米管的生產(chǎn),并在隨后多壁碳納米管的生產(chǎn)過(guò)程中減少其它形式碳的形成。另外,存在鎂離子阻止形成CoAl2O4和FeAlO3,可防止催化金屬的損失。煅燒并減小粒徑后,所得催化劑前體粒子含有經(jīng)MgO表面處理的催化劑載體γ-Al2O3/MgAl2O4。另外,催化劑載體的表面載負(fù)所引述金屬氧化物的混合相。如以上所指出,優(yōu)選的混合的金屬氧化物包括但不必限于:CoFe2O4、CoMoO4、CoxMoO4、Fe2(MoO4)3、CoxFeyMoO4,其中CoxFeyMoO4為最優(yōu)選。將所得催化劑前體放置在反應(yīng)室中。優(yōu)選地,反應(yīng)室設(shè)計(jì)成當(dāng)流動(dòng)氣體通過(guò)該室及位于其中的粒子時(shí)能產(chǎn)生催化劑粒子的流化床。為了最后將催化劑前體轉(zhuǎn)化成催化劑,前體必須加熱并與含碳的氣體反應(yīng)。在以下用于生產(chǎn)多壁納米管的方法中,優(yōu)選的氣體碳化合物為乙烯。催化劑前體向催化劑的轉(zhuǎn)化發(fā)生在約600℃-700℃的溫度下、在與氣體碳化合物接觸的第一個(gè)10分鐘的過(guò)程中。在該時(shí)間周期中,金屬氧化物被還原成以上討論的相應(yīng)金屬和金屬碳化物。另外,形成Fe3C和Mo2C可防止還原鈷和鐵在載體表面上的燒結(jié)和團(tuán)聚。因此,所得還原的鈷的納米粒子優(yōu)選地具有約1.5nm-約3.5nm的直徑。更優(yōu)選地,催化劑載體表面上的還原的鈷金屬粒子具有約1.5nm-約2.2nm的直徑。還原鐵粒子具有類似的尺寸,即約1.5nm-約3.5nm,優(yōu)選約1.5nm-約2.2nm。所得催化劑包括經(jīng)MgO表面處理的γ-Al2O3/MgAl2O4載體,和在載體表面上的納米尺寸的Fe3C和Mo2C粒子。還原的金屬鈷可以由γ-Al2O3/MgAl2O4載負(fù),也可以在碳化鉬(Mo2C)和碳化鐵(Fe3C)上存在。另外,還原的鐵可以由γ-Al2O3/MgAl2O4載負(fù),也可以在碳化鉬(Mo2C)和碳化鐵(Fe3C)上存在。如以上討論的,所得催化劑粒子的粒徑為約20μm-約500μm。優(yōu)選地,所述粒徑為約20μm-250μm。更優(yōu)選地,催化劑粒徑為約20μm-約150μm。在目前優(yōu)選的制造多壁納米管的方法中,目前優(yōu)選的粒徑為約70μm-約150μm。催化劑粒子包括約91.0-97.6重量%的γ氧化鋁(γ-Al2O3),優(yōu)選約94.8-約97.3重量%;約0.5-約3.3重量%的Mg(以MgO和MgAl2O4的形式),優(yōu)選0.5-1.0重量%;約0.5-約2.0重量%的還原的Co,優(yōu)選約0.75-約1.5重量%;約0.3-約2.0重量%的Mo,以Mo2C的形式,優(yōu)選約0.5-約1.0重量%;以及約0-約3.0重量%的Fe,以還原的鐵和碳化鐵(Fe°、Fe3C)的形式,優(yōu)選0.5-2.0重量%。典型地,低于2.0重量%的催化劑粒子為金屬碳化物。用于多壁碳納米管催化生產(chǎn)的還原金屬的原子比與催化劑前體相比不會(huì)有很大變化,因?yàn)闆](méi)有大量產(chǎn)生金屬碳化物。在用于制備催化劑前體的替代方法中,從初始溶液中省去了硝酸鎂。在該方法中,氫氧化鎂粉末與氫氧化鋁粉末混合,并與金屬化合物的溶液反應(yīng),所述金屬化合物包括選自乙酸鈷、硝酸鈷的鈷化合物,選自乙酸鐵、硝酸鐵的鐵化合物,選自七鉬酸銨和二鉬酸銨的鉬化合物,及它們的混合物。優(yōu)選的溶液包括水中的乙酸鈷、硝酸鐵、七鉬酸銨和硝酸鎂。與所選的鈷化合物無(wú)關(guān),溶液含有的鈷離子濃度為約20g/L-約50g/L;鉬離子濃度為約10.5g/L-約70.3g/L;鐵離子濃度為約35g/L-約105g/L;并且,Mg離子濃度為約6.7g/L-約27.0g/L。優(yōu)選的溶液含有的鈷離子為約26.7g/L-約40.0g/L;鉬離子為約17.6g/L-約35.2g/L;鐵離子為約52.7g/L-約70.1g/L;并且,鎂離子為約6.7g/L-約13.5g/L。最優(yōu)選的是以下離子濃度的溶液:鈷離子為約33.4g/L;鉬離子為約17.6g/L;并且鐵離子為約63.1g/L。金屬離子溶液隨后與過(guò)量的粒徑約20μm-約150μm的氫氧化鋁粉末和粒徑約20μm-約150μm的氫氧化鎂粉末反應(yīng)。該反應(yīng)后,催化劑前體和隨后的催化劑的制備與如上所述方法相同。具有窄分布范圍的管壁和直徑的多壁碳納米管批料的制造有關(guān)多壁碳納米管的催化生產(chǎn)的以下討論基本上是有關(guān)催化劑前體和催化劑制備的以上討論的繼續(xù)。將煅燒的催化劑前體放置在反應(yīng)器室中后,所述粒子被流化并轉(zhuǎn)化為催化劑粒子。如以上所指出的,催化劑的粒徑可以是約20μm-約500μm。優(yōu)選地,粒徑為約20μm-250μm。更優(yōu)選地,催化劑前體粒徑為約20μm-約150μm。在目前優(yōu)選的制造多壁納米管的方法中,目前優(yōu)選的粒徑為約70μm-約150μm。因此,所述粒子很適合用于流化床反應(yīng)器中。將催化劑前體粒子置于反應(yīng)室中后,使氮?dú)鈿饬魍ㄟ^(guò)反應(yīng)室,從而使粒子床流化。將氮?dú)饧訜嶂烈欢ǖ臏囟?,所述溫度?yīng)足以將流化床內(nèi)的溫度提高至約600℃-約700℃。或者,反應(yīng)室可以位于爐中或其它合適的加熱裝置中。當(dāng)位于爐中時(shí),反應(yīng)室典型地通過(guò)爐和氣體兩者加熱。更優(yōu)選地,流化床預(yù)先加熱至約600℃-約650℃的溫度。最優(yōu)選地,流化床預(yù)先加熱至約610℃-630℃。本領(lǐng)域技術(shù)人員可以理解,例如氬氣或氦氣的其它非反應(yīng)性氣體可以代替氮?dú)狻nA(yù)加熱步驟的主要要求是流化床的流化并加熱至所要求的溫度,沒(méi)有不合要求的副反應(yīng)。流化床內(nèi)的溫度穩(wěn)定后,將通往所述床的氣流從氮?dú)廪D(zhuǎn)換到反應(yīng)性氣體。反應(yīng)性氣體為含有含碳?xì)怏w的非反應(yīng)載氣。優(yōu)選的載氣為氮?dú)?,?yōu)選的含碳?xì)怏w為乙烯;然而,例如氬氣或氦氣的其它載氣也能同樣很好地起作用。乙烯在氮?dú)庵械膬?yōu)選共混物按體積計(jì)為約10-80體積%。更優(yōu)選,反應(yīng)性氣體在氮中含約20-約50體積%的乙烯。最優(yōu)選的是在氮中含約20-約40體積%乙烯的反應(yīng)性氣體。含乙烯氣體的流速不取決于反應(yīng)室的尺寸。相反,通過(guò)反應(yīng)室的氣體的體積取決于反應(yīng)室內(nèi)催化劑前體的克數(shù)。流速為約70L/分鐘每kg催化劑前體-約150L/分鐘每kg催化劑前體。更優(yōu)選地,流速為約90L/分鐘每kg催化劑前體-約120L/分鐘每kg催化劑前體。含乙烯氣體與催化粒子的初始反應(yīng)將金屬氧化物還原為其相應(yīng)的金屬(Co°和Fe°)和金屬碳化物(Mo2C和Fe3C)。該還原步驟通常發(fā)生在反應(yīng)過(guò)程的第一個(gè)5分鐘內(nèi)。優(yōu)選地,反應(yīng)溫度為600℃-750℃。更優(yōu)選地,反應(yīng)溫度為610℃-650℃。最優(yōu)選地,反應(yīng)溫度為610℃。另外,在反應(yīng)過(guò)程的第一個(gè)10分鐘期間,乙烯與催化劑前體和隨后的催化劑粒子進(jìn)行的反應(yīng)為放熱反應(yīng)。因此,優(yōu)選的方法保持流化床溫度低于670℃。通過(guò)降低進(jìn)入反應(yīng)室氣體的溫度可以實(shí)現(xiàn)溫度的保持。如果使用了爐子,那么也可以降低爐子的溫度。優(yōu)選地將所述溫度保持低于650℃,因?yàn)楦叩臏囟葧?huì)導(dǎo)致增加產(chǎn)生的無(wú)定形碳。由于金屬氧化物被還原,乙烯氣體接觸所得催化粒子,并開始生長(zhǎng)多壁碳納米管。金屬氧化物還原成催化粒子后,反應(yīng)過(guò)程繼續(xù)約10-約40分鐘。更優(yōu)選地,金屬氧化物還原后的反應(yīng)過(guò)程繼續(xù)進(jìn)行約15-25分鐘。現(xiàn)在廢催化劑粒子載負(fù)的所得碳產(chǎn)物為98%,其不含無(wú)定形碳和其它形式的碳。因此,98%的碳產(chǎn)物為多壁的碳納米管。進(jìn)一步,所得多壁碳納米管主要有3-8個(gè)管壁。更優(yōu)選地,廢催化劑粒子載負(fù)的所得納米管主要有3-6個(gè)管壁,并且外徑為約4.0nm-約7.0nm。優(yōu)選地,至少60%的所得多壁碳納米管具有3-6個(gè)管壁,并且外徑為約4.0nm-約7.0nm。更優(yōu)選地,本發(fā)明的方法可獲得多壁碳納米管,其中至少75%的所得到多壁碳納米管具有3-6個(gè)管壁和約4.0nm-約7.0nm的直徑的所要求的窄分布范圍。更優(yōu)選地,廢催化劑載負(fù)的至少85%的所得多壁碳納米管具有3-6個(gè)管壁和約4.0nm-約7.0nm的外徑。最優(yōu)選地,連續(xù)保持催化劑粒子的流化,本發(fā)明可提供載負(fù)多壁碳納米管的廢催化劑,其中至少90%的所得多壁碳納米管可以具有3-6個(gè)管壁和約4.0nm-約7.0nm的直徑。以下實(shí)施例和試驗(yàn)數(shù)據(jù)并不限制本發(fā)明的性質(zhì)。相反,該信息會(huì)加強(qiáng)對(duì)本發(fā)明的了解。實(shí)施例1目的該實(shí)施例示范說(shuō)明各種催化劑金屬組合物對(duì)碳收率和碳納米管直徑的影響。方法制備各種催化劑前體來(lái)證明催化金屬對(duì)所得多壁產(chǎn)物的重要性。圖1表表明了用于該項(xiàng)比較的所產(chǎn)生的納米管產(chǎn)物。對(duì)于這些實(shí)施例,將如以上討論制備的粒徑150-300微米的600克催化劑前體置于流化床反應(yīng)器中。如以上所討論,本發(fā)明的方法將催化劑前體轉(zhuǎn)化成催化劑,并且隨后在所得催化劑上生長(zhǎng)多壁碳納米管。對(duì)于圖1中提供的每個(gè)實(shí)例,最終的催化劑在610℃下與氮?dú)庵?0%的乙烯反應(yīng)20分鐘,氣體流速為60L/分鐘(氣體流量/催化劑的質(zhì)量比為100L/分鐘每kg催化劑)。結(jié)果如圖1中所繪,催化金屬組成明顯影響所得多壁納米管產(chǎn)物。例如,試驗(yàn)PXE2-282、PXE2-285、PXE2-292和PXE2-293提供了用含有Co、Mo和約0.75重量%鐵-約1.9重量%鐵的催化劑制備的多壁碳納米管的有關(guān)數(shù)據(jù)。所得納米管批料的碳納米管收率高,其中位外徑為約6.72nm-約8.24nm,眾數(shù)外徑為約4.97nm-約6nm。75-85%的這些碳納米管的外徑小于10nm。具體地,PXE2-282代表眾數(shù)直徑為6.0nm的多壁納米管批料,該批料的中位直徑為8.24nm,并且該批料73%的直徑小于10nm。類似地,PXE2-285代表了眾數(shù)直徑是5.38nm的多壁納米管批料,該批料的中位直徑是6.72nm,且該批料85%的直徑小于10nm。從圖1可以很容易確定PXE2-292和PXE2-293的值。如本領(lǐng)域技術(shù)人員所知,術(shù)語(yǔ)“眾數(shù)”以該方式使用時(shí)表示在數(shù)據(jù)組中發(fā)生頻率最高的值。因此,對(duì)PXE2-285而言,在該批料內(nèi)納米管最常見的直徑是6.72nm。這些結(jié)果表明所述催化劑前體組合物產(chǎn)生了很高百分比收率的小直徑碳納米管,所述催化劑前體組合物包括催化劑前體總金屬約0.75-約1重量%的Co,催化劑前體總金屬約0.75-約1.9重量%的Fe,以及催化劑前體總金屬約0.4-約0.5重量%的Mo。相比之下,缺少鐵的催化劑前體粒子導(dǎo)致了碳收率的明顯減少。例如,試驗(yàn)PXE2-288表明,從前體催化劑配方中除去鐵時(shí),碳收率損失57%。有趣的是,所得產(chǎn)物包括中位外徑為6.98且眾數(shù)外徑為4.68的碳納米管。這暗示鐵并不是得到小直徑碳納米管的原因。然而,結(jié)果似乎暗示鉬在限制碳納米管直徑上起到了作用。例如,試驗(yàn)PXE2-284產(chǎn)生了中位外徑和眾數(shù)外徑分別為9.63nm和11.06nm的碳納米管。另外,只有54%的所得到碳納米管的外徑小于10nm,相比之下試驗(yàn)PXE2-285中的是85%,其中在前體組合物中使用了Mo。圖2A-2D進(jìn)一步圖示說(shuō)明了從催化劑前體中除去Fe或Mo之任一對(duì)碳納米管直徑分布的影響。結(jié)合起來(lái),這些結(jié)果表明鐵起到了保持碳收率的作用,而鉬則可促進(jìn)產(chǎn)生較小直徑的碳納米管。實(shí)施例2目的參考圖3,該實(shí)施例說(shuō)明了反應(yīng)溫度和氣體組成對(duì)碳收率和碳納米管直徑的影響。方法在該試驗(yàn)中使用具有圖1中PXE2-282和PXE2-285配方的催化劑組合物作為參考。為了確定反應(yīng)溫度對(duì)所得納米管產(chǎn)物的影響,反應(yīng)在610-675℃的溫度下進(jìn)行。進(jìn)一步,這些試驗(yàn)確定氣體物料中乙烯濃度在30-40%之間變化時(shí)由于乙烯濃度的變化對(duì)所得納米管產(chǎn)物的影響。結(jié)果增加反應(yīng)溫度和/或?qū)怏w組成中乙烯從40%降至30%時(shí)會(huì)降低碳收率,提高碳納米管直徑。因此,為碳收率最大化并且產(chǎn)生小直徑碳納米管,催化反應(yīng)應(yīng)在約610℃,且反應(yīng)性氣體混合物含40%的乙烯。實(shí)施例3目的該實(shí)施例比較了主要含具有3-6個(gè)管壁的小直徑多壁碳納米管(直徑4-8nm)的復(fù)合材料與包括大直徑碳納米管的復(fù)合材料的導(dǎo)電性。該實(shí)施例和其后的實(shí)施例使用根據(jù)本發(fā)明制備的在圖1中標(biāo)識(shí)為PXE2-282的材料(稱為SMW-100)。方法通過(guò)本發(fā)明的方法和催化劑組合物而制得的碳納米管(在下文中,SMW-100是指通過(guò)圖1中針對(duì)PXE2-282描述的催化劑組合物而制得的多壁碳納米管)與直徑分布在表1和圖4A-D中描述的各種商業(yè)途徑可得到的碳納米管進(jìn)行了比較。以下表1提供了各種商業(yè)途徑可獲得的多壁碳納米管和SMW-100的碳納米管直徑分布。例如,對(duì)于SMW-100,10%納米管的直徑小于4.2nm,全部納米管50%的直徑小于6.7nm,全部納米管90%的直徑小于12nm。10%50%90%SMW-1004.2nm6.7nm12.0nmMWCNTA5.5nm7.8nm13.0nmMWCNTB7.4nm12.0nm16.5nmMWCNTC7.1nm9.9nm13.3nm表1使聚碳酸酯Makrolon2600PC顆粒與表1中描述的碳納米管源熔融混合。熔融混合在以下條件下在DSM微混煉機(jī)(15cm3)中進(jìn)行:螺桿速度-200rpm;溫度-280℃;時(shí)間-5分鐘。從擠出料條(溫度:280℃,時(shí)間:1分鐘,壓力:100kN)制備壓板(60mm直徑x0.5mm厚度)。碳納米管樣品用TGA和TEM分析進(jìn)行表征(圖4A-D)。用Keithley6517A電位計(jì)、結(jié)合Keithley8009試驗(yàn)夾具(對(duì)于電阻率>107Ohmcm)或條式試驗(yàn)夾具(對(duì)于電阻率<107Ohmcm)測(cè)定電阻率。為了本公開內(nèi)容的目的,術(shù)語(yǔ)滲濾閾值是指材料中有一個(gè)、且只有一個(gè)連續(xù)的導(dǎo)電路徑時(shí)的碳負(fù)載濃度。結(jié)果圖5證明SMW-100碳納米管材料提供了最低的電滲濾閾值。如圖5中所描繪的,0.33重量%的CNT負(fù)載可滿足電滲濾的要求。如圖5所示,對(duì)于0.5-1.0重量%的負(fù)載,SMW-100提供了104-102Ohm/cm的電阻率讀數(shù)。相比之下,直徑是7-9nm(MWNTA)、10-11nm(MWNTC)、和12-15nm(MWNTB)的對(duì)比碳納米管分別得到0.50重量%、0.50重量%和0.55-0.60重量%的滲濾閾值?;谏鲜鼋Y(jié)果,使用具有表1和圖1所提供的SMW-100特征的直的(straight)多壁碳納米管的批料,能在比其它商業(yè)途徑可獲得的多壁碳納米管源更低的負(fù)載水平下提供更高的導(dǎo)電率性能。實(shí)施例4目的該研究比較基于分散在尼龍66樹脂中的商業(yè)途徑可獲得的多壁碳納米管的復(fù)合材料,與分散在尼龍66樹脂中的SMW-100碳納米管制備的復(fù)合材料的性能。方法CNT-尼龍6,6的混煉通過(guò)雙螺桿擠出進(jìn)行。然后將所得復(fù)合材料注射成型為標(biāo)準(zhǔn)的ASTM試驗(yàn)條和試驗(yàn)片(4英寸×4英寸×3.2毫米)。然后在注射成型的試驗(yàn)片上,使用標(biāo)準(zhǔn)的ProStat電阻計(jì)、根據(jù)體積和表面電阻的標(biāo)準(zhǔn)ASTMD-257進(jìn)行導(dǎo)電率測(cè)量。使用PRF-912B探頭在注塑片每個(gè)表面的25個(gè)預(yù)定位置上,即注塑片前表面上的25個(gè)點(diǎn)和后表面上的25個(gè)點(diǎn)測(cè)定表面電阻。設(shè)計(jì)該嚴(yán)格測(cè)試是為了發(fā)現(xiàn)由于材料和/或處理不均勻造成的電氣性能上的任何微小變化。片的前表面對(duì)應(yīng)于頂桿所處的位置。片的后表面對(duì)應(yīng)于工具的固定部分(更靠近噴嘴)。使用PRF-911同心環(huán),在每個(gè)試樣的5個(gè)位置測(cè)試片的體積電阻,并且對(duì)片的前和后的數(shù)據(jù)進(jìn)行平均。結(jié)果圖6A和6B中繪出了表面電阻數(shù)據(jù)。與商業(yè)途徑可獲得的多壁碳納米管(MWCNT)相比,模制成型后的SMW-100復(fù)合材料表現(xiàn)出更低且更均勻的電阻性能。MWCNT和SMW-100填充的樣品的表面電阻比較均勻,片的前后表面很一致。此外,基于尼龍6,6的與SMW-100的復(fù)合材料比基于尼龍6,6的與商業(yè)途徑可獲得的MWCNT牌號(hào)的復(fù)合材料顯示出更高的導(dǎo)電率值。SMW-100復(fù)合材料還進(jìn)一步顯示出均勻的電阻值,測(cè)試點(diǎn)之間和片的前后表面之間的標(biāo)準(zhǔn)偏差范圍更窄。如圖6A和6B所反映,由本發(fā)明的碳納米管材料,即直徑和管壁數(shù)分布窄的納米管批料制備的復(fù)合材料與現(xiàn)用材料相比,改善了導(dǎo)電率。實(shí)施例5目的該實(shí)施例比較了分別含以下納米管的薄膜的表面電阻率:SMW-100;單壁碳納米管(SWNT);雙壁碳納米管(DWNT);和,商業(yè)途徑可獲得的多壁碳納米管(實(shí)施例3的MWCNTB)。方法使用在1%Triton-X100表面活性劑中含1g碳納米管/升的溶液,制備具有不同透明度(80-95%透光度)的基于碳納米管的薄膜。溶液然后經(jīng)聲波處理和離心分離。使用棒涂方法在PET505基材上沉積各種碳納米管墨。結(jié)果如在圖7中所示,用SWNT制備的透明度80-90%的薄膜比薄膜中有其它類型碳納米管的材料表現(xiàn)出更高的導(dǎo)電性。然而,使用本發(fā)明的新型批料材料,即采用SMW-100制備的薄膜,比結(jié)合常規(guī)DWNT和MWNT的薄膜具有更好的導(dǎo)電率性能。根據(jù)本說(shuō)明書或本說(shuō)明書中公開的本發(fā)明的實(shí)施,本發(fā)明的其它實(shí)施方案對(duì)于本領(lǐng)域技術(shù)人員是顯而易見的。因此,上述說(shuō)明應(yīng)認(rèn)為僅僅是本發(fā)明的示范,本發(fā)明的真正范圍和精神應(yīng)由以下權(quán)利要求定義。當(dāng)前第1頁(yè)1 2 3